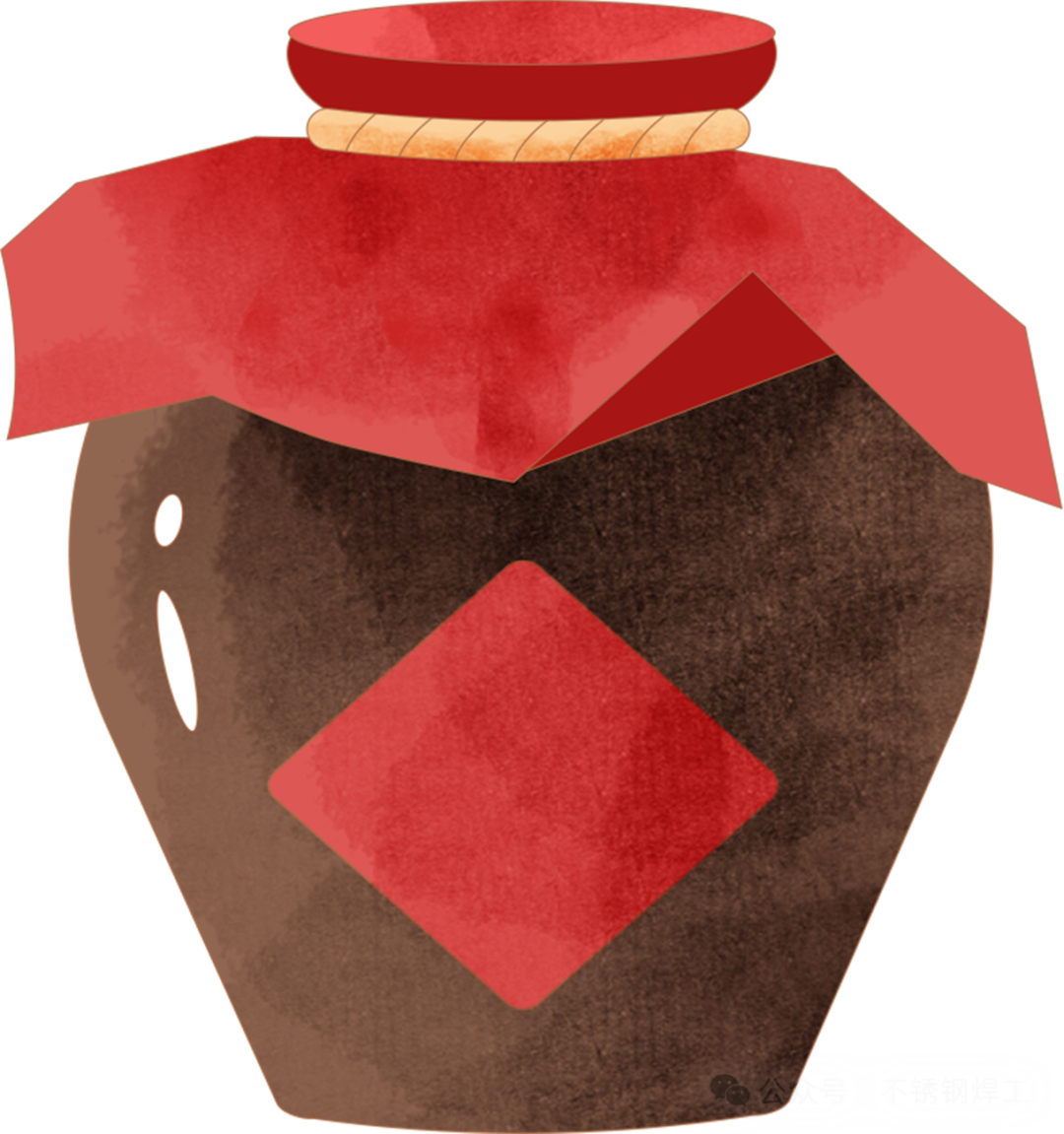
There are many grades of stainless steel. According to the alloy composition, it can be divided into chromium-based stainless steel and chromium-nickel stainless steel. According to the metal structure of stainless steel, it can be divided into austenite type, ferrite type, martensite type, etc. The most commonly used type in construction is austenitic, such as: 0Crl9Ni9, 1Crl8Ni9Ti, etc. Austenitic stainless steel has good weldability and is relatively easy to weld. The welded joint has high toughness even in the as-welded state. However, compared with ordinary carbon steel, its thermal conductivity is about one-third of that of carbon steel, but its coefficient of expansion is 1.5 times greater than that of carbon steel. Due to the low thermal conductivity and high coefficient of expansion of austenitic stainless steel, significant deformation and strain will occur during the welding process. So the welding quality mainly depends on whether the welding process is compatible with the base material. Therefore, when determining the welding process, the following aspects must be considered.
The commonly used welding methods for stainless steel include manual arc welding, gas shielded welding, and automatic submerged arc welding. It is mainly determined based on the design medium parameters, construction conditions and operating environment, as well as construction costs. In the construction of process pipelines, due to the uneven diameter of the pipes and the large number of valves and fittings on the pipelines, the changes in the position of the welds are more complex. So manual arc welding is generally used. For pipelines that transport flammable, explosive, or media with certain cleanliness requirements, argon arc welding is usually used as a base. The manual arc welding method is used to cover the surface and improve the internal quality of the weld seam. The selection of welding materials: Stainless steel welding rods are divided into chromium stainless steel welding rods (with the prefix “G”) and chromium nickel stainless steel welding rods (with the prefix “A”). Chromium stainless steel welding rods are mainly used for welding martensitic stainless steel. The selection of welding rods mainly considers various aspects such as the chemical composition of the base material, the temperature and pressure of the pipeline medium, the welding machine current (AC or DC), the welding method, and the ambient temperature during welding. Generally speaking, through selection confirmation, there will be multiple grades of welding rods that can meet the welding requirements. At this time, the optimal selection can be made based on the cost-effectiveness of the welding rod.
The selection of weld groove form by the design unit is usually based on the stress conditions of the weld. Indicate in the construction drawing that the groove form adopts the corresponding specifications or standards. However, the commonly used specifications or standards do not subdivide the groove size based on the different base materials and welding materials. It is only determined based on the thickness of the base material and the welding method. But in reality, different base materials and welding materials have different requirements for groove size during welding. This is because the chemical composition and physical properties of the material are different, and the penetration force (penetration depth) during welding is also not the same. So during construction, it is necessary to adjust the alignment gap, blunt edge, and groove angle of the groove according to the specific material. If the groove size is too large, it will not only increase the construction cost, but also cause excessive stress on the weld seam, which is prone to deformation and cracking; If the groove size is too small, quality defects such as incomplete welding and slag inclusion are prone to occur. When using manual arc welding for operations, stainless steel has a lower penetration force than carbon steel welding rods. So the angle of the groove and the gap between the joints should be appropriately increased. It can be controlled according to the specified positive deviation value or determined through trial welding.
When selecting welding current, the specific resistance of austenitic stainless steel is nearly 5 times higher than that of carbon steel. Therefore, welding rods are prone to overheating and burning red during welding. However, using high current will cause overheating of the welding rod and burning of the effective components in the coating, which can lead to poor protection of the weld and easily cause defects. At the same time, the expected metal composition of the weld cannot be obtained, so the welding current should not be too high. It is generally advisable to use a smaller welding current.
Before welding operation. We need to make targeted preparations. This preparation is an important component in ensuring welding quality. The content is mainly considered from the following three aspects:
1. Confirmation of welding operator skills: Welders engaged in welding operations must hold certificates and strictly follow the allowed welding projects specified on the operation certificate. Welders should have at least two years of welding experience in stainless steel or chromium molybdenum steel.
2. Welding material pipe: Before using the welding rod, it should be baked according to the instructions in the user manual (if not specified, it is generally treated with a drying temperature of 150-200 ℃ and a drying time of 1 hour). Baking must use a specialized drying oven with controllable temperature. Bake as much as you need, take as you like. The dried welding rod should be placed in an insulated cylinder for use. If exposed for more than 2 hours, it should be baked again. The repetition should not exceed 3 times. Stainless steel pipe grooves can be machined or plasma cut before welding. The oxide layer and burrs at the groove should be removed first. In order to facilitate the removal of spatter after welding, chalk slurry can be applied within 50mm on both sides of the weld, and then removed after welding. Due to the “carburization” phenomenon that occurs when stainless steel comes into contact with carbon steel, special grinding wheels and stainless steel brushes must be used for the weld bead and splash cleaning.
3. Prevention of deformation and cracking: Due to the large expansion coefficient and small thermal conductivity of austenitic stainless steel, significant welding deformation is prone to occur during welding. Therefore, when assembling, different types of anti deformation fixtures should be used according to the welding seams at different positions. The distance between the positioning welding and the fixed welding should be smaller than that of general carbon steel. When welding, the welding sequence should be reasonably determined. If the diameter of the pipe is large, two people can weld it symmetrically in the same direction at the same time. When the base material is thicker than 8mm. The weld bead should be welded in multiple layers and welded with small wire energy. Welding adopts the “reverse connection” method of connecting the negative electrode to the welding piece to reduce the temperature of the welding piece.
To prevent cracks, after baking the welding rod, it should be stored in an insulated container. The welding environment temperature should be above 0 ℃, and significant fluctuations should not occur during the welding process. When the temperature is below 0 ℃, preheating treatment should be carried out for welding, with a preheating temperature of 80-100 ℃. The reverse method is used to initiate the arc within slope 13, and it is strictly prohibited to initiate the arc on the base material. The strip transportation adopts a straight line transportation method that pulls forward without swinging. If lateral swing is necessary during vertical welding, the swing amplitude should be minimized as much as possible. Excessive lateral swing can easily cause thermal cracks and poor protection. The arc length should be kept as short as possible. A long arc not only causes the burning of alloy components, but also may lead to the reduction of ferrite and the formation of thermal cracks due to the invasion of nitrogen gas in the air. The arc pit should be filled when extinguishing the arc. Especially for positioning welding, it is easier to overlook filling the arc pit, and concave arc pits are difficult to avoid the occurrence of hot cracks.
Disclaimer
This public account partially reprints texts and images from the Internet. Reprinting this article is for the purpose of conveying more information and non-commercial educational and research purposes. Copyright belongs to the original author. If there are any errors in source attribution or if the original author does not agree with the reprint, please contact the author with proof of ownership, and we will correct or delete it in a timely manner. Thank you!