Life is like a marathon; sometimes pausing to relax helps you go further.
Common Industrial Communication Protocols
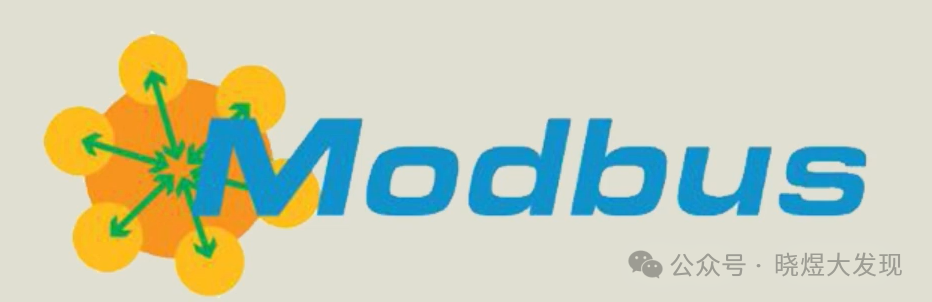
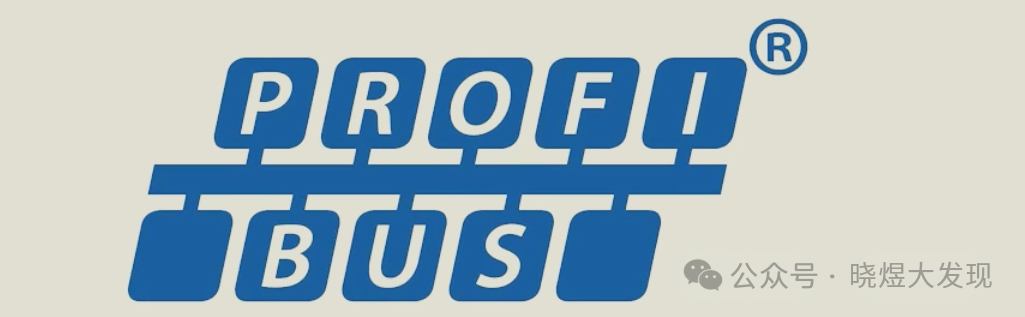
3. PROFInet Communication Protocol
Features: Uses Ethernet to transmit data, supports real-time and non-real-time communication, and can seamlessly integrate with PROFIbus.
Application Scenarios: Mainly used for production automation and machine manufacturing.
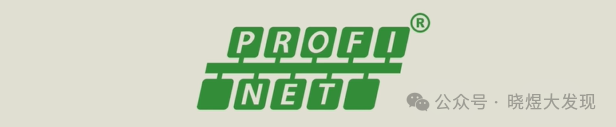
4. CANopen Communication Protocol
Features: Embedded systems, real-time data exchange, node monitoring and diagnostics.
Application Scenarios: Widely used in real-time industrial applications, robotics, medical, transportation, automotive, and aerospace fields.

5. EtherCAT Communication Protocol
Features: Uses standard Ethernet hardware, high speed, high real-time performance, supports complex topologies.
Application Scenarios: Applied in high-speed, high-performance automation systems.
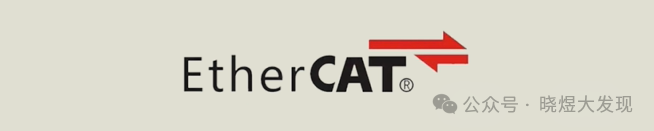
6. DeviceNet Communication Protocol
Features: Based on CAN, supports multi-master structure. Provides power and communication functions.
Application Scenarios: Mainly used for connecting industrial devices such as drives, sensors, and actuators.
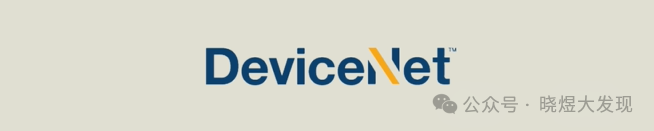
7. EtherNet/IP Communication Protocol
Features: Uses Ethernet to transmit data, supports multiple transmission rates, achieving high-speed data transmission and real-time control, supports various topologies.

8. CC-Link Communication Protocol
Features: Based on RS485 and Ethernet communication, high-speed communication, scalable and highly reliable, easy programming, but expensive.
Application Scenarios: Used in automation equipment, machine tools, robotics, PLCs, and distributed control systems.
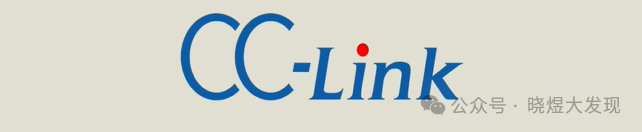
9. CC-LinkIE Communication Protocol
Features: Based on Ethernet communication, CC-Link iE protocol, transmission rate up to 1Gbps, supports 121 nodes.
Application Scenarios: Used in automation equipment, machine tools, robotics, PLCs, and distributed control systems.
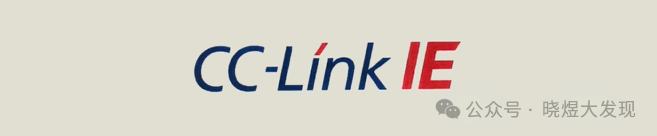
10. OPC Communication Protocol
Features: Supports various data structures and complex data types, requires more hardware and software resources, higher cost, and higher security.
Application Scenarios: Connects multiple different industrial automation devices.
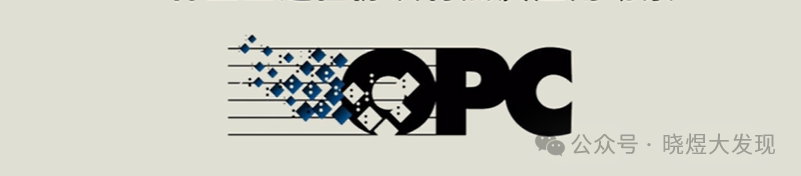
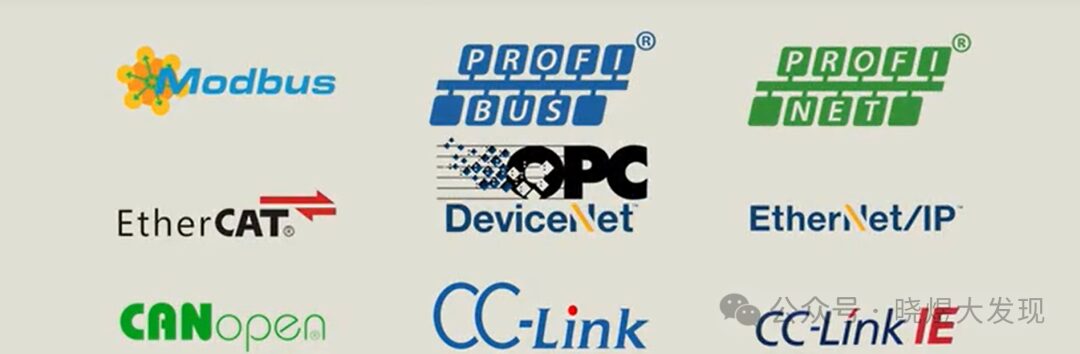
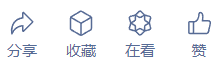
For more exciting content, follow the WeChat public account: Xiaoyu Discovery
You can also follow Xiaoyu’s recent new software sharing account, sharing fresh software every day.
If you like it, please share and give a thumbs up! Your likes are my motivation to move forward!
