Click blue words to followServo and Motion Control
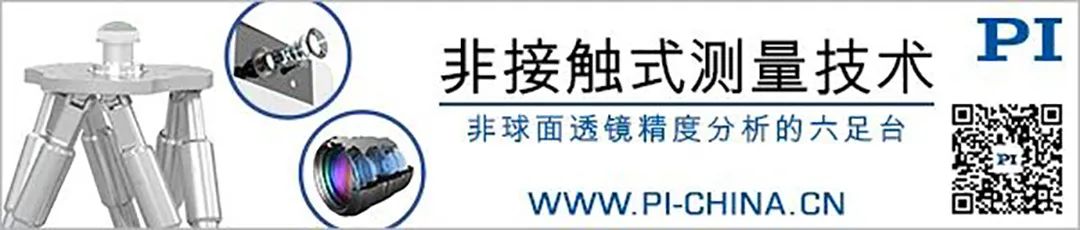
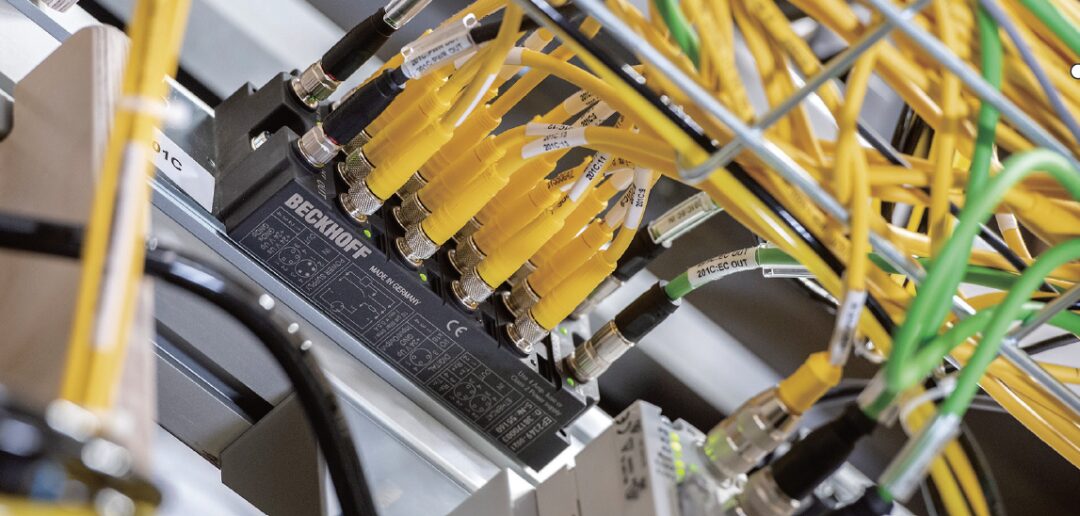
Determinism and Reliability
Industrial-Grade Ethernet Hardware
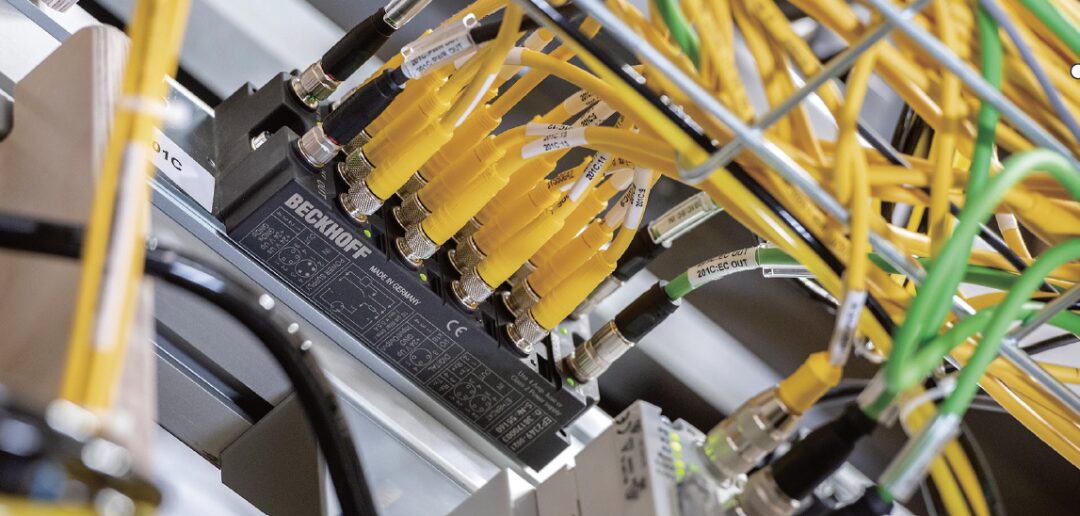
Providing Synchronization Functions
Functional Safety
Popular Articles
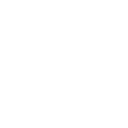
Chairman Su Meiping of Transmission Network: Twenty Years of Motion Control
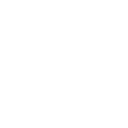
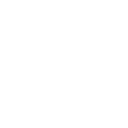
China Motion Control/Direct Drive Industry Summit Forum
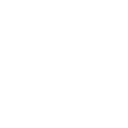
Professor Yang Ming: Thoughts on Three Issues of Servo Positioning Systems
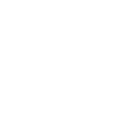
“Paying Tribute to the Original Intention, Paying Tribute to Twenty Years of Motion Control” Interview
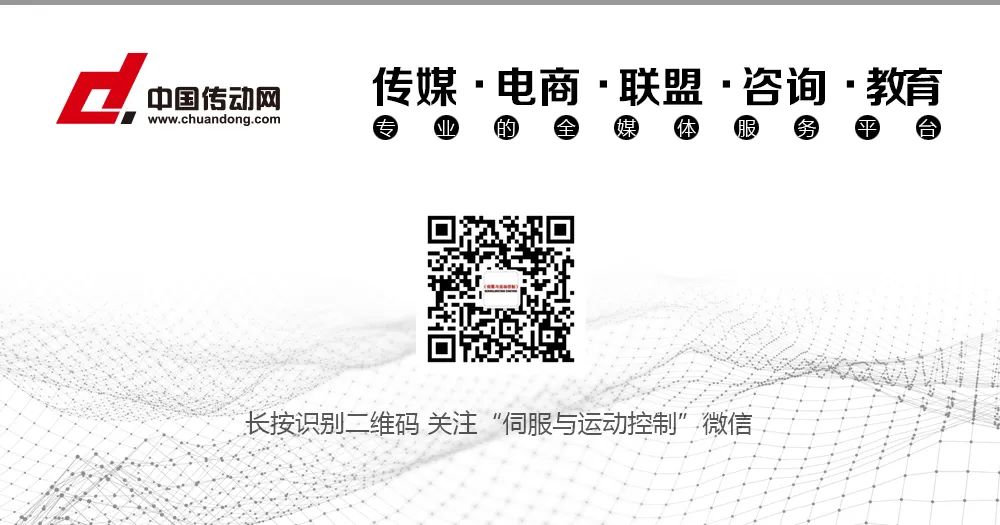