Click on the above“Motion Control Assistant”, stay updated with new developments!
Friends, we are back. In the last issue, we briefly introduced some features of EtherCAT. This time, we will provide a more detailed introduction to the implementation of EtherCAT, the significance of the communication cycle, and concepts such as SDO and PDO.
First, it should be stated that although this issue goes a bit deeper, using the motion controller is very simple. You can fully utilize the various advantages of motion control on the bus without understanding the concepts below. This article is written for those interested and wanting to learn more. Only by understanding more can we solve complex problems.
The core technology of ZMC408CE adopts advanced FPGA technology, achieving hardware position comparison output and precise output functions, ensuring excellent performance and stability in continuous trajectory processing, as well as real-time dynamic data capture, thus achieving more precise control and improving production efficiency and quality.
ZMC408CE supports EtherCAT + pulse axis mixed interpolation, can operate offline or online, with 8-32 axes selectable, and supports ZDevelop + various advanced upper computer mixed programming, enabling point motion, electronic cam, linear interpolation, circular interpolation, continuous trajectory processing, and control of 30+ robot models.
2. One-dimensional/two-dimensional/three-dimensional, multi-channel visual fly shooting, high speed and high precision;
3. Position synchronous output PSO, precision control of glue amount in continuous trajectory processing, and laser energy control;
4. Multi-axis synchronous control, independent control of multiple coordinate systems;
5. EtherCAT synchronous cycle can be as fast as 125us;
6. Mixed interpolation of EtherCAT bus and pulse axis;
7. Linear interpolation, arbitrary space circular interpolation, spiral interpolation, spline interpolation, etc.;
Industrial sites often require stable and real-time communication, where sensors and IO signals need high-speed responses, and motor data needs to be transmitted in real-time. Before EtherCAT, there were already field buses like CAN bus.
However, as the automation systems in the field become larger, the bottlenecks of traditional buses become more evident:Insufficient bandwidth, low data transmission volume, and inability to fully utilize the development of IT technology, etc..Thus, a batch of field buses based on Ethernet was born, among which EtherCAT is one of the best.
The official description of the EtherCAT bus is a field bus based on Ethernet (as shown in the figure above). Why not directly use Ethernet? Because some characteristics of field communication are completely different from those in the IT field:
2. These nodes generally need to transmit a small amount of data, but the real-time requirements are very high.
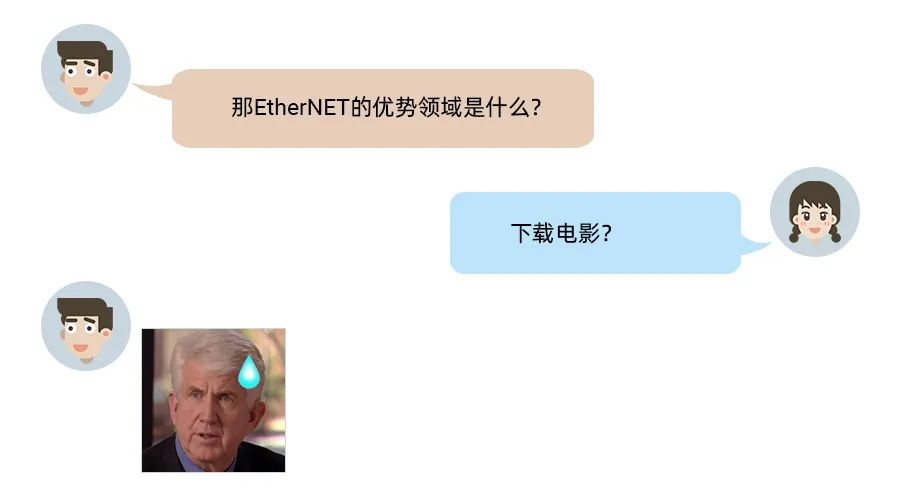
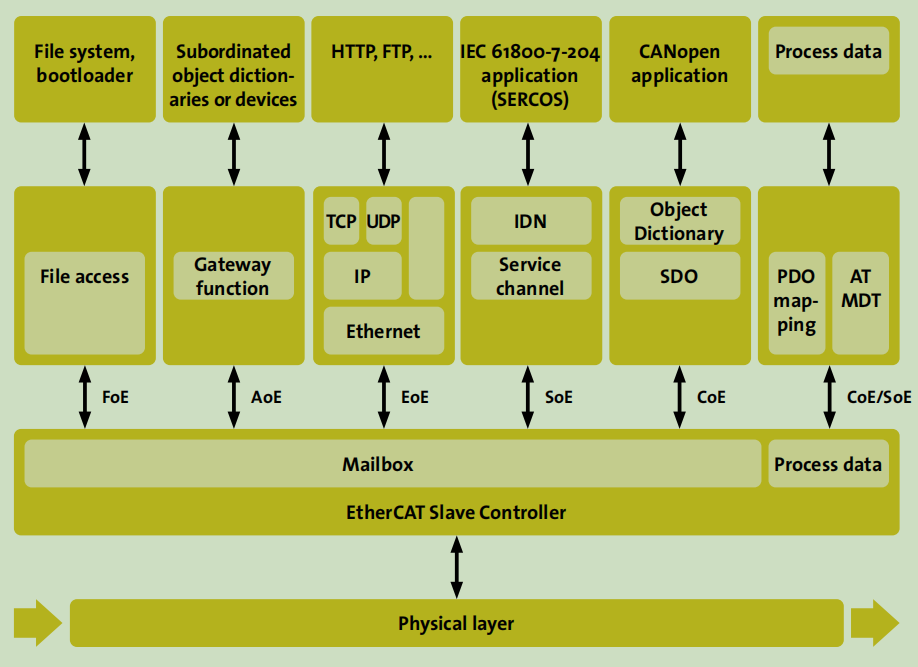
The transmission cycle of PDO information is what we often refer to as the EtherCAT communication cycle. For example, the regular firmware of Motion Control defaults to a cycle of 1ms (1K communication frequency), while some products can set a cycle of 125us (8K communication frequency). Why is the default 1ms instead of a shorter cycle (higher frequency)? What is the controller doing in this 1ms? What is the slave doing?
This needs to be explained from the working mode of CSP and the control loop of the motor, which will be detailed in later chapters.[Generally, 1ms is already small enough (1K is already high enough). Furthermore, motor synchronization is not based on the arrival time of data frames, but on a distributed clock, which can achieve nanosecond-level synchronization, as mentioned in the previous article].
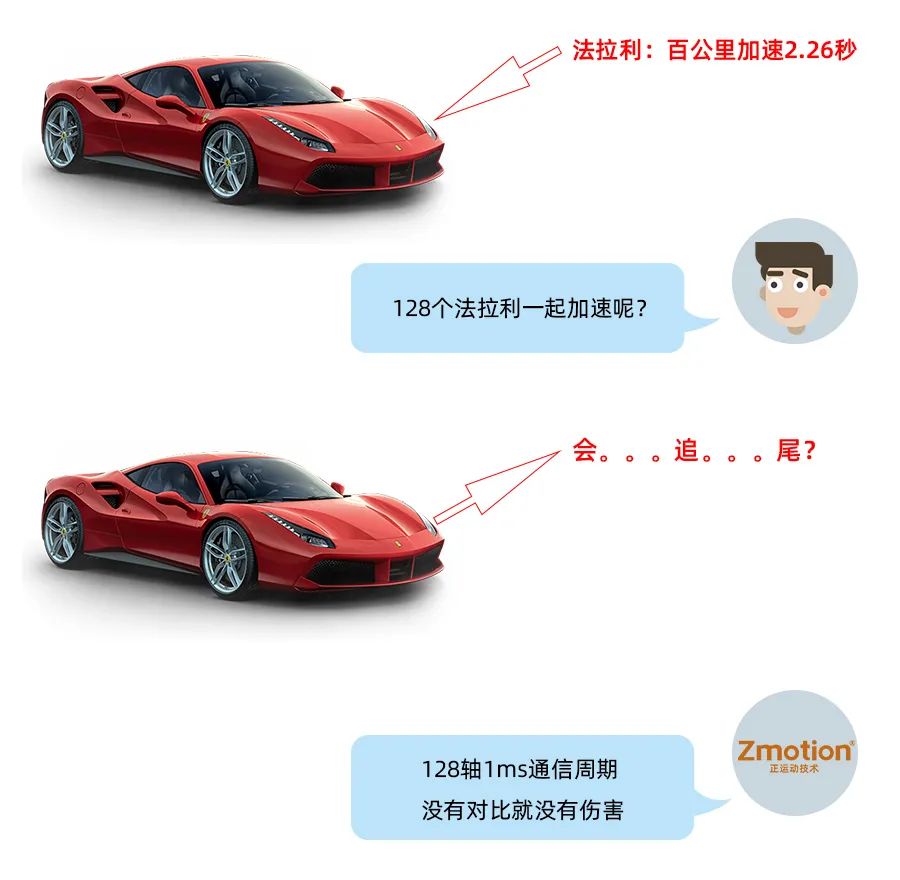
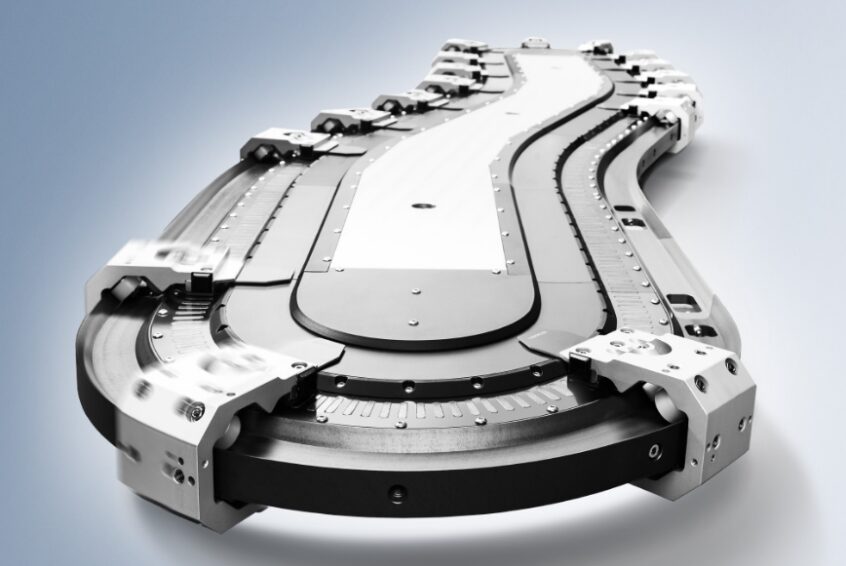
For more exciting content, please follow the “Motion Control Assistant” public account. For related development environments and example codes, please consult Motion Control Technology sales engineers: 400-089-8936.
Review of Previous Content
Announcement! Fans participating in the “Motion Control System Application and Practice” book giveaway, look here
Book Giveaway! Fully Autonomous IDE’s “Motion Control System Application and Practice”
In the era of industrial Ethernet, how to choose a bus motion controller?
Motion Controller PSO Visual Fly Shooting and Precise Output C++ Development (III): Two-dimensional/Three-dimensional/Multi-axis PSO Output
Motion Controller PSO Visual Fly Shooting and Precise Output C++ Development (II): Multi-axis PSO Equidistant/Cyclic Output
Motion Controller PSO Visual Fly Shooting and Precise Output C++ Development (I): Single-axis PSO
Motion Controller 8-channel PSO Visual Fly Shooting and Precise Output
Windows Real-time Motion Control Soft Core (VII): LOCAL High-speed Interface Testing with Labview
Windows Real-time Motion Control Soft Core (VI): LOCAL High-speed Interface Testing with Matlab
Windows Real-time Motion Control Soft Core (V): LOCAL High-speed Interface Testing with VC6.0
Windows Real-time Motion Control Soft Core (IV): LOCAL High-speed Interface Testing with VB.NET
Windows Real-time Motion Control Soft Core (III): LOCAL High-speed Interface Testing with C++
Windows Real-time Motion Control Soft Core (II): LOCAL High-speed Interface Testing with Qt
Windows Real-time Motion Control Soft Core (I): LOCAL High-speed Interface Testing with C#
Open Laser Galvo Motion Controller: C++ Fast Call Graphics Library Application
Open Laser Galvo Motion Controller: C++ Galvo Correction Method and Implementation
Open Laser Galvo Motion Controller: C++ Rapid Development
Open Laser Galvo Motion Controller (V): ZMC408SCAN Fiber Laser Energy Control
Open Laser Galvo Motion Controller (IV): ZMC408SCAN Galvo Control Fiber Laser Processing
Open Laser Galvo Motion Controller (III): ZMC408SCAN Axis Control Fiber Laser Processing
Open Laser Galvo Motion Controller (II): ZMC408SCAN Laser Interface and Control
Open Laser Galvo Motion Controller (I): ZMC408SCAN Interface and Functions
Motion Controller PSO Position Synchronous Output (III): High-precision Equidistant Two-dimensional Three-dimensional PSO Output
Motion Controller PSO Position Synchronous Output (II): Detailed Explanation of PSO Mode
Motion Controller PSO Position Synchronous Output (I): Hardware Platform and PSO Instruction Introduction
Economic EtherCAT Motion Controller (X): Quick Start to EtherCAT Bus
Economic EtherCAT Motion Controller (IX): Oscilloscope Use
Economic EtherCAT Motion Controller (VIII): Axis Parameters and Motion Instructions
Economic EtherCAT Motion Controller (VII): Motion Buffering
Economic EtherCAT Motion Controller (VI):Data Storage
Economic EtherCAT Motion Controller (V): Multi-task Operation
Economic EtherCAT Motion Controller (IV): ModbusRTU or ModbusTcp Communication with Touch Screen
Economic EtherCAT Motion Controller (III): PLC Implementation of Multi-axis Linear Interpolation and Electronic Cam
Economic EtherCAT Motion Controller (II): ZBasic Implementation of Multi-axis Linear Interpolation Motion
Economic EtherCAT Motion Controller (I): Function Introduction and Application Scenarios
Motion Control + Machine Vision Demo Software Framework (III): Visual Correction + Continuous Interpolation Recipe Editing
Motion Control + Machine Vision Demo Software Framework (II): Mobile Calibration and Shape Matching
Motion Control + Machine Vision Demo Software Framework (I): Mechanical Parameters and Recipe File Management
Motion Control + Machine Vision Demo Software Framework System Overview
Open Laser Galvo + Motion Controller (VI): Dual Galvo Motion
Open Laser Galvo + Motion Controller (V): ZMC408SCAN Controller Hardware Introduction
Open Laser Galvo + Motion Controller (IV): PSO Position Synchronous Output Application in Laser Galvo Processing
Open Laser Galvo + Motion Controller (III): Galvo Correction
Open Laser Galvo + Motion Controller (II): Galvo Filling
Open Laser Galvo + Motion Controller (I): Hardware Interface
Quick Start | Part 21: Introduction to ZHMI Configuration Programming of Motion Controller
Quick Start | Part 21: Custom Communication of Motion Control Technology Motion Controller
Quick Start | Part 20: MODBUS Communication of Motion Control Technology Motion Controller
Quick Start | Part 19: Multi-axis Synchronization and Electronic Cam Instruction Introduction of Motion Control Technology Motion Controller
Quick Start | Part 18: Using Pulse Type Motion Controllers of Motion Control Technology
Quick Start | Part 17: Usage of Multi-axis Interpolation Motion Instructions of Motion Control Technology Motion Controller
Quick Start | Part 16: Quick Start to EtherCAT Bus of Motion Control Technology Motion Controller
Quick Start | Part 15: Introduction to Motion Buffer of Motion Controller
Quick Start | Part 14: Basic Axis Parameters and Basic Motion Control Instructions of Motion Controller
Quick Start | Part 13: Usage of ZDevelop Programming Software of Motion Control Technology Motion Controller
Quick Start | Part 12: Usage of USB Interface of Motion Control Technology Motion Controller
Quick Start | Part 11: Application of Interrupts in Motion Control Technology Motion Controller
Quick Start | Part 10: Characteristics of Multi-task Operation of Motion Controller
Quick Start | Part 9: How to Apply Oscilloscope in Motion Controller?
Quick Start | Part 8: How to Use EtherCAT Bus of Motion Controller?
Quick Start | Part 7: How to Use ZCAN Bus Expansion Module of Motion Controller?
Quick Start | Part 6: How to Apply Data and Storage in Motion Controller?
Quick Start | Part 5: How to Apply Input/Output IO in Motion Controller?
Quick Start | Part 4: How to Communicate with Touch Screen in Motion Controller?
Quick Start | Part 3: How to Develop ZPLC Programs in Motion Controller?
Quick Start | Part 2: How to Develop ZBasic Programs in Motion Controller?
Quick Start | Part 1: How to Upgrade Firmware in Motion Controller?
Configuration and Implementation of EtherCAT and RTEX Driver Axis Return to Zero
Application of G-code in Motion Controllers
Custom G-code Programming Application in Motion Controllers
Offline Simulation Debugging, Accelerating Project Progress!
Usage of 8-axis EtherCAT Axis Expansion Module EIO24088
Demo of Motion Controller Following Cutting Application
Configuration and Implementation of Axis Return to Zero in Motion Controllers
Application of Position Latching Function in Motion Controllers
Quick Start for ZMC Motion Controller SCARA Robot Application
Quick Start for RTEX Bus Usage in Motion Controllers
Usage Method of Motion Control Technology CAD Mapping Software with Controllers
Advanced Applications of EtherCAT Bus Motion Controllers
Development Tutorial of EtherCAT Motion Control Card with Qt (Middle): Continuous Trajectory Processing, Pause and Continue
Development Tutorial of EtherCAT Motion Control Card with Qt (Upper): Development Environment Configuration and Simple Motion Control Application
Development Tutorial of EtherCAT Motion Control Card with Python
Application of EtherCAT Motion Control Card with SCARA and Other Robots
PWM and Analog Output of EtherCAT Motion Control Card and Motion Speed Synchronization
Hardware Comparison Output of EtherCAT Motion Control Card and Encoder Latching
IO Actions and Motion Control Synchronization of EtherCAT Motion Control Card
Real-time Program Operation and Read/Write Control of EtherCAT Motion Control Card
Motion Pause, Resume and System Security Settings of EtherCAT Motion Control Card
Continuous Interpolation Motion of EtherCAT Motion Control Card with Small Line Segment Prediction
Multi-axis Interpolation Motion and Hand Wheel Motion of EtherCAT Motion Control Card
Auxiliary Debugging Tools and Methods of EtherCAT Motion Control Card
Axis Parameter Settings and Axis Motion of EtherCAT Motion Control Card
Hardware Wiring of EtherCAT Motion Control Card and C# Hardware Peripheral Read/Write and Return to Zero Motion
Hardware Wiring of EtherCAT Motion Control Card and C# Single-axis Motion Control
Simple and Easy-to-use Motion Control Card (XVI): Pitch Compensation and Backlash Compensation
Simple and Easy-to-use Motion Control Card (XV): Real-time Program of PC Start/Stop Controller
Simple and Easy-to-use Motion Control Card (XIV): PWM, Analog Output and Motion Control Synchronization
Simple and Easy-to-use Motion Control Card (XIII): IO Actions and Motion Control Synchronization
Simple and Easy-to-use Motion Control Card (XII): Safety Settings of Motion Control System
Simple and Easy-to-use Motion Control Card (XI): Motion Pause, Resume and Speed Ratio Settings
Simple and Easy-to-use Motion Control Card (X): Continuous Interpolation and Small Line Segment Prediction
Simple and Easy-to-use Motion Control Card (IX): Circular Interpolation and Spiral Interpolation
Simple and Easy-to-use Motion Control Card (VIII): Linear Interpolation and Hand Wheel Motion
Simple and Easy-to-use Motion Control Card (VII): Loading Multiple Continuous Small Line Segment Data at Once
Simple and Easy-to-use Motion Control Card (VI): Basic File Download and Continuous Trajectory Processing
Simple and Easy-to-use Motion Control Card (V): IO Configuration and Return to Zero Motion
Simple and Easy-to-use Motion Control Card (IV): Function Library Packaging
Simple and Easy-to-use Motion Control Card (III): Axis Parameter Configuration and Single-axis Motion Control
Simple and Easy-to-use Motion Control Card (II): Peripheral Read/Write and ZDevelop Diagnosis
Simple and Easy-to-use Motion Control Card (I): Hardware Wiring and Upper Computer Development
Application of Motion Control Card in ROS (Lower)
Application of Motion Control Card in ROS (Upper)
Building Intelligent Equipment with EtherCAT Motion Control Card and LabVIEW (V)
Building Intelligent Equipment with EtherCAT Motion Control Card and LabVIEW (IV)
Building Intelligent Equipment with EtherCAT Motion Control Card and LabVIEW (III)
Building Intelligent Equipment with EtherCAT Motion Control Card and LabVIEW (II)
Building Intelligent Equipment with EtherCAT Motion Control Card and LabVIEW (I)
Motion Control Card in LabVIEW for Motion Control and Data Acquisition
Application Development Tutorial of Motion Control Card with MATLAB
Application Development Tutorial of Motion Control Card with C++
Application Development Tutorial of Motion Control Card with Python
Application Development Tutorial of Motion Control Card with C#
Application Development Tutorial of Motion Control Card with Linux
Application Development Tutorial of Motion Control Card with VB.NET
Application Development Tutorial of Motion Control Card with VB6.0
Application Development Tutorial of Motion Control Card with VC6.0
Application Development Tutorial of Motion Control Card with Qt
Application Development Tutorial of Motion Control Card with LabVIEW
Application Development Tutorial of Motion Control Card for Laser Galvo Control
Application Development Tutorial of Motion Control Card for Hardware Comparison Output
About Motion Control Technology
Motion Control Technology focuses on research in motion control technology and the development of general motion control software and hardware products, is a national high-tech enterprise, with main products including motion controllers, motion control cards, visual motion control integrated machines, human-machine interfaces, and expansion modules..
Motion Control Technology gathers excellent talents from companies like Huawei and ZTE, actively collaborates with major universities to research basic technologies in motion control while adhering to independent innovation, making it one of the fastest-growing companies in the industrial control field in China, and one of the few companies that fully master core motion control technologies and real-time industrial control software platform technologies.
Motion Control Technology is backed by the booming manufacturing industry, keeping pace with the times, rich in innovation, dedicated to continuously enhancing technical applications and manufacturing levels for intelligent manufacturing equipment suppliers and end users. After years of application development with numerous partners, products are widely used in domestic and foreign fields such as 3C electronics, semiconductors, printing and packaging, textiles and garments, laser processing, mechanical processing, robotics, new energy, healthcare, and stage entertainment.
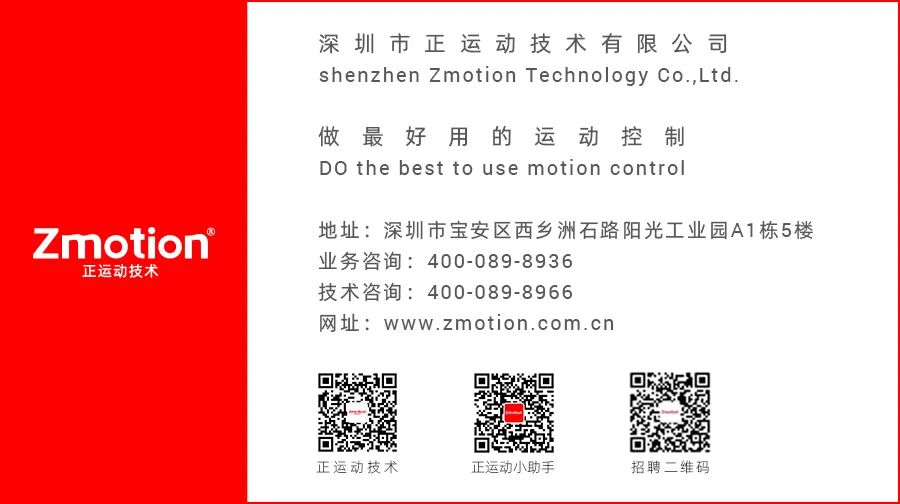