GigE Vision is a network camera interface standard based on Ethernet infrastructure and protocols. It is widely used in industrial fields. ADI’s GMSL is a point-to-point serial link technology specifically designed for video data transmission, originally intended for automotive camera and display applications.
Both technologies aim to extend the transmission distance of image sensor video data, but each solution has its own characteristics. Over the years, we have seen an increasing number of GMSL cameras adopted outside of automotive applications, often serving as alternatives to GigE Vision cameras.
Image Sensor Connection
The signal chain of a GigE Vision camera (as shown in Figure 1) typically consists of three main components: the image sensor, the processor, and the Ethernet PHY. The processor converts the raw image data from the image sensor into Ethernet frames, a process that usually involves image processing and compression or frame buffering to make the data rate suitable for the bandwidth supported by Ethernet.
Figure 1. Main signal chain components on the sensor side of GigE Vision cameras.
The signal chain of a GMSL camera (as shown in Figure 2) is typically simpler, consisting only of the image sensor and serializer. In typical applications, the serializer converts the raw data from the image sensor and then transmits it in its original format through the link. These cameras do not require a processor, making the design simpler and more suitable for applications that require small-sized cameras and low power consumption.
Figure 2. Main signal chain components on the sensor side of GMSL cameras.
Host Processor Connection
GigE Vision cameras are widely recognized in the industry for their compatibility with numerous host devices. Gigabit Ethernet ports are almost standard configurations for personal computers (PCs) or embedded platforms. Some GigE Vision cameras can use generic drivers, providing a true plug-and-play experience.
GMSL cameras require the host side to provide a deserializer. In most use cases, the host device is a custom embedded platform with one or more deserializers. The deserializer transmits image data in the raw format output from the image sensor’s MIPI using its MIPI transmitter. For such cameras, each custom camera design requires a matching driver, just like any other MIPI camera. However, if the driver for the image sensor already exists, a pair of SerDes only needs a few preset registers or to perform a few register write operations to transfer the video stream from the camera to the SoC.
When only one camera is used, GigE Vision may have some advantages in system complexity over GMSL, as it can be directly connected to a PC or embedded platform with an Ethernet port. However, when multiple GigE cameras are used, an Ethernet switch is required. This can be a dedicated Ethernet switch device, a network interface card (NIC) with multiple Ethernet ports, or an Ethernet switch IC between multiple Ethernet ports and the SoC. In some cases, this can lead to a reduction in maximum total data rate, and worse, it can introduce unpredictable latency, depending on the interface between the camera and the endpoint device. See Figure 3.
Figure 3. Typical GigE Vision network.
In a GMSL camera system, a deserializer can connect up to four links, with its MIPI C-PHY or D-PHY transmitter supporting the total bandwidth of all four cameras. As long as the SoC can handle the aggregated data rate, using one or more GMSL devices will not affect bandwidth or add excessive system complexity.
Figure 4. Typical connection from GMSL camera to host.
Sensor Interface
The GMSL serializer only supports parallel LVDS (GMSL1) and MIPI (GMSL2/GMSL3) sensor interfaces. MIPI is a widely used image sensor interface in consumer electronics and automotive cameras, allowing GMSL cameras to support a wide variety of image sensors. However, due to the internal processor used in GigE Vision cameras, they are more flexible in terms of sensor interfaces.
Operating Principle
Figure 5 shows a timing diagram example of data transmission from the image sensor to the GMSL link or GigE network in a continuous video stream.
Figure 5. Video transmission timing diagram.
In each frame of the video stream, the image sensor emits data immediately after the exposure period and then enters an idle state before the next frame begins. The example diagram better illustrates the case for global shutter sensors. For rolling shutter sensors, exposure and readout are controlled individually for each row, thus overlapping exposure and readout periods at the frame level.
The GMSL serializer on the sensor side serializes the data from the image sensor and then immediately transmits the data to the link via its proprietary protocol.
The processor in the GigE Vision camera buffers and usually processes the data from the image sensor, then arranges the video data into Ethernet frames and sends it to the network.
Link Rate
The link rate specifies the theoretical maximum speed of data transmission over the link. When comparing different data link technologies, the link rate is often a key metric. GMSL2, GMSL3, and GigE Vision all use discrete fixed link rates.
GMSL2 supports data rates of 3 Gbps and 6 Gbps. GMSL3 supports a data rate of 12 Gbps, and all GMSL3 devices are backward compatible with GMSL2 devices using the GMSL2 protocol.
GigE Vision follows Ethernet standards. GigE, 2.5 GigE, 5 GigE, and 10 GigE Vision cameras frequently appear in common applications. As the name suggests, they support link rates from 1 Gbps up to 10 Gbps. Advanced GigE Vision cameras will support link rates of 100 Gbps. For GigE Vision, all high-speed protocols will backward support low-speed protocols.
While link rate is closely related to video resolution, frame rate, and latency, it is difficult to make a direct comparison between the two technologies based solely on link rate.
Effective Video Data Rate
In data communication, effective data rate describes the data rate capacity excluding protocol overhead, a concept that also applies to video data communication. Typically, the amount of effective video data transmitted in a data packet or frame is: pixel bit depth × pixel count. Figure 6 illustrates the relationship between effective video data and overhead.
Figure 6. Payload and overhead in data frame/packet.
GMSL transmits video data in packets. GMSL2 and GMSL3 devices use fixed packet sizes, so the effective video data rate is also clearly defined. Taking GMSL2 devices as an example, when the link is set to 6 Gbps, it is recommended to use video bandwidth not exceeding 5.2 Gbps. However, since the link also carries some overhead and blanking time from the sensor MIPI interface, 5.2 Gbps reflects the aggregated data rate of all input MIPI data channels, not 5.2 Gb of video data per second.
Ethernet transmits data in frames. GigE Vision does not have a standard frame size; it is usually a trade-off for software solutions to improve efficiency (the advantage of long frames) or reduce latency (the advantage of short frames). For these cameras, overhead is typically less than 5%. Higher-speed Ethernet reduces the risk of using long frames for better effective video data rates.
Both technologies transmit data in bursts. Therefore, the average data rate over longer periods (one video frame or longer) may even be lower than the effective video data rate during transmission. For GMSL cameras, burst time only depends on the readout time of the image sensor, and in practical applications, burst ratios can reach 100% to support the full effective video data rate. GigE Vision cameras may operate in more complex and unpredictable network environments, where burst ratios are usually lower to avoid data collisions. See example in Figure 7.
Figure 7. Data flow of GMSL and GigE Vision networks.
Resolution and Frame Rate
Resolution and frame rate are two critical specifications of cameras that drive link rates higher. For these specifications, both technologies have their pros and cons.
GMSL devices do not provide frame buffering and processing. Resolution and frame rate entirely depend on the capabilities of the image sensor or the sensor-side ISP within the link bandwidth, which is often a simple trade-off between resolution, frame rate, and pixel bit depth.
GigE Vision’s models are more complex. Although in many cases its available link rate may be slower than GMSL, it can leverage additional buffering and compression to support higher resolutions and/or higher frame rates. However, all of this comes at the cost of increased latency and power consumption, and expensive components are required on both sides of the camera system. In some less common use cases, such cameras also transmit raw image data at lower frame rates.
Latency
Latency is another key specification of cameras, especially in applications where real-time data processing and decision-making are required.
The latency of a GMSL camera system from the input of the serializer/sensor output to the output of the deserializer/input to the receiving SoC is lower and deterministic.
In contrast, the latency of GigE Vision cameras is usually higher and non-deterministic due to internal processing and more complex network traffic. However, these latencies do not always lead to longer system-level latencies, especially when camera-side processing is part of a more dedicated and efficient system image pipeline.
Transmission Distance
By design, GMSL serializers and deserializers can transmit data up to 15 meters using coaxial cables in passenger vehicles. However, as long as the camera hardware system meets the GMSL channel specifications, the transmission distance is not limited to 15 meters.
Through Ethernet protocols, GigE Vision can transmit data up to 100 meters using copper cables and even farther using fiber optics, though it may lose some features such as Power over Ethernet (PoE).
PoC and PoE/PoDL
Both technologies can transmit power and data over the same cable. GMSL uses coaxial cable for power supply (PoC), while GigE Vision uses PoE for four pairs of Ethernet and Power over Data Line (PoDL) for single-pair Ethernet. Most GigE Vision cameras use traditional 4-pair lines and PoE.
PoC is straightforward, and camera applications configured with coaxial cables typically default to this method. In this configuration, power and data on the link come from a single wire, and the PoC circuit requires only a few passive components.
PoE circuits supporting 1 Gbps or higher data rates require dedicated circuits, as both the camera and host (or switch) sides need active components. This makes PoE functionality more costly and less accessible. GigE Vision cameras that support PoE typically also have local external power supply options.
Peripheral Control and System Connection
GMSL, as a dedicated camera or display link, is not designed to support a wide variety of peripherals. In typical GMSL camera applications, the link transmits control signals (UART, I2C, and SPI) and communicates only with camera peripherals such as temperature sensors, ambient light sensors, IMUs, LED controllers, etc. Larger systems using GMSL as a camera interface usually have other low-speed interfaces, such as CAN and Ethernet, for communication with other devices.
GigE Vision cameras generally utilize their built-in processors for peripheral control. As a popular connection solution in industrial applications, industrial Ethernet has various standard protocols to support diverse machines and devices, and GigE Vision cameras directly connect to networks through their software and hardware interfaces.
Camera Trigger and Timestamp
Both forward and reverse channels of the GMSL link support microsecond-level low-latency GPIO and I2C signal tunneling, enabling various camera trigger/synchronization configurations. The trigger signal source in a GMSL camera system can come from the SoC on the deserializer side or from one of the image sensors on the serializer side.
GigE Vision cameras typically provide hardware and software trigger options through dedicated pins/ports or Ethernet trigger/synchronization packets. In typical applications, hardware triggering is the standard method for responsive and accurate synchronization with other cameras or non-camera devices. The main issue with software triggering for these cameras is network latency. Although some protocols can improve synchronization accuracy, they either lack sufficient precision (Network Time Protocol (NTP), synchronized to the millisecond level) or are not cost-effective (Precision Time Protocol (PTP), synchronized to the microsecond level but requires compatible hardware).
When using synchronization protocols over Ethernet, all devices from the same network (including GigE Vision cameras) will be able to provide timestamps within the same clock domain.
GMSL does not have timestamping capabilities. Some image sensors can provide timestamps through MIPI embedded headers, but this is usually not relevant to other devices at higher system levels. In some system architectures, the GMSL deserializer connects to an SoC on a PTP network to use a centralized clock. If this feature is needed, please use AD-GMSL2ETH-SL as a reference.
In summary (see Table 1), GMSL is a strong alternative to existing GigE Vision solutions. Compared to GigE Vision cameras, GMSL cameras typically provide equivalent or better link rates and features at lower costs, lower power consumption, simpler system architecture, and smaller system sizes. Moreover, since GMSL was originally designed for automotive applications, it has been validated by automotive engineers over decades in harsh environments. In the development of systems where reliability and functional safety are critical, GMSL will provide engineers and system architects with confidence assurance.
Table 1. Comparison of Main Features between GMSL and GigE Vision
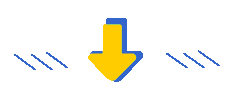

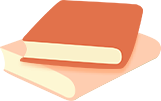
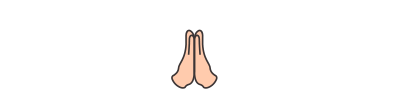