Advertisement | Click to View
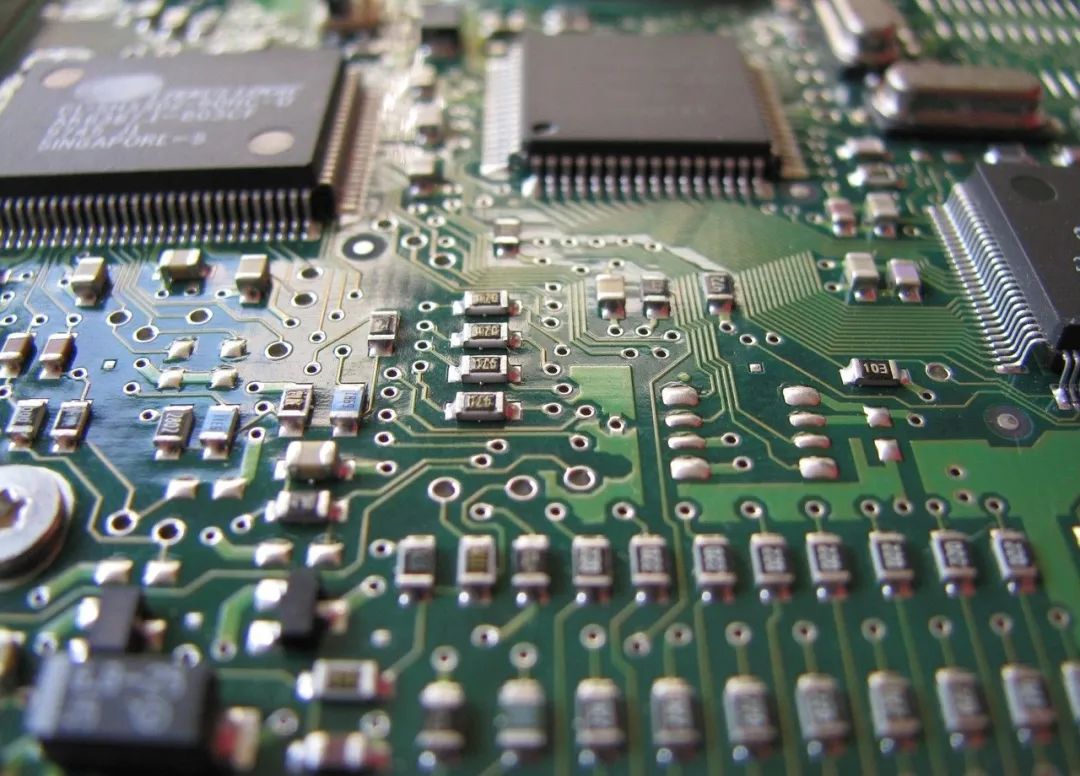
Image Source: pixabay
In recent years, the semiconductor industry has experienced significant fluctuations, partly due to its own cyclical patterns, currently in a downturn; on the other hand, global supply and demand changes have also had an impact.
At present, the semiconductor industry is generally tending towards a balance of supply and demand, with some sub-sectors even experiencing oversupply. Yan Lihong, a senior consultant at Dafu (China) Logistics Equipment Co., Ltd., pointed out: “As market expansion slows and the room for reducing manufacturing costs is limited, the semiconductor industry needs a more automated logistics model to improve efficiency and reduce costs, creating a third profit for enterprises.”
Logistics Automation
Helps Semiconductor Industry Reduce Costs and Increase Efficiency
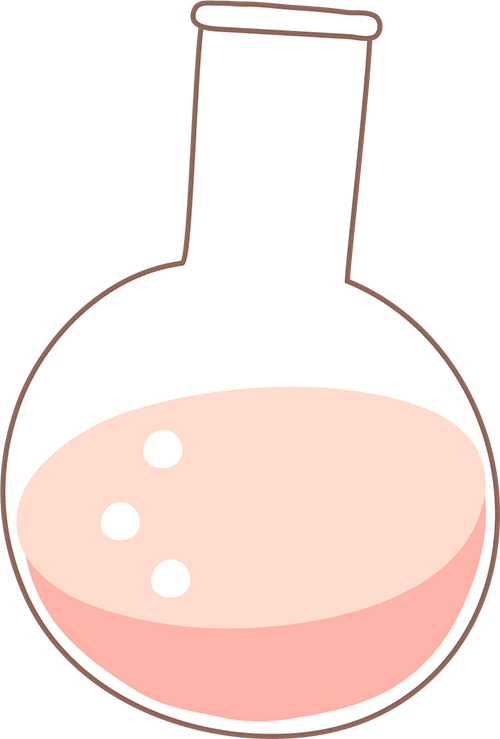
From the perspective of typical materials and applications in the semiconductor industry, material handling automation is mainly divided into two major scenarios: one is for automated material handling between semiconductor manufacturing production lines. The other is for automated storage before semiconductor products are transferred from wafer manufacturers to semiconductor manufacturers.
The former mainly involves the handling of Front Opening Unified Pods (FOUP), which are used in cleanroom environments for automated handling in dust-free workshops. Dafu utilizes an Automatic Material Handling System (AMHS) to provide automation benefits for semiconductor industry clients. The latter’s handling and storage materials are Front Opening Shipping Boxes (FOSB), which have high sealing properties to ensure internal cleanliness, allowing them to be stored in ordinary environments. Dafu uses an Automatic Storage and Retrieval System (ASRS) to meet clients’ automation needs in this regard. From the perspective of the semiconductor supply chain, the finished product of the former serves as the raw material for the latter.
Currently, whether from rough raw materials in the form of ingots to final products loaded into FOSB, Dafu has corresponding equipment to provide automation solutions for clients.
With technological development, the size of wafers has gradually increased from 150mm to 200mm and 300mm, with both size and weight becoming larger, making traditional manual and semi-automated handling increasingly difficult. Dafu’s self-developed AMHS can directly automate the transport of silicon products between production equipment, greatly enhancing efficiency. Dafu’s wholly-owned subsidiary in China, Dafu Automatic Transport Equipment (Suzhou) Co., Ltd., has delivered multiple AMHS systems to domestic wafer manufacturing and semiconductor frontend production factories, accumulating rich preliminary planning experience. Additionally, through the assembly and debugging of some equipment in the domestic Suzhou factory, it has greatly increased the flexibility of supply for domestic clients.

Correspondingly, finished products stored in FOSB enter the storage area for storage, utilizing Dafu’s ASRS, specifically employing high-speed and stable lightweight box-type stackers for storage, achieving dense storage. Compared to traditional warehouses, it has typical advantages:
Automated vertical storage controlled by a computer system can achieve automated handling at different points, greatly increasing storage capacity within the same area, creating a space advantage;
Eliminating the heavy labor of manual loading and unloading, freeing up human resources to enhance efficiency;
Achieving real-time synchronization of information, ensuring data accuracy;
Improving product safety, with multiple options to meet the cleanliness requirements of goods.
Core Equipment to Meet Cleanroom Challenges
Helps Semiconductor Industry Reduce Costs and Increase Efficiency
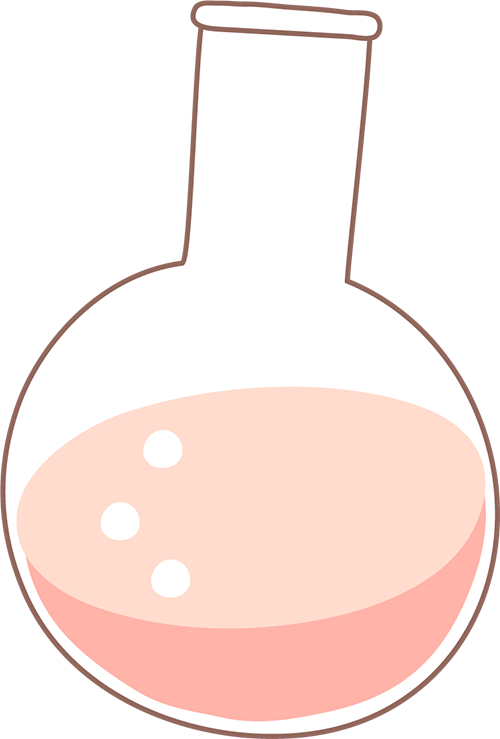
In the semiconductor industry, due to the high value of goods, clients pay the most attention to the stability of goods, with very high requirements for pollution prevention during the process, dust handling of docking equipment, and the lifting and placement of wafer materials. This poses a challenge to the stability of automated storage equipment. Based on nearly 60 years of experience in developing core storage equipment, Dafu has achieved high-precision operation of equipment and high stability in goods handling through unique technologies such as S-curve speed control and infinitely variable vector frequency control.
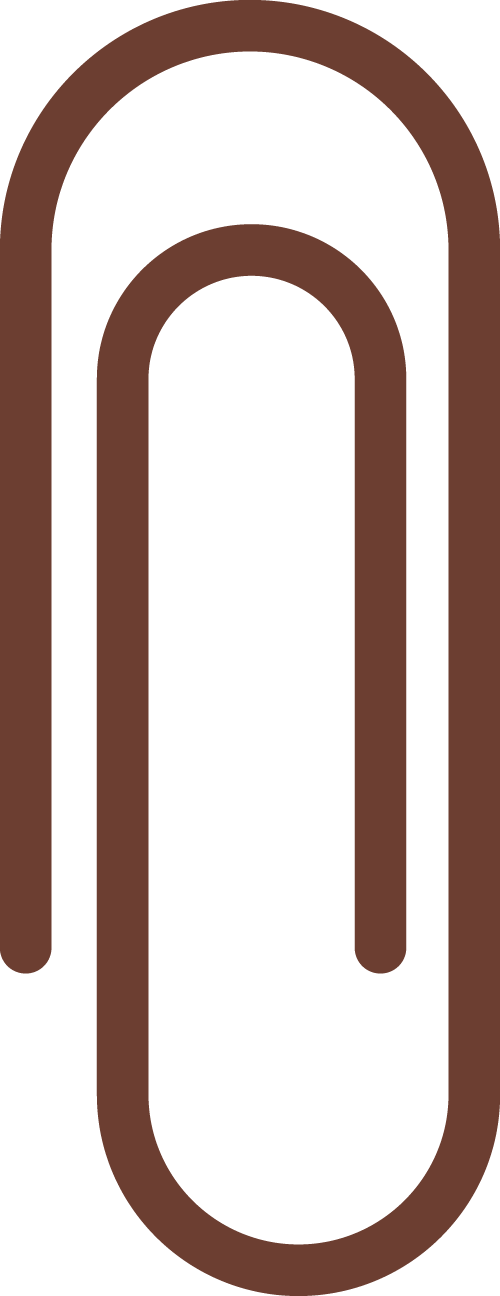
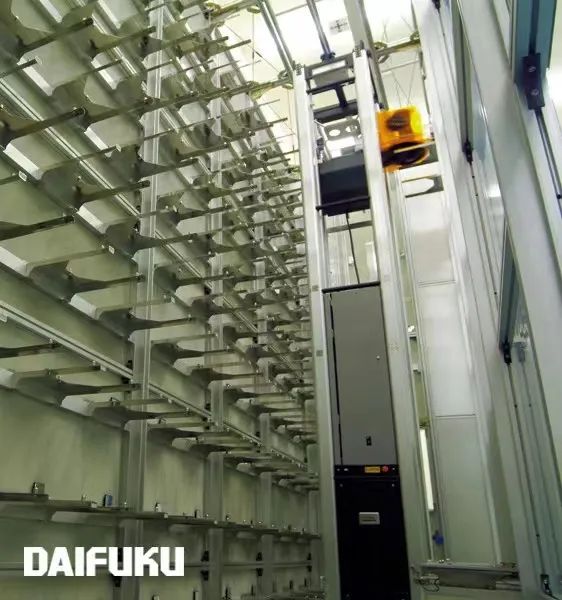
The storage and management of goods in the semiconductor industry are sensitive to cleanliness. To maintain cleanliness, it is crucial to suppress dust generation during equipment operation. Dafu’s stacking machine system has comprehensive cleanliness options, not only can some key components be upgraded to aluminum alloy materials, but it is also equipped with polymeric walking wheels, special dust-absorbing devices for electric rails, and anti-static measures for the load platform, with FUU dust-filtering devices available for both overhead and ground tracks. After equipping with these dust prevention options, Dafu’s equipment has been able to operate steadily in a Class 1000 cleanroom environment.
It can be said that Dafu has specifically developed and accumulated extensive experience in the semiconductor field. Whether it is a dust-free production workshop or automated storage in a regular environment (with optional cleanliness accessories), Dafu can provide complete automation equipment selection and customized solutions according to different client requirements.
Business Scenarios Linked
Empowering the Realization of Overall Intelligence
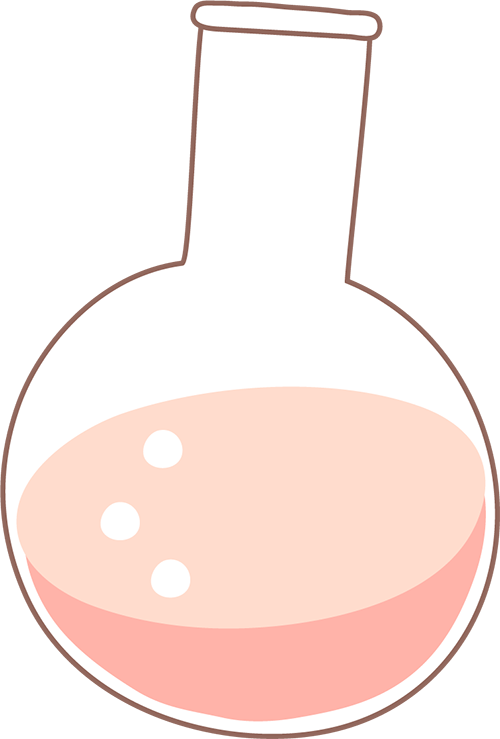
“Clients hope to connect production line handling and storage through automation, which is a challenge in the industry, but Dafu has its own divisions in both sectors and rich experience.”
Dafu has provided storage solutions for a top three wafer manufacturing company in East China, with the stored items being packaged FOSB. This project utilized Miniload lightweight stackers and box-type STV rail transport vehicles, with a travel speed of 200 meters/minute and a system operation capacity of 255 boxes/hour. In this solution, the Miniload storage system connects different functional floors through transitional areas, linking with the production workshop, providing clients with a complete automated logistics solution, achieving overall intelligence through the linkage of business scenarios.
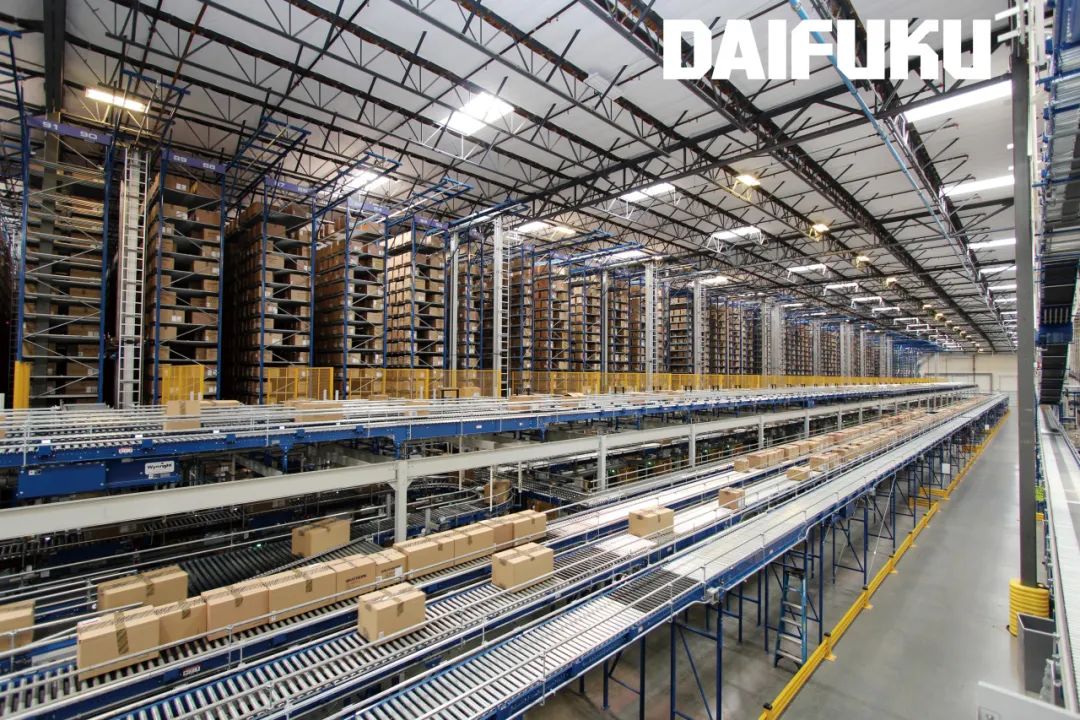

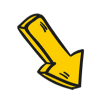
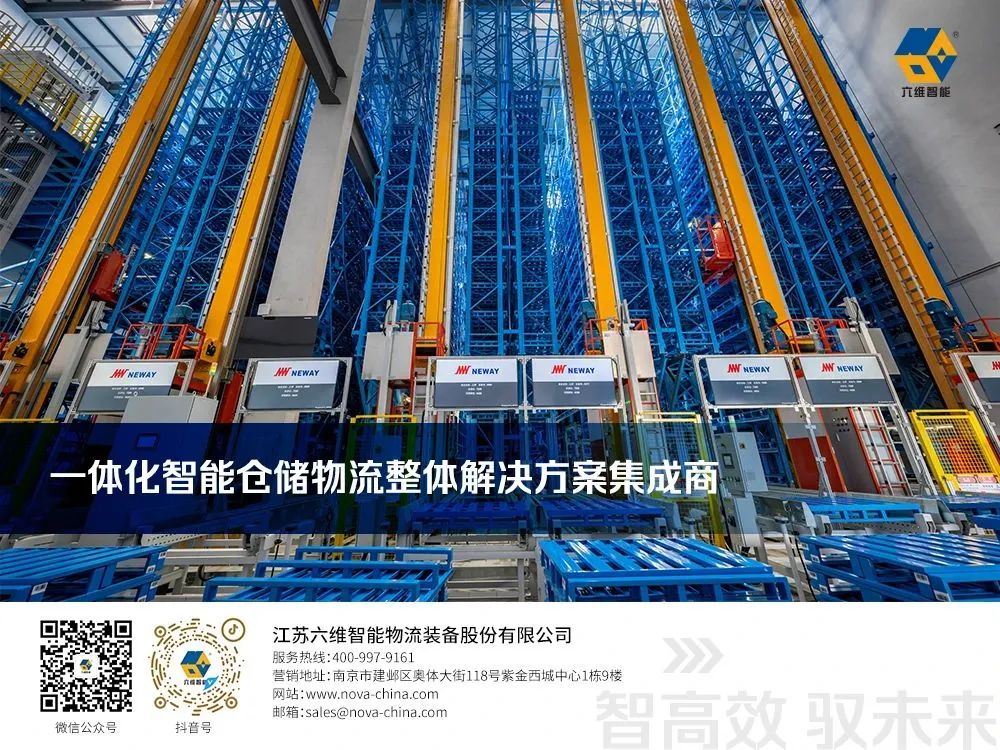
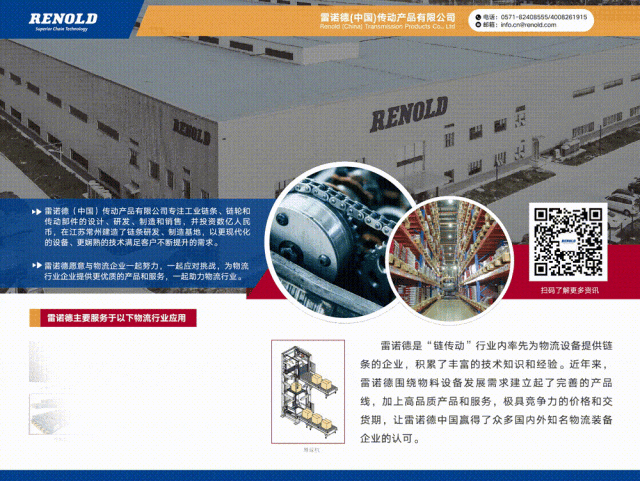

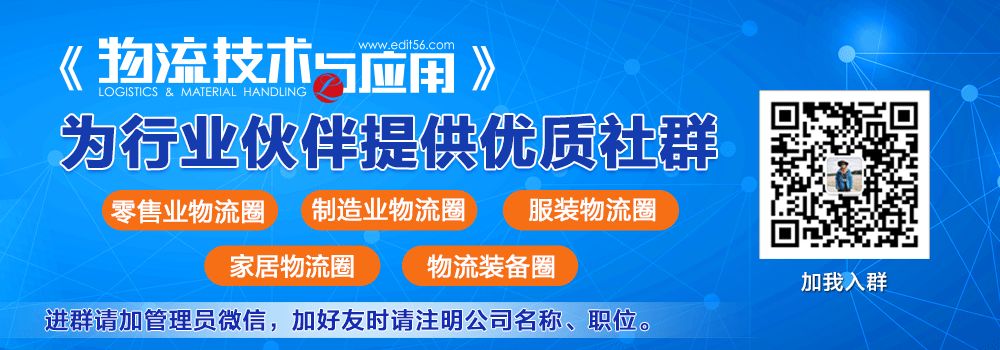