Method 1:
1. Cut the copper-clad board to the required size for the circuit diagram.
2. Place wax paper on a steel plate, use a pen to draw the circuit diagram on the wax paper at a 1:1 scale, and cut out the drawn circuit diagram according to the size of the circuit board. Place the cut wax paper on the printed copper-clad board. Take a small amount of paint and mix it with talcum powder to create a suitable printing paste. Use a brush to evenly apply the paste onto the wax paper, repeating this several times until the circuit is printed onto the board. This engraving plate can be reused, making it suitable for small batch production.
3. Prepare an etching solution with a ratio of 1 gram of potassium chlorate to 40 milliliters of 15% hydrochloric acid, and apply it to the areas of the circuit board that need etching.
4. Rinse the etched printed board repeatedly with water. Use banana oil to wipe off the paint, then rinse several times to ensure the printed board is clean and free of etching solution. Apply a layer of rosin solution and drill holes after it dries.
There are many methods to make printed circuit boards under amateur conditions, but they are either time-consuming, complex in “craftsmanship”, or the quality is unsatisfactory. My method of making printed boards is one that has a good overall effect, as follows:
1. Create the printed board diagram. Represent the pads in the diagram with dots, and connect the lines with single lines, but the position and size must be accurate.
2. Cut the printed board according to the size of the printed board diagram, and clean the copper foil surface.
3. Use carbon paper to copy the diagram onto the printed board. If the circuit is relatively simple and the maker has some experience in board making, this step can be skipped.
4. Depending on the actual components, paste different inner and outer diameter standard pre-cut symbols (pads); then, according to the current size, paste tape lines of different widths. Standard pre-cut symbols and tape are available in electronics stores. Common specifications for pre-cut symbols include D373 (OD-2.79, ID-0.79), D266 (OD-2.00, ID-0.80), D237 (OD-3.50, ID-1.50), etc. It is best to purchase those made from paper-based materials (black), and to avoid plastic-based (red) materials as much as possible. Common specifications for tape include 0.3, 0.9, 1.8, 2.3, 3.7 mm.
5. Use a soft small hammer, such as smooth rubber or plastic, to tap the diagram stickers so that they adhere well to the copper foil. Focus on tapping at the corners and overlaps of the lines. In cold weather, it is best to use a heater to warm the surface to enhance adhesion.
6. Place it in ferric chloride for etching, but be careful, the liquid temperature should not exceed 40 degrees. After etching, it should be taken out and rinsed clean immediately, especially in cases with fine lines.
7. Drill holes, use fine sandpaper to polish the copper foil, apply a rosin alcohol solution, and let it dry to complete the production. The quality of this printed board is very close to that of standard printed boards. The 0.3 mm tape can cross between IC pins, greatly reducing the short jumpers on the front of the board for convenience and time-saving.
1. Dissolve one part of shellac (available in chemical supply stores) in three parts of anhydrous alcohol, and stir appropriately. Once it is fully dissolved, add a few drops of medical purple medicine (gentian violet) to give it a certain color. Stir well, and it can be used as a protective paint for drawing on the circuit board.
2. First, polish the copper-clad board with fine sandpaper, then use a drawing tool such as a fountain pen (or a compass used for drawing shapes) to draw. The fountain pen has a nut to adjust the thickness of the stroke, allowing for smooth and uniform lines without jagged edges, giving a smooth and flowing appearance. At the same time, Chinese characters, English, pinyin, or symbols can be written in the free space on the circuit board.
3. If the drawn lines bleed, the concentration is too low, and you can add a bit more shellac; if the ink is too thick and cannot be spread, add a few drops of anhydrous alcohol. If you make a mistake, it’s okay; just use a small stick (like a matchstick) to make a small cotton swab, dip it in a bit of anhydrous alcohol, and easily wipe it off, then redraw. Once the circuit board diagram is completed, it can be etched in ferric chloride solution. After the circuit board is etched, removing the paint is also easy; just use a cotton ball dipped in anhydrous alcohol to wipe off the protective paint, let it dry slightly, and then you can apply rosin water for use.
4. Since alcohol evaporates quickly, the prepared protective paint should be stored in a small bottle (like an ink bottle) and sealed. After use, don’t forget to cap it. If you find the concentration thickens the next time you use it, just add an appropriate amount of anhydrous alcohol.
1. Stick instant adhesive paper on the copper foil of the copper-clad board, then draw the circuit on the adhesive surface, and use a craft knife to cut through the adhesive surface to form the required circuit. Finally, remove the non-circuit parts and etch with ferric chloride or use current electrolysis to make a better circuit board.
2. The etching temperature can be around 55℃, and the etching speed is relatively fast. Rinse the etched circuit board with clean water, remove the instant adhesive from the circuit, drill holes, clean, and apply rosin alcohol solution for use.
1. Arrange the density and positions of the components reasonably based on the shapes of the components used in the circuit schematic and the area of the printed board. The positioning of components should follow the principle of placing larger components first, then smaller ones, and arranging them in a neat and uniform manner.
2. The connecting wires between components should not have right angles at bends and intersections; they must transition with curves and should not cross or deviate too far from each other. If some wires cannot achieve this, consider printing the wires on the back of the printed board and connecting them to the front circuit with through holes, or using insulated wires when soldering components.
3. It is better to keep a distance between the input and output sections to avoid mutual interference.
Radio enthusiasts have all encountered difficulties in making circuit boards. Now I will introduce a “semi-printing” method for making printed circuit boards. The specific method is as follows:
1. Print the circuit board diagram at a 1:1 scale on 80g copy paper using a printer. Hand drawing is also acceptable, but the base paper must be flat.
2. Find a fax machine, take out the fax paper, and replace it with hot melt plastic film. Place the circuit diagram into the fax machine’s entrance, and use the copy button to copy the circuit diagram onto the hot melt plastic film. This will create the “printing original” for the printed circuit board.
3. Use double-sided tape to neatly stick the prepared film onto the copper-clad board. Make sure it is flat without wrinkles, and the tape should not cover the melted part; otherwise, it will affect the production effect of the circuit board.
4. Use a paintbrush to evenly apply paint on the plastic film, noting that:it should not be brushed back and forth, only in one direction, otherwise, the plastic film will wrinkle, and the lines on the copper board will overlap. Once the circuit diagram is fully brushed, carefully remove the plastic film. At this point, a printed circuit board is completed. After drying, it can be etched.
If you want to print multiple boards, you can make a wooden frame slightly larger than the circuit board, stretch the silk screen (which our company sells) evenly over the frame, and secure it. Then use double-sided tape to attach the prepared film under the silk screen. Place the copper-clad board on the table, close the silk screen frame (aligning the printed diagram with the copper-clad board), and use a paintbrush to apply the paint in one direction, then remove the screen frame. The printed circuit board is done. If there are defects, you can modify them with paint and bamboo sticks.
The above process must be noted: when brushing paint, the pressure of the hand should be just right; too heavy will make the paint film too thick, causing the lines to blur, while too light will result in broken lines. The plastic film must always face up.
Copyright statement: This article is copyrighted by the original author and does not represent the views of the association. Articles promoted by the “Jiangxi Province Electronic Circuit Industry Association” are for sharing purposes only and do not represent the position of this account. If there are copyright issues, please contact us for deletion.
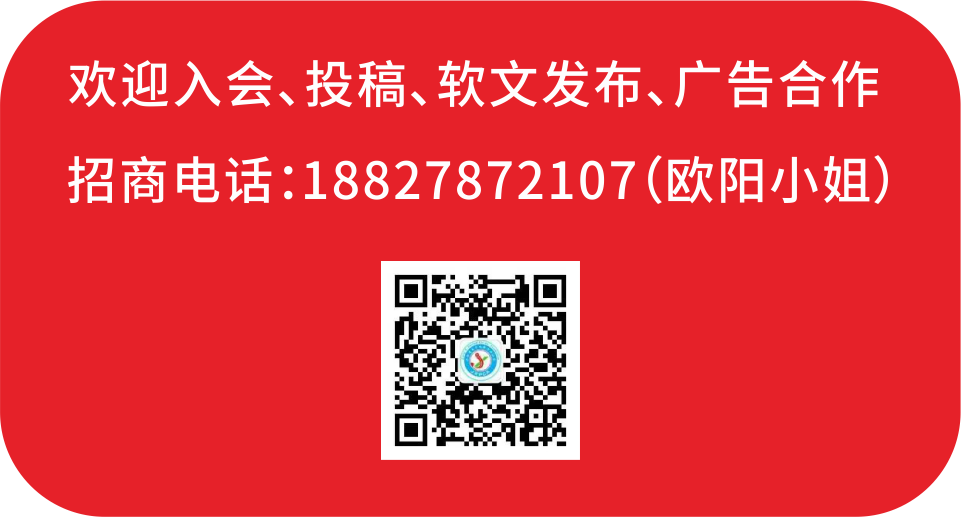