Think Tank Highlights #GlobalDefenseDynamics #USMilitaryDynamics #RussianMilitaryDynamics #TaiwanKeyEvents #MicroShopForSale
#SouthKorea #Raytheon #Japan #ElectronicWarfare #NortheastAsiaMilitaryDynamics #Unmanned
The following article is from Aerospace Defense Observer, author Development Center Dai Sheng, reprinted from Strategic Frontier Technology.
Abstract: Compared to traditional industrial robots, collaborative robots have four main characteristics: low cost, flexible deployment, strong safety, and ease of use. They can fully combine machine efficiency and human intelligence, better adapting to the personalized production needs of enterprises of different scales, and have become one of the main development trends in industrial robots. Currently, many research institutions, robot manufacturers, and innovative technology companies in the US, Europe, and Japan are jointly developing process equipment based on collaborative robots in cooperation with aerospace manufacturing giants such as Airbus, Boeing, and Lockheed Martin, striving to accelerate the formation of a new intelligent “generation gap” in aerospace manufacturing.
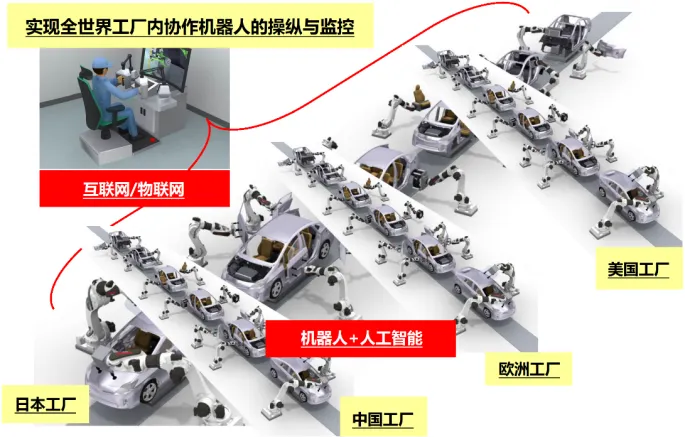
1. Introduction
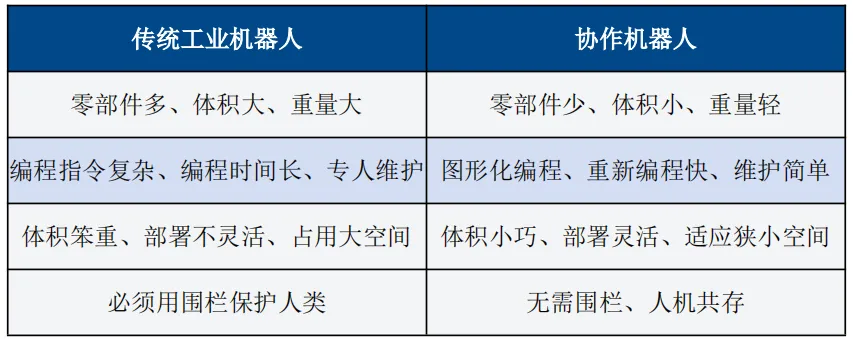
2. The US, Europe, and Japan Support the Development of Collaborative Robots with National Strategies for Widespread Application in Aerospace
(1) The US Accelerates Innovation with National Robotics Program, Focusing on Collaborative Robots for Smart Factory Layouts
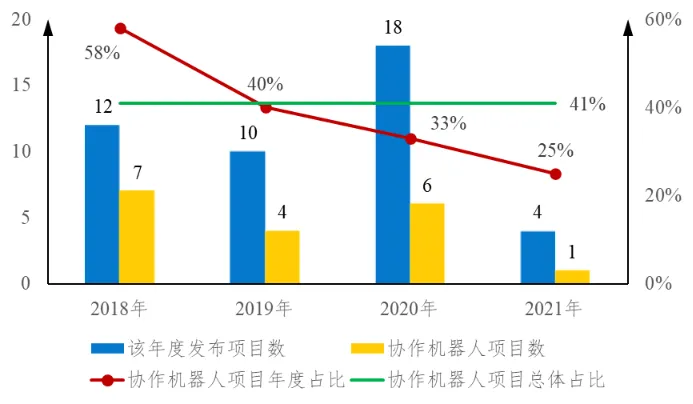
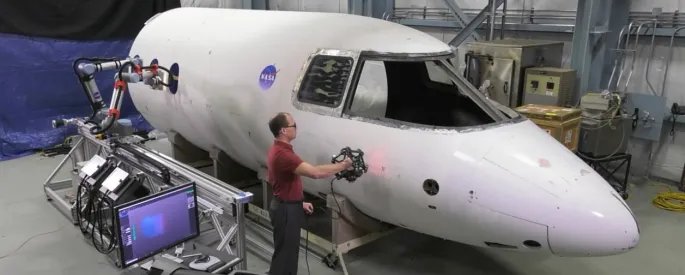
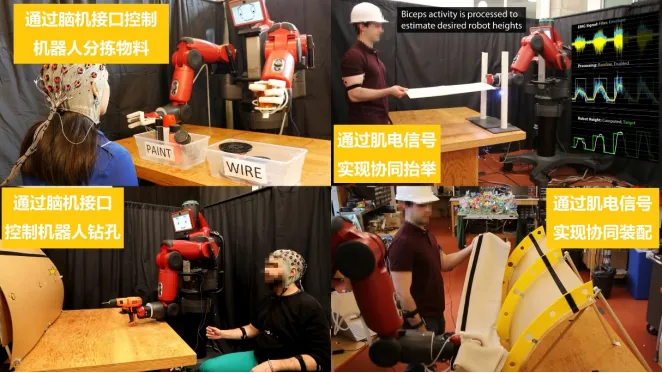
(2) The EU Continues to Invest in Core Technologies Through Framework Programs, Mainly Targeting Collaborative Robot Deployment in Aerospace Manufacturing
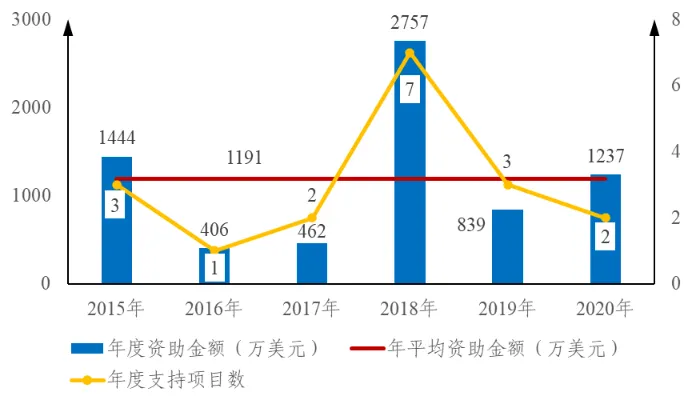
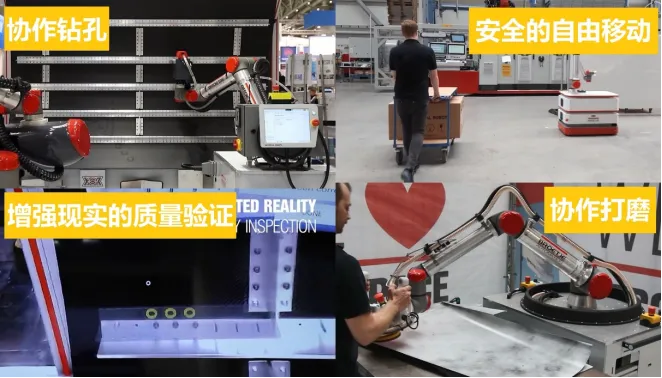
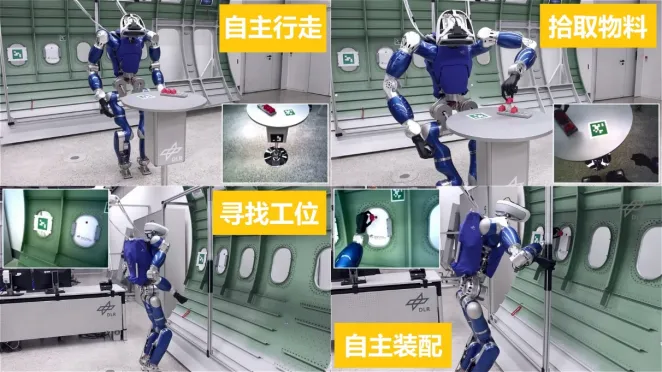
(3) Japan Vigorously Promotes Collaborative Robots Due to Aging Population and Low Birth Rate, Utilizing Collaborative Robots to Accumulate Workers’ Labor Experience
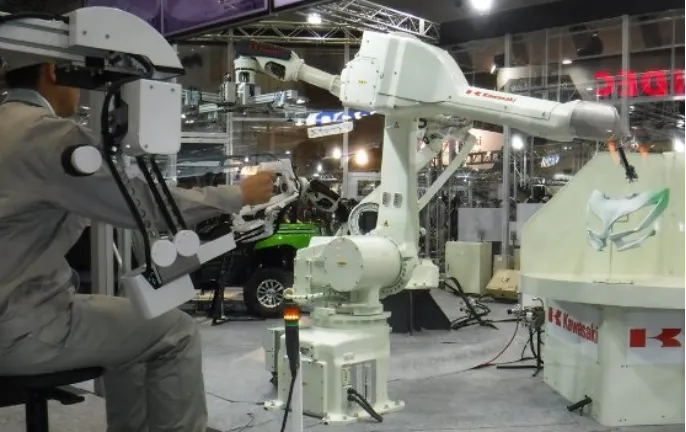
3. China’s Collaborative Robot Technology Has Low Autonomy, Difficulty in Application in Aerospace
4. Recommendations
(1) Accelerate Core Components and Emerging Frontier Technology Research
(2) Build a Complete Collaborative Robot Industry Ecosystem
(3) Focus on Promoting Typical Demonstration Applications in Aerospace
Reprint Statement
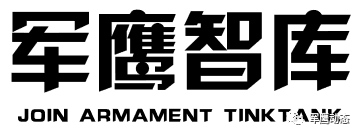