The structure of the robot adopts a spatial open-link structure, with the movement of each joint being independent. To achieve the motion trajectory of the end point, multi-joint motion coordination is required. Therefore, its control system is much more complex than ordinary control systems, featuring the following characteristics: 1. The control of the robot is closely related to the kinematics and dynamics of the structure. The state of the robot’s gripper can be described in various coordinate systems, with different reference coordinate systems chosen as needed and appropriate coordinate transformations performed; 2. It often requires solving the direct and inverse kinematics problems, and in addition, the influences of inertial forces, external forces (including gravity), Coriolis forces, and centripetal forces must be considered. 3. A simple robot has at least 3 to 5 degrees of freedom, while more complex robots have a dozen or even dozens of degrees of freedom. Each degree of freedom generally contains a servo mechanism, which must coordinate to form a multivariable control system. 4. The task of organically coordinating multiple independent servo systems to act according to human will, and even endowing the robot with certain intelligence, can only be accomplished by a computer. Therefore, the robot control system must be a computer system. 5. The mathematical model describing the robot’s state and motion is a nonlinear model, with parameters varying with different states and external forces, and there is coupling between variables. 6. The robot’s motion can be completed in different ways and paths, thus presenting an ‘optimal’ problem. More advanced robots can use artificial intelligence methods to establish a large information database with the help of the database for control, decision-making, management, and operation.Traditional automatic machinery focuses on its own actions, while industrial robot control systems emphasize the interrelationship between the body and the operating object. Thus, the robot control system is a coupled, nonlinear multivariable control system closely related to the principles of kinematics and dynamics. Depending on the actual working conditions, various control methods can be employed, from simple programming automation, microprocessor control to small computer control, and so on. The Characteristics and Basic Requirements of Robot Control Systems To implement good control over the robot, it is important to understand the characteristics of the controlled object. From what we understand about robot dynamics, it has the following characteristics: 1. The robot is essentially a nonlinear system. Many factors contribute to the nonlinearity of the robot, including structural aspects, transmission components, drive elements, etc. 2. There is a coupling effect between joints, manifested as the motion of one joint affecting the dynamics of others, meaning each joint must endure disturbances caused by the motion of others. 3. It is a time-varying system, with dynamic parameters changing as the joint motion positions vary.
From a usage perspective, robots are a special type of automation device, and their control has the following characteristics and requirements: 1. Multi-axis motion coordination control to produce the required working trajectory. Since the movement of the robot’s hand is a composite motion of all joint movements, to make the hand move according to set patterns, it is necessary to control the coordinated actions of each joint well, including motion trajectory, action timing, and other aspects of coordination. 2. High position accuracy with a wide range of speed adjustments. 3. The static error rate of the system should be small. 4. The speed error coefficients of each joint should be as consistent as possible. 5. No overshoot in positioning, with dynamic response as fast as possible. 6. Acceleration (deceleration) control is required. 7. From the operator’s perspective, the control system should have a good human-machine interface, minimizing the requirements on the operator. 8. From the system cost perspective, it is required to minimize the hardware costs of the system and to rely more on software servo methods to improve the performance of the control system.
Robot Control Methods There is no unified standard for classifying industrial robot control methods: A. Robot Motion Control Methods a. Robot Motion Control Methods (1. Robot Position Control Methods: Positioning Control Methods—Fixed Position Method, Multi-Point Position Method, Servo Control Method; Path Control Methods: Continuous Trajectory Control, Point-to-Point Control) (2. Robot Speed Control Methods: Speed Control Methods—Fixed Speed Control, Variable Speed Control; Acceleration Control Methods—Fixed Acceleration Control, Variable Acceleration Control) (3. Robot Force Control Methods) b. Robot Action Sequence Control Methods B. Robot Teaching Control Methods (1. Teaching with Actual Robot: Direct Teaching Method—Power Level Disengagement Teaching, Servo Level Connection Teaching; Remote Control Teaching Method—Teaching Box Teaching Method, Joystick Teaching Method, Master-Slave Teaching) (2. Teaching without Robot: Indirect Teaching Method—Model Robot Teaching, Special Tool Teaching; Offline Teaching Method—Numerical Input Teaching, Graphic Teaching, Software Language Teaching) Structure and Working Principle of Robot Control Systems An industrial robot system is usually divided into two main parts: the robot body and the control system. The elements that constitute the robot control system mainly include the computer hardware system and operational control software, input/output devices and apparatus, drive systems, and sensor systems. The control system of industrial robots is an important component of the robot, designed to complete designated work tasks, with basic functions including: 1. Memory Function 2. Teaching Function 3. Peripheral Device Communication Function 4. Coordinate Setting Function 5. Human-Machine Interface 6. Sensor Interface 7. Position Servo Function 8. Fault Diagnosis and Safety Protection Function. Of course, there is much more knowledge about robot control, such as robot single-joint position servo control, robot force control, and intelligent control of robots, etc.
-END-
Image and text source from Robot Network
Initial review: Tang Cuimei
Re-examination: Huo Xiaoyin
Final review: Wang Xianfang
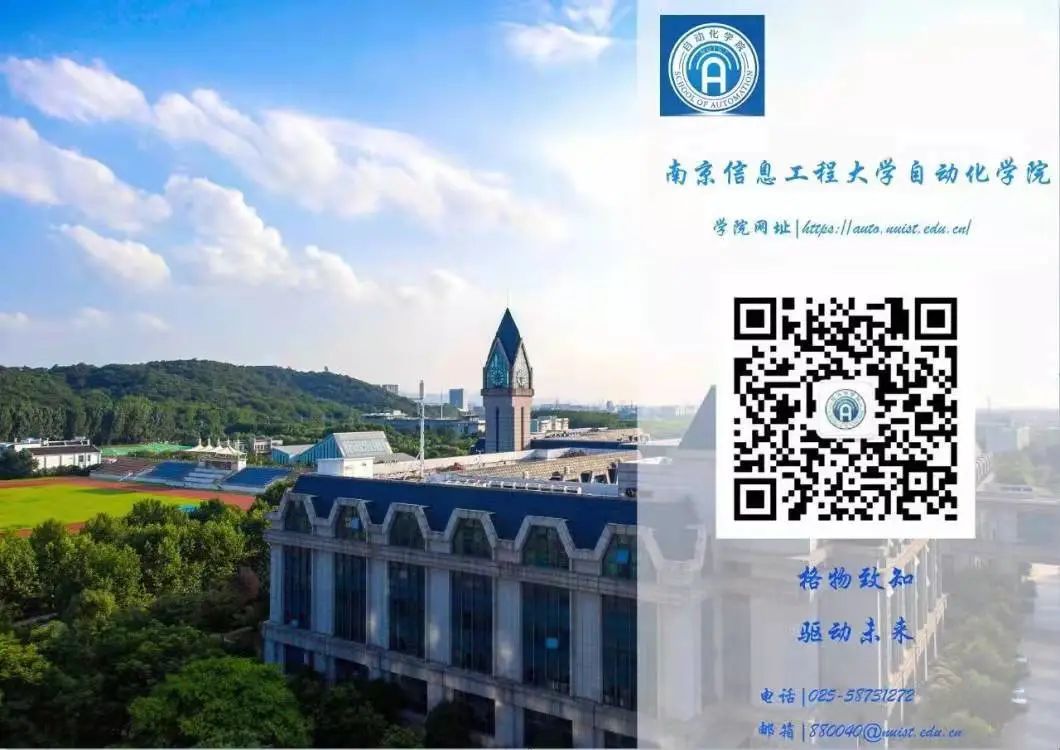