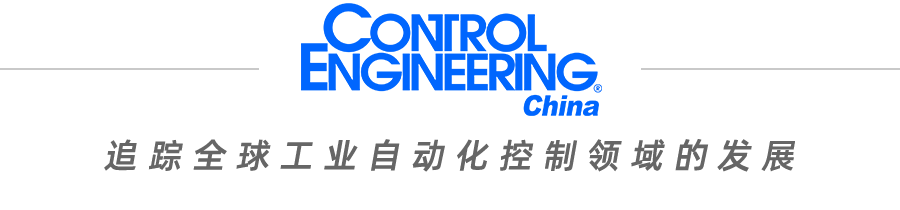
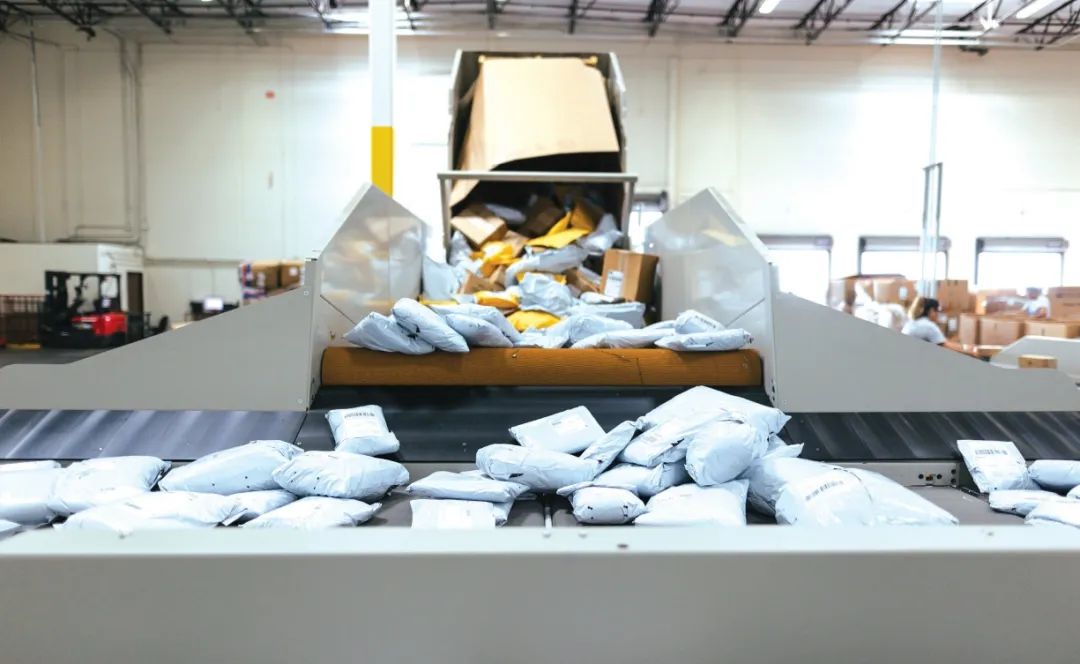
| Soft Packaging Sorting System.Image source: Beckhoff
Author | James Fig
Through a PC-based control device and EtherCAT sorting solutions, NPI helped a distribution center reduce its hard-to-fill labor demands while increasing throughput and shortening turnaround times.
The internal logistics industry is booming. However, for large postal and parcel providers, e-commerce retailers, and third-party logistics companies, capital investments still need to make good business sense. NPI, a mail sorting system design company, understands this well, which is why it always focuses on return on investment when designing package sorting solutions. Their third-generation Xstream linear sliding shoe sorter and independent Singulator package induction device are two examples.
“Typically, our customers need to handle at least 40,000 packages daily, so they need to maximize uptime and throughput while reducing costs and alleviating labor shortages,” said NPI CTO Joshua Owens. “To achieve this and help customers shorten their return on investment cycle as much as possible, we allocated 60% of our engineering resources to this project, and we will continue to invest in key areas as the product upgrades.”
NPI was founded in 1977, and the following year released its first fully automatic mail sorting machine. The company, based in Fort Worth, Texas, focuses on sorting letters and flat items. It wasn’t until 2007 that NPI began operating an e-commerce warehouse for shipping medications in foam boxes. Owens and COO Brent Daboub found that standard equipment struggled to handle such soft packaging, leading them to develop the Xstream system.
The recently released NPI Singulator requires only two operators and can handle over 7,500 packages per hour. This package induction device provides a cost-effective modular package induction system for Xstream or other OEM manufacturers’ equipment. “Compared to bulky, complex, and costly automatic induction systems on the market, Singulator reduces footprint, costs, and labor requirements,” Daboub explained.
To meet current demands and ensure future innovation, NPI expanded its 100,000 square foot facility, adding 18,000 square feet of storage space and 25,000 square feet of manufacturing space. Standardized automation technology, EtherCAT networks, scalable controllers, and operating system programming environments contribute to the company’s long-term growth.
01
Overcoming Throughput Limitations of Traditional Controllers
While NPI’s solutions continue to evolve to meet today’s demands, traditional networking and control technologies have not kept pace. Sorting systems are inherently large, complex systems filled with various nodes, exacerbating performance limitations based on switch protocols. Additionally, the company desired a modular design for its systems that would be easy to scale. Previously used discrete I/O and Ethernet brought unnecessary complexity, costs, and installation workloads.
The first and second-generation Xstream systems utilized ARM-based microcontrollers and NPI’s self-developed dedicated motherboards. However, these microcontrollers were not flexible enough to meet customer needs. In 2017, engineers began evaluating scalable off-the-shelf solution providers before redesigning the third-generation Xstream. NPI ultimately chose Beckhoff and collaborated with their team in Dallas.
“Standardized hardware provides us with room for growth without needing to redesign circuit boards, find new processors, or add memory. After comparing system availability, scalability, and EtherCAT I/O performance, the choice was clear,” Owens said.
02
High-Performance Controllers and Scalable Systems
NPI selected high-performance, scalable industrial controllers, equipping the Singulator device used in conjunction with third-party manufacturers’ sorters with ultra-compact industrial PCs. For systems using both Singulator and Xstream, DIN rail-mounted embedded PCs or PLCs have become the main controllers for most applications. NPI recently began using embedded PCs equipped with quad-core AMD Ryzen processors (clock frequency of 3.35 GHz) to reserve sufficient computing power for future system expansions.
The new devices use modern UNIX-based operating systems instead of Microsoft’s Windows 10 IoT. This operating system alternative combines internal control development, scalable hardware, and real-time functionality with enhanced security and performance from modern UNIX-based operating systems. Modern PLCs utilize real-time operating systems (RTOS) rather than proprietary firmware. The controllers are enhanced with real-time kernels, higher RAM, and options for megabyte removable media, as well as extended functionalities such as assigning program tasks to specific CPU cores and running third-party software alongside PLCs. Engineers can also choose from a variety of processors, from single-core and multi-core microprocessors to ultra-high-performance multi-core processors. Virtual machine management architecture allows virtual machines running Microsoft Windows or Linux systems to operate simultaneously.
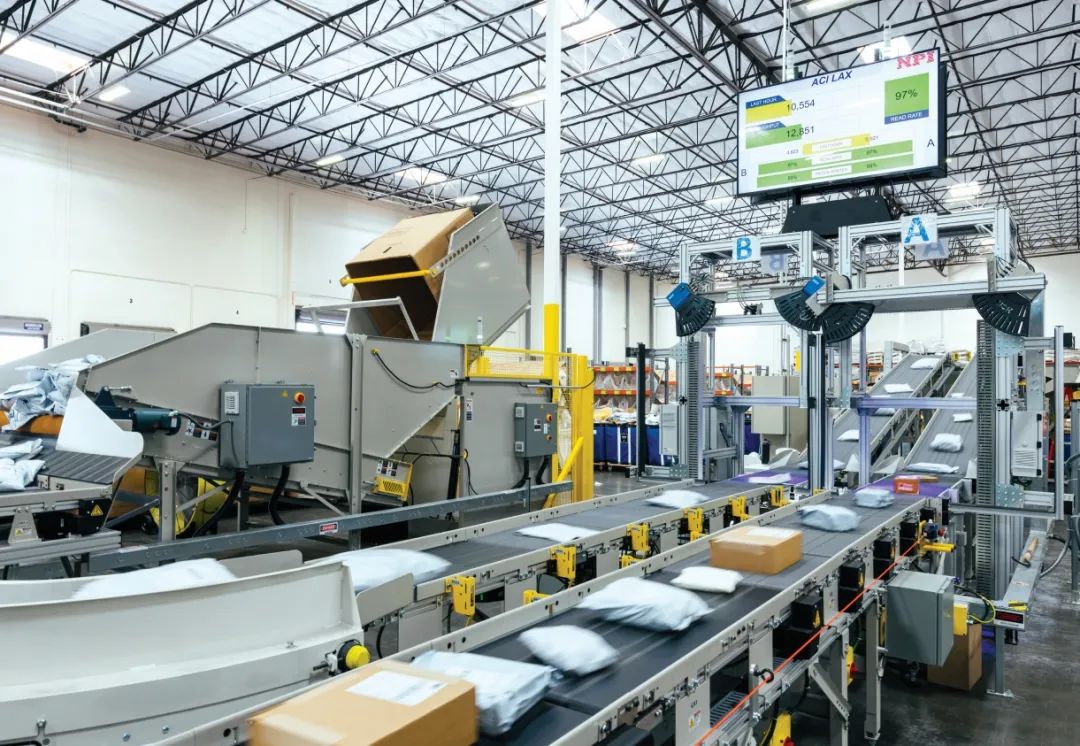
▲GigE camera and scanner combination measures package dimensions to ensure they are placed in the correct boxes.
In addition to performance improvements, smaller images also reduce the demand for compact flash memory, thereby lowering costs and speeding up NPI’s deployment of images by 70%. Owens stated, “We have always been looking for the most powerful and secure automation systems for our customers. After migrating to TwinCAT/BSD, our system performance has been further strengthened. Most importantly, the FreeBSD-based platform has eliminated our dependence on the Windows operating system, making PC-based control technology a viable option for customers sensitive to operating systems.”
03
Software Development Environment and Industrial Ethernet Technology
NPI appreciates the powerful performance of TwinCAT automation software and EtherCAT industrial Ethernet systems. PLCs, motion control, and the Internet of Things adopt end-to-end development and runtime environments. This enables engineers to program using the IEC 61131-3 programming language and object-oriented extensions, function blocks, and computer science standards in the language they are most familiar with or best suited for the application. Owens stated, “Migrating from C++ code on NPI’s traditional microcontrollers to the new platform was crucial, and the Visual Studio-based integrated development environment provided strong support for our progress.”
TwinCAT automatically scans devices on the EtherCAT network based on the ADS protocol, speeding up debugging. NPI also adopted Beckhoff’s various EtherCAT I/O terminal modules and terminal boxes. These IP67 rated remote I/O solutions come with M8 and M12 connectors, directly installed on each 11-foot middleware of the Singulator and Xstream. Because the EtherCAT Technology Group ensures device interoperability, this open protocol also simplifies the use of third-party devices.
“We are looking for a solution that can eliminate common performance degradation issues in I/O intensive systems,” Owens said. “EtherCAT is a high-speed, highly deterministic communication protocol. Using redundant EtherCAT wiring throughout our system, along with diagnostics available at any time, are also significant advantages.”
Doug Schuchart, Beckhoff’s global material handling and internal logistics industry manager, added, “The reduction in costs and complexity is just one of the benefits EtherCAT brings to our customers after simplifying system architecture; it also provides significant diagnostic and system lifecycle advantages, as well as simplifying digital transformation for IIoT and Industry 4.0 solutions.”
04
Helping Third-Party Logistics Companies Increase Throughput
According to local NPI sales support manager Shane Potter, the powerful performance of the Singulator and third-generation Xstream systems has been validated in a third-party logistics facility in the Greater Los Angeles area. Workers use pallet trucks to transfer large cardboard boxes containing unsorted packages to lifts at two package induction stations. Each lift dumps the packages onto the Singulator’s accumulation conveyor. Before operators confirm that the packages enter the main conveyor, various sensor devices limit the speed of package flow induction.
NPI’s high-speed, high-dynamic intermittent conveyors are driven by servo motors controlled via EtherCAT, allowing downstream peripheral devices to precisely separate packages. Tracking information is transmitted via EtherCAT to the Beckhoff controller, then transmitted via TCP/IP to NPI’s Warehouse Control System (WCS) software to determine the centralized sorting point.
“When packages arrive at the correct output, NPI’s patented step-driven diverter transports the appropriate number of shoes onto the diverter track. Packages are loaded into mailbags or containers and sent to post offices across the United States,” Potter explained. “By utilizing large-diameter polyurethane-coated bearings at both ends of the diverter and a patented chain automatic tensioning system, our engineering team strives to ensure that the Xstream system operates as safely, smoothly, and quietly as possible.”
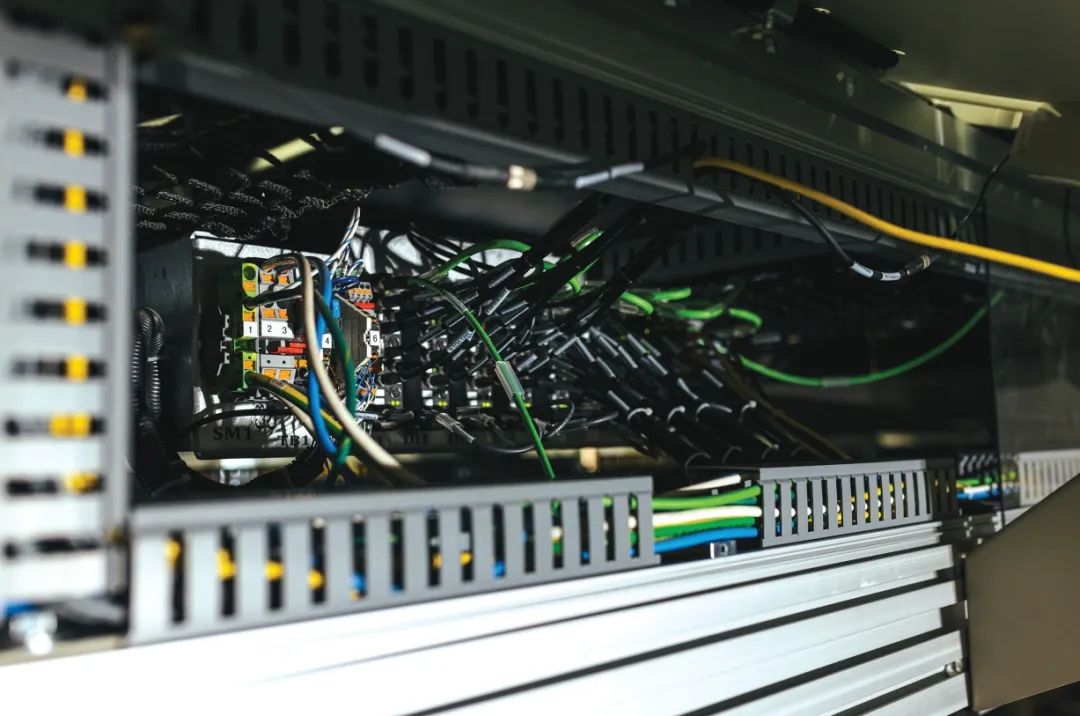
▲EtherCAT terminals and field-installed EtherCAT Box modules provide NPI with a high-performance distributed network.
By implementing NPI solutions, the throughput of third-party logistics companies has more than doubled year over year. The company now offers same-day delivery services, meaning packages leave within 24 hours of arriving at the transfer station. The company has also significantly alleviated its labor shortage issues, which is crucial for coping with peak sales seasons, especially as labor shortages become increasingly severe. Before the technological upgrade, this site required three shifts working six days a week to maintain normal operations. Now, it only requires one shift working five days a week and can handle more packages than previously expected.
05
Continuously Scalable Automation Platform
While achieving these impressive results, NPI has also constructed larger-scale systems and plans to continue developing automation solutions. First, NPI released a 22-inch dual chute that can use pneumatic actuators to divert packages, doubling the number of mailbags for more precise sorting. The company created an AWS operating interface to visualize WCS data, allowing management to compare performance across various sites using powerful analytical tools. Owens and Daboub are also exploring custom robots to fill the labor gap at Singulator operator stations. These robots will be deployed to address issues during peak seasons or overnight operations, enabling 24/7 operations and enhancing productivity.
In the largest Xstream application, EtherCAT allows for systems with up to 481 nodes on one network without any performance issues. EtherCAT terminal boxes ensure the expansion of intermediate sorting modules, alleviating concerns for NPI and its customers, who can confidently scale their systems based on future demands.
Additionally, IP67 I/O modules can significantly reduce system costs, including a potential 50% reduction in wiring work. After applying this solution, the overall wiring savings per Xstream system can amount to $4,700. Owens explained, “This also helps us save five days of on-site wiring time, which is a significant improvement.”
A mature hardware platform helps NPI escape the endless cycle of redesigning microcontrollers, Beckhoff sales engineer Jeff Kuzniar noted, “NPI’s application experience illustrates how we protect customers from being phased out due to outdated control systems. When our next-generation industrial PCs are released, they can use the same TwinCAT PLC projects without replacing any I/O, even when we release more powerful hardware in the future, they can still use the same TwinCAT PLC projects.”
Transitioning from microcontrollers to embedded controllers means NPI needed to transfer a decade of experience to the new platform within just a few months. Owens believes that the assistance of Beckhoff’s local team and free phone technical support played a crucial role in troubleshooting various issues. “When we started evaluating control vendors, we weren’t yet a company proficient in using PLCs; Beckhoff’s strong technical support structure was key to our success. Besides robust technical support, their control platform also provides us with the expansive space needed to maintain rapid growth.”
Key Concepts:
■ Understand how sorting companies upgrade their automation systems to improve operational activities.
■ Understand PC-based control and its role in reducing wiring and costs for sorting systems.
Reflect:
How can industrial PCs improve the operations of your factory facility?
– END –
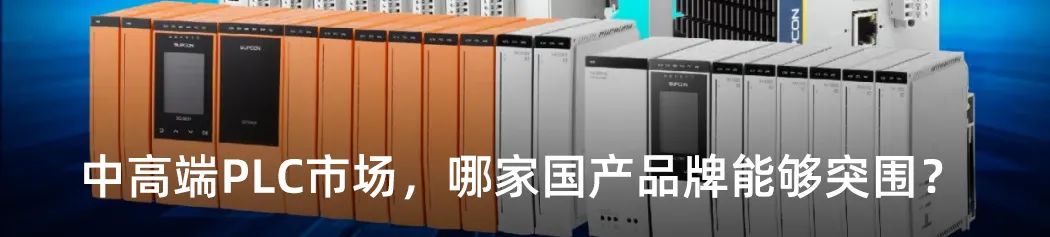
This article is from the March 2024 issue of CONTROL ENGINEERING China magazine in the “Technical Articles” section: Automation Upgrade: How to Reduce System Wiring and Lower Costs?
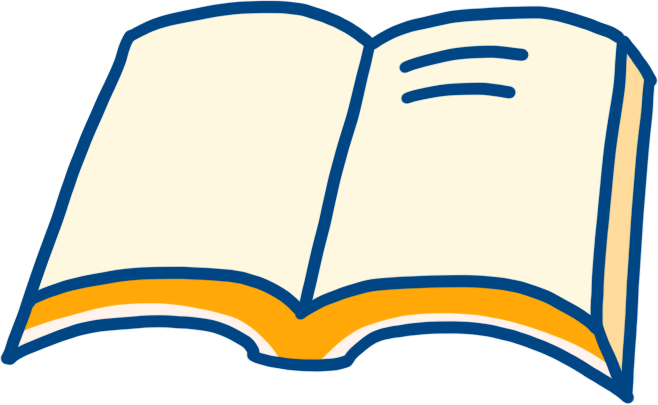
✦
Recommended Reading
✦
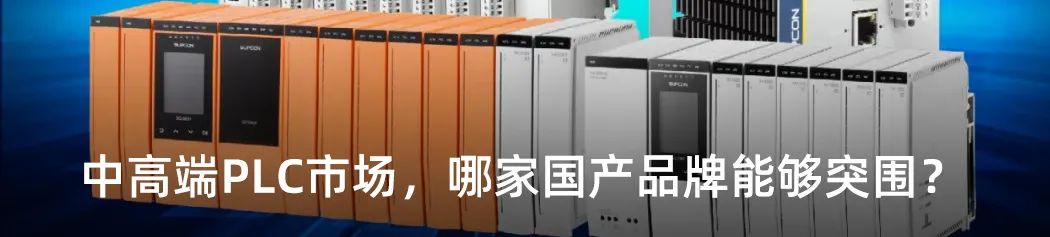
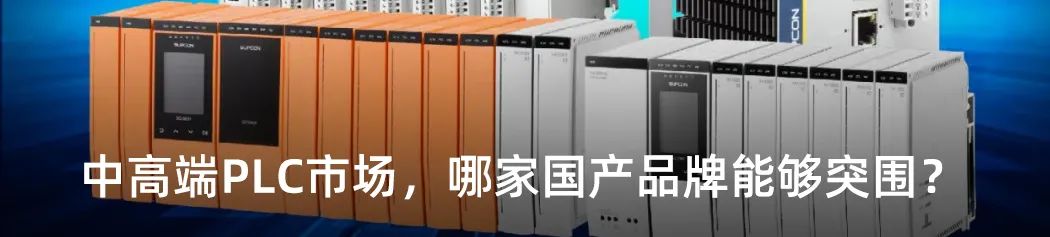
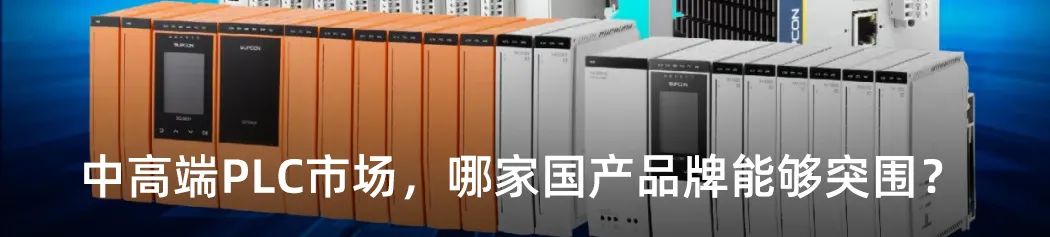
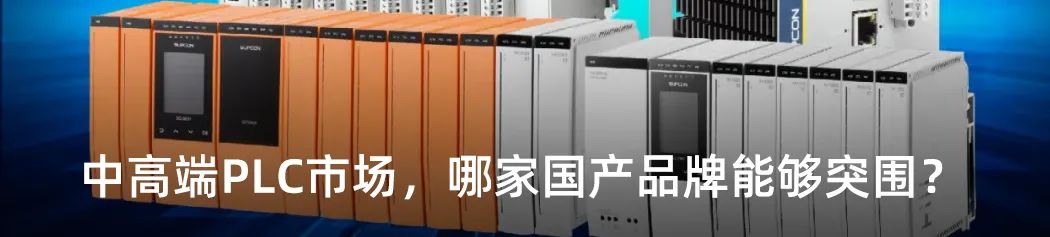
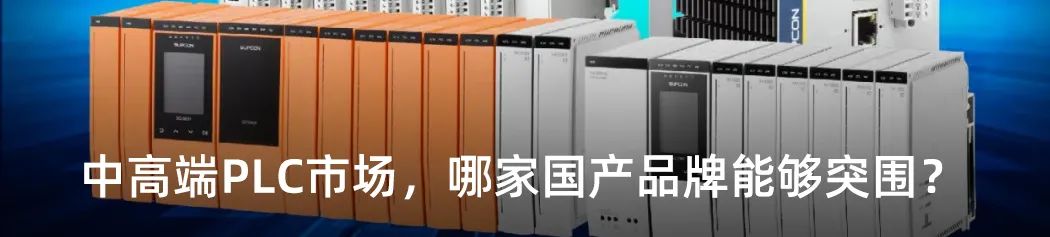
