Report Publisher: Galaxy Securities
LCD panels are driven by policies, technology, and capital.
Reviewing the development path of display technology and the rise and fall of LCD industries in various countries, the LCD panel industry is capital-intensive, labor-intensive, and continuously innovates driven by market demand. The development of panel companies requires the joint promotion of policy support, technological development, and capital investment.
For the complete PPT report, please reply with the keyword “21507” in the WeChat public account of Lei Feng Network.
LCD panels will remain the mainstream display technology for the next 5-10 years.
The main driving force behind emerging technologies is the growing consumer demand, while the core of commercializing emerging technologies remains price. With the support of technologies such as Mini-LED backlighting, LCD panels will meet consumers’ new demands for high-definition and large screens. Considering the short-term issues of yield and cost for emerging technologies, despite competition from emerging technologies like OLED, it is expected that LCD panels will still be the mainstream technology in the large-size display field for the next 5-10 years.
The cyclical weakness of LCD panels will significantly enhance manufacturers’ profitability.
Due to a two-year construction period and a one-year capacity ramp-up period, LCD panels have shown strong cyclicality in the past. As the industry enters the mature late stage, manufacturers’ willingness to build new capacities has significantly decreased. According to our supply-demand model forecast, the compound annual growth rate of LCD capacity over the next three years is 3.1%; the compound annual growth rate of LCD demand is about 6.5%, improving the industry supply-demand structure, reducing cyclicality, and maintaining panel prices within a reasonable range, which will significantly enhance the profitability of LCD manufacturers.
The LCD panel industry has entered a great era in China, with the “dual giants” of panels taking off.
The display panel industry is a key industry supported by the state, with multiple policies issued to support the development of China’s panel industry. China has completed a “leapfrog” development of LCD panel manufacturing in nearly 10 years, breaking through foreign technology barriers, enhancing core technology mastery, and completing patent layout. The LCD industry chain is shifting to China, and it is expected that the market share in mainland China will exceed 70% in the next 3-5 years.
1
LCD panels will remain the mainstream display technology for the next 5-10 years.
It is the mainstream in the display field.
The replacement of mainstream display technology from CRT to LCD has taken approximately 50 years. Reviewing the last round of display technology replacement, the main driving force of emerging technologies is the growing consumer demand, while the core of commercializing emerging technologies remains price. We believe that with the support of technologies like Mini-LED backlighting, LCD panels will meet consumers’ new demands for high-definition and large screens. Considering the short-term issues of yield and cost for emerging technologies, it is expected that LCD panels will still be the mainstream technology in the display field for the next 5-10 years.
(1) Rise: From CRT to LCD technology.
With the development of material technology, display technology has evolved from the initial CRT technology to flat panel display technology (FPD), which has further extended to plasma displays (PDP), liquid crystal displays (LCD), and organic light-emitting diode displays (OLED).
The development of display technology can be divided into three stages. Taking television as an example, the first stage is the CRT era of the 20th century: In 1897, the world’s first CRT was born, displaying images by exciting the phosphor on the screen’s inner surface through an electron beam, achieving the conversion of electrical signals to light output. With the improvement of technology, CRT technology was industrialized in the 1950s, and black-and-white CRT televisions and color CRT televisions became the most important display devices in life. Although CRT production costs were low, due to the limitations of cathode ray tubes, CRTs could generally only achieve sizes up to 34 inches and could not meet the growing demand for larger sizes.
The second stage, the 1990s transitional era: rear projection technology, plasma technology, and LCD technology co-existed. Traditional CRT televisions could not meet consumer demands for larger sizes, and around 1990, manufacturers began to explore various technologies to achieve larger display effects. Rear projection televisions, based on projection and emission principles, installed projectors at the bottom of the chassis, reflecting the signal onto a semi-transparent screen’s back for imaging. Despite having advantages like large size and high brightness at the time, rear projection televisions were gradually eliminated due to their bulky chassis and lamp lifespan issues. Plasma televisions used plasma tubes as light-emitting elements, injecting a mixed gas between two ultra-thin glass plates, and utilizing fluorescent powder to produce images by applying voltage. Although plasma televisions offered high picture clarity, they failed to become the next-generation mainstream due to the unresolved burn-in phenomenon.
The third stage, the 21st century LCD era: Early LCD televisions used CCFL light tubes for internal illumination, but due to the size limitations of the tubes, the thickness of televisions was not ideal. After 2000, with the improvement of liquid crystal technology, LED light-emitting diodes as backlight sources reduced the thickness of LCD televisions. At the same time, LED backboards significantly reduced power consumption, decreasing it by more than 30% compared to traditional LCD televisions. Starting in 2005, the cost of LCD televisions dropped significantly, and with the fierce price war among manufacturers at that time, the prices of LCD televisions plummeted: According to CNN news reports, the price of a 32-inch LCD television rapidly dropped from $1,566 in January 2005 to $580 in 2008, comparable to the price of CRT televisions of the same size. In the same year, the shipment of LCD televisions in China exceeded 50% for the first time, becoming the mainstream technology in the display field.
From the evolution of display technology, it is clear that high-definition, large size, and thinness (portability) have always been the main factors driving consumer demand. The new generation of display technology not only needs to meet the consumer demands of the time, have sufficient performance advantages, and long-term verified stability, but also needs to continuously reduce costs during the industrialization process to achieve competitive pricing in order to replace existing mainstream display technologies.
(2) Challenges: The development and bottlenecks of emerging technologies.
As mentioned above, the demand in the display industry mainly revolves around portability-flexibility, large size, and high definition. Currently, the emerging technologies explored by major manufacturers mainly include OLED and Micro-LED direct display technologies.
Although Micro-LED has high display effects, commercial realization still requires time: Micro-LED is currently a research hotspot in the display industry and one of the most promising display technologies for the future. However, there are still technical difficulties such as massive transfer, packaging testing, full color, and uniformity, and it is still in the R&D stage, with several years to go before commercialization.
OLED technology has gradually achieved commercial production and is now being applied in small-sized fields such as watches and mobile phones. OLED, which stands for Organic Light-Emitting Diode, produces images through self-emission, has low power consumption, high contrast, flexibility, and a relatively simple manufacturing process. Currently, OLED displays mainly feature active matrix AMOLED technology, primarily used in foldable screens on smartphones. Due to depreciation, labor costs, and other expenses, there is still a price gap between AMOLED and LCD mobile phone panels: Research data from Zhiyan Consulting shows that AMOLED needs to achieve a yield of over 80% for its cost to be lower than that of LCD. With the improvement of yield rates, Trendforce expects that the penetration rate of AMOLED in smartphones will rise from 31% in 2019 to 38% in 2021, and it is expected to break 50% by 2025.
Although OLED has begun to be applied in small-sized devices, it is still difficult for OLED to replace LCD screens as the market mainstream in the next few years for three main reasons: First, OLED still faces substantial technical barriers compared to the more mature TFT-LCD. Currently, there is no unified mass production technology for OLED, and continuous optimization is required for devices, equipment, and processes, such as masks and vacuum deposition machines: The various raw materials of OLED sublime into atoms and molecules in a vacuum chamber through low-voltage heating, electron beam bombardment, or laser heating, and then condense onto the substrate through a mask. The higher the precision of the mask, the more uniform the thickness of the layers of materials condensed, and the more accurately the locations of the three color-emitting materials deposited on the same layer. Enlarging the production size greatly increases the difficulty of achieving the required precision, and the high standards for vacuum deposition machines make them still “hard to come by.”
Second, the stability and lifespan of OLED panels are inferior to those of LCD panels. When screens are used at high brightness for extended periods, the self-emitting materials of OLED are sensitive to humidity and oxygen concentration, leading to a much faster degradation rate (half-life) of some sub-pixels compared to TFT-LCD, and the speed of degradation varies among sub-pixels displaying different colors, potentially causing OLEDs to experience black screens, color distortion, or burn-in phenomena during long-term high-intensity use. Although this does not have a significant impact on small-screen consumer terminals such as mobile phones, OLED panels still require technological updates for display applications in large-sized devices, which cannot be achieved in the short term.
Third, OLED lacks a cost advantage compared to LCD. According to IHS Markit data, the mainstream panel sizes in the market are 49-60 inches. Taking a 55-inch ultra-high-definition OLED as an example, the manufacturing cost of an OLED panel with only a 60% yield is about 2.5 times that of the same size TFT-LCD. In the short term, due to the high technical barriers in the two key steps of sublimation purification and vacuum distillation, OLED cannot quickly improve its yield. For large-sized OLED panels, even if the yield reaches over 90%, the manufacturing cost is still about 1.8 times that of the same size TFT-LCD. Considering that depreciation is also an important cost factor, even if the OLED factory’s depreciation is completed, the cost difference at 60% yield remains 1.7 times, narrowing to 1.3 times at 90% yield.
Although OLED has a trend of capacity expansion in small and medium-sized screens and has performance advantages, in the large-sized field, compared to TFT-LCD, OLED still faces technical and capacity limitations in the next 3-5 years. The large-scale investments in this technology by Samsung and LGD will result in their combined shipments not exceeding 10% of global TV panel demand, still significantly lagging behind TFT-LCD shipments.
(3) New opportunities: Mini-LED backlight technology brings growth opportunities for LCD.
Compared to OLED technology, LCD technology has obvious advantages in terms of cost and lifespan; in color gamut, resolution, and power consumption, the differences are minimal, while LCD is at a disadvantage in contrast and motion blur. Although OLED’s excellent picture quality is widely recognized as the new development direction for the display industry, the stability of OLED materials and packaging technologies still need improvement. Compared to the mature traditional backlight source LCD, there is still room for further cost reduction.
The emergence of Mini-LED has changed the passive situation of LCD. The addition of Mini-LED backlight technology has significantly improved the performance of LCDs, allowing them to directly compete with OLED in various performance aspects of non-flexible displays: Mini-LED possesses local dimming technology, enabling high dynamic contrast and wide color gamut display through dynamic adjustment of the overall picture. Through special packaging structures and processes, it can increase light-emitting angles, reduce halo effects, and achieve near-zero OD design with uniform self-mixing light effects, resulting in thin and lightweight products that achieve effects comparable to OLED displays.
As an LCD backlight technology, Mini-LED has shown several advantages: high dynamic contrast, high dynamic range, and the number of dimming zones depends on the size, distance, and resolution of the LCD screen.
For television applications, compared to traditional backlight LCDs, LCDs using Mini-LED backlight technology have increased from 50 LEDs to 10,000 to 20,000, with sizes only 100-200 microns. They perform better in dynamic contrast and brightness, while also being lightweight, high-quality, low-power, and energy-saving, greatly enhancing LCD performance. Compared to OLED TVs with equivalent performance, Mini-LED TVs are priced similarly to QLED backlight LCD TVs before their price drop, showing a clear price advantage. According to LEDinside’s forecast, if LCD competes directly with OLED, the product lifecycle is expected to be around 5-10 years. If Mini-LED enhances the performance of LCD products, the product lifecycle is expected to be extended by 1.5 to 2 times.
In 2021, the commercialization of Mini-LED backlight technology accelerated. Since 2019, companies like BOE, TCL, Innolux, and AUO have launched various Mini-LED application prototypes and entered small-scale production, including Mini-LED backlight displays ranging from 27 to 75 inches, televisions, and gaming laptop panels. Meanwhile, Apple, Samsung, and LGD are actively investing in Mini-LED production projects: Apple is expected to launch Mini-LED display iPads and MacBooks in the first or second quarter of 2021, which will drive the application of this technology. From the perspective of the layout of upstream and downstream manufacturers in the industry chain, Mini-LED has successfully met the conditions for technology, capacity, and yield, and is about to enter a fast development phase: According to Arizton’s statistics and forecasts, the global Mini-LED market size was approximately $25 million in 2019, and is expected to exceed $2.3 billion by 2024, with a CAGR of 148%. China has significant advantages in the Mini-LED industry; according to statistics and forecasts from Gaogong LED, the Mini-LED market size in China was 300 million yuan in 2018, and is expected to exceed 2.2 billion yuan by 2020, with a growth rate of over 170%.
We believe that the combination of Mini-LED and LCD can expand the lifecycle of existing liquid crystal display products and strengthen the differentiated bargaining power of panel manufacturers. It is expected that from 2021 onwards, Mini-LED backlight LCD displays will be expected to see large-scale production in mid-to-high-end laptops, gaming monitors, and large-sized televisions.
2
LCD panels are one of the core foundations of the electronic information industry.
LCD, short for Liquid Crystal Display, refers to liquid crystal displays. Generally, the structure of an LCD display consists of two parallel glass substrates combined with polarizing materials, with a liquid crystal box in between, controlling the rotation direction of liquid crystal molecules through voltage to control the polarized light of each pixel point, thereby achieving imaging.
Liquid crystal display technology is mainly applied in televisions, laptops, and mobile phones, featuring right-angle display, low power consumption, compact size, and zero radiation, making it one of the core foundations of the electronic information industry. The market commonly uses TFT-LCD (Thin Film Transistor LCD) technology, which incorporates thin-film transistors to independently control the switches of each liquid crystal molecule, achieving a more stable thin-film transistor liquid crystal display. TFT-LCD display modules mainly consist of liquid crystal panels and backlight modules. In liquid crystal panels, the liquid crystal itself does not emit light; the backlight module provides stable and uniform background light, which is transformed into natural light—polarized light—through polarizers. Thin-film transistors control signal transmission by switching, controlling whether to refract polarized light, and finally, the transmitted light passes through color filters to change colors, achieving the final imaging.
(1) Origin: Liquid crystal display technology originated in the United States.
As early as 1888, “liquid crystals” were discovered by Austrian botanist F. Reinertz, and German physicist D. Leimann named this crystalline molecular structure that exists only in a cloudy state at specific temperatures as liquid crystals. Although liquid crystals were not taken seriously at the time, two American companies developed the era of liquid crystal displays a hundred years later.
In the 1960s, the American company RCA, which led the world in consumer electronics, invented the thin-film transistor, solving the problem of poor contrast caused by unstable voltage, and produced the first basic liquid crystal display: a sandwich-shaped flat display that worked using optical opening and reflected light, sandwiching liquid crystals between two glass plates and applying low-voltage to maintain the opacity of the crystals. In 1968, RCA showcased a liquid crystal board capable of displaying static monochrome images and dynamic scattering liquid crystal displays (DSM-LCD) at a press conference, demonstrating applications such as digital electronic clocks, which attracted significant media attention. Due to the management’s lack of planning for the future development direction of liquid crystals in consumer electronics and focusing on challenges from IBM in the computer field, RCA abandoned further development and application of liquid crystals. In 1971, RCA divested its computer business and completely terminated LCD R&D.
Meanwhile, Westinghouse Electric Company in the United States also actively participated in liquid crystal research since the 1950s. Westinghouse’s research institute produced two directions of LCD technology: performance far superior to RCA’s milky dynamic scattering DCM-LCD twisted nematic liquid crystal displays (TN-LCD); and active matrix thin-film transistor (TFT) technology liquid crystal displays. The small-scale TFT research project initiated in 1963 only received support from the television and semiconductor divisions, so when Westinghouse closed these two divisions in the mid-1970s, the initiator of the TFT research project, Brody, left due to lack of company support.
Although thin-film transistors could make active matrix liquid crystals superior to any other liquid crystal produced at that time, and foreseeably lead to revolutionary applications—flat displays could generate considerable revenue, the technology of thin-film transistors and displays was still in its infancy, requiring continuous improvement of material stability, and could not be applied to consumer electronics. The long wait for R&D investment conversion led many large American enterprises involved in liquid crystal displays to abandon the development of TFT-LCD technology, ultimately failing to achieve the industrialization of flat displays.
(2) Development: Japan realizes industrial production.
In 1968, at RCA’s press conference, the Japanese industry developed a strong interest in LCD technology, gradually realizing the industrialization of TFT-LCD technology and constantly enriching the application fields of flat displays based on market demand. Japanese companies were the first to apply LCD technology to small electronic products, such as the first LCD electronic watch by Suwa Seiko and calculators by Sharp.
Due to the boom of electronic watches and widespread use of calculators in the 1970s, funding for developing flat display technology was secured; meanwhile, from the launch of the 2-inch TFT-LCD micro-color television by Suwa Seiko in 1983 to Sharp’s successful development of a 14-inch color television in 1988, the application of liquid crystal displays constantly updated and upgraded manufacturing capabilities, production processes, and performance, laying the foundation for the subsequent development of notebook computer screens, computer monitors, and ultimately television flat displays.
The process of achieving mass production was not smooth; Japanese companies achieved large-scale manufacturing of TFT-LED through collaboration with American technology companies. In 1991, Toshiba and IBM jointly established the DTI manufacturing alliance, combining Toshiba’s DRAM, STN-LCD, and IBM’s TFT display configuration experience, but the initial yield rate was only 10%, primarily constrained by equipment and dust during production. After 1993, through collaboration with Applied Materials, the improved CVD equipment successfully raised the yield rate to 90%.
Due to the dynamic relationship between market demand and industrial innovation, the strong cyclical nature of the liquid crystal display industry began to emerge. Between 1991 and 1996, 21 out of 25 large-scale production lines built globally were established in Japan, which led to the emergence of a complete upstream and downstream TFT-LCD industrial enterprise in Japan, such as Asahi Glass and Schott for upstream glass substrate production, Nitto Denko for color films and polarizers, and Nikon, Canon, and NEC-Aniwa for providing scanning lithography machines, stepper lithography machines, and dry etching machines, respectively. However, due to Japan’s adherence to vertical integration from design to production, it failed to ensure continuous innovation through timely horizontal adjustments, gradually fading from the historical stage as South Korea and Taiwan surpassed them.
(3) Maturity: Capacity shifts to South Korea and matures.
From 1995 to 1996, the second recession period of the liquid crystal industry emerged. Unlike the usual behavior of reducing investment during recession periods, South Korea rapidly completed scale expansion through continuous counter-cyclical investments with government support, importing technology from Japan: Samsung and Hyundai completed their third-generation lines in October and November 1996, respectively; LG launched the world’s first 14.1-inch XGA-grade notebook panel with its 3.5-generation line at the end of 1997. Despite Japan still holding a monopoly in the global LCD field during the Asian financial crisis in 1997, most companies were still operating at a loss. In the same situation, South Korean companies Samsung and LG, which had been losing for 7-8 years, continued to invest billions of dollars in the globally sluggish liquid crystal display market, and it was during this year that South Korea finally ended nearly a decade of losses and successfully surpassed Japan again in 1998—Samsung and LG achieved market shares of 18.8% and 16.2% in the display market, respectively, surpassing the leading company Sharp. In 2000, under the Korean government’s demand for “horizontal integration,” companies like Hyundai gradually exited the market.
At the same time, Taiwan, China, due to its large electronic terminal market, has been striving to build a technological foundation for large-sized TFT-LCD through the Industrial Technology Research Institute (ITRI), leading to the establishment of companies like Chi Mei Optoelectronics and TPO Displays. The financial crisis and the recession in the liquid crystal market made it difficult for Japanese companies to maintain the confidentiality of TFT-LCD manufacturing technology, producing only in Japan. To counter the increasing competitiveness of Korean companies due to the depreciation of the Korean won and the loss of market share in Taiwan, Japanese companies like Toshiba and Sharp were forced to build factories in Taiwan and transfer technology to make up for their investment losses in the LCD industry. During the third recession period, six Taiwanese companies seized the opportunity, rapidly rising and forming an industrial scale that could compete with Korean companies.
The fourth recession period of the liquid crystal panel industry provided space for another batch of emerging Taiwanese companies to develop, with companies like AUO, Innolux, and TPO originating from this period. Overall, during 2004-2006, Taiwan’s LCD panel companies manufactured large-scale 5th and 6th generation lines, competing closely with South Korea’s Samsung and LG, capturing a significant share of the global liquid crystal display market. However, with the onset of the 2008 economic crisis, local demand weakened, and Japanese and Korean companies successively canceled orders, leading to Taiwanese LCD panel companies’ operating rates dropping to below 50%. Meanwhile, the demand for liquid crystal display panels in mainland China kept increasing, ultimately driving the rise and rapid development of the TFT-LCD industry in mainland China.
By reviewing the development path of LCD technology and the rise and fall of various countries’ LCD industries, it can be seen that the LCD industry is a typical capital-intensive, labor-intensive industry that continuously innovates driven by market demand. The development of LCD companies requires the joint promotion of policy support, technological development, and capital investment.
3
The cyclical weakening of LCD panels boosts
industry profitability.
LCD panels are typical technology-intensive and capital-intensive industries. Due to the supply-demand mismatch caused by the two-year construction period for new production lines and a one-year capacity ramp-up period, the industry has shown strong cyclicality. We believe that as the industry enters a mature phase, manufacturers’ willingness to build new capacities has significantly decreased, with demand remaining relatively stable and supply-side capacity tending to stabilize. The improvement in the industry supply-demand structure will significantly reduce cyclicality, and panel prices will maintain within a reasonable range, significantly enhancing the profitability of LCD manufacturers.
(1) Demand side: Large size and high definition remain the main themes.
Large size and high definition continue to be the main trends in the future development of panel displays.
Specifically for LCD panels, the main growth in demand comes from the increase in shipment area of large-sized panels such as televisions; the commercialization of Mini-LED backlight technology will also bring new growth space for the industry, with the global demand area for liquid crystal panels expected to grow at a compound annual growth rate of 6.5% over the next three years.
1. TV: The demand for large size and high definition upgrades, and LCD remains mainstream.
In the TV sector, the global LCD television market is nearing saturation.
According to Wind data statistics, the global shipment of LCD television panels was 230 million units in 2013, increasing to 269 million units in 2020, with a compound annual growth rate of approximately 2.4%. The main driving force for global LCD television replacement is consumer demand for larger and high-definition televisions, and it is expected that global LCD television shipments will maintain a compound annual growth rate of over 2% in the next 3-5 years.
Consumer upgrading drives the demand for large-sized TVs.
Television applications are becoming increasingly diverse, and consumers’ pursuit of display effects for movies and games is growing, leading to an increase in the average size of televisions. According to statistics from Qunzhi Consulting, the shipment proportion of 65-inch televisions increased from 4.3% in 2017 to 8.2% in 2019, and it is expected that the shipment proportion will reach 9.2% in 2020.
TV consumer upgrading drives the large size of panels.
Over the past five years, the average size of TV panels has grown by 1 inch each year: According to statistics from Qunzhi Consulting, the average size of television panels was approximately 41.4 inches in 2014; in 2019 it increased to approximately 45.3 inches, and it is expected that the average size of television panels will reach 50.8 inches by 2022. We believe that large size will be the main driving force for the growth of panel demand, and manufacturers such as BOE and Huaxing Optoelectronics, who have taken the lead in high-generation production lines, are expected to maintain a leading advantage and continue to increase their global market share.
High definition is another driving factor for panel demand growth.
Improving resolution will significantly enhance the picture quality of panel displays to meet consumer demands for display effects. The 4K technology took 7 years to become popular from its launch in 2013. According to WitsView statistics, the penetration rate of 4K televisions was approximately 53.4% in 2019, and it is expected to reach 62.8% by 2022. Based on the development of the 8K industry chain, Qunzhi Consulting predicts that the global shipment of 8K panels will exceed 7 million units by 2022, with a penetration rate of about 3%. The improvement in resolution is expected to drive panel prices up, enhancing the profitability of panel manufacturers; at the same time, the average size of 8K televisions will be larger than that of 4K televisions, and the increase in 8K television penetration will also boost the penetration rate of large-sized panels, allowing panel manufacturers to fully benefit from the growth in large size and high definition.
The global shipment area of LCD television panels is expected to maintain a growth rate of over 6%.
According to our calculations, the compound annual growth rate of global LCD television shipments from 2021 to 2023 is expected to be 2.2%; with the average size of global televisions increasing by 1 inch each year, and the ratio of 16:9 calculated, the global shipment area of LCD television panels is expected to reach 203 million square meters by 2023, with a compound annual growth rate of 7.64% from 2020 to 2023.
2. IT: The demand for PCD is strong under the home economy, and new products bring new space for LCD.
In the IT sector, the “home economy” has led to strong demand for medium-sized laptops. Although the COVID-19 pandemic suppressed consumer demand in the first quarter of 2020, the demand for home-based classes and office work during the pandemic led to a significant rebound in PCD shipments since the second quarter of 2020: According to IDC data statistics, the global PCD shipment was 130 million units in Q3 2020, a year-on-year increase of 19.7%, reaching a 10-year high. Among them, laptops and tablets are important growth points in the PCD market, with global shipments of 63 million and 47 million units respectively in Q3 2020, representing a year-on-year increase of 36% and 25%. The repeated COVID-19 pandemic and various countries’ consumer stimulation policies may further stimulate market demand, and it is expected that global computer shipments will increase by 14% year-on-year in Q4 2020, with a total shipment of about 455 million units in 2020, a year-on-year increase of 10.47%. IDC predicts that if the pandemic begins to subside in 2021, global computer shipments will gradually return to around 441 million units.
PCD LCD panel sizes are also developing towards larger sizes.
Due to consumer demand for LCD screens focusing on large sizes and high definition, the average size of PCD LCD panels has also shown an increasing trend each year. According to Strategy Analytics data, the average size of tablet computers was about 7.58 inches in 2015, growing to 8.03 inches in 2019, with an average annual growth of 0.09 inches. According to NPD DisplaySearch data, the average size of laptops has increased by about 1 inch every three years.
Based on the scenario of the COVID-19 pandemic gradually easing in 2021, we expect the shipments of LCD monitors, laptops, and tablets to return to 114 million, 247 million, and 94 million units respectively in 2021. It is expected that from 2022 to 2023, the shipment growth rate of LCD monitors will recover to around 1%; laptop shipments may gradually return to long-term average levels from high levels; considering the boosting effect of new technologies like Mini-LED backlighting on tablet demand, the shipment growth rate of tablet LCD panels is expected to remain at 1.5%. According to data analysis from Strategy Analytics and NPD DisplayResearch, with the average sizes of LCD monitors, laptops, and tablets increasing by 0.33 inches, 0.06 inches, and 0.09 inches respectively each year, and the screen ratio selected as 4:3, the global shipment area of LCD panels for IT is expected to reach 0.29 million square meters by 2023, with a compound annual growth rate of 1.02% from 2020 to 2023.
3. Mobile phones: 5G replacement demand is recovering, and LCD penetration is decreasing.
Due to the impact of the COVID-19 pandemic, global smartphone shipments plummeted in 2020.
According to IDC data statistics, global smartphone shipments were 1.26 billion units in 2020, a year-on-year decrease of 7.92%. In 2021, global smartphone shipments are expected to return to growth. With the rapid progress of COVID-19 vaccines, the global pandemic is expected to reach a turning point, and the rapid development of 5G will drive a quick recovery in the smartphone market, with shipments expected to maintain positive growth over the next three years: IDC predicts that global smartphone shipments will reach 300 million units in Q1 2021, a year-on-year increase of 9.34%; total shipments for 2021 are expected to reach 1.35 billion units, a year-on-year increase of 6.87%.
In the mobile phone sector, the penetration rate of LCD panels is gradually declining.
As OLED products have developed and applied technologies such as folding screens, under-screen fingerprints, and under-screen cameras, the penetration rate of OLED products has increased. According to DSCC predictions, by 2023, the penetration rate of LCD panels in global smartphones will decrease to 46%. The panel sizes in the mobile phone sector are also trending towards larger sizes: According to IDC data, the penetration rate of 6-7 inch mobile phones in China increased from 5% in 2014 to 7% in 2018; the penetration rate of 5.5-6 inch mobile phones increased from 5% in 2013 to 38% in 2018, with an average size increase of about 0.15 inches per year.
Based on IDC’s predictions for global smartphone shipments over the next three years, it is expected that smartphone shipments will be 1.35 billion, 1.39 billion, and 1.42 billion units respectively from 2021 to 2023. According to DSCC data, the penetration rates of LCD smartphones are expected to be 55%, 50%, and 46% respectively from 2021 to 2023. Assuming an average size increase of 0.35 inches each year, with a screen ratio of 16:9 calculated, the global shipment area of smartphone LCD panels is expected to remain around 7 million square meters over the next three years.
According to our supply model calculations, it is expected that by 2023, the global shipment area of LCD panels will reach 238 million square meters, with a compound annual growth rate of 6.5% from 2020 to 2023, driven by the demand for large sizes.
(2) Supply side: Capacity expansion is lagging, and the willingness to add new capacity is low.
Liquid crystal displays are technology-intensive and capital-intensive industries.
According to NPD Display Search statistics, the investment amount for a 4th generation production line is approximately $700 million, while that for a 10th generation production line is approximately $4 billion. Despite the high investment scale for high-generation lines, due to scale effects, the production efficiency of high-generation lines significantly improves, leading to higher profitability: under the same technical level, the larger the display area, the higher the unit area price and profit.
In contrast to the stable growth of demand, the supply side is gradually decreasing due to the withdrawal of overseas capacity.
The new round of cyclical downturn in the panel industry lasted from the second half of 2017 until 2019, during which the entire panel industry experienced long-term massive losses. For example, the price of a 32-inch panel dropped from a peak of $75 in the second half of 2017 to $30 by the end of 2019. The cyclical downturn in the panel display industry has led to continuous losses for overseas leading enterprises such as Samsung and LGD in the LCD business, prompting manufacturers to shift to the OLED market and gradually withdraw from the TFT-LCD market. In 2019, SDC’s L8 and LGD’s P8 factories began the first round of capacity conversion, resulting in a significant decrease in capacity. By the end of 2020, Samsung and LG planned to shut down the remaining LCD production lines in 2021, but it cannot be ruled out that in the case of supply tightness, the remaining production lines may continue to be delayed in shutting down.
The industry is entering a mature phase, and manufacturers’ willingness to build new production lines has decreased.
From 2017 to 2020, more than two new production lines were launched annually in mainland China, mainly including BOE’s Wuhan production line, CSTO’s T6 and T7 production lines, etc. Considering the impact of the COVID-19 pandemic on the progress of production line construction, it is expected that the new production capacity will mainly be released in the second half of 2021. We believe that the LCD industry has entered a mature phase, and under the high investment and high technical barriers of liquid crystal displays, manufacturers’ willingness to build new production lines has decreased, significantly improving the competitive landscape on the supply side.
Based on the current plans for overseas manufacturers to withdraw capacity and the announcements of new production line construction by various companies, we expect that the overall capacity of global panels will be at a low point from June 2020 to June 2021. According to our supply model predictions, it is expected that by 2022, the global capacity of LCD panels will be approximately 231 million square meters. If no new LCD production lines are built in 2021, it is expected that the capacity of LCD panels will remain the same in 2023 as in 2022, with a compound annual growth rate of 3.08% from 2020 to 2023.
The supply-demand relationship is reversing, and the supply-demand ratio is gradually improving.
Historically, due to increased capacity and weak demand, the panel supply-demand ratio has been rising since 2017, and the decline in panel prices has led to losses for some overseas production lines starting in 2019. In 2019, with the withdrawal of overseas capacity, the panel supply-demand ratio continued to decline. In the optimistic case where there are no new production lines under the existing capacity withdrawal plans, it is expected that the panel supply-demand will remain below the balance line for the next 3-5 years. Even if the overseas capacity withdrawal plan is extended indefinitely, the existing capacity accounts for about 2.23%, and the industry supply-demand will still remain below the balance line. Based on data from BOE’s G10.5 generation line, the added capacity from a new 10.5 generation line is approximately 1.94%. We believe that under the pessimistic scenario where overseas capacity is retained and a new 10.5 generation line is added in the next two years, the LCD panel industry will still remain within the supply-demand balance range.
(3) Price: Cyclicality is weakening, and prices are expected to stabilize within a reasonable range.
The inventory cycle remains low, and the prices of large-sized panels continue to rise.
In early 2020, due to the impact of the COVID-19 pandemic, global television demand decreased, disrupting the previous market growth logic, leading to a decline in panel demand. In the second half of the year, panel inventory was effectively reduced, with the inventory cycle maintaining a low level of about one week. The demand for large-sized panels gradually warmed up, and panel supply capacity decreased, leading to a continuous rise in prices: According to Wind data statistics, since June, the average price of large-sized panels has increased by about 64%, with the price of 32-inch panels rising by 91% from the low point. In January 2021, the average price of large-sized panels increased by 4%, with the increase narrowing but still exceeding market expectations. It is expected that this round of price increases will continue until June 2021. In the context of improving supply-demand structure, panel prices are expected to remain at a reasonable range for the long term.
The prices of medium-sized panels are recovering.
In 2019, the demand for PCD fell from a high level, leading to a decline in the prices of medium-sized panels. Due to the significant recovery in notebook demand in 2020, the prices of notebook panels began to rise from February, and the price increase trend continued into 2021, with the increase accelerating: According to Wind data statistics, the price of 14.0-inch notebook panels increased by 4.7% month-on-month in January 2021. We believe that notebook computer demand will remain strong in 2021, and the prices of notebook panels still have some upward potential.
Prices of small-sized panels (a-Si LED) are recovering.
In the small-size segment, panel prices are relatively differentiated. Due to the COVID-19 pandemic leading to a decrease in disposable income, high-end mobile phone sales have been affected, while the impact on mid-range and low-end phones has been minimal. According to CINNO Research statistics, since August 2020, a-Si small-sized panel prices have slightly increased by $0.1/panel; prices of flexible OLED, rigid OLED, and LTPS LCD panels continue to decline by $1/panel each month.
The rise in panel prices is expected to significantly improve the profitability of panel manufacturers.
Panel manufacturers’ profitability is significantly influenced by panel prices: from 2019 to the first quarter of 2020, except for Samsung Electronics, which maintained profitability due to the high proportion of OLED and other businesses, LGD, Innolux, AUO, and other manufacturers were in a loss state, with an average net profit margin of -8.2% in Q1 2020. Since the price increase of panels in the second half of 2020, the profitability of various manufacturers has significantly improved, with the average net profit margin recovering to 2.7% in Q3 2020. As panel prices rise to the high point seen in early 2017, we expect that the average net profit margin of liquid crystal panel manufacturing businesses will recover to over 10%.
We believe that with the improvement of the industry supply-demand structure, the cyclicality of panel prices will gradually weaken.
Specifically, as the demand for mobile terminals recovers, the prices of small-sized panels are expected to continue to repair; the demand for notebook computers will remain high in 2021, and the prices of medium-sized panels are expected to continue to rise; the continued withdrawal of overseas panel capacity, coupled with the recovery of TV demand, is expected to maintain the upward trend in large-sized panel prices until the first half of 2021, significantly improving the profitability of panel manufacturers.
4
The LCD panel industry enters a great era in China.
China began to enter the flat panel display industry in the early 1980s and only began to realize the industrialization of new display panels after 2005, completing a “leapfrog” development in nearly 10 years. The first stage from 2003 to 2008 was the learning phase: China’s flat panel display began with the “three plus one” model: in terms of technology, mergers, joint ventures, and team efforts were conducted simultaneously; in terms of capital, strong support was obtained from local governments. In 2003, large-scale research on the flat panel display industry began domestically, and in 2005, through the acquisition of South Korea’s third-generation line technology, BOE’s fifth-generation line was put into production. In the same year, the Shanghai Shanghai Electric NEC, a joint venture with Japan’s NEC, also began production (later known as Shanghai Tianma’s fifth-generation line). In 2006, Kunshan Longteng Optoelectronics led by a Taiwanese technology team and Shenzhen Super Optoelectronics began construction.
The second stage from 2009 to 2015 was the rapid development phase: due to the significant driving effect of the display industry on local economic development, local governments continued to increase investment in the display field, with BOE A receiving over 8 billion yuan in government subsidies during this period, and Huaxing Optoelectronics receiving over 7 billion yuan in subsidies. With strong funding support, China’s display industry solidified its foundation, expanded factory scale and efficiency, and gradually turned losses into profits. The third stage from 2016 to the present is the rapid expansion phase: during this period, technology has improved, and production has been actively expanded, utilizing scale advantages to reduce costs and increase efficiency. Despite losses from overseas production capacity, active mergers and acquisitions have achieved market scale expansion. In the future, China’s LCD market share will stabilize at over 70%, and the industry will overall enter a mature phase, enhancing profitability and transitioning from manufacturing to upstream materials and equipment transmission.
(1) Policy support: China’s policies strongly support the LCD industry.
The display panel industry is a key industry supported by the state, with multiple policies issued to support the development of China’s panel industry.
Since 2009, the construction of TFT-LCD industrial lines of 6 generations or more has been clearly supported by the “Electronic Information Industry Adjustment and Revitalization Plan.” In 2012, the Ministry of Industry and Information Technology released the “12th Five-Year Development Plan for the Electronic Information Manufacturing Industry” and the “12th Five-Year Plan for Electronic Basic Materials and Key Components,” focusing on supporting the development of high-generation LCD related devices, enhancing the performance of thin-film transistors (TFT), improving the transmittance of LCD panels, and reducing production costs.
In 2015, the National Development and Reform Commission and the Ministry of Industry and Information Technology passed the “2014-2016 New Display Industry Innovation Development Action Plan,” mainly promoting the research and industrialization of high-performance hybrid liquid crystal materials required for preparing high-generation TFT-LCD panels, aiming to reach the second-largest shipping area in the world within a year. In the same year, the signing of the “China-South Korea Free Trade Agreement” adopted an “8+2” policy for panel industry tariffs, maintaining an 8% tariff for eight years and a 2.5% tariff during a one-year adjustment period, before implementing a zero-tariff policy, allowing sufficient development time for domestic panel manufacturers to compete on the same level with China’s 8.5/10 generation lines and Korea. This move also attracted Korean manufacturers to invest and establish factories in China to reduce tariffs, such as Samsung and LGD establishing 8.5 generation lines in Suzhou and Guangzhou, respectively, which also triggered a chain reaction of cooperation between the Taiwanese panel industry and the mainland, promoting future trade relations development.
In 2019, the “Action Plan for the Development of the Ultra High Definition Video Industry (2019-2022)” was jointly issued by the Ministry of Industry and Information Technology, the National Radio and Television Administration, and the Central Radio and Television Station, expecting that by 2022, the overall scale of China’s ultra-high definition video industry will reach 4 trillion yuan, comprehensively driving upgrades in networks, hardware, terminals, and content production.
Many local governments have invested in supporting China’s liquid crystal panel manufacturing industry.
In 2018, BOE, a leading liquid crystal panel manufacturer, launched the “8425 strategy,” combining local urban investment platforms of 20 billion yuan, local bank loans of 20 billion yuan, and its own assets of 6 billion yuan, officially putting into production the 10.5 generation TFT-LCD production line, achieving a higher self-sufficiency rate for 4K/8K panels. China’s policies, funding support, and scaling effects give mainland panel manufacturers a significant advantage compared to Korean and Japanese manufacturers.
At the same time, under policy support, the liquid crystal panel industry chain has achieved vertical integration development.
The state has introduced a series of major policies to encourage the development of liquid crystal materials and equipment from the perspectives of national development strategy, industry cultivation and development encouragement policies, technology talent training, and innovation system construction. Under the background of encouraging the localization of display technologies, the domestic production rate of upstream equipment and materials for liquid crystal panels has entered a period of rapid increase, providing broad growth space for the industry.
(2) Scale effects: Dual improvements in market share and brand influence.
With the support of policies and funds, China has become the world’s largest supplier market for LCD panels.
According to statistics from the China Commercial Industry Research Institute, in 2016, China’s panel capacity accounted for about 29%, and it is expected that by 2022, China’s panel capacity will reach 56%. Considering that since 2019, Korean manufacturers like Samsung and LG have gradually shut down their LCD industry chains, according to our supply model calculations, it is expected that in the next three to five years, China’s panel capacity share may rise to over 70%.
In addition to the withdrawal of overseas capacity, Chinese panel manufacturers are also actively integrating and merging, leading to a significant increase in industry concentration.
Chinese panel manufacturers have gradually formed a two-strong pattern: according to data from Lott Technology, based on global television liquid crystal panel shipment area rankings, BOE and Huaxing Optoelectronics (TCL Technology) rank first and second respectively; based on global television liquid crystal panel shipment volume rankings, BOE A and Huaxing Optoelectronics ranked first and fourth in global liquid crystal television panel shipments and shipment areas in 2019.
BOE and Huaxing Optoelectronics are orderly advancing new production capacity and planning to acquire high-quality assets at home and abroad to further enhance market share: In 2020, BOE planned to acquire the G8.5 generation line of China Electronics Panda in Nanjing and the G8.6 generation line in Wuhan, which is expected to be completed in January 2021; in 2020, TCL acquired equity in Suzhou Samsung Display, further integrating the panel market. According to DISCIEN’s forecast, by 2021, BOE and Huaxing Optoelectronics’ market share is expected to reach around 50%.
For more details, please refer to the original report.For the complete PPT report, please reply with the keyword “21507” in the WeChat public account of Lei Feng Network.
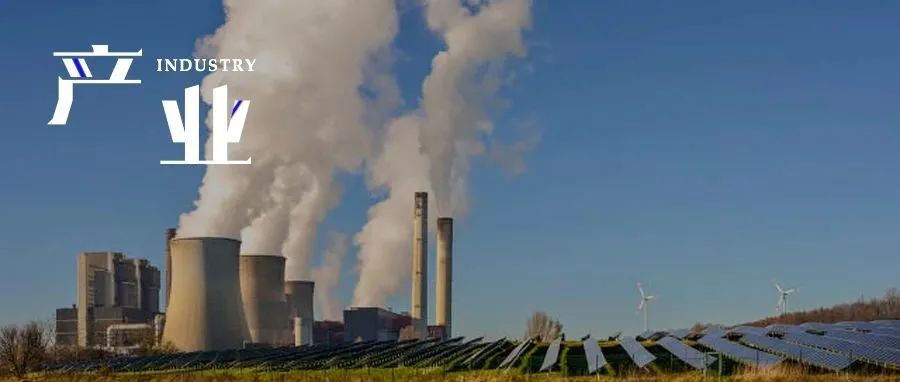
Is industrial manufacturing “carbon neutral” possible?
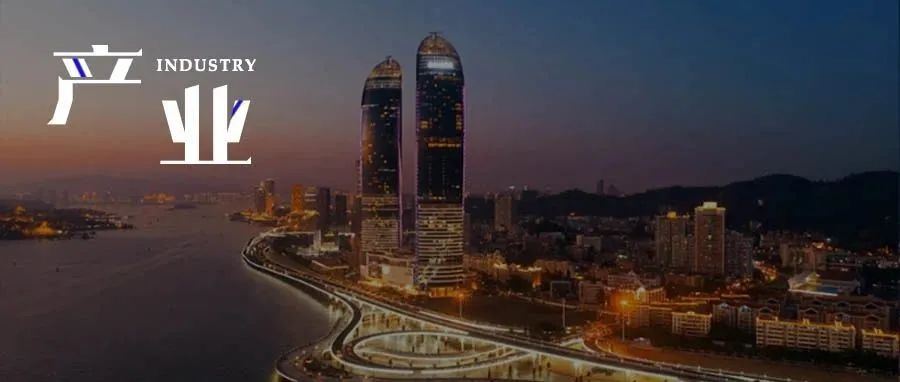
A LED chip’s “fantastic drift” | Ten cities’ chip manufacturing record④