Abstract
In the wave of bus-type alternatives, major automation manufacturers have launched their own bus-type motion control products. Among the various types of bus communications, EtherCAT stands out remarkably. According to MIR Rui Industry statistics, as of 2021, the market size of bus-type motion controllers in China exceeded 6 billion, accounting for more than 70% of the overall motion controller market. Among them, the market size of EtherCAT bus-type motion controllers exceeded 4 billion, accounting for more than 60% of the bus-type motion controller market. It can be said that EtherCAT has taken the C position in automation communication protocols.
01
“Craftsmanship Level” Products
At the 2003 Hannover Messe, a booth by a company renowned for motion controllers attracted a crowd, showcasing a brand new industrial communication protocol.
Almost all attendees related to the automation industry visited this booth and were astonished. Some directly asserted that this was a forward-looking high-end technology, a new generation product of cutting-edge control concepts.
This company is Beckhoff Automation GmbH, and this forward-looking high-end technology is called EtherCAT (Ethernet for Control Automation Technology).
The subsequent story unfolded as those who first encountered EtherCAT had anticipated. This industrial communication protocol, which can be described as “revolutionary,” has been widely used in applications such as packaging machines, all-steel plants, robots, cutting systems, wind tunnels, and wind energy systems due to its diversity of applications, openness, and high efficiency.
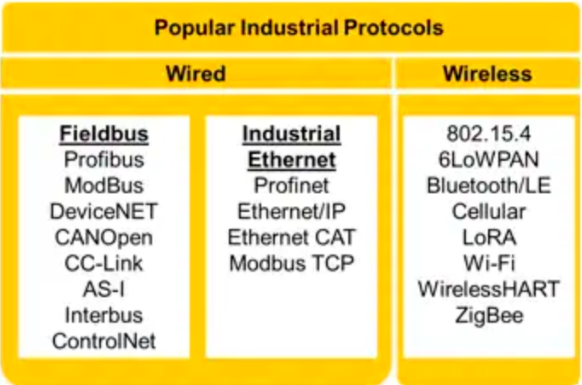
(Illustration: Some mainstream industrial communication protocols)
Even 10 years after its inception, the communication speed of EtherCAT still surpasses the fastest CPU operation speed. Moreover, controllers using EtherCAT from 2003 could still be compatible with automation devices in 2013 – in a sense, it has broken Moore’s Law for over a decade (though the application fields vary slightly). This means that a single version of EtherCAT, namely the first version of EtherCAT, is sufficient to support most industrial scenarios today; all subsequent additions are merely extensions rather than modifications, making it a truly “craftsmanship-level” product. Compared to what some companies today call “phenomenal” products, it is on a whole different level.
As a real-time industrial fieldbus communication protocol based on Ethernet development architecture, EtherCAT can be simply described as a row of students sitting upright in a specific class. The teacher hands a test paper (which can be different subjects) with everyone’s names to the first student, who then passes it along from front to back. The first student only takes the test with their name, the second student only takes theirs, and so on. Additionally, the teacher can collect the papers within a certain time frame, grade them, analyze, and then provide feedback to specific students. The teacher, in this case, is the master station, the students are the slave stations, and the test papers are the data content conveyed by the master station.
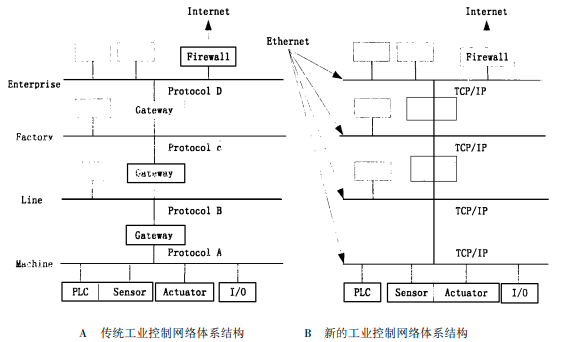
(Illustration: Differences between traditional industrial control architecture and new industrial control architecture)
Thanks to the wave of bus-type replacing pulse-type motion control products, EtherCAT has emerged in the automation market. From a performance perspective, EtherCAT stands out among many bus-type control protocols mainly due to the following three points:
1. EtherCAT communication speed is extremely fast. It processes 1000 distributed I/O signals on 30 axes within 100μs using twisted pair or optical cables, setting a new limit for real-time performance. This high speed makes EtherCAT very suitable for automation, Industrial Internet of Things (IIoT), and other applications requiring real-time optimization.
2. It is a widely adopted open standard. An increasing number of devices are connecting via field buses or wirelessly. Since the data uses the same format as Ethernet, it can be directly connected to Ethernet without the need for specific routers or switches. This means users can efficiently use EtherCAT-IP to select multiple products on the same interface.
3. Its sustainability. Using mature Ethernet cables, the EtherCAT communication protocol can operate continuously under extreme conditions; for instance, EtherCAT terminals can work continuously within a temperature range of -25°C to +60°C (Trinamic’s EtherCAT motion controllers can even meet automotive-grade temperature specifications of -40°C to 125°C).
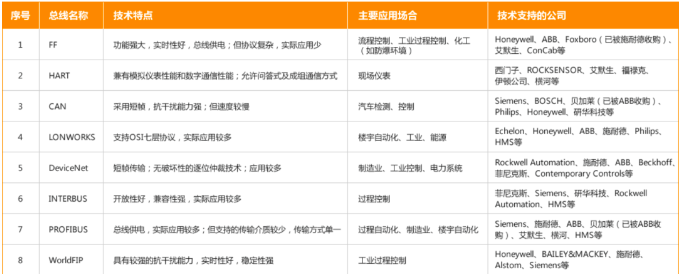
(Illustration: Some bus-type communication protocols)
It is no wonder that in today’s automation market, motion control products equipped with EtherCAT bus communication have a wide range of applications in fields such as semiconductors, photovoltaics, and lithium batteries.
According to MIR Rui Industry statistics, as of 2021, the market size of bus-type motion controllers in China exceeded 6 billion, accounting for more than 70% of the overall motion controller market. Among them, the market size of EtherCAT bus-type motion controllers exceeded 4 billion, accounting for more than 60% of the bus-type motion controller market. It can be said that EtherCAT has taken the C position in motion control communication protocols.
02
The “Sweet Cake” in the Eyes of Foreign and Domestic Capital
In the Chinese automation market, especially in the general AC servo product line, bus-type communication has become a popular trend. Each servo manufacturer has launched its own dedicated bus protocol (Yaskawa Mechatrolink, Panasonic RTEX, Mitsubishi CC-Link, etc.). This wave of bus communication was initiated by European and American manufacturers and further developed by Japanese manufacturers, and there seems to be a historic tacit agreement between foreign and domestic companies in the application of EtherCAT bus communication.
European and American manufacturers, represented by Beckhoff, have the largest market share of PC-based motion controllers in China, and naturally, their choice of communication protocol is primarily their own EtherCAT. Moreover, Beckhoff has been actively promoting the EtherCAT communication protocol in China, and with Beckhoff’s vigorous promotion, EtherCAT has been accepted by most domestic PC-based motion controller manufacturers.
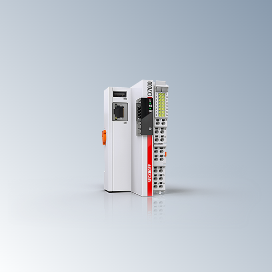
(Illustration: CX7000 | Embedded Controller Series)
Possibly out of a competitive mentality towards their fellow German company Beckhoff, the electrical giant Siemens has also launched an industrial Ethernet-based fieldbus system called Profinet. The difference between Profinet and EtherCAT is that EtherCAT was initially researched by Beckhoff, and then a union was formed in Europe to promote this technology. After this technology was introduced, it controlled the market with underlying chips and licensing, thereby enriching the entire EtherCAT ecosystem. In contrast, Profinet is an ecosystem established by Siemens. Despite Siemens’ continuous efforts to promote its Profinet, trying to “break out,” the relationship between the two is somewhat akin to that between the Android system and the Apple system in the smartphone industry.
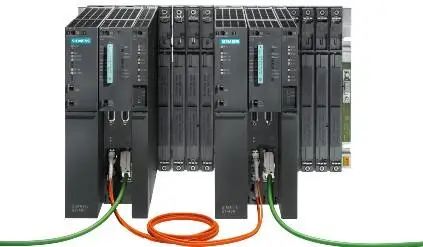
(Illustration: Siemens S7-400H V6 version controller supporting PROFINET)
Japanese manufacturer Omron began promoting EtherCAT bus servos in 2012, primarily targeting high-end markets such as lithium batteries and packaging (traditional pulse servos cannot meet the high precision positioning control required, and low-end markets do not need the high performance of bus servos). Especially in the lithium battery industry, Omron’s presence is particularly strong, with its PLC products leading the market share in the lithium battery industry in 2021. Generally speaking, from the perspective of uniformity and compatibility in a lithium battery production line, the EtherCAT bus protocol is favored. Currently, most domestic servo manufacturers’ motion control PLC products also predominantly choose EtherCAT as their main bus protocol.
In the future, lithium battery equipment will develop towards multi-process integrated machines and multi-station devices, and the number of servo axes equipped on devices will also increase, making bus-type servo products an inevitable trend, further expanding the market share of bus-type servos in the lithium battery equipment industry. At the same time, with the development of domestic servos, EtherCAT protocol servo products will also see further growth.
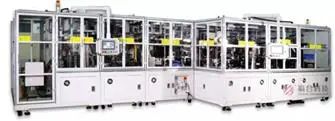
(Illustration: Lithium battery equipment stacking integrated machine, using 90–210 general servos)
Another Japanese player, Panasonic, also believes that bus communication is the development trend of servo products, and its market share will continue to grow. As an old manufacturer, Panasonic also has its own dedicated bus protocol RTEX.
Although its own RTEX is also appealing, the characteristics of EtherCAT, such as fast communication speed, easy wiring, and no interference, make equipment processing more efficient and increase equipment profits, leading to high customer acceptance. Generally, customers request servo products with EtherCAT communication, using Beckhoff IPC + soft PLC or Omron’s PLC in combination. Even in 2019, the price of Panasonic EtherCAT bus servos was 8-10% higher than traditional servos, yet this future trend has not changed.
In recent years, Yaskawa Electric has felt somewhat conflicted compared to other Japanese manufacturers. On one hand, it recognizes the development of bus communication and actively promotes its Mechatrolink products within the bus (MetroLink-III is a motion control fieldbus protocol developed by Yaskawa based on the EtherCAT physical layer, which has now evolved to MetroLink-4, and will be applied on Σ-10 in the future); on the other hand, due to many upper-level controls in industries such as lithium batteries and electronics using the EtherCAT protocol, Yaskawa Electric has many products supporting the EtherCAT bus, and benefitting from the increased demand in the lithium battery and electronics markets, Yaskawa Electric’s sales of EtherCAT bus products saw a slight rise in 2021.
This conflicted mentality is influenced by Yaskawa Electric’s own sales strategy (promoting its bus protocol), leading to a general scarcity of EtherCAT products. A few years ago, Yaskawa Electric mainly promoted the M2 and M3 buses in the China region, without applying the EtherCAT protocol, while many domestic CNC systems and servo motor manufacturers had already installed Yaskawa Electric’s M2 and M3 bus products.
Among domestic manufacturers, Inovance’s servo products also frequently use EtherCAT, especially in the lithium battery industry, where the application ratio of EtherCAT accounts for a significant proportion. This is not only because the lithium battery industry itself takes EtherCAT as a mainstream communication protocol but also relates to Inovance’s competition with Omron in the lithium battery sector. In the industry, Inovance’s servo products are paired with Omron’s PLCs (Omron’s motion control PLC uses EtherCAT as its communication protocol), and this solution has been established as an industry benchmark, directly determining the selection of communication protocols for servos.
Another domestic manufacturer, Hechuan, also primarily uses EtherCAT for its bus communication protocol, and in the robotics industry, some CANopen bus protocols are also used, while X6 and Y7 may involve Siemens’ Profinet or Yaskawa Electric’s Mechatrolink communication protocols.
From the perspective of servo product development, Hechuan’s main servo series X3E predominantly uses EtherCAT as its communication protocol. Additionally, the originally planned communication protocol for the newly developed X6 and Y7 products was that X6 would focus on EtherCAT supporting Profinet high-performance products, while Y7 would focus on EtherCAT supporting Mechatrolink protocol products. However, due to the widespread chip shortage affecting the entire industry, production and supply have faced certain difficulties; therefore, Hechuan has accelerated the research and testing of the Y7 product’s EtherCAT communication mode and began mass sales in April 2022.
In the future, as the applicability of EtherCAT bus continues to expand, the sales proportion of EtherCAT bus-type products will gradually increase, and Hechuan will also strengthen its promotion of EtherCAT bus-type products.
*Some manufacturers, such as Leadshine, Guangzhou CNC, Advantech, etc., also have many motion control products using the EtherCAT communication protocol, but due to space limitations, this article will not elaborate.
03
How EtherCAT Solidified Its C Position
In today’s automation market, especially in the servo product line, bus-type protocols will gradually replace pulse-type protocols. In some downstream application industries of servos, the EtherCAT protocol, which combines the characteristics of both “bus type” and “Ethernet,” is gradually occupying the mainstream market position.
In 2021, the market performance of bus-type products in the electronic manufacturing equipment industry accounted for over half of the market share, among which bus-type servo products were mainly based on the EtherCAT protocol. Foreign companies like Panasonic and domestic companies like Inovance and Hechuan tend to provide EtherCAT servo products when offering bus products in the electronic manufacturing equipment industry, primarily because many electronic manufacturing equipment products are non-standard customized products developed based on customer needs, especially in vision-related applications, with many domestic PC-based manufacturers like Leadshine promoting EtherCAT communication products, making EtherCAT servos more compatible.
In recent years, the emerging photovoltaic market’s bus-type products have also captured a significant share of the market, with bus-type servo products largely based on the EtherCAT protocol. Companies like Inovance and Hechuan tend to provide EtherCAT servo products in the photovoltaic industry, primarily because the applications in the photovoltaic industry often use Omron or Beckhoff PLC products, making the use of EtherCAT servos more compatible with them.
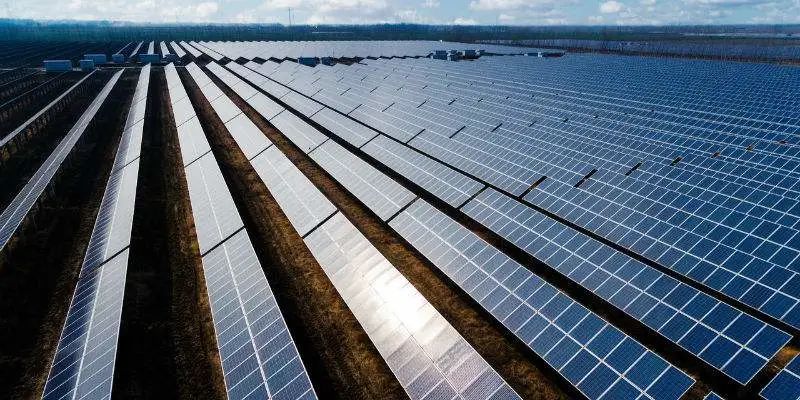
In 2021, the market share of bus-type products in the lithium battery manufacturing equipment market accounted for nearly all of the market. This is partly related to the characteristics of lithium battery industry equipment and the gradual rise of domestic servo products. We have analyzed this in detail when discussing the application of EtherCAT communication protocol by Omron and Inovance, so we will not elaborate further here.
In 2021, the market share of bus-type products in the semiconductor market exceeded half, with the EtherCAT protocol being the primary one. The current industry situation is as follows:
-
First, it is related to the market share of suppliers. In 2021, Panasonic’s servo products held a significant share in the semiconductor equipment industry, and Panasonic’s servo products mainly support EtherCAT communication;
-
Second, as the EtherCAT communication protocol is supported by the International Semiconductor Industry Association (SEMI), it possesses better openness, facilitating communication between devices from different manufacturers;
-
Third, due to the high precision control requirements in the semiconductor industry, the application of PC-based systems in semiconductor equipment is gradually increasing, replacing some PLC applications, thus favoring the more open EtherCAT protocol in terms of communication protocols.
04
EtherCAT – Playing the Ecosystem
Overall, in recent years, the gradual solidification of EtherCAT’s position as the C protocol in communication protocols in the automation industry is a trend driven by its superior performance. EtherCAT originated from traditional industrial power Germany, gradually establishing a foothold in the industrial automation field by uniting the entire Europe to cultivate an ecosystem.
Whether it is Beckhoff’s EtherCAT or Siemens’ Profinet, they have gained extensive application in the entire industrial automation market due to a common logic: Siemens occupies the leading position in the overall PLC market in China, while Beckhoff is also at the forefront of the PC-based motion controller market in China. Being the leader in controllers means that you grasp the upper-level products in the automation product line, based on which you can often define many standards and rules in the automation field, such as the PROFIBUS standard established by Siemens and the MindSphere World global user organization, the former helping to establish a “circle of friends” and the latter creating the optimal ecosystem.
As the saying goes, “whoever controls the standards, controls the world.” As ecosystem builders, Beckhoff, Siemens, and others stand at the top of the “ecological chain,” and the products used by downstream equipment manufacturers almost all adhere to their standards. For instance, Beckhoff recognizes and uses EtherCAT, and with vigorous promotion, downstream manufacturers (especially those using PC-based motion controller products) must use EtherCAT for compatibility. Consequently, automation products equipped with EtherCAT communication protocols can smoothly enter the vast market of downstream supply chains.
Similarly, Japanese manufacturer Omron is also in the same situation in the lithium battery industry. Omron’s motion control PLC is undoubtedly the ace product in the lithium battery industry, and most manufacturers use Omron’s PLC products, which utilize the EtherCAT ecosystem. Thus, this chain reaction influences all automation manufacturers competing in the lithium battery industry, showcasing the power of the ecosystem and the most crucial factor for the longevity of the EtherCAT communication protocol.
In the future, in the Chinese automation market, as bus-type servos continue to develop, the market share of bus-type servos in various downstream industries will further expand. Moreover, as the market share of domestic servos gradually increases, the upper-level control communication protocols for domestic servos will mainly continue to use EtherCAT, thus further developing the market share of EtherCAT protocol servo products.
*The servo products mentioned in this article refer to general AC servos.
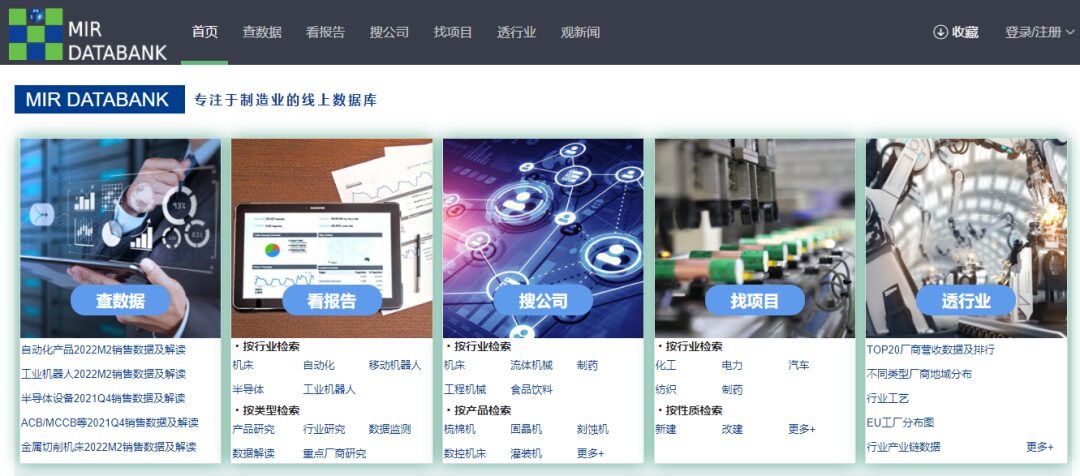