
Sensor is a common yet very important device that senses various quantities to be measured and converts them into useful signals according to certain rules. For sensors, the input can be divided into static and dynamic quantities based on the input status. We can obtain the static characteristics of the sensor by analyzing the relationship between the output and input quantities under stable conditions.
The main indicators of the static characteristics of a sensor include linearity, hysteresis, repeatability, sensitivity, and accuracy. The dynamic characteristics of a sensor refer to its response to input quantities that change over time. Dynamic characteristics are usually described using models like transfer functions in automatic control. Typically, the signals received by sensors contain weak low-frequency signals, and external interference can sometimes exceed the measured signal, making noise elimination a critical sensor technology.
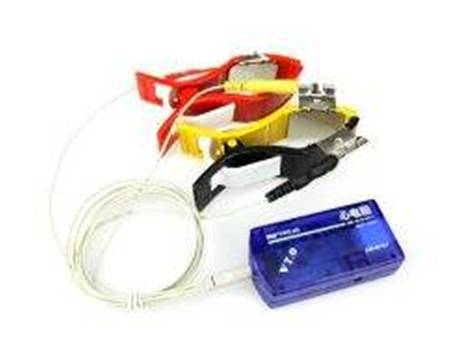
1. Physical Sensors
Physical sensors are devices that detect physical quantities. They utilize certain physical effects to convert the measured physical quantities into energy forms that are easy to process. The output signal has a definite relationship with the input signal. Major types of physical sensors include photoelectric sensors, piezoelectric sensors, resistive sensors, electromagnetic sensors, thermoelectric sensors, and optical fiber sensors. For example, let’s look at the commonly used photoelectric sensor. This sensor converts light signals into electrical signals, directly detecting radiation information from objects and can also convert other physical quantities into light signals.
The main principle is the photoelectric effect: when light illuminates a material, the electrical effects within the material change, including electron emission, conductivity, and potential current. Clearly, devices that easily generate such effects become the main components of photoelectric sensors, such as photoresistors. Thus, we understand that the main workflow of a photoelectric sensor is to receive the corresponding light illumination, convert light energy into electrical energy through devices like photoresistors, and then through amplification and noise reduction processing, obtain the desired output electrical signal. The output electrical signal has a certain relationship with the original light signal, usually close to linear, making it not very complicated to calculate the original light signal. The principles of other physical sensors can be analogized to that of the photoelectric sensor.
The application range of physical sensors is very broad. Let’s look at the application of physical sensors from a biomedical perspective, and it is not difficult to infer that physical sensors also have important applications in other fields.
For example, blood pressure measurement is one of the most routine medical measurements. Our usual blood pressure measurements are indirect, detecting the relationship between blood flow and pressure on the body surface to determine the blood pressure value in the blood vessels. The sensors used for blood pressure measurement usually include a flexible diaphragm that converts pressure signals into diaphragm deformation and then converts this deformation into corresponding electrical signals according to the strain or displacement of the diaphragm. At the peak of the electrical signal, we can detect systolic pressure, and through an inverter and peak detector, we can obtain diastolic pressure, while an integrator can provide the average pressure.
Let’s take a look at respiratory measurement technology. Respiratory measurement is an important basis for clinical diagnosis of lung function and is essential in surgery and patient monitoring. For instance, when using a thermistor sensor to measure respiratory frequency, the sensor’s resistance is mounted on the outer side of a clip that is clamped to the nostril. When the breathing airflow passes over the thermistor’s surface, it can measure the respiratory frequency and the state of the heated air through the thermistor.
Another common example is the measurement of body surface temperature, which may seem straightforward but has a complex measurement mechanism. Body surface temperature is determined by various factors such as local blood flow, thermal conductivity of underlying tissues, and heat dissipation from the skin. Therefore, measuring skin temperature requires consideration of multiple influences. Thermocouple sensors are commonly used for temperature measurement, typically in rod-shaped and thin-film forms. Due to their very small size, high-precision thermocouples can achieve micron-level accuracy, allowing for precise temperature measurements at specific points, and with subsequent statistical analysis, comprehensive results can be derived. This is unmatched by traditional mercury thermometers and demonstrates the broad prospects brought by applying new technologies to scientific development.
From the above introduction, it can be seen that physical sensors have a wide variety of applications, even just in biomedicine. The development direction of sensors is towards multifunctionality, imaging capabilities, and intelligence. Sensor measurements, as an important means of data acquisition, are essential devices in industrial production and even in household life, while physical sensors are the most common family of sensors. Flexibly utilizing physical sensors will undoubtedly create more products and better benefits.
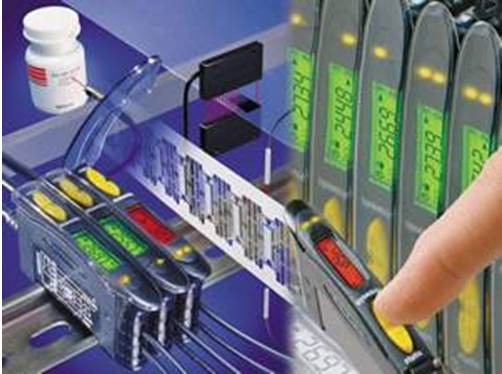
2. Optical Fiber Sensors
In recent years, sensors have been developing towards sensitivity, precision, adaptability, compactness, and intelligence. In this process, optical fiber sensors, a new member of the sensor family, have gained much favor. Optical fibers possess many excellent properties, such as resistance to electromagnetic interference and atomic radiation, fine diameter, soft texture, lightweight mechanical properties, insulating and non-inductive electrical properties, as well as resistance to water, high temperatures, and corrosion.
Optical fiber sensors are a new technology that has emerged in recent years and can be used to measure various physical quantities such as sound fields, electric fields, pressure, temperature, angular velocity, and acceleration, and can accomplish measurement tasks that existing technologies find difficult. In confined spaces, under strong electromagnetic interference and high voltage environments, optical fiber sensors have shown unique capabilities. Currently, there are over 70 types of optical fiber sensors, generally divided into self-sensing optical fibers and optical fiber-utilizing sensors.
The so-called self-sensing optical fiber sensors directly receive external measured quantities. External physical quantities can cause changes in the length, refractive index, or diameter of the measuring arm, leading to changes in the light transmitted within the optical fiber in terms of amplitude, phase, frequency, and polarization. The light transmitted by the measuring arm interferes with the reference light from the reference arm, causing changes in the phase (or amplitude) of the output light, which can be used to detect changes in the measured quantities. The sensitivity of the phase transmitted in the optical fiber to external influences is very high, and using interference technology, we can detect physical quantities corresponding to minute phase changes of 10^-4 radians. By utilizing the flexibility and low loss of optical fibers, very long fibers can be wound into small diameter loops to increase utilization length and obtain higher sensitivity.
Optical fiber acoustic sensors are a type of self-sensing optical fiber sensor. When a very small external force acts on the optical fiber, it causes a slight bending, resulting in significant changes in light transmission capability. Sound is a mechanical wave, and its effect on the optical fiber is to apply force and cause bending, thus allowing us to measure the strength of sound through this bending. Optical fiber gyroscopes are also a type of self-sensing optical fiber sensor, which, compared to laser gyroscopes, have higher sensitivity, smaller size, and lower cost, making them suitable for high-performance inertial navigation systems in aircraft, ships, missiles, etc.
The other major category of optical fiber sensors is those that utilize optical fibers. Their structure is generally as follows: the sensor is located at the end of the optical fiber, which only serves as a transmission line for light, converting the measured physical quantities into changes in light amplitude, phase, or intensity. In this type of sensor system, traditional sensors are combined with optical fibers. The introduction of optical fibers enables remote measurement with a probing capability. These optical fiber transmission sensors have a wide range of applications and are easy to use, but their precision is slightly lower than that of the first type of sensor.
Optical fibers are a latecomer in the sensor family, but they have gained widespread application due to their excellent performance, making them a noteworthy sensor in production practices.
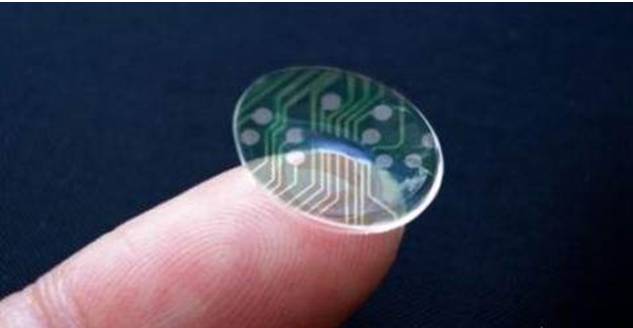
3. Bionic Sensors
Bionic sensors are a new type of sensor that employs new detection principles, combining immobilized cells, enzymes, or other bioactive substances with transducers. This type of sensor is a new information technology that has developed from the intersection of biomedicine, electronics, and engineering in recent years. The characteristics of this sensor are high functionality and long lifespan. Among bionic sensors, the most commonly used are bio-simulating sensors.
Bionic sensors can be classified based on the medium used: enzyme sensors, microbial sensors, organelle sensors, tissue sensors, etc. In the figure, we can see that bionic sensors are closely related to various aspects of biological theories, being a direct result of the development of biological theories. In bio-simulating sensors, urea sensors are a recently developed type of sensor. Below, we will introduce the application of bionic sensors using the urea sensor as an example.
The urea sensor mainly consists of a biomembrane and its ion channels. The biomembrane can sense external stimuli, while the ion channel receives information from the biomembrane and amplifies and transmits it. When the sensing part of the membrane is influenced by external stimulating substances, the permeability of the membrane changes, causing a large influx of ions into the cells, forming the transmission of information. The key component in this process is the membrane proteins that make up the biomembrane, which can produce conformational network changes, altering the membrane’s permeability for information transmission and amplification. The ion channels of the biomembrane, composed of amino acid polymers, can be replaced by easily synthesized polymers in organic chemistry, such as poly-L-glutamic acid (PLG), which has better chemical stability than enzymes.
PLG is water-soluble and not suitable for the modification of electrical machines, but it can be synthesized into block copolymers with polymers to form sensing membranes for sensor use. The principle of the ion channels of the biomembrane is essentially the same as that of the biomembrane itself. When the block copolymer membrane is fixed onto electrodes and substances that induce changes in the PLG conformational network are added, the permeability of the membrane will change, resulting in a change in current, which can be used to detect stimulating substances. Urea sensors have been proven to be stable bio-simulating sensors, with a detection limit in the order of 10^-3, and they can detect stimulating substances, but they are currently not suitable for biological measurements.
Although many bionic sensors have been successfully developed, their stability, reproducibility, and mass production capabilities are significantly lacking, indicating that bionic sensing technology is still in its infancy. Therefore, in addition to continuing to develop new series of bionic sensors and improve existing series, further research into the immobilization technology of bioactive membranes and the solidification of bionic sensors is warranted.
In the near future, bionic sensors that simulate the functions of smell, taste, hearing, and touch may appear, potentially surpassing human sensory capabilities and enhancing the current capabilities of robots in visual, taste, touch, and operational tasks. We can see the broad prospects for the application of bionic sensors, but all this requires further development of biotechnology, and we look forward to the arrival of that day.
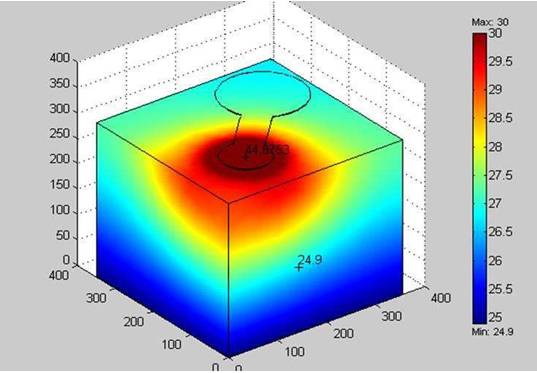
4. Infrared Sensors
Infrared technology has developed to a point where it is widely known, and this technology has found extensive applications in modern science and technology, national defense, and agriculture and industry. Infrared sensing systems are measurement systems that use infrared rays as the medium, which can be classified into five categories based on their functions: ① Radiometers for radiation and spectral measurements; ② Search and tracking systems for searching and tracking infrared targets, determining their spatial position and tracking their motion; ③ Thermal imaging systems, which can produce distribution images of infrared radiation from entire targets; ④ Infrared ranging and communication systems; ⑤ Hybrid systems, which are combinations of two or more of the above systems.
The core of infrared systems is the infrared detector, which can be divided into two main categories based on the detection mechanism: thermal detectors and photon detectors. Below, we will analyze the principles of thermal detectors as an example.
Thermal detectors utilize the radiation heat effect, causing the temperature of the detection element to rise upon receiving radiated energy, thereby causing changes in temperature-dependent performance of the detector. By detecting changes in one of these performances, radiation can be detected. Most of the time, radiation is detected through thermoelectric changes. When the element receives radiation, it causes non-electrical physical changes, which can be measured as corresponding electrical changes after appropriate transformations.
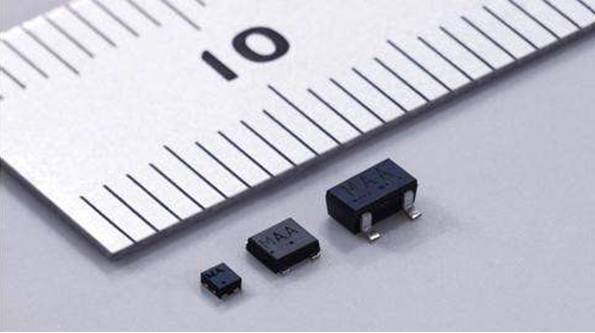
5. Electromagnetic Sensors
Magnetic sensors are the oldest type of sensors, with the compass being one of the earliest applications of magnetic sensors. However, as modern sensors, magnetic sensors need to convert magnetic signals into electrical signals for easier signal processing. The earliest applications were magnetic-electric sensors based on the principle of electromagnetic induction. These magnetic-electric sensors made outstanding contributions in the field of industrial control but have now been replaced by new magnetic sensors based on high-performance magnetic-sensitive materials.
Among the electromagnetic effect sensors used today, magnetic rotary sensors are an important type. Magnetic rotary sensors mainly consist of semiconductor magnetoresistive elements, permanent magnets, fixtures, and housings. A typical structure involves installing a pair of magnetoresistive elements on a permanent magnet’s stimulus, connecting the input and output terminals of the elements to the fixture, and then installing them in a metal box, sealed with engineering plastics to form a closed structure, providing good reliability. Magnetic rotary sensors have many advantages in shape that cannot be matched by many semiconductor magnetoresistive elements. In addition to high sensitivity and large output signals, they also have a wide range of rotational speed detection, thanks to advancements in electronic technology. Moreover, these sensors can operate over a wide temperature range and have a long service life, with strong resistance to dust, water, and oil contamination, making them suitable for various environmental conditions and external noise. Therefore, these sensors are widely emphasized in industrial applications.
Magnetic rotary sensors have extensive applications in factory automation systems because they possess satisfactory characteristics and require no maintenance. They are primarily used in detecting the rotation of machine tool servo motors, positioning robotic arms in factory automation, detecting hydraulic strokes, positioning related equipment in factory automation, detecting units in rotary encoders, and various rotating detection units. Modern magnetic rotary sensors mainly include four-phase sensors and single-phase sensors. During operation, four-phase differential rotary sensors use one pair of detection units for differential detection and another pair for reverse differential detection. Thus, the detection capability of four-phase sensors is four times that of single units. The two-element single-phase rotary sensors also have their own advantages, namely their compact and reliable design, large output signals, ability to detect low-speed movements, strong resistance to environmental influences, and low noise susceptibility, making them cost-effective. Therefore, single-phase sensors also have good market potential.
Magnetic rotary sensors also have significant application potential in household appliances. In cassette recorders, magnetoresistive elements can be used to detect the end of the tape. Most home video recorders have variable speed and high-speed playback functions, which can also utilize magnetic rotary sensors to detect spindle speed and control it for high-quality images. The forward and reverse rotation and high and low-speed functions of motors in washing machines can also be achieved through servo rotary sensors for detection and control. Such switches can sense metallic objects entering their inspection area, controlling their internal circuits to turn on or off. The switch generates its own magnetic field, and when a metallic object enters the magnetic field, it causes a change in the magnetic field. This change can be converted into an electrical signal through the internal circuit of the switch.
Furthermore, electromagnetic sensors are a widely applied high-tech field, with significant research efforts invested both domestically and internationally. The applications of these sensors are infiltrating various sectors of the national economy, national defense construction, and daily life. With the arrival of the information society, their status and role will surely increase.
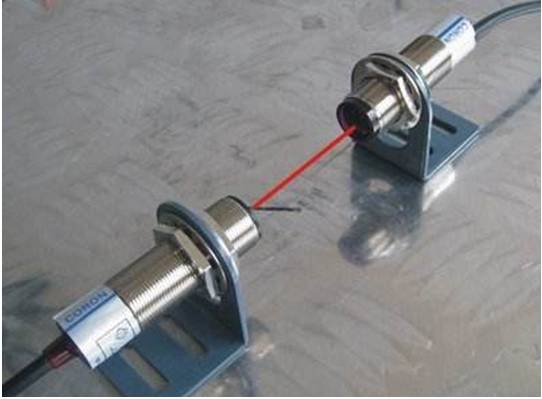
6. Magneto-Optic Effect Sensors
Modern electrical measurement technology is maturing, and due to its advantages of high precision and ease of connection to microcomputers for automatic real-time processing, it has been widely applied in the measurement of electrical and non-electrical quantities. However, electrical measurement methods are easily affected by interference, and during AC measurements, the frequency response may not be wide enough, and there are certain requirements for voltage resistance and insulation. With the rapid development of laser technology, these problems can now be solved.
Magneto-optic effect sensors are high-performance sensors developed using laser technology. Lasers, which rapidly developed in the early 1960s, marked a new phase in the mastery and utilization of light waves. Previously, ordinary light sources had low monochromaticity, limiting many important applications; the advent of lasers has propelled radio and optical technologies to leap forward, mutually permeating and complementing each other. Today, many sensors utilizing lasers have been developed, solving many technical challenges that were previously insurmountable, making them suitable for hazardous and flammable environments such as coal mines, oil, and natural gas storage.
For instance, laser-made optical fiber sensors can measure parameters such as crude oil jetting and cracking in large oil tanks. In real measurement locations, there is no need for power supply, which is particularly suitable for petrochemical equipment that requires strict safety and explosion-proof measures. They can also be used to implement optical methods for remote chemical measurements in certain processes at large steel plants.
The principle of magneto-optic effect sensors is mainly based on the polarization state of light to realize the sensor’s functionality. When a beam of polarized light passes through a medium, if there is an external magnetic field in the direction of light propagation, the light beam will rotate at an angle upon passing through the polarization plane. This is known as the magneto-optic effect. The angle of rotation can be used to measure the applied magnetic field. Under specific experimental setups, the deflection angle is proportional to the output light intensity, and by shining the output light onto a laser diode (LD), digitized light intensity can be obtained to measure specific physical quantities.
Since the late 1960s, when RCLecraw published research reports on the magneto-optic effect, it has garnered significant attention. Countries such as Japan and the Soviet Union have conducted research, and scholars domestically have also explored this field. Magneto-optic effect sensors possess excellent electrical insulation, anti-interference, wide frequency response, fast response, and safety explosion-proof characteristics, making them uniquely effective for measuring electromagnetic parameters in special situations, especially in measuring high voltage and large currents in power systems, where they exhibit significant advantages. Additionally, by developing software and hardware for processing systems, automatic real-time measurements can be achieved for welding machines and robotic control systems.
In the use of magneto-optic effect sensors, the most important aspect is selecting the magneto-optic medium and laser. Different devices have varying capabilities in sensitivity and operational range. With the emergence of high-performance lasers and new magneto-optic media in recent decades, the performance of magneto-optic effect sensors has become increasingly robust, and their applications are becoming more widespread. As a type of specific-purpose sensor, magneto-optic effect sensors can perform their functions in special environments and are very important industrial sensors.
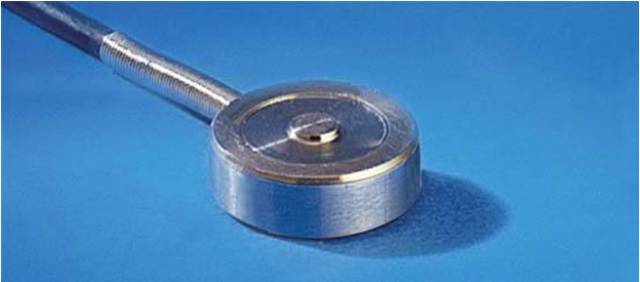
7. Pressure Sensors
Pressure sensors are the most commonly used type of sensor in industrial practice, and the pressure sensors we typically use are mainly made using the piezoelectric effect, also known as piezoelectric sensors.
We know that crystals are anisotropic, while amorphous materials are isotropic. Certain crystalline media, when subjected to mechanical force along a specific direction, undergo deformation and produce a polarization effect. When the mechanical force is removed, they revert to a non-charged state; that is, when subjected to pressure, certain crystals can generate electrical effects, which is known as the polarization effect. Scientists have developed pressure sensors based on this effect.
The main piezoelectric materials used in piezoelectric sensors include quartz, sodium tartrate, and ammonium dihydrogen phosphate. Among them, quartz (silicon dioxide) is a natural crystal where the piezoelectric effect was first discovered. The piezoelectric properties persist within a certain temperature range, but when temperatures exceed this range, the piezoelectric properties completely disappear (this high temperature is known as the “Curie point”). As the change in electric field with stress is minimal (indicating a relatively low piezoelectric coefficient), quartz has gradually been replaced by other piezoelectric crystals. Sodium tartrate has a high piezoelectric sensitivity and coefficient but can only be used in low-temperature and low-humidity environments. Ammonium dihydrogen phosphate is a synthetic crystal that can withstand high temperatures and relatively high humidity, making it widely used. Nowadays, the piezoelectric effect is also applied to polycrystals, such as piezoelectric ceramics, including barium titanate piezoelectric ceramics, PZT, niobate piezoelectric ceramics, and lead magnesium niobate piezoelectric ceramics.
The piezoelectric effect is the main working principle of piezoelectric sensors. Piezoelectric sensors cannot be used for static measurements because the electric charge generated by external force can only be preserved if the circuit has infinitely large input impedance. In reality, this is not the case, which determines that piezoelectric sensors can only measure dynamic stresses.
Piezoelectric sensors are primarily used in the measurement of acceleration, pressure, and force. Piezoelectric accelerometers are a common type of accelerometer. They have advantages such as simple structure, small size, lightweight, and long service life. Piezoelectric accelerometers have been widely used in measuring vibrations and impacts in aircraft, automobiles, ships, bridges, and buildings, particularly holding a special position in the aerospace field. They can also be used to measure combustion pressure inside engines and vacuum levels. Additionally, they can be used in military applications, such as measuring the pressure changes in the chamber at the moment a bullet is fired and the shockwave pressure at the muzzle.
They can measure both large and small pressures. Piezoelectric sensors are also widely used in biomedical measurements, such as the ventricular catheter microphone made from piezoelectric sensors. Since measuring dynamic pressure is so common, piezoelectric sensors have a very broad range of applications. In addition to piezoelectric sensors, there are also resistive sensors made using the piezoresistive effect and strain sensors made using the strain effect; these different pressure sensors utilize different effects and materials to perform their unique functions in different situations.
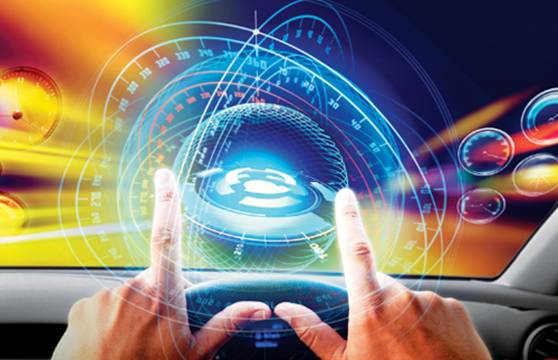
■ This article is sourced from: China Machine Tool Business Network
“Recommended Articles” column is always recruiting good articles
From now on,
The research institute’s WeChat platform
will periodically recommend good articles.
If you read an article you like,
If you read an educational article,
If you read an article that touches your heart,
If you read an article that inspires your work,
Then please send the article link and the name of the recommender
to the WeChat editor:
Leave a message or write a comment on this WeChat,
or send an email to
Let us read, think, and progress together!