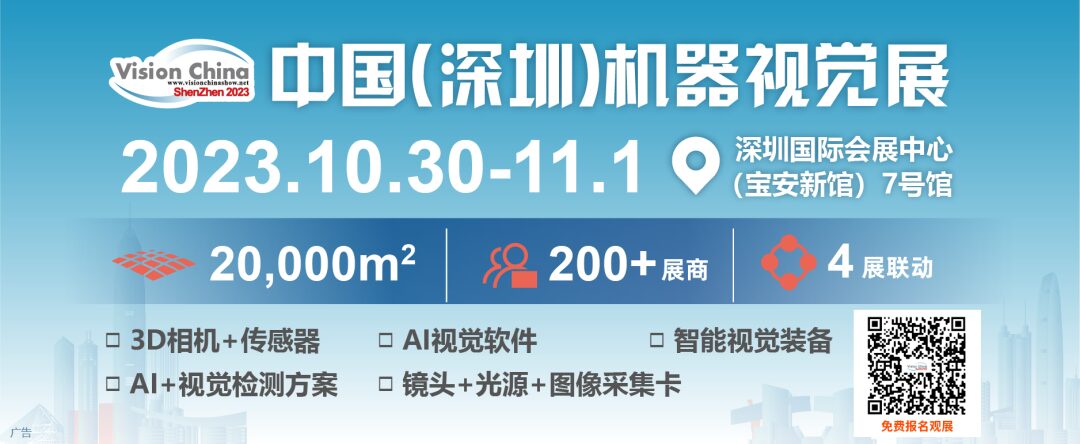
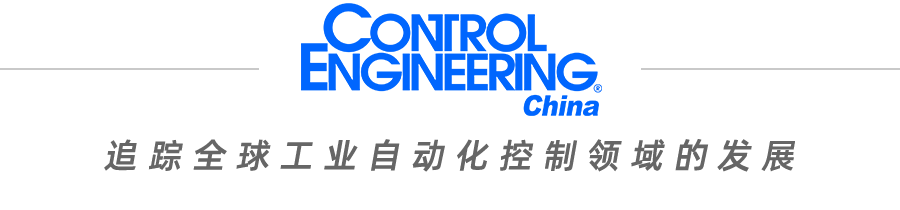
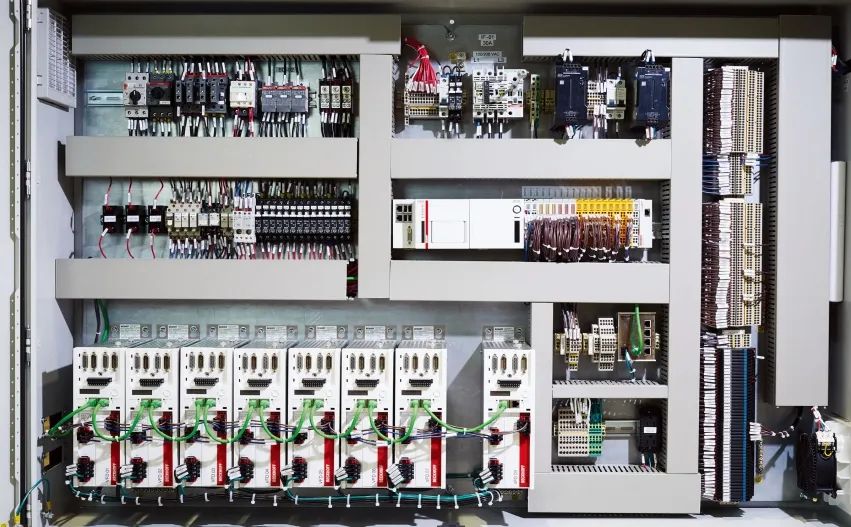
Image Source: Beckhoff Automation
Author | James Figy
By deploying EtherCAT, robotics, and AI technology, the production capacity of a sterile sampling bag factory has increased by 15% to 35% through the redesign of production machines for quality control.
Focusing on quality standards and flexibility in production is crucial for the sterile sampling industry. After all, sampling bags need to accommodate various sizes of sampling sponges, food, pharmaceuticals, or organic materials for laboratory testing to prevent contamination and ensure consumer safety.
Labplas has built a custom machine production line in its Montreal facility that not only produces standard-sized sampling bags and kits but also custom products made from various materials ranging from 3 to 33 inches wide with almost no need for conversion.
Benoit Brouillette, General Manager of Labplas, stated, “By continuously improving our systems through automation, we achieve more products and higher throughput while maintaining agility.”
The company, headquartered in Sainte-Julie, Quebec, Canada, has an independent distributor network in about 55 countries, serving customers in industries such as food, agriculture, environment, veterinary, and pharmaceuticals. Products include sterile sampling bags, testing stick kits, food industry bags, and environmentally friendly biodegradable bags.
From the first machine put into production 20 years ago to the current 24 MM series production lines, there have been multiple iterations. Christian Fontaine, head of R&D at Labplas, mentioned that several MM production lines were recently redesigned, with the engineering department adding robotics and GigE cameras to enhance output and repeatability, and AI is being deployed for better quality control. For Labplas, the key to any upgrade is the careful consideration of control platforms down to every component.
“To maintain enough diversity to produce custom products, the MM production line must remain highly complex. If you do not trust every part of the machine, you will not trust the final result,” Fontaine said.
01
Adopting Reliable, Open Technologies
The engineering team prioritized system openness, which is necessary for increasing data collection and integrating third-party components and real-time software. For instance, Labplas sought to upgrade its assembly technology to produce sampling bags and load sampling accessories such as sponges, cloths, spoons, or scissors with robotic arms.
Previously, operators needed to manually load sponges and place kits into finished open bags. To achieve the design upgrade for the MM production line, Labplas considered different types of molding, filling, and sealing, and designed a method to integrate the equipment with a 6-axis robot.
All components need to work in real-time without communication issues between different vendors while collecting and storing data on the company server or dedicated computing hardware for reporting and process improvement.
Moreover, in the upcoming complete factory renovation, the redesigned production line will serve as a model for future improvements, increasing output and making it easier for operations and maintenance personnel to transfer from one production line to another.
Brouillette said, “Our goal is to develop a standardized system where automated equipment and machines remain as fixed as possible, even though we have a multifunctional production line capable of producing over 1000 different product types.”
Since the traditional Programmable Logic Controllers (PLC) from previous suppliers could not support the requirements of robotics or AI, Labplas began seeking new partners starting in 2015. The engineering team deemed PC-based control as the best approach.
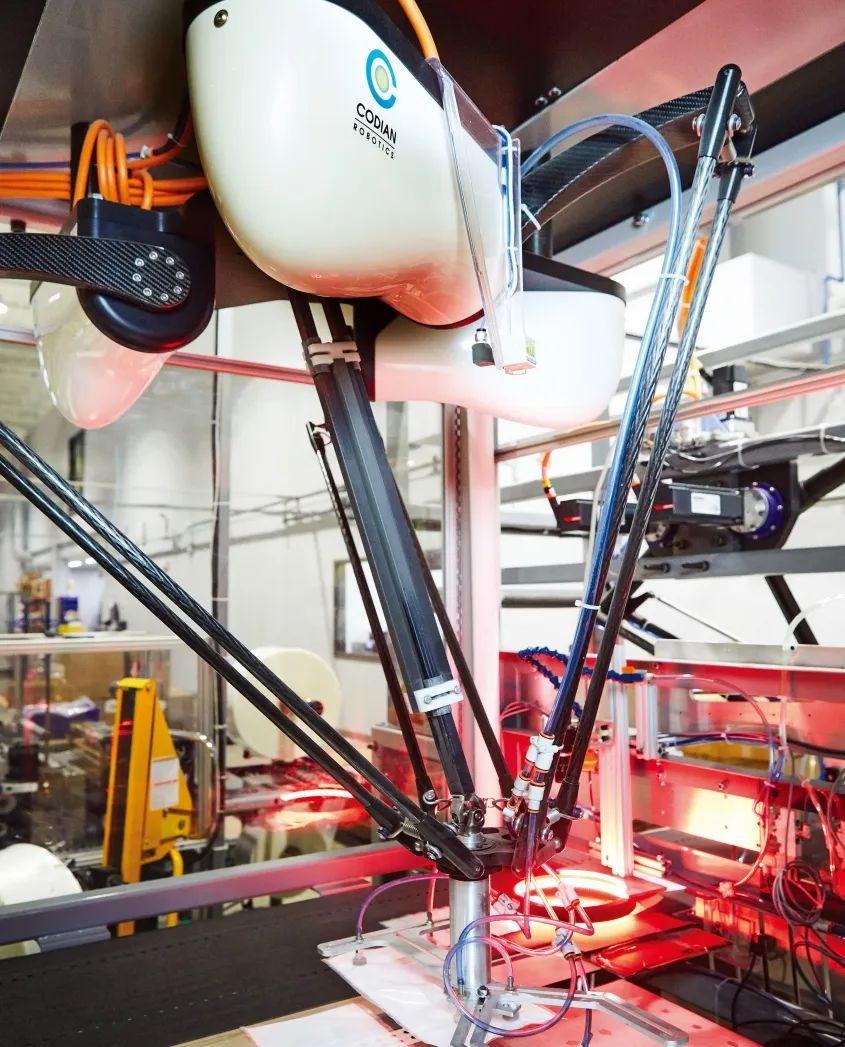
▲ Figure 2: The speed of inserting sampling tools has increased sixfold with the configured pick-and-place robot using TwinCAT software and other advanced technologies.
02
Robotics and Software Enhance Production
The design of the new machine includes multiple PC-based control solutions, motion control hardware, and general automation software with motion functionality. Labplas has equipped 15 production lines with robots. The pick-and-place robots and other motion axes are equipped with servo motors controlled by EtherCAT servo drives.
High-performance synchronous servo motors provide very low rotor inertia and very high overload capacity for dynamic applications. The design connects to the drive with a single cable, transmitting power and feedback signals in the same cable, thus reducing the number of connections. The fast control algorithms of the servo drives allow minimum current control, speed control, and position control at 62.5μs.
“Servo drives must provide extremely high precision and acceleration for servo motors, especially delta robots,” Fontaine said. Additionally, integrated functional safety drive cards with Safe Torque Off (STO) and Safe Stop 1 (SS1) functions can optionally add programmable safety I/O hardware via standard automation software.
Besides safety, the automation software also serves as a general software platform for PLC, motion control, and other requirements for the MM production line. The motion conversion feature of the software supports the design and debugging of various types of robots, including delta pick-and-place robots.
“With integrated dynamic pre-control, high-precision motion can be achieved through kinematic conversion even at high speeds and accelerations, allowing the automation software suite to control robots and machine production lines in real-time,” said Ted Sarazin, regional sales manager at Beckhoff Automation.
The software supports programming in multiple languages simultaneously, covering everything from IEC61131-3 with object-oriented extensions to C language, enabling users to use the appropriate language for each application. Free trial opportunities help determine design needs and reduce risks before purchase.
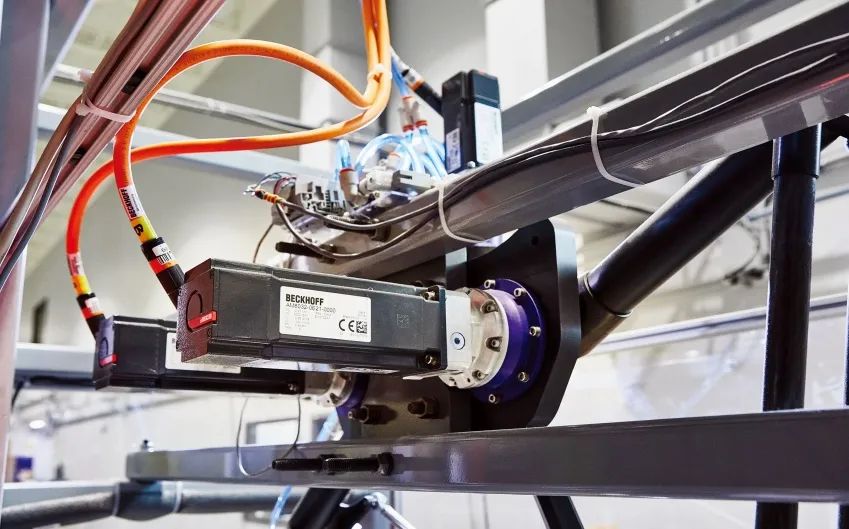
▲ Figure 3: The AM8000 servo drives provide excellent responsiveness for Codian robots.
03
Breaking Traditional Thinking in Industrial Hardware
To enhance flexibility and repeatability, the MM machine production line adopts many advanced control solutions. Engineers and operators interact with the MM machines through a built-in widescreen panel, which provides a multi-touch display hardware with an IP65 protection rating. The single-cable design integrates power, USB 3.0 signals, and DVI signals for transmission from the PC-based machine controller to the control panel, up to 100m away.
The embedded PC mounted on a DIN rail serves as the main machine controller for the advanced MM production line. This PC-based controller features a dual-core processor, which can automatically produce samples through general automation software.
These industrial-grade PCs control all automation devices, including servo drives and sensors on the MM production line. For example, in the MM9 series, the small embedded controller must provide the processing power required to drive complex machines with seven motion axes and one 5-axis and two 3-axis delta robots, and it needs CPU power for quality monitoring and potential self-repair software.
The embedded PC also provides installation and processing capabilities for third-party software running in a Microsoft Windows environment. This includes customer-customized Laplas AI applications for quality control.
04
Deploying AI Tools
“We deploy AI tools on the sampling bag production line mainly to automatically detect and handle product defects and to predict quality through device condition monitoring data from motors, sensors, and cameras, which would not be possible without strong computing power,” Brouillette said.
EtherCAT provides real-time networking and I/O solutions for the MM machine production line, further enhancing system openness. Fontaine explained that the DIN rail-mounted I/O terminals connect to the embedded PC and link to sensors, valves, terminal blocks, solid-state relays (SSR), and other devices on the MM machines.
With a single Ethernet cable, the EtherCAT protocol allows users to transfer information between components at speeds faster than controller cycles, including information required for safety functions.
05
Unlocking Future Productivity and Flexibility
By implementing PC-based open solutions, each product line achieved a return on investment in less than a year after upgrades. They also enhanced the flexibility of MM machines, enabling them to produce more specifications with less conversion work and fully leverage AI and robotics technologies to complete processes with the highest quality quickly.
“By applying AI directly on the machine for quality control, operators can focus on product supply and packaging rather than quality control. This also allows us to implement predictive maintenance to resolve any equipment and process issues before they lead to production stoppages,” Brouillette said.
In addition to improving quality assurance levels, Labplas has also increased the yield of all specification sampling bags, with the redesigned MM machines averaging a 25% increase in productivity. As bag sizes become wider, the efficiency gains slightly decrease. For example, for bags over 10 inches, productivity increases by an average of 15%, while smaller bags see a 35% increase. Additionally, by adding robots and other upgrades, the speed of inserting sampling kits on the MM8 machine has increased sixfold.
Key Concepts:
■ By leveraging PC-based control, robotics, and AI technology, users enhance efficiency and manage operational activities better.
■ Implementing PC-based open solutions has helped each production line achieve a return on investment in less than a year.
Think About:
What benefits can your factory gain from upgrading using PC-based control?
– END –
▲ This article is from the July 2023 issue of CONTROL ENGINEERING China magazine, in the column “Focusing on Machine Automation”: Improving Production Efficiency through PC-Based Control and AI Technology
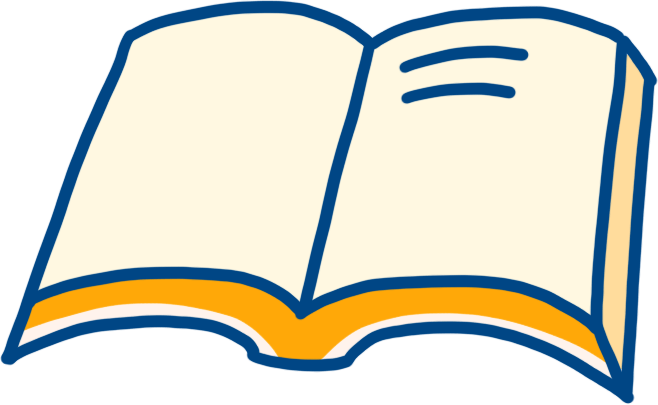
✦
Recommended Reading
✦
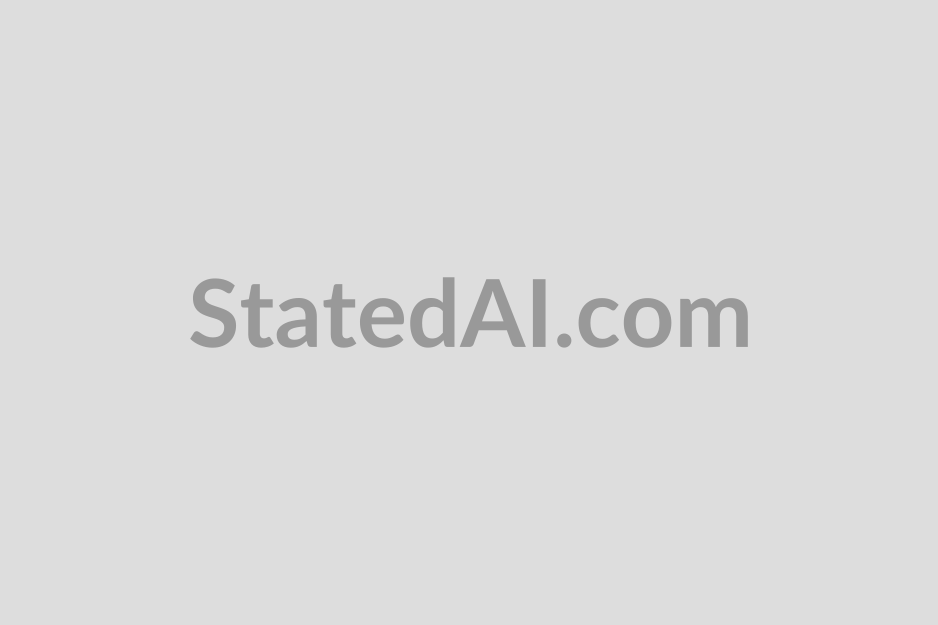
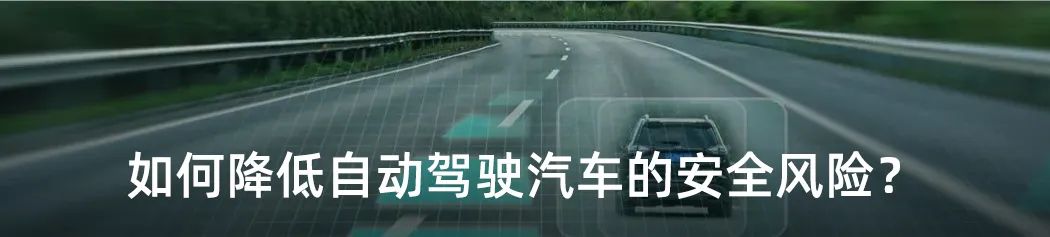
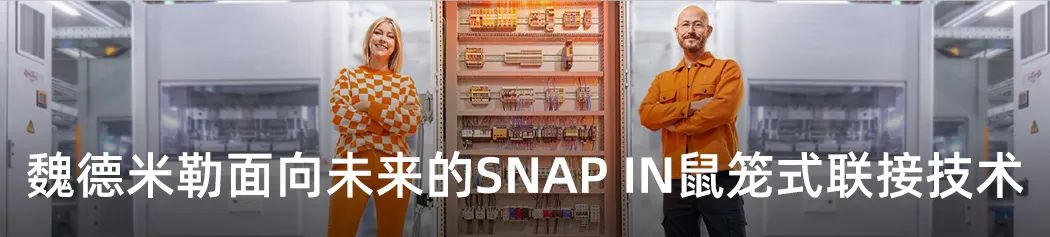
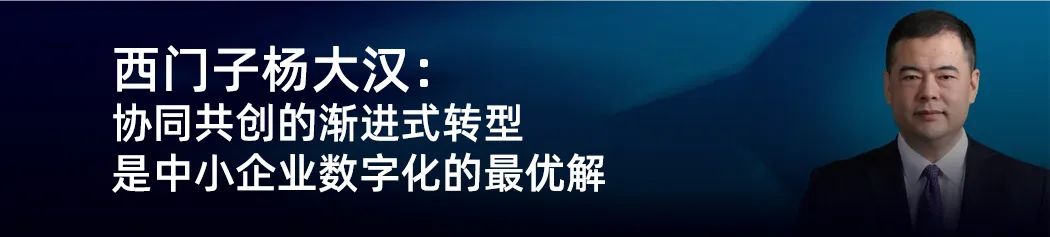
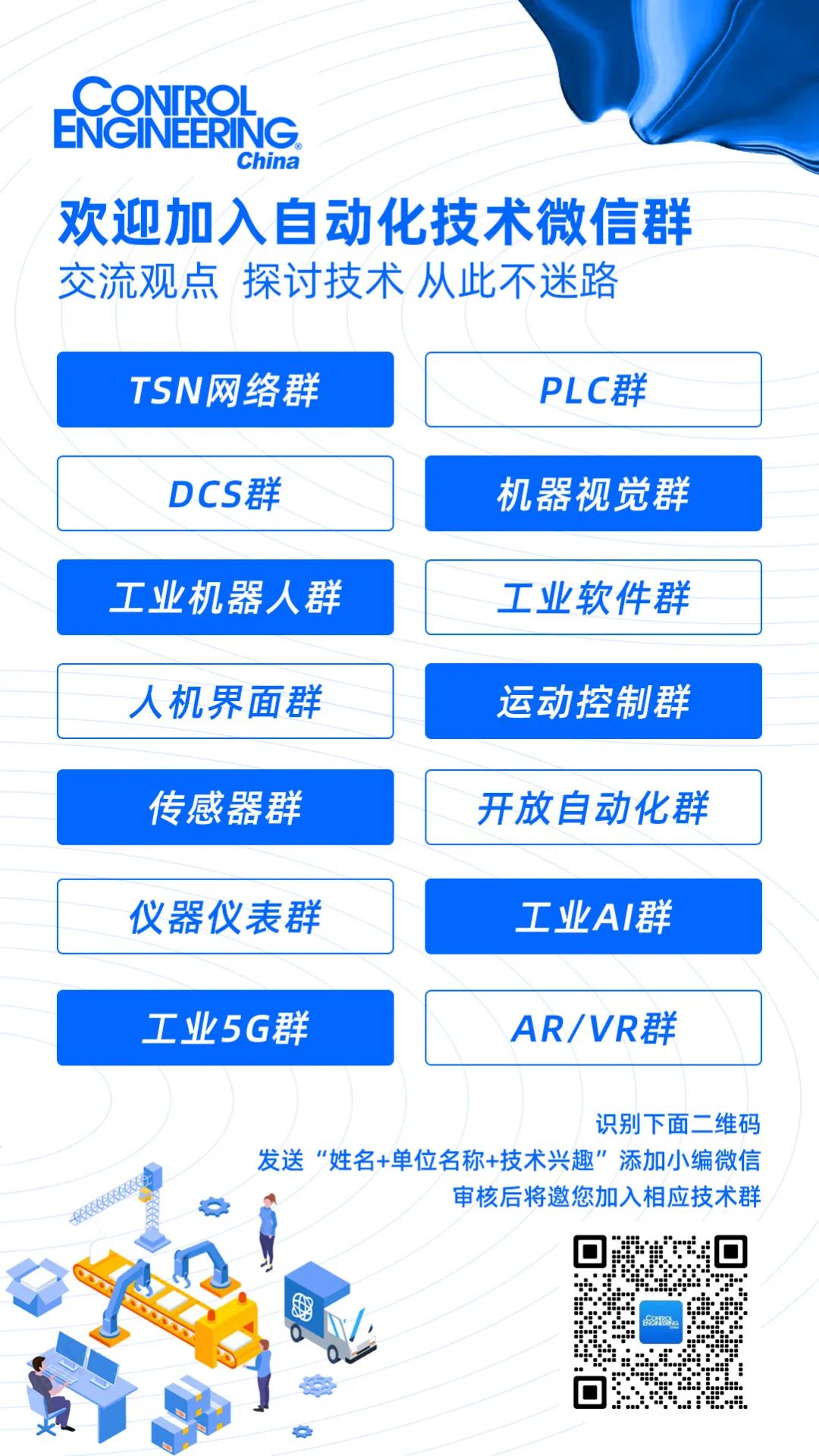
