Introduction
In recent years, the popularity of battery-powered electronic products has made power consumption an increasingly important issue for analog circuit designers. This article will introduce how to use low-power operational amplifiers for system design, while also covering low-power operational amplifiers with low supply voltage capabilities and their applications. We will discuss how to correctly understand the specifications in the operational amplifier datasheets, comprehensively consider energy-saving technologies in circuit design, and achieve more efficient component selection.
Understanding Power Consumption in Operational Amplifier Circuits
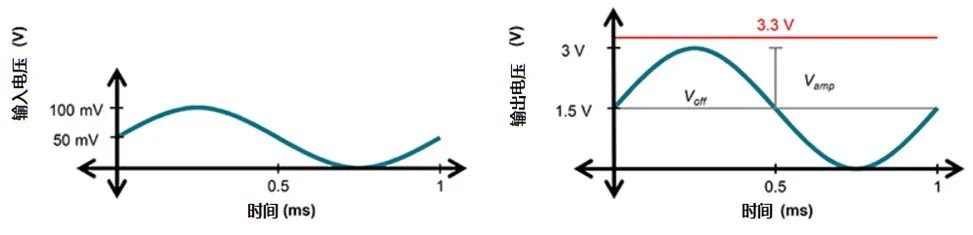
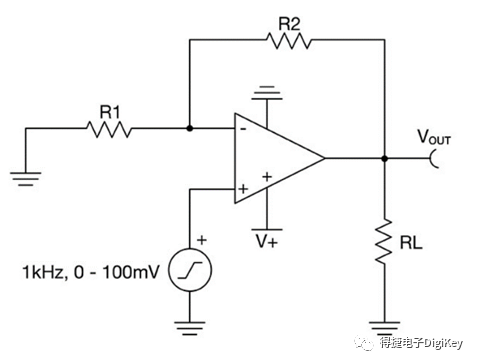

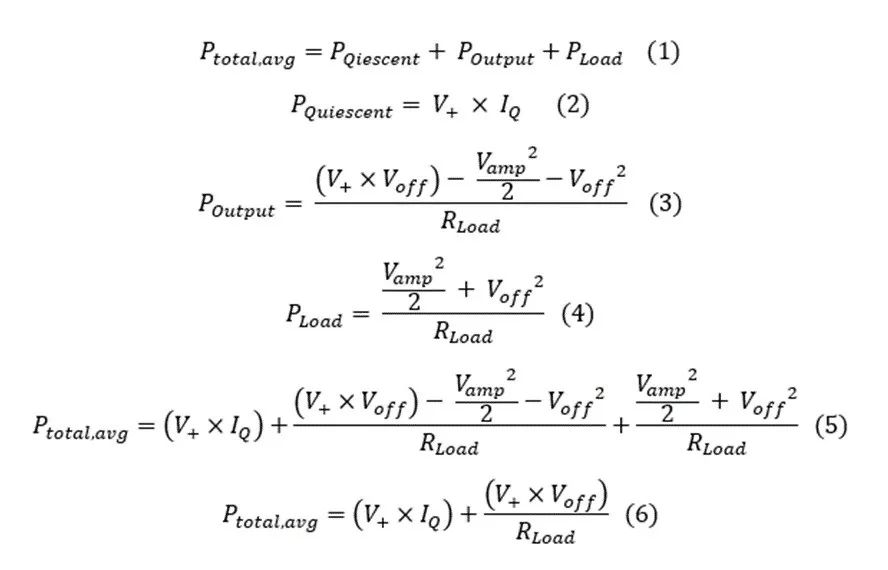
Choosing Components with AppropriateIQ Values
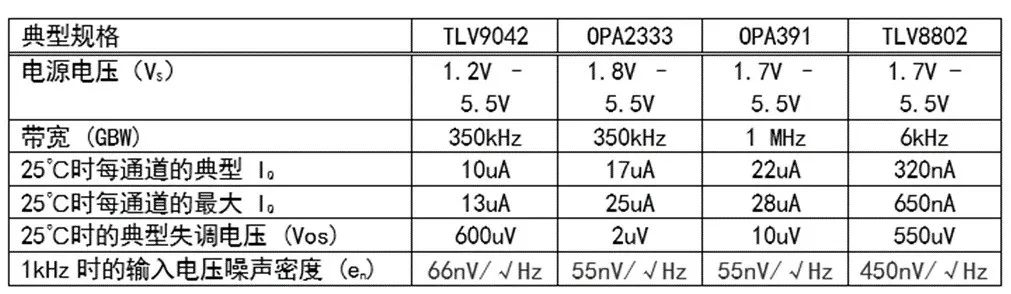
Reducing the Resistance Value of the Load Network
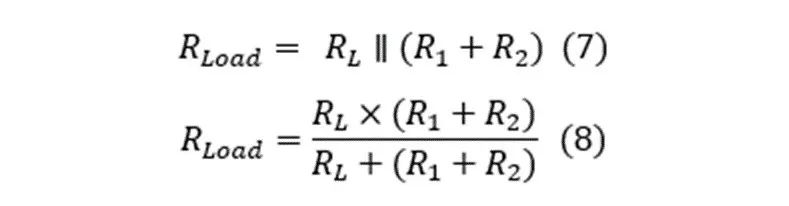
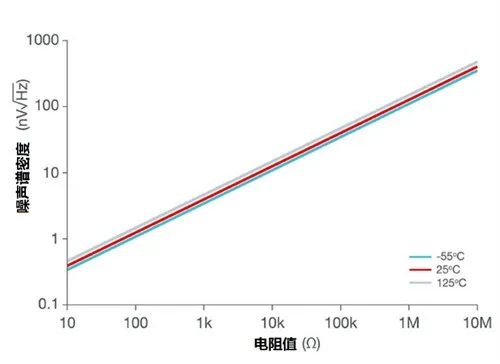
Real-World Examples
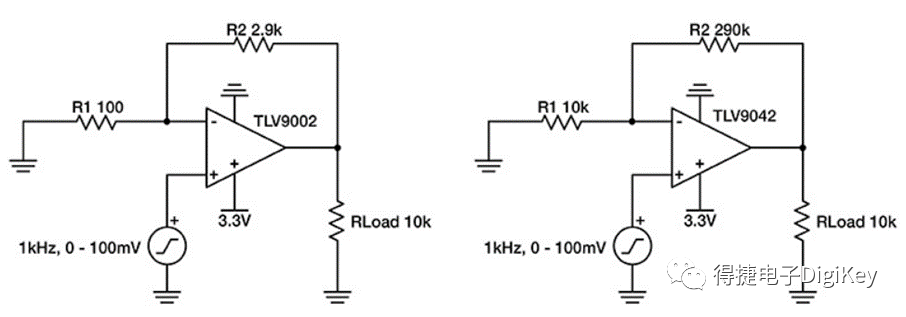
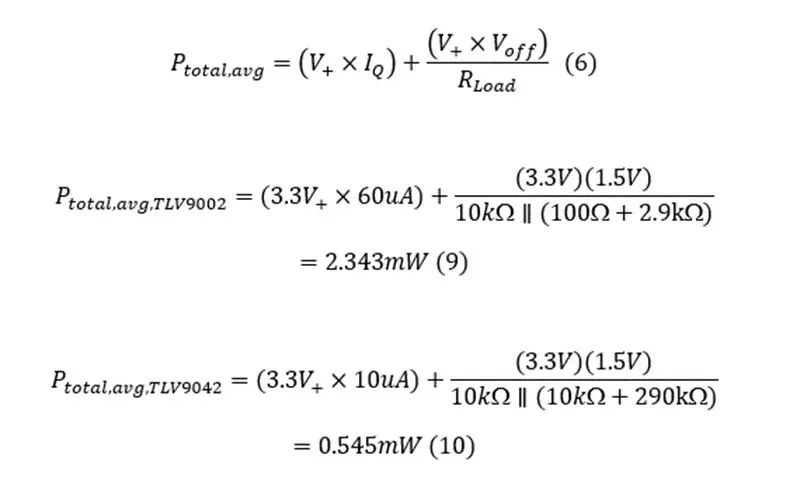
Saving Power with Low Voltage Rails
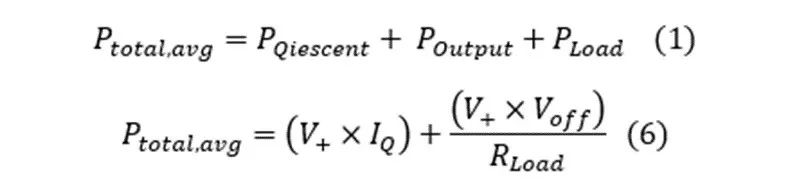
Battery-Powered Applications
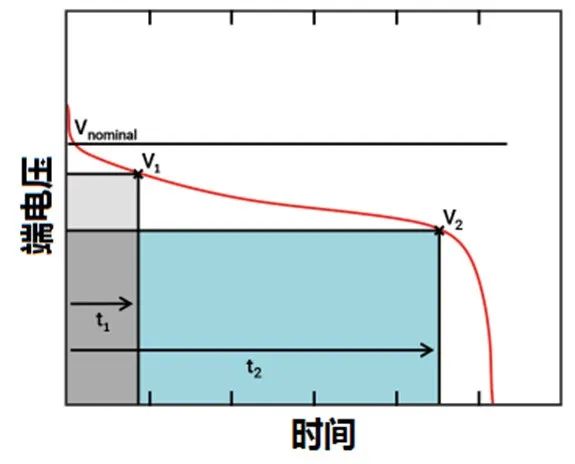
Low Voltage Digital Logic Levels
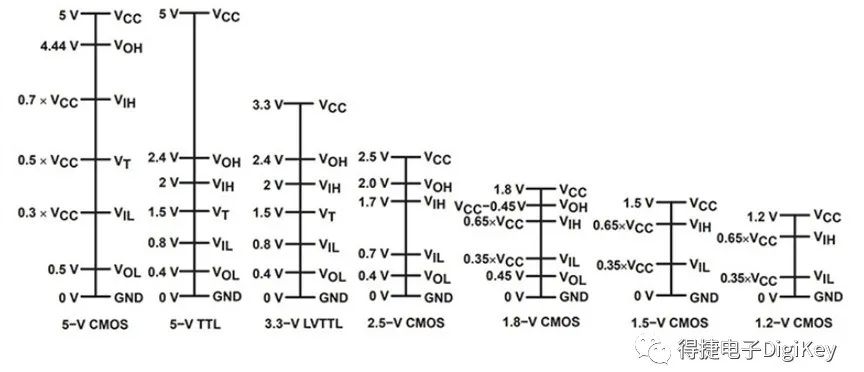
Digi-Key Operational Amplifier Parameter Filtering Tool
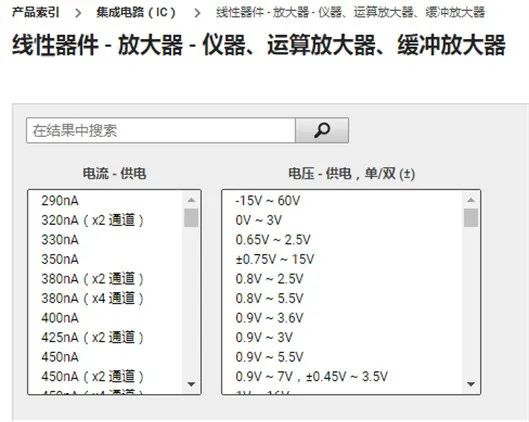
Conclusion
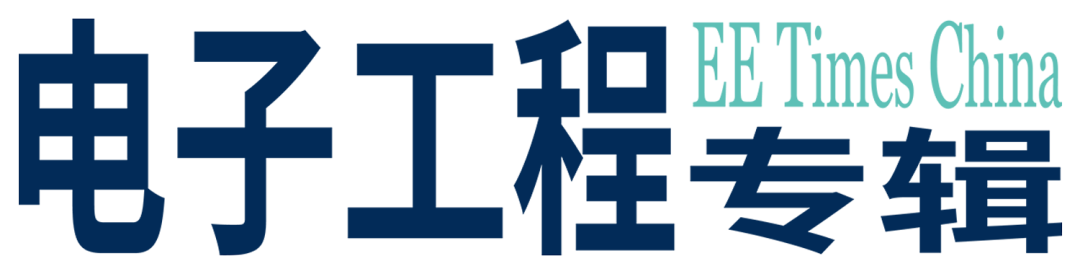
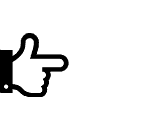