


EtherCAT G, as an extension of EtherCAT technology, elevates EtherCAT performance to a whole new level, achieving Gigabit (Gbit/s) Ethernet speeds, thus supporting high data-intensive applications.
The latest technological extension is not only fully compatible with the globally accepted 100 Megabit EtherCAT (100 Mbit/s EtherCAT) standard, but also retains the same ease of use. Additionally, the branching controller mode of EtherCAT G enables efficient operation of multiple subnet segments in parallel.
EtherCAT G supports standard Gigabit Ethernet transmission; while EtherCAT G10, as a proof-of-concept technology study, achieves even faster transmission rates of up to 10 Gigabits (10 Gbit/s). The significant speed improvement over the standard 100 Megabit allows for increased data throughput. Although still limited by device transmission latency, the newly introduced branching controller mode can enhance performance by 2-7 times (depending on specific applications).
Mr. Hans Beckhoff, President of Beckhoff Automation, stated: “EtherCAT G and G10 elevate performance to a new height, helping our customers build the best and highest-performing machines globally! The release of EtherCAT G and G10 does not mean replacing the already successful 100 Megabit EtherCAT standard; the new performance extension remains consistent.”
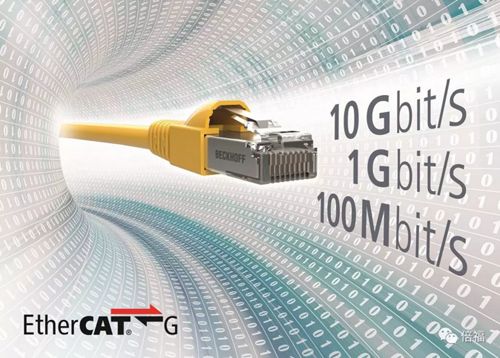
EtherCAT G elevates EtherCAT technology performance to a new level while being fully compatible with standard EtherCAT technology and maintaining the same ease of use.
EtherCAT G features the same outstanding performance and ease of use as EtherCAT and retains all functionalities of EtherCAT, achieving higher transmission rates without the need to modify protocols or EtherCAT master software. EtherCAT G is completely compatible with the widely adopted EtherCAT standard and exhibits the same proven performance characteristics as EtherCAT, including built-in diagnostic capabilities, high-precision synchronization, and the critical message processing mechanism “Ethernet on the fly,” while also complying with IEEE 802.3 Ethernet standards.
The high performance of standard EtherCAT is still more than sufficient to meet current mainstream application demands. EtherCAT G is developed for large-scale applications and broader use of high data-intensive devices, such as machine vision cameras, complex motion control systems, and measurement testing equipment that requires high sampling rates.
EtherCAT and EtherCAT G can connect to the same heterogeneous network, meaning that EtherCAT G slaves can operate within a 100 Megabit EtherCAT network, and vice versa. In both cases, EtherCAT G devices will operate at 100 Megabit speeds. Utilizing the new EtherCAT G branching controller mode, the Gigabit network can be configured to run parallel 100 Megabit subnet segments through transmission rate conversion. For example, the newly released EtherCAT G coupler EK1400 can create a branch that reduces Gigabit speeds to 100 Megabit, allowing various standard EtherCAT I/O modules to operate within the EtherCAT G network. The functionality of the EK1400 branching controller does not affect the EtherCAT G backbone network.
Another advantage of the EtherCAT G branching controller system is that it can minimize latency. The new CU14xx series branching controllers are specifically designed to connect EtherCAT and EtherCAT G subnet segments and support parallel operation. This setup can significantly reduce signal latency, thereby shortening communication and cycle times, as messages returning from a designated subnet segment are transmitted directly from the branching controller to the master station at a higher Gigabit transmission rate, independent of other subnet segments.
Beckhoff Automation GmbH is headquartered in Verl, Germany. With branches around the world and global partners, the company operates in over 70 countries and regions.
Beckhoff has always focused on PC-based automation technology as its development philosophy. The industrial PCs, fieldbus modules, drive products, and TwinCAT automation software produced form a complete, compatible control system that provides open automation systems and complete solutions for various industrial control fields. For over 30 years, Beckhoff components and system solutions have been widely applied globally. In March 2001, Beckhoff established its first representative office in Beijing, China. In May 2007, Beckhoff established a wholly-owned company in Shanghai and moved its China headquarters to Shanghai. Since then, the company has entered a rapid development phase, establishing offices in 25 major cities across the country, including Beijing, Guangzhou, Chengdu, Wuhan, and Nanjing. With the continuous introduction of cost-effective new products and technologies into the Chinese market, Beckhoff’s commitment to breaking traditional control models and promoting PC control technology has gained acceptance from an increasing number of Chinese users.
▼
The CMCD Award for Smart Manufacturing and Motion Control Industry is now open for applications! Stay tuned!
The Nine Major Issues with Servo Motors That Cannot Be Ignored, and How to Address Them
Common Issues with Servo Motors You May Have Encountered
Reflections on Huawei’s Situation: The Path of Localization, There Is No Other Choice!
A Comprehensive Overview of Domestic Industrial Robot Core Component Manufacturers