Testing Standards, Testing Solutions, Testing Tools
|
Ethernet, like LIN, is a product of competition in the automotive communication field, alongside the CAN bus.
In specific areas, the former two are more suitable than the CAN bus. If we set aside R&D costs and focus solely on technical reasoning, the existence of both is justified.
Standard Ethernet technology uses four pairs of unshielded twisted pairs to transmit data, requiring eight wires. In contrast, vehicle Ethernet can operate with a single pair, using just two wires.
Compared to standard Ethernet, it is better suited to vehicle environments, meeting the automotive industry’s requirements for high reliability, low electromagnetic radiation, low power consumption, bandwidth allocation, low latency, and synchronous real-time performance.
The automotive industry has increasingly stringent requirements for reliability and safety. To ensure the reliability and safety of vehicle Ethernet during application, there is an urgent need to conduct testing.
There are certain differences between traditional Ethernet testing and vehicle Ethernet testing, so traditional Ethernet testing methods are not suitable for automotive Ethernet testing.
The automotive industry has higher testing requirements, thus necessitating the establishment of vehicle Ethernet testing standards by relevant organizations or alliances.
Currently, the commonly used vehicle Ethernet testing methods reference the TC8-OPEN Alliance Automotive Ethernet ECU Test Specification and TC-11 Ethernet Switch Test Specification. The testing content mainly includesphysical layer testing, vehicle Ethernet switch testing, and consistency testing of protocol and application layers excluding AVB/TSN.
Vehicle Ethernet physical layer testing mainly includes two aspects: PMA (Physical Media Attachment) testing and IOP (Interoperability) testing. The purpose of physical layer testing is to ensure the interconnection performance of ports and to detect whether the signals sent or received by the transmitter and receiver comply with automotive communication standards.
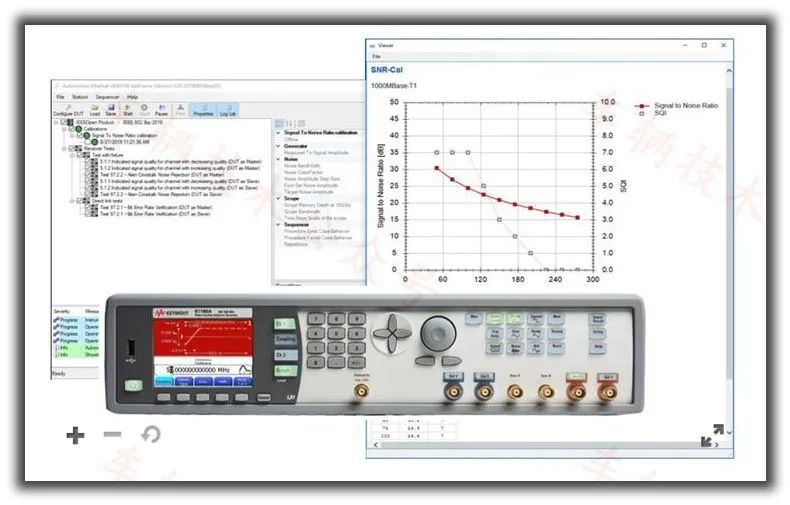
PMA (Physical Media Attachment) mainly evaluates the electrical characteristics of vehicle Ethernet. Regarding PMA testing, the OPEN Alliance released the “BroadR-Reach Physical Layer Transceiver Specification For Automotive Applications V3.2” standard in June 2014, defining the electrical specifications of BroadR-Reach’s PMA. In the OPEN TC8 specification, the testing content mainly includes six conventional testing items: transmission attenuation, transmission distortion, transmission clock jitter (Master & Slave), transmission power spectral density, transmission clock frequency, MDI return loss, and other testing items: MDI mode transition loss, common mode radiation, etc.
In the testing process, the instruments required include oscilloscopes, vector network analyzers, analysis software, fixtures, etc.
During the testing process, to complete different testing items, the DUT PHY needs to be set to different test modes by modifying registers, allowing it to send specific data packets. BroadR-Reach defines four test modes.1) Test mode 1-Transmit droop test mode.2) Test mode 2-Transmit jitter test in MASTER mode. 3) Test mode 4-Transmit distortion test.4) Test mode 5-Normal operation at full power (for the PSD mask).
Vehicle Ethernet physical layer IOP testing, or interoperability testing, is used to verify the reliability of vehicle Ethernet PHY (commonly referred to as transceivers) and to check whether the PHY can establish a stable link within a given limited time; it is also used for diagnosing vehicle Ethernet PHY, such as signal quality index (SQI) and detecting wiring faults.
Simulating open and short circuit faults at the far and near ends of vehicle Ethernet as a Link Partner, establishing a connection with the DUT, and obtaining the Link Up time (accuracy up to 1ms), signal quality index, and cable diagnostic information.
The content of IOP testing mainly includes the following items.
1) Wake-up time (Link-up time) Performing multiple power on/off operations on the Link Partner’s PHY, calculating the time required for the DUT to establish a connection with the Link Partner; performing multiple power on/off operations on the DUT, calculating the time required for the DUT to establish a connection with the Link Partner; performing multiple wake/sleep operations on the DUT, calculating the time required for the DUT to establish a connection with the Link Partner.
2) Signal quality Gradually increasing the artificial noise level to obtain the variation curve of the signal quality index SQI; gradually decreasing the artificial noise level to obtain the variation curve of the signal quality index SQI.
3) Wiring diagnostic testing Checking whether the DUT can reliably detect open circuit faults when one or two lines open at the far or near end; checking whether the DUT can reliably detect short circuit faults when short circuits occur at the far or near end.
During the testing process, a Golden Device is used as the Link Partner, and the schematic diagram of the connection is shown below.
Vehicle Ethernet switch testing involves testing the conventional data frame transmission and reception functions of vehicle Ethernet switches. The testing specification mainly follows the TC-11 Ethernet Switch Test Specification standard, and the testing content is as follows.
1) General functions Normal forwarding of data frames, port mirroring, port disabling, handling jumbo frames, reading device ID, and other basic functions.
2) Address resolution functions Address learning, address aging time, address resolution table, address learning configuration mode, and other functions.
3) VLAN functions TPID Ethernet type field free configuration function, double-tag Q-in-Q function, non-tagged data frame support, VLAN hop attack suppression, shared VLAN learning, and other functions.
4) Time-sensitive networking synchronization functions (TSN) Correct handling of received time synchronization frames.
5) Quality of service (QoS) Correct handling of priority traffic and implementation of different traffic shaping strategies, including priority-based quality of service, WRR-based packet forwarding capability, PCP field overriding capability, priority mapping capability, and support for leaky bucket algorithm capabilities.
6) Configuration functions Reconfigurable functions during operation, individually configurable ports, support for starting in “forbidden forwarding” mode before configuration completion, read-back of configuration information, support for locking configuration items, etc.
7) Filtering functions Whether the receiving port can filter received data frames according to settings, including port broadcast protection functions, general filtering requirements, VLAN-related filtering rules, and filtering rules based on upper-layer addresses.
8) Diagnostic functions Whether counters can correctly count diagnostics, feedback functions for cable and connection status diagnostics, etc.
During the testing process, the testing platform can be used as a traffic generator to send different types of data packets. The software on the connected computer configures the types of packets, and the testing results are checked on the software. The computer connected to the DUT also configures the working mode of the DUT.
Protocol Conformance Testing
Protocol conformance testing refers to the testing of the degree to which the protocol implementation of open systems interconnection (OSI) products conforms to OSI protocol standards.
For vehicle Ethernet, the protocol conformance testing from layer 2 to layer 7, excluding AVB/TSN, is mainly based on the TC8-OPEN Alliance Automotive Ethernet ECU Test Specification standards.
The testing items are mainly to verify two aspects: ① Conformance test – to verify whether the tested device/system adheres to the protocol standards; ② Negative test – to verify the stability/robustness of the tested device/system by sending illegal packets.
During testing, auxiliary testing tools called Upper Tester need to be installed on the DUT.
Upper Tester (UT) is essentially an application running on the DUT that can receive commands from the testing platform to configure the parameters of the tested protocol stack (IUT) or trigger specific behaviors from the tested protocol stack.
The commands and formats supported by the UT follow the “Testability Protocol and Service Primitives” specifications under the AUTOSAR framework.
Connecting the testing platform with the DUT, selecting the corresponding protocol testing suite, and conducting specific communication with the DUT, configuring the parameters of the testing suite such as IP, MAC addresses, etc., along with the auxiliary function of Upper Tester to conduct tests on specified protocols, the testing platform collects testing data and generates a testing report.
In addition, vehicle Ethernet testing also includes testing of the AVB protocol suite, with the testing content and reference standards mainly being:
Clock synchronization function (IEEE 802.1AS)
Traffic control function (IEEE 802.1Qav)
Flow management function (IEEE 802.1Qat)
Audio/Video Transport Protocol (IEEE 1722(a)).
1. Physical Layer Testing
2. Network Layer Protocol
3. Transport Layer Protocol
4. Application Layer Protocol
-
SOME/IP Protocol Function/Conformance Testing
-
AUTOSAR UDPNM Protocol Function/Conformance Testing
-
DoIP Protocol Function/Conformance Testing
Honestly, the author feels that Ethernet testing is quite cumbersome. I just wanted to eat an apple, but ended up being fed a bunch of things: plant nutrition, plant hormone studies, light research, climate research, soil and water research, apple cultivation technology research, apple variety comparison research, laborer mental health research, agricultural engineering machinery research, storage equipment research, market price curve research…
However, this is precisely the charm of a thriving industry, with new things emerging continuously. Who knows, one day these new technologies might become mainstream and occupy the commanding heights.
Shanghai Kunyii has strong capabilities in vehicle ultra-high-speed data transmission, storage, and testing, and it is a domestically developed technology. We previously mentioned their autonomous driving testing solution, which has gained a lot of user favor and recognition.
Rapid advancements in autonomous driving testing by Shanghai Kunyii
Kunyii has introduced a similar approach in the Ethernet testing field:Data Collection and Replay Analysis. Collecting Ethernet data packets from multiple network segments in the vehicle, bringing them back to the office for offline analysis, which is fully automated,automatically identifying non-compliant areas.
• To meet the needs of users for vehicle Ethernet testing, Kunyii has independently developed the VBE module product specifically for vehicle Ethernet testing. This product has a completely domestically developed hardware and software structure, compatible with 100T1 and 1000T1 auto-negotiation capabilities, and can switch between transparent transmission and mirroring modes, gaining the trust and support of many automotive companies.
•Supports 10G/2.5G/1000/100 BASE T1: 10G, 1G, 100M Ethernet conversion, can be flexibly applied to various network ports
•Supports IEEE/Legacy conversion:
Switching between two network protocols, covering the vehicle Ethernet protocols available on the market
•Mirror function: Vehicle Ethernet T1-1 and Vehicle Ethernet T1-2 intercommunication, standard Ethernet (RJ45) can capture all packets from Vehicle Ethernet T1-1 and Vehicle Ethernet T1-2 and send them out
•Transparent function: Vehicle Ethernet T1-1 and Vehicle Ethernet T1-2 do not intercommunicate, standard Ethernet (RJ45) can capture all packets from vehicle Ethernet
•Multiple convenient functions: Supports device discovery function, device configuration information reading, device configuration status modification, device firmware online upgrade (requires pairing with Kunyii VCAR DAS software).
|
In simplified terms, vehicle Ethernet has five layers: application layer, transport layer, network layer, data link layer, and physical layer.It is evident that Kunyii’s tool cannot test the physical layer.
However, it still depends on the application scenario. Currently, most Ethernet products’ physical layers are standardized, which is generally not an issue. Clients mainly need to verify aspects beyond the physical layer.
Furthermore, we cannot dismiss the value of a tool just because it cannot handle everything. “Choose the best cost-performance testing solution based on the application scenario, make good combinations of high and low, and use flexibly” is the core value of engineers.
|
|
|
|
|
|
|
|
Vehicle Ethernet T1 Channel Count
|
|
|
|
Standard Ethernet TX Channel Count
|
|
|
|
|
|
|
|
Master-Slave Mode Configuration
|
|
|
|
|
|
|
|
|
|
|
|
|
|
|
|
Operating Power Consumption
|
|
|
|
|
|
Bus 10 Lectures, the best Excel2DBC tool in the Eastern Hemisphere, always free to give away