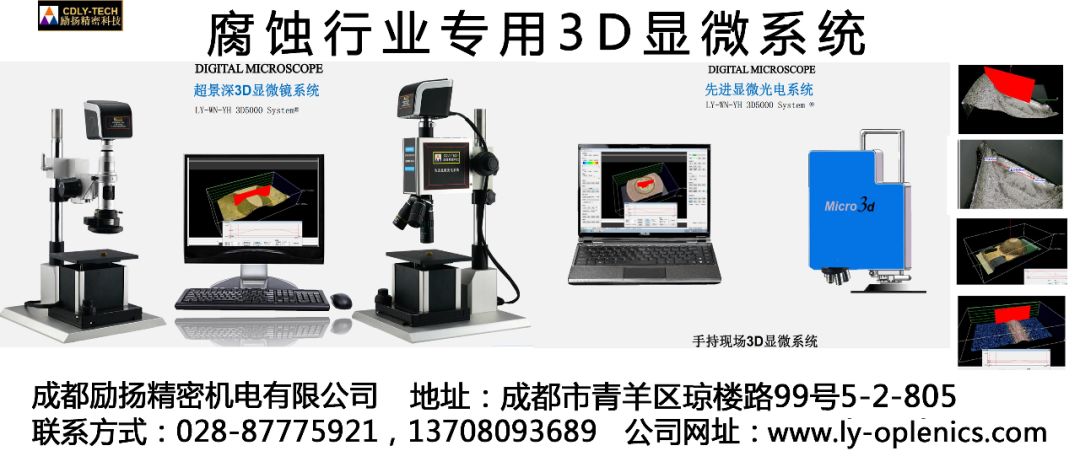
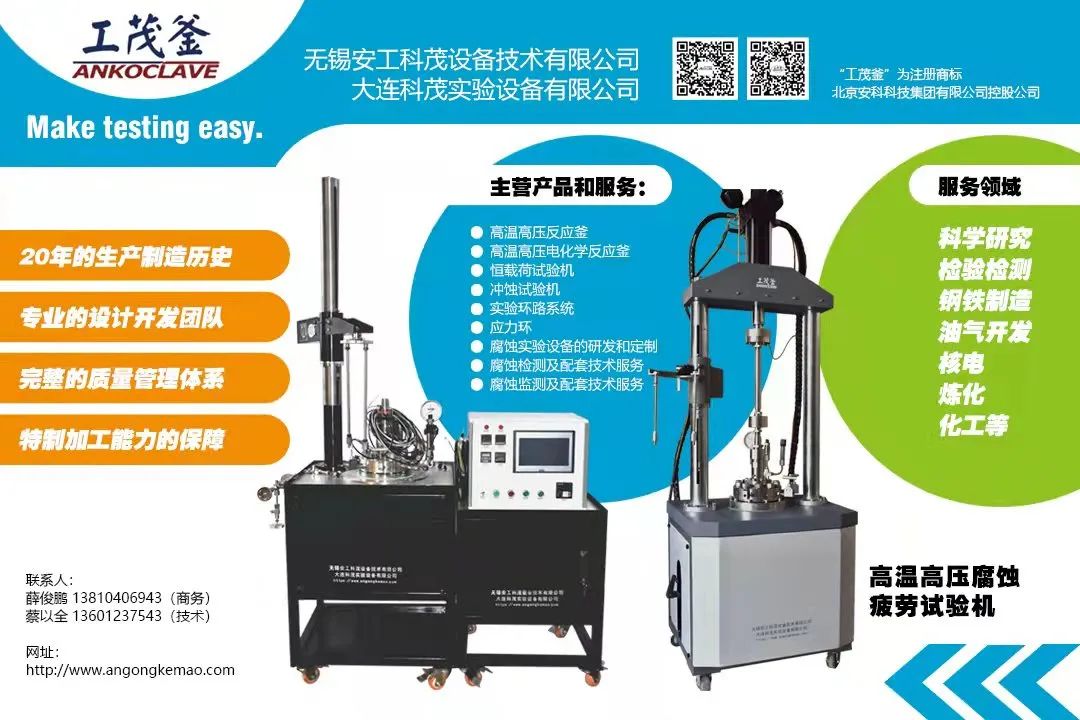
Click to Follow: PTC Coating Anti-Corrosion Technology
Authors: Du Juan, Li Fang, Song Hai Peng, Wei Zi Ming, Li Xiang Yun
School of European Aviation Engineering, Civil Aviation University of China, Tianjin 300300
0 Introduction
The single-layer anti-corrosion coatings prepared on metal surfaces cannot provide efficient and lasting protection due to issues like insufficient density and performance. Therefore, the research on preparing high-performance composite anti-corrosion coatings on metal surfaces has increasingly attracted attention from scholars worldwide, gradually becoming a research hotspot in the fields of corrosion prevention and protection.
Currently, the research mainly focuses on the preparation methods, performance, and mechanisms of composite anti-corrosion coatings on metal surfaces. Common methods used in the preparation of composite anti-corrosion coatings include plasma electrolytic oxidation (PEO) technology, sol-gel method, and self-assembly method. Compared to single anti-corrosion coatings, composite anti-corrosion coatings have significantly improved performance, particularly in their ability to combine anti-corrosion properties, hydrophobic properties, or bactericidal properties; the mechanisms of composite anti-corrosion coatings are more complex, mainly involving the addition of corrosion inhibitors, nanoparticles, and synergistic effects of multiple mechanisms. This article summarizes the research progress on the preparation methods, performance analysis, and mechanism studies of composite anti-corrosion coatings on metal surfaces based on the latest literature from home and abroad, and proposes questions for further research.
1 Preparation Methods of Composite Coatings on Metal Surfaces
There are many preparation methods for composite coatings on metal surfaces. Due to the significant differences in performance between inorganic materials and polymers and the strong aggregation of nanoparticles, some composite coatings, such as organic-inorganic hybrid coatings, cannot be prepared directly using mixing methods. Common methods for preparing hybrid coatings include the sol-gel method, blending method, self-assembly method, and in-situ polymerization.
1.1 Plasma Electrolytic Oxidation (PEO) Technology
Plasma electrolytic oxidation (PEO) is an environmentally friendly technology for surface electrolytic oxidation treatment of metal materials, widely used to produce wear-resistant and corrosion-resistant coatings on lightweight metals (such as magnesium, aluminum, and titanium alloys). There are many types of PEO, including micro-arc oxidation (MAO), micro-arc discharge oxidation, spark anodic oxidation, and discharge anodic oxidation. The PEO process is mainly divided into three steps: (1) During the electrolytic oxidation process in the aqueous electrolyte, PEO occurs at the anode of the electrolyte; (2) PEO initially occurs as conventional anodic oxidation; (3) As the voltage increases, the rupture of the electrolyte film and ionization of the oxide are accompanied by gas generation. The main advantages of the anti-corrosion coatings prepared using PEO technology are good wear resistance and corrosion resistance. However, the anti-corrosion effect of the film in corrosive environments is not ideal. Therefore, it is necessary to improve PEO technology, with two main improvement measures: one is to add other additives to the electrolyte; the other is to embed nanoparticles into the coating structure.
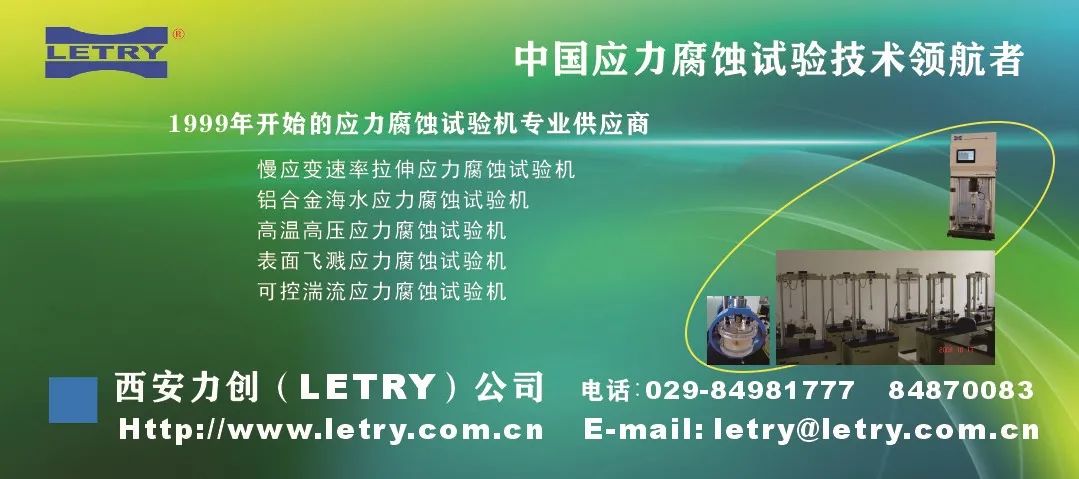
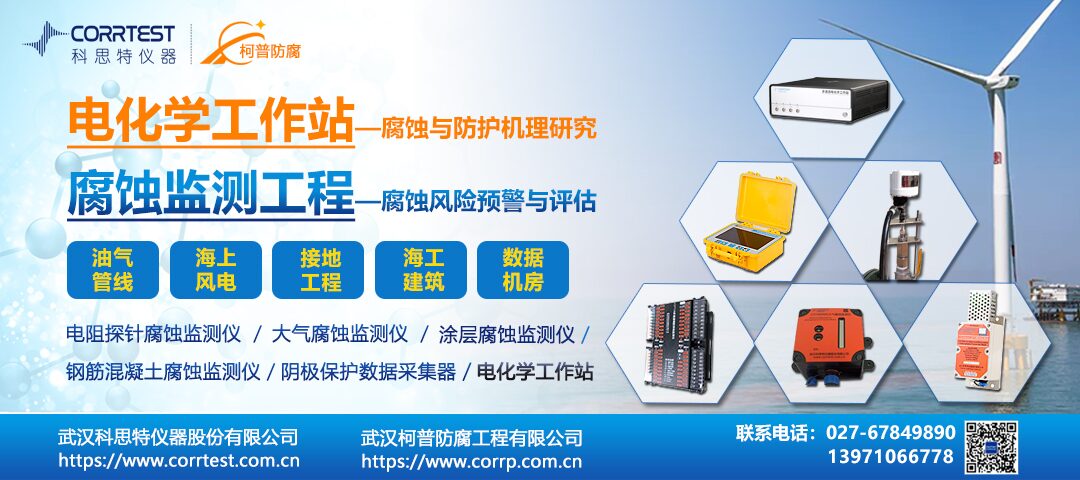
Li et al. used PEO technology to prepare composite coatings on the surface of AM60B magnesium alloy in an electrolyte solution containing NaAlO2 and other additives. The results showed that the coating was dense with relatively low porosity. As the concentration of NaAlO2 increased, the relative content of MgAl2O4 in the coating also increased. Kinetic polarization test results indicated that the dense and thicker composite coating could provide good corrosion protection for magnesium alloys. Additionally, PEO treatment also improved the wear resistance of the alloy. Alex et al. used PEO technology to prepare composite coatings on the surface of 5052 aluminum alloy. Experimental results showed that under different SiO2/Na2O (molar ratio) conditions, oxide layers of 20-90 μm thickness were obtained in all electrolytes. The oxide layer of the “n=1 electrolyte” (n indicates the silicate index) mainly consisted of several aluminum oxides, while the oxide layer of the “n=3 electrolyte” was mainly mullite. The PEO film formed in the electrolyte with a silicate index of n=3 exhibited better protective properties than the PEO film of n=1, and the corrosion resistance of the samples prepared under these two conditions was significantly better than that of the untreated aluminum alloy substrate. Dmitry et al. used PEO technology to prepare composite coatings on the surface of MA8 magnesium alloy by adding nanosized titanium nitride particles. The results indicated that X-ray photoelectron spectroscopy (XPS) and Raman spectroscopy showed the presence of TiN, TiOxNy, and TiO2 compounds in the PEO composite layer; the coating formed in the electrolyte with a TiN concentration of 2-3 g/L exhibited the best corrosion and mechanical properties. Compared to coatings without added nanoparticles, the hardness of the nanoparticle-containing coating increased twofold, wear resistance improved by 2.2 times, and corrosion resistance was also significantly enhanced. Therefore, incorporating TiN nanoparticles into the PEO coating can significantly improve the anti-corrosion and mechanical properties of the magnesium alloy surface.
The sol-gel method is a chemical synthesis process of hydrolysis and condensation, which can environmentally coat chemically stable and protective coatings on metal surfaces using metal alkoxides (mainly organosilanes). Therefore, the sol-gel method is also an important preparation method for composite anti-corrosion coatings. The main advantages of this method are its green and pollution-free nature, while the main disadvantage is that the film layer is prone to cracking in high-temperature environments. Although blended sol-gel coatings can provide relatively dense films for metals, under certain corrosive environments, ions that are soluble in water can still penetrate the micropores of the coating and corrode the metal surface. Therefore, to extend the anti-corrosion performance of the film layer, inhibitors with active corrosion protection functions can be incorporated into the sol-gel formulation.
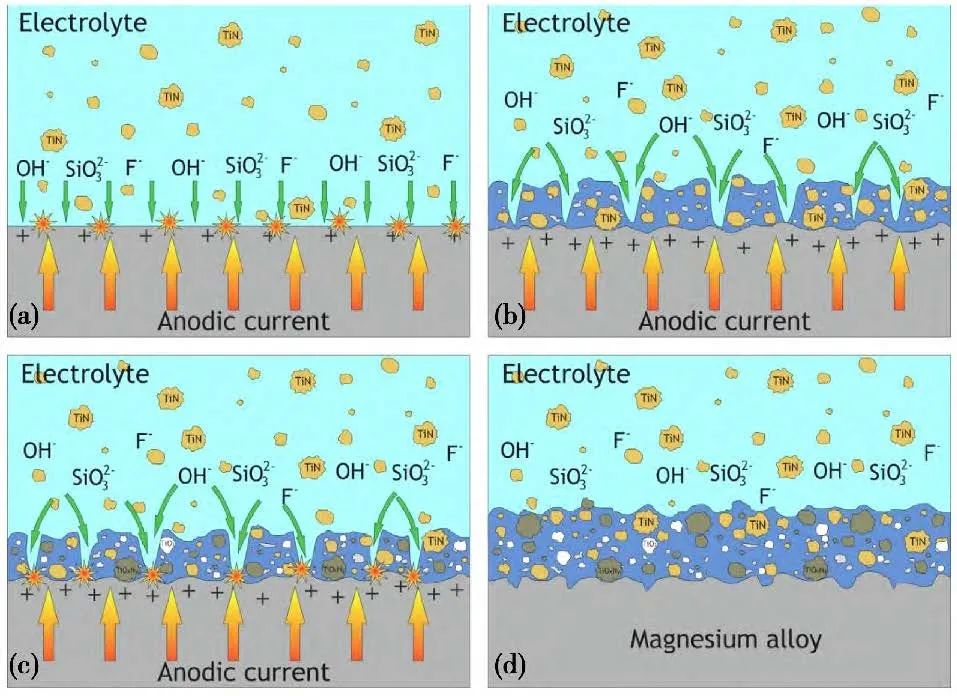
Figure 1 Formation process of PEO coating, (a) nanoparticles are adsorbed by the positive electrode (b) the anode layer is formed and the nanoparticles are incorporated to form a porous PEO (c) spark discharge begins and local melting of the substrate surface occurs (d) the porous layer and non-porous sublayer grow into a uniform composite layer, and TiN NPs enter the coating.
Tuan et al. used the sol-gel method to prepare composite coatings on the surface of low carbon steel and studied their corrosion inhibition performance in a 3.5% NaCl solution. The results indicated that the mixed sol-gel coating containing 100 ppm caffeine had the highest inhibition rate, reaching 88.79%. Li et al. synthesized a core-shell structure of SiO2@PANI sol using (3-glycidoxypropyl)trimethoxysilane (GPTMS) as the core and polyaniline (PANI) as the shell on the surface of magnesium-lithium alloy, embedding vinyltrimethoxysilane (VTMS) into SiO2@PANI, and prepared SiO2@PANI/VTMS composite sol. The results showed that the SiO2@PANI sol, which was stably dispersed in ethanol, improved the hydrophobicity of the composite coating, achieving a contact angle of up to 133.8°; the Mg-Li alloy exhibited good corrosion resistance, with an impedance value of up to 5×10^9 Ω/cm2, and the corrosion current density was only 6.7×10−7 A/cm2. The main mechanism was the synergistic effect of hydrophobicity, barrier properties, and passivation of the SiO2@PANI/VTMS composite sol coating, which resulted in a highly effective anti-corrosion effect.
Chen et al. used the sol-gel method to prepare organic-inorganic composite coatings on the surface of AA2024 aluminum alloy. The coating was composed of organosilicon-epoxy resin and pre-hydrolyzed ethyl silicate (HTEOS). The mixed coating was characterized by Fourier-transform infrared spectroscopy (FT-IR), thermogravimetric analysis (TGA), scanning electron microscopy (SEM), and contact angle testing. The results indicated that when the HTEOS content was 4% (mass fraction), the composite coating exhibited the best corrosion resistance. Nezamdoustand et al. prepared a composite coating consisting of cerium-vanadium conversion coating and sol-gel coating on AM60B magnesium alloy. XPS analysis revealed that the coating mainly consisted of O, Ce, V, and Mg atoms, and SEM results indicated that the coating had a crack-like spherical structure. The results of dynamic potential polarization curves and electrochemical impedance spectroscopy indicated that the conversion coating containing only cerium and vanadium had minimal protective effect on magnesium alloys, while the composite coating significantly increased the corrosion resistance of magnesium alloys, effectively delaying corrosion.
The self-assembly method refers to the technology where active molecules or atoms with appropriate structures spontaneously adsorb and combine with materials such as metal substrates through various interactions like chemical bonding without external forces, forming ordered molecular films. Self-assembled monolayers (SAMs) belong to the category of supramolecular chemistry, where there is no actual breaking and forming of chemical bonds, mainly relying on weak interactions such as hydrogen bonding between molecules to form supramolecular structures with different functions. SAMs have been widely applied in many fields such as metals, electronics, engineering, and medicine due to their rapid film formation, high coverage, few defects, high efficiency, and low cost. The main disadvantage of this film is poor adhesion to the metal surface, making it prone to detachment from the metal substrate. To improve the adhesion of the film layer to the metal substrate, three aspects of improvement can be made: (1) using adsorbing corrosion inhibitors on the metal surface to form a compact structure through self-assembly to effectively protect the metal; (2) generating polymer nanofilms; (3) forming multilayer composite films, which can be more dense and uniform to some extent, complementing the stability and voids between each film layer.
Yang et al. successfully prepared self-assembled molecular films of octadecane thiol (C18H37-SH) and benzotriazole (BTA) on copper surfaces, as well as a composite self-assembled molecular film of C18H37-SH & BTA. The preparation process is illustrated in Figure 2. The results showed that both C18H37-SH and BTA could successfully self-assemble on the copper surface, forming compact SAMs. Compared to the monolayer film, the C18H37-SH & BTA SAMs composite film exhibited higher charge transfer resistance, demonstrating excellent anti-corrosion performance, and the resulting composite self-assembled film greatly improved the corrosion resistance of copper.
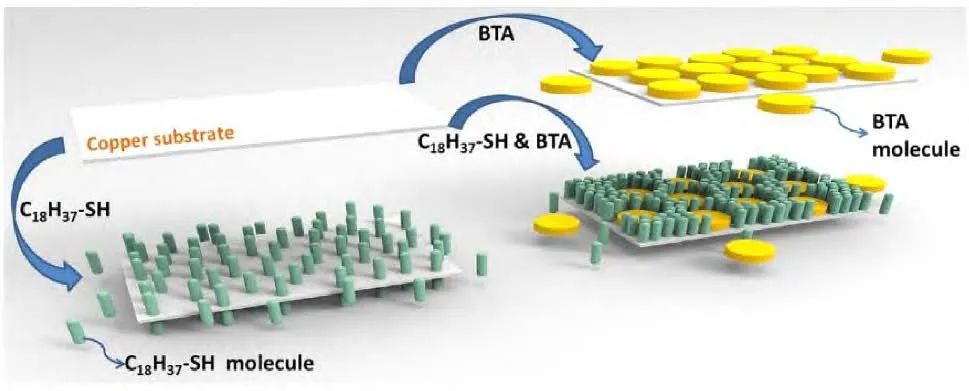
Figure 2 Schematic diagram of the self-assembly process of BTA SAMs, C18H37-SH SAMs, and C18H37-SH & BTA SAMs on copper substrates.
Wang et al. prepared a polymer nanofilm (TESPA) on the copper surface using self-assembly technology, and the results indicated that the polymer nanofilm significantly inhibited the chemical corrosion of copper. On the one hand, XPS results indicated the presence of chemical bonds between the copper and TESPA polymer monomer, and the formation of three-dimensional disulfide bonds and siloxane networks protected copper from corrosion; on the other hand, SEM and energy dispersive spectroscopy (EDS) results showed that the copper surface was uniformly covered by the TESPA self-assembled polymer nanofilm. The copper surface covered by TESPA was smoother than the exposed copper surface and exhibited better anti-corrosion performance. Zhu et al. further improved the corrosion resistance of the graphene oxide (GO)-based composite film by self-assembling a double [3-(triethoxysilyl) propyl] tetrasulfide (BTESPT)/GO multilayer film on the surface of AA2024 aluminum alloy. Experimental results indicated that the composite film significantly improved the stability and corrosion resistance of the AA2024 substrate. The GO in the composite film effectively hindered the corrosion reaction by reducing the rates of cathodic and anodic reactions. Additionally, the formation of Si-O-C covalent bonds based on XPS analysis reflected the bonding strength between the silane film and the intermediate GO layer. By adding GO to the silane solution to form the BTESPT/GO composite film, a film with fewer defects and a more complete geometry can be obtained, resulting in superior anti-corrosion performance of the self-assembled composite film.
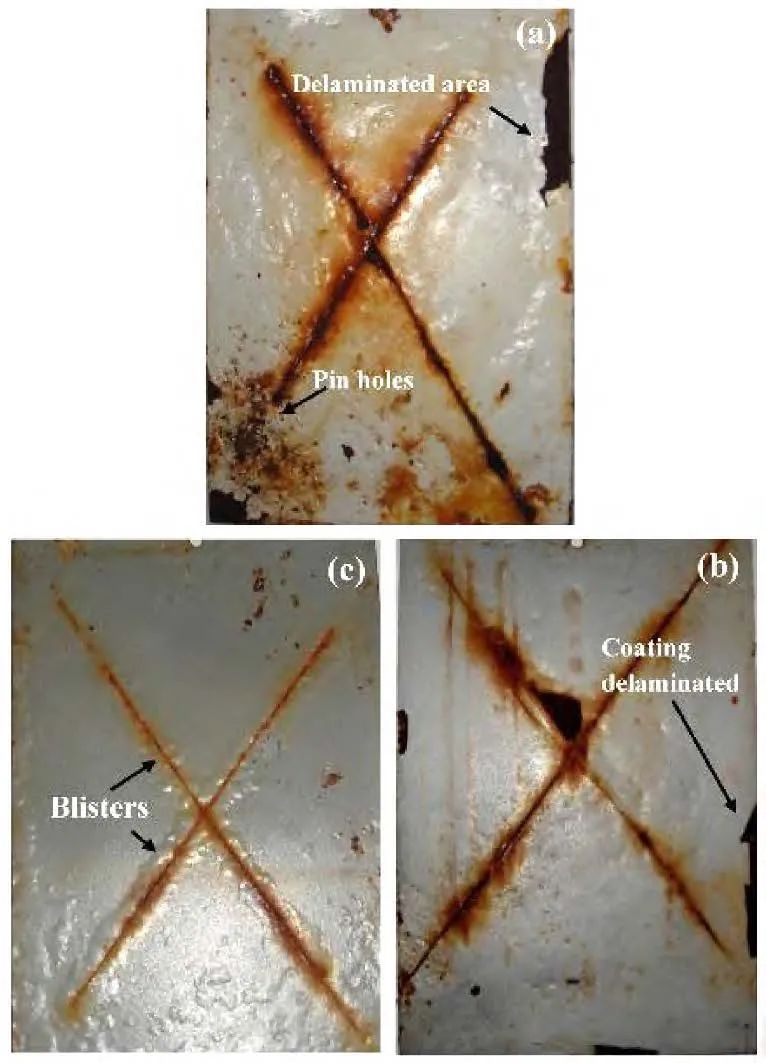
Figure 3 Self-assembly diagram of BTESPT/GO composite film.
1.4 Comparative Analysis of Three Preparation Methods
The main preparation methods for composite anti-corrosion coatings on metal surfaces include plasma electrolytic oxidation, sol-gel method, and self-assembly method. Among them, plasma electrolytic oxidation mainly forms anti-corrosion coatings with better corrosion resistance by adding electrolyte components or nanoparticles; the sol-gel method can enhance corrosion resistance by adding inhibitors or nanoparticles; the self-assembly method primarily enhances corrosion resistance by self-assembling self-assembled films containing different components. Based on the literature from home and abroad, the advantages and disadvantages of the three preparation methods are summarized in Table 1. Additionally, plasma electrolytic oxidation is mainly used to prepare inorganic composite anti-corrosion coatings, the sol-gel method is mainly used to prepare organic-inorganic composite anti-corrosion coatings, and the self-assembly method is mainly used to prepare organic composite anti-corrosion coatings. Therefore, researchers can make certain selections during experimental preparations.
Table 1 Comparison of PEO, Sol-gel method, and Self-assembly method
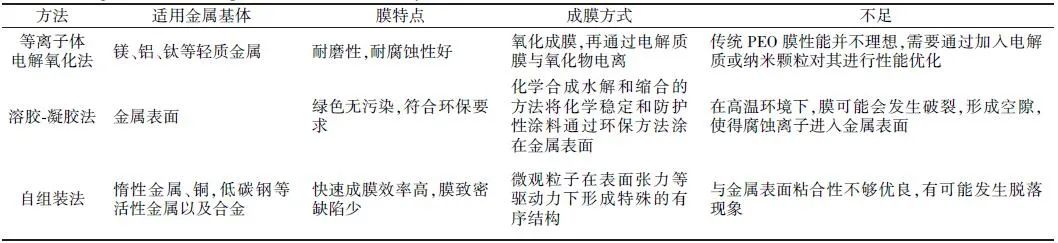
2 Performance Research on Composite Coatings on Metal Surfaces
2.1 Research on Anti-Corrosion Performance
When metals corrode, changes in morphology, performance, and organizational structure occur simultaneously, such as becoming brittle and reduced strength. Changes in the elemental content in metals or phase transitions in the internal structure can severely affect their performance; therefore, it is necessary to study their performance.
Qi et al. doped GO into a silica core-shell copolymer emulsion to prepare a thin organic anti-corrosion film on the surface of galvanized steel, while studying the influence of GO on the composition, morphology, and corrosion resistance of the protective film. XPS results indicated that the composition of the film remained unchanged after adding GO; SEM results showed a significant change in the morphology of the defects in the film, and the roughness of the galvanized steel surface decreased; the corrosion rate and corrosion current density of the composite film decreased by one and two orders of magnitude, respectively. These results demonstrate that GO can effectively improve the corrosion resistance of the anti-corrosion films. The corrosion resistance mechanism is illustrated in Figure 4. When cracks occur in the film, the corrosive medium can diffuse inward along the crack path. After adding GO modification to the film, the diffusion path of the corrosive medium can be effectively extended, improving the corrosion resistance of the film.
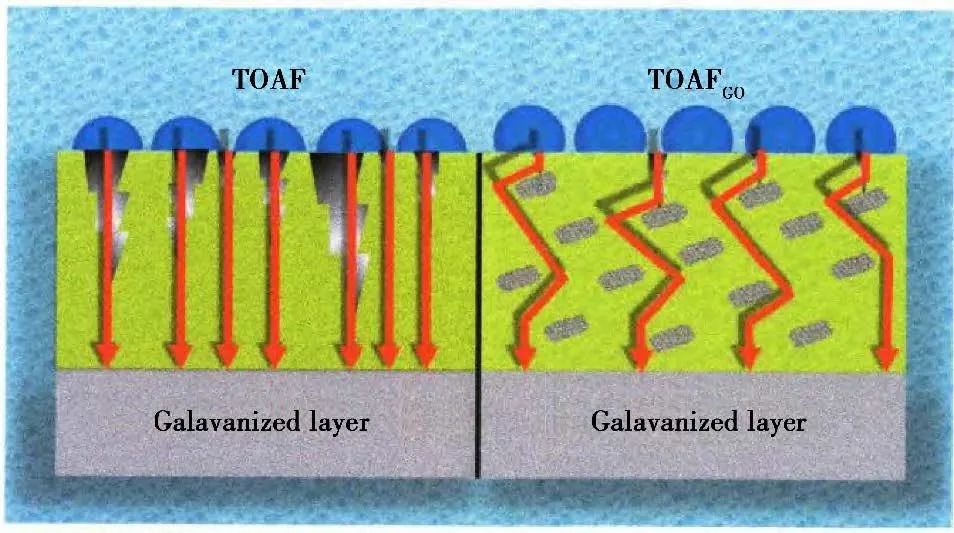
Figure 4 Schematic diagram of enhanced corrosion resistance after adding GO.
Gazala et al. synthesized a polypyrrole/SiO2 composite film through the chemical oxidative polymerization reaction of pyrrole, then added it to epoxy resin, and finally coated it on a soft steel substrate. SEM and TEM images showed that SiO2 was uniformly dispersed in the polypyrrole matrix. Thermogravimetric analysis (TGA) confirmed that the polymer composite film had good thermal stability. Tafel polarization and electrochemical impedance spectroscopy (EIS) results indicated that the epoxy coating with the added polymer composite film significantly improved the anti-corrosion performance compared to the epoxy coating without added polymer composite film. Salt spray test results showed that the epoxy coating without added polymer composite film was severely corroded and blistered after 75 days under salt spray conditions, while the epoxy resin coating containing 3.0% (mass fraction) polypyrrole/SiO2 effectively suppressed the spread of corrosion and contained very few bubbles. From the above results, it can be seen that the interaction between the polymer composite film and the epoxy resin formed good adhesion, making it a high-quality anti-corrosion coating for low carbon steel substrates.
2.2 Research on Hydrophobic Performance
Metal materials with superhydrophobic surfaces can achieve self-cleaning, suppress surface corrosion and oxidation, and reduce the friction coefficient (using water as a lubricant). Currently, the main method to improve hydrophobic performance is to add nanoparticles such as SiO2 and TiO2 to modify the film layer, while better blocking corrosive substances that dissolve in water. Research on the application of superhydrophobic surfaces is still far from sufficient, and this area of research will be a focus of future related work.
Conradi et al. successfully synthesized a 50 um thick epoxy coating and a composite epoxy coating with 2% (mass fraction) SiO2 particles on AISI 316L austenitic stainless steel, and characterized their surface morphology and mechanical properties. The results indicated that the addition of SiO2 particles improved the hardness, surface roughness, and hydrophobicity of the coating; Ko et al. successfully prepared a composite functional coating with corrosion resistance, hydrophobicity, and oleophobicity on the AZ91D magnesium alloy substrate using a normal pressure plasma jet (APPJ) system with tetraethoxysilane as a precursor. Electrochemical impedance spectroscopy testing results indicated that the coating exhibited good anti-corrosion performance, and the contact angle, as shown in Figure 6, of the hydrophobic composite coating effectively suppressed corrosion, providing a second layer of protection for the metal substrate. Therefore, hydrophobicity and anti-corrosion can effectively synergize, achieving better anti-corrosion effects.
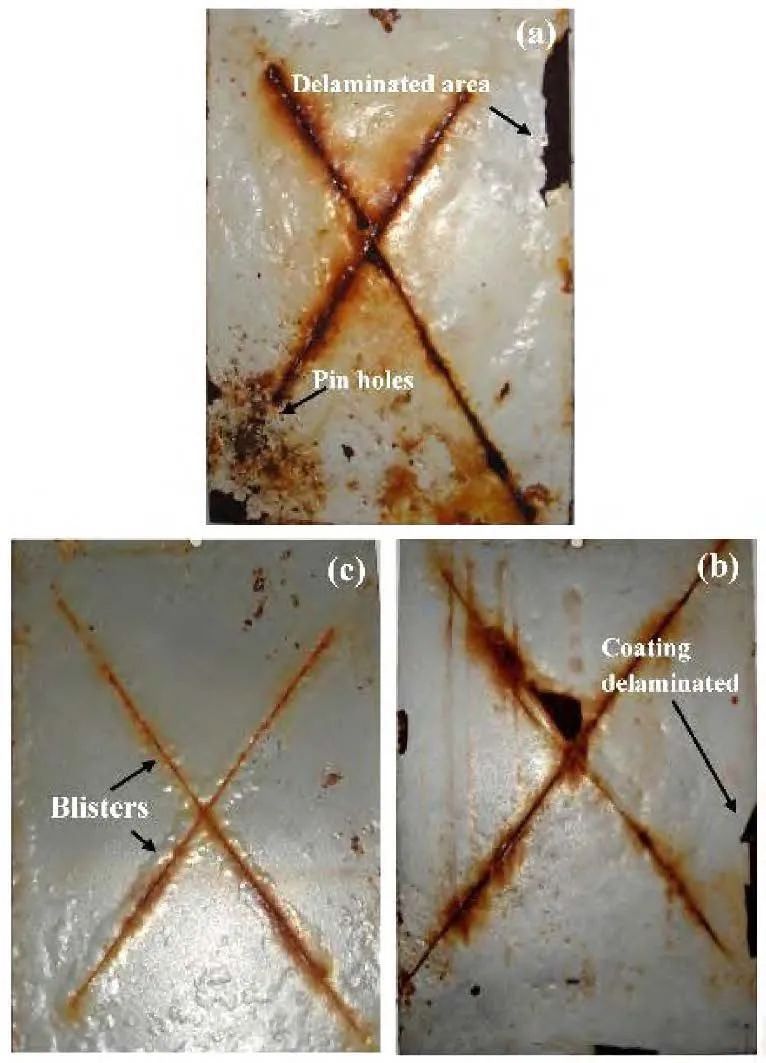
Figure 5 (a) Photograph of blistering of epoxy-coated steel sheet after 75 days of salt spray; (b) 2.0% epoxy resin polypyrrole/SiO2 composite coated soft steel sheet and (c) 3.0% epoxy resin polypyrrole/SiO2 composite coated soft steel sheet exposed to salt fog for up to 150 days.
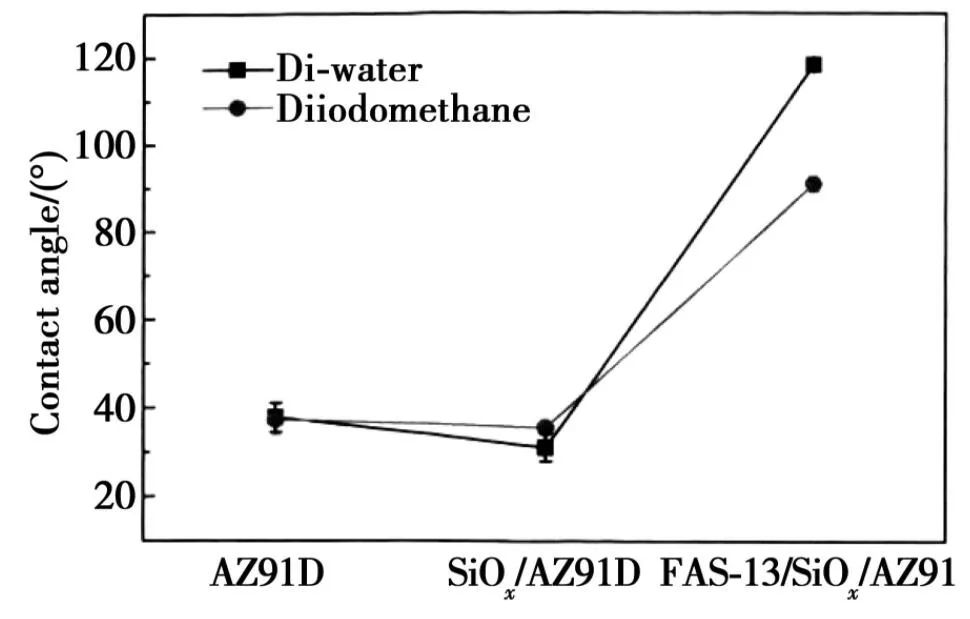
Figure 6 Measurement of contact angle of bare AZ91D, SiO2/AZ91D and FAS-13/SiO2/AZ91D.
2.3 Research on Bactericidal Performance
The requirements for metal materials in the environment are increasing, for example, in high-temperature and high-humidity areas such as cabins, bacteria can easily breed, and corrosion is also more severe; thus, it is necessary to study and prepare coatings with both antibacterial and anti-corrosion properties. Antibacterial anti-corrosion coatings can kill pathogenic bacteria attached to the metal surface, ensuring the health of passengers, and can also kill corrosion bacteria that damage the coatings and materials, thereby achieving the anti-corrosion purpose. Antibacterial anti-corrosion coatings play an increasingly important role in medical, environmental, and public health fields. Therefore, developing coatings that possess both anti-corrosion and antibacterial properties is an important topic that has attracted widespread attention from academia and industry.
Abdolreza et al. synthesized a multifunctional polyaniline/cationic reduced graphene oxide (P-RGO+) nanohybrid material and incorporated the resulting nanohybrid product into a water-based polyurethane (WPU) dispersion system to obtain a composite anti-corrosion coating. The effects of the hybrid on the anti-corrosion, antistatic, antibacterial, and mechanical properties of the composite coating were studied using infrared spectroscopy, X-ray diffraction (XRD), and field emission scanning electron microscopy (FESEM). The P-RGO+ nanohybrid agent not only improved the antibacterial activity of the composite coating against Gram-positive and Gram-negative bacteria but also significantly enhanced the mechanical properties of the composite coating compared to coatings without added nanohybrid products.
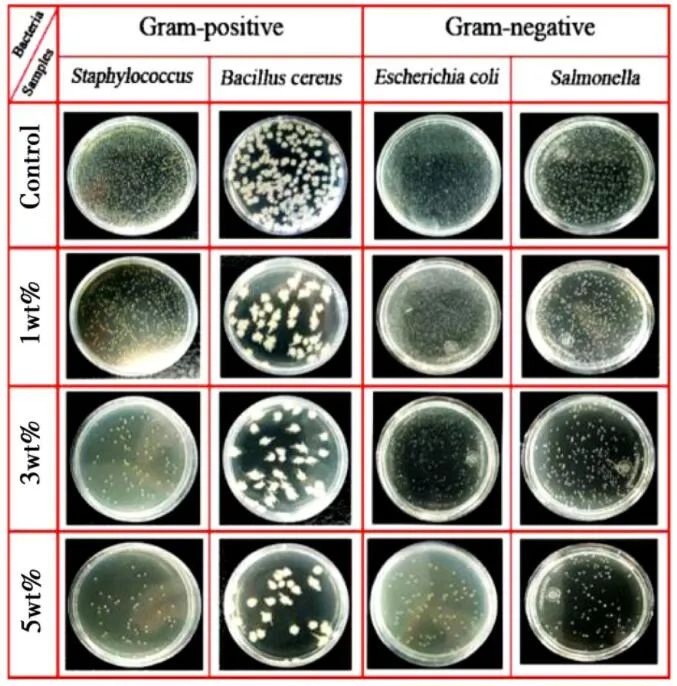
Figure 7 Evaluation of the antibacterial activity of P-RGO*3 containing different drug loadings against Staphylococcus aureus, Bacillus cereus, E. coli, and Salmonella by colony counting method.
Li et al. prepared a self-healing and self-antibacterial layered double hydroxide conversion film (GLDHs) using L-aspartic acid as a raw material, and the results indicated that GLDHs not only exhibited anti-corrosion properties but also demonstrated good antibacterial activity against E. coli and Bacillus subtilis.
2.4 Performance Comparison
A comparative analysis of the three main performances of composite anti-corrosion coatings on metal surfaces, namely, anti-corrosion, hydrophobicity, and antibacterial properties, was conducted. Among them, anti-corrosion mainly manifests through waterproofing, gas and corrosive ions, achieved by filling numerous cracks in the film and forming complexes (such as salicylate ions or complexes with zinc ions in pigments); hydrophobicity is primarily achieved by adding nanoparticles such as SiO2 and TiO2 to confer hydrophobic functions to the anti-corrosion film; antibacterial properties mainly involve adding antibacterial ions (such as silver ions and thiols) that react within the cells to form Ag-S complexes or inhibit DNA replication, thus affecting cell membrane structure and permeability to achieve antibacterial effects.
Based on extensive reading of domestic and foreign references, the performance change patterns from single films to composite films were summarized as shown in Figure 8. As can be seen from Figure 8, the three performances of anti-corrosion films are not independent of each other, and there is a certain relationship between them; hydrophobicity can effectively reduce the corrosion of soluble corrosive substances on metal surfaces, and antibacterial properties can also prevent corrosion substances from corroding metals to a certain extent. Both performances enhance the anti-corrosion performance of the film. In certain high-temperature and high-humidity environments, metal surfaces are very prone to bacterial growth and corrosion; therefore, it is crucial to prepare multifunctional films that possess hydrophobicity, antibacterial properties, and anti-corrosion performance.
3 Mechanism Research of Composite Coatings on Metal Surfaces
3.1 Addition of Corrosion Inhibitors
The corrosion inhibitor protection method is a common measure for metal anti-corrosion. By adding a small amount of corrosion inhibitors to the environment in which the metal is located, a protective film can be formed through physical and chemical reactions with the metal surface, which can delay the corrosion of the metal material. Adding corrosion inhibitors to the anti-corrosion film can form a thin film on the outer side of the anti-corrosion film, increasing the impedance of the composite film, thereby reducing the corrosion current and enhancing the anti-corrosion performance of the metal.
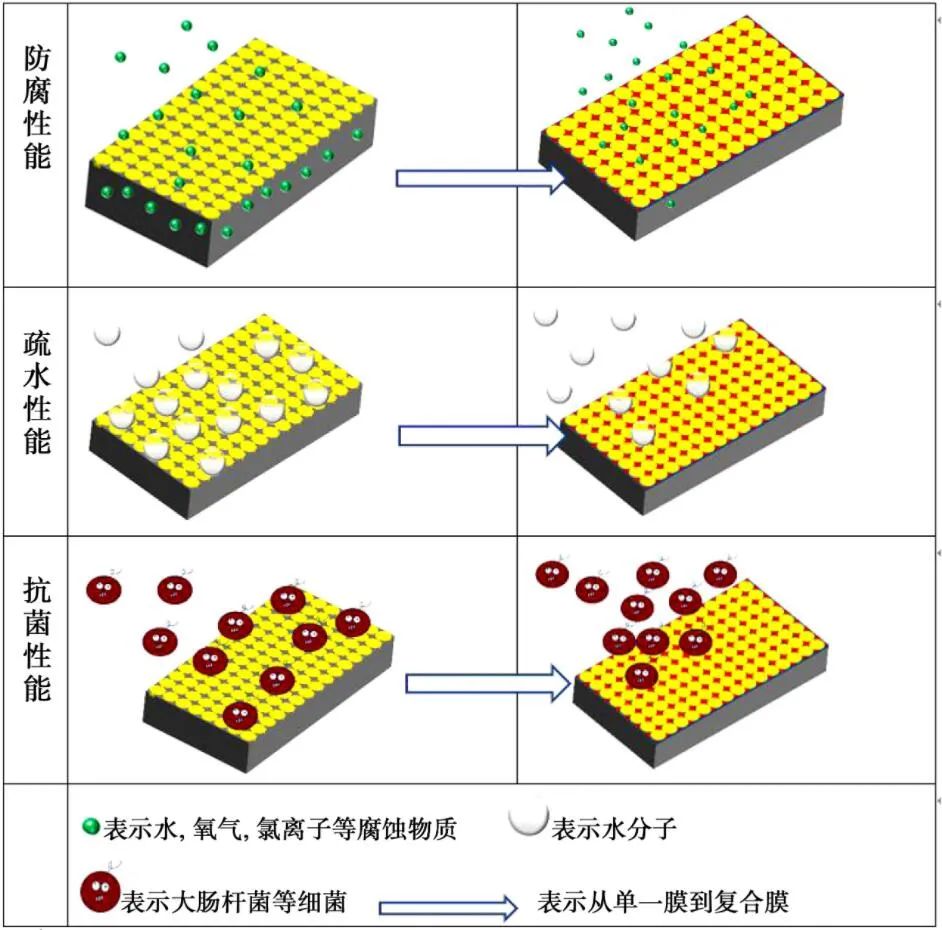
Figure 8 Performance change law from single membrane to composite membrane.
Liang et al. prepared a double-doped layered double hydroxide (LDH) film on anodized magnesium alloy AZ31, and the results indicated that the prepared LDH film was relatively uniform, and the incorporation of Ce3+ and vanadate altered the LDH crystal structure, significantly improving its anti-corrosion performance. Zhi et al. synthesized phosphorus molybdenum acid-doped polyaniline (PANI) anti-corrosion coating on stainless steel by electro-polymerization, and the results indicated that the improvement in corrosion resistance of the PANI coating was due to the presence of phosphorus molybdenum acid, which promoted the formation of oxides, filling the pores in the PANI coating and forming an interfacial oxide layer that blocked the corrosion of 304SS in acidic media. Qiang et al. synthesized two new long-chain alkyl chain indole derivatives, namely, 1-dodecyl-1H-indole (DI) and N,1-docosyl-1H-indole-5-amine (DDIA). Electrochemical analysis indicated that DDIA-SAMs had a significant inhibitory effect on the corrosion of copper in 3.0% (mass fraction) NaCl medium. DI-SAMs mainly functioned by inhibiting the anodic dissolution of copper, while DDIA-SAMs hindered the formation of cathodic and anodic corrosion products. Additionally, immersion tests indicated that due to the dual-chain effect and multiple solid coupling effects, DDIA-SAMS exhibited good anti-corrosion performance and had a strong interaction with the metal surface, as illustrated in the molecular simulation results in Figure 9.
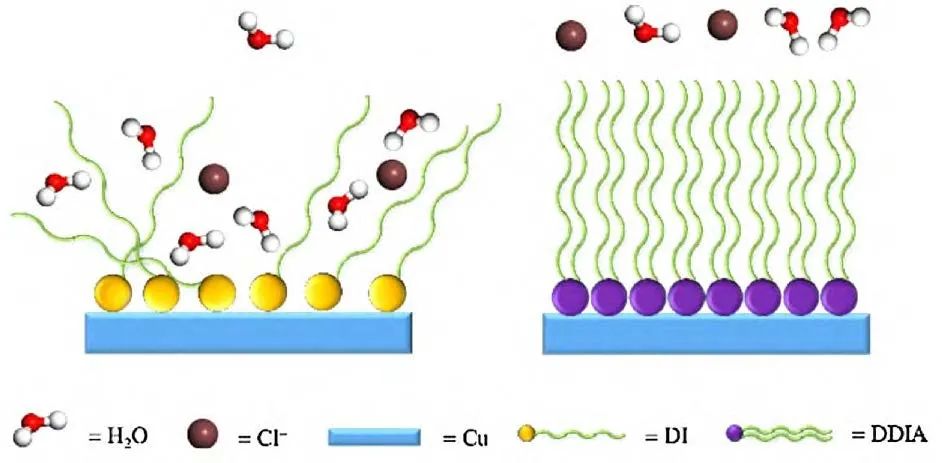
Figure 9 Block diagram of the inhibition mechanism of DI-SAMs, DDIA-SAMs for copper corrosion.
Yun et al. studied the composite inhibition effects of sodium molybdate (Na2MoO4) and benzotriazole (BTA) on pitting corrosion of Q235 steel in NaCl and NaHCO3 solutions. The results indicated that the addition of Na2MoO4 and BTA significantly enhanced the inhibition effect of the coating on steel, with the optimal ratio of Na2MoO4 to BTA being 4:1; in the test solution containing the composite inhibitors, the pitting potential increased significantly, with an inhibition efficiency exceeding 97%. Therefore, the addition of the composite inhibitors Na2MoO4 and BTA promoted the adsorption and film formation on the steel surface, enhancing the anti-corrosion performance of the steel.
3.2 Addition of Nanoparticles
The small size of nanoparticles can improve the corrosion resistance of coatings by adding nanoparticles to the coating or modifying the coating with nanoparticles. The addition of nanoparticles with adsorption capabilities can also promote the formation of deposits covering the metal surface. Many composite anti-corrosion coatings improve the performance of existing coatings by incorporating nanoparticles.
Samadianfard et al. prepared a fullerene oxide (OF)/sol-gel nanocomposite film on AM60B magnesium alloy by adding OF nanoparticles to the sol-gel solution, and the research results confirmed that the addition of nanoparticles enhanced the corrosion resistance of the sol-gel film. Wang et al. prepared a composite anti-corrosion film of polydimethylsiloxane (PDMS), furan, and mesoporous SiO2 (SBA-15) on the steel surface. The results indicated that as the SBA-15 content increased, the surface of the anti-corrosion film changed from hydrophilic to hydrophobic and then to superhydrophobic due to the micro-nano structure of SBA-15. Increasing the SBA-15 content effectively reduced the diffusion efficiency of the electrolyte, and the anti-corrosion mechanism is illustrated in Figure 10. The addition of SBA-15 is beneficial for enhancing the bonding strength of the coating while maintaining high thermal stability, greatly enhancing the anti-corrosion performance of the composite film. Park et al. prepared a TiO2-graphene composite layer using electrophoretic deposition (EPD), and the results indicated that the addition of graphene nanosheets helped prevent crack formation in the EPD layer, thereby blocking corrosive ions from entering the metal and achieving anti-corrosion objectives.
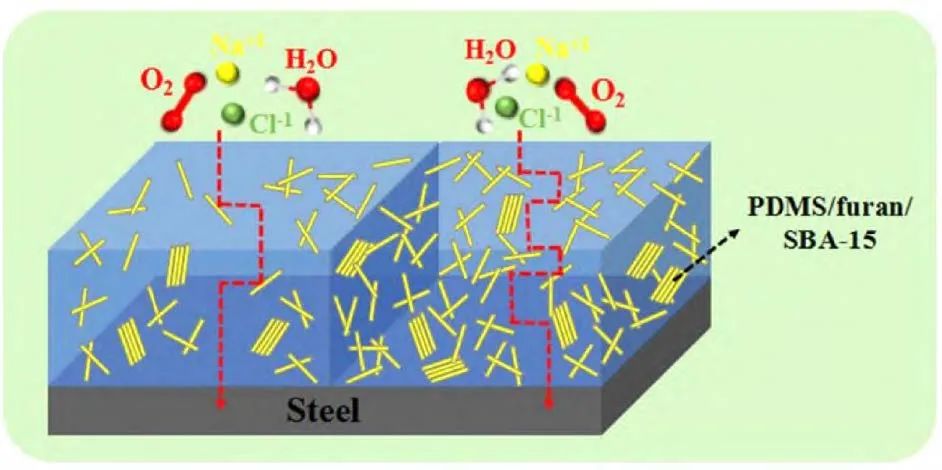
Figure 10 Anti-corrosion mechanism of blended coatings.
3.3 Synergistic Effects of Multiple Mechanisms
Under certain conditions, the formation mechanisms of composite films on metal surfaces can be complex, leading to synergistic effects that achieve better results. Taking organic-inorganic hybrid films as an example, in 1999, Lu Yanping et al. prepared an organic composite chromate film (KD-PC) on the surface of electroplated zinc steel plates, and the results indicated that the composite film effectively blocked water, oxygen, and chloride ions from corroding the zinc steel plate. The main components of the outer layer of this composite film are organic resins, where hydroxyl groups can undergo addition reactions and crosslink to form a network structure of high polymers, which can not only block corrosive ions from entering but also inhibit the leaching of Cr3+ from the film; the inner layer of the chromate film improves the anti-corrosion performance through polymer formation and the action of corrosion inhibitors, ultimately achieving better results through the synergistic effect of the inner and outer layers.
Deng et al. formed a composite film by effectively utilizing the good 3-D shielding structure between linear/three-dimensional organosilicon and linear siloxanes, where small molecular corrosion inhibitors filled the gap positions, forming a compact composite structure. Qiu et al. obtained a functionalized graphene film (PAT-G) through π-π interactions (non-covalent bonds) between poly(2-aminothiazole) and graphene, and then mixed epoxy resin with PAT-G organic solvent to prepare an epoxy resin/PAT-G composite coating. The anti-corrosion shielding performance and friction performance of the coating were evaluated through water absorption tests, electrochemical measurements, and wear tests. The results indicated that the graphene composite coating exhibited excellent protective functions when immersed in a 3.5% NaCl solution for 80 days; the PAT-G composite coating reduced the wear rate by 69.48% compared to pure epoxy resin coatings, demonstrating good wear resistance.
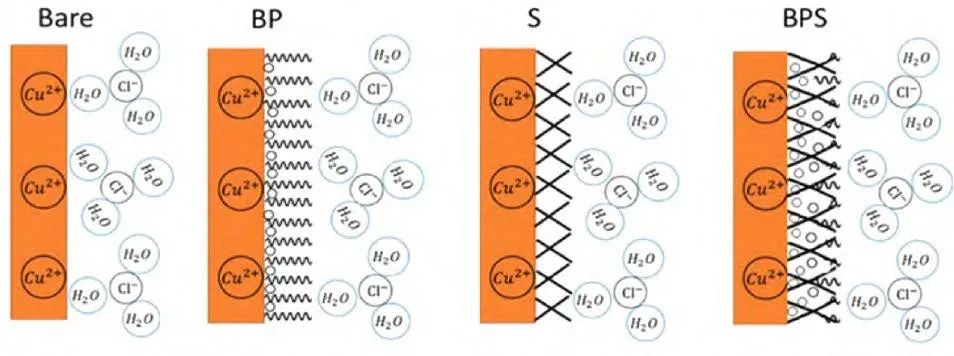
Figure 11 Interface conditions of copper electrodes (uncovered and covered) in solution.
3.4 Comparative Analysis of Mechanisms
This section mainly introduces the three mechanisms of action of composite anti-corrosion coatings on metal surfaces, where the addition of corrosion inhibitors forms a film on the metal surface, increasing the impedance of the composite film and filling surface gaps; the addition of nanoparticles modifies the anti-corrosion film on the metal surface, filling gaps and generating deposits; the synergistic effects of multiple mechanisms mainly include surface adsorption, inhibition of electron mobility processes, chemical bond formation, or polymer generation. Several processes occur simultaneously and synergistically, significantly enhancing the performance of composite anti-corrosion films. Through extensive research of relevant literature at home and abroad, the action mechanisms of composite anti-corrosion films on metal surfaces were summarized as shown in Figure 12.
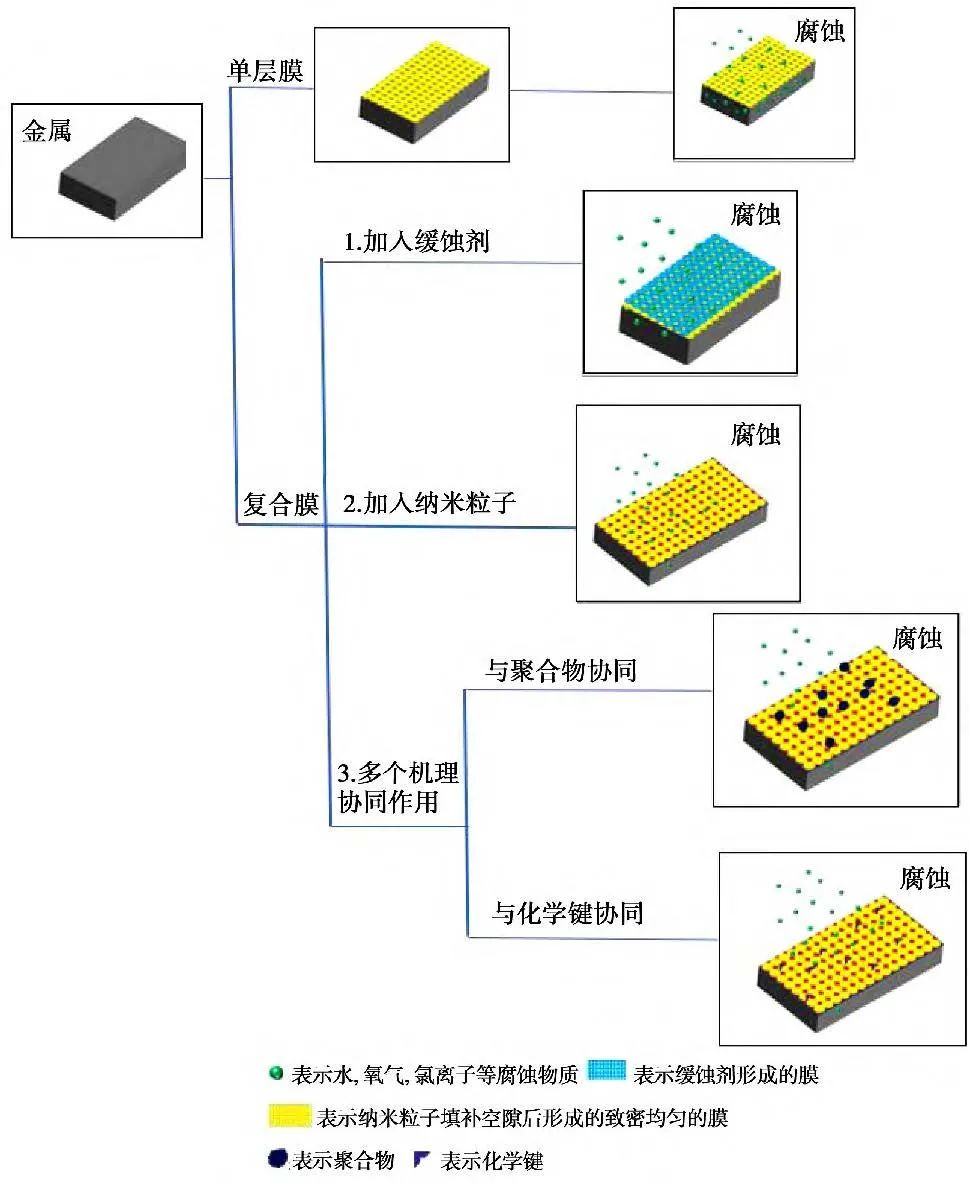
Figure 12 Schematic diagram of the composite anti-corrosion film mechanism.
In recent years, due to the increasing demands for metal surface composite film technology at home and abroad, the research on composite films has received more and more attention in both industrial and scientific fields. The main conclusions are as follows:
(1) The main preparation methods for composite anti-corrosion coatings on metal surfaces include plasma electrolytic oxidation technology, sol-gel method, and self-assembly method;
(2) In terms of performance research on composite anti-corrosion coatings on metal surfaces, hydrophobicity, antibacterial properties, and anti-corrosion are not independent of each other; hydrophobicity can effectively reduce the corrosion of corrosive substances on metal surfaces, and antibacterial properties can also prevent corrosion substances from corroding metals to a certain extent, enhancing the anti-corrosion performance;
(3) The mechanisms of action of composite anti-corrosion coatings on metal surfaces mainly include the addition of corrosion inhibitors, the addition of nanoparticles, and the synergistic effects of multiple mechanisms.
In light of this, preparing high-performance and environmentally friendly composite anti-corrosion films on metal surfaces has always been a research hotspot in the field of corrosion prevention and protection. There are still some issues to be addressed regarding the functionalization and preparation mechanisms of composite films, such as how to achieve multifunctional film materials that possess anti-corrosion, hydrophobicity, and environmental friendliness, which require further research and exploration; the research on the mechanisms of composite films is still not systematic, complete, and in-depth. Therefore, domestic scholars can further explore and study the components, preparation methods, parameter optimization, and interrelationships of various performances of high-performance and environmentally friendly composite films on metal surfaces to improve the comprehensive performance of composite films, enhance the bonding strength of composite films with metal substrates, and solve issues regarding the corrosion resistance of composite films under wide-ranging conditions.
References
[1]. Zhang N, Xiao F, Cao YQ, et al. Packaging Engineering, 2020, 41(3), 138 (in Chinese).
[2]. Zhao LB, Li QN, Hong YP, et al. Hot Working Technology, 2016, 45(12), 15 (in Chinese).
[3]. Luo HH, Cai QZ, Wei BK, et al. Acta Physico-Chimica Sinica, 2008 (3), 481 (in Chinese).
[4]. Tang YR, Pan LH, Chang Y, et al. Surface Technology, 2015, 44(2), 48 (in Chinese).
[5]. Huang WX. SiCp/IAZ91 magnesium-based composite micro-arcoxidation process and coating corrosion resistance. Master’s Thesis, Harbin Institute of Technology, China, 2008 (in Chinese).
[6]. Xu J, Liu X, Xiao QF, Lai T, et al. Materials Reports, 2018, 32(2), 249 (in Chinese).
[7]. Wang JP, Yu ZX, He J. Journal of Functional Materials, 1999 (3), 100 (in Chinese).
[8]. Li LJ, Ou XT, Chen DX, et al. Corrosion Science and Protection Technology, 2009, 21(2), 197 (in Chinese).
[9]. Lin B, Lu J. Transactions of Nonferrous Metals Society of China, 2014, (8), 2722.
[10]. Fu J, Zhang M, Jin L, et al. Applied Surface Science, 2019, 470, 543.
[11]. Wang JP, Cheng FY, Du XF, et al. Journal of Inorganic Materials, 2018, 33(6), 617 (in Chinese).
[12]. Li SY, Dong YH, Zhou Q, et al. Corrosion & Protection, 2015, 36(8), 748 (in Chinese).
[13]. Wang SC, Wang HC, Xie HH, et al. New Chemical Materials, 2019, 47(7), 82 (in Chinese).
[14]. Wang AP, Zhou AH. Periodical of Ocean University of China, 2020, 50(3), 81 (in Chinese).
[15]. Jiang F, Zhao Y, Hu JM. Surface Technology, 2020, 49(2), 109 (in Chinese).
[16]. Zhou T, Li H, Cheng L, et al. Journal of Xuzhou Institute of Technology (Natural Sciences Edition), 2019, 34(2), 1 (in Chinese).
[17]. Jin DY, Zhang XW, Fan H, et al. Fine Chemicals, 2020, 37(2), 412 (in Chinese).
[18]. Wen QC. Study on the environmental adaptability of micro-nano bacteriostatic anticorrosive coating. Master’s Thesis, Beijing University of Chemical Technology, China, 2018 (in Chinese).
[19]. Wu YN. Exploration of antibacterial and anticorrosive properties of composite coatings based on cuprous oxide. Master’s Thesis, Huazhong University of Science and Technology, China, 2016 (in Chinese).
[20]. Liu JL. Preparation and antibacterial properties of in-situ grafted quaternary ammonium salt antibacterial materials. Master’s Thesis, Southwest Jiaotong University, China, 2017 (in Chinese).
[21]. Li S, Zhang SH, Yang B, et al. China Plastics, 2018, 32(12), 1 (in Chinese).
[22]. Hara M, Ichino R, Okido M, et al. Surface & Coatings Technology, 2003, 169, 679.
[23]. Xue SQ, Ma YZ, Wu YF, et al. Speciality Petrochemicals, 2018, 35(3), 50 (in Chinese).
[24]. Feng HL, Wei ZB, Xia CF, et al. Journal of Hubei Engineering University, 2019, 39(6), 21 (in Chinese).
[25]. Gong L, Lu YP, Yu Y. Surface Technology, 2004(6), 18 (in Chinese).
[26]. Ni AQ, Zhu KK, Wang JH. Acta Materiae Compositae Sinica, 2019, 36(11), 2579 (in Chinese).
[27]. Wang X, Shi SC, Chen YX, et al. Materials Reports, 2016, 30(S2), 335 (in Chinese).
[28]. Fan YD, Guo HL, Zhang JX. In: 2018 National Academic Conference on Corrosion Electrochemistry and Test Methods. Beijing, 2018, pp.244 (in Chinese).
[29]. Wang HF, Que YS, Wu CC, et al. Plating & Finishing, 2015, 37(7), 15 (in Chinese).
[30]. Wang H, Miao CL, Chen GR. Chemical Research and Application, 2016, 28(2), 239 (in Chinese).
[31]. Liu Y, Zhou W, Liao JH, et al. New Chemical Materials, 2019, 47(11), 9 (in Chinese).
[32]. Zhao SJ, Zhang W, Deng HN, et al. Acta Physico-Chimica Sinica, 2016, 32(3), 723 (in Chinese).
[33]. Wang YJ, Zhang XF, Zhang K, et al. Coating and Protection, 2016, 37(9), 21 (in Chinese).
[34]. Huang R, Shao X, Zhang KY, et al. Paint & Coatings Industry, 2017, 47(12), 30 (in Chinese).
[35]. Zhou XS, Lei YY, Zhang XY, et al. Ordnance Material Science and Engineering, 2013, 36(3), 63 (in Chinese).
[36]. Li Xijin, Liu Xingyang, Luan Benli. Applied Surface Science, 2011, 257(21), 9135.
[37]. Alex L, Michael Z, Aleksey K, et al. Applied Surface Science, 2013, 264, 743.
[38]. Dmitry VM, Sergey LS, Igor M, et al. Applied Surface Science, 2020, 503, 144062.
[39]. Wang H, Ren F, Huang CB, et al. In: The 38th Chinese Society of Chemical Engineering Inorganic Acid and Alkali Salt Academic and Technology Exchange Conference and 2018 Annual Conference Paper Collection. Hebei, 2018 (in Chinese).
[40]. Tuan SH, MHH. Progress in Organic Coatings, 2020, 140, 105478.
[41]. Li Yufeng, Li Jiyu, Gao Xiaohui, et al. Applied Surface Science, 2018, 462, 362.
[42]. Chen X, Wen SF, Feng T, Yuan X. Progress in Organic Coatings, 2020, 139, 105374.
[43]. Nezamdoust S, Seifzadeh D. Transactions of Nonferrous Metals Society of China, 2017, 27(2), 352.
[44]. Cao XY, Du J, Yang ZM, et al. Journal of Aeronautical Materials, 2019, 39(6), 20 (in Chinese).
[45]. Du J, Wei ZM, Zheng SJ, et al. Journal of Materials Engineering, 2020, 48(2), 22 (in Chinese).
[46]. Cao ZY, Huo SJ, Wang L, et al. Plating & Finishing, 2016, 38(9), 1 (in Chinese).
[47]. Xu BH, Zhu GS, Huang C, et al. Anhui Chemical Industry, 2018, 44(5), 26 (in Chinese).
[48]. Yang Wenji, Li Tianqi, et al. Electrochimica Acta, 2016, 220, 245.
[49]. Wang Yabin, Liu Zhong, et al. Applied Surface, 2015, 356(30), 191.
[50]. Zhu Hongzheng, Yue Longfei, Zhuang Chen, et al. Surface & Coatings Technology, 2016, 304, 76.
[51]. Liu Qi, Ma Ruina, Du An, et al. Applied Surface Science, 2019, 480, 646.
[52]. Gazala R, Hema B, et al. Progress in Organic Coatings, 2014, 77(9), 1484.
[53]. Peng FZ, Li CQ, et al. Jiangxi Chemical Industry, 2020(1), 84 (in Chinese).
[54]. Conradi M, Kocijan A, et al. Applied Surface Science, 2014, 292, 432.
[55]. Ko ChiLiang, Kuo YuLin, Guo JhaoYu, et al. Japanese Journal of Applied Physics, 2018, 58(SA), SAADO3.
[56]. Wang ZH, Zhu R, Liu B, et al. China Coatings, 2019, 34(5), 9 (in Chinese).
[57]. Abdolreza Mirmohseni, Maryam Azizi, Mir Saeed Seyed Dorraji. Progress in Organic Coatings, 2020, 139, 105419.
[58]. Li Ji, Lin Kaidong, Luo Xiaohu, et al. Applied Surface Science, 2019, 480, 384.
[59]. Liang W, Xingxing D, et al. Journal of Materials Science & Technology, 2019, 9, 31.
[60]. Yangzhi G, Junaid AS, et al. Applied Surface Science, 2016, 360, 389.
[61]. Qiang Yujie, Fu Shulei, Zhang Shengtao, et al. Corrosion Science, 2018, 140, 111.
[62]. Yun Z, Yu Z, et al. Materials Chemistry and Physics, 2017, 192, 86.
63 Shan W W. Guangzhou Chemical Industry, 2019, 47(14), 17 (in Chinese).
[64]. Samadianfard R, Seifzadeh D, Habibi Yangjeh A, et al. Surface & Coatings Technology, 2020, 385, 125400.
[65]. Wang Zhi, Zhang Lei, Hu Weihong, et al. Progress in Organic Coatings, 2018, 125, 500.
[66]. Park J, Park M, et al. Surface & Coatings Technology, 2014, 258, 62.
[67]. Lu Y P, Qu Z Y, Ren Y L. The Chinese Journal of Nonferrous Metals, 1999(2), 111 (in Chinese).
[68]. Deng Qi, Li Weiping, Zhu Liqun, et al. Colloids and Surfaces A: Physiochemical and Engineering Aspects, 2018, 558, 359.
[69]. Qiu Shihui, Liu Gang, Li Wei, et al. Journal of Alloys and Compounds, 2018, 747, 60.
Source: Materials Reports
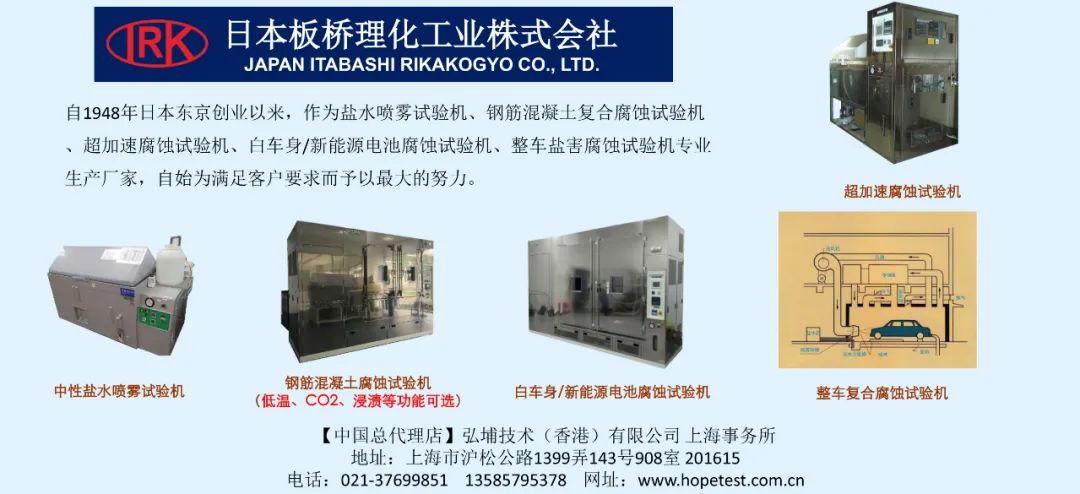
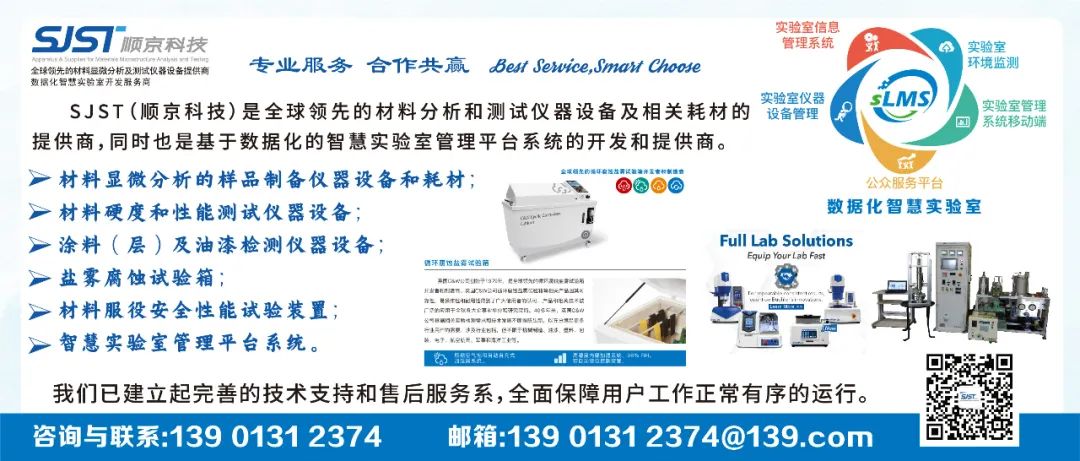
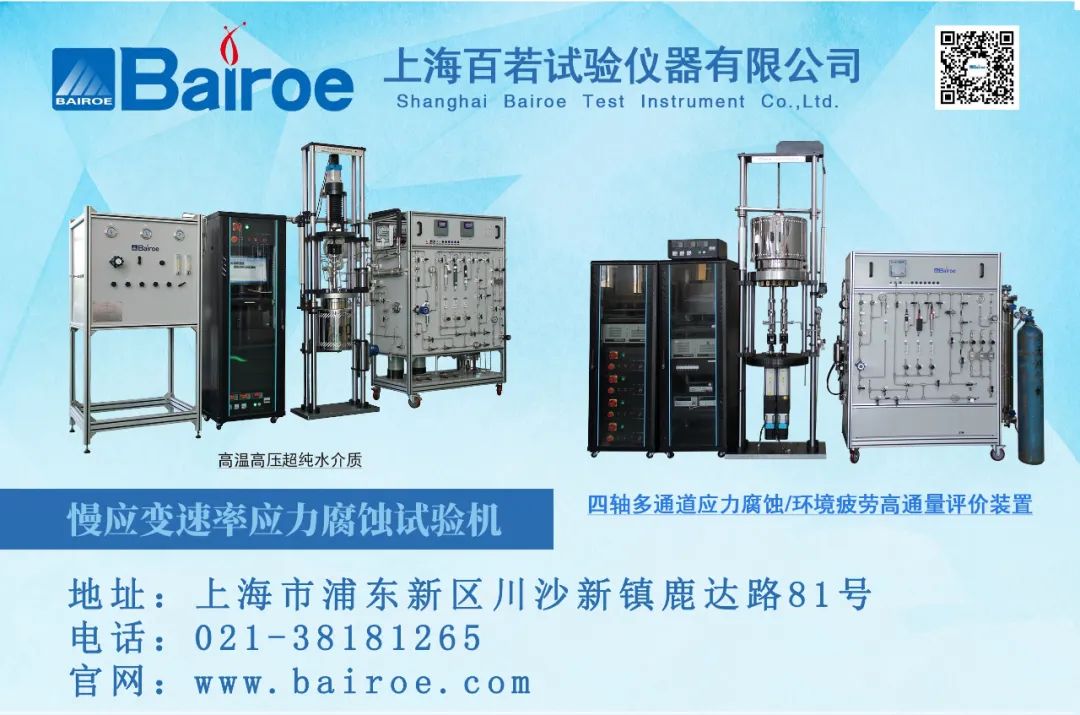