

With the rapid development of industrial technology, distributed control systems and field control systems have emerged. The three major control systems in industrial process control are PLC, DCS, and FCS. Some people believe that FCS has developed from PLC, while others think it has evolved from DCS. FCS, PLC, and DCS are closely related yet have some differences.
PLC controllers are electronic systems designed for digital operation in industrial environments. They use a type of programmable memory to store programs internally, execute logical operations, sequential control, timing, counting, and arithmetic operations based on user instructions, and control various types of machinery or production processes through digital or analog inputs and outputs.
DCS, or Distributed Control System, is a computer-based control system. It rapidly developed in the mid-1970s, integrating control technology, computer technology, image display technology, and communication technology, also known as 4C technology, to monitor, control, and manage production processes. It breaks the limitations of conventional control instrument functions and effectively addresses the risks associated with early computer systems’ overly centralized information, management, and control.
The core of FCS, or Fieldbus Control System, is the bus protocol, with a foundation in digital intelligent field devices, fundamentally focusing on localized information processing.
The Basic Characteristics of Process Control Systems Composed of Large PLCs
(1) A top-down structure where PLC can function as an independent DCS or as a subsystem of DCS.
(2) PID is placed in the control station, allowing for continuous PID control and various functions.
(3) A PC can be used as the master station, with multiple PLCs as slave stations; alternatively, one PLC can serve as the master, with multiple PLCs as slaves, forming a PLC network.
(4) Primarily used for sequential control in industrial automation, newer PLCs also have closed-loop control capabilities.
The Basic Characteristics of DCS Control Systems
(1) A top-down tree structure where communication is key.
(2) PID is in the controller, connecting computers with field instruments.
(3) A tree topology with parallel continuous link structures, with numerous cables running from relay stations to field instruments.
(4) The signal system includes both digital and analog signals.
(5) DCS generally consists of field instrument layer, control unit layer, factory (workshop) layer, and enterprise management layer.
The Basic Characteristics of FCS Control Systems
(1) FCS is a fusion of 3C technology. It is suitable for intrinsically safe, hazardous areas, variable processes, and extremely challenging environments.
(2) Field devices are highly intelligent, providing fully digital signals; a single bus connects all devices.
(3) A bidirectional digital communication bus from the control room to field devices is interconnected, bidirectional, serial multi-node, and open, replacing the unidirectional, single-point, parallel, closed analog systems.
(4) Control functions are thoroughly decentralized.
Comparison of DCS Control Systems and PLC Control Systems
DCS is a “distributed control system,” while PLC is merely a control “device”; the difference lies in “system” versus “device.” Systems can realize the functions and coordination of any device, while PLC devices only fulfill the functions of their respective units. In terms of networking, the network acts as the central nervous system of the control system.
The DCS system, such as the HOLLiAS MACS system, is divided into two levels: system network and control network. The system network interconnects field control stations and system operator stations, while the control network facilitates communication between field control stations and intelligent I/O units, ensuring real-time and reliable information transfer.
On the other hand, PLCs typically operate individually, and when communicating with other PLCs or host computers, they primarily use a single network structure. In terms of network security, PLCs lack robust protective measures.
DCS systems are designed with numerous expandable interfaces, making it convenient to connect external or expanded systems. In contrast, once a PLC system is established, adding or removing operator stations becomes challenging. To ensure the safety and reliability of DCS control devices, DCS employs dual redundant control units, which switch seamlessly to operational units when critical control units fail, ensuring the overall system’s safety and reliability.
PLC systems generally lack the concept of redundancy, making it difficult to implement redundant control strategies. Particularly when a PLC unit fails, the entire system must be halted for replacement and maintenance, requiring reprogramming. Thus, DCS systems are considered one level safer and more reliable than PLC systems. The hardware reliability of DCS and PLC is comparable. The advantage of PLC lies in software, utilizing a sequential scanning mechanism, dominating in high-speed sequential control. The cycle time for PLC is around 10ms, while for DCS control stations, it is approximately 500ms.
In terms of implementing sequential interlocking functions, DCS is at a disadvantage compared to PLC, and its logical execution speed is not as fast as PLC. Relatively, systems built with PLCs are less costly. DCS control stations typically adopt centralized control, although they support remote distributed I/O, it is rarely used due to cost reasons. PLCs, based on fieldbus, offer remote distributed I/O that is smaller, more flexible, and cost-effective in wiring.
Comparison Between FCS Control Systems and DCS Control Systems
FCS can be said to combine the characteristics of both DCS and PLC while taking a revolutionary step forward.
(1) FCS is an open system with open technical standards; its field devices have interoperability and device compatibility, allowing users to choose products from different manufacturers and brands for optimal system integration, whereas DCS systems are closed and products from different manufacturers are incompatible.
(2) FCS achieves fully digital signal transmission, with communication extending from the lowest level sensors and actuators to the highest level, providing strong support for MES and ERP systems, and importantly, it allows for remote diagnostics, maintenance, and configuration of field devices; DCS’s communication capabilities are significantly limited, and although it can connect to the Internet, it cannot reach the lowest level, providing limited information and lacking remote operation capabilities for field devices.
(3) FCS adopts a fully decentralized structure, eliminating the I/O units and control stations found in DCS, delegating control functions to field devices, achieving complete decentralization, and making system expansion very easy; DCS’s decentralization only extends to the controller level, emphasizing the controller’s functions, while the data highway is crucial.
(4) FCS’s full digitalization allows for high control system precision, achieving an accuracy of ±0.1%; in contrast, DCS’s signal system is binary or analog, requiring A/D and D/A conversion, resulting in an accuracy of ±0.5%.
(5) FCS can implement PID closed-loop functionality in field transmitters or actuators, combined with digital communication, shortening sampling and control cycles from DCS’s 2-5 times per second to 10-20 times per second, improving regulation performance.
(6) By eliminating significant hardware, cables, and installation auxiliary equipment, FCS significantly reduces installation and debugging costs, making its overall cost much lower than DCS.
FCS is an open, fully distributed, intelligent control system. However, traditional DCS and PLC systems have been in use for decades, evolving into practical and highly reliable systems. As they develop, both exhibit trends of converging towards each other. For instance, new DCS systems now have strong sequential control capabilities, while new PLCs are not weak in handling closed-loop control, and both can form large control networks.
2021 Junior Electrician Exam Question Bank Complete Version (with Answers)
Trouble with Inverter Faults? Just One Click to Fix!
Want to review all electrical exam questions with one click? Have you got this amazing tool yet?
Which of the five major electrical drawing software (CAD, Eplan, CADe_simu…) do you prefer?
Latest Electrical CAD Drawing Software, with Detailed Installation Guide!
Latest Electrical Drawing Software EPLAN, with Detailed Installation Guide!
Common Issues with S7-200 SMART Programming Software for Beginners (with Download Links)
Comprehensive Electrical Calculation EXCEL Sheets, Automatically Generated! No Need for Help with Electrical Calculations!
Bluetooth Headphones, Electrician/PLC Starter Books as Gifts? Come and Claim Your Electrical Gifts!
Fundamentals of PLC Programming: Ladder Diagrams and Control Circuits (with 1164 Practical Mitsubishi PLC Cases)
Still can’t understand electrical diagrams? Grab the basics of electrical diagram recognition and simulation software for quick hands-on practice!
12 Free Electrician Video Courses, 10GB Software/E-books, and 30 Days of Free Electrician Live Courses Are Now Available!
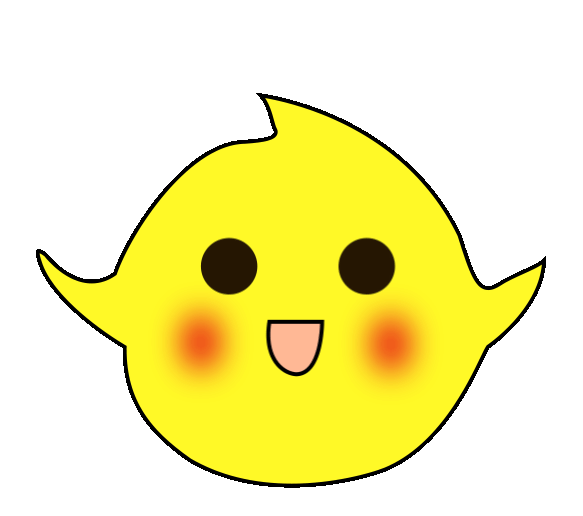