On January 10, 2006, Apple’s annual Macworld conference was held, but the star of the event was not Steve Jobs, but Intel CEO Paul Otellini, dressed in a lab coat. Amidst the swirling dry ice fog, Otellini slowly walked towards Jobs and solemnly handed him a silicon wafer, saying loudly:“Report to Steve, Intel is ready!”
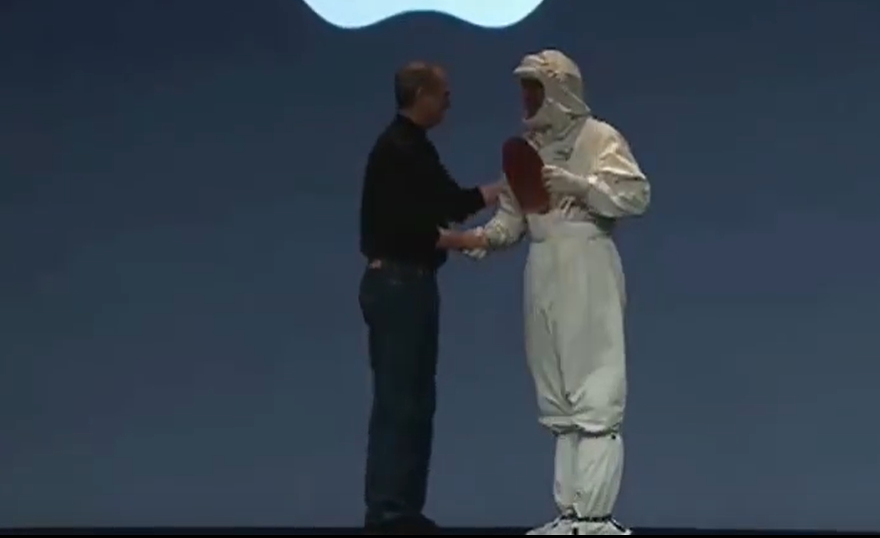
Chosen One
On the morning of August 10, 2002, as the word “login:” flashed on the computer, cheers erupted in the Institute of Computing Technology, Chinese Academy of Sciences—Longxin No. 1 CPU finally worked. The engineers who had not slept all night became even more excited, taking a taxi to Tiananmen, queuing for over an hour in front of the Memorial Hall of the Leaders to report the success of Longxin [2].
This CPU was named “Summer 50,” named by 32-year-old Hu Weiwu, in honor of his doctoral advisor, “Mother of Chinese Computing” Xia Peisu, who had been engaged in computing for 50 years. A year before Longxin’s birth, Li Guojie, the leader of the Institute who advocated the launch of a general-purpose domestic CPU, scraped together 1 million yuan from the tight research funding to raise the flag for the CPU. Faced with this hot potato, Hu Weiwu made a military pledge:If it fails, come to see me with my head.
Chief Designer of Longxin Hu Weiwu
The success of Longxin not only signifies a breakthrough in domestic CPU design but also a victory in chip manufacturing. The foundry for Longxin at that time was none other than the famous SMIC. In addition to the engineers who participated in the initial development working tirelessly, the quick success of Longxin was also due to the “limited autonomy” principle of domestic CPUs at that time.
As the name suggests, “limited autonomy” refers to self-research based on overseas reduced instruction set. At that time, there were two instruction sets in the CPU field(similar to command methods): one is the reduced instruction set, which can be understood as a command that only does one thing; the other is the complex instruction set represented by Intel, which is costly, technically complex, and powerful.
Under the conditions at that time, completely self-researching all instructions from scratch would lead to a situation with no compilers, no operating systems, and no available software, which was neither realistic nor efficient, let alone comparable to Intel’s complex instruction set. Therefore, domestic enterprises focused their attention on overseas reduced instruction sets and conducted self-research based on that.
In addition to Longxin, Feiteng had developed its first CPU as early as 1999, using the SPARC architecture. Shenwei was developed by the historical 56 Institute in Wuxi, using the ancient Alpha architecture. Longxin from the Chinese Academy of Sciences was based on the open-source MIPS architecture. Although MIPS is now nearly forgotten, as a product of the microarchitecture war of the 1990s, MIPS64 was not only the earliest commercialized 64-bit architecture but also had a complete microarchitecture design and relatively complete software chain support.
At the same time, with the support of numerous national-level funds such as 863 and core high-tech, domestic CPUs ushered in a spring: basically maintaining a pace of releasing a chip every one or two years, making unremitting efforts to catch up in performance. The Longxin No. 2 released in 2004 was already able to catch up with the Pentium III from 1999. However, despite seemingly favorable circumstances, domestic CPUs faced three difficulties:
Performance difficulty: Although domestic CPUs made significant progress, competitors were also advancing, especially Intel entering the new century with explosive combat power, leaving domestic CPUs always behind; Ecological difficulty: The x86 patent wall was towering, and domestic autonomous CPUs adopted a circumvention strategy, making it difficult to adapt to Microsoft systems; Mass production difficulty: Users had already adapted to Microsoft’s operating system, and a barren desktop had no appeal, let alone mass production.
At the beginning of the domestic CPU, Longxin, Feiteng, and Shenwei, these research groups were originally small research workshops within national research institutions, a product left over from the planned economy system. After twenty years of reform and opening up, they faced two constraints: first, extremely limited budgets, and second, a complete loss of supporting industrial chains. Under these two constraints, domestic CPUs could only strive to complete the R&D tasks assigned by superiors within the tight financial framework.
In this situation, the reduced instruction set architecture became a stopgap measure: due to the narrow market, the licensing prices were often unbelievably low; Feiteng initially purchased the SPARC license for only 99 dollars. Architectures like SPARC and Alpha were often created behind closed doors by many large factories competing fiercely with Intel, who were well-equipped and willing to form alliances against Intel at low costs.
The MIPS architecture adopted by Longxin had another special advantage: as an independent architecture not relying on any large factory, MIPS was more inclined towards embedded devices such as game consoles, optical discs, and set-top boxes, where these scenarios scaled quickly and brought in money quickly. At that time, the design industry in Taiwan was booming, and MIPS was doing well on the island, receiving substantial licensing fees. However, like most foreign tech companies, MIPS faced tricky intellectual property issues in mainland China.
Previously, Longxin had been developing MIPS architecture computer CPUs without authorization, but since it was not commercialized, both sides coexisted peacefully. However, in 2005, when Longxin cooperated with Microsoft to develop Windows CE, just as the Longxin board was about to be sent to the U.S., MIPS sent Microsoft a fatal email: As soon as Longxin sets foot on American soil, it will violate MIPS’s patent rights. Longxin saw the imminent Microsoft support buff slip away.
MIPS’s warning letter unveiled a nearly default lid in the Chinese tech community: at the beginning of the reform and opening up, foreign companies paid little attention to the Chinese market and did not apply for patents simultaneously, while China’s patent law at that time stipulated that if a patent was not applied for within a year, it could not be applied for thereafter, creating an unprecedented opportunity—though the downside was that it was only applicable within China.
Without the protection of the mainland patent lid, Longxin encountered a series of patent attacks: In July 2005, the semiconductor research firm In-Stat released an independent analysis report stating that the similarity between Longxin’s processor architecture and MIPS reached 95%. Due to lack of authorization, once Longxin began commercialization, it might trigger intellectual property disputes.
As a key project of the national 863 program, the Institute of Computing Technology urgently refuted the rumors, and Hu Weiwu, the head of the research group, also clarified that Longxin was independently developed by Chinese people, and the instruction system deliberately avoided existing foreign patents.
However, MIPS was clearly dissatisfied with this statement. After several rounds of negotiations, MIPS demanded a sky-high price of 1 million dollars. In 2006, the notorious Hanxin incident erupted in the chip industry, coupled with SMIC’s loss and compensation in the TSMC lawsuit, the entire public opinion launched indiscriminate attacks on the semiconductor industry, with negative evaluations flooding in.
Chen Jin, holding “Hanxin No. 1” to showcase the chip, 2003
Seeing the fire getting closer, the crisis had to be resolved. In 2007, during the flourishing exchanges between China and France, the Institute of Computing Technology, through its partner STMicroelectronics, indirectly obtained all patents of the MIPS architecture for Longxin. Under the leadership of the leaders of both China and France, Longxin also held a press conference at the Great Hall of the People, announcing the cooperation, with the headline of the People’s Daily reading:
China’s Longxin is facing the global market.

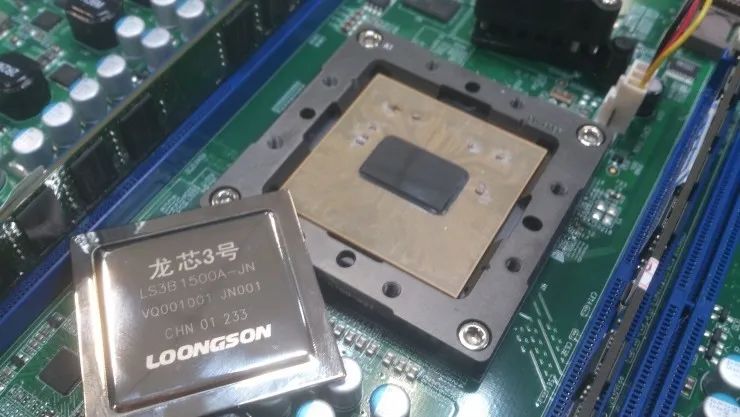

Concerns of the Import Faction
The “import faction” became the mainstream in the industry after 2010, subsequently influencing decision-making directions. There are factors related to the domestic CPU’s own shortcomings, but more importantly, changes in the global industrial landscape.
After 2006, Intel’s rival AMD made a series of mistakes, first acquiring ATI’s GPU business and struggling to handle both the graphics and CPU markets; then, its own foundry, GlobalFoundries, stumbled, leading to a narrow survival space. Coupled with obstacles in process upgrades, its stock price plummeted from over 40 dollars at its peak to just over one dollar.
In 2012, AMD lost over 1 billion dollars and laid off 15% of its workforce, with Wall Street declaring AMD dead: “There is no investment value.” During this stormy period, Su Zifeng, a distant relative of Huang Renxun, took over AMD’s leadership. Similarly, VIA, founded by Wang Yongqing’s daughter, who was the father of Taiwan’s Formosa Plastics, faced difficulties.
AMD’s new leader Su Zifeng
In the 1980s, VIA began to encroach on Intel’s territory starting from CPU peripherals, and in the 1990s, Wang Xuehong even acquired two American companies that developed CPUs, possessing many x86 architecture patents, once seen as a hope for industrial upgrading in Taiwan. However, in the new century, Intel began self-developing chipsets. Coupled with Wang Xuehong’s main focus on HTC smartphones, VIA gradually became a non-essential player.
The misfortunes of the two major players in the x86 camp gave the domestic industry hope. In the new round of domestic CPU route conversion, local governments became an unignorable supporting force behind emerging powers.
In 2013, Shanghai’s state-owned assets collaborated with VIA to establish Zhaoxin—Wang’s family has deep ties with Shanghai, and Wang Xuehong’s brother almost founded a wafer foundry in Shanghai at the same time as Zhang Rujing. VIA had also set up operations in Shanghai as early as the beginning of the century, and the mainland design team had developed for over a decade, allowing Zhaoxin to leverage VIA’s experience and save significant effort.
Similarly, Zhongke Shuguang, also under the Chinese Academy of Sciences, chose to collaborate with AMD to establish Haiguang in 2016. Behind Haiguang was the strong support of Chengdu’s state-owned assets. Li Guojie, who once led the development of Shuguang servers in the 1990s, became a key figure in Shuguang’s rise, making it a domestic server manufacturer on par with Lenovo over the next twenty years.
For China, AMD’s Zen architecture is an attractive option due to its strong performance. After paying around 300 million dollars in cooperation fees, through eleven processes across two companies, Haiguang was ultimately able to sell products in mainland China. Although the introduced chips were significantly trimmed after joint development, their performance still far exceeded many domestic CPUs, and Haiguang’s inherited architecture from five years ago remains a first-tier player today.
The collaboration between AMD and Haiguang provided Su Zifeng with ample startup capital; on the day of the announcement, the company’s stock price irrationally surged by 50%. The transaction between Zhaoxin and VIA was also a three-bird deal, acquiring a CPU R&D team, x86 architecture patents, and the chipsets supply chain; Haiguang, backed by the listed company Zhongke Shuguang, learned from AMD’s operations and combined with national encryption algorithms, quickly gained traction in commercial servers.
More importantly, both companies had starting funds of around 2 billion, compared to the 800 million spent by Longxin over fifteen years, giving the import faction ample ammunition. Two years after its establishment, Zhaoxin achieved mass production, selling over ten thousand sets. In the first half of 2020, Haiguang reported revenue of 270 million, with a net profit of over 60 million.
While the import route appears to yield immediate results, it carries a fatal risk—changes in the international situation.
In mid-2019, during the China-U.S. trade friction, the Wall Street Journal suddenly labeled Haiguang with a “military background”. That same year, Haiguang was placed on the U.S. Entity List, leading AMD to announce that it would no longer authorize the next generation of Zen architecture. Zhaoxin, which purchased patents from VIA, had also received warnings from Intel: do not cross the red line.
As the saying goes, this time is different from the last; compared to the previous turmoil, AMD had now traversed the long valley of death and no longer needed external support. Moreover, at the Lawrence Livermore National Laboratory in the Bay Area, AMD chips were used to power America’s nuclear deterrent. AMD knew which was more important.
The “importation” route has ultimately proven to have fundamental flaws. Historically, the mainland has always lacked x86 talent, and whether “importation” can evolve into “absorption and innovation” remains a big question mark. If it can only stay at the level of copying and pasting x86 hardware, it will be difficult to conduct in-depth R&D and meet high security and consumer market demands.
The difficulties in absorbing x86 architecture can be partially glimpsed from Zhaoxin. In 2010, VIA brought x86 to Shanghai, and its technical leader, along with hundreds of people, spent two years in a small black room just to understand the source code of the CPU core. When Zhaoxin began developing CPUs, its R&D team of four to five hundred people devoted three to four years to maintaining the development of just one and a half CPU projects. The heavy historical burden of x86 is a huge drag on “absorption and innovation.”
Complete independence is nearly impossible from the ground up; introducing the x86 architecture requires strong capabilities for digestion, absorption, and re-innovation. The next step for domestic CPUs must return to the most fundamental issue: ecology.

Exploring Ecology
In 2018, the ZTE incident broke out, and the domestic CPU market began to rise.
During the twenty years after leaving Lenovo, Ni Guangnan has been tirelessly advocating for domestic CPUs. The past dispute between Ni and Liu has become a story in the history of Chinese technology, with the conflict between “trade, industry, and technology” and “technology, industry, and trade” still being a topic on social media today.
Ni Guangnan’s young assistant, Liang Ning, described Ni as a noble idealist after the ZTE incident, igniting heated discussions, evoking nostalgia among the Chinese [6].
In 1994, with the dismantling of trade barriers, overseas companies like Intel and Microsoft entered China in droves, and Ni Guangnan traveled between Beijing and Shanghai, planning to establish a computer CPU design center, but failed. Subsequently, he attempted to create the “Ark CPU,” a concept similar to today’s Google netbook, but government officials were assigned to use it and showed no interest, resulting in a second failure.
Many high-tech industries in China follow several steps:Leaders’ keen concern – High emphasis from ministries – Massive financial input – Concentrated efforts from enterprises – Breakthroughs in technology. Most fields rely on this uniquely Chinese model of industry-academia-research collaboration, but this model has two key prerequisites—no consideration for costs, no consideration for yield.
There is an interesting question:Who has the highest R&D expenditure: Intel, Apple, or Huawei?
However, even Huawei, which is strong, only launched its self-developed server CPU in recent years, even earlier than Apple’s M1 chip. In the CPU stronghold of computers and servers dominated by Intel, apart from AMD, which has had years of ups and downs, there has been a lack of strong competitors.
Recently, Hu Weiwu’s remark about “14nm chips being sufficient” has sparked controversy. Many people only noticed the statement, “We don’t want the U.S. to make 5nm; we want to make 5nm ourselves,” while ignoring the latter part: “90.9% of applications can use 14nm; with good system optimization, we can be very competitive in the market.”
Compared to the arduous journey 30 years ago, today’s China has markets, policies, urgency, and slogans. However, for domestic CPUs, it requires the idealistic enthusiasm, respect for market rules, and generosity, tolerance, and patience towards researchers.
Many industries in China are not afraid of repeated failures; they fear the oscillation between “today we build, tomorrow we buy.”