
Live Broadcast Preview
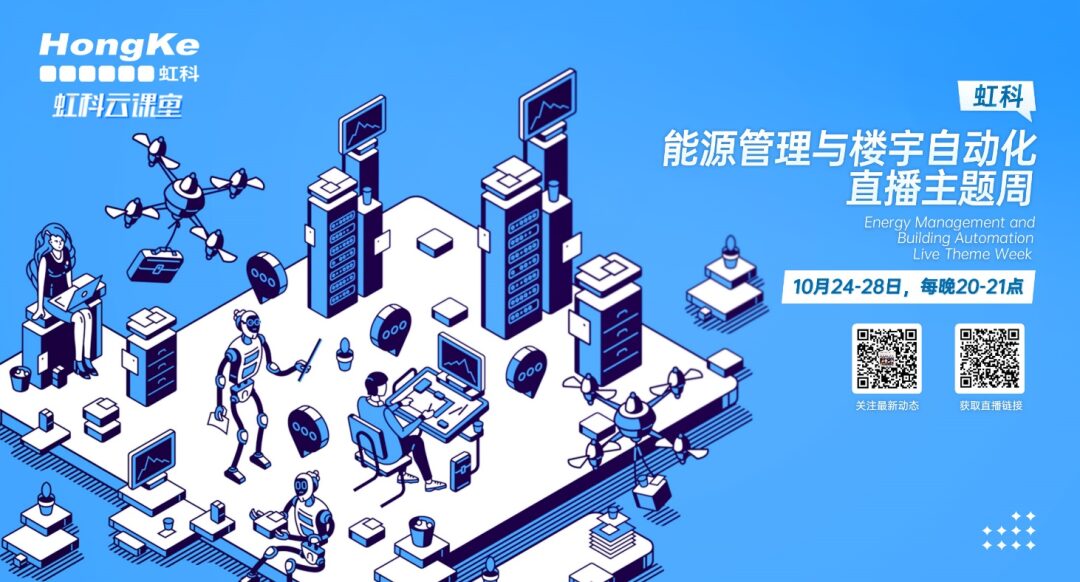
Do you want to learn how relays play a role in improving energy efficiency? Do you want to learn about HSR/PRP/PTP technologies that can be used for building smart grids? Do you want to learn the basics of building automation protocols such as KNX and BACnet? To accelerate the construction of an intelligent future for automated networks connecting all things, achieving multi-system coordination and efficient energy management, Hongke will hold a series of free live courses from October 24 to October 28 on the theme of “Energy Management and Building Automation,” packed with valuable content that you won’t want to miss! Scan the QR code above to book your spot for the live broadcast~
EtherCAT is an ideal choice for distributed high-performance I/O systems. Is there a market-validated EtherCAT remote I/O module available domestically? Today, we will introduce a module integrated on a PCB that allows you to easily achieve high-speed data acquisition.
EtherCAT is a high-performance, low-cost, easy-to-use, topologically flexible, and open-source deterministic industrial Ethernet technology. This technology overcomes the system limitations of other Ethernet solutions: with this technology, there is no need to receive Ethernet packets, decode them, and then copy process data to each device. Its key working principle lies in how its nodes process Ethernet data frames: during the downstream transmission of data frames, each node reads the data addressed to it and writes its data into the data frame. This transmission method improves bandwidth utilization, allowing the entire system’s data refresh to typically be accomplished with a single data frame per cycle, while the network does not require switches or hubs, ensuring real-time operation and avoiding delays.
The operational mechanism of EtherCAT gives it greater advantages over other standard Ethernet: fast response times, minimal data requirements per device, and low implementation costs. Furthermore, EtherCAT supports almost all topologies, making it possible to have pure bus or linear topologies with hundreds or thousands of nodes. Therefore, EtherCAT has become the ideal choice for high-performance distributed I/O systems. EtherCAT networks can connect up to 65,535 devices, with almost no limitations on network capacity, allowing modular I/O devices to be designed such that each I/O chip is an independent EtherCAT slave, and program data exchange with a thousand distributed digital inputs/outputs can be completed in just 30 microseconds.
EtherCAT Remote I/O Module Integrated on PCB
01
Overview of Hongke HK-MXB I/O Module
The Hongke HK-MXB series is an EtherCAT industrial Ethernet bus interface, integrating digital input and output in a hybrid I/O module, providing an ideal channel for higher-level EtherCAT master controllers. The HK-MXB uses industrial 24V NPN/PNP type digital logic input signals and provides current limiting and electrical isolation for captured signals as safety protection.
At the same time, the HK-MXB can convert instruction signals sent from the master controller into NPN/PNP type industrial 24V digital logic signal outputs, with a maximum driving current of 0.5A/CH, suitable for driving relays, indicator lights, and digital logic signals.
Both the input and output channels of the HK-MXB, the EtherCAT communication interface, and the power interface are equipped with corresponding LED indicators for quick observation and diagnosis of signal and instruction status.
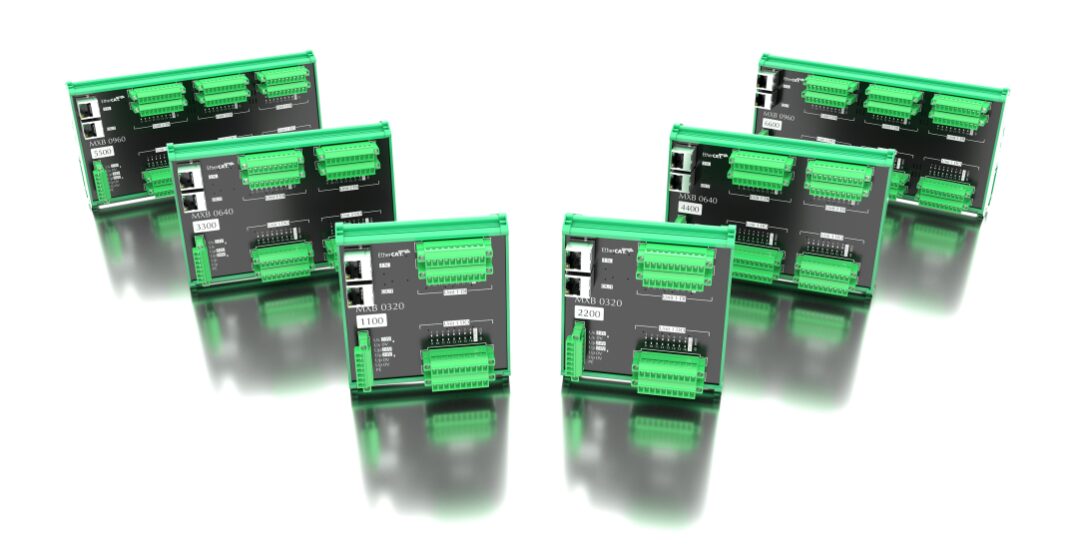
02
Main Features:
Key features of the Hongke HK-MXB I/O module:
1) Supports 16, 32, or 48 channels of 24V NPN/PNP type digital inputs
2) Supports 16, 32, or 48 channels of 24V NPN/PNP type digital outputs
3) Input current limiting protection
4) Output current limiting and short-circuit protection
5) Bus communication fault indicator
6) Pluggable terminal blocks
7) DIN35 rail mounting
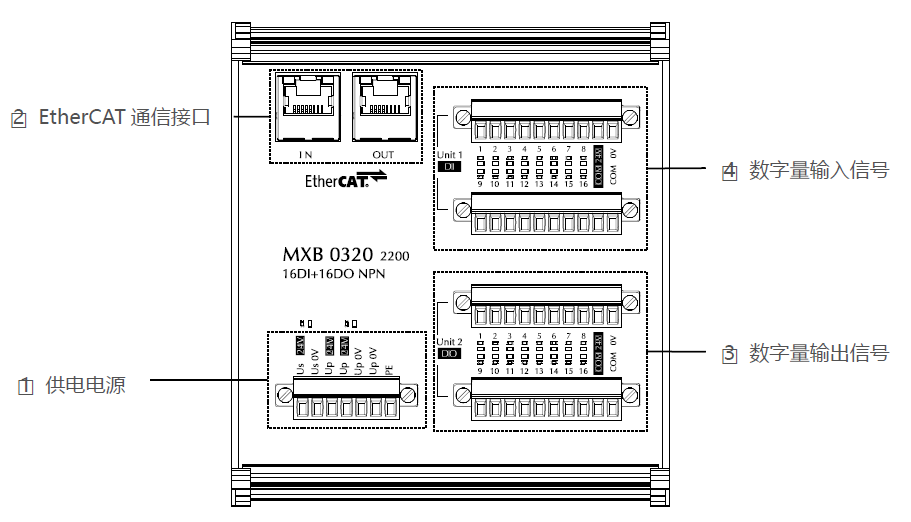
The Hongke HK-MXB I/O module is based on the concept of PCB wiring, integrating I/O signal channels, RJ45 communication ports, power signal terminals, etc., related to EtherCAT remote I/O on the PCB, eliminating the need for extra wiring boards and couplers, facilitating on-site installation and wiring.
HK-MXB I/O Module On-Site Implementation
01
Device Installation
The module supports DIN35 rail installation, making it relatively easy to place in electrical cabinets.
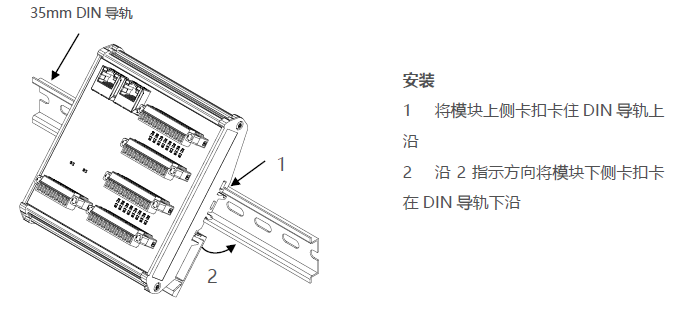
02
Connecting Power Supply
The module’s power supply design consists of Us and Up, corresponding to the communication system and the field device side, respectively. Us is used for the module’s communication system power supply, while Up is used for the field device power supply. During use, users can employ two isolated power converters to supply power to Us and Up respectively. This design ensures that when the field input/output signal circuit of the MXB series module experiences anomalies (such as power issues, load short circuits, or surges), the communication circuit remains unaffected, preventing interference signals from the field from affecting the communication circuit.
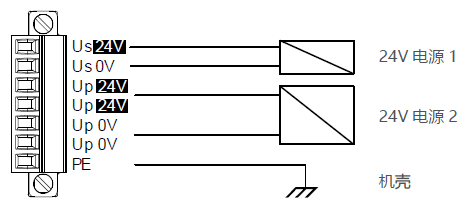
03
Bus Topology
The module integrates the RJ45 communication port related to EtherCAT remote I/O onto the PCB, allowing for direct connection to other devices using CAT5e cables in field applications.
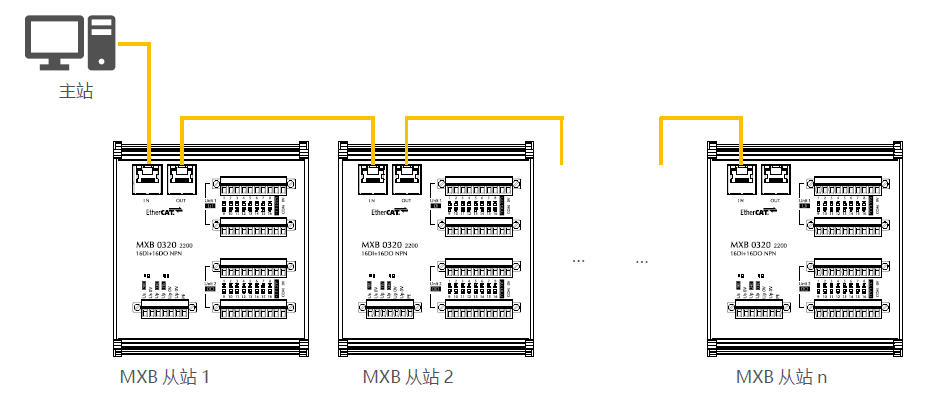
1) When the module is the first slave device connected to the master station, it must use the IN port on the module to connect to the master station.
2) When the module is a middle slave device, it must use the IN port to connect to the previous slave device and the OUT port to connect to the next slave device.
3) When the module is the last slave device, it must use the IN port to connect to the previous slave device and leave the OUT port empty.
04
Field Applications
1) When using for the first time, the slave XML configuration file needs to be imported into the master station; please refer to the respective manufacturer’s master station user manual for specific procedures.
2) Connect the power supply and use a shielded CAT5e Ethernet cable to connect the module to the master station.
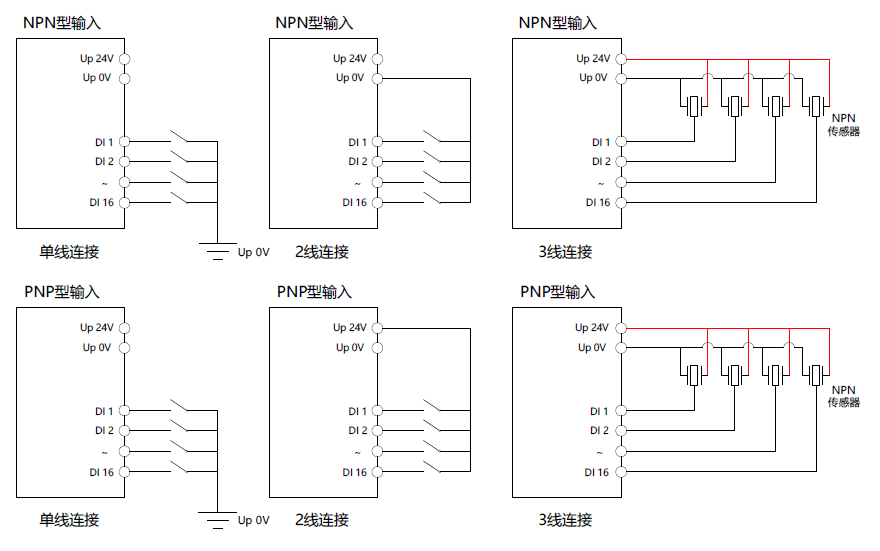
3) Wiring for DI digital signal input.
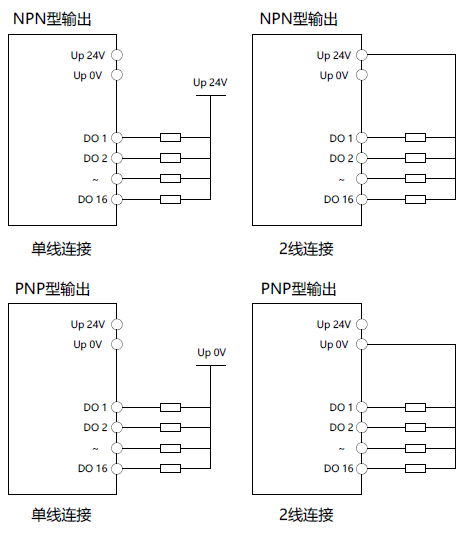
4) Wiring for DO digital signal output.
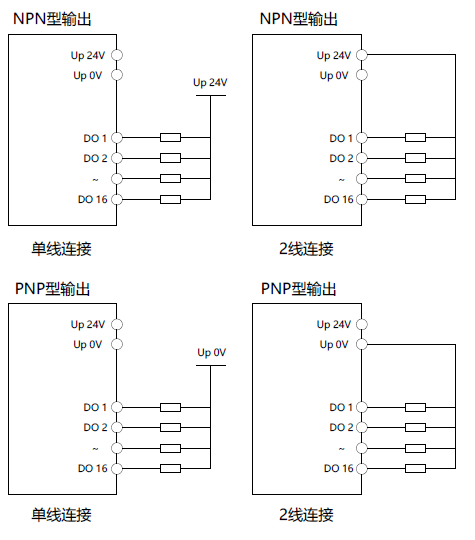
5) Power on and scan the slave through the master station.
6) The master station can operate 16 DI and DO signals respectively through PDO operations.
7) Observe the input and output indicator light statuses on the module to confirm signal continuity.
Typical Applications
01
Typical Applications
The HK-MXB I/O module can associate I/O signals with some special functions of robotic systems, used for controlling robots and monitoring the status of robotic systems. At the same time, the MXB module can be installed in remote rack cabinets, placing remote I/O sites in suitable locations. Signals from an area can all be routed to this site, which then communicates with the main control PLC.
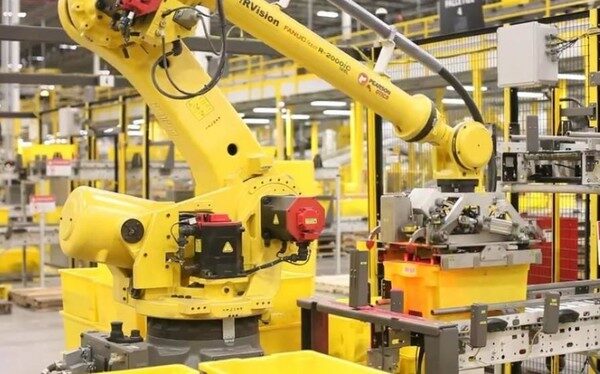
02
Semi-Conductor Production
Due to its high communication speed, good communication quality, and flexible network topology, EtherCAT can be applied in high safety level hazardous environments. In semiconductor manufacturing, there are often many valve islands, actuators, sensors, and pneumatic or electric devices, and the HK-MXB I/O module can achieve signal acquisition, control, or remote maintenance of the corresponding signals.
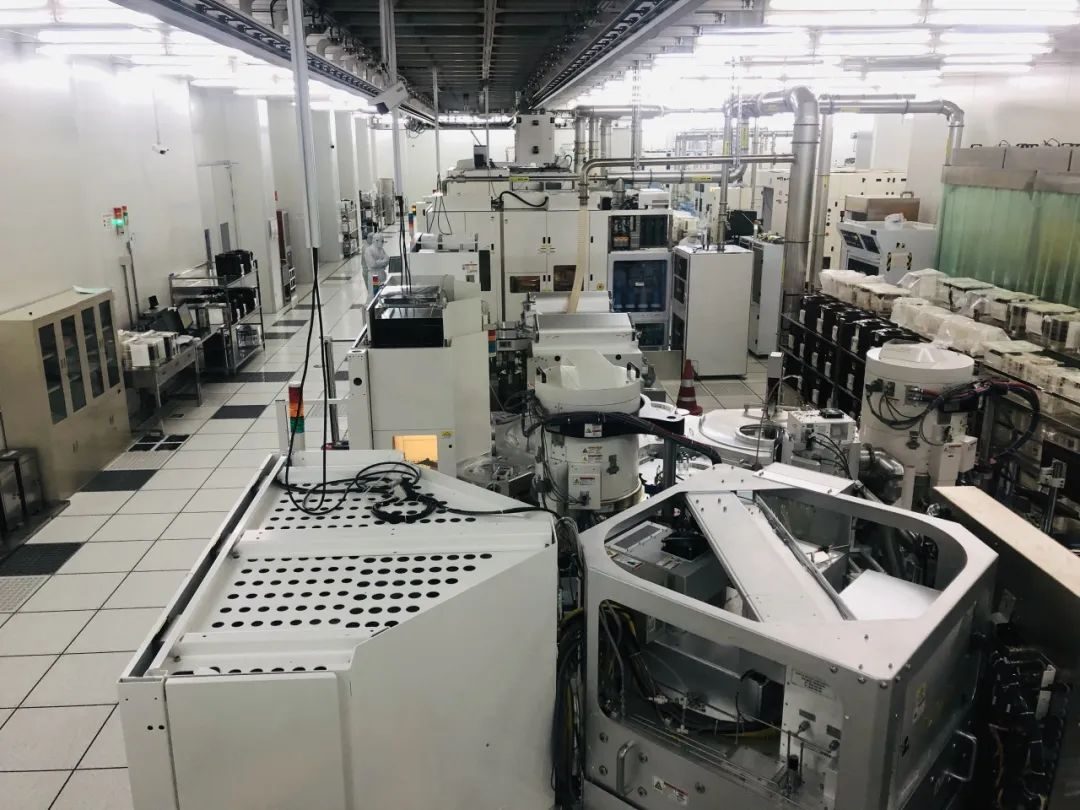
03
Photovoltaics and Wind Power
The photovoltaic industry is a rising sun industry based on semiconductor technology and the demand for new energy, and it is also a high ground for future global advanced industry competition. In photovoltaic tracking control, the control center receives various data uploaded from multiple photovoltaic tracking devices and sends tracking control signals based on the results of data processing. The HK-MXB I/O module can undertake the functions of detecting position signals from sensors within the equipment and driving relays and other related devices to upload data to the control center and receive instructions.
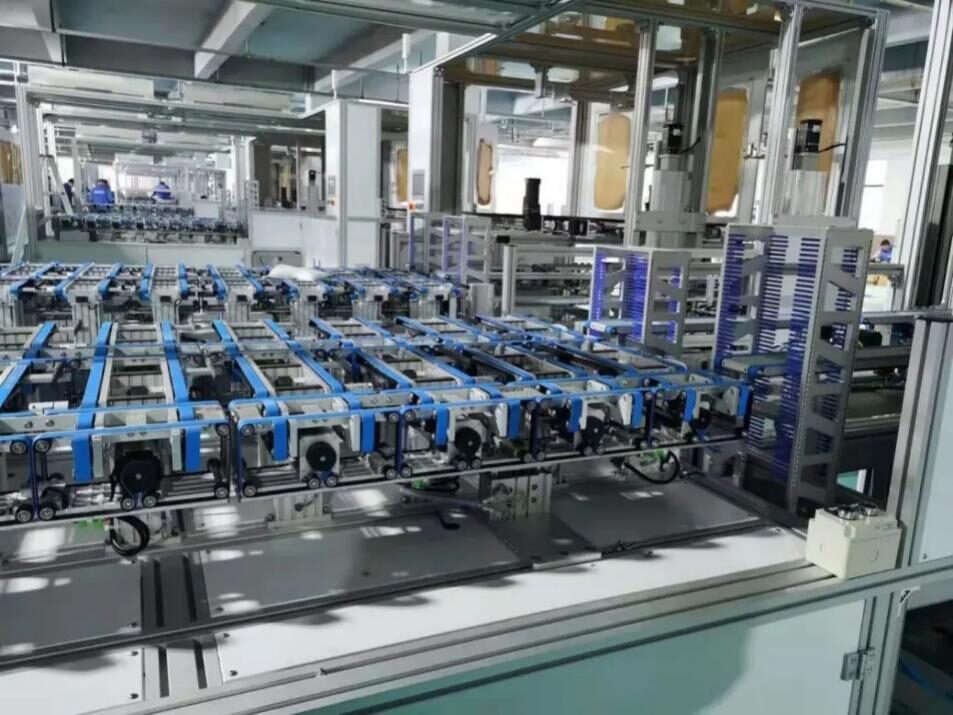
Summary
With the advent of the Industrial 4.0 era, the demand for improving factory production efficiency is increasing. The application of data networks in factories is becoming more widespread, and the number of devices connected to the network, such as manufacturing equipment, is also rapidly increasing. EtherCAT, which provides efficient data conversion, makes high-speed and high-precision control possible, making it particularly suitable for fields requiring high-speed and high-precision control such as industrial robots, semiconductor production, CNC machine tools, photovoltaics, wind power, and process control.
Hongke Intelligent Automation Division
Hongke is a high-tech company with over 15 years of experience in the field of industrial automation, particularly in industrial bus communication. The Hongke Intelligent Automation Division has deep collaborations with world-renowned experts in industrial automation, energy management, and building automation in Europe and the United States, providing top-level communication protocol hardware and software solutions in the industry. The types of communication technologies involved include industrial automation communication protocols such as CAN, CANopen, EtherCAT, Profinet, Ethernet/IP, IO-Link, OPC UA, MQTT, TSN, and energy management and building automation communication protocols such as ASCII, BACnet, KNX, Modbus, etc. The solutions include code, chips/modules, boards, gateways, I/O, industrial computers, relays, testing solutions, training, and development services. Therefore, Hongke is one of the few suppliers in China with extensive technical experience in the OT field.
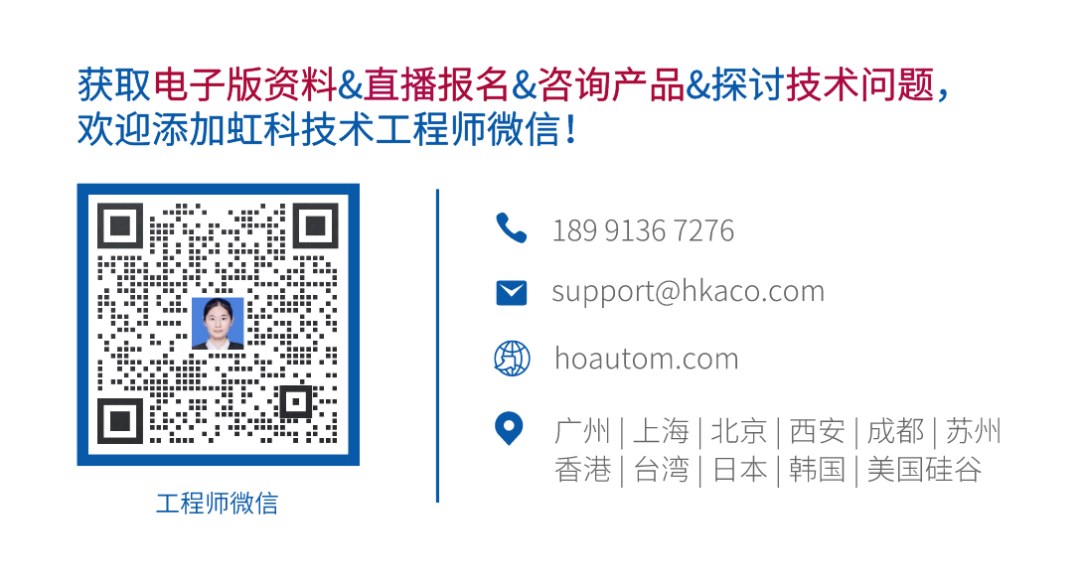
– END –