Click on the above“Zhèng Yùndòng Assistant”, stay updated with new developments!
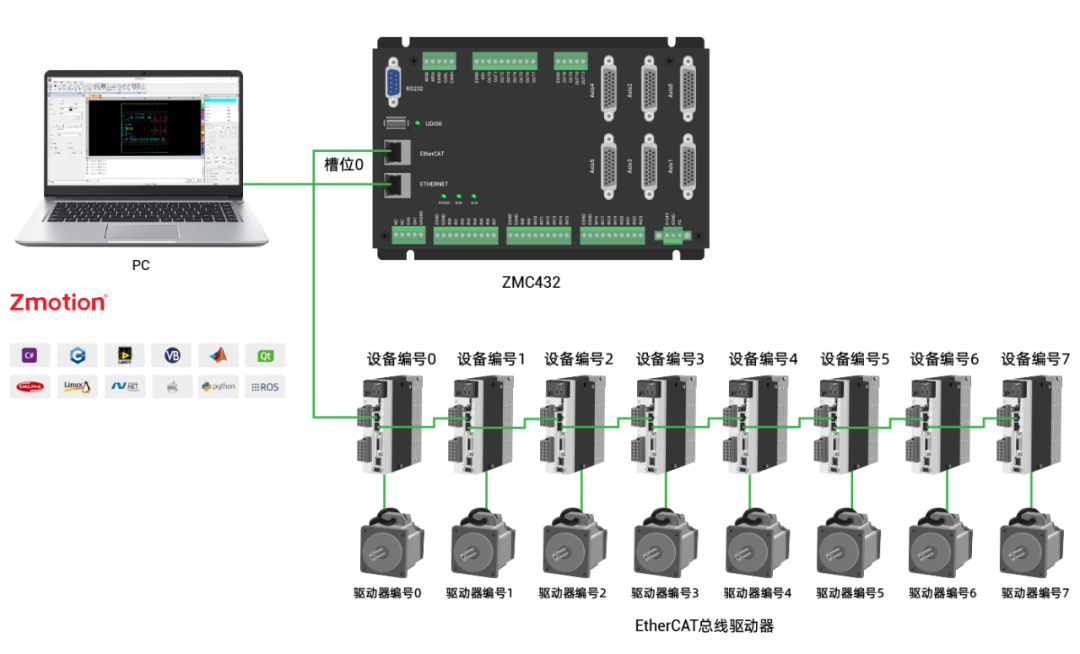
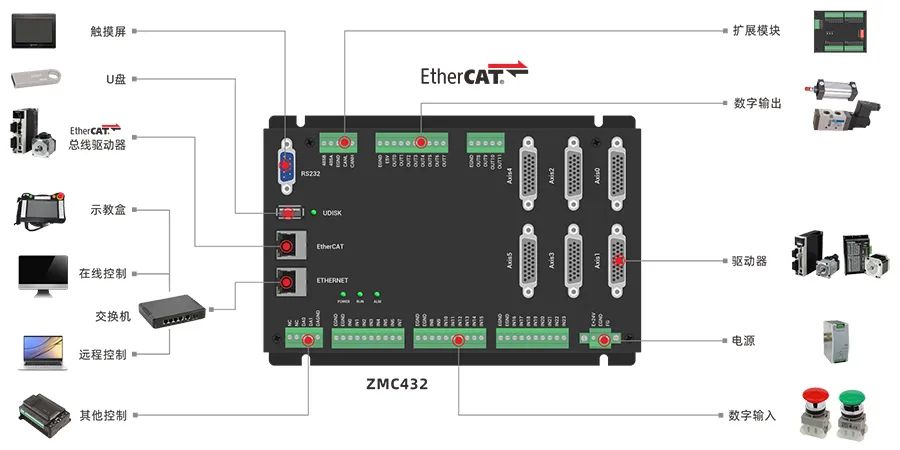
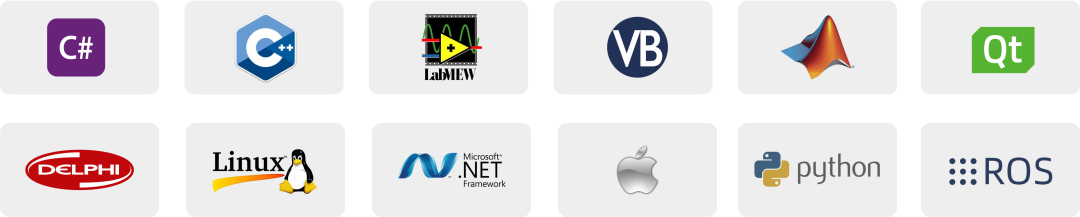
Common motion curves are divided into trapezoidal velocity curves and S-shaped velocity curves. Based on this, Zhèng Yùndòng has introduced another type of velocity curve: SS velocity curve.
1. Trapezoidal Velocity Curve
2. S-shaped Velocity Curve
3. SS Velocity Curve
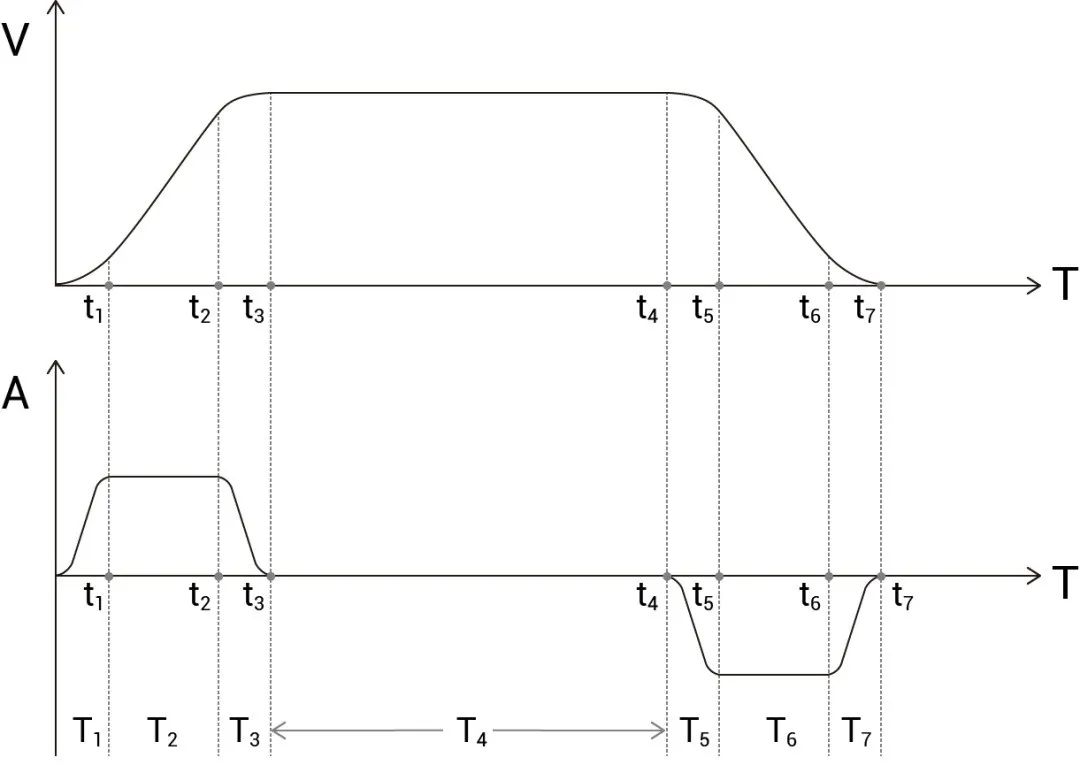
The trapezoidal velocity curve has only three stages: uniform acceleration, constant speed, and uniform deceleration. The S-shaped curve, due to its smoothing of the acceleration and deceleration stages, can be divided into seven stages, as shown in the figure below. The effective ranges of the S curve are T1, T3, T5, T7; the effective ranges of the SS curve are the same, with the difference that the acceleration changes more gently in the SS curve.
J=da/dt
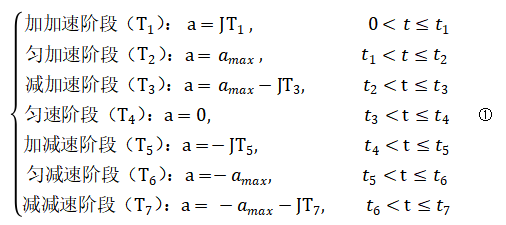
To determine the entire operation process, three basic system parameters need to be known:
1. Acceleration Time Relationship
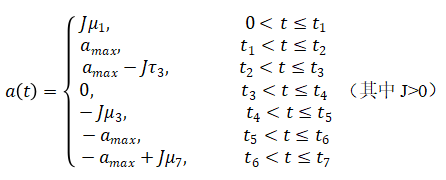
2. Velocity Time Relationship
The VP_MODE instruction can be used to set the type of acceleration and deceleration curves, with multiple modes to choose from, allowing for the setting of S-shaped curves and SS curves, making trapezoidal curves smoother. This instruction is generally used in axis parameter initialization programs and can be used together with the SRAMP instruction. When VP_MODE is set to mode 0, the values set by SRAMP take effect.
Syntax:VAR1 = VP_MODE or VP_MODE(axis)=mode
mode:Mode selection
The VP_MODE modes are as follows:
Mode |
Description |
0 |
Default value, usingSRAMP to set the S curve; |
4 |
Maximum acceleration at startup, the acceleration gradually becomes 0 when reaching maximum speed; the S and SS curve graphs are shown below. This mode is suitable for high-speed start-stop processing occasions where there are no impact requirements.
|
6 |
New type SS curve, a continuous curve type for acceleration acceleration, the SS mode increases deceleration time by 87% compared to T-shaped deceleration. This mode only takes effect during the deceleration phase; the acceleration phase takes effect in mode 0, facilitating continuous small segment interpolation; This mode is suitable for high-speed startup and smooth stopping processing occasions. ![]() |
7 |
New type SS curve, a continuous curve type for acceleration acceleration. Dynamic modification of axis parameters or continuous interpolation may cause acceleration acceleration to be non-continuous; in this case, it will switch to mode 0, so it is recommended to set appropriate values for SRAMP as well. This mode is suitable for high precision and smooth speed start-stop processing occasions without impact. |
2. Usage Examples
(1) Set VP_MODE to mode 0, taking single-axis motion as an example.
RAPIDSTOP(2) 'Stop all axes before WAIT IDLE(0) 'Wait for axis 0 to stop BASE(0) 'Set axis ATYPE=1 'Set axis type to pulse UNITS=1000 'Pulse equivalent DPOS=0 MPOS=0 SPEED=100 'Set speed to 100 ACCEL=1000 'Set acceleration to 1000 DECEL=1000 'Set deceleration to 1000 SRAMP=50 'Set S curve time to 50ms VP_MODE=0 'Set axis 0 to mode 0 TRIGGERMOVE(25) 'Single-axis motion 25 END
(2) Set VP_MODE to mode 4, taking multi-axis linear interpolation motion as an example.
RAPIDSTOP(2) 'Stop all axes before WAIT UNTIL IDLE(0) AND IDLE(1) 'Wait for axis 0 and axis 1 to stop BASE(0,1) 'Set axes, axis 0 as the main axis ATYPE=1,1 UNITS=1000,1000 DPOS=0,0 MPOS=0,0 SPEED=100,100 'Set speed for axes 0 and 1 to 100 ACCEL=1000,1000 DECEL=1000,1000 MERGE=ON 'Enable continuous interpolation SRAMP=0,0 'Do not set S curve VP_MODE=4,0 'Set axis 0 to mode 4, axis 1 to mode 0 TRIGGERMOVE(25,25) 'Interpolation motion END
Note: Since this motion is interpolation motion, axis 0 is the main axis, so just look at the velocity and acceleration curves of the main axis. The VP_ACCEL data source needs to be manually input, collecting the changes in acceleration values under the S curve and SS curve.
(3) Set VP_MODE to mode 6, taking multi-axis linear interpolation motion as an example.
RAPIDSTOP(2) 'Stop all axes before WAIT UNTIL IDLE(0) AND IDLE(1) 'Wait for axis 0 and axis 1 to stop BASE(0,1) 'Set axes, axis 0 as the main axis ATYPE=1,1 UNITS=1000,1000 DPOS=0,0 MPOS=0,0 SPEED=100,100 'Set speed for axes 0 and 1 to 100 ACCEL=1000,1000 DECEL=1000,1000 MERGE=ON 'Enable continuous interpolation SRAMP=0,0 'Do not set S curve VP_MODE=6,0 'Set axis 0 to mode 6, axis 1 to mode 0 TRIGGERMOVE(25,25) 'Interpolation motion END
When VP_MODE is set to mode 6, it only smooths the deceleration phase. When the acceleration phase is not set to S or SS curves, the acceleration reaches the maximum value instantly upon power-on and moves at the set acceleration. When the deceleration phase is set to SS curve, as shown in the figure below, the acceleration curve is smoothed during deceleration, making the motion transition more natural and smooth.
This mode is suitable for continuous interpolation occasions, improving efficiency under the condition of ensuring smooth motion.
(4) Set VP_MODE to mode 7, taking trajectory processing motion in the lithium battery industry as an example.
RAPIDSTOP(2) 'Stop all axes before WAIT UNTIL IDLE(0) AND IDLE(1) 'Wait for axis 0 and axis 1 to stop BASE(0,1) 'Set axes 0 and 1 ATYPE=1,1 UNITS=1000,1000 DPOS=0,0 MPOS=0,0 SPEED=100,100 'Set speed for axes 0 and 1 to 100 ACCEL=1000,1000 'Set acceleration for axes 0 and 1 to 1000 DECEL=1000,1000 MERGE=ON SRAMP=100,100 'Set S curve time to 100 VP_MODE=7,7 'Set axis 0 to mode 7, i.e., set SS curve TRIGGERMOVE(10,0) 'Axis 0 moves forward 10 MOVECIRC(2.5,2.5,0,2.5,0) 'Perform arc motion with a radius of 2.5 MOVE(0,10) 'Axis 1 moves forward 10 MOVECIRC(-2.5,2.5,-2.5,0,0) MOVE(-20,0) 'Axis 0 moves backward 20 MOVECIRC(-2.5,-2.5,0,-2.5,0) MOVE(0,-10) 'Axis 1 moves backward 10 MOVECIRC(2.5,-2.5,2.5,0,0) MOVE(10,0) 'Axis 0 moves forward 10 END
(5) The following is the velocity curve graph without setting the SS curve.
SRAMP=100,100 'Set S curve time to 100 VP_MODE=0,0 'Cancel SS curve
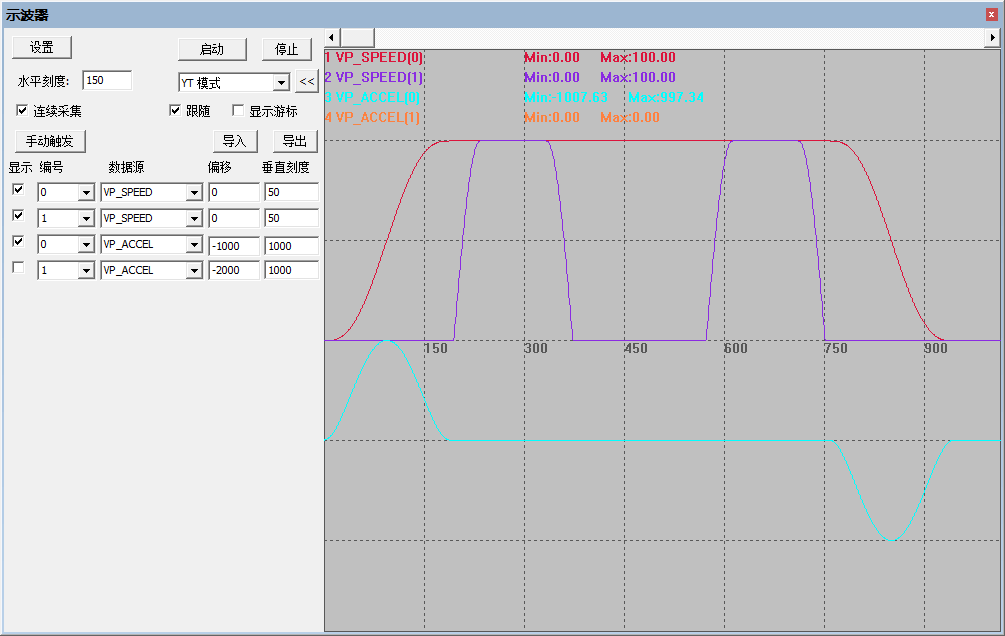
The following video is sourced from Zhèng Yùndòng Assistant
About Zhèng Yùndòng Technology
Zhèng Yùndòng Technology is backed by the rapidly developing manufacturing industry, keeping pace with the times, rich in innovation, and committed to continuously improving the technical application and manufacturing level of intelligent manufacturing equipment suppliers and end users. After years of application development with numerous partners, the products are widely used in various fields such as domestic and foreign 3C electronics, semiconductors, printing and packaging, textiles and clothing, laser processing, mechanical processing, robotics, new energy, medical care, and stage entertainment.
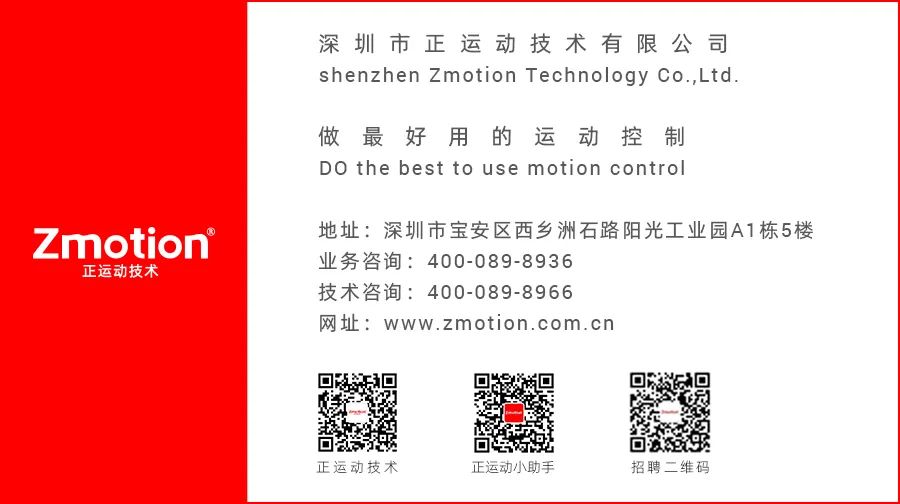
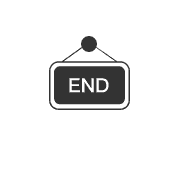