Industrial Control Classroom【www.gkket.com】Essential Website for Engineers
Add WeChat:gkket123 Join a 500-member WeChat group
Electrical Automation – Free Materials Worth Over Ten Thousand Yuan
Click to Download for Free
(DownLoad)
With the development of automatic control technology, the application of field bus technology in industrial control is becoming increasingly widespread. The reliability of the bus directly affects the safe production and economic operation of industrial enterprises.A certain steel rolling plant uses fully automatic rolling, and all roller tracks are controlled automatically. If a fault occurs on a certain roller track, automatic rolling will be canceled.The roller tracks are divided into 8 major groups and 19 minor groups, with each minor group using a Siemens PLC 37-300 for logic control, and the drive uses a frequency converter.These 19 PLCs are connected through communication module CP342-5 and twisted pair cables to form a DP network, communicating with SIMADYN D.Substations 4 to 20 are in the main control room, with a straight-line distance of 30 m from the SIMADYN D control room, while substations 22 to 25 are in another distribution room, with a straight-line distance of 100 m from the main control room.The communication cable runs from the SIMADYN D cabinet to the main control room and then to another distribution room.After running for a period of time, communication interruptions or frequent communication faults reported by certain substations often occur, affecting automatic control, necessitating a thorough investigation.
1 Fault Phenomena
Fault 1: During commissioning, as soon as power is supplied, communication faults occasionally occur, with various substations randomly reporting communication faults, particularly the 4 substations 22 to 25, which are especially frequent. A rough inspection of the loop resistance shows a value of about 112 Ω, which is within the normal range.
Fault 2: During normal production, various substations randomly report communication faults, leading to tripping and inability to produce. A rough inspection of the loop resistance shows a value of 85 Ω, which is not within the normal range.
Fault 3: During normal production, when the roller track is running, occasionally substations 22 to 25 report communication faults, causing tripping and inability to produce, while there are no issues when the roller track is not running. A rough measurement shows a resistance of 112 Ω, which is within the normal range.
Fault 4: During normal production, occasionally some substations report communication faults, causing tripping, but not frequently. A rough inspection of the loop resistance shows values above 112 Ω, with occasional fluctuations, which are within the normal range.
2 Fault Analysis and Solutions
1) For Fault 1, first check the wiring order, whether the communication DP head A and B terminals have been reversed, then check for any poor connections, and measure the loop resistance on the bus. Theoretically, a resistance value of around 110 Ω indicates no issues; occasional communication faults are generally due to signal attenuation, mainly caused by wiring and communication heads. However, through measurement, these two reasons can be excluded. The length of this twisted pair cable is calculated to be about 150 m in a straight line, but considering the cable is laid in a winding manner and there is a certain length for entering and exiting the substations, the total length of this cable should be around 260 m, which can lead to signal attenuation and thus abnormal communication. The temporary installation of optical fiber is costly, so it is considered to add an RS485 repeater in the distribution room where substations 22 to 25 are located to stabilize the signal. After adding the repeater, communication stabilized.
2) For Fault 2, check the DP communication heads at both ends, and find that the resistance of the DP communication head at the end is abnormal, which should be 220 Ω, but is only around 140 Ω. After replacing the normal DP communication head, it returned to normal.
3) For Fault 3, based on experience, first determine whether it is Faults 1 or 2. The measured resistance is 112 Ω, which is within the normal range, and there are no new cables, so it should not be one of the above faults. However, communication faults occur when the roller track is running, indicating that the operation of the roller track causes the fault. It is suspected to be due to electromagnetic interference, as the frequency converter motor running affects communication. In the cable tunnel, the communication cable is alongside the power cable of the motor. To confirm this judgment, all motors connected to these 4 substations were stopped, and then tests were conducted, finding no more communication faults reported. Therefore, the cause of the fault is electromagnetic interference. The communication cable was re-laid, changing the path to avoid being in the same tunnel as the power cable. After the replacement, it has been observed for a long time with good results.
4) For Fault 4, after checking Faults 1, 2, and 3, the cause of the fault is interference. To address the interference, first check the grounding; a chaotic grounding system can interfere with the PLC system mainly due to uneven potential distribution at various grounding points, leading to ground potential differences and causing ground loop currents that affect the normal operation of the system. The communication system requires one end to be grounded, or the relevant parts should be made into a unified grounding system. During measurement, it was found that the shielding to ground resistance was very high, exceeding 20 kΩ. By grounding at the starting end, it was normal after testing. This indicates that grounding was omitted during initial construction, causing signal interference faults.
3 Summary of Profibus DP Field Bus Faults The encountered field bus faults are all caused by incomplete design and careless construction in the early stages. Therefore, when standardizing design, attention should be paid to the following points:
1) Pay attention to the standards of communication types. Different communication types have different specifications.
2) Pay attention to the selection and laying of cables. The type of cable is an important means to solve electromagnetic interference. For example, using copper strip armored shielded power cables can reduce electromagnetic interference caused by power lines. Different types of signals should be transmitted by different cables, and signal cables should be layered according to the type of transmission signal, strictly prohibiting the use of different wires in the same cable to simultaneously transmit power and signals, and avoiding placing signal lines parallel to power cables to reduce electromagnetic interference. If conditions allow, communication cables can be laid separately.
3) Pay attention to system grounding. Profibus DP communication can be grounded in the control cabinet. When there are joints in the communication line, the shielding layer should be securely connected and insulated, and multi-point grounding should be avoided. It is best for the entire system to have a unified grounding to prevent faults caused by inconsistent grounding.
Important Notice
Want to join the Electrical Automation Technology Exchange Group?
Please add the group leader as a friend
and note: region-industry-name/nickname to obtain group entry qualifications.
Electrical Automation
Professional Focus Sharing
Share to Moments and share with friends
——————————————————————
▣ Source: Internet - Baidu Wenku, infringement deletion!
▣ Statement: We respect originality. The copyright of text, images, and video materials belongs to the original author. Some articles were pushed without being able to contact the original author for various reasons. If there are copyright issues, please contact the original author for deletion (contact 17621634088 - WeChat same number). We only share for use, not for commercial purposes.
They are all paying attention, what are you waiting for?
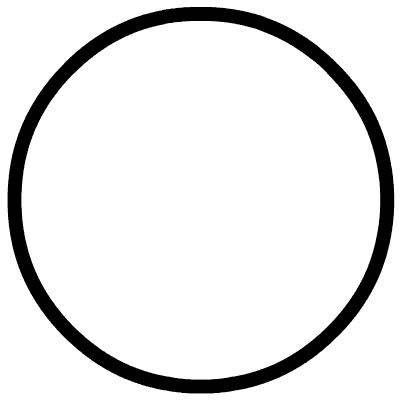