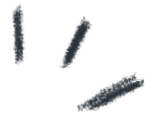
Introduction
You may have heard of terms like “Industry 4.0”, “Smart Manufacturing”, and “Industrial Internet of Things (IIoT)”. According to statistics, IIoT has already captured the largest share of global IoT spending. A study by Business Insider predicts that global manufacturers will invest $70 billion in IoT solutions by 2020. In the continuously evolving industrial production landscape, IIoT gateways are one of the crucial pathways to connect devices (M2M) and provide a solid foundation for industrial manufacturing and automation upgrades.
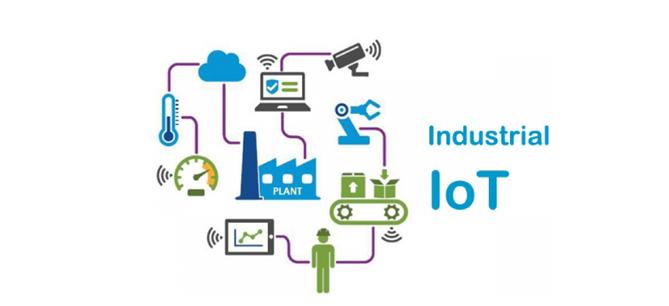
So, what advantages do companies that have adopted IIoT and achieved digital production have over traditional methods?
01
Remote Equipment Management
By directly connecting various industrial protocols and integrating devices into the IIoT, users can remotely manage equipment, monitor its status, and reduce on-site failure rates, effectively avoiding production delays due to downtime and ensuring production efficiency.
02
Production Process Monitoring
In the industrial production process, the IoT comprehensively monitors the entire production flow and provides real-time suggestions for operational adjustments, optimizing operational costs.
03
Product Quality Control
IoT sensors collect and aggregate product data and other relevant information from various stages of production. This data may involve raw material composition, environmental temperature, waste generated, transportation, and other quality-related data, including user experience data if available. Ultimately, this enables manufacturing companies to analyze data, identify, and correct product quality issues.
04
Safety Production Assurance
Manufacturing enterprises leverage IoT combined with big data analysis to enhance overall employee safety assurance, ensuring production safety. By monitoring key data (such as injury and accident rates, near misses, and frequent failures), they effectively ensure production safety and provide more considerations for the HSE department’s safety management.
05
Logistics and Supply Chain Optimization
Manufacturing companies track the movement of materials, equipment, and products within the supply chain through IIoT, collecting real-time data for access. Accurate data can be integrated into management systems like ERP and PLM, connecting with supplier systems to control material flow and production cycles. This effectively helps manufacturing companies predict issues, reduce inventory, and manage capital.
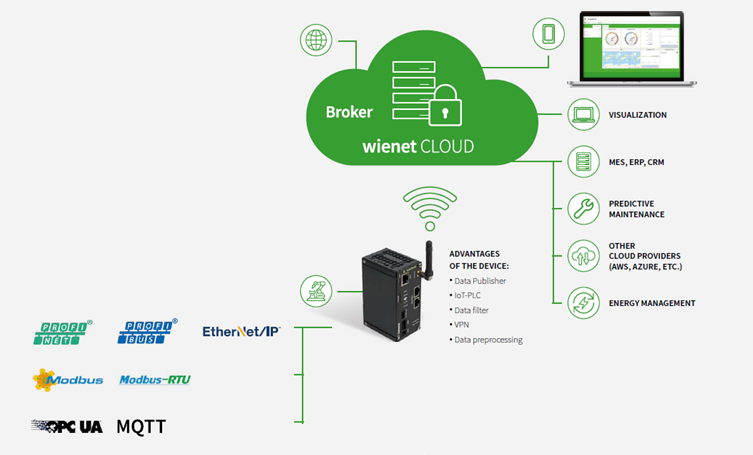
The Wienet Industrial IoT Gateway from Weilang Electric serves as a bridge for internal communication networks, integrating numerous industrial communication protocols such as Profinet and Modbus. It can be deployed at the network and device ends within the enterprise through a “southbound interface”, enabling standalone industrial control devices to connect to the IIoT. The gateway features an IoT-PLC, allowing for direct online logic control via I/O points and preprocessing of equipment data to record effective data.
Additionally, the Weilang Electric Industrial IoT Gateway supports connection to “cloud services” via communication protocols like OPC UA and MQTT, enabling direct connection to “Weilang Cloud” or third-party cloud services (AWS, AZURE). It flexibly connects to the enterprise MES system through a “northbound interface”, achieving visualization of on-site information such as device data and production data through cloud computing and big data analysis, using data visualization dashboards to assist enterprise managers in managing industrial sites and ensuring safe production.