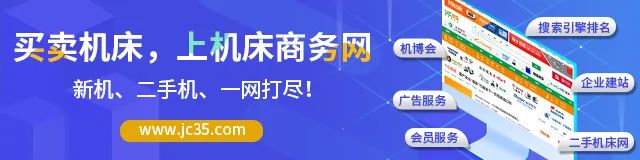
However, one cannot help but wonder, has China transformed from a major machine tool power into a strong machine tool nation from 2009 to 2020?
In 2008, the top ten machine tool producers were: Germany’s Trumpf, Japan’s Yamazaki Mazak, Germany’s Gildemeister, Japan’s Okuma, Japan’s Amada, the USA’s MAG, Japan’s Mori Seiki, China’s Shenyang Machine Tool, Japan’s Jtekt, and China’s Dalian Machine Tool. Among the top ten, Germany had two, Japan five, the USA one, and China two.
Thirteen years later, in the world’s top ten machine tool companies, Germany and Japan still dominate, while the two Chinese companies have been replaced by Taiwanese firms. More sadly, the four major pillar companies in China’s machine tool industry—Shenyang Machine Tool, Dalian Machine Tool, Qin Chuan Machine Tool, and Kunming Machine Tool—are nearing the end of the road. Shenyang and Dalian Machine Tools have declared bankruptcy, while Kunming Machine Tool has also been delisted, leaving only Qin Chuan struggling, increasingly distant from the world’s top ten…
Why is it that today, when both output value and consumption are number one in the world, China’s machine tools still remain “large but not strong”?
The machine tool industry is of great significance. For high-tech industries, machine tools are the culmination of modern process technology; without advanced processing technology, there is no core competitiveness in modern manufacturing. For the country, the machine tool industry is a national treasure, belonging to the foundation of nation-building; without independent innovation in high-end machine tools, there is no qualification to become a world-class strong nation.
China’s machine tool industry did not start late. After the founding of New China in 1949, under the suggestion of Soviet experts, during the first five-year plan, the state transformed some machine repair factories and built several new enterprises, among which 18 were identified as key backbone enterprises in machine tool production, known in the industry as the “Eighteen Arhats”. They represented the highest level of equipment manufacturing in China at that time and created numerous firsts in the machine tool industry: the first lathe in New China (Shenyang No. 1 Machine Tool), the first horizontal milling and boring machine (Shenyang No. 2 Machine Tool), the first CNC gantry milling machine (Qing No. 2 Machine Tool), and the first three-axis CNC gantry mobile milling machine (Beijing No. 1 Machine Tool)… all were the masterpieces of the “Eighteen Arhats”.
In the autumn of 1958, when Kim Il-sung, Chairman of the Workers’ Party of Korea, visited Tsinghua University’s workshop accompanied by Premier Zhou Enlai, the waiting teachers and students warmly welcomed this foreign guest: not with flowers or applause, but by intently operating a complex machine tool, processing something.
Before long, a steel plate engraved with the words “Long Live Kim Il-sung” was handed to Kim Il-sung, who immediately took it with great interest, stroking it and asking questions. Subsequently, another plate inscribed with “Long Live Chairman Mao” was handed to Premier Zhou Enlai. Chairman Kim praised this advanced technology and immediately left a note. The device that completed the engraving was China’s first CNC machine tool, the X53K1, developed jointly by Tsinghua University and Beijing No. 1 Machine Tool Factory.
Figure: China’s first CNC machine tool X53K1 in 1958
At that time, industrialized countries that mastered the “CNC” technology imposed an absolute blockade on China. Without prototypes or reference technical materials, an average age of only 24 years among researchers, including professors, engineers, technicians, and students, relied solely on a page of “for reference only” materials and a schematic diagram, successfully overcoming numerous challenges in just nine months to develop a CNC system that controlled the machine tool’s worktable, lateral saddle, and vertical milling head feed motion, achieving three-axis linkage.
Figure: Team members who designed China’s first CNC machine tool
This can’t help but be called a miracle. It’s worth noting that it took the USA four years to successfully develop a CNC machine tool, the UK two and a half years, while Japan had not yet fully mastered the technology and was still exploring.
After that, in the 1980s, Beijing University of Technology successfully developed China’s first industrial control single-board computer, and by the early 1990s, China was still closely chasing the pace of developed countries in Europe and America. Taking five-axis machine tools as an example, Germany only began producing five-axis processing machine tools in 1987, while Shenyang Machine Tool Factory launched a “table-to-table” five-axis four-linkage processing machine tool at the 1991 Beijing Machine Tool Exhibition.
In terms of control systems, Tsinghua University had already conducted relevant research at that time, and Beijing University of Technology was also developing the 8080 single-board computer, while the West was still dominated by Philips and Bosch systems, and Siemens had not yet emerged.
It can be said that at that time, the gap between China and industrialized countries in the machine tool field was only about five years. However, starting from the mid-1990s, the gap between China’s machine tool industry and developed countries gradually widened.
Here, we must mention one of the biggest events of the twentieth century: the dissolution of the Soviet Union.
On December 25, 1991, the Soviet Union announced its dissolution, and this once superpower completely disappeared from the world stage, leading to an imbalance in the global military-industrial market and indirectly causing changes in the world machine tool industry.
Why? Machine tools are the foundation of the manufacturing industry, and manufacturing is the cornerstone of the military industry. The sudden change in military market demand led to a lack of procurement for high-end machine tools used to produce military supplies. In 1994, Germany’s three largest machine tool manufacturers, Deckel, Maho, and Gildemeister, all faced losses and closures. Before this, Deckel was a well-known lathe brand, Maho was a well-known milling machine brand, and Gildemeister produced both lathes and milling machines. To save the crisis, Gildemeister integrated Deckel and Maho into the DMG Mori Seiki Group. The “bundling” of these three manufacturers brought technological and scale advantages, and driven by marketization, DMG quickly transformed technology into new productivity and rapidly expanded in the global market.
When significant changes occur in market demand, adjustments on the supply side can create opportunities and challenges for enterprises; if demand changes drastically, the industry may even undergo reconstruction.
At this time of reconstruction of Western industrial power, far away in East Asia, China had just ended its planned economy system.
In 1992, the 14th National Congress of the Communist Party of China clearly stated that “the goal of China’s economic system reform is to establish a socialist market economy system to further liberate and develop productive forces”. After the Third Plenary Session of the 11th Central Committee, China established the guidelines for state-owned enterprise reform, emphasizing the expansion of enterprise autonomy as the main form, adjusting the production management authority and benefit distribution relationship between the state and enterprises, and establishing various forms of economic responsibility systems within enterprises.
By 1990, China’s machine tool industry had eight comprehensive research institutes, 37 specialized research institutes, and enterprise design departments, forming a research and development system for the machine tool industry. In the wave of state-owned enterprise reform, the eighteen state-owned machine tool backbone enterprises established at the beginning of the founding of the country either reformed or were restructured, and “seven institutes and one institute” also transformed into enterprises, each seeking its own path. The original machine tool research and development system was shattered.
To promote market-oriented development, in 1998, the Ministry of Machinery Industry, which had over 4,600 people managing over 900 enterprises, was also dissolved.
After the economic system reform, to produce more market-competitive products, some Chinese enterprises spared no expense to import CNC technologies from Japan, Germany, and the USA to narrow the gap with developed countries.
For example, Jiyi Machine Tool first collaborated with Japan’s Yamazaki Mazak, pioneering international cooperation in the machine tool industry. Subsequently, Shenyang No. 2 Machine Tool collaborated with Germany’s Scharmann, and Qiyi Machine Tool collaborated with Germany’s Witzig & Frank… Learning from advanced foreign technologies allowed the “Eighteen Arhats” to significantly enhance their capabilities.
This introduction is actually a double-edged sword; some enterprises gained technology, but the original machine tool system was impacted, and the evolution of independent innovation capabilities was somewhat distorted, creating concerns for sustainable development in the future.
In 2001, China joined the World Trade Organization (WTO), leading to an explosive growth in manufacturing and a surge in machine tool demand. As the “leader” of China’s machine tool industry, Shenyang Machine Tool seized an unprecedented good time, advancing rapidly: in 2004, it merged with Yunji and Kunji, monopolizing the lathe and boring machine markets; in 2005, it acquired Germany’s Heller, striving to master high-end CNC technology.
In 2008, Shenyang Machine Tool and Dalian Machine Tool ranked 8th and 10th in the world machine tool company output value ranking, respectively; Jiyi Machine Tool became one of the “world’s three major CNC stamping equipment manufacturers”, allowing China’s large automobile stamping production lines to enter the manufacturing workshops of Ford, Nissan North America, and Peugeot Citroën. Notably, in the 2012 global machine tool rankings, Shenyang Machine Tool achieved a sales revenue of 18 billion yuan, becoming the world’s number one.
“Although on the surface, after 2001, China’s machine tool industry ushered in a ‘golden decade’, with the total industry output value skyrocketing tenfold, most enterprises focused solely on quantity and scale, placing technological research second. Moreover, the original apprenticeship system disappeared, and workers became contract workers, overly pursuing economic benefits, which led to the loss of craftsmanship spirit. Even more regrettably, the original complete industrial research system collapsed due to the reform, leaving only the aerospace and military research and development systems relatively intact. As a result, the gap between China’s machine tools and advanced countries has widened; originally, the gap might have been five years, but now it has widened to 15 years.”
————Dan Xilin
However, as the Chinese market bid farewell to explosive growth and returned to a state of limited growth with fierce global competition, various shortcomings in China’s machine tool industry were once again exposed. Once rapidly developing leading enterprises have quickly become the fastest-declining negative examples, collectively entering the “farewell performance” era in recent years.
Data shows that in 2019, 15.1% of China’s large-scale machine tool enterprises reported losses; in the first half of 2020, this figure further expanded to 24.1%. The former “Four Heavenly Kings” of China’s machine tool industry, the leader (Shenyang Machine Tool), the second (Dalian Machine Tool) declared bankruptcy restructuring, and the third (Qin Chuan Machine Tool) is also facing severe losses.
Moreover, from the perspective of the entire industry, the localization rate of high-end CNC machine tools in China is less than 10%, with over 90% relying on imports. China’s machine tools are completely suppressed by foreign enterprises in high-end fields. The self-sufficiency rate of five-axis and above processing centers is less than 10%, and the self-sufficiency rate of gantry processing centers and vertical processing centers is even less than 1%, with most materials, tools, and coolants relying on imports.
The Chinese machine tool industry has faced the following reasons for such results:
1. Core Technology Deficiency
In 1996, Shenyang Machine Tool spent over 100 million yuan to introduce CNC technology from Bridgeport, USA, but the foreign side only sent a source code data package without disclosing core technological principles and usage principles, resulting in the developed CNC machine tools becoming waste; in 1999, when Dalian Guangyang imported Japanese machine tools, the Japanese side imposed a series of “unfair clauses”: the installation location and usage must be limited, and any unauthorized movement of the machine tool would cause it to automatically lock, turning it into scrap iron; in 2005, Shenyang Machine Tool bought Germany’s Heller, thinking they had acquired the technology. Unexpectedly, German laws stipulated that “local knowledge cannot be transferred abroad”, and technology for five-axis and above machine tools was also embargoed against China. In 2007, Shenyang Machine Tool planned to spend 60 million euros to buy a set of CNC system source code, but experts estimated that interpretation would take five years, and industrialization another five years, making the technology obsolete.
In fact, due to political and technological security considerations, the Federal Office for Economic Affairs and Export Control of Germany has always imposed strict restrictions on machine tool exports.
On the one hand, strict restrictions are placed on the precision of exported machine tools. For example, in 2013-2014, machine tools with positioning precision less than 5 microns and repeat positioning precision less than 2 microns could not be exported to China; on the other hand, strict restrictions are imposed on the intended use of exported machine tools, following the “three no principles”. Germany prohibits the sale of high-precision machine tools to China’s military enterprises, educational institutions, and machine tool factories.
Japan’s Ministry of International Trade and Industry (MITI) has similar policies, and Japanese companies have corresponding protective measures. For example, before selling Japanese machine tools, they would send personnel to visit Chinese purchasing enterprises, conduct on-site inspections of the workshop, take photos, upload the workshop’s GPS location, and confirm the future working position and environment of the machine tools. If the machine tool deviates from the preset working position in the future, it would malfunction and cease to work normally. If the purchasing party needs to move the machine tool to a new workshop, they would need to apply again to Japan and obtain on-site confirmation from a Japanese representative to unlock it before processing in the new workshop.
2. Suppression by Foreign Enterprises
For anything that China cannot manufacture independently, foreign brands sell at high prices or ban sales; for anything that China achieves independent breakthroughs, foreign enterprises immediately resort to low-price dumping, causing Chinese enterprises to waste huge amounts of research and development costs. As a result, Chinese enterprises find themselves in an awkward situation of “high-end difficulties, mid-range weaknesses, and low-end imitation”.
In high-end fields, Chinese machine tool enterprises dare not even touch the demands of some high-end industries. For instance, in recent bidding processes for mainframe manufacturers, there were numerous strict acceptance criteria for production programs and CPK, CMK (CPK, Complex Process Capability Index, is a modern enterprise indicator used to represent process capability. CMK, Machine Capability Index, refers to the critical machine capability index, which mainly evaluates the ability of production equipment to meet requirements and stability), leading mainland manufacturers to retreat in difficulty. The enterprises participating in the bidding for production line machine tools were almost all German, Japanese, or Swiss companies, with occasional appearances by Taiwanese and Korean enterprises, but very few mainland Chinese enterprises participated in bidding.
In mid-range fields, Japanese machine tools firmly occupy China’s mid-range market with their reliable and durable performance and relatively low prices. For example, in horizontal machining centers, Japan’s Mori Seiki, Yamazaki Mazak, and Okuma occupy over 80% of China’s market. In the production lines of domestic automobile brands like Geely and Great Wall, the market has long been dominated by German and Japanese machine tools.
In low-end fields, on one side, there are numerous small and medium-sized private machine tool enterprises clustered in places like Tengzhou (China’s small and medium-sized machine tool capital) and Yuhuan (China’s economic CNC lathe capital), engaged in low-end mixed battles; on the other side, there are large enterprises attempting to break foreign monopolies, but after investing heavily in research and development, they fail to generate profits, falling into the dilemma of “the more they innovate, the more they go bankrupt”. For instance, during the rapid development years of Shenyang Machine Tool, despite a surge in sales, profits were minimal. Data shows that a machine tool sold for 350,000 yuan incurs a cost of 280,000 yuan just for purchasing the CNC system from Germany’s Siemens or Japan’s Fanuc; when adding subsequent system maintenance and upgrade costs, Shenyang Machine Tool has little to no profit. It can be said that in the low-end field, China’s machine tool industry is overall still in the stage of “still on the road to automation, with intelligence just beginning”, mainly focused on imitation, with low technical content, extremely low technical thresholds, and a fierce price war.
3. Violation of Industrial Rules
The machine tool industry is characterized by high technical thresholds, high professional division of labor, and the need for long-term accumulation. Germany has a complete industrial system, and its apprenticeship and dual education systems continuously provide high-quality “fresh blood” for the manufacturing sector, while enterprises are rigorous and pragmatic, pursuing strength in “narrow fields”. On this basis, Germany has produced over 1,300 single-item champion enterprises, providing fertile soil for the development of Germany’s high-end machine tool industry.
Japanese enterprises emphasize generational inheritance and technological transmission, avoiding fields they are not familiar with, and striving for perfection. Under this cultural dominance, Japan currently boasts a high number of long-lived enterprises, with 3,900 existing long-lived enterprises. Many well-known machine tool companies have been in existence for over a century, surviving several generations, such as Yamazaki Mazak (established in 1919), Fanuc (established in 1956), Mori Seiki (established in 1951), and Komatsu (established in 1945).
In contrast, Chinese machine tool enterprises, once they achieve certain results, tend to adopt a “greedy and fast” approach, leading Shenyang Machine Tool and Dalian Machine Tool into difficult situations of “irreversible doom”.
For example, Shenyang Machine Tool invested over 1 billion yuan to create the world’s first intelligent, interconnected CNC system—i5 and launched the i5 CNC machine tool. The then-chairman of Shenyang Machine Tool Group, Guan Xiyou, even proposed to forge i5 into the “Apple” of the machine tool industry, aiming to revolutionize the business model of the machine tool industry. However, it ultimately proved to be a step too far: by early 2016, i5 had received 10,000 super orders, but that year, Shenyang Machine Tool suffered a loss of 1.4 billion yuan.
The reasons for the huge losses concentrated on two points: on the one hand, to quickly capture the market, Shenyang Machine Tool adopted a strategy of renting instead of selling, resulting in unsustainable costs; on the other hand, Shenyang Machine Tool long-term engaged in short-term debt for long-term investment in research and development and expansion. In 2017 alone, Shenyang Machine Tool implemented a debt-to-equity swap of 9.251 billion yuan, still struggling to resolve cash flow exhaustion and debt explosions.
Meanwhile, Dalian Machine Tool, which completed its mixed ownership reform, not only touted “making machine tools like making cars” but also rushed into expansion, leading to significant financial issues and ultimately creating a debt hole of hundreds of billions.
4. Weak Industrial Foundation
China’s industrial foundation is weak, and its “nutrients” are scarce. Since the late 1990s, China has lacked a complete machine tool industry research and development system, severely restricting the development of China’s machine tool industry. In the upstream design and manufacturing sectors, China is weak in materials, components, and experience, making it difficult to achieve full independence in the high-end machine tool field; in the downstream application sector, high-end machine tools in China are as useless as “scrap metal” without imported raw materials.
Taking materials as an example, China’s basic materials have significant gaps in uniformity and cutting performance compared to foreign ones. Not only does China rely on imports for high-end tools, but a large number of high-end materials in the downstream application sector also heavily rely on imports. A factory in Beijing once spent a fortune to purchase Swiss machine tools, but when testing with domestic materials (rod materials with a tolerance of h7), after three months of attempts, they could not pass the test. After contacting the manufacturer, the factory used Swiss materials for processing tests, and everything worked fine.
In this context of “internal troubles and external threats”, China’s machine tool industry has been rapidly left behind by Europe, America, and Japan, struggling to catch up.
Currently, developed countries are fully ahead in the machine tool industry, while we still show obvious shortcomings in many basic common areas. According to data from China’s Machine Tool Industry Association, technically, the gaps between China’s machine tools and foreign ones mainly manifest in the following six aspects: processing accuracy; reliability; internal electrical, gas, and control systems; processing speed; appearance; and intelligence.
1. Processing Accuracy
Machine tools are complex electromechanical information systems that are influenced by statics, dynamics, vibration, and heat during processing. Taking internal thermal influence as an example, it includes dozens or even hundreds of influencing factors such as heat generated by the rotation of the motor cutting magnetic lines, heat generated by friction of the screw guide rail movement, and heat generated during the cutting process, which can lead to thermal deformation of parts, changes in tool and material performance, and ultimately result in processing errors.
Europe has already established corresponding physical models in this regard, able to simulate and analyze the sources of processing errors through high-precision simulation methods and compensate for them to improve processing accuracy. However, currently, Chinese enterprises do not even have effective research on heat sources such as heat generated by the motor’s rotation cutting magnetic lines.
2. Reliability
Germany’s DMG has a strict quality control system for return rates. Several years ago, DMG’s allowable annual return rate had dropped to 1.8 times per (1,000 units per year), a figure at least an order of magnitude lower than China’s current return rate.
3. Electrical, Gas, and Control Systems
An effective and complete control system is a prerequisite for machine tools to achieve high processing accuracy and intelligence, while a complete and reasonable sensor system is the core hardware foundation of the control system.
German, Swiss, Japanese, and American machine tool companies have accumulated a wealth of know-how over the long development process, understanding the number, types, precision, and installation locations of the sensors required. Taking DMG’s current five-axis milling and turning processing center DMC 80 FD duo BLOCK as an example, a single machine is equipped with over 60 sensors, including temperature, force, vibration, lubrication flow, and coolant temperature at critical points. Through these sensors, the required machine tool and processing information can be accurately collected and timely corrected and compensated through appropriate control methods.
4. Processing Speed
China’s slow processing speed can be partially attributed to the lack of machine tool design capabilities. Currently, there are many small and medium-sized factories in China, many of which still use simple machine tools like the CA6150 from Shenyang Machine Tool Factory. In some well-known single-item champion companies, many of the machines used are outdated CNC machines from the 1990s, leading to low production efficiency. Reports indicate that by 2019, all machine tool companies in Taiwan had eliminated manual machine production, while one-third of Shenyang Machine Tool’s production lines still produce manual machine tools priced at only 50,000 yuan, lacking full CNC capabilities, which prevents them from focusing on cutting-edge technology and gradually being surpassed by Taiwanese and Korean machine tool companies.
In contrast, European machine tool manufacturers can design and improve machines targeted at application scenarios. For example, Switzerland’s famous machine tool manufacturer Tonors has developed numerous processing centers for long slender rods and high-precision small parts in watches. The machine tool used to produce automotive engine fuel injectors can automatically load and unload, processing a single injector in just a few seconds, achieving millions of parts processed annually while ensuring high precision and production efficiency.
5. Appearance
In the past, machine tool designs were all square and boxy, just like cars over thirty years ago. However, starting in 2000, machine tool manufacturers such as Germany’s DMG began inviting Ferrari car designers to design the appearance of their machines, emphasizing streamlined shapes and considering ergonomic applications, moving away from the “bulky” and “boxy” designs of the past. Although Chinese machine tools have also made progress in appearance improvements over the years, they have yet to achieve streamlined designs.
6. Intelligence
Some practitioners in China’s machine tool industry still have a shallow understanding of machine tool intelligence. A senior expert in the machine tool industry publicly stated in an interview that the intelligence of their machine tools is simply reflected in the ability to control the machine’s operation via a mobile phone. This simplistic view of intelligence as “remote control” is insufficient to guide China in breaking through in the field of machine tool intelligence and achieving “self-learning, self-adaptive, self-diagnostic,” and even “self-decision-making” capabilities.
Currently, European machine tool companies have significantly outpaced us in intelligence. Taking DMG’s Celos as an example, this machine can greatly optimize human-machine interaction, modularize machine functions, and develop them into app-like functionalities, allowing users to carry out processing programming operations more conveniently and quickly on the panel. Moreover, Celos has achieved high-precision simulation of the processing process; when the processing center receives processing instruction segments, it can first visualize the processing process through modeling simulation for the operator.
Other aspects of machine tool intelligence require building on a complete sensor system, layering with big data and artificial intelligence methods to automatically optimize processing processes, parameters, paths, and speed curves, providing early warnings for potential conflicts, and correcting and compensating for internal and external interference factors to ensure precision. However, both big data and artificial intelligence applications in machine tools currently rely on a wealth of experience data. For example, in the case of intelligent optimization of tools, we can monitor the torque in real-time through sensors and detect damage through torque monitoring. However, if we want to further predict tool life and provide early warnings for wear, we need a large amount of torque curves before tool wear as experience, which has been extensively researched and achieved in Europe.
The intelligence behind it is the digitization and editability of knowledge and experience. Without a data foundation, the stability and high precision of machine tools cannot be achieved, and intelligent control is just an empty phrase.
The machine tool industry in Europe is valued far more than in China, at least reflected in the levels of attention from high-level officials, the industry, and society.
The attention from high-level officials is not only reflected in the regular funding of research institutes and sponsorship of enterprise research and development; the German Chancellor or President almost attends the European Machine Tool Exhibition (EMO) held in Hannover every session.
At the industry level, just taking the scale and professionalism of the European Machine Tool Exhibition as an example, the EMO held at the Hannover Exhibition Center has 27 venues, occupying 496,000 square meters of indoor venue space, nearly four times that of China’s International Machine Tool Exhibition (CIMT). At the same time, the ticket price of several tens of euros also limits the scope of professionals, increasing the range of exhibition visitors. Moreover, themes are proposed each year, highlighting the key development points of the machine tool industry.
Figure: German Chancellor Merkel attending the Hannover Industrial Exhibition in 2010
At the social education level, Germany has a complete and sound multi-level education system, including apprenticeship, dual education, and universities, providing talent assurance for various positions in the industrial field. Factory workers enjoy generous salaries (in 2020, the salary of mechanical engineering undergraduates in Germany even exceeded that of IT, economics, and finance), and practitioners, students, parents, and friends all have a high recognition of workers and engineers.
However, the common feature of healthy development in foreign machine tool industries is a mature market environment.
From the perspective of industrial ecology, Germany has a large automotive industry, as automobile production requires machine tools that can be produced on a large scale. Thus, many machine tool manufacturers in Germany focus on products suitable for mass production, while Switzerland is renowned for its watchmaking and precision manufacturing, leading Swiss machine tool manufacturers to primarily produce high-precision machines.
In contrast, the entrepreneurs of state-owned machine tool enterprises in China are mostly appointed by administrative means, and enterprise development is often guided by the completion of political tasks.
“The domestic machine tool market in China is like an Olympic arena, essentially a fierce global competition. If we want to go out, we must first achieve leadership in the domestic market.”
Dan Xilin offered the suggestion of “three transformations and one innovation”:
1. Marketization
We should vigorously cultivate entrepreneurs and operate according to market rules. Enterprises must first become economic entities, delve into cutting-edge technologies, and focus on solving “bottleneck” issues, centering everything on economic benefits. Only by ensuring good product quality and solving real problems for users can enterprises generate profits. At the same time, it is essential to stabilize the employee team to ensure continuity.
2. Internationalization
We need to assemble the best athletes from around the world to form a football team to achieve top-tier results. Internationalized enterprises require internationalized talents. Besides bringing in a large number of talents from France, Germany, and Japan, we also need to study what the German, Japanese, and Vietnamese markets need and consider whether we can provide good after-sales service when selling products in foreign markets and whether we have the confidence to compete with foreign enterprises.
3. Legalization
We lag behind in respecting talents and knowledge; we must act according to market rules and national standards. We must emphasize intellectual property rights and fair competition.
4. Only through differentiation and innovation can we win the market
The future development direction of the machine tool industry includes “smart production” and “increasing single-machine standards”.
“Smart production” means that machine tools will have communication capabilities, achieving real-time interconnectivity between machine tools, other production equipment, and management centers. “Increasing single-machine standards” focuses on “higher, faster, stronger”. The development of machine tools has always revolved around the enhancement of three core indicators: precision, speed, and performance, ultimately aiming to meet the processing needs of new materials and new industries while reducing costs and improving efficiency. Therefore, additive manufacturing, the compound and specialization of single-machine functions, are all future innovation focal points.
In summary, local machine tool enterprises must keep a close eye on international first-class enterprises, utilize international first-class talents, and let professionals handle professional matters. Whether state-owned, private, or foreign enterprises, they must adhere to market rules.
–END–
➽ Source: Crazy Mechanical Control
Disclaimer: If there are copyright issues with the videos, images, and texts used in this article, please inform us promptly. We will confirm copyright based on the proof materials you provide and pay remuneration according to national standards or immediately delete the content!
Please follow the Machine Tool Business Network video account