Guangdong Intelligent Robot Research Institute
Breakthrough Core Technologies for Independent Innovation
▼
Industrial robots are widely used in manufacturing industries such as automotive, electronics, and food. They can replace repetitive machine operations and are machines that rely on their own power and control capabilities to perform various functions. They can be commanded by humans or operate according to pre-programmed instructions. Now, let’s discuss the main components of industrial robots.
1. Main Body
The main mechanical body includes the base and the actuators, consisting of the upper arm, lower arm, wrist, and hand, forming a multi-degree-of-freedom mechanical system. Some robots also have walking mechanisms. Industrial robots typically have 6 degrees of freedom or even more, while the wrist commonly has 1 to 3 degrees of movement.
2. Drive System
The drive system of industrial robots can be categorized into hydraulic, pneumatic, and electric types based on the power source. Depending on the requirements, these three types can also be combined into a hybrid drive system. Alternatively, they can be driven indirectly through mechanical transmission mechanisms such as synchronous belts, gear trains, and gears. The drive system consists of a power unit and a transmission mechanism to execute corresponding actions. Each of these three basic drive systems has its own characteristics, with electric drive systems being the mainstream today.
Due to low inertia and high torque, the widespread adoption of AC and DC servo motors and their matching servo controllers (frequency converters, DC pulse width modulators) has occurred. This type of system does not require energy conversion, is easy to use, and has sensitive control. Most motors require precise transmission mechanisms, such as reducers. Their gears use gear speed converters to reduce the motor’s rotation speed to the desired level while achieving greater torque. When the load is large, simply increasing the power of the servo motor is not cost-effective; increasing output torque can be achieved within an appropriate speed range through reducers. Servo motors easily heat up and produce low-frequency vibrations when operating at low frequencies, and prolonged repetitive work is not conducive to ensuring their accuracy and reliable operation. The existence of precision reducers allows servo motors to operate at suitable speeds while enhancing the rigidity of the machine body and outputting greater torque. Currently, the mainstream reducers are of two types: harmonic reducers and RV reducers.
3. Control System
The robot control system is the brain of the robot and is a key factor determining its functions and capabilities. The control system issues command signals to the drive system and actuators based on the input program and performs control. The main task of industrial robot control technology is to control the robot’s range of movement, posture, trajectory, and timing of actions within its workspace. It features easy programming, software menu operation, a user-friendly human-machine interface, online operation prompts, and ease of use.
The controller system is the core of the robot, and foreign companies have conducted strict closed experiments in China. In recent years, with the development of microelectronics technology, the functions of microprocessors have become increasingly powerful, while their prices have decreased. Currently, 32-bit microprocessors are available on the market for as low as 1-2 US dollars. The high cost-performance ratio of microprocessors has provided new development opportunities for robot controllers, making it possible to develop low-cost, high-performance robot controllers. To ensure that the system has sufficient computing and storage capabilities, most robot controllers now use powerful ARM series, DSP series, POWERPC series, and Intel series chips.
Due to existing general-purpose chips not fully meeting the requirements of some robot systems in terms of price, functionality, integration, and interfaces, there has been a demand for SoC (System on Chip) technology in robot systems. This integrates specific processors with necessary interfaces, simplifying the design of peripheral circuits and reducing system size and cost. For example, Actel integrates the NEOS or ARM7 processor core into its FPGA products, forming a complete SoC system. Research on robot technology controllers mainly concentrates in the United States and Japan, with mature products available, such as those from DELTATAU in the United States and PONTEK in Japan. Their motion controllers are based on DSP technology and adopt an open structure based on PC.
4. Perception System
This consists of internal sensor modules and external sensor modules, obtaining meaningful information about the internal and external environmental states.
Internal Sensors: These sensors detect the robot’s own state (e.g., angles between arms) and are mostly position and angle sensors. Specific types include position sensors and angle sensors.
External Sensors: These sensors detect the robot’s environment (e.g., detecting objects, measuring distances to objects) and conditions (e.g., checking if grasped objects have slipped). Specific types include distance sensors, vision sensors, and tactile sensors.
The use of intelligent sensor systems enhances the mobility, practicality, and intelligence of robots. The human perception system is agile in processing external world information, while for certain specialized information, sensors can be more effective than human systems.
5. End Effector
The end effector is a component connected to the last joint of the robotic arm. It is generally used to grasp objects, connect with other mechanisms, and perform required tasks. In robot manufacturing, end effectors are generally not designed or sold; in most cases, they only provide a simple gripper. Typically, the end effector is mounted on the flange of the robot’s 6-axis to complete tasks in a given environment, such as welding, painting, gluing, and loading/unloading parts.
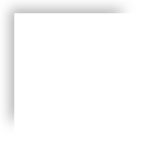
Servo Motor
Servo drives, also known as “servo controllers” or “servo amplifiers”, are controllers used to manage servo motors, functioning similarly to frequency converters for standard AC motors, and are part of the servo system. They generally control servo motors in three ways: position, speed, and torque, achieving high-precision positioning of the transmission system.
1. Classification of Servo Motors
They are divided into two main categories: DC and AC servo motors. AC servo motors are further divided into asynchronous and synchronous servo motors. Currently, AC systems are gradually replacing DC systems. Compared to DC systems, AC servo motors have advantages such as high reliability, good heat dissipation, low rotational inertia, and the ability to operate under high voltage conditions. Because they are brushless and do not have commutators, AC servo systems are also referred to as brushless servo systems, and the motors used within are brushless cage asynchronous motors and permanent magnet synchronous motors.
1) DC servo motors are divided into brushed and brushless motors.
① Brushed motors are low-cost, have a simple structure, high starting torque, a wide speed range, and are easy to control, but require maintenance (changing carbon brushes), generate electromagnetic interference, and have environmental requirements, typically used in cost-sensitive general industrial and civilian applications;
② Brushless motors are compact and lightweight, provide high output, fast response, high speed, low inertia, stable torque, smooth rotation, complex control, intelligent features, and flexible electronic commutation methods, whether square wave or sine wave commutation. They are maintenance-free, energy-efficient, have low electromagnetic radiation, low temperature rise, and long service life, suitable for various environments.
2. Characteristics of Different Types of Servo Motors
1) Advantages and Disadvantages of DC Servo Motors
Advantages: precise speed control, rigid torque-speed characteristics, simple control principles, ease of use, and low cost.
Disadvantages: brush commutation, speed limitations, additional resistance, generation of wear particles (not suitable for dust-free or explosive environments).
2) Advantages and Disadvantages of AC Servo Motors
Advantages: good speed control characteristics, smooth control across the entire speed range, almost no oscillation, over 90% efficiency, low heat generation, high-speed control, high precision positioning control (depending on encoder accuracy), and the ability to achieve constant torque within the rated operating area, low inertia, low noise, no brush wear, maintenance-free (suitable for dust-free and explosive environments).
Disadvantages: more complex control, the driver parameters need to be adjusted on-site to determine PID parameters, and require more wiring.
Currently, mainstream servo drives generally use digital signal processors (DSP) as the control core, enabling more complex control algorithms and achieving digitization, networking, and intelligence. The power devices commonly adopt driver circuits designed around intelligent power modules (IPM), which integrate driving circuits and include fault detection and protection circuits for overvoltage, overcurrent, overheating, and undervoltage. A soft-start circuit is also added to the main circuit to reduce the impact of the startup process on the driver. The power drive unit first rectifies the input three-phase power or mains power through a three-phase full-bridge rectifier circuit to obtain the corresponding DC power. The rectified three-phase power or mains power is then converted through a three-phase sine PWM voltage-type inverter to drive a three-phase permanent magnet synchronous AC servo motor. The entire process of the power drive unit can be simply described as AC-DC-AC. The main topology circuit of the rectifier unit (AC-DC) is a three-phase full-bridge uncontrolled rectifier circuit.
3. Wiring Diagram of Servo System
1. Driver Wiring
The servo driver mainly consists of control circuit power supply, main control circuit power supply, servo output power supply, controller input CN1, encoder interface CN2, and connection point CN3. The control circuit power supply is a single-phase AC power supply, and the input power can be single-phase or three-phase, but it must be 220V. This means that when using three-phase input, our three-phase power supply must be transformed using a transformer. For smaller power drivers, single-phase direct drive is possible, and the single-phase connection must connect to R and S terminals. The servo motor output U, V, W must not be connected to the main circuit power supply, as it may burn out the driver. The CN1 port is mainly used for connecting the upper-level controller, providing input, output, encoder ABZ three-phase output, and various monitoring signal analog outputs.
2. Encoder Wiring
From the diagram, we can see that among the nine terminals, we only use five: one shielded wire, two power lines, and two serial communication signals (+-), which are similar to our common encoder wiring.
3. Communication Port
The driver is connected to the upper-level PC, PLC, HMI, etc. through the CN3 port, using MODBUS communication to control the driver, and can use RS232 or RS485 for communication.
4. Servo Driver Market
Robots have very strict requirements for joint drive motors, and AC servo motors are widely used in industrial robots. Currently, the high-end domestic market is mainly occupied by foreign well-known enterprises, primarily from Japan and Europe and America, and there is great potential for domestic replacements in the future. At present, foreign brands occupy nearly 80% of the Chinese AC servo market, mainly from Japan and Europe and America. Among these, Japanese products hold the largest market share of about 50%, with well-known brands including Panasonic, Mitsubishi Electric, Yaskawa, Sanyo, and Fuji, whose products are characterized by technology and performance levels that meet the needs of Chinese users, gaining a stable and continuous customer base with good cost performance and high reliability, particularly dominating the small and medium-sized OEM market.
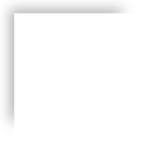
Precision Reducer
Recently, I saw a piece of news: the robot industry needs to overcome the “bottleneck” problem, which resonated with me. With the increase in labor costs, it has become a trend for industrial robots to replace humans. As the foundation of intelligent manufacturing, industrial robots are constrained by core components that hinder the development of China’s robot industry. According to related surveys, domestic robot reducers are generally reliant on imports. For the robot industry in China to thrive, it must decisively solve the core component issues.
Next, I will introduce the core precision components of industrial robots: reducers. Compared to general reducers, robot reducers are required to have a short transmission chain, small size, high power, light weight, and ease of control. In the reducer industry, we must mention two giants: Nabtesco (also known as Nabtesk) and Harmonica Drive, commonly referred to as RV reducers and harmonic reducers. They almost monopolize the global market for robot reducers. Both types of reducers are manufactured with micron-level processing precision, making reliability during mass production challenging, let alone high-speed operation at thousands of revolutions per minute while ensuring long life. The reducers applied in industrial robots on the market mainly fall into two categories: RV reducers and harmonic reducers.
RV Reducers: They use low tooth difference engagement but typically employ cycloidal pin wheels compared to harmonic reducers. RV reducers consist of cycloidal pin wheels and planetary brackets. The key to RV reducers lies in their manufacturing and assembly processes, which provide higher fatigue strength, rigidity, and lifespan. Unlike harmonic drives, which significantly lose motion accuracy over time, RV reducers are used in high-torque joints such as robot legs, waists, and elbows, with large load industrial robots often utilizing RV reducers for their first, second, and third axes.
They have much higher fatigue strength, rigidity, and lifespan than the commonly used harmonic drives, and their backlash accuracy remains stable, unlike harmonic drives that significantly lose motion accuracy over time. Therefore, many countries worldwide prefer RV reducers for high-precision robot drives, indicating a trend towards gradually replacing harmonic reducers.
RV Reducer Exploded View
Harmonic Reducers: They also use low tooth difference engagement, with a key flexible gear that requires repeated high-speed deformation, making it relatively fragile, with limited load capacity and lifespan.
Harmonic reducers are a type of harmonic drive device, which includes harmonic accelerators and harmonic reducers. Harmonic reducers mainly consist of rigid wheels, flexible wheels, and a radial deforming wave generator. They utilize flexible gears to create controllable elastic deformation waves, causing relative tooth misalignment between rigid and flexible wheels to transmit power and motion. This type of transmission fundamentally differs from typical gear transmissions and has special considerations in engagement theory, collective computation, and structural design. Harmonic gear reducers have advantages such as high precision and high load capacity. Compared to ordinary reducers, they use 50% less material, resulting in at least a one-third reduction in size and weight. Therefore, harmonic reducers are primarily used in small robots, characterized by their small size, light weight, high load capacity, and high motion accuracy, with a large single-stage transmission ratio. They are generally used for small load industrial robots or several axes at the end of large robots.
Harmonic Reducer Exploded View
Nabtesco of Japan proposed the RV-type design in the early 1980s, achieving substantial breakthroughs in RV reducer research by 1986, which took 6-7 years; while domestic companies such as Nantong Zhenkang and Hengfengtai also took 6-8 years to produce results. Does this mean that local Chinese enterprises have no opportunities? Fortunately, after several years of layout, Chinese companies have finally made some breakthroughs. Major domestic suppliers include Nantong Zhenkang, Qin Chuan Machine Tool, Wuhan Jinghua, Zhejiang Hengfengtai, and Zhejiang Shuanghuan Drive. It is said that Nantong Zhenkang’s output has surpassed 10,000 units, and the production line of Qin Chuan Machine Tool has been opened, with output gradually increasing. Qin Chuan Machine Tool’s 90,000 sets of industrial robot joint reducer technology transformation project and industrial robot joint reducer production line have a combined investment of 314 million yuan.
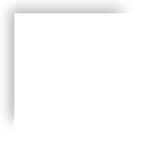
Control System
The robot control system is the brain of the robot and is a key factor determining its functions and capabilities. The control system issues command signals to the drive system and actuators based on the input program and performs control. The following article mainly introduces the robot control system.
1. Control System of the Robot
The purpose of “control” refers to having the controlled object behave in an expected manner. The basic condition of “control” is understanding the characteristics of the controlled object.
The essence is controlling the output torque of the driver. The robot’s control system
2. Basic Working Principle of the Robot
The working principle is teaching and reproduction; teaching, also known as guided teaching, involves manually guiding the robot through the required operation process step by step, during which the robot automatically memorizes the posture, position, process parameters, motion parameters, etc., of each action taught, generating a continuous execution program. After teaching, the robot only needs a start command to automatically complete the entire process according to the taught actions;
3. Classification of Robot Control
1) Divided into open-loop control and closed-loop control based on feedback presence:
Open-loop precise control conditions: knowing the model of the controlled object accurately, and this model remains unchanged during the control process.
2) Based on expected controlled quantities, divided into: force control, position control, and mixed control.
Position control is divided into: single-joint position control (position feedback, position speed feedback, position speed acceleration feedback), multi-joint position control.
Multi-joint position control is divided into decomposed motion control and centralized control. Force control is divided into: direct force control, impedance control, and force-position mixed control.
3) Intelligent control methods
Fuzzy control, adaptive control, optimal control, neural network control, fuzzy neural network control, expert control.
4. Hardware Configuration and Structure of the Control System: Electrical Hardware and Software Architecture.
Due to the large number of coordinate transformations and interpolation calculations, as well as lower-level real-time control involved in the robot’s control process, most robot control systems on the market adopt a layered structure of microcomputer control systems, typically using a two-level computer servo control system.
1) Specific Process:
The main control computer receives the work instructions input by the staff, first analyzes and interprets the instructions, determining the motion parameters of the hand. It then performs kinematics, dynamics, and interpolation calculations, finally deriving the coordinated motion parameters for each joint of the robot. These parameters are output to the servo control level through communication lines as the set signals for each joint servo control system. The servo drives on the joints convert this signal from D/A and drive each joint to produce coordinated motion.
The sensors feed back the motion output signals of each joint to the servo control level computer, forming a local closed-loop control, achieving precise control of the robot’s motion in space.
2) Motion Control Based on PLC: Two Control Methods:
① Using the output port of the PLC to generate pulse commands to drive the motor while using general I/O or counting components to implement closed-loop position control of the servo motor.
② Using an external extended position control module of the PLC to achieve closed-loop position control of the motor. This method mainly issues high-speed pulses for control, which belongs to position control, and position control is generally more point-to-point.
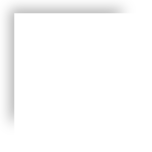
Important Parameters of the Robot
This article focuses on the technical parameters of industrial robots, with detailed descriptions and illustrations, hoping to be of help to everyone!!
The technical parameters of robots reflect their capabilities and highest operational performance, which are essential considerations in the design and application of robots. The main technical parameters of robots include degrees of freedom, resolution, working space, working speed, and working load.
1. Degrees of Freedom
This refers to the number of independent axes of motion the robot possesses.
The degrees of freedom of a robot refer to the number of independent motion parameters required to determine the position and posture of the robot’s hand in space. The number of degrees of freedom of a robot generally equals the number of joints.
Common robots typically have 5 to 6 degrees of freedom. Some robots also come with external axes.
2. Joint
This refers to the moving pairs that allow relative motion between the components of the robot arm.
3. Working Range
This refers to the entire spatial range that the robotic arm or end effector can reach.
The shape of the working range depends on the number of degrees of freedom and the types and configurations of the motion joints. The working range of robots can generally be represented using graphical or analytical methods.
4. Speed
This refers to the distance moved or angle rotated by the mechanical interface center or tool center point per unit time during the robot’s operation under load conditions and at a constant speed.
5. Working Load
This refers to the maximum weight that the robot wrist can bear at any position within its working range, typically expressed in terms of mass, torque, or moment of inertia.
It is also related to parameters such as running speed and acceleration. The working load is generally indicated by the weight of the workpiece that the robot can grasp during high-speed operation.
When considering the load weight for handling robots, the total weight of the gripper and the workpiece must be taken into account.
6. Resolution
This refers to the smallest movement distance or angle that the robot can achieve.
7. Accuracy
Repeatability or repeat positioning accuracy: This refers to the difference in reaching a specific target position repeatedly. For example, if you require an axis to move 100 mm but in the first instance it actually moved 100.01, and when repeating the same action it moved 99.99, the difference of 0.02 is the repeat positioning accuracy. It measures the concentration of a series of error values, i.e., repeatability. The accuracy of the robot is not only dependent on the joint reducers and transmission devices but also significantly influenced by the mechanical assembly process, as many issues arise from improper assembly leading to decreased repeat positioning accuracy.
This article is reproduced from Robot Network.

Guangdong Intelligent Robot Research Institute (abbreviated as “Guangdong Academy”)
Approved by the Guangdong Provincial People’s Government and established by the Dongguan Municipal People’s Government, it is a new type of research institution headquartered in the Songshan Lake University Innovation City. With the development philosophy of “investigating things and seeking principles, maintaining integrity while innovating,” it focuses on high-precision and efficient intelligent industrial robots as its key research direction. It has successively been approved for two Guangdong Provincial Innovation Teams and one Dongguan City Innovation Team. The intelligent equipment R&D center it has built has been approved as one of the first national specialized makerspaces. The Guangdong Academy has formed core technologies and products in fields such as integrated drive control, multi-axis robots, AGV, Internet of Things, machine vision, intelligent equipment, and industrial big data. It has served nearly 300 leading enterprises in robot and intelligent manufacturing applications, including Jinsheng Co., Gionee, BBK Electronics, Huawei, Gree, Midea, and Suori. It cooperated with the listed company Jinsheng Co. to build an intelligent manufacturing workshop oriented towards Industry 4.0, which was rated as one of the first national intelligent manufacturing demonstration projects (46 units nationwide were approved, and Dongguan is the only one), and was selected as the only demonstration site for the national intelligent manufacturing pilot demonstration exchange meeting.

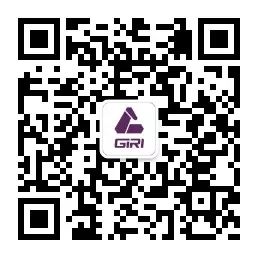