Follow us, Diamond open access, no publication fee
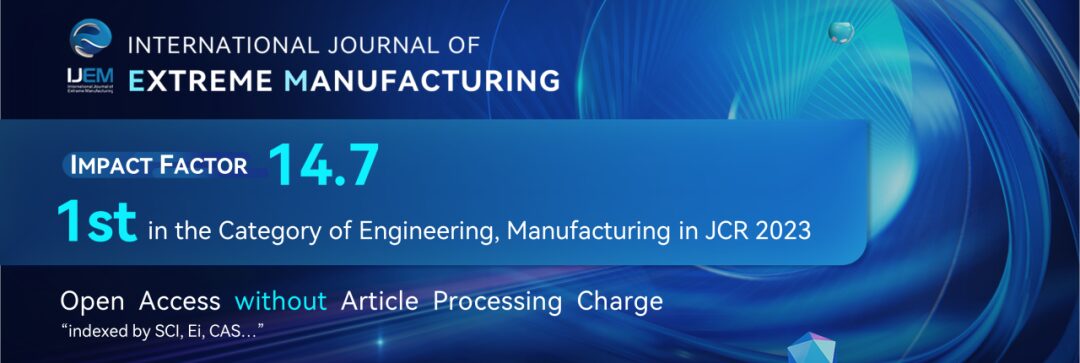
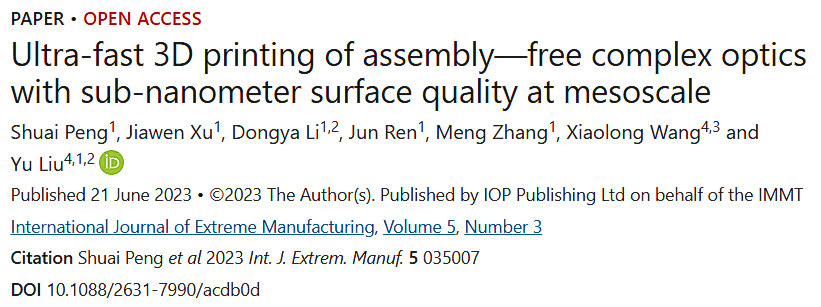
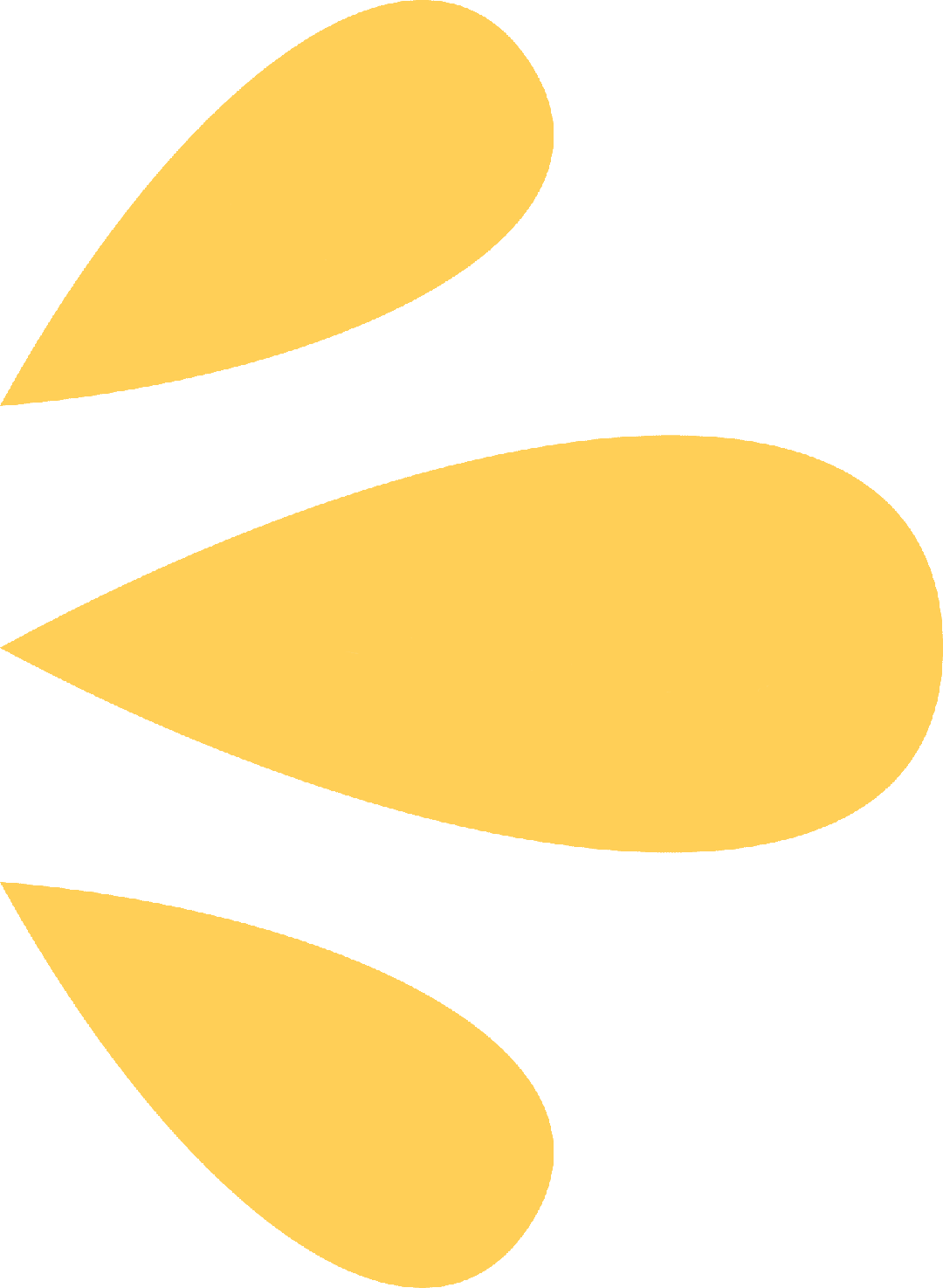
Author:
Peng Shuai1,*, Xu Jiawen1, Li Dongya1, Ren Jun1, Zhang Meng1, Wang Xiaolong2,#, Liu Yu1,#
*First author, #Corresponding author
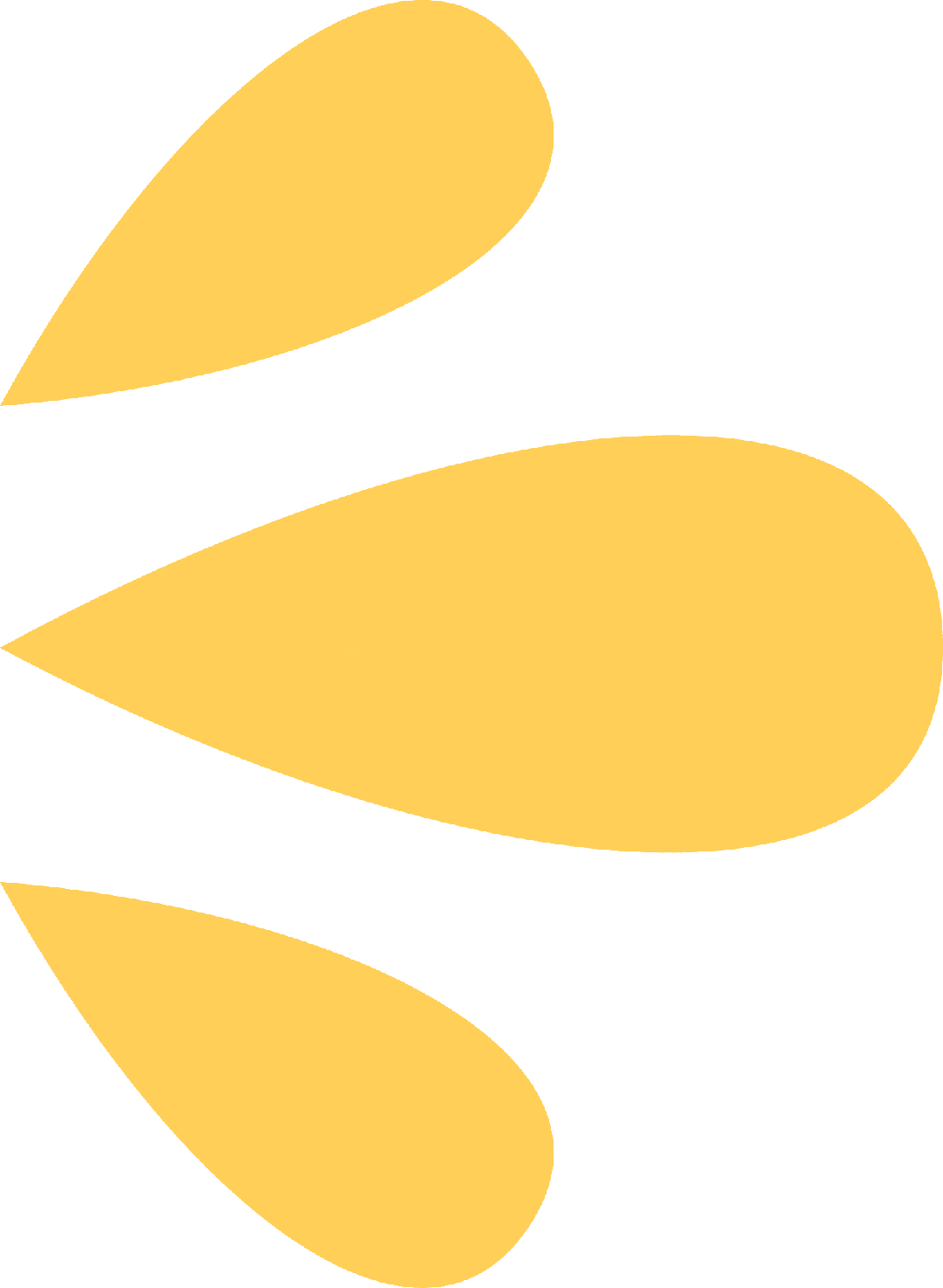
Affiliation:
1 Jiangnan University
2 Lanzhou Institute of Chemical Physics, Chinese Academy of Sciences
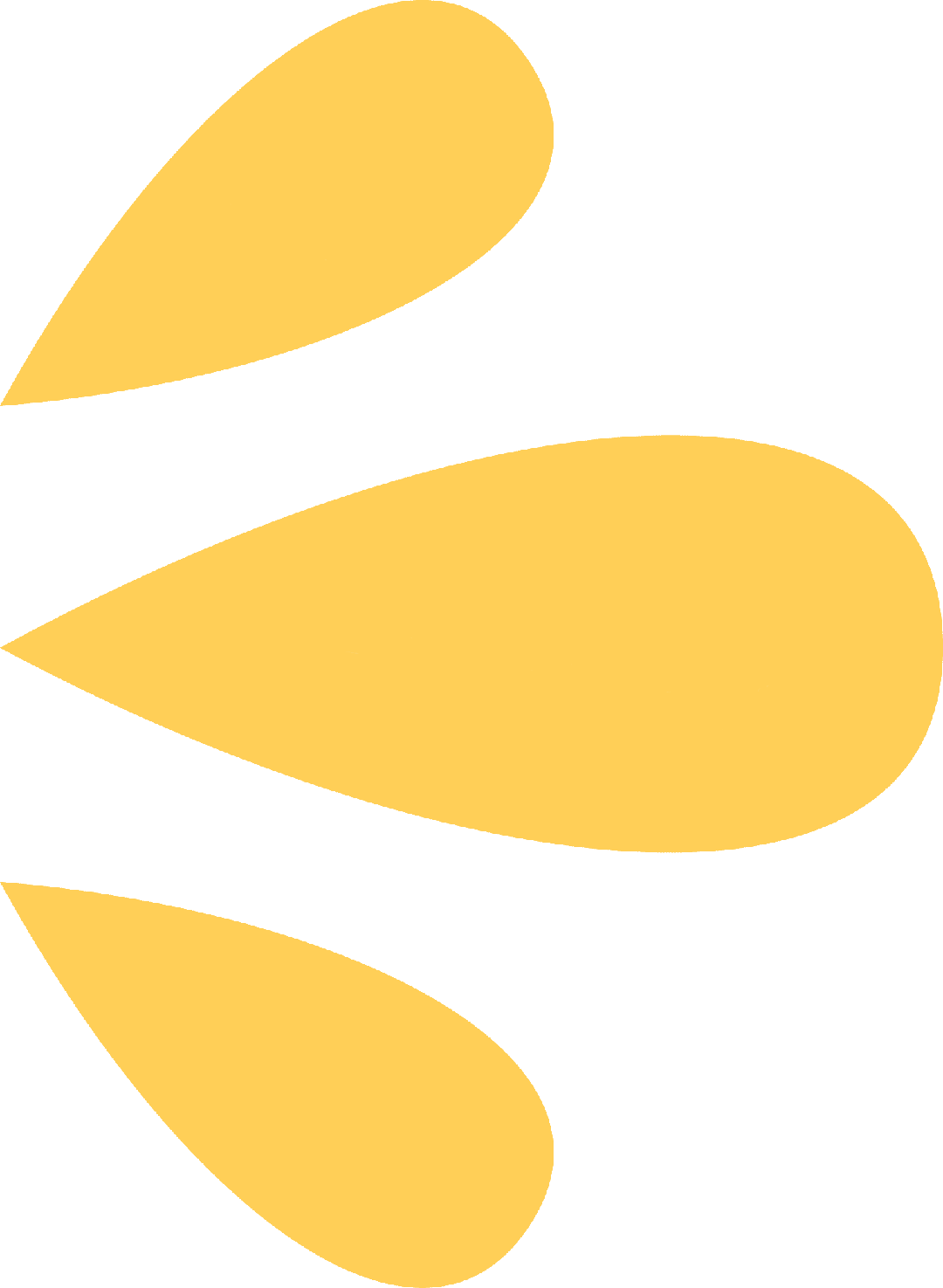
Citation:
Peng S, Xu J W, Li D Y, Ren J, Zhang M, Wang X L, Liu Y. 2023. Ultra-fast 3D printing of assembly-free complex optics with sub-nanometer surface quality at mesoscale. Int. J. Extrem. Manuf. 5 035007.
Free access to the full text
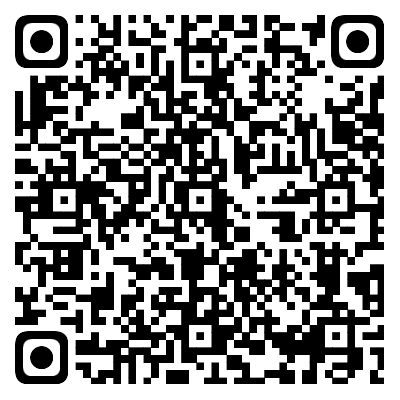
https://doi.org/10.1088/2631-7990/acdb0d
▲ Written by | Article Author
Article Overview
Optical lenses with complex spatial morphology are widely used in laser processing, machine vision, optical communication, and other fields. Traditional manufacturing methods for optical lenses mainly involve ultra-precision machining combined with grinding and polishing post-processing techniques, which typically involve multiple steps, high costs, and are difficult to meet complex degrees of freedom requirements. Additive manufacturing technology is showing significant advantages in preparing complex structured optical devices. However, the layer-by-layer additive manufacturing method faces issues such as low printing speed and poor surface quality caused by interlayer step effects. Recently, Professor Liu Yu from Jiangnan University’s School of Mechanical Engineering, PhD student Peng Shuai, and Professor Wang Xiaolong’s team from the Lanzhou Institute of Chemical Physics, Chinese Academy of Sciences jointly published a research paper titled “Ultra-fast 3D Printing of Assembly-Free Complex Optics with Sub-Nanometer Surface Quality at Mesoscale” in Extreme Manufacturing (International Journal of Extreme Manufacturing, IJEM), proposing the use of computed tomography volume printing technology combined with a meniscus balancing post-curing process to achieve high-speed printing (3.1 × 104 mm3 h−1) while ensuring sub-nanometer level (RMS = 0.3340 nm) surface quality of the printed structure.
Keywords:
Computed Tomography Volume Printing (TVP); Meniscus Balancing Post-Curing Method; Spherical Lens; Sub-Nanometer Roughness
Highlights:
-
Achieved ultra-fast 3D printing of complex morphology optical components through parameter optimization.
-
Improved surface quality of computed tomography volume printed structures through the combination of meniscus balancing post-curing process.
-
Simple design and rapid prototyping of functional spatial complex optical lenses.
Research Background
Optical devices, due to their good illumination, sensing, optical modulation, and display capabilities, can be directly applied to sensors, holographic reconstruction, human-computer interaction, and other optoelectronic devices. Traditional manufacturing methods for optical devices mainly include ultra-precision machining, casting, and injection molding. However, the current mainstream processing technologies are expensive, involve multiple steps, and have low degrees of freedom, limiting the further development of optical devices.
Recently, 3D printing has attracted significant attention in the manufacturing of highly complex morphology optical devices. Compared with two-photon polymerization (TPP), fused deposition modeling (FDM), direct ink writing (DIW), and stereolithography (SLA), which are based on points as basic manufacturing units, the digital light processing (DLP) technology, which uses layers as basic manufacturing units, is considered a more efficient method for high-speed manufacturing of polymer lenses. However, about 90% of the processing time is consumed in reapplying new photopolymer resin to ensure uniformity between layers. The Continuous Liquid Interface Printing (CLIP) process eliminates the time-consuming reapplication step, providing a significant opportunity to increase manufacturing speed. However, despite the significant increase in printing speed with CLIP, the surface quality of the printed structure is still somewhat limited by the step effect.
To address the issues of manufacturing speed and surface quality of printed structures for complex optical devices, Peng Shuai and others explored the feasibility of using TVP technology to further improve the manufacturing speed of complex optical lenses. As shown in Figure 1, the TVP technology first generates the lens structure within seconds. After removing the manufactured object from the resin container, the residual resin film on its surface is further cured to achieve sub-nanometer ultra-smooth surface. The printed optical lenses can be directly mounted on smartphone cameras for observing small features.
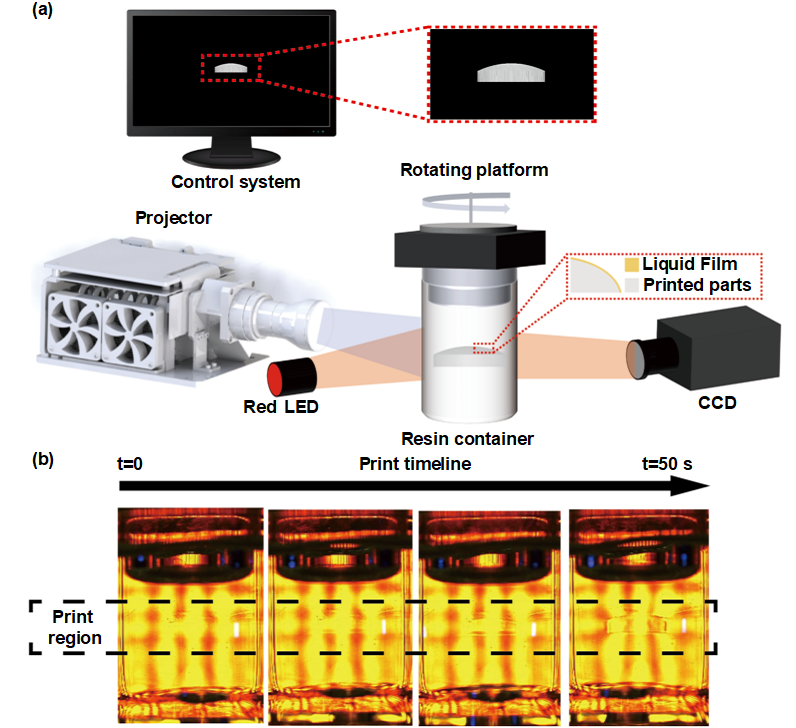
Figure 1. Schematic diagram of the TVP system printing. (a) Key components of the TVP system. (b) Process diagram of TVP printing. A centimeter-sized plano-convex lens is printed within seconds.
Latest Developments
The authors compared the surface morphology characteristics and printing times of the same lens model manufactured using three different photopolymerization technologies. As shown in Figures 2(a-c), the SLA and DLP methods, which involve solid manufacturing through layer-by-layer stacking, require support to be printed, and the subsequent removal of the support process can also damage the surface morphology, while TVP printing is conducted in high-viscosity resin without the need for support, achieving integrated molding of complex structures. As shown in Figure 2(d), TVP has an absolute advantage in printing efficiency, achieving centimeter-sized lens printing in seconds. As shown in Figures 2(e-h), the structures printed using SLA and DLP have surface step effects, affecting their surface quality. In contrast, the integrated printing of TVP avoids step effects and successfully produces optical lenses with high surface quality.
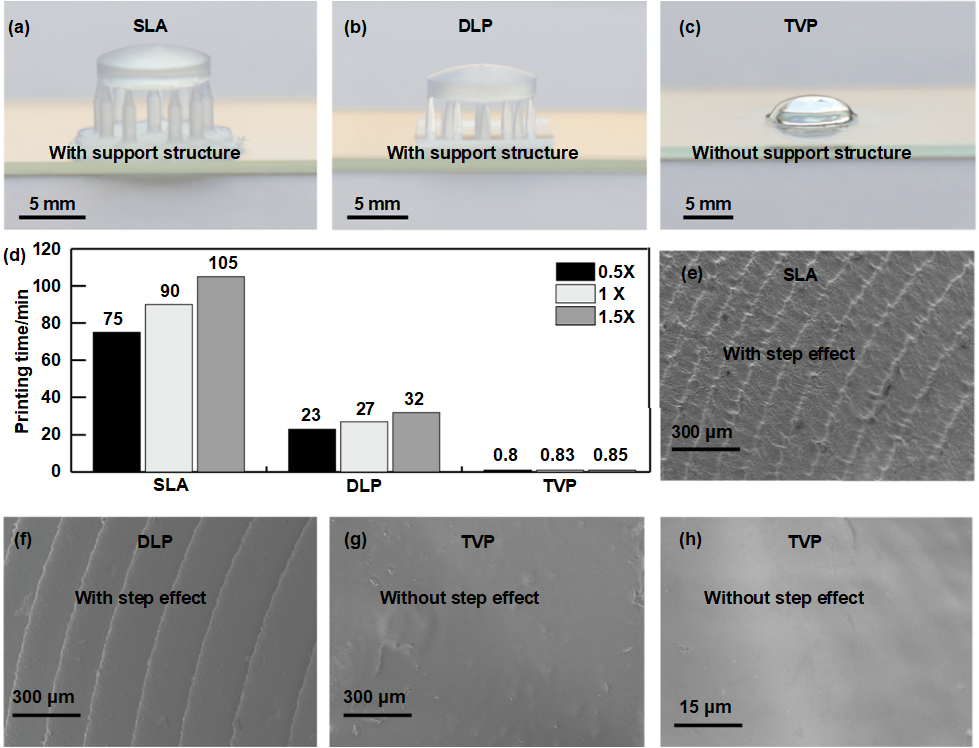
Figure 2. Comparison of surface morphology characteristics and printing times of the same lens manufactured using different photopolymerization printing technologies. (a)-(c) SLA, DLP, and TVP printing of the same model. (d) Comparison of the time required to manufacture lenses of 0.5×(16.1 mm3), 1×(128.6 mm3), and 1.5×(434.1 mm3) proportions using different photopolymerization printing technologies. (e)-(g) SEM images of lenses made by SLA, DLP, and TVP before meniscus balancing post-curing. (h) is an enlarged view of (g).
To verify the role of the meniscus balancing post-curing process in improving the surface quality of TVP printed structures, the authors compared the three-dimensional morphology of lens structures with and without post-curing treatment. As shown in Figures 3(a-g), the lens surface of TVP combined with the meniscus balancing post-curing process can achieve sub-nanometer surface roughness (RMS=0.3340nm, Sa=0.4898nm). Cross-sectional profiles in Figures 4(f-g) show variations within ±4 nm, indicating that the optical lenses manufactured by this process are very suitable for optical applications. Figures 3(h-j) show the three-dimensional morphology after removing the surface resin of the printed structure with isopropanol, revealing an RMS as high as 75.42nm.
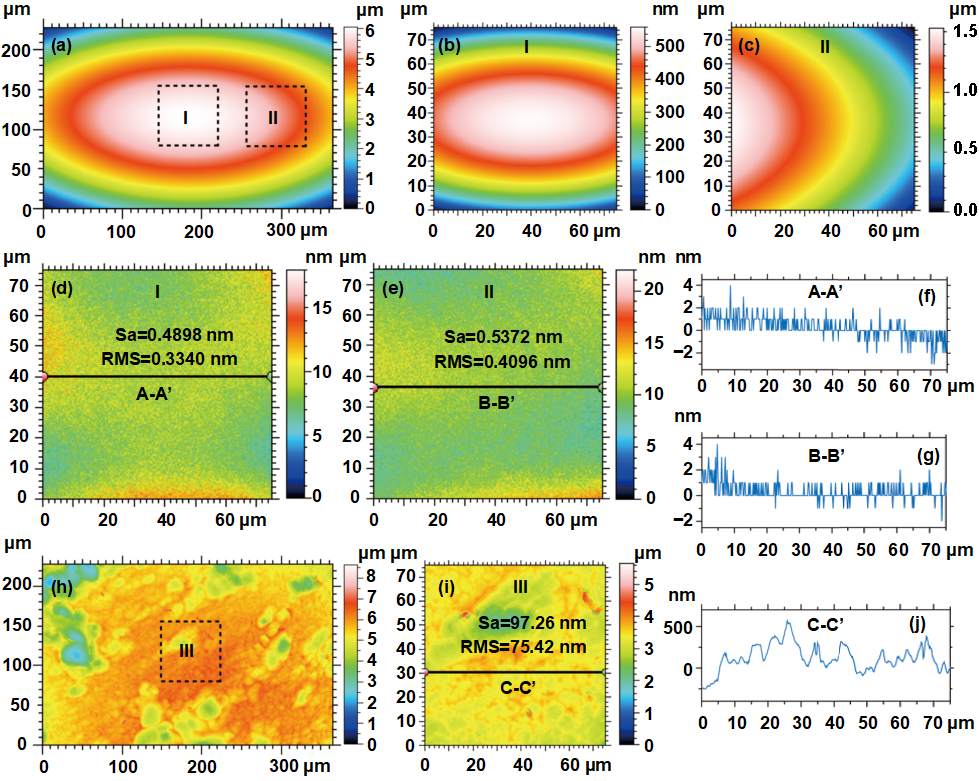
Figure 3. Three-dimensional morphology of TVP printed lenses. (a) Surface profile captured by optical surface profiler. (b) Enlarged surface morphology of region I and (c) region II. (d) Three-dimensional roughness distribution of region I and (e) region II. (f) Cross-sectional A-A’ and (g) B-B’ profile. (h) Three-dimensional morphology of the lens manufactured by TVP without post-curing treatment. (i) Three-dimensional roughness distribution of region III. (j) Cross-sectional C-C’ profile.
To demonstrate the high degree of freedom of TVP printing, as shown in Figures 4(a-d), the authors also printed more complex structured optical lenses, including the integrated printing of lens groups. Figures 4(e-h) show that the complex morphology lenses have certain functionalities.
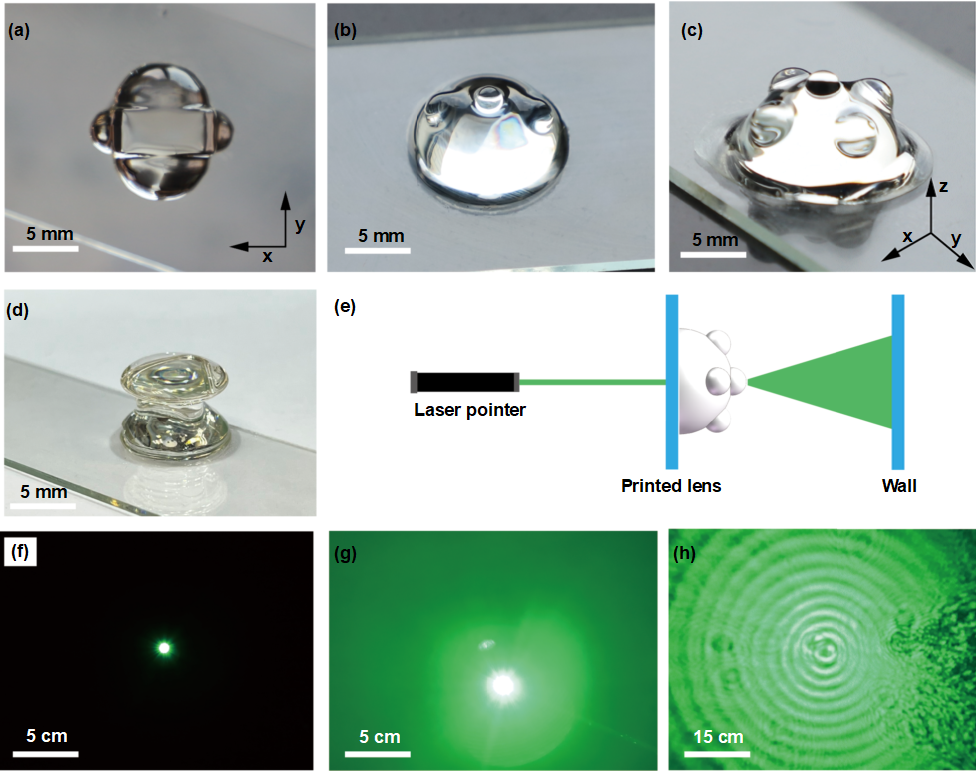
Figure 4. Manufacturing complex morphology lenses. (a-c) Complex morphology lenses. (d) Integrated printing of lens groups. (e) Schematic diagram of the experimental optical system used to demonstrate the functional characteristics of complex lenses. (f) Imaging of a green laser pen without printed lenses. (g) Imaging of a green laser passing through (a) along the Y-axis. (h) Imaging of a green laser passing through (c) along the Z-axis.
To demonstrate the imaging characteristics of TVP printed lenses, the experimental setup in Figure 5(a) uses a resolution test target with 8 sets of patterns ranging from 0 to +7. Figure 5(b) shows the target image captured by CCD. Figure 6(c) shows the stripes of the 3rd set, 6th unit. Figures 5(d-g) show that the TVP printed spherical lens can be directly mounted on a smartphone to capture two magnified images of the Arduino Mega 2560 surface, where the electrical components in focus and wires with a width of 500μm can be clearly seen. The authors used the coordinate lines in Figure 6(i) as the object. By directly mounting the printed compound eye lens on the smartphone shown in Figure 6(h), two blurred coordinate lines can be observed. The test results confirm that the TVP printed lenses can be effectively applied in commercial smartphones, providing high-quality images.
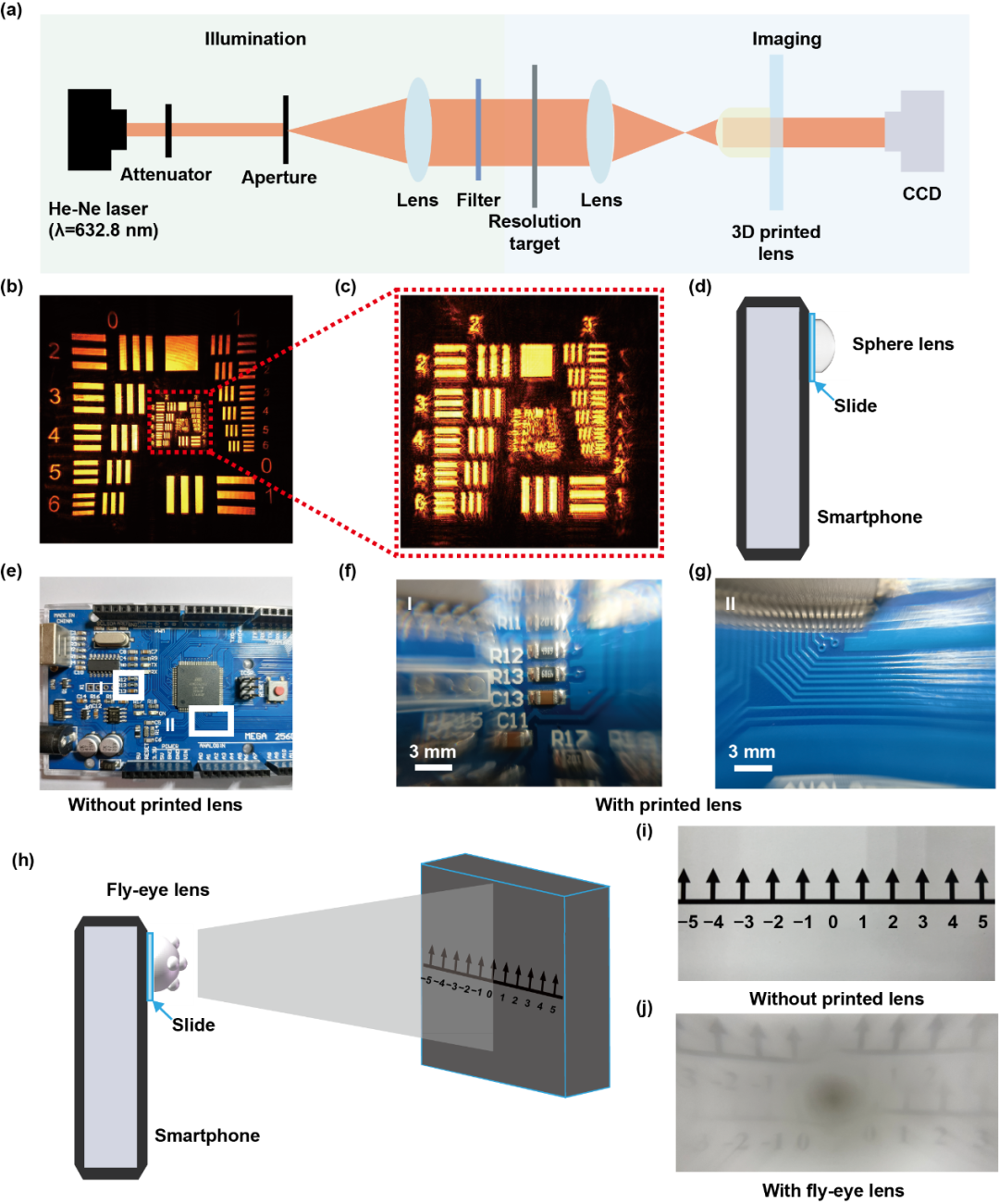
Figure 5. Imaging characteristics of TVP printed lenses. (a) Schematic diagram of the experimental system characterizing the imaging performance of TVP printed custom lenses. (b) Image of the resolution test target captured by the embedded printed lens. (c) Close-up views of the 2nd and 3rd sets. (d) Schematic diagram of the setup using a spherical lens. (e) Image of the circuit board captured by a smartphone without using a lens. (f)-(g) Two magnified images captured using the spherical lens from (e). (h) Schematic diagram of the device using a compound eye lens. (i) Image of the board engraved with coordinates taken by the smartphone without using a lens and (j) with the compound eye lens.
Future Prospects
TVP technology is an ultra-fast printing method, and combined with the meniscus balancing post-curing technology, it is bound to play an increasingly important role in the field of optical manufacturing. Its prospects mainly include the following aspects: Although TVP can achieve ultra-fast printing processes, its precision is still a certain distance from ultra-precision machining; to achieve high-precision device manufacturing, algorithm simulation and material ratios need further coordination; currently, most materials used for TVP are transparent materials; to achieve multifunctional coupling, future exploration of multi-material TVP technology is required; currently, TVP technology can only print centimeter-scale structures; future methods for large-scale structure printing need to be developed. After solving these problems, TVP will surely become a powerful tool in various manufacturing fields.
Author Biography
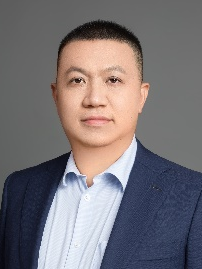
Professor Liu Yu
Jiangnan University
Professor Liu Yu is a professor and doctoral supervisor at the School of Mechanical Engineering of Jiangnan University. He has been selected for various talent introduction programs, including the Youth Project of the Overseas High-level Talent Introduction Program, Jiangsu Province’s Double Innovation Talent University Innovation Program, and Wuxi City’s Hundred Science and Technology Stars. He mainly engages in research on additive manufacturing of functional devices, micro-nano manufacturing, and precision measurement, undertaking various national and provincial-level projects/topics. His research results have been published in over 100 papers in high-level academic journals such as Nat. Comms., Adv. Mater., and Addi. Manu.. He holds over 80 domestic and international invention patents; his technical achievements have won the second prize of Jiangsu Province Science and Technology Award, Xerox Achievement Awards, etc. He serves as a member of the Extreme Manufacturing Branch of the Chinese Mechanical Engineering Society, a member of the Additive Manufacturing Branch of the Chinese Mechanical Engineering Society, a youth editorial board member of Int. J. Extrem. Manuf., a youth editorial board member of Nanotech. Precis. Eng. (NPE), and has been invited to give academic reports or serve as a session chair at various domestic and international academic conferences, as well as to review for well-known journals in the field.
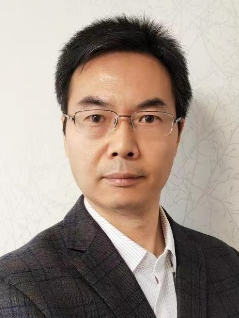
Researcher Wang Xiaolong
Lanzhou Institute of Chemical Physics, Chinese Academy of Sciences
Wang Xiaolong is a researcher at the Lanzhou Institute of Chemical Physics, Chinese Academy of Sciences, and a “Oasis Scholar” chair professor at Shihezi University. He obtained his bachelor’s and doctoral degrees from Lanzhou University in 1999 and 2007, respectively; he served as a research assistant at The Hong Kong Polytechnic University from 2010 to 2011; was a visiting scholar at The University of Western Ontario, Canada from 2012 to 2013; and was selected for the “West Light” talent training program of the Chinese Academy of Sciences in 2014; he is the chief scientist of the key special project on “Additive Manufacturing and Laser Manufacturing” of the National Key R&D Program during the 14th Five-Year Plan. He is a member of the Additive Manufacturing Branch of the Chinese Mechanical Engineering Society, a council member of the Gansu Materials Society, and an editorial board member of journals such as Coatings and Tribology; he won the 2021 IAAM Scientist Award (International Advanced Materials Association Scientist Award), first prize of Gansu Province Patent Award (first inventor), and first prize of Gansu Province Medical Science and Technology Award (second contributor). His research areas mainly include new materials and functional devices for 3D printing, bionic friction and lubrication, and materials surface/interface engineering, with over 120 academic papers published in journals such as Adv. Mater., Adv. Funct. Mater., and Small, and over 30 authorized Chinese invention patents and 2 US patents.
Related Articles
3D Printing Ultra-Fast Photothermal Responsive Shape Memory Hydrogels for Micro-Robotic Control
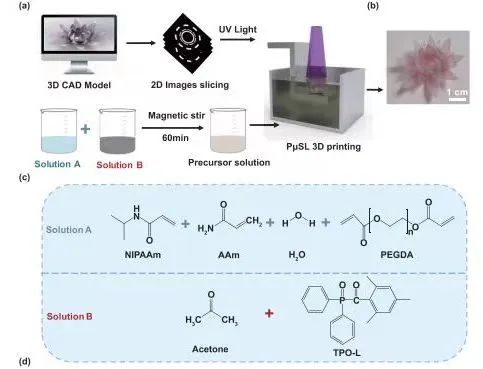
DOI: https://doi.org/10.1088/2631-7990/ac376b
Programmable Robotic “Transfer-Printing” Hybrid Manufacturing for Large Area Complex 3D Curved Electronic Devices
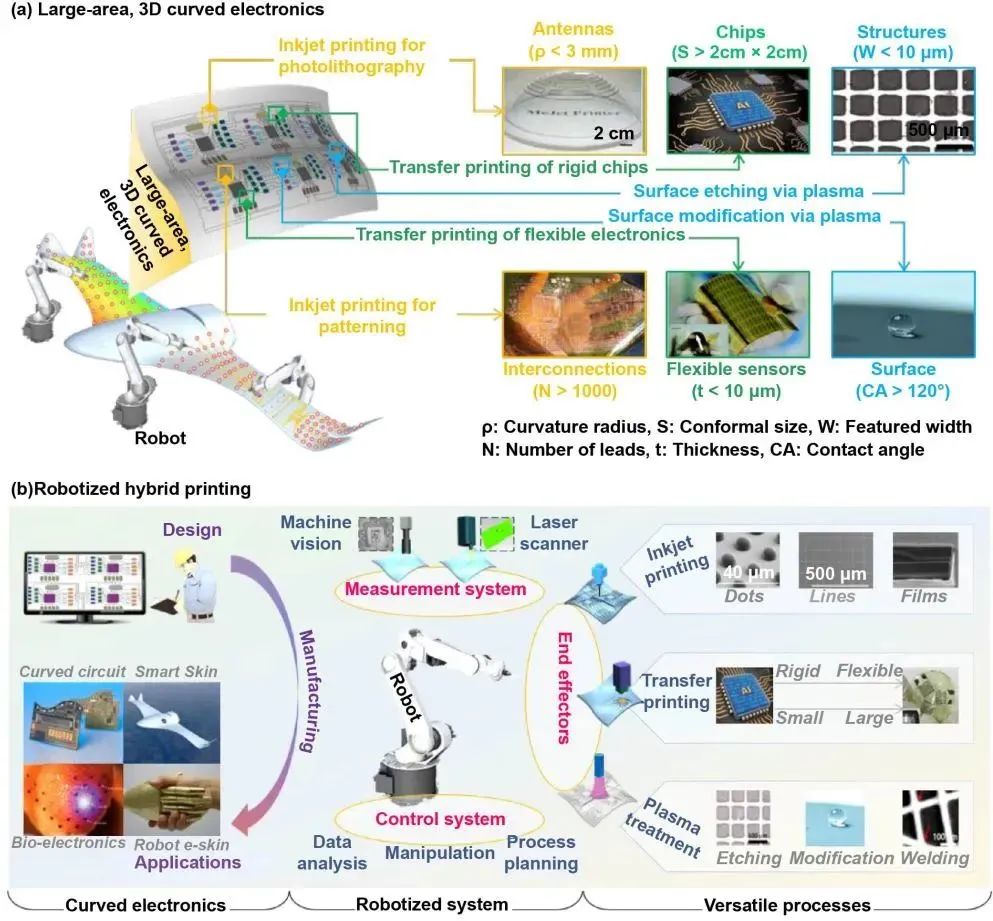
About the Journal
The journal International Journal of Extreme Manufacturing (IJEM) is the first international journal in the field of extreme manufacturing, dedicated to publishing high-quality and latest research results in the field of extreme manufacturing. The articles are mainly original and review articles. Currently, the journal has four major sections: Material and Energy Field Interaction, Process Methods, Extreme Functional Materials/Structures/Devices, Measurement and Systems. IJEM is now indexed by SCI, EI, Scopus, CNKI, etc. The latest 2023 JCR impact factor is 14.7, ranking first in the engineering/manufacturing discipline. It is in the top tier of engineering technology in the Chinese Academy of Sciences and is a TOP journal. It has also been selected as one of the “Most Internationally Influential Academic Journals in China” (TOP 5%). Diamond open access, no author publication fee, double-blind peer review.
Submitting to IJEM will provide you with
• An open-access (OA) journal, free access and submission
• Provides a green channel for rapid review of original breakthrough results
• Online within 24 hours of acceptance
• Free global promotion and publicity
• Free high-quality image editing
• Free standardized literature proofreading
Article Highlights
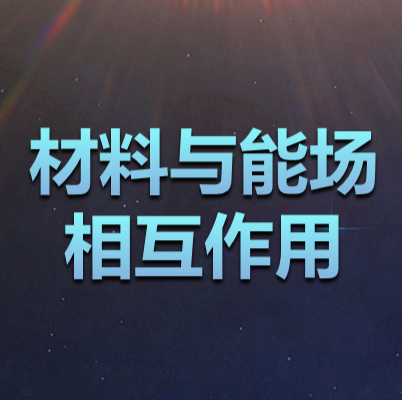
Material and Energy Field Interaction
Process Methods
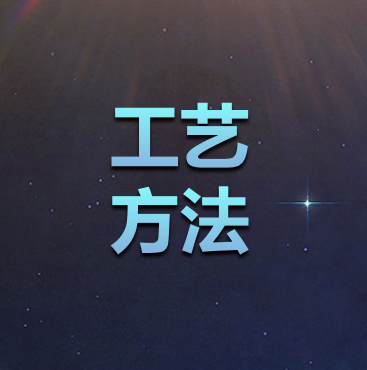
Extreme Functional Materials/Structures/Devices
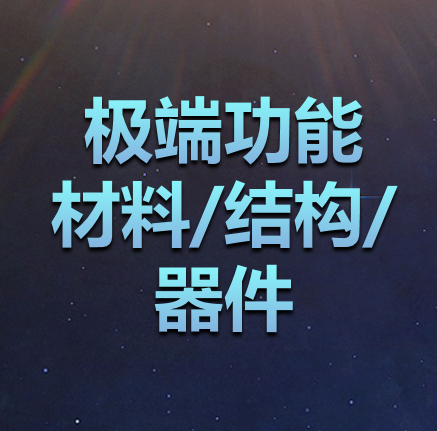
Measurement and Systems
Special Articles
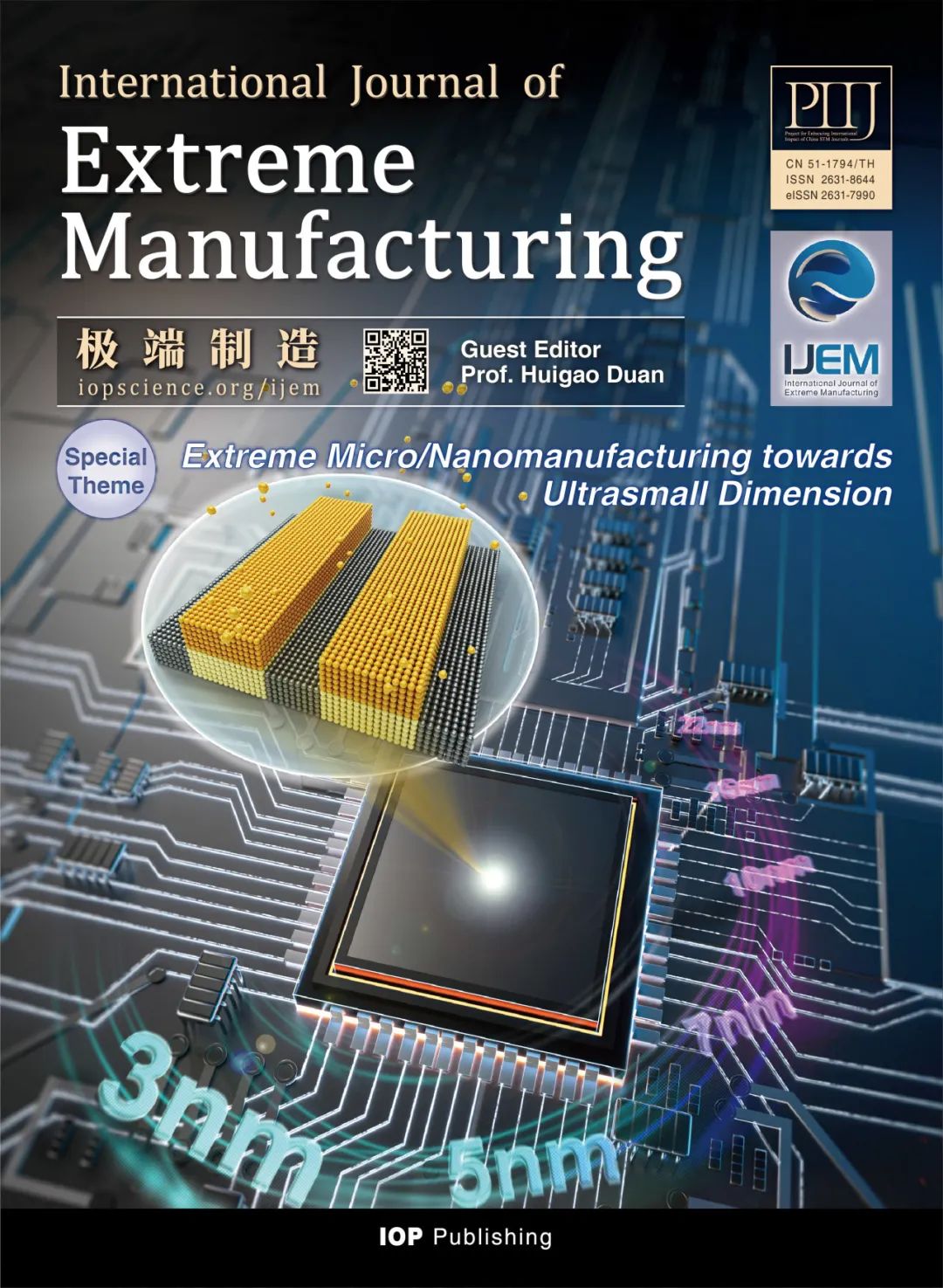
“Extreme Micro-Nano Manufacturing at the Extreme Small Scale”
Special Topic Recommendations
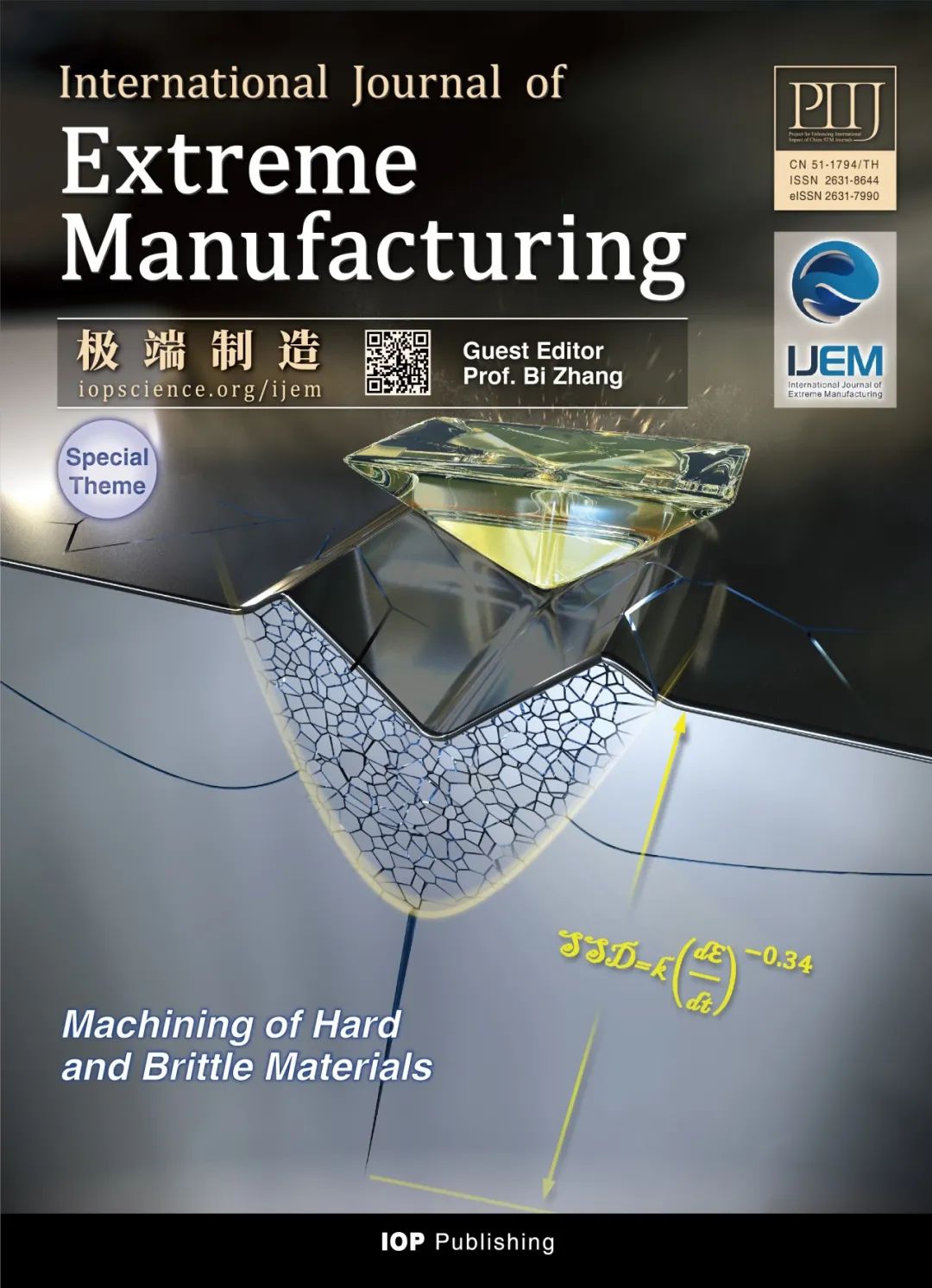
“Processing of Hard and Brittle Materials”
Special Topic Recommendations
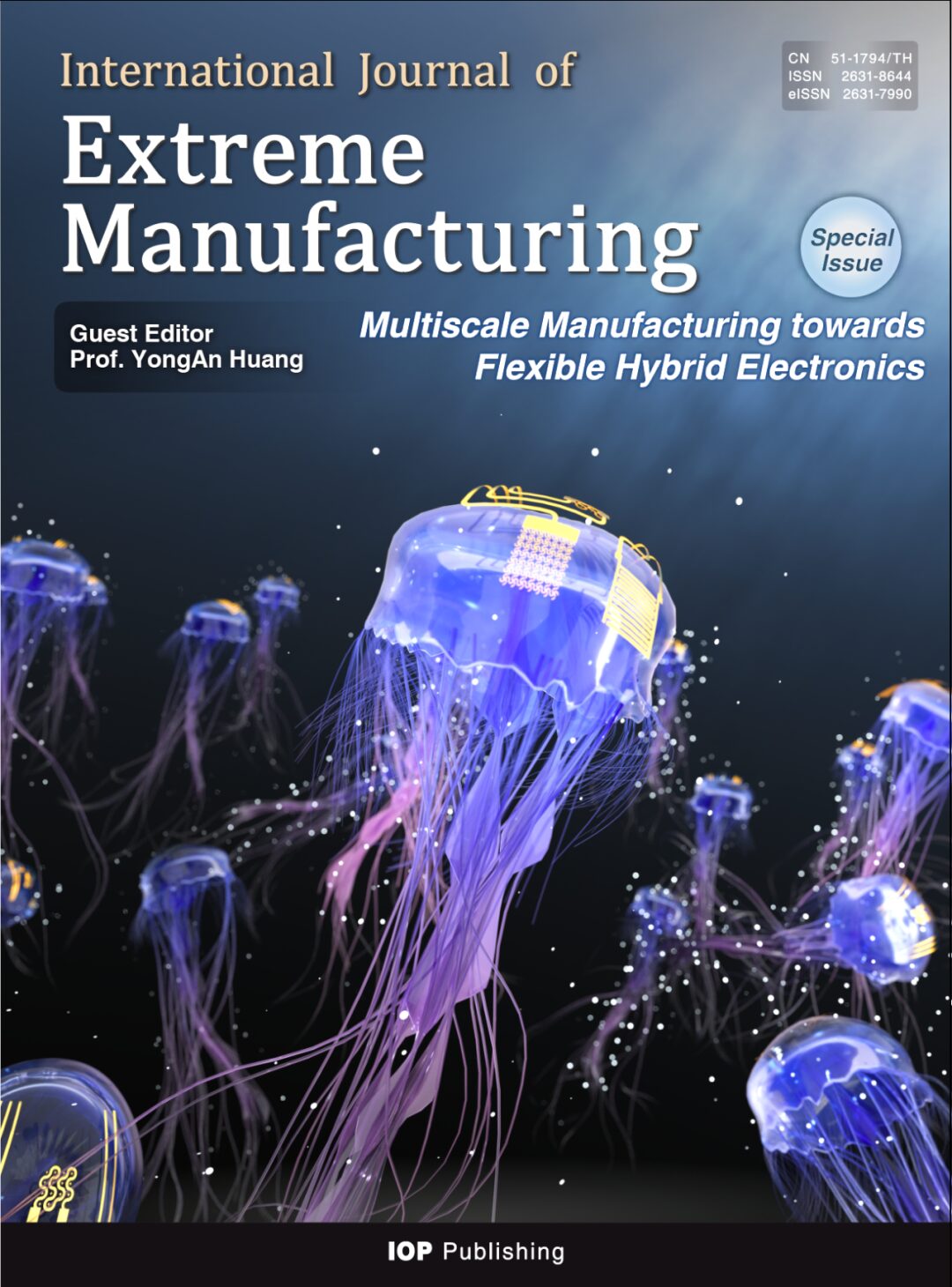
“Flexible Hybrid Electronic Cross-Scale Manufacturing”
Special Topic Recommendations
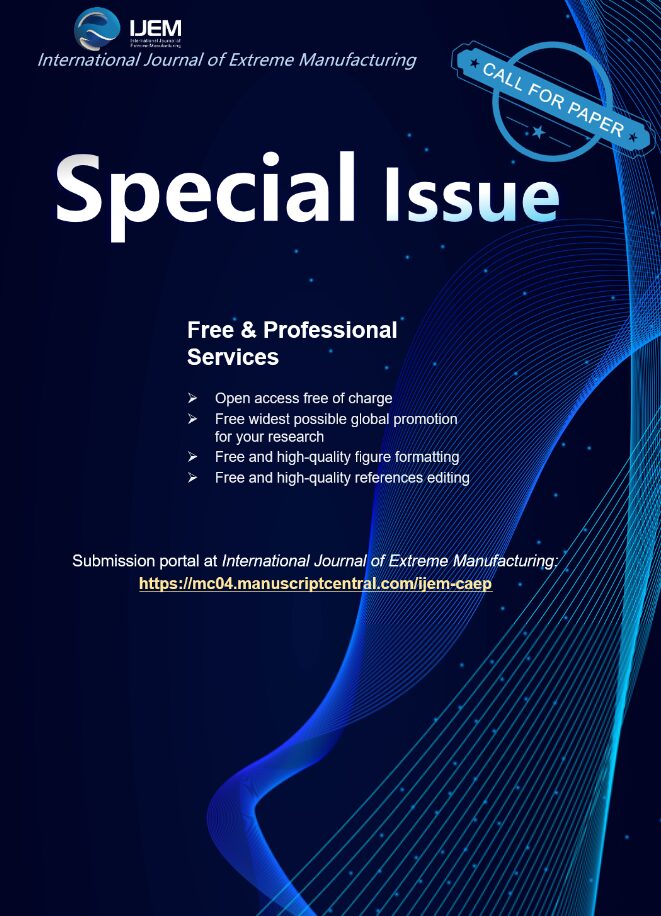
Special Call for Papers
Article Directory
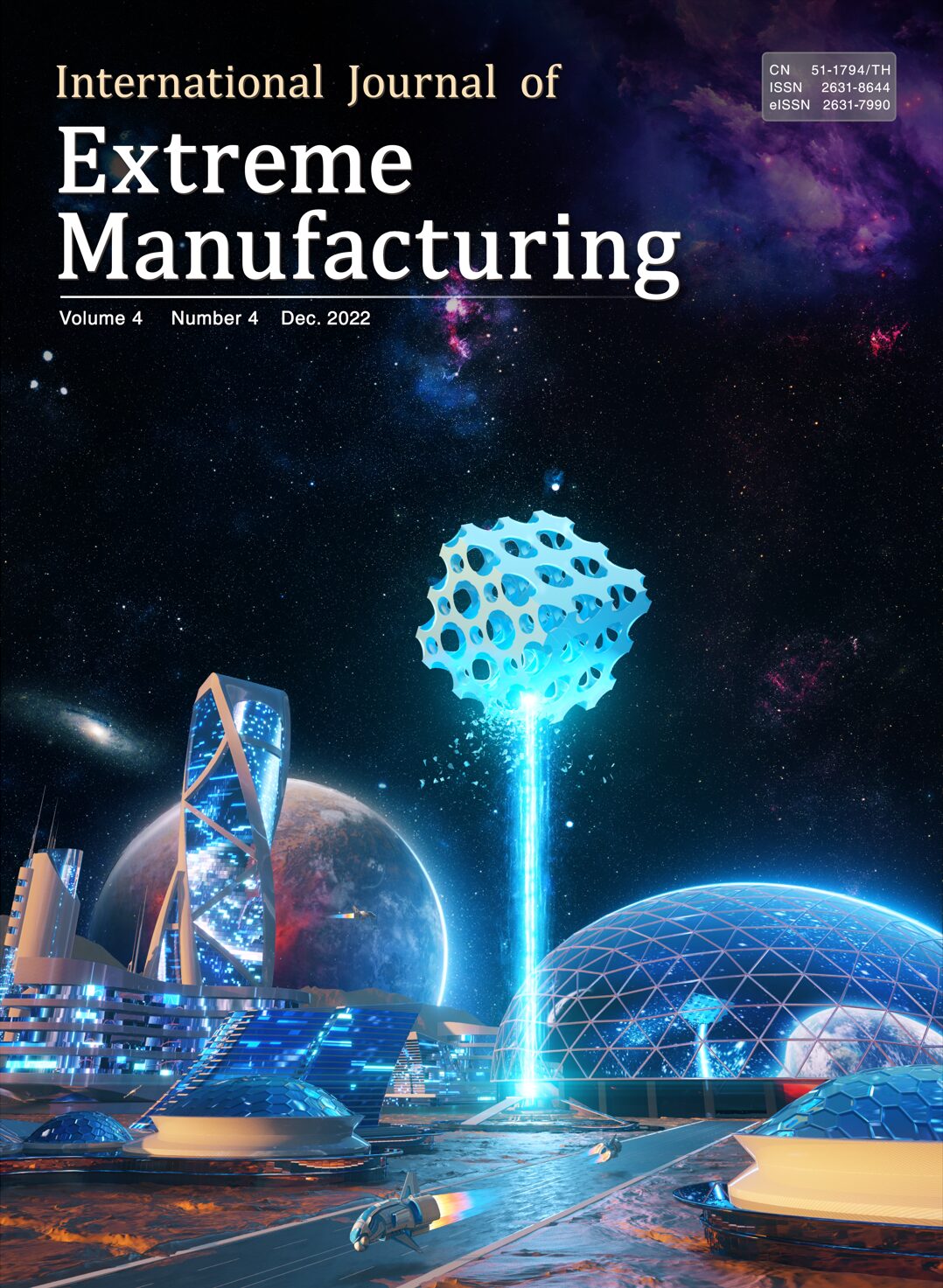
April 2022
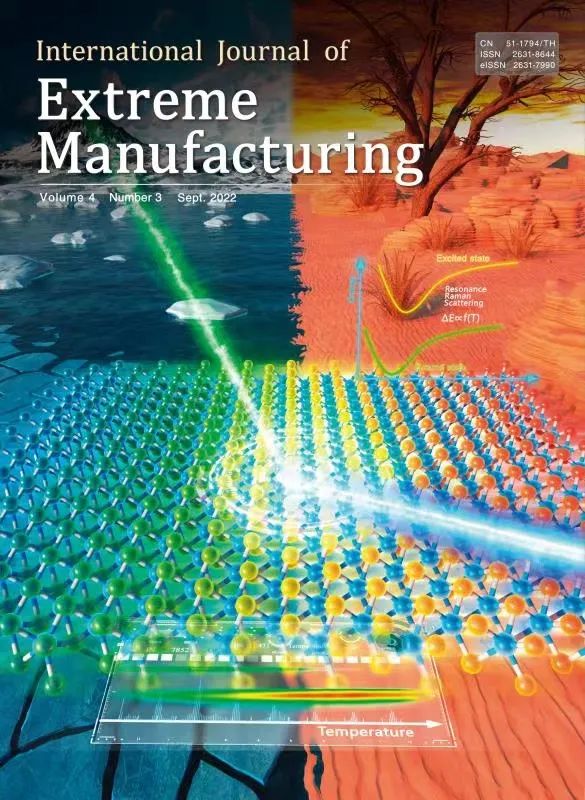
March 2022
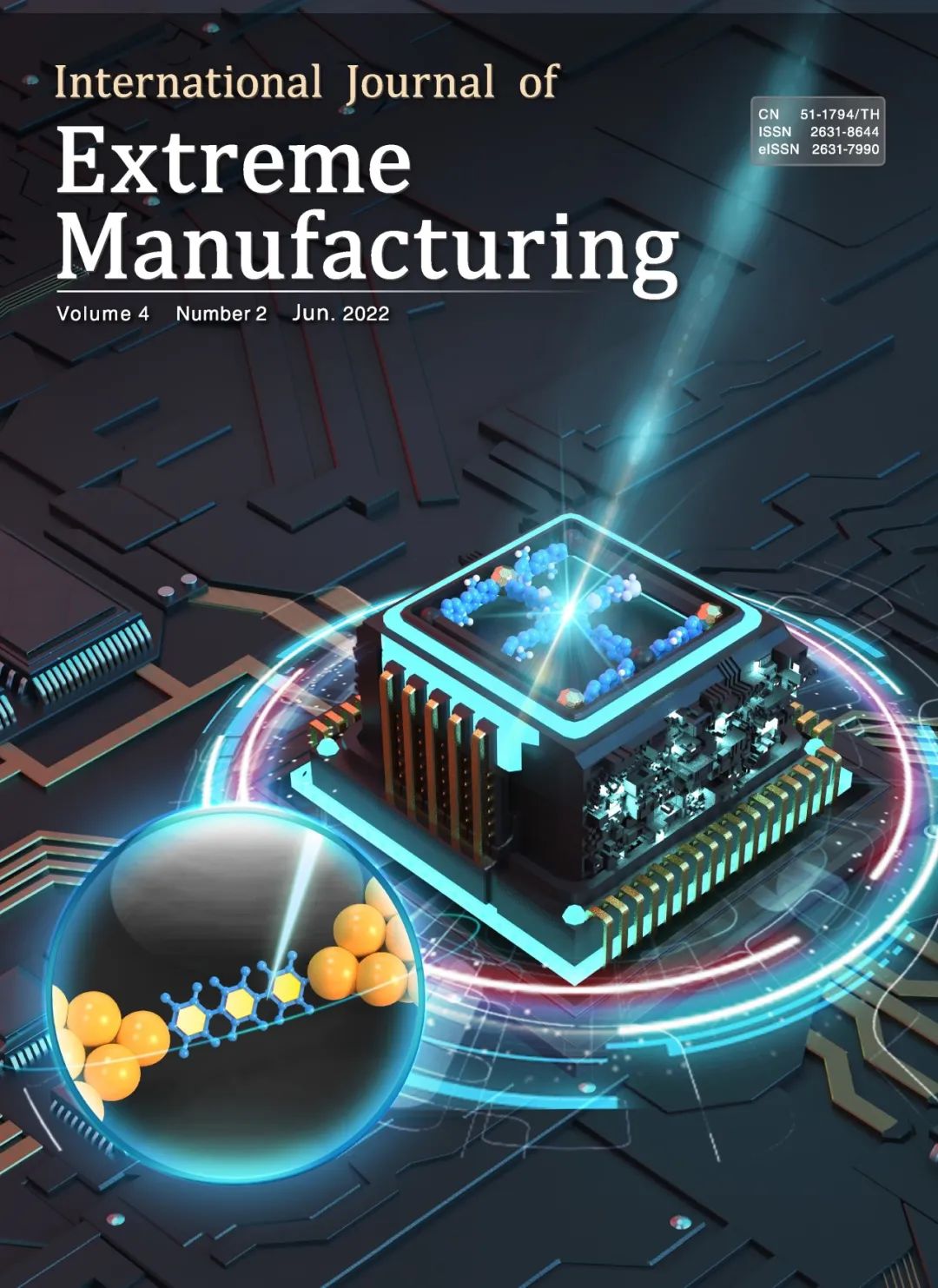
February 2022
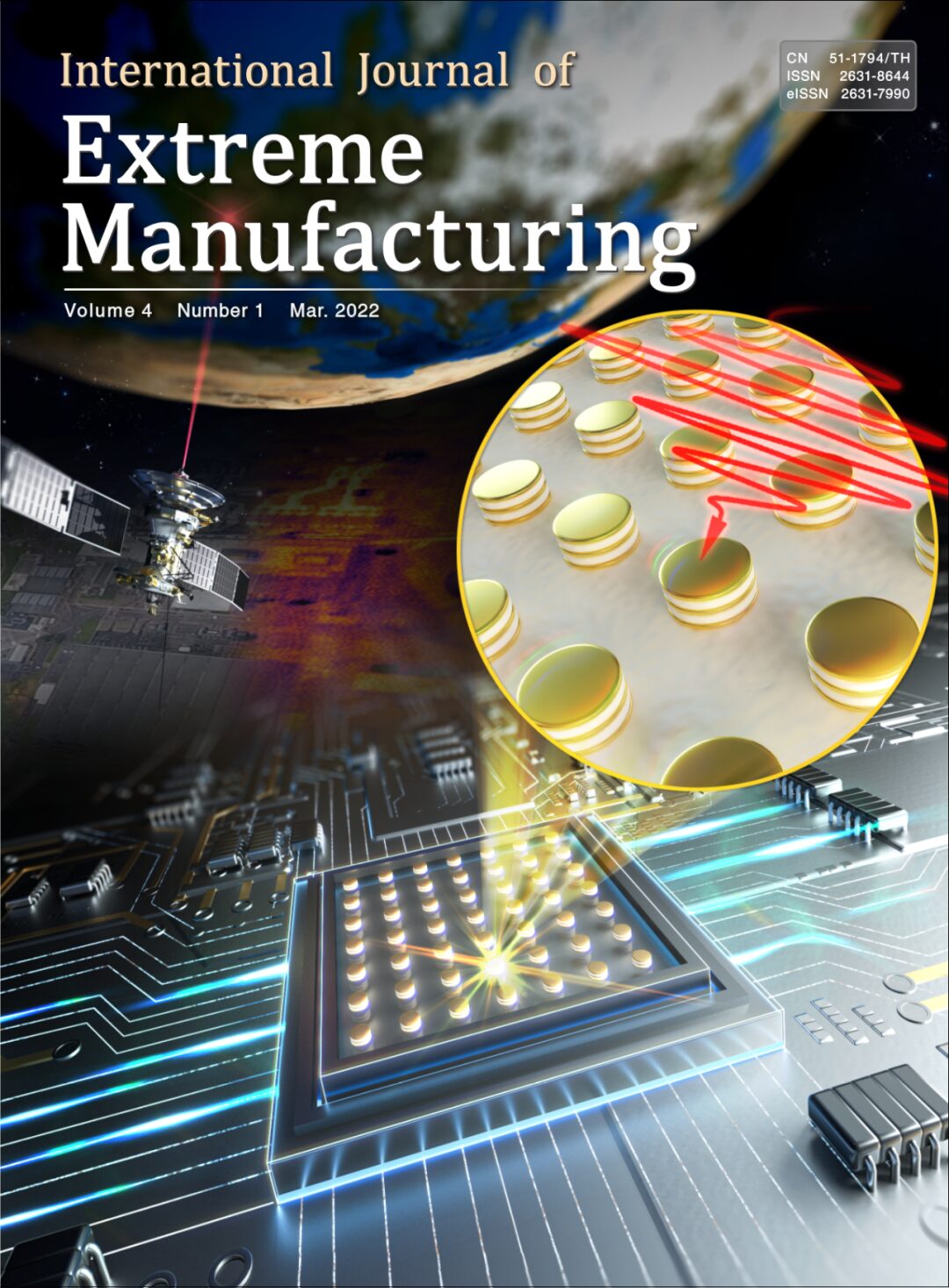
January 2022
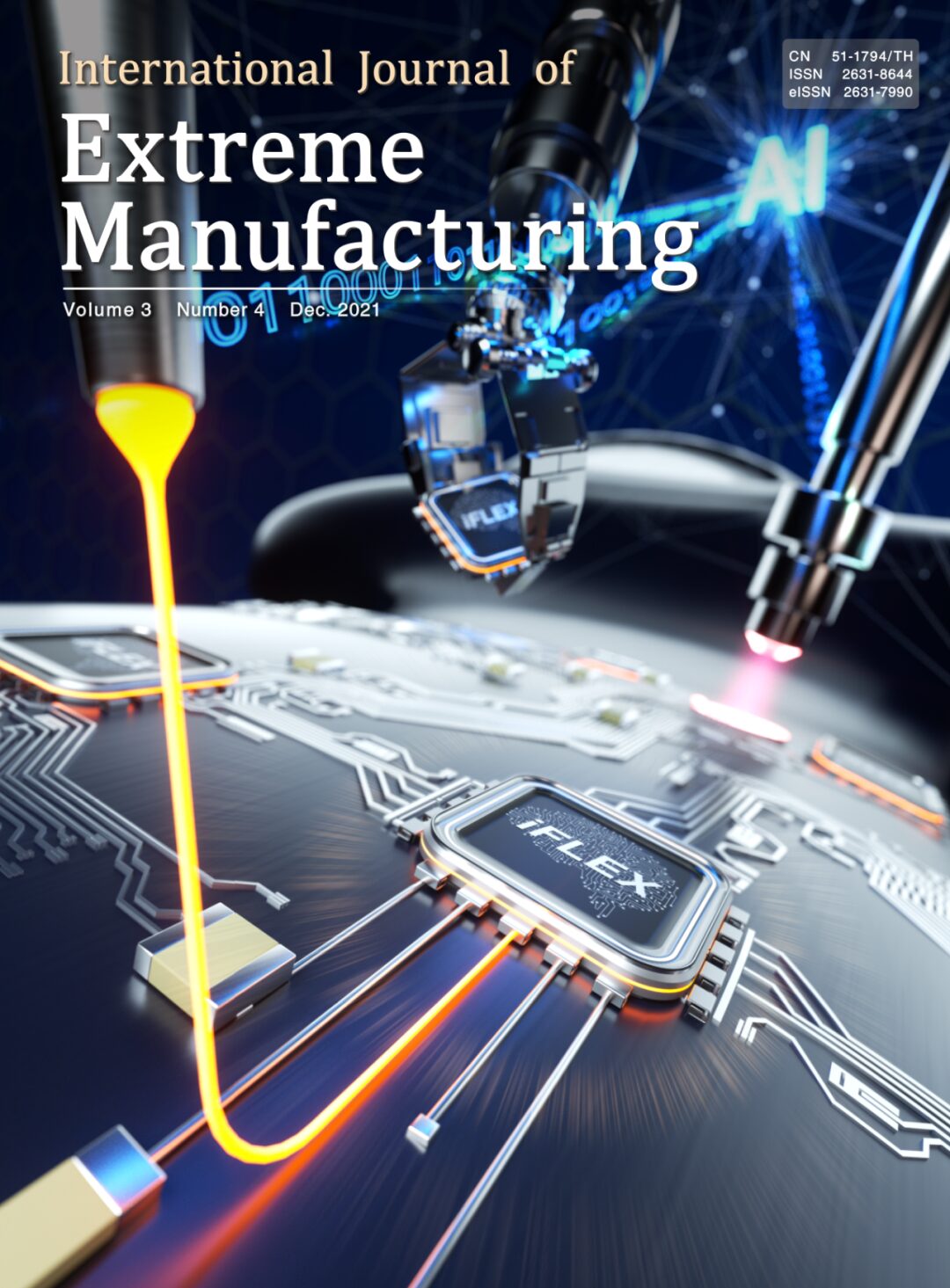
April 2021
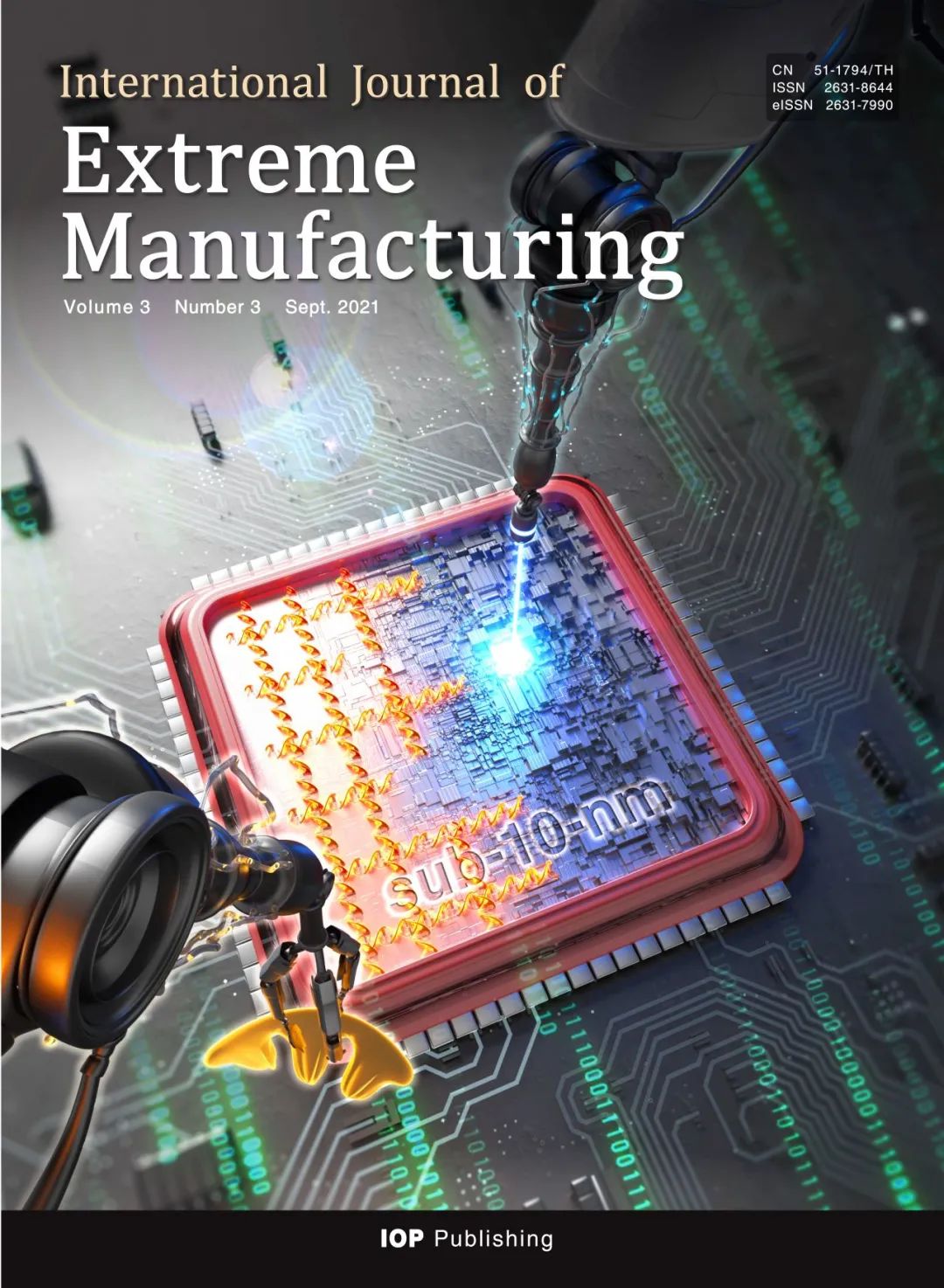
March 2021
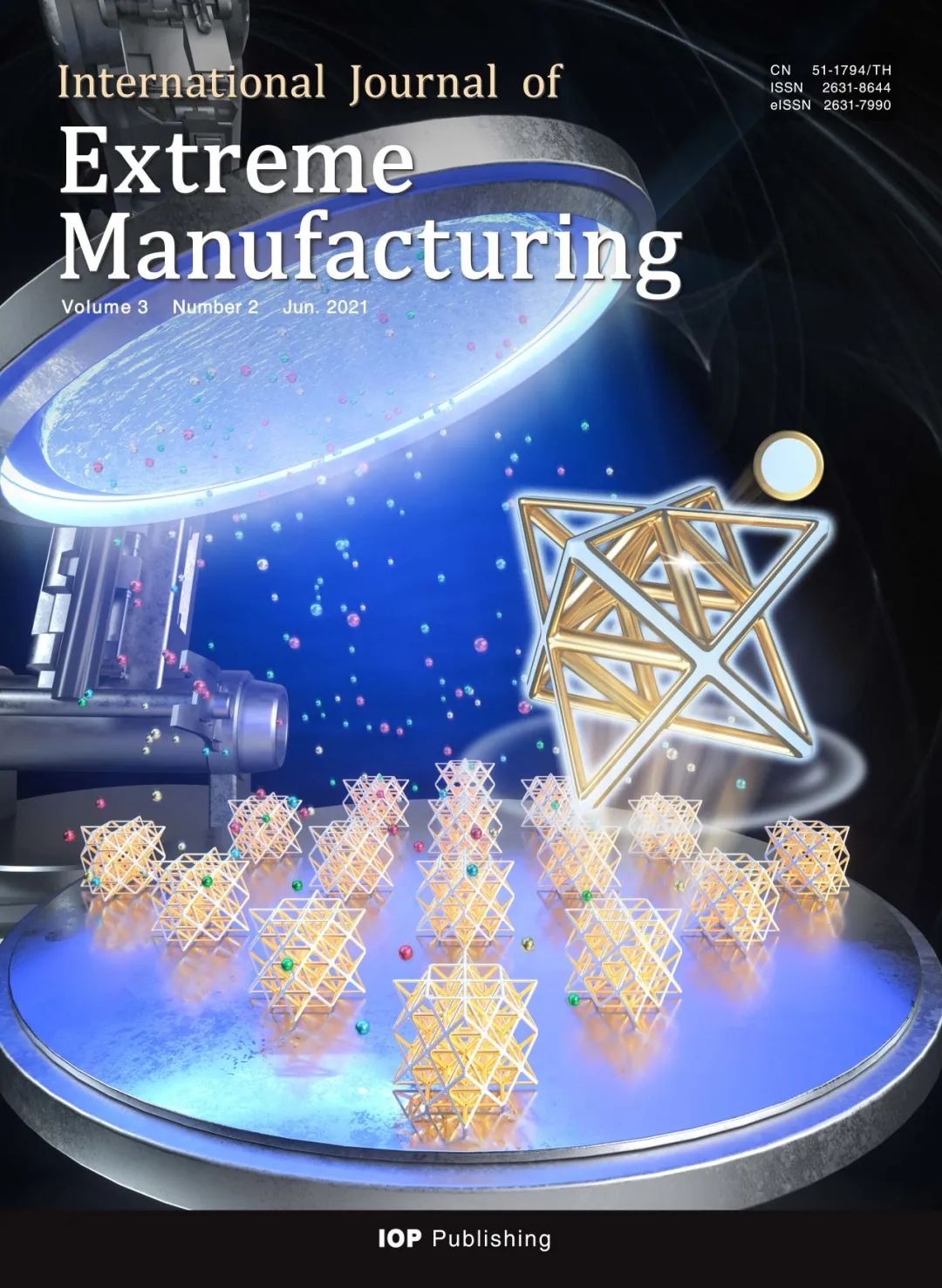
February 2021
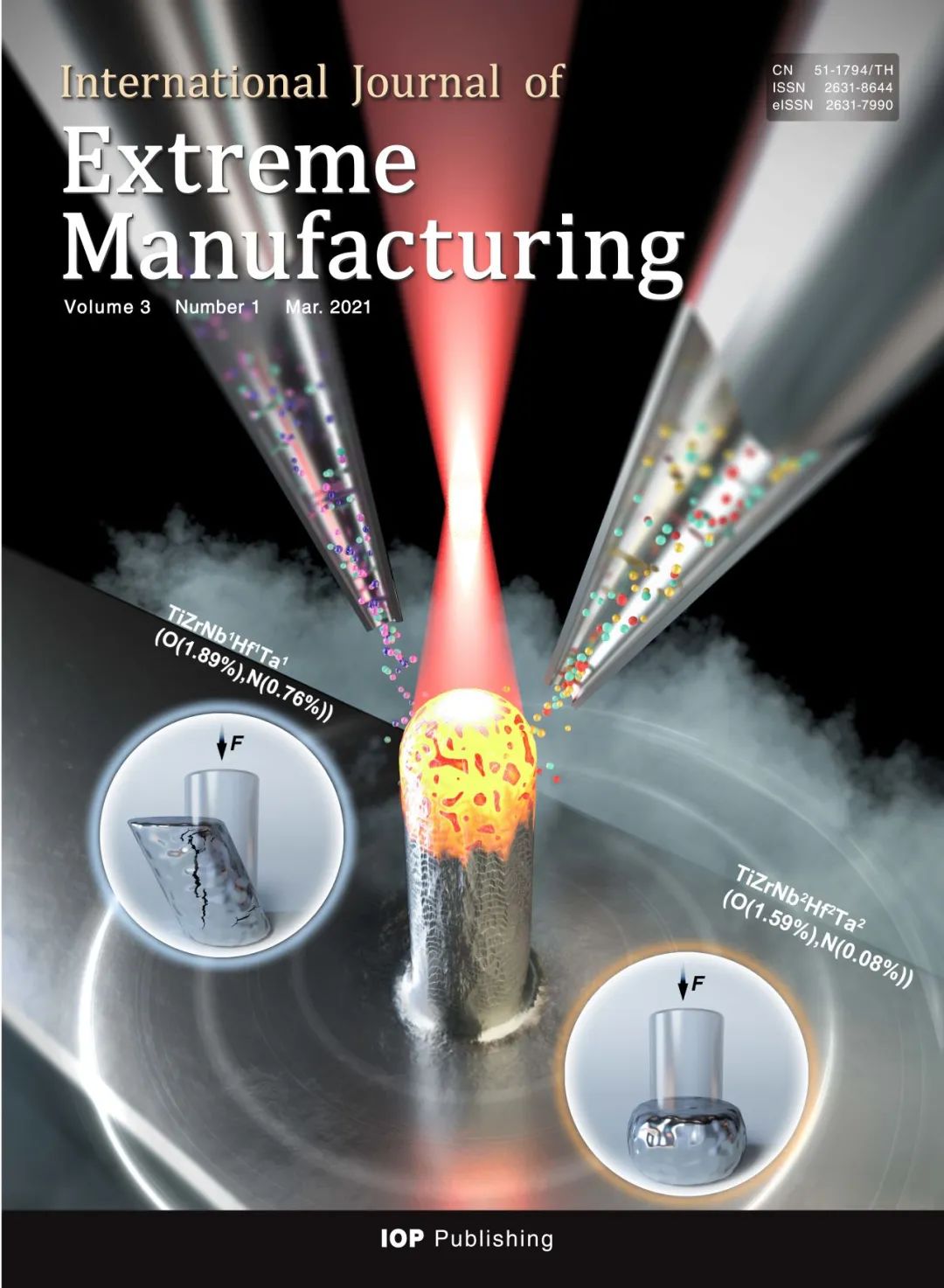
January 2021
More about IJEM
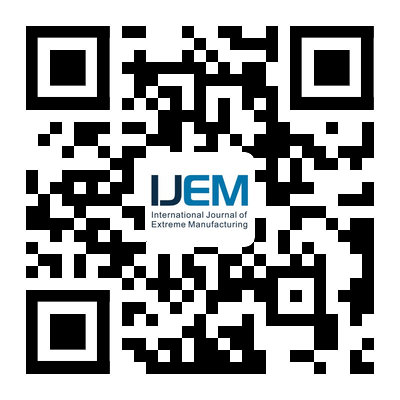
Submission Link
https://mc04.manuscriptcentral.com/ijem-caep
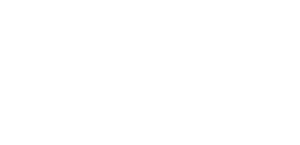
This article aims to convey and share the latest scientific research information. If there are any copyright issues regarding the work, please contact us in a timely manner, and we will handle it promptly to protect your rights. Thank you for your continued attention and support to our public account!
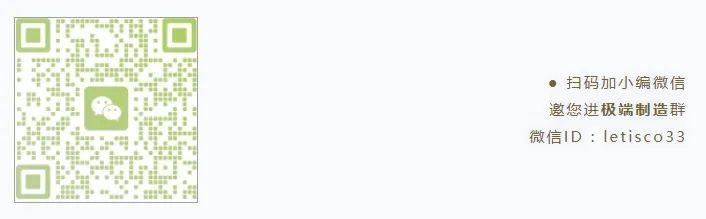
Written by: Author Edited by: Fan Keyan Reviewed by: Guan Lichao