
Without a doubt.
With the release of the 2020 global machine tool industry data from the World Trade Organization, China’s machine tool output and consumption reached 16.95 billion euros and 18.61 billion euros, respectively, both ranking first in the world. This reaffirms that China is a major machine tool nation since it first became the world’s output leader in 2009.
However, one cannot help but wonder, has China transitioned from a major machine tool nation to a strong machine tool nation from 2009 to 2020?
In 2008, the world’s top ten machine tool manufacturers included: Germany’s Trumpf, Japan’s Yamazaki Mazak, Germany’s Gildemeister, Japan’s Okuma, Japan’s Amada, the US’s MAG, Japan’s Mori Seiki, China’s Shenyang Machine Tool, Japan’s Jtekt, and China’s Dalian Machine Tool. Among the top ten, Germany had 2, Japan had 5, the US had 1, and China had 2.
Thirteen years later, in the world’s top ten machine tool companies, German and Japanese firms still dominate, while two of China’s mainland machine tool companies have been replaced by Taiwanese companies. Even more concerning is that the four pillar companies of China’s machine tool industry—Shenyang Machine Tool, Dalian Machine Tool, Qin Chuan Machine Tool, and Kunming Machine Tool—are heading towards a dead end. Shenyang Machine Tool and Dalian Machine Tool have both declared bankruptcy, and Kunming Machine Tool has also been delisted, leaving only Qin Chuan barely holding on, increasingly distant from the world’s top ten…
Why, despite being first in both output and consumption, is China’s machine tool industry still “big but not strong” today?

This article is an original piece from the Dongxi Think Tank, primarily based on insights from Mr. Shan Xilin, General Manager of Tonus Machine Tools for Greater China.
The machine tool industry is of great significance.
For high-tech industries, machine tools are the embodiment of modern technological processes; without advanced processing technology, there is no core competitiveness in modern manufacturing. For the country, the machine tool industry is a national heavy weapon, fundamental to nation-building; without independently innovated high-end machine tools, there is no qualification to become a world-class power.
Brief Glory
China’s machine tool industry did not start late.
After the founding of New China in 1949, based on the advice of Soviet experts, during the First Five-Year Plan, the state transformed some machine repair plants and established new enterprises, among which 18 were identified as key backbone enterprises in machine tool production, known in the industry as “The Eighteen Arhats”.
They represented the highest level of equipment manufacturing and even the entire industrial development in China at that time, and created numerous firsts in the machine tool industry: the first lathe in New China (Shenyang No. 1 Machine Tool), the first horizontal milling and boring machine (Shenyang No. 2 Machine Tool), the first CNC gantry milling machine (Qiqi No. 2 Machine Tool), and the first three-coordinate CNC gantry milling machine (Beijing No. 1 Machine Tool)…. all were masterpieces of the “Eighteen Arhats”.
In the autumn of 1958, when Kim Il-sung, Chairman of the Workers’ Party of Korea, visited Tsinghua University’s workshop accompanied by Premier Zhou Enlai, the waiting teachers and students warmly welcomed this foreign guest: not with flowers or applause, but by intently operating a complex machine tool and processing something.
Before long, a steel plate engraved with the words “Long Live Kim Il-sung” was handed to Kim Il-sung, who immediately took it with great interest, stroking it and asking questions. Then, another plate inscribed with “Long Live Chairman Mao” was handed to Premier Zhou Enlai. Chairman Kim praised this advanced technology and immediately inscribed a commemorative note. The machine that completed the engraving was China’s first CNC machine tool: X53K1.
Caption: China’s first CNC machine tool X53K1
At that time, industrialized countries that mastered the cutting-edge “CNC” technology implemented an absolute blockade against China. Without prototypes or reference technical data, a research team with an average age of only 24 years old, including professors, engineers, technicians, and students, managed to overcome one challenge after another in just 9 months using merely a single page of “for reference only” data and a schematic diagram.
Caption: Team members who designed China’s first CNC machine tool
This is undoubtedly a miracle.
It should be noted that the United States took 4 years, the UK took 2.5 years to successfully develop CNC machine tools, while Japan was still in the exploratory stage and had not fully mastered the technology.
After that, in the 1980s, Beijing University of Technology successfully developed China’s first industrial control single-board computer, and by the early 1990s, China was still closely chasing the pace of developed countries in Europe and the United States. For example, in 1987, Germany began producing five-axis machining centers and marketing them, while Shenyang Machine Tool Factory launched a “table-to-table” five-axis four-linkage machining center at the Beijing Machine Tool Exhibition in 1991.
At that time, Tsinghua University had relevant research on control systems, and Beijing University of Technology was developing the 8080 single-board computer, while the West was still dominated by Philips and Bosch systems, with Siemens not yet established.
It can be said that at that time, the gap between China and industrialized countries in the machine tool field was only about five years. However, starting in the mid-1990s, the gap between China’s machine tool industry and developed countries gradually widened.
30 Years Since the Collapse of the Soviet Union
Here, one cannot help but mention one of the biggest events of the 20th century, the collapse of the Soviet Union.
On December 25, 1991, the Soviet Union announced its dissolution, and this once superpower completely vanished from the world stage, leading to an imbalance in the global military-industrial market, which indirectly caused changes in the world machine tool industry.
Why?
Machine tools are the foundation of manufacturing, and manufacturing is the cornerstone of military industry.
The sudden change in demand in the military market led to a lack of procurement for high-end machine tools used in military supplies. In 1994, Germany’s three largest machine tool manufacturers, Deckel, Mahle, and Gildemeister, began to experience losses and bankruptcies.Prior to this, Deckel was a well-known lathe brand, Mahle was a well-known milling machine brand, and Gildemeister produced both lathes and milling machines. To save the crisis, Gildemeister merged with Deckel and Mahle to form the DMG Mori Seiki Group. The “bundling” of these three major manufacturers brought about technical and scale advantages, and driven by marketization, DMG quickly transformed technology into new productive forces, and quickly expanded in the global market.
When there is a significant change in market demand, adjustments on the supply side can bring opportunities and challenges for enterprises; if demand changes drastically, industries may even undergo reconstruction.
During this reconstruction of Western industrial power, China, far away in East Asia, had just ended its planned economic system.
In 1992, the 14th National Congress of the Communist Party of China clearly stated, “The goal of China’s economic system reform is to establish a socialist market economic system to further liberate and develop productive forces.”After the Third Plenary Session of the 11th Central Committee, China established the guidelines for the reform of state-owned enterprises, emphasizing the expansion of enterprise autonomy as the main form, adjusting the production management authority and profit distribution relationships between the state and enterprises, and establishing various forms of economic responsibility systems within enterprises.
By 1990, China’s machine tool industry had 8 comprehensive research institutes, 37 specialized research institutes, and enterprise design departments, forming a research and development system for the machine tool industry.In the wave of state-owned enterprise reform, the eighteen state-owned backbone enterprises established at the beginning of the founding of the country either reformed or reorganized due to bankruptcy, and the “Seven Institutes and One Institute” also transformed into enterprises, each seeking its own way of survival.The original machine tool research and development system was shattered.
To promote market-oriented development, in 1998, the Ministry of Machinery Industry, which had over 4,600 people and managed over 900 enterprises, was also abolished.
After the economic system reform, to produce more competitive products, some Chinese enterprises did not hesitate to introduce advanced CNC technology from Japan, Germany, and the United States at high prices to narrow the gap with developed countries.
For instance, Ji Yi Machine Tool cooperated with Japan’s Yamazaki Mazak, pioneering international cooperation in the machine tool industry. Subsequently, Shenyang No. 2 Machine Tool and Germany’s Scharmann, and Qi Yi Machine Tool and Germany’s WFL Millturn Technologies also collaborated… Learning from foreign advanced technologies allowed the “Eighteen Arhats” to gain significant strength.
This introduction was actually a double-edged sword; some enterprises obtained technology, but the original machine tool system was impacted, and the evolution of independent innovation capabilities was distorted to some extent, leading to concerns for sustainable development in the future.
In 2001, China joined the World Trade Organization (WTO), and the manufacturing industry boomed, leading to a surge in machine tool demand. As the “leader” of China’s machine tool industry, Shenyang Machine Tool seized this unprecedented good era and surged forward: in 2004, it merged with Yunji and Kunji, monopolizing the lathe and boring machine market; in 2005, it further acquired Germany’s Heller, striving to master high-end CNC technology.
In 2008, Shenyang Machine Tool and Dalian Machine Tool ranked 8th and 10th respectively in the world machine tool enterprise output ranking. Ji Er Machine Tool became one of the “three major CNC stamping equipment manufacturers” in the world, bringing China’s large automotive stamping production lines into the manufacturing workshops of Ford, Nissan North America, and Peugeot Citroen of France. Notably, in the 2012 global machine tool ranking, Shenyang Machine Tool topped the list with a sales volume of 18 billion yuan.
“Although on the surface, after 2001, China’s machine tool industry welcomed a ‘golden decade’ with a tenfold increase in total industry output, most enterprises pursued quantity and scale at the expense of technological research, and the original apprenticeship system disappeared, with workers being contract workers; excessive pursuit of economic benefits led to a loss of craftsmanship spirit. Unfortunately, the original complete industrial research system collapsed due to reforms, leaving only the aerospace and military industries with relatively complete research and development systems. This has caused the gap between China’s machine tools and advanced countries abroad to widen; what was once a 5-year gap has now become a 15-year gap.”
————Shan Xilin
However, as the Chinese market bid farewell to explosive growth and returned to a state of limited increment with fierce global competition, various shortcomings of China’s machine tool industry were once again exposed. Once fast-growing leading enterprises have quickly become negative examples of decline and have collectively entered the “farewell performance” era in recent years.
Data shows that in 2019, 15.1% of large-scale machine tool enterprises in China reported losses; in the first half of 2020, this figure further expanded to 24.1%. The former “Four Heavenly Kings” of China’s machine tool industry, the leader (Shenyang Machine Tool), the second (Dalian Machine Tool) have undergone bankruptcy restructuring, while the third (Qin Chuan Machine Tool) is also in serious losses.
Furthermore, from the industry as a whole, the localization rate of high-end CNC machine tools in China is less than 10%, with over 90% relying on imports, and China’s machine tools are completely suppressed by foreign enterprises in high-end fields. The self-sufficiency rate for five-axis and above machining centers is less than 10%, with the self-sufficiency rate for gantry machining centers and vertical machining centers even below 1%, and most materials, tools, and cooling fluids are heavily reliant on imports.
Many Hands around the Throat
The Chinese machine tool industry has reached such a conclusion for the following reasons:
1. Lack of Core Technology
In 1996, Shenyang Machine Tool spent over 100 million yuan to introduce CNC technology from the United States, but the foreign side only sent a source code data package without informing the core technology principles and usage principles, resulting in the developed CNC machine tool becoming waste; in 1999, when Dalian Guangyang imported Japanese machine tools, the Japanese side imposed a series of “unreasonable terms”: installation location and purpose had to be restricted, and unauthorized relocation of the machine tools would lead to automatic locking, rendering the machine tools worthless; in 2005, Shenyang Machine Tool bought Germany’s Heller, thinking they had obtained the technology. However, German laws stipulated that “local knowledge cannot be transferred abroad,” and technology for machine tools above five axes was embargoed against China. In 2007, Shenyang Machine Tool planned to spend 60 million euros to purchase a CNC system source code, but experts estimated that interpretation would take 5 years, and industrialization another 5 years, rendering the technology outdated.
In fact, due to political and technological security considerations, the German Federal Office for Economic and Export Control has always imposed strict restrictions on machine tool exports.
On one hand, there are strict restrictions on the precision of exported machine tools. For example, between 2013-2014, machine tools with positioning accuracy of less than 5 microns and repeat positioning accuracy of less than 2 microns could not be exported to China;On the other hand, strict limitations are placed on the usage of exported machine tools, implementing the “three no principles.” Germany stipulates that high-precision machine tools cannot be sold to military enterprises, educational institutions, and machine tool factories in China.
Japan’s Ministry of International Trade and Industry (MITI) also has similar policies, and Japanese companies have corresponding protective measures. For example, before selling machine tools, Japanese manufacturers send personnel to visit Chinese purchasing enterprises, conduct on-site inspections of workshops, take photographs, and upload GPS location data of the workshops to confirm the future working position and environment of the machine tools. If the machine tools deviate from the preset working position in the future, they will malfunction and fail to operate normally. If the purchasing party needs to move the machine tools to a new workshop, they must apply again to Japan and obtain on-site confirmation from a Japanese representative to unlock them before processing in the new workshop.
2. Suppression by Foreign Enterprises
For anything that China cannot manufacture independently, foreign brands sell at high prices or prohibit sales; for anything that China has achieved independent breakthroughs, foreign enterprises immediately resort to low-price dumping, causing Chinese enterprises’ huge research and development expenses to go down the drain. Thus, Chinese enterprises find themselves in an awkward situation of “high-end difficulties, mid-range weakness, and low-end imitation.”
In high-end sectors, Chinese machine tool enterprises do not dare to touch the demands of some high-end industries. For example, in recent main engine factory bidding processes, there are numerous strict acceptance criteria such as production specifications and CPK, CMK (CPK, Complex Process Capability index is an indicator used by modern enterprises to represent process capability. CMK, Machine Capability Index, refers to the critical machine capability index, which mainly assesses the ability of production equipment to meet requirements and stability), leading mainland manufacturers to withdraw from the competition; almost all enterprises participating in production line machine tool bidding are German, Japanese, or Swiss companies, with few Chinese mainland companies involved.
In mid-range sectors, Japanese machine tools firmly occupy China’s mid-range market due to their reliable and durable performance and relatively low prices. For example, in horizontal machining centers, companies like Mori Seiki, Yamazaki Mazak, and Okuma occupy over 80% of the market in China. In the production lines of domestic automotive brands like Geely and Great Wall, German and Japanese machine tools dominated over a decade ago.
In low-end sectors, there are numerous small and medium-sized private machine tool enterprises clustered in places like Tengzhou, Shandong (China’s small and medium machine tool capital) and Yuhuan, Zhejiang (China’s economic CNC lathe capital), caught in low-end chaos. On the other hand, large enterprises attempting to break foreign monopolies, after investing heavily in research and development, fail to generate profits, falling into the dilemma of “the more they innovate, the more they go bankrupt.”
For instance, during the rapid growth years of Shenyang Machine Tool, while sales surged, profits were minimal. Data shows that a machine tool sold for 350,000 yuan costs 280,000 yuan just for purchasing the CNC system from Germany’s Siemens or Japan’s Fanuc; adding subsequent system maintenance and upgrade costs, Shenyang Machine Tool barely made a profit. It can be said that in the low-end sector, China’s machine tool industry is overall at the stage of “still on the road to automation, with intelligence just beginning,” mainly focusing on imitation, with low technological content, low technical barriers, and fierce price wars.
3. Violation of Industrial Laws
The machine tool industry is characterized by high technical barriers, high specialization, and a need for long-term accumulation.
Germany has a complete industrial system, and its apprenticeship and dual education systems continuously provide high-quality “new blood” for manufacturing. Meanwhile, enterprises are rigorous and pragmatic, pursuing strength in “narrow fields.” On this basis, Germany has produced over 1,300 single-item champion enterprises, providing “fertile soil” for the development of Germany’s high-end machine tool industry.
Japanese enterprises value intergenerational and technical inheritance, avoiding fields they are unfamiliar with, and striving for excellence. Under this cultural dominance, Japan has a high number of long-lived enterprises, with many well-known machine tool companies having lifespans exceeding a century, passing through several generations, such as Yamazaki Mazak (founded in 1919), Fanuc (founded in 1956), Mori Seiki (founded in 1951), and Komatsu (founded in 1945).
However, Chinese machine tool enterprises, once they achieve certain results, tend to embark on the path of “seeking size and speed.” Both Shenyang Machine Tool and Dalian Machine Tool have fallen into difficult situations because of this.
For instance, Shenyang Machine Tool invested over 1 billion yuan to create the world’s first intelligent, interconnected CNC system—i5—and launched the i5 CNC machine tool after that. The then chairman of Shenyang Machine Tool Group, Guan Xiyou, even proposed to forge the i5 into the “Apple” of the machine tool industry, aiming to revolutionize the business model of the machine tool industry, but it was ultimately proven to be an overreach: by early 2016, the i5 had received 10,000 super orders, yet Shenyang Machine Tool suffered a loss of 1.4 billion yuan that year.
The reasons for the huge losses can be summarized into two points: on one hand, to quickly capture the market, Shenyang Machine Tool adopted a leasing strategy, resulting in financial losses; on the other hand, Shenyang Machine Tool also engaged in long-term investments funded by short-term debts for research and expansion. In 2017 alone, Shenyang Machine Tool implemented a debt-to-equity swap of 9.251 billion yuan but still struggled with cash flow depletion and debt crises.
Meanwhile, Dalian Machine Tool, which completed its mixed-ownership reform, not only proclaimed that it would “manufacture machine tools like making cars” but also rushed into expansion, leading to significant financial issues, ultimately resulting in hundreds of billions of debt.
4. Weak Industrial Foundation
China’s industrial foundation is weak and lacks “nutrients.” Since the late 1990s, China has lost a complete machine tool industry research and development system, severely limiting the development of China’s machine tool industry. In the upstream design and manufacturing sector, China is weak in materials, components, and experience, making it difficult to support the comprehensive independence of high-end machine tools; in the downstream application sector, high-end machine tools in China are like “scrap metal” without imported raw materials.
For example, China’s basic materials have significant gaps in uniformity and cutting performance compared to foreign materials; not only are high-end tools reliant on imports, but a large number of high-end materials in downstream applications are also heavily reliant on imports. A certain factory in Beijing once spent a large sum to purchase Swiss machine tools, but when testing with domestic materials (bars, tolerance h7 grade), after three months of attempts, they could not pass the tests. After contacting the manufacturer, they tested with Swiss materials, and everything worked normally.
In this situation of “internal troubles and external threats,” China’s machine tool industry has been rapidly surpassed by countries like Europe, the United States, and Japan, with little hope of catching up.
Dissecting the “Focal Points”
Currently, developed countries are fully leading in the machine tool industry, while we still exhibit significant shortcomings in many fundamental common areas. According to data from China’s Machine Tool Industry Association, the technological gaps between China and foreign machine tools mainly manifest in the following six aspects: processing accuracy; reliability; internal electrical, pneumatic, and control systems; processing speed; appearance; and intelligence.
1. Processing Accuracy
The machine tool is a complex electromechanical information system that is influenced by static mechanics, dynamics, vibrations, and heat during processing. Taking internal thermal effects as an example, it includes dozens or even hundreds of influencing factors such as heat generated by the motor rotating to cut magnetic lines, heat generated by friction in the screw guide movement, and heat generated during the cutting process, which can cause thermal deformation of parts and changes in the performance of tools and materials, ultimately reflected in processing errors.
Europe has already established corresponding physical models in this regard, able to simulate and analyze the sources of processing errors through high-precision simulations and compensate for them to improve processing accuracy. However, currently, Chinese enterprises have not even conducted effective research on the heat source caused by the motor’s rotation cutting magnetic lines.
2. Reliability
Germany’s DMG has a strict quality control system for its repair rates. Several years ago, the allowable annual repair rate for DMG was as low as 1.8 times/(thousand units*year), a figure at least an order of magnitude lower than China’s current repair rate.
3. Electrical, Pneumatic, and Control Systems
An effective and complete control system is a prerequisite for machine tools to achieve high processing accuracy and intelligence, and a complete and reasonable sensor system is the core hardware foundation of the control system.
German and Japanese machine tool companies have accumulated a wealth of know-how over a long development process, understanding the necessary number, types, accuracy, and installation positions of sensors. For example, DMG’s current market five-axis milling and turning center DMC 80 FD duo BLOCK is equipped with over 60 sensors, including temperature, force, vibration, lubrication flow, and cooling liquid temperature at key positions. Through sensors, the required machine tool and processing information can be precisely collected, and appropriate control methods can be used to timely complete online corrections and compensations.
4. Processing Speed
China’s slow machine tool processing speed can be partly attributed to the lack of machine tool design capabilities. Currently, there are numerous small and medium-sized factories in China, many of which still use simple machine tool equipment such as Shenyang Machine Tool Factory’s CA6150, while some famous single-item champion companies still use relatively backward CNC machine tools from the 1990s, leading to low production efficiency. Reports indicate that by 2019, all machine tool companies in Taiwan had eliminated manual machine tool production, while one-third of Shenyang Machine Tool’s production lines still produce manual machine tools priced at only 50,000 yuan, without comprehensive CNC implementation, leading to a lack of energy to tackle cutting-edge technologies, gradually being surpassed by Taiwanese and Korean machine tool companies.
In contrast, European machine tool manufacturers can design and improve machines specifically for application scenarios. For instance, Swiss machine tool manufacturer Tonus has developed numerous machining centers aimed at long slender bars and high-precision small parts in watchmaking. The machine tool used for producing automotive engine fuel injectors can complete automatic loading and unloading, processing a single fuel injector in just a few seconds, achieving an annual processing volume of several million parts while ensuring high precision and production efficiency.
5. Appearance
In the past, machine tool designs were all square and blocky, just as cars were styled over thirty years ago. However, starting in 2000, machine tool manufacturers like Germany’s DMG began inviting Italian Ferrari designers to design the machines’ appearances, highlighting streamlined designs and considering ergonomics, moving away from the “clunky” and “blocky” look. Although they still use black and dark gray colors, they have moved away from the past’s white, green, and orange color schemes, creating a high-end artistic feel that stabilizes operators’ minds and allows them to focus, no longer feeling like they are engaged in industrial processing. Although domestic machine tools in China have also improved in appearance over the years, especially in color design, streamlined designs have yet to be achieved.
6. Intelligence
Some practitioners in China’s machine tool industry still have a shallow understanding of machine tool intelligence. A senior expert in the machine tool industry publicly stated in an interview that the intelligence of his machine tool is reflected in the ability to control the machine’s operation via a mobile phone. This equation of intelligence with “remote control” is insufficient to guide breakthroughs in machine tool intelligence, achieving “self-learning, self-adaptive, self-diagnostic,” and even “self-decision-making” capabilities.
Currently, European machine tool companies are far ahead of us in intelligence. For instance, DMG’s Celos has significantly optimized human-machine interaction, modularizing machine tool functions into app-like features, allowing users to conduct programming operations more conveniently and quickly on the panel. Additionally, Celos has achieved high-precision simulation of the processing process, allowing the machining center to visualize the processing process before executing the instructions.
Some other works on machine tool intelligence require a complete sensor system as a foundation, combined with big data and artificial intelligence methods to automatically optimize processing processes, parameters, paths, and speed curves, providing early warnings for potential conflicts, and correcting for internal and external interference factors to ensure precision. However, both big data and the artificial intelligence currently applied in the machine tool field must be based on a large amount of empirical data. For instance, in optimizing tool intelligence, we can monitor the torque in real-time through sensors, and if the tool is damaged, cutting resistance and torque will increase rapidly. However, to further predict tool life and provide early warnings for wear, a large amount of torque curve data before tool wear is needed as an empirical foundation, a study that has been ongoing in Europe with significant results.
The intelligence behind machine tools is the digitalization and editability of knowledge and experience. Without a data foundation, the stability and high precision of machine tools cannot be achieved, and intelligent control is just an empty talk.
Path Forward
The machine tool industry is valued far more in Europe than in China, at least reflected in the high-level attention, industry attention, and social attention across three levels.
High-level attention is not only reflected in the usual funding for research institutes and sponsorship for enterprise research and development; the German Chancellor or President almost attends the European Machine Tool Exhibition (EMO) held in Hanover every session.
In terms of industry, the scale and professionalism of the European Machine Tool Exhibition are evident; the EMO held at the Hanover Exhibition Center has 27 venues, occupying 496,000 square meters of indoor space, nearly four times that of China’s International Machine Tool Exhibition (CIMT). Furthermore, the high ticket prices, reaching dozens of euros, limit attendance to professionals, increasing the quality of attendees. Each year, themes are proposed that highlight the development priorities of the machine tool industry.
Caption: German Chancellor Merkel attending the Hanover Industrial Exhibition in 2010
In terms of social education, Germany has a well-established multi-level education system, with apprenticeship, dual education, application technology universities, and universities providing talent assurance for industrial sectors. Factory workers enjoy generous salaries (in 2020, mechanical engineering graduates in Germany even earned more than those in IT, economics, and finance), and practitioners, students, parents, and friends all have a high recognition of workers and engineers.
However, the common characteristic of healthy development in foreign machine tool industries is a mature market environment.
From the perspective of industrial ecology, Germany has a large automotive industry, as the production of automobiles requires machine tools that can be produced on a large scale. Therefore, many machine tool factories in Germany focus on products more suitable for mass production, while Switzerland is known for its watchmaking and precision manufacturing, so Swiss machine tool factories mainly produce high-precision machine tools.
In contrast, the entrepreneurs of China’s state-owned machine tool enterprises are mostly appointed by administrative orders, and enterprise development often aims to complete political tasks.
“The domestic machine tool market in China is like an Olympic arena; essentially, it involves fierce global competition. If we want to go global, we must first achieve leadership in the domestic market.”
Shan Xilin proposed the suggestion of “three transformations and one innovation”:
1. Marketization
We must vigorously cultivate entrepreneurs, operating according to market principles. Enterprises must first become economic entities, research cutting-edge technologies, and focus on solving “bottleneck” issues, with everything centered on economic benefits. Only by ensuring product quality and solving practical problems for users can enterprises generate profits. At the same time, they must stabilize their workforce to ensure continuity.
2. Internationalization
We must select the best athletes from around the world to form a soccer team to accomplish first-class things. Internationalized enterprises require international talent; in addition to introducing a large number of talents from France, Germany, and Japan, we must also research what the markets in Germany, Japan, and Vietnam need, and consider whether we can provide good after-sales service for products sold in foreign markets, and whether we have confidence to compete with foreign enterprises on the same stage?
3. Legalization
We have much to learn regarding respect for talent and knowledge, and must operate according to market principles and national standards. We must value intellectual property and fair competition.
4. Only by relying on differentiation and innovation can we win the market
The future development direction of the machine tool industry has two main goals: “intelligent production” and “improving single-machine standards.”
“Intelligent production” means that machine tools will possess communication capabilities, enabling real-time interconnection between machine tools, other production equipment, and management centers.“Improving single-machine standards” focuses on “higher, faster, and stronger.” The development of machine tools has always revolved around enhancing precision, speed, and performance, ultimately meeting the processing needs of new materials and new industries while achieving cost reduction and efficiency improvement. Therefore, additive manufacturing, the integration and specialization of single-machine functionsare all future innovation focal points.
In summary, local machine tool enterprises must closely follow international first-class enterprises, utilize international first-class talents, and ensure that professionals handle professional matters, regardless of whether they are state-owned, private, or foreign enterprises, all must adhere to market principles.
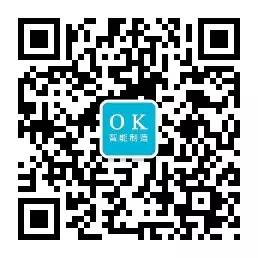
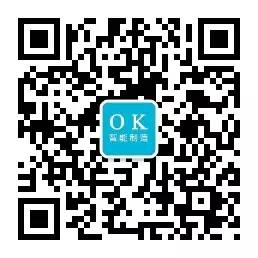
Submission Email: [email protected]
Official Website: http://www.ouzhoujc.com/
http://www.158jixie.com/