Audio Version
Comparative Advantages of Semiconductor Value Chains in Various Countries (Regions)
The U.S. companies dominate the entire semiconductor value chain. The massive share of U.S. IDM comes from Intel (the largest semiconductor company by revenue), Texas Instruments, ADI (analog semiconductors), and Micron (memory chips), among others. The position of the U.S. in fabless chip design is also noteworthy.
U.S. companies have a quasi-monopoly in EDA software, making them significant IP suppliers as well. The largest equipment suppliers in the semiconductor field (Applied Materials, KLA, Lam Research) are all located in the U.S. Companies like Amkor Technologies are globally significant assembly and testing enterprises.
South Korea is another important player in the semiconductor value chain. Typical South Korean IDM enterprises include Samsung and SK Hynix, which dominate the global memory chip market (both DRAM and NAND). For instance, Samsung is strong in various fields—memory chips and chip design (mobile processors)—and possesses the world’s second-largest foundry business scale. South Korea has the largest wafer production capacity, which also means it is one of the most important regions for equipment sales. However, South Korea lacks equipment suppliers, and there are few suppliers of chemicals (LG Chem) and wafers (SK Siltron), and it also does not have any fabless companies.
Overall, European companies play a secondary role in the global semiconductor value chain. European enterprises are strong in sensors, discrete semiconductors, especially automotive integrated circuits. Companies such as Bosch, Infineon, NXP, and STMicroelectronics are IDMs that typically adopt a fab-based approach, which means they rely on foreign chip manufacturing companies like Taiwan Semiconductor Manufacturing Company, Global Foundries, and Samsung. Additionally, European companies play an important role as suppliers in the semiconductor value chain in the following areas: ASML, ASM International, Aixtron (semiconductor equipment suppliers); BASF, Linde, Merck KGaA (semiconductor chemicals); Siltronic (wafers). However, overall, Europe lags behind in wafer manufacturing (high capacity, advanced fabs) and chip design.
Taiwan has companies like Mediatek and Novatek, exerting strong influence in the fabless segment. Although there are not many Taiwanese IDMs, Taiwan Semiconductor Manufacturing Company’s foundry business highlights Taiwan’s important position and role in the global semiconductor value chain. The global advanced chip fabless industry relies on Taiwan Semiconductor Manufacturing Company for foundry services, which may be the most critical single point in the entire semiconductor value chain. Taiwan also has the largest wafer manufacturing capacity and, together with South Korea, is currently one of the most important markets for equipment suppliers. Additionally, due to the numerous subsidiaries of ASE Group, Taiwan occupies a portion of the semiconductor backend market.
Japan’s position in the global semiconductor value chain is comparable to that of Europe. Japanese companies are major suppliers of wafers, holding over 50% of the silicon wafer market, and are crucial for the supply of chemicals and gases, also playing an important role as equipment suppliers (e.g., Tokyo Electron). With IDM KIOXIA, Japan has also entered the NAND memory market. Similar to Europe, Japanese companies play a secondary role in chip design.
Overall, China’s share in the semiconductor value chain is relatively small. Chinese companies have made significant progress in design and packaging, and have invested in wafers, manufacturing equipment (AMEC, Naura, SMEE), and chemicals, but still lag behind foreign counterparts.
Investment Suggestions for Key Segments in the Semiconductor Value Chain by Various Countries
Key PracticesSuggested
The entire production process of semiconductors seems simple, consisting of three main steps: design, front-end manufacturing, and back-end manufacturing. However, it includes numerous supplier markets, from electronic design automation (EDA) tools, to semiconductor chemicals, semiconductor equipment, wafers, process automation, and cleanroom technologies. Chip manufacturing involves over 1000 process steps, and there are about 50 different types of manufacturing equipment in the upstream semiconductor supplier market, with over 400 different chemicals, each with different characteristics. The diversity of equipment, processes, materials, and business models makes semiconductor production extraordinarily complex.Different process technology methods exist for designing and manufacturing power semiconductors and memory chips using silicon carbide, for instance. Furthermore, in the entire semiconductor production process, different products are processed according to different companies’ business models, from integrated device manufacturers IDMs to fabless chip design companies, manufacturing companies, to outsourced semiconductor assembly and testing companies. Many chips are standardized products, such as memory chips, while more chips are highly customized products. Despite the overlap in most production steps, the applicable technologies and functions of the final products differ, such as the market characteristics and business models of memory chips (DRAM and NAND) being significantly different from those of 5G radio frequency (RF) semiconductors. For instance, although all memory chips are based on wafers, 5G RF chips are silicon-based gallium nitride chips, and their specialized processing is completely different from ordinary memory chips.
Given such complex products and processes, what strategies should governments adopt for planning and production to secure a place in the global value chain? A German think tank has provided specific recommendations, namely: understand the market, understand market access barriers, and understand technical characteristics. Subsequently, determine material inputs, such as what type of photoresist to use; determine production steps, such as whether it is 28nm front-end manufacturing or a specific semiconductor product (such as memory chips) market; and for different products, materials, and equipment, also determine their interdependencies and technological bottlenecks.
-
What is the market concentration in terms of companies and regions (limited sources and single sources, laying the groundwork for subsequent multi-technology source evaluations to compensate for single sources)?
-
Who are the key players in this market, and what is their business model?
-
What are the future market scale forecasts and expected growth rates?
-
What is the relationship between upstream and downstream participants?
-
What are the product market characteristics? For example, how much spot volume is there, how much is highly customized, how many customers are there, etc.
-
Are there economic barriers to entry, such as high capital investment, and are there labor bottlenecks?
-
Are there technological barriers to entry, such as technology-intensive investments and specific field knowledge bottlenecks?
-
Is there serious supplier lock-in or path dependence?
-
If a product is preliminarily determined, it is also necessary to assess bottlenecks in product certification, intellectual property, technology licensing, and what position potential investors will have in these factors (to avoid complete dependency).
-
What are the types and uses of the preliminarily determined products and technologies?
-
What are the technological trends, for example, are they in the experimental stage, are they close to the end of the product cycle, and can they serve new markets?
-
Outside the semiconductor ecosystem, such as in chemicals and rare earth minerals, is it relevant? How much dependence is there?
-
Does the product or technology have implications for national security, such as being usable for military purposes?
Policy Tools for Managing the Semiconductor Value Chain
In recent years, various unexpected events have put significant pressure on the global semiconductor supply chain. The COVID-19 pandemic, the Russia-Ukraine conflict, restrictive trade measures, and natural disasters have caused interruptions and shortages in the semiconductor industry chain, impacting production across countries. Consequently, governments and companies have fully recognized the complexity of the global semiconductor value chain and are committed to untangling the “deadlock,” thoroughly sorting out supply relationships, and focusing on the security of key product supplies through policy tools to address unsafe factors and hidden dangers.
In the proposed “EU Chips Act,” the European Commission introduced four policy tools: information gathering, joint procurement, export controls, and setting priority procurement orders and national reserves. However, due to the complexity of the manufacturing process and technological processes of semiconductor products, the effectiveness and feasibility of the aforementioned policy tools vary.
Available Policy Tools for Semiconductor Manufacturing
Wafer semiconductor manufacturing (front-end and back-end) can be roughly divided into two steps: wafer manufacturing (also known as front-end manufacturing) and assembly, packaging, and testing (also known as back-end manufacturing). In the event of a chip supply shortage, the government can increase investment in front-end and back-end factories through subsidies, prioritizing the fulfillment of chip demands in specific key sectors, but this only applies to some priority orders, such as in military and medical device production.
Priority orders refer to using this tool for front-end or back-end wafer factories during chip crises, but this production organization method may not necessarily ensure supply security due to the following reasons:
The semiconductor manufacturing cycle generally requires 4 to 6 months, involving over 1000 process steps. If chips are ordered in January, they typically will not be delivered to customers until after June of the same year.
The manufacturing technologies for different types of chips are entirely different. The process nodes for cutting-edge mobile chipsets manufactured for smartphones are completely different from those for silicon carbide power semiconductors for electric vehicle charging batteries. Furthermore, chip design is always based on and associated with the process nodes of specific wafer fabs. For example, an automotive microcontroller designed on Taiwan Semiconductor Manufacturing Company‘s 28nm node cannot simply be replaced with another product; if a replacement is necessary, substantial redesign of the entire chip is required, which consumes nearly 1/4 of the semiconductor production cycle time. Thus, if a chip’s order delivery cycle is six months, this replacement design will take at least one and a half months.
Generally, front-end wafer fabs need to accelerate the high utilization of equipment (>80%) to quickly amortize investment costs. Some companies can achieve equipment utilization rates of 95% to 100%. In the dense production scheduling of enterprises, if the factory has to reschedule to meet the production of priority orders due to product shortages, it will impose additional burdens or losses on other contracted projects, even leading to defaults with existing customers. Therefore, priority orders are only applicable to a very small range of orders led by the government, such as military and medical emergency needs. If the government arranges priority orders on a large scale, it will disrupt the original production order, causing broader losses and will not fundamentally resolve the shortage issue.
Currently, the global chip shortage is not only due to capacity constraints in front-end and back-end wafer fabs but is also affected by shortages of key chemicals and materials (such as substrates), which drag down the entire industry. If front-end or back-end wafer fabs cannot meet demand due to a lack of certain gases, chemicals, or materials, then even priority government orders will be of no use.
Additionally, semiconductor equipment and front-end manufacturing technology depend on over 50 different types of complex manufacturing equipment, while back-end manufacturing relies on more than 10 different types of equipment, along with numerous suppliers of various wafer manufacturing technologies, such as valves and pipelines for gas delivery, carriers, vacuum pumps, and cleanroom technologies for automated wafer processing. Currently, all equipment and wafer fab technology suppliers are striving to fulfill orders, as more new fabs will be built globally in the coming years. If there is again a mismatch between semiconductor front-end and back-end manufacturing and equipment process materials, leading to chip shortages, the proposed policy tools may impose restrictive measures on semiconductor equipment and wafer processes. Any restrictive measures will only have medium- to long-term impacts on the global semiconductor industry, as the construction cycle for new plants is 3 years, and the expansion cycle for existing plants is 1.5 years. This means that restrictive measures will only show results 1.5 to 3 years later, which is not helpful in alleviating temporary shortages. Using export controls to limit the export of wafer fab technology may help domestic (regional) capacity expansion, but it will also invite retaliation from other countries (regions) and make it impossible for its own large-scale capacity expansion products to be delivered for export, creating additional risks (compared to technology exports) and even harming the competitiveness of the domestic industry. Therefore, implementing export controls on wafer manufacturing is inadvisable.
Available Policy Tools for Chemicals and Materials
Wafer semiconductor manufacturing relies on over 400 different chemicals and materials and 15 different types of wafers, with extremely high purity and ultra-clean environment requirements. Only a few suppliers worldwide can provide specific “semiconductor-grade” gases or chemicals. The network of chemical suppliers relied upon by wafer fabs mainly comes from (but is not limited to) Japan, Europe, and the United States. The qualification of new suppliers for specific chemicals or gases often takes more than a year, as even minor changes in the manufacturing process can negatively impact yield, so wafer fabs are extremely cautious in selecting and qualifying material suppliers.
However, implementing export control measures in the chemicals and materials field may not achieve stable supply security in the medium to long term. Considering that chemicals and materials are consumables, short-term export controls may ensure domestic supply security, but control measures will provoke retaliation from allies, and in the long run, foreign companies will reduce their trust in enterprises from countries implementing controls, deeming suppliers unreliable.
If collaborative procurement and national reserves can be achieved in the chemicals and materials field with allies, it may be the most effective way to alleviate short-term supply shortages. Imagine if the bulk or inert gases required by each factory were elevated to the level of national reserves, but these reserves need not be entirely constructed and maintained by the government; some could be organized through public-private partnerships, which would solve some issues at different levels while also facing challenges: First, it must be determined which gases and chemicals need to be reserved long-term by the government; if shortages occur in the future, what would the severity of the shortages be? (How much needs to be reserved); if these gases and materials are used in wafer fab production in the future, can they obtain qualified supplier status? If implemented through national reserves or collaborative procurement, will it suppress wafer fabs from establishing their own inventories, and how can regional clusters form between national reserves and enterprises to better coordinate reserves and supplies?
In summary, regarding the four policy tools proposed in the “EU Chips Act,” the think tank report believes that no single policy tool is deemed universally effective in ensuring semiconductor supply security. The main reason for ineffectiveness is the characteristics of the semiconductor value chain: highly diverse and customized products, high specialization of each process step and supplier market, strong division of labor, multinational lock-in effects, and long manufacturing cycles. The global semiconductor value chain is not singular; many different value chains have significant overlaps, while the non-overlapping parts exhibit clear distinctions. Therefore, filling the shortages in the value chain is not a simple task. It cannot be achieved solely through one policy (such as export controls).
Governments Should Shift from Crisis Management to Long-Term Crisis Prevention
For governments, the best way to address shortages is to commit to incentivizing end customers to optimize and reorganize their supply chains to make them resilient. This will incur high costs for the end customer industries, as they will need to invest in expanding strategic inventories, establishing multiple sources, redesigning end products and chips, and fundamentally changing their supply chain models.
For the industry itself, after the chip crisis, many companies have begun to redesign chips with resilience and availability, but there are no short-term solutions, as redesigning chips may take over 9 months, qualifying new chemical suppliers may take at least 12 months, adding new process nodes to existing wafer fabs (cleanrooms) takes about 18 months, and constructing new wafer fabs (greenfield) requires over 3 years. The government cannot participate in the aforementioned investment activities; what it can do is enhance the resilience of the semiconductor value chain through legal and institutional design, incentivizing and guiding the industry onto the right path. The government must shift its regulatory focus from crisis management to long-term crisis prevention. To this end, the government should do the following:
(1)Increase Transparency. This can be achieved by combining the views of policies, industries, and end customers to create a platform to address transparency issues. Meanwhile, in collaboration with existing industry alliances, a standardized framework for increasing supply chain transparency and sharing best practices should be established.
(2)Improve Long-Term Supply Chain Management through Standards and Regulations in the Semiconductor Industry and End Customer Industries. The report suggests that part of the current chip shortage is due to poor procurement decisions and supply chain controls focused on just-in-time delivery. The core solution to this contradiction is to separate end customer industries from just-in-time supply chain models and purely cost-driven procurement decisions, which is not achievable in the short term. Therefore, the government should engage more closely with end customer industries to better understand their supply chain models and the potential risks to semiconductor supply security, and when necessary, consider regulatory measures for supply chain resilience to urge end customers to adjust their business and supply chain models to enhance their resilience from a medium- to long-term perspective.
(3)Establish Long-Term Connections with Industries to Better Understand the Development and Trends of the Global Value Chain. Many governments still know very little about the global semiconductor value chain, including key suppliers, technological trends, market dynamics, bottlenecks, and interdependencies. Meanwhile, as industrial and societal digitalization continues, semiconductors will play an important role. Geopolitical tensions caused by climate change and global warming, natural disasters, etc., will exacerbate the risks in the global semiconductor value chain and may lead to further disruptions. Therefore, governments should increase investment in their national resources to map the long-term semiconductor ecosystem, identify and evaluate their country’s interdependencies and bottlenecks in the global value chain, and develop meaningful long-term industrial, trade, and diplomatic policy measures.
(4)Strengthen International Partnerships. The high efficiency and innovation of the semiconductor value chain are rooted in a highly collaborative and complex multinational network. This means that no matter how much investment is increased to strengthen regional ecosystems, strong interdependencies will continue to exist. Therefore, only through international cooperation can long-term resilience of the semiconductor value chain be successfully addressed. Based on the mapped global semiconductor dependency chart, governments can grasp the strengths and weaknesses of regional ecosystems and accordingly increase investments to establish long-term strategic partnerships with trusted allies.
Conclusions of the Think Tank Report
In recent years, with the intensification of geopolitical tensions and the spread of the global COVID-19 pandemic, various disruptions on value chains have occurred, forcing many governments into crisis management mode. Many countries (regions) have taken different measures, such as introducing new legislation targeting different technologies. The common characteristic among countries is the adoption of protective and reactive actions, such as re-planning industrial chains and nationalizing to ensure the stability and security of key product supply chains. For the complex and diverse global semiconductor industry, the new role of government is a complicated task. Only by considering the uniqueness and dynamic trends of the technological ecosystem can government management be effective and successful. The think tank report believes that although the “EU Chips Act” mentions four policy tools, in practice, the government’s action space regarding semiconductor shortages may be very limited. The government cannot assess what specific product disruptions mean; it cannot adjust inventory levels, find alternatives, or shift production. Therefore, the government should focus on institutional construction for crisis prevention and long-term strategic formulation, distinguishing the responsibilities among the government, semiconductor industry, and end-user industries, addressing the resilience issues in the value chain from the end-user perspective.
The think tank report comprehensively describes the complex, intertwined manufacturing processes of the semiconductor chip value chain and offers recommendations on how the government should manage chip supply shortages, particularly addressing the issues and shortcomings in the “EU Chips Act.” From the perspective of global chip value chain development, the report’s viewpoints are relatively objective, and its policy suggestions are worth referencing:
(1) We should map the global semiconductor value chain, deconstruct and analyze the value chain relationship diagram, to identify and grasp the direction of the key nodes our country occupies. This is a fundamental and extremely important task that must be done when formulating long-term development strategies.
(2) In terms of preventing supply chain security risks, we should start from the demand of the end industry, identify the risk points of key technology nodes, and build a diversified procurement system to increase reserves of risk point products.
(3) Semiconductors are a foundational industry for the future. Currently, researchers in various countries are committed to improving semiconductor products’ computing power, storage density, speed, and reducing costs and power consumption. However, using semiconductor export controls to set obstacles for competitors will short-term suppress their development, but this approach cannot change the objective laws and industry characteristics of the open, cooperative development of the semiconductor industry. As the world’s factory and manufacturing center, China provides rich application scenarios and end-user demands for semiconductor R&D. The recent new export control policies from the United States regarding semiconductors will ultimately delay its own R&D cycle and impose huge compliance costs on global semiconductor R&D and manufacturing companies. If it leaves the Chinese market, even if new (requiring an investment of 15 billion) and integrates any product value chain system, the costs and consequences will exceed billions of dollars, especially considering the complexity of the global semiconductor value chain!
By: JG Intelligence Institute
Initial Review: Chang Yan
Editor: Lu Xin
Reviewer: Cui Hongman
JG Intelligence New Media Editorial Department
Phone: 010-88379889
WeChat: luxin0909
Trade Risk Early Warning Network: www.risk-info.com
Address: No. 22, Million Village Street, Xicheng District, Beijing
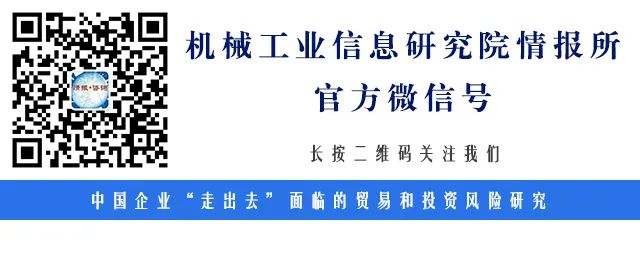