
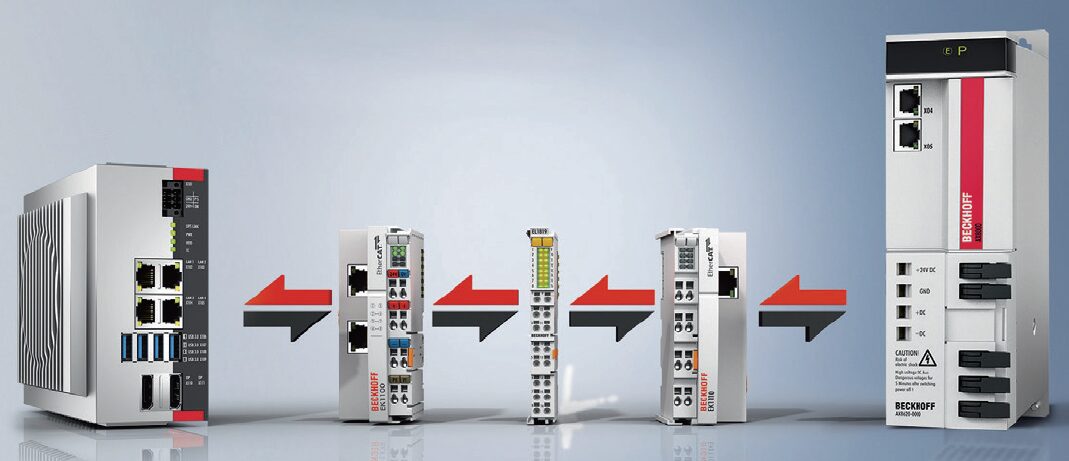
In manufacturing applications that require determinism and real-time performance, EtherCAT industrial Ethernet systems have significant advantages over standard Ethernet. Image source: Beckhoff
Author | Sree Swarna Gutta
In industrial environments, the determinism and real-time nature of data transmission are crucial. EtherCAT G offers more reliable communication for industrial applications through its unique functional principles and industrial-grade hardware.
Industrial application network technologies have made significant progress in both functionality and quantity. The fieldbus, introduced in the late 1980s, was a digital replacement for analog 4-20mA relay systems used in programmable logic controllers (PLCs), but the emerging PC-based machine control systems have faster scan cycles, making fieldbuses often lag behind.
During the subsequent fieldbus wars, engineers and factory managers began to favor Ethernet-based real-time bus systems, which not only provide high-speed transmission but also help promote the convergence of Information Technology/Operational Technology (IT/OT).
Many functions currently in use have been validated, resulting in widespread application of Ethernet-based systems. However, the question is not which type of system factories should choose, but whether they need to choose one at all. Since its inception, Ethernet, compliant with the IEEE 802.3 communication standard, has been in use for a long time, and many new components support communication without needing to be bundled with traditional fieldbuses. Does this help factories escape the costly management switches and other shortcomings of popular fieldbuses? Can it escape vendor proprietary communication protocols?
Despite certain limitations of some industrial Ethernet systems, applying standard Ethernet directly to critical manufacturing, packaging, and material handling scenarios could pose risks.
The real-time performance, time synchronization, and independence sought by engineers in various applications have been achieved in open technologies (such as EtherCAT industrial Ethernet systems). EtherCAT can provide determinism, robust hardware suited for industrial environments, flexibility in system architecture, and built-in security to protect machines and enterprise networks without intervention from the IT department.
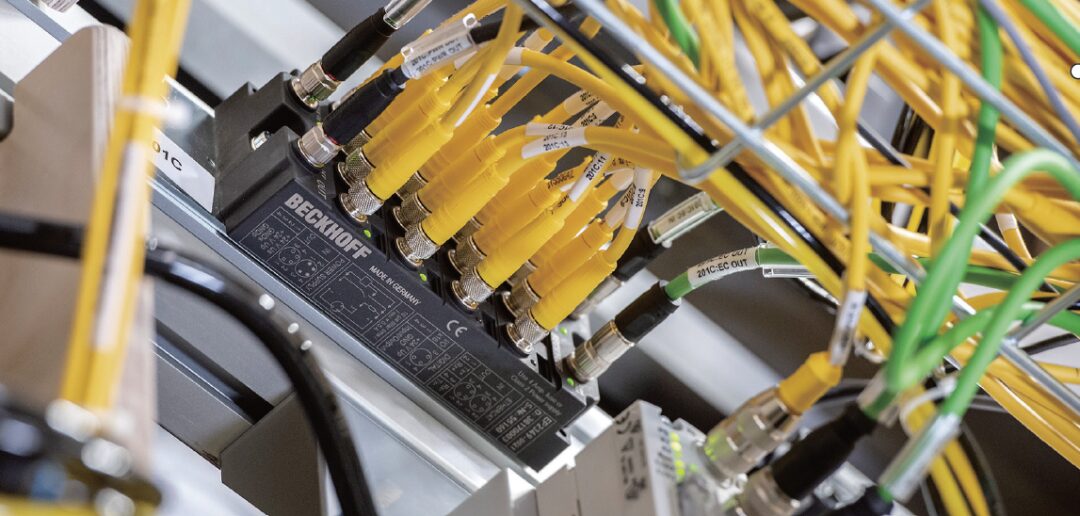
▎Industrial applications require industrial-grade devices. EtherCAT provides IP67 rated I/O modules that can be installed in industrial environments.
Determinism and Reliability
In home environments, using Ethernet rarely leads to severe consequences due to system failures. Typically, it results in web pages failing to load, emails not sending, or system crashes, none of which are critical tasks. Waiting an additional 2 seconds or even a minute does not meet the definition of a critical task. Most consumers do not particularly care about the shortcomings of standard Ethernet, such as poor bandwidth utilization, stack delays, switch delays, and star topology.
However, in industrial environments, reliable data transmission is crucial. If the instructions from the device controller are not transmitted promptly to various components, or if the controller does not receive sufficient feedback, it could lead to severe consequences. Compared to standard Ethernet and other industrial Ethernet protocols, EtherCAT provides the reliability and determinism required across various industry applications. Industrial Ethernet systems can ensure reliable and synchronized sending and receiving of data frames between machines and factories of different scales, even at communication speeds of 100Mbit/s.
EtherCAT G and G10, with transmission speeds of 1Gbit/s and 10Gbit/s respectively, can provide the necessary bandwidth for applications such as high-resolution machine vision, high-end measurement, advanced motion control, robotics, and complex mechatronic systems. Coupled with the newly introduced branch controller mode, EtherCAT G can reduce industrial communication time by 2-7 times and increase bandwidth by 10 times (depending on the application). EtherCAT G10 can even increase bandwidth by 100 times.
The unique branch controller mode allows a 100Mbit/s EtherCAT network to be integrated into the EtherCAT G branch, and vice versa, simply by adding couplers. This ensures the scalability of the system, allowing for upgrades of the application system without a complete overhaul and replacement.
EtherCAT G technology was introduced by Beckhoff Automation in Germany in 2018 as an extension of the EtherCAT technology protocol. In 2019, the EtherCAT Technology Group (ETG) technical committee officially supported this technology after review. Currently, ETG is working to add EtherCAT G technology to the technical specifications.
Industrial-Grade Ethernet Hardware
Manufacturing environments require technology that can withstand extreme conditions. Compared to consumer-grade routers and switches that IT departments might use in offices, industrial-grade I/O terminals offer more form factors and functionalities. These may include IP20 rated cards for batch production equipment, IP67 and IP69K rated I/O modules installed on-site, and plug-in modules mounted on PCB boards. Even standard Ethernet cables should be configured with appropriate shielding and use connectors designed specifically for industrial applications; otherwise, communication issues may arise.
As an open solution, EtherCAT can connect with “regular Ethernet” and over 25 other fieldbus and industrial Ethernet systems simply by adding couplers or gateways without causing transmission delays. Using multiple couplers, EoE (Ethernet over EtherCAT) with TCP/IP communication capabilities can ensure interoperability of the EtherCAT network.
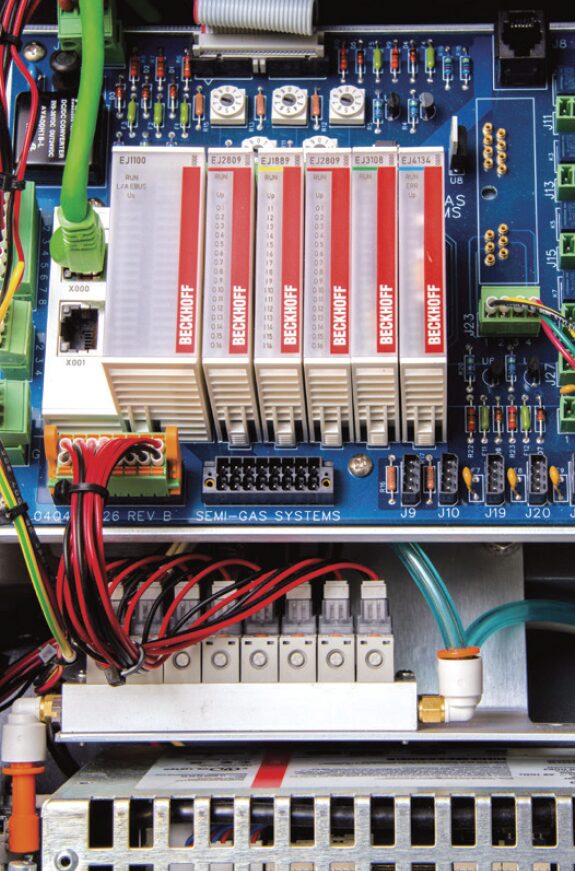
▎The EtherCAT plug-in module installed on the PCB board helps achieve optimal batch production of devices.
Providing Synchronization Functionality
A single EtherCAT network can support 65,535 devices without the need for MAC or IP addresses to automatically configure hardware. It features built-in free topology selection, whether star, line, tree, or other types, without performance loss. Improved diagnostic interfaces allow for the collection of existing diagnostic information from the network, enhancing already robust diagnostic capabilities and making troubleshooting easier.
Through dynamic processing, EtherCAT can communicate in a loop with many nodes at a rate of 100 Mbit/s within a single Ethernet frame. Using EtherCAT, 1,000 distributed digital I/Os can be polled every 30μs, and 100 servo axes can be polled every 100μs.
EtherCAT ASIC or FPGA hardware is integrated within the slave stations and can be directly accessed from the master station’s network card. The communication protocol processing is independent of CPU performance, protocol stack, or software implementation.
EtherCAT network devices are synchronized through a distributed clock. All EtherCAT devices have a built-in local clock to continuously maintain a standard time base, with clock deviations of less than 100 ns, representing different communication run times. This ensures precise synchronization between all devices. It also allows for deterministic actual value acquisition and deterministic setpoint output to achieve absolutely precise response times.
Functional Safety
EtherCAT also provides FSoE (Safety over EtherCAT), a functionally safe protocol certified by TüV. All other redundant safety devices use FSoE, which employs a “black channel” method to provide necessary safety communication redundancy via the same Ethernet cable used for machine control. FSoE offers digital and analog safety for numerous discrete and process industrial applications.
The functional principles of EtherCAT also help protect factories from network threats. The EtherCAT master controls all slave devices, rendering man-in-the-middle attacks ineffective. Because the system is not based on Internet protocols, malware cannot propagate through EtherCAT. The network only forwards EtherCAT frames, filtering out any other Ethernet frames, including those with corrupted data or infected frames, from the controller chip. These features, combined with the lack of managed switches, eliminate the need for IT department intervention in production systems.
Key Concepts:
■ Industrial Ethernet provides higher levels of connectivity for factory floors, allowing better real-time access to information.
■ EtherCAT provides determinism, robust hardware, and built-in security for industrial environments to protect machines and enterprise networks.
Consider This:
What benefits will your company gain from industrial Ethernet? What improvements can be made?
– END –
This article is from the CONTROL ENGINEERING China, October 2020 issue, under the “Technical Article” section, originally titled:The Advantages of Merging Ethernet and Fieldbus
Recommended Reading
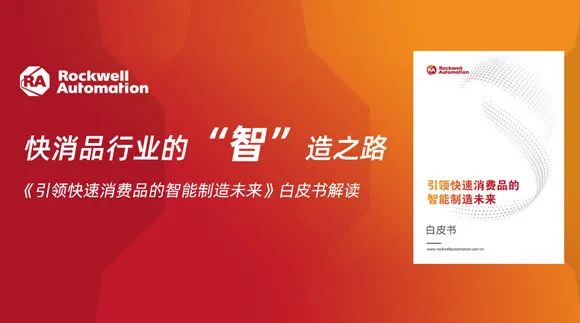
The Intelligent Manufacturing Path of the Fast-Moving Consumer Goods Industry—Interpretation of the White Paper “Leading the Future of Intelligent Manufacturing in Fast-Moving Consumer Goods”
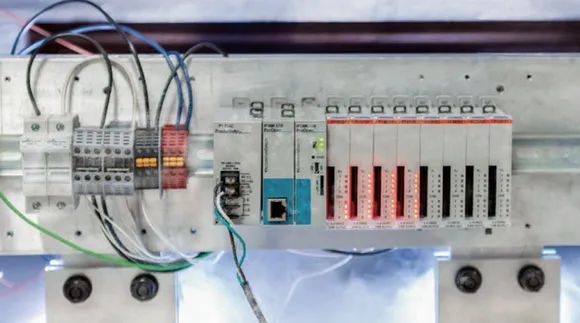
Has your controller been open-sourced?—Discussing the Advantages of Open Source for Industrial Microcontrollers
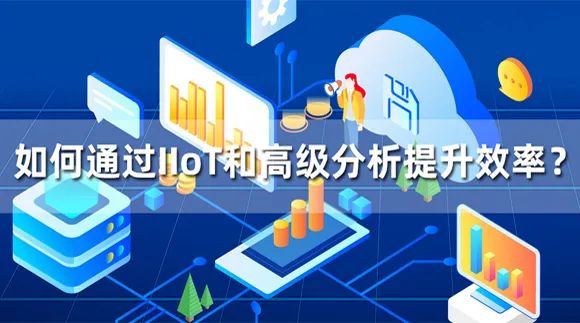
Doing the Right Thing | Enhancing Overall Equipment Efficiency (OEE) Through IIoT and Advanced Analytics Tools
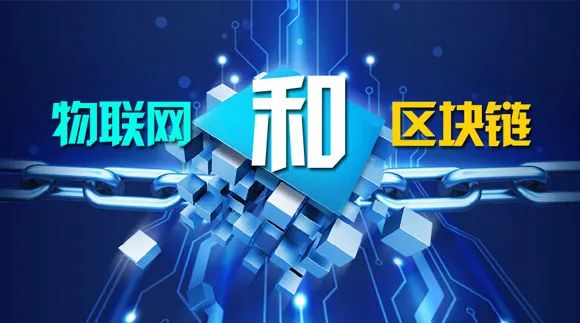
Blockchain 3.0—Application of Blockchain Technology in Intelligent Manufacturing
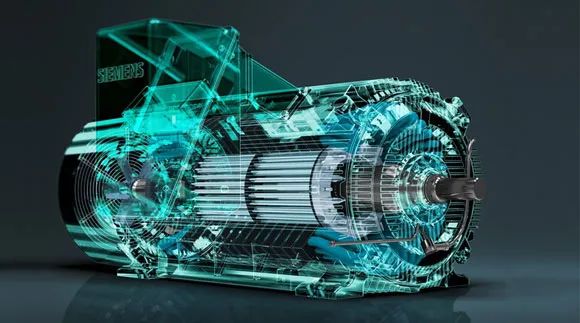
Four Areas of Innovation in Motors—All-Electric Aircraft May Be Realized in the Next Decade

We invite you to join the industrial automation community.
Since 2020, to strengthen communication between editors and readers, and between readers themselves, we have established various WeChat groups for professional readers focusing on industrial automation technology.
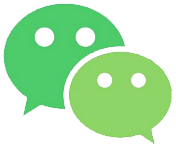
TSN Network Group
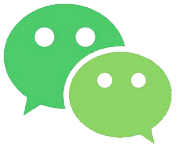
PLC Group
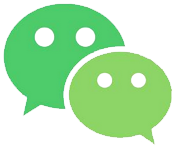
DCS Group
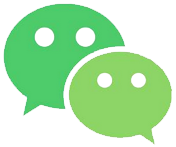
Machine Vision Group
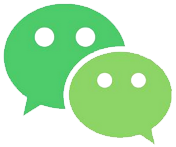
Robotics Group
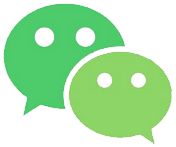
Industrial Software Group
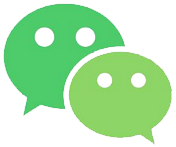
Human-Machine Interface Group
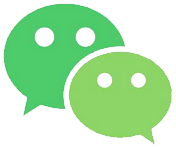
Motion Control Group
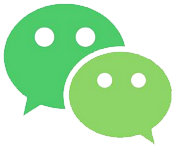
Sensor Group
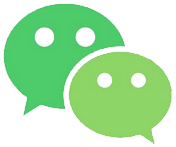
Industrial Safety Group
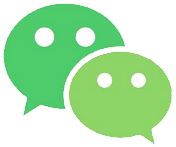
Instrumentation Group
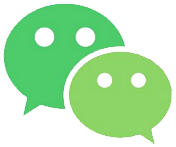
Industrial AI Group
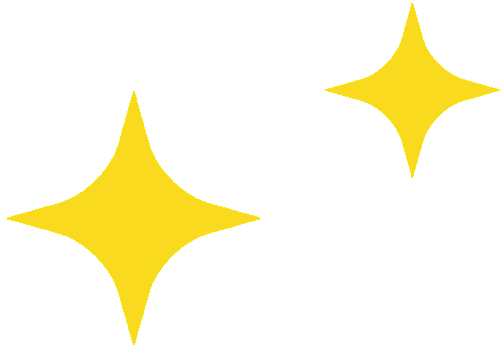
Scan the QR code on the right, to send “Name + Technical Interest + City” to add the editor’s WeChat (cec_editor). After verification, you will be invited to join the corresponding technical group.

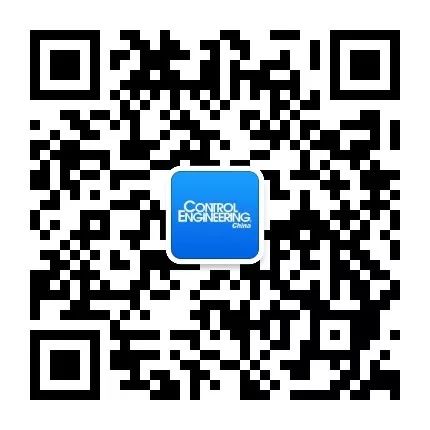