1968
Dick Morley invented the Programmable Logic Controller (PLC) and began deploying them in the automatic transmission manufacturing at General Motors, marking the era of precise control by controllers in various production stages of the manufacturing chain.
1975
Honeywell and Yokogawa Electric launched the world’s first Distributed Control Systems (DCS) TDC2000 and CENTUM, which allowed flexible process control across the entire production chain and even within the entire factory, without worrying about the impact of controller failures on production.
Today
With the introduction of Ethernet in 1980, people began to combine Ethernet with process control technology on the production chain; this combination had two main directions: one was control-oriented, which eventually evolved into the industrial Ethernet technology we know today, while the other was the exploration of smart device networks, which ultimately led to today’s Internet of Things (IoT).

The earliest IoT device dates back to 1982, when Carnegie Mellon University modified a vending machine that could report its remaining inventory and the temperature of the drinks via Ethernet, which is probably the first device to realize the concept of IoT. Since then, various devices we now refer to as early IoT devices emerged, until 2002, when cloud technology allowed devices to access historical data and trends through cloud storage; in 2006, the development of OPC UA led to the concept of IIoT, or Industrial Internet of Things, which defined secure, remote communication between devices that required no manual operation or intervention.
Ten years ago on the production line, we needed employees to manually record inventory and check out goods; relied on maintenance teams to visually inspect goods and quality; and made phone calls to check the logistics of goods—these inefficient methods plagued the entire supply chain. The various technologies under the concept of Industrial IoT exist to improve the efficiency of these links, specifically manifested in the following aspects:
1
The Cyber-Physical Systems (CPS)
The basic technology platform of Industrial IoT integrates physical processes and software communication processes, thereby providing further modeling, design, and analysis technologies;
2
Cloud Computing
With cloud computing, IT services and computing resources can be moved to the cloud rather than being limited to local servers;
3
Edge Computing
A distributed computing method, which, compared to cloud computing, allows data storage to be closer to the local needs, as distributed data processing significantly reduces the demand for device data processing capabilities and lowers the risk of errors and attacks.
4
Artificial Intelligence & Machine Learning
Artificial Intelligence (AI) is a field of computer science whose creations can make decisions like humans through effective predictions;
The concept of cyber-physical systems is quite vast, but it is also constantly reflected in our current production environment, such as bus protocols used for process control on production lines. The control devices and controlled devices within these systems can automatically complete corresponding tasks.
However, to the outside world, they remain information silos. This is completely contrary to the concept of Industry 4.0: the capacity of our production line is still reported by people manually recording data, trends are still calculated using simple predictive models in spreadsheets, and ultimately, the allocation of production line capacity is still a human decision…
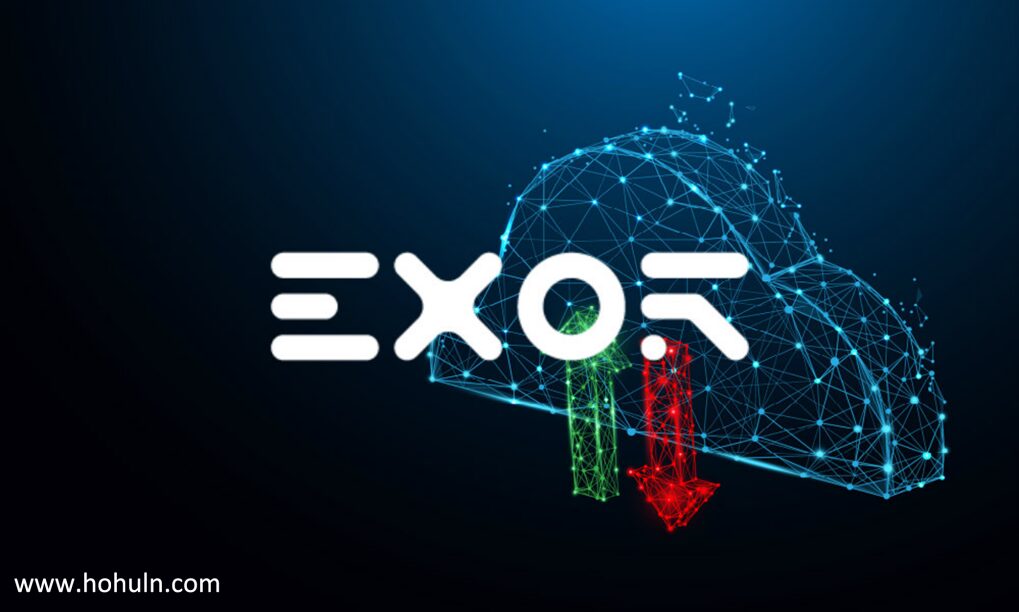
The solution is simple to state; the key point is to connect the upper and lower MES systems with the on-site devices, allowing cloud computing and its AI and machine learning capabilities to predict and make decisions about production line trends.
But how to achieve this? I could set up Ethernet in the production line and management system based on today’s beverage factory needs, define the message format, and perfect the network and transport layers to create a simple protocol; I could do the same based on tomorrow’s electronics factory needs; but please note, in such cases, we only achieve interoperability, not interconnectivity.
These systems, or even more such systems, do not use a unified framework or protocol. The cost of achieving “interoperability” is very high, and the cost of connectivity increases exponentially with the number of systems.
In this case, we need a unified framework and protocol that can be used across various fields and applications. Traditional industrial field bus protocols and industrial Ethernet protocols often have limitations on the number of devices and communication distances for real-time data, making them unsuitable for large networks of Industrial IoT. However, many architectures have emerged in the development of Industrial IoT, all possessing strong interconnectivity and universality, such as:
OPC and OPC UA are a series of standard frameworks launched by the OPC Foundation for linking computer systems to automation devices.
Node-RED, an open-source software designed by IBM, is used to connect APIs, hardware, and online services.
MQTT is a publish-subscribe architecture over TCP/IP that allows devices to communicate with MQTT brokers.
REST is a scalable architecture that allows communication via HTTP and easily transfers IoT information to integrated web servers.
These architectures and protocols provide uniformity, allowing interfaces to be maximally cross-industry: OPC technology (OPC UA) allows data from industrial protocols to be extracted and directly transmitted to upper-level computer networks; MQTT allows production process data to be fed back to industrial cloud platforms, facilitating cross-space data transmission; while REST provides a convenient standard for reading and analyzing data from cloud platforms.
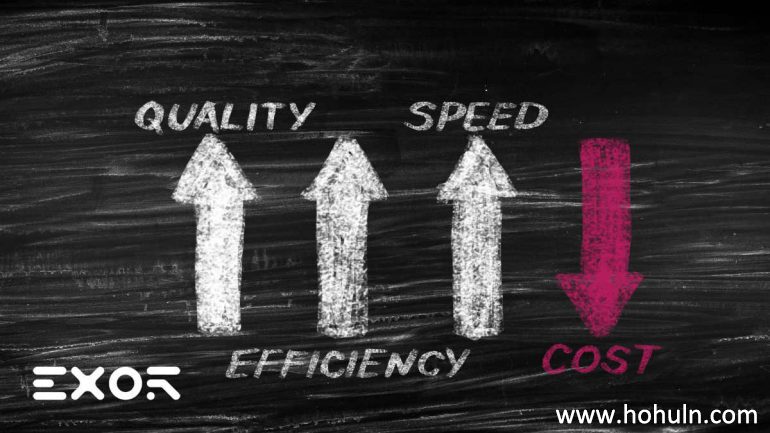
Industrial IoT is not the ultimate goal; it is merely a “small target.” As mentioned earlier, with the development of technology, especially internet technology, the concept of Industrial IoT has become possible to improve the efficiency of all production links.
The main applications of Industrial IoT can be categorized into several aspects, some of which have already become a reality:
For instance, remote services, where maintenance personnel can access devices in other locations with full permissions, significantly improving maintenance efficiency. Some studies indicate that this method can save maintenance costs by 12% to 30% compared to traditional maintenance methods, with a 70% higher chance of eliminating faults;
For example, data-driven services, where decisions regarding inventory optimization, quality control, production line optimization, and predictive maintenance are entirely made by AI algorithms based on data analysis through cloud computing (or fog computing or edge computing);
Additionally, leveraging big data analysis for digital twin simulations to calculate the lifecycle of equipment and parts and perform predictive maintenance, or provide large-scale simulation scenarios for new employees to conduct various practical training. These diverse applications can change existing production modes and enhance production efficiency.
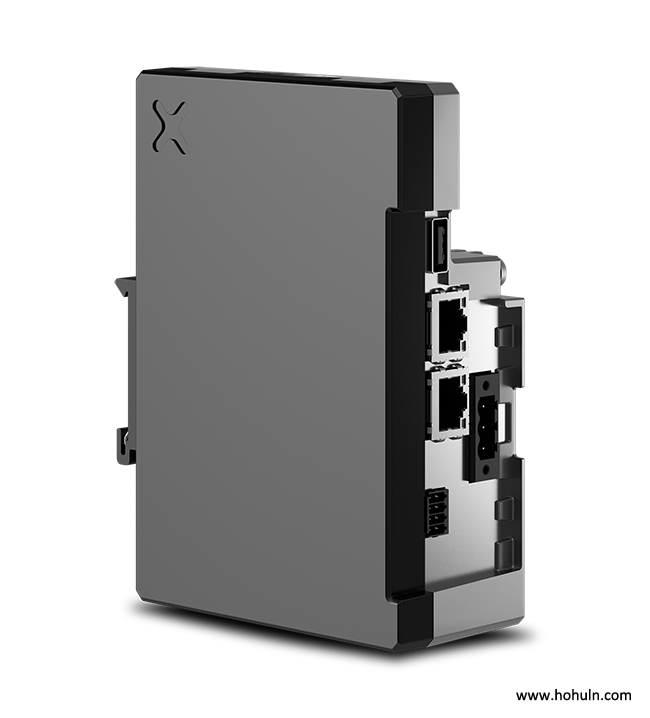
From the previous content, it is not difficult to see that implementing applications of Industrial IoT can reduce costs at various stages and improve production efficiency; the method to achieve this is quite simple, merely breaking down existing information silos on the production line and transmitting data. The simplest way in this process is to use a gateway or pair it with an appropriate industrial cloud platform, such as the products from Guangzhou Hongke Electronics, provided by EXOR from Italy—edge gateways and displays that can be used under various conditions, including extreme environments, and the Corvina Cloud platform, which converts existing communication protocols on the production line into the frameworks and protocols mentioned above; allowing data to realize its true potential can effectively improve production efficiency and reduce production costs.
If you happen to have such needs or are very interested in this, please feel free to contact us. We look forward to further communication and exchange.
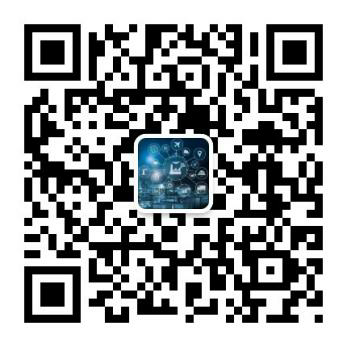
Guangzhou Hongke Electronics Technology Co., Ltd.
Hotline: 400 999 3848
Email: [email protected]
– END –