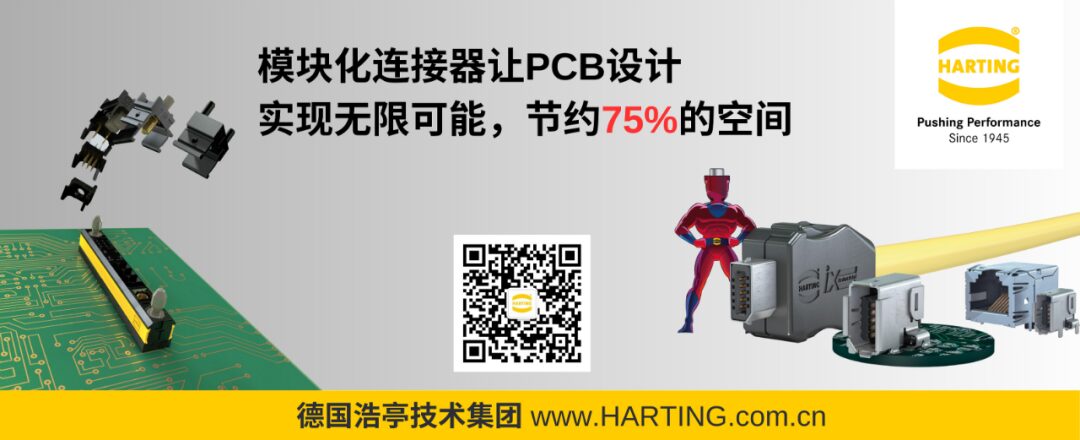
For more information about HARTING products, please click at the bottom of the article“Read the original text”to get it
Technical communication, click here to join the group

The 20-Year Development History of EtherCAT Technology
Since its launch, EtherCAT has a history of over 20 years, and its success continues to this day. Indeed, EtherCAT communication system, developed by Beckhoff and first showcased at the Hannover Messe in 2003, has been proven through practice as a high-performance real-time Ethernet solution widely applied globally, establishing its market position through the continuity of its technological development, further becoming an open IEC standard. In this interview, Hans Beckhoff and Martin Rostan mainly recount the exciting moments of this technology in the company’s history, while Johannes Beckhoff, representing the next generation of management at Beckhoff, focuses more on future demands.
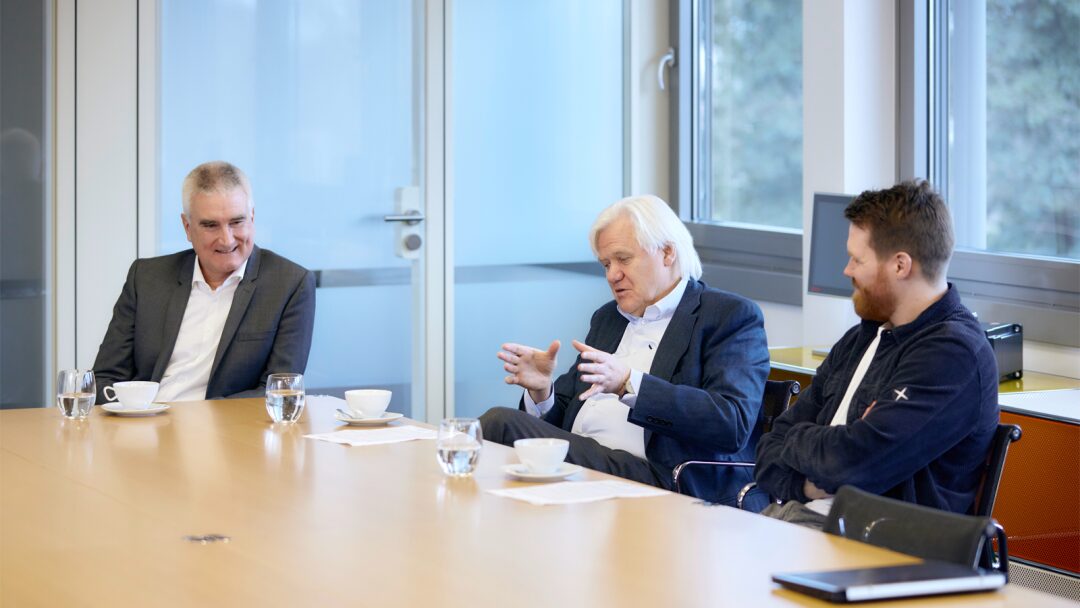
Hans Beckhoff (middle) and Martin Rostan (left) review the development of EtherCAT technology over the past 20 years and share their accumulated experiences with Johannes Beckhoff (right), representing the next generation of management.
As early as 1989, Beckhoff first launched the Lightbus high-performance bus system. So, what considerations did you have when developing the new EtherCAT communication system later?
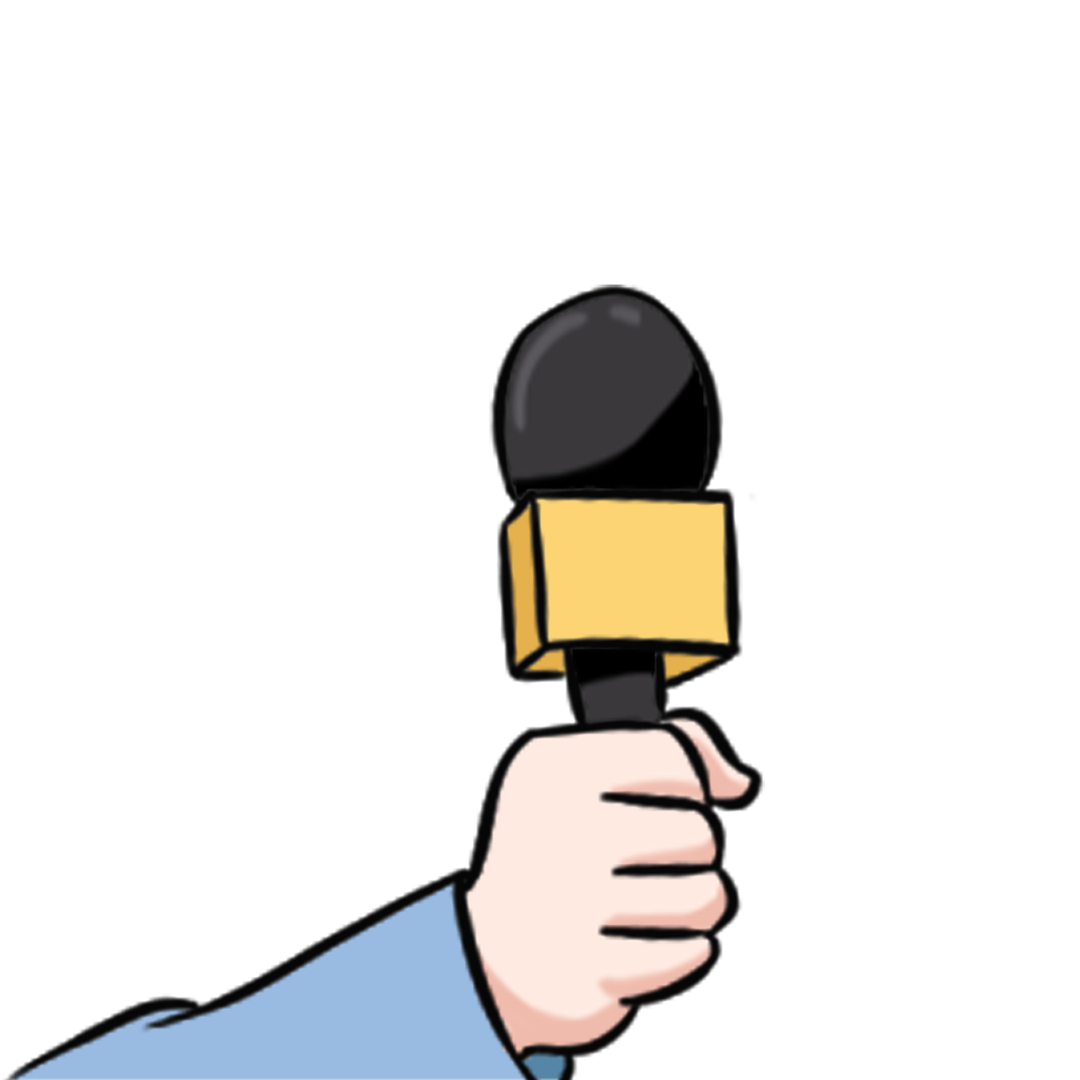

Hans: Beckhoff has always focused on the development of high-performance control solutions and continues to break through the performance limits in the field of automation. This is all based on the PC control technology concept, which allows us to leverage all the advantages of PCs, including high computing power, thereby benefiting machines. In terms of data communication, we launched the excellent Lightbus solution in 1989. By the early 21st century, Ethernet interfaces became the mainstream trend, and the first processors with integrated Ethernet interfaces began to enter the market. The development of EtherCAT enabled us to use this new IT data transmission medium on devices, aligning with our concept of integrating IT technology with automation technology. We have extensive application experience with Lightbus and other fieldbuses such as CANopen and PROFIBUS, and we integrated all these experiences into our R&D philosophy, which significantly contributed to EtherCAT’s later success.
Martin: Our initial intention for developing EtherCAT was that Lightbus and other fieldbuses, as well as the first industrial Ethernet technologies, could not keep up with the increasing performance of PCs. At that time, the control structures were all distributed, making them very complex. On the other hand, PC-based control technology primarily used centralized control methods, which required corresponding high-performance communication technologies. EtherCAT bridged this gap and broke the previous data communication bottlenecks, and 20 years later, everything remains the same.
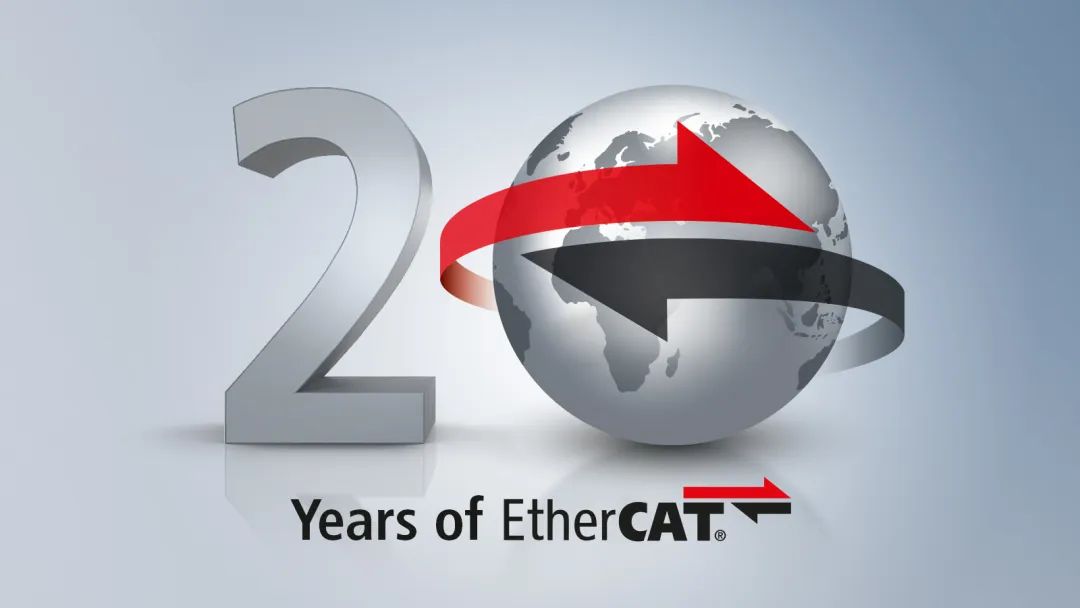
With Ethernet and the subsequent hundred-megabit data transmission rates, the tenfold increase in transmission speed has greatly benefited control technology. At that time, networks based on RS485 and CAN were generally good, but they were limited in bandwidth and performance.
—— Hans Beckhoff
When developing this technology based on industrial application needs, which aspects of Ethernet are particularly important?
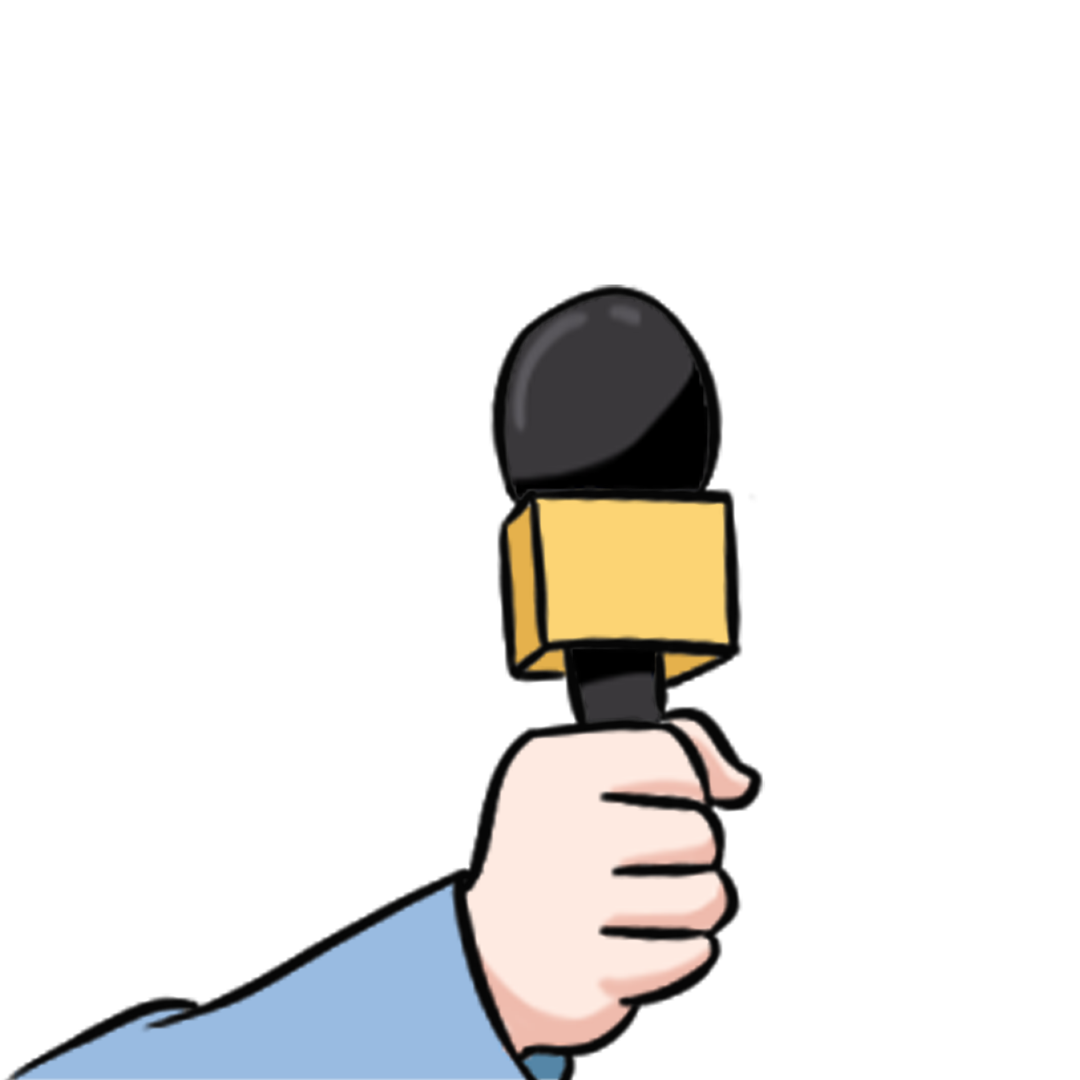

Hans: Standard Ethernet protocols are designed for transmitting large amounts of data and long data packets, not the small amounts of information commonly found in machines—such as a 1-bit limit switch value or a 16-bit analog value. Therefore, our task is to combine the hundred-megabit data transmission rate with the 1…16-bit data transmission applications in the automation field, which can only be achieved through EtherCAT. We not only completely redefined the required technical principles but also integrated them into the EtherCAT protocol and EtherCAT hardware.
Martin: We adopted the basic principle of message processing from Lightbus, “processing on the fly,” and elevated data communication to a whole new level. We also made reasonable use of the new Ethernet technologies that were already popular in the field of automation, skillfully avoiding the main bottlenecks of Ethernet for real-time communication.
The key factor for success is the high efficiency of the EtherCAT protocol, with bandwidth utilization exceeding 90%. Equally important is that the complexity of the protocol is fully mapped to the hardware, significantly simplifying the EtherCAT implementation process for device manufacturers.
—— Martin Rostan
In summary, what are the basic advantages of EtherCAT?
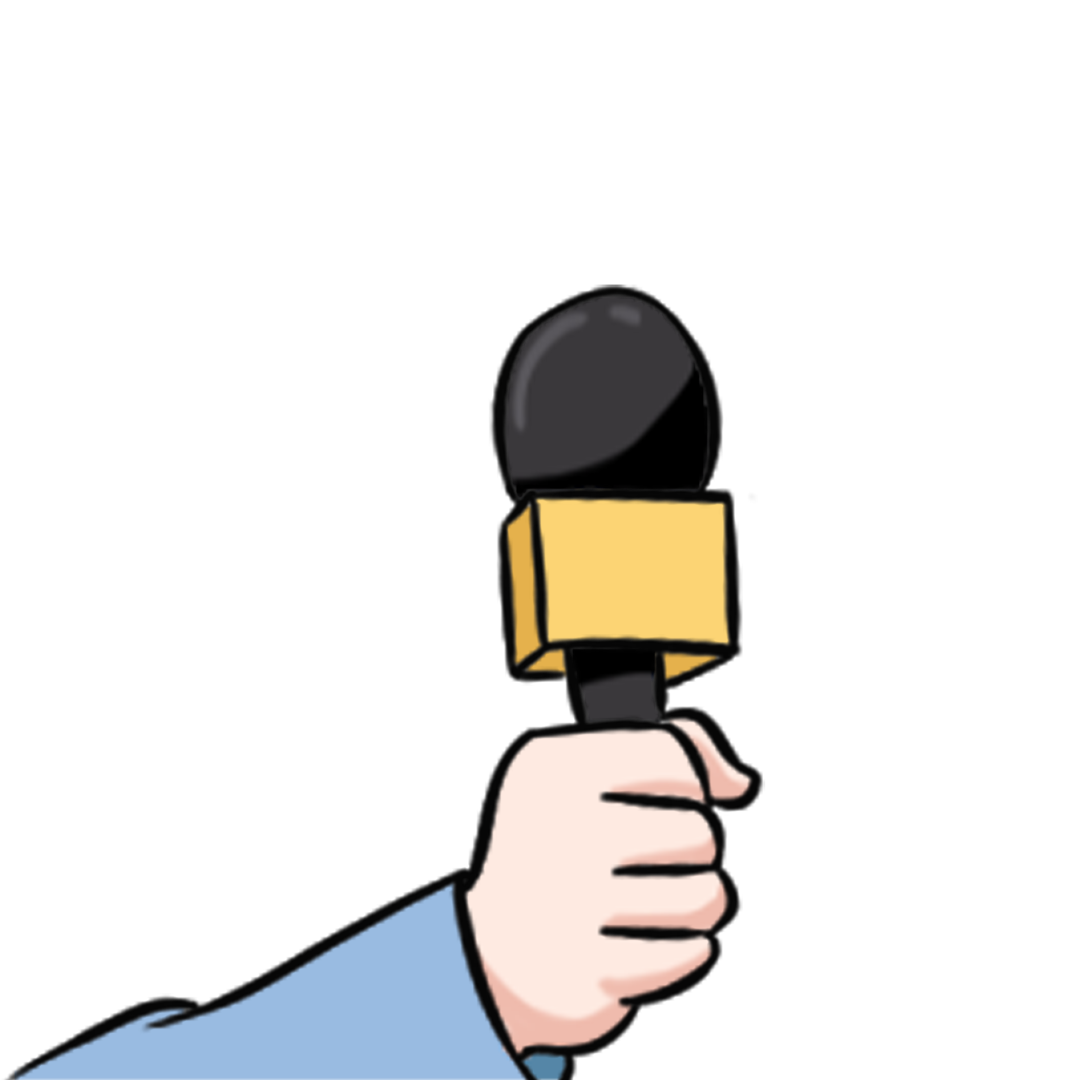

Hans: First of all, traditional fieldbuses based on RS485 and CAN are merged buses, characterized by multiple devices using the same link, making network diagnostics and troubleshooting much more complex. In contrast, EtherCAT uses Ethernet point-to-point links, allowing for accurate diagnosis of each transmission path, which is a significant functional advantage. We also decided early on that we could use standard Ethernet packets, so the master device does not require a dedicated communication card, which remains a major advantage of EtherCAT. However, the most critical advantage is the protocol efficiency we just mentioned, which allows data to be extracted or added in real-time to Ethernet packets ranging from 64 to 1500 bytes. In a network with many automation devices, where each device has a small amount of data, this is the only way to ensure efficient and continuous use of high bandwidth; a packet can even carry data from over 65,000 devices on the same network.
Martin: This operating principle brings another advantage: the controller can perfectly compile the process image in the data packet, as any node in the network can insert or remove its data at any time. This avoids the complex bit manipulation required by other systems through interface cards. On the other hand, EtherCAT masters do not affect the controller because the logical process image can be processed directly. Therefore, EtherCAT is not only faster due to its shorter communication cycles but also highly efficient in data exchange on both the slave and master sides.
Hans: Indeed. This operating principle is based on the memory management unit functionality used in the IT field; for this purpose, we further developed the Fieldbus Memory Management Unit (FMMU). FMMU is one of the fundamental functions of EtherCAT, allowing data to be read from distributed memory and written to memory in an “on the fly” manner. Thus, data in physical devices can be mapped to data in active packets in any form. Moreover, individual tasks and processor cores can also be mapped via FMMU and define corresponding time levels to meet the advanced task-based control technology requirements. Another core function of EtherCAT is the distributed clock, which introduces a deterministic, automatically synchronized system time for the communication system. This is crucial because modern control schemes are almost all based on time slices, needing synchronized sampling points for data and signals. Such a complete concept of a distributed clock was absent in previous fieldbuses.
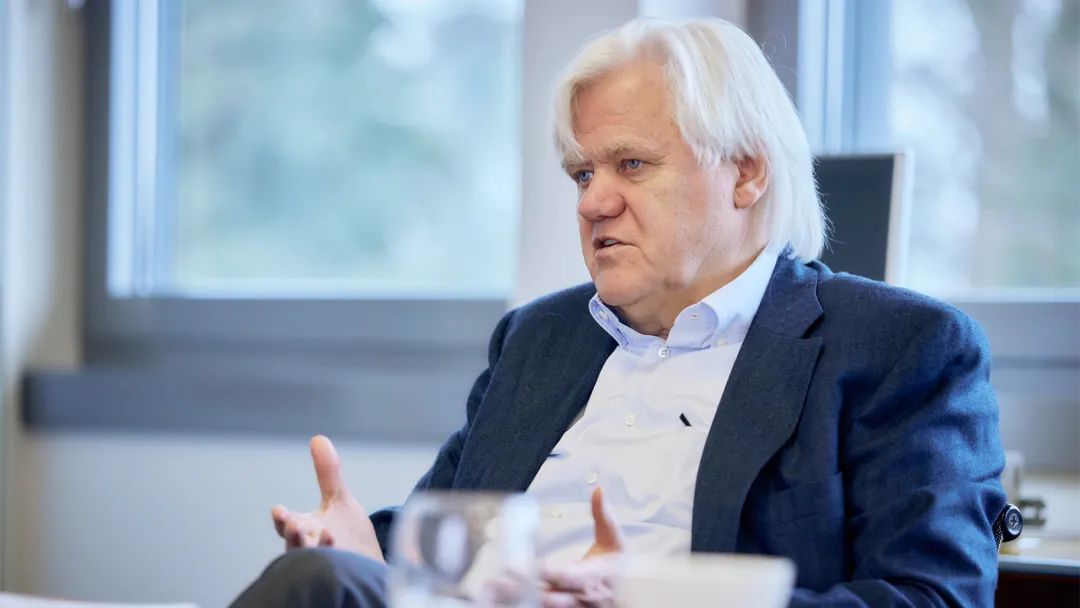
The Fieldbus Memory Management Unit (FMMU) is one of the fundamental functions of EtherCAT, allowing data to be extracted from distributed memory and written in an “on the fly” manner.
—— Hans Beckhoff
Does the market recognize these fundamental advantages of EtherCAT?
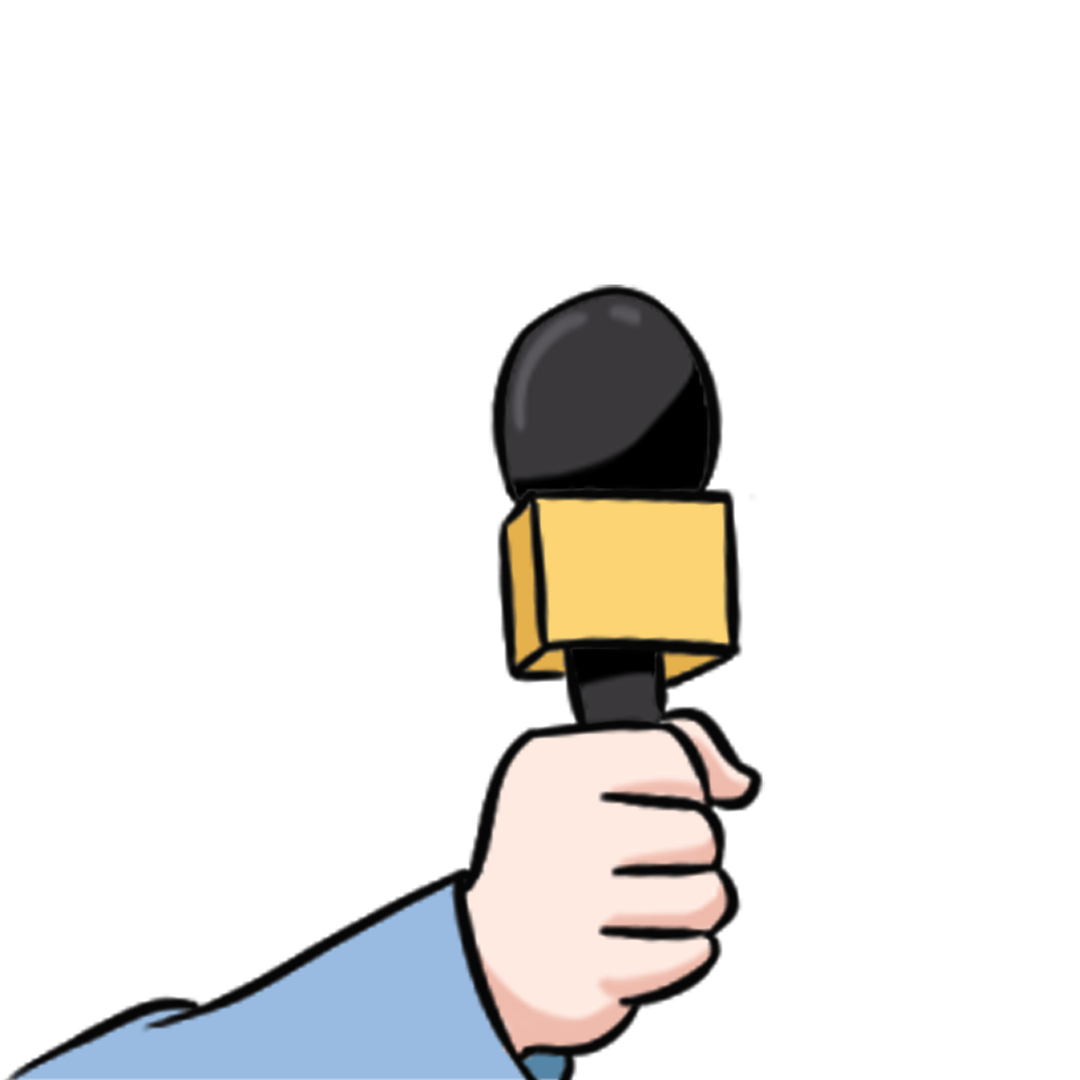

Hans: Indeed! All these advantages combined form a technology that is essentially logical, easily understood, and deeply loved by engineers worldwide. This rather intuitive aspect is certainly one of the reasons EtherCAT has established its market position globally.
Johannes: I completely agree with this, although I personally did not experience the early development of EtherCAT technology. EtherCAT is essentially a high-performance yet simple and rational protocol. Without understanding other communication systems, I asked myself: EtherCAT is obviously the best solution; how else can we use industrial Ethernet?
Martin: Yes, at that time we even created the phrase “EtherCAT is the best choice for engineers”! This phrase summarizes it well: EtherCAT was, and still is, a more compelling technology compared to previous systems, making it easy to prove its rationality from a technical perspective.
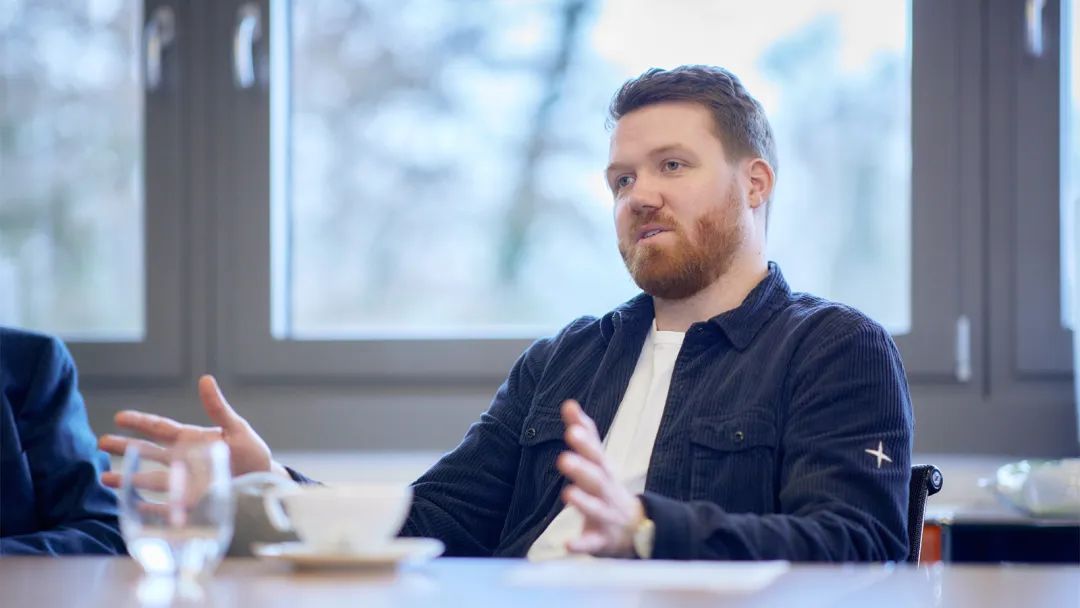
Johannes Beckhoff is Hans’s son and joined Beckhoff Automation in 2019. His major in university was also Physics (Master’s), and he is currently engaged in basic research and development, helping shape the future of PC-based control technology.
What significant importance did the presentation of EtherCAT at the 2003 Hannover Messe hold for Beckhoff at that time? How was the market response?
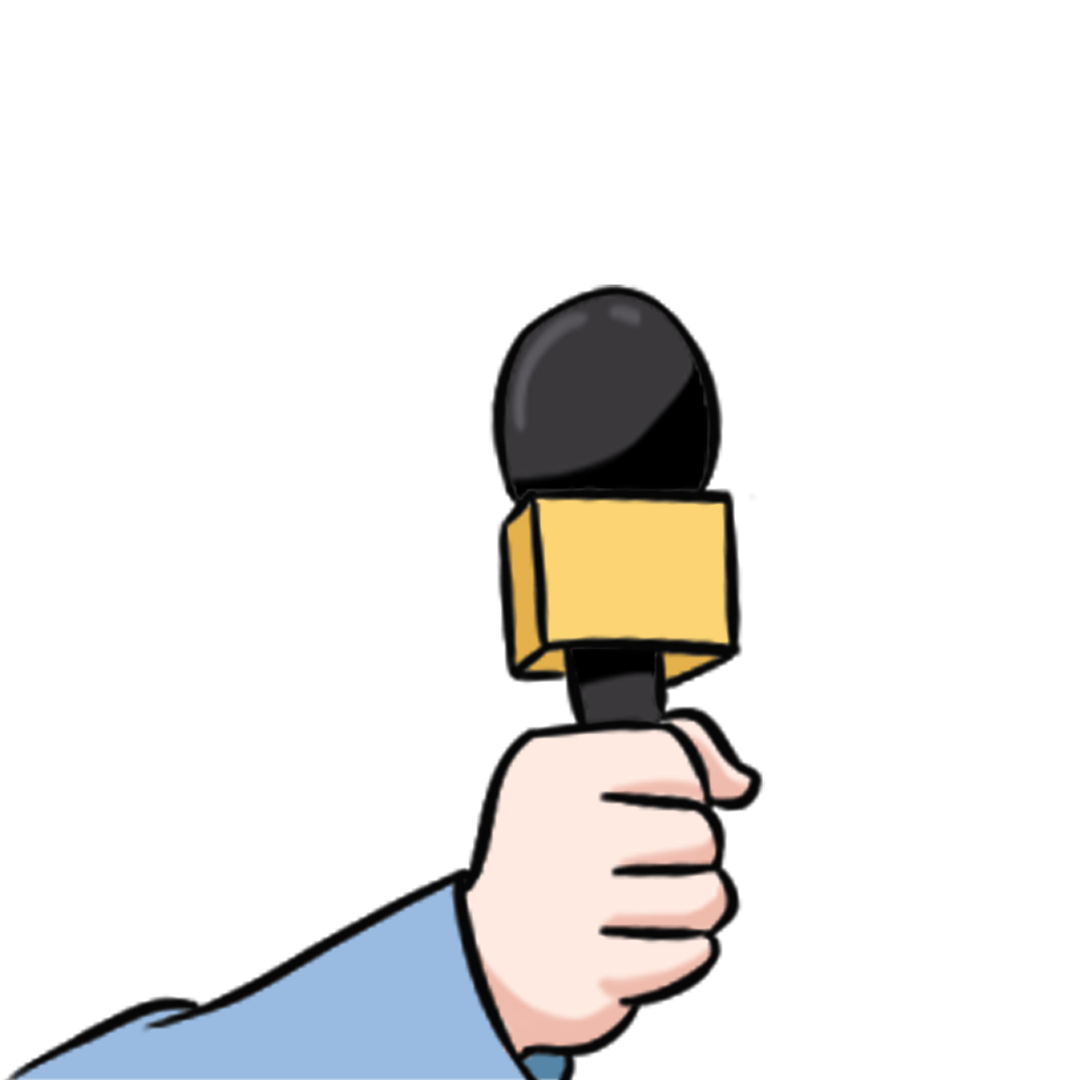

Hans: This was undoubtedly a particularly significant event for the R&D team. Our core team, consisting of six experts, felt proud of it. We set up a 4-meter-long giant display at our booth to maximize the demonstration effect of EtherCAT technology principles, even using an oscilloscope to showcase its real-time performance. Everything went smoothly from the start to the end of the exhibition, and customers were as enthusiastic as we expected. Clearly, visitors from other fieldbus organizations and control component suppliers were deeply impressed by EtherCAT, at least that’s what I felt from the shocked silence and pale faces at that time!
Martin: Indeed, I remember one of our competitors left our booth with a pale face and without even saying hello. That’s the effect we aimed to achieve. Everyone who understood EtherCAT technology immediately showed great enthusiasm and recognized it as the best way to utilize industrial Ethernet.
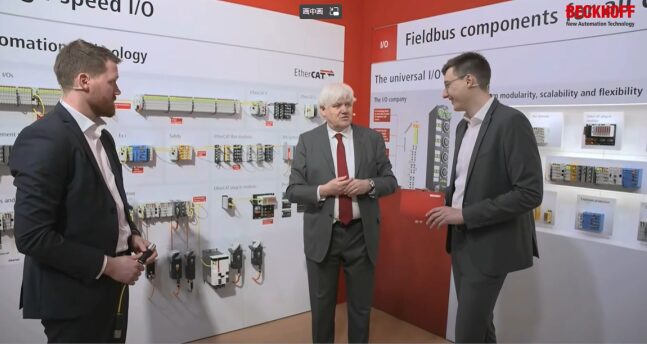
The EtherCAT display area at the 2023 Hannover Messe.
One of the main factors for EtherCAT’s success was the announcement of the open EtherCAT protocol and the establishment of the EtherCAT Technology Group (ETG) at the 2003 Nuremberg International Industrial Automation Exhibition. Why did Beckhoff choose this timing to announce to the market?
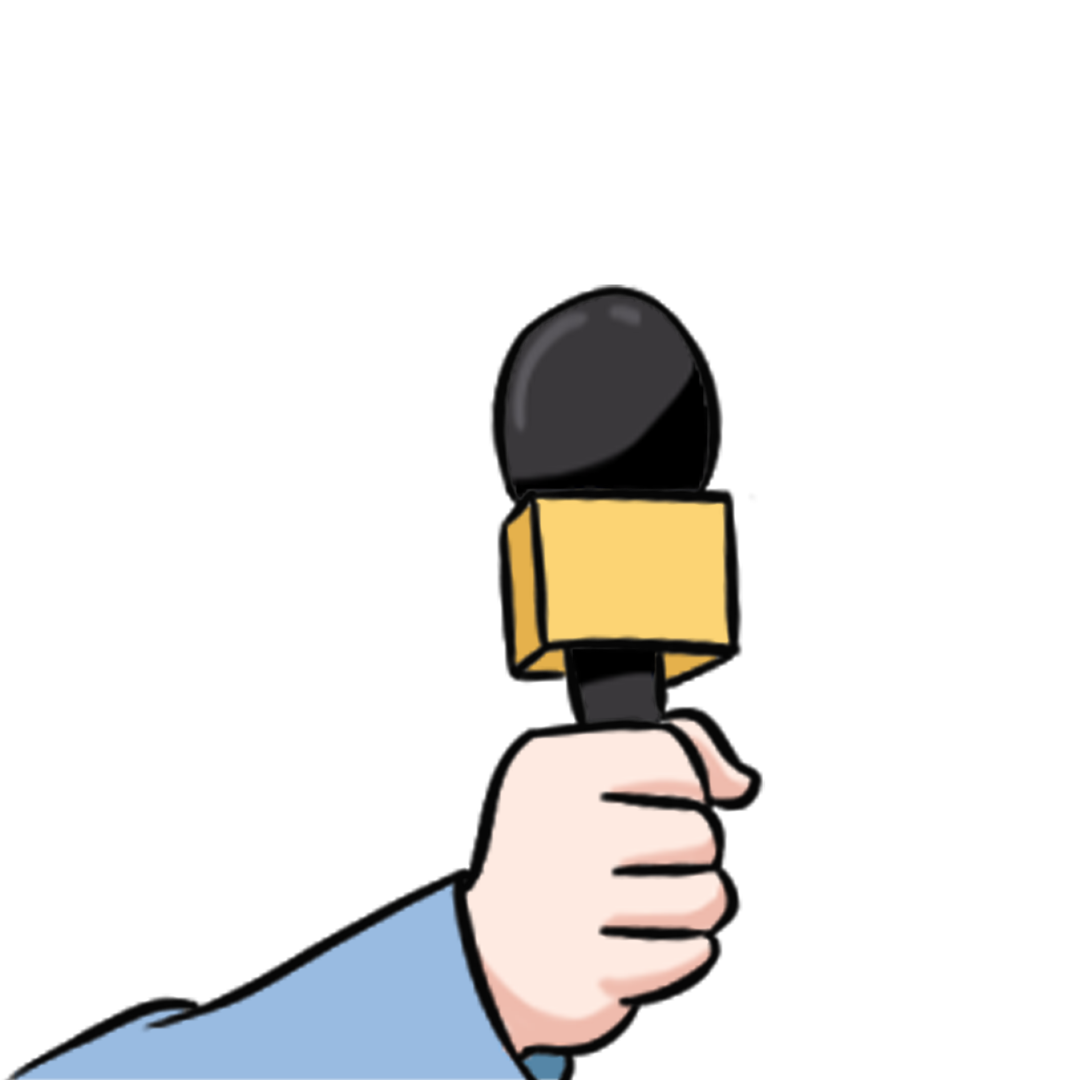

Hans: Undoubtedly, the establishment of ETG, just like the advanced nature of the technology, has made an important contribution to our success. ETG was founded by Martin and is now an independent organization promoting EtherCAT technology globally. Without ETG, EtherCAT might still be an exciting technology with some followers but would never have become a globally recognized standard that has won widespread acclaim.
Martin: Beckhoff has always advocated for open technology and supported all relevant open fieldbus technologies. At that time, there were about 20 different communication technologies and industry-specific variants on the market, and Beckhoff had corresponding technical experts in all these technologies. ETG drew on the strengths and weaknesses of these technologies and various user organizations. Again, in terms of openness, ETG members greatly appreciated the management approach to EtherCAT technology development: Beckhoff is the driving force behind technological innovation, but always considers the needs of all partners when developing new features for the technology. The principles of open fieldbus organizations have been well validated here.
ETG has now become the world’s largest industrial fieldbus user organization, with over 7,000 member units from 72 countries around the globe, of which over 40% are members from Asia. Only 14% of the members are from the Americas, making it the largest fieldbus organization in the Americas. The availability of EtherCAT is also very important, so device manufacturers and end-users have been involved from the beginning.
—— Martin Rostan
Although EtherCAT has been around for 20 years, it is by no means outdated. Why is it still the world’s largest industrial communication system even today?
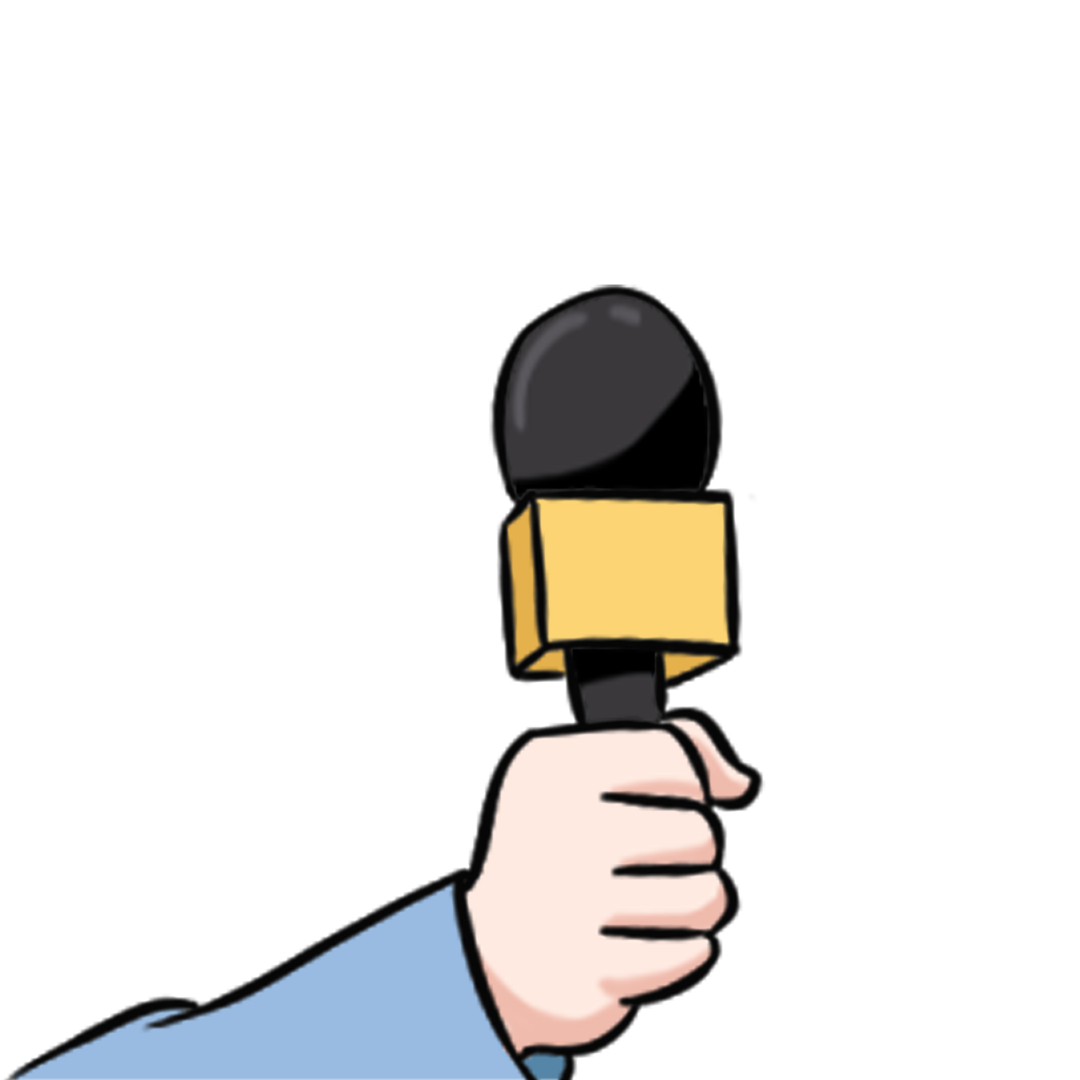
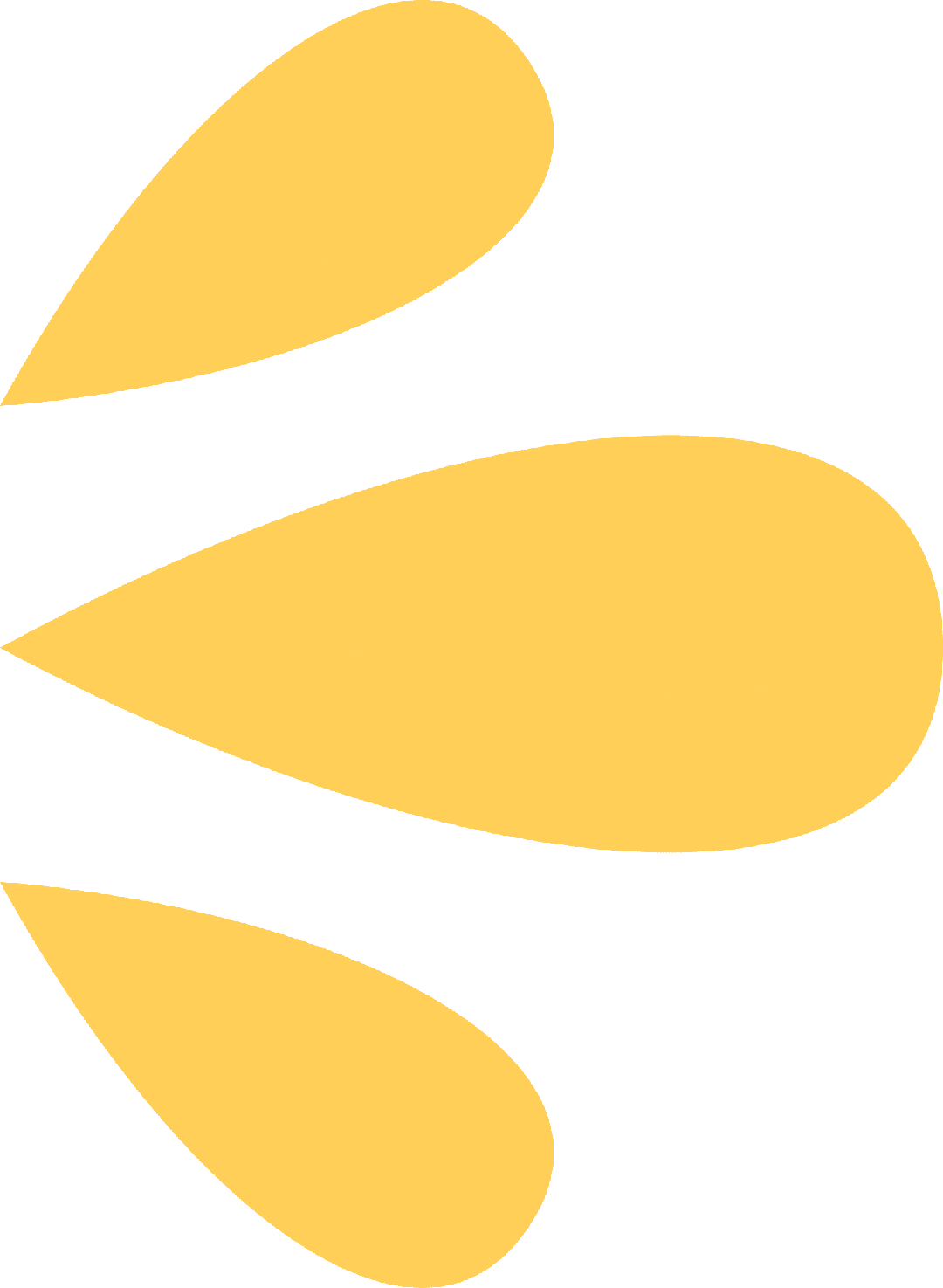
Hans: Over the past 20 years, this technology has fully proven its perfect design, and the basic protocol has remained unchanged without any modifications. This is the key to our success. In addition, we have applied EtherCAT technology principles to other application layers, such as the EtherCAT Automation Protocol (EAP) for inter-controller communication. We have even introduced EtherCAT G/G10 with transmission rates of up to 1 Gbit/s and 10 Gbit/s, which means that the EtherCAT protocol also supports higher transmission rates.
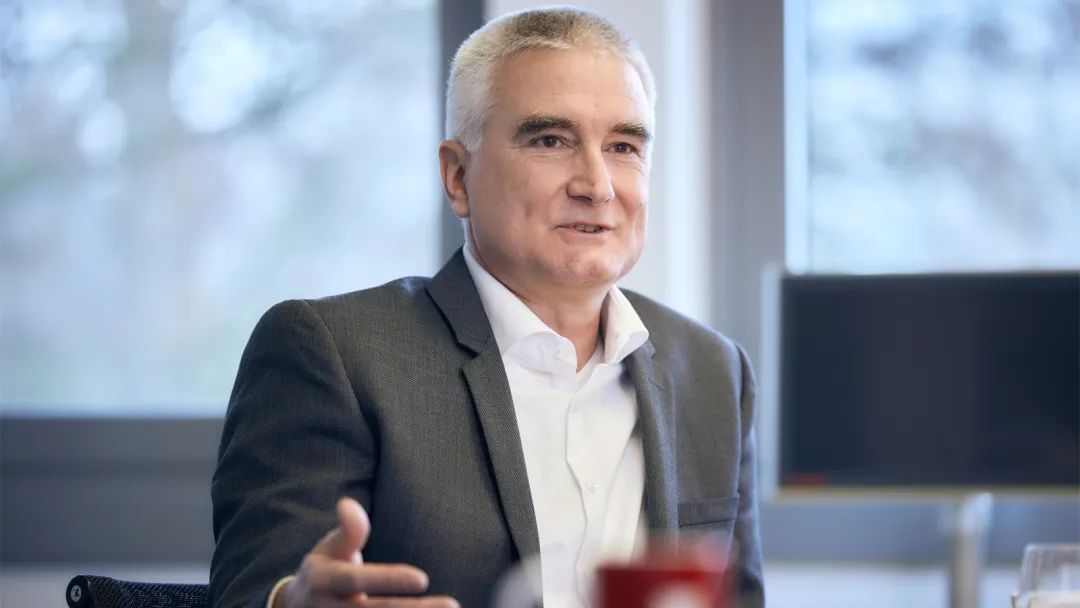
One of EtherCAT’s unique selling points is that the technology itself has remained unchanged over the years. The basic protocol contained in the chip has always remained the same and has been expanded in a fully backward-compatible manner, including Safety over EtherCAT.
—— Martin Rostan
Martin: EtherCAT G networks can even integrate and run hundred-megabit EtherCAT devices.This means that today’s EtherCAT devices can directly operate in a 20-year-old system.This also means that EtherCAT technology in the control architecture will not face bottlenecks, and this fact alone is enough to make many users choose this fieldbus.The vast majority of applications can still use hundred-megabit rates;while EtherCAT G has enough potential to easily meet all high-end demands for the next 20 years without any technological gaps.
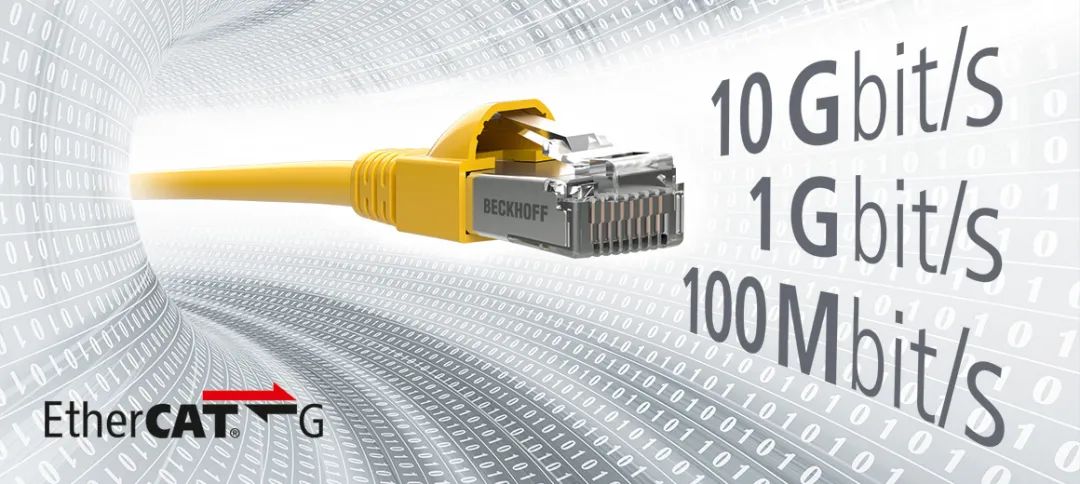
The ETG Technical Committee has accepted EtherCAT G as a supplement to the EtherCAT standard.
Johannes: I must agree with Martin: hundred-megabit rates are sufficient to meet the requirements of most devices, even with cycle times of less than 1 ms. EtherCAT G supports high data-intensive applications such as XPlanar or vision, capable of transmitting thousands of bytes of data within cycle times of less than 1 millisecond. Without EtherCAT G, the scale of XPlanar systems would be limited to 20 planar modules, making it impossible to develop truly large XPlanar systems. Gigabit rates can now achieve systems equipped with more than 100 planar modules. This also applies to the XTS magnetic drive flexible conveying system, which performs excellently at hundred-megabit rates, but would be impossible without the efficient EtherCAT protocol. This is because the system must transmit thousands of bytes of data within an extremely short cycle of 250 μs. Other communication systems cannot achieve this, requiring a complex distributed control architecture to achieve similar systems.
Hans: And it is precisely our centralized control solution that allows us to calculate the entire process’s mathematical and physical model on the same CPU. Its operation is fundamentally similar to that of a human being, where the human brain receives all data from various parts of the body through the central nervous system. The subprograms inside the brain are modular structures and can efficiently control the movements of various parts of the body. Our automation technology is based on the same principle, so EtherCAT corresponds to the central nervous system of the machine, allowing as much peripheral data as possible to be quickly delivered to the central control system. Beckhoff’s success as an automation supplier is largely due to our pursuit of this approach: the “trilogy of technology” of PC technology, EtherCAT, and centralized control concepts.
What are the current and mid-term focuses of EtherCAT development?
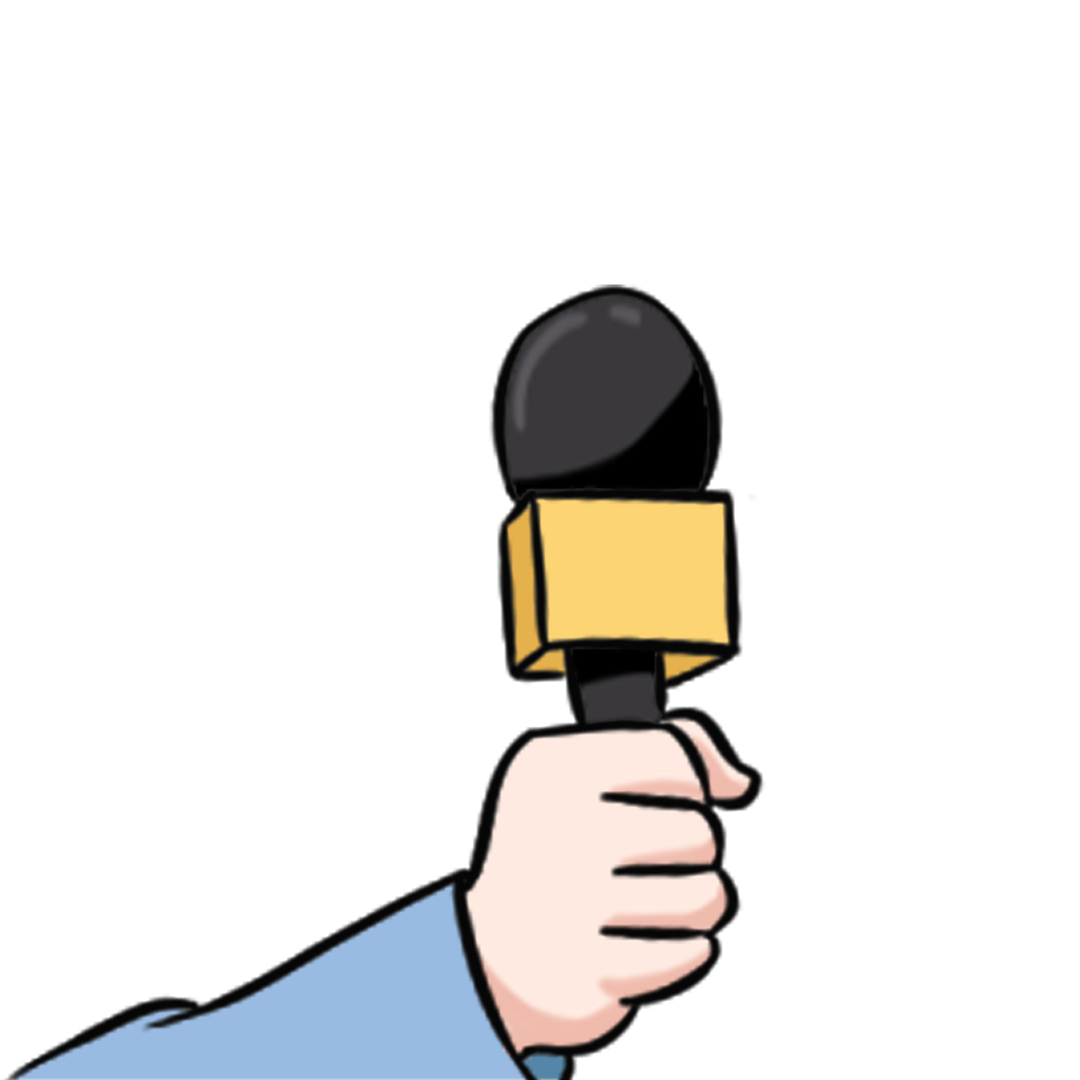

Hans: As an Ethernet-based system, EtherCAT and EtherCAT products will continue to closely follow the development of market hardware layers. Even today, Beckhoff has designed multiple couplers for RJ45, M8, and plastic and fiber optic cables, and will further expand based on other physical transmission types emerging in the market. Another important development step is the introduction of hybrid connector products for single-cable solutions. This is also the reason why we developed EtherCAT P, which integrates EtherCAT communication with power supply in a standard four-core Ethernet cable. In this context, another particularly exciting development outcome is the EtherCAT P hybrid connector series, with sizes of B12, B17, B23, and B40, which will be included in the IEC standard as the standard circular connector for future distributed automation.
We initially positioned EtherCAT as a communication protocol and utilized the complete physical characteristics of Ethernet hardware. We also developed the electromechanical functionalities required for automation to make the system more practical. In this case, EtherCAT P and the EtherCAT P connector series represent a significant technological advancement.
—— Hans Beckhoff
Martin: Information security is becoming increasingly important in the field of automation.EtherCAT has many advantages in safety, as its system structure and characteristics have provided all the intrinsic conditions to address these challenges.Moreover, it is worth mentioning that EtherCAT does not require new protocol versions, hardware modifications, or special measures to conduct any safety-related communication.
大家都在看
【视频】德国工程师是如何制作PLC柜的?
【视频】德国威图电气柜是如何生产出的?
【视频】德国工程师的办公环境是怎样的?
【视频】PROFINET为何比PROFIBUS牛?
回复“V18”获取博途最新版全家桶(含授权)