Today, we will explain the three methods for PLC control of servo motors:
1. Torque Control
2. Position Control
3. Speed Mode
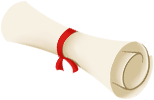
1. Torque Control
The torque control method sets the output torque of the motor shaft to the outside based on external analog input or direct address assignment. For example, if 10V corresponds to 5Nm, when the external analog input is set to 5V, the motor shaft outputs 2.5Nm: if the motor shaft load is less than 2.5Nm, the motor rotates forward; when the external load equals 2.5Nm, the motor does not rotate; and when it exceeds 2.5Nm, the motor rotates in reverse (usually occurs under gravitational load).
The set torque can be adjusted instantly by changing the analog input or by modifying the corresponding address value through communication.
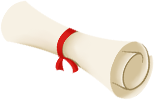
2. Position Control
The position control mode generally determines the rotation speed based on the frequency of externally input pulses and the number of pulses to determine the rotation angle. Some servos can also directly assign values to speed and displacement through communication.
Since position mode can strictly control both speed and position, it is generally used in positioning devices.
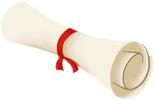
3. Speed Mode
Rotation speed can be controlled through analog input or pulse frequency. In the presence of an upper-level control device with external loop PID control, speed mode can also perform positioning, but the motor’s position signal or the direct load position signal must be fed back to the upper-level for calculations.
Using the SINAMICS V90 System as an Example
SINAMICS V90 is divided into two versions based on different applications:
1. Pulse Sequence Version (integrates pulse, analog, USS/MODBUS)
2. PROFINET Communication Version
The SINAMICS V90 pulse version can achieve internal positioning block functionality while having pulse position control, speed control, and torque control modes.
The following figure shows the default interface definition under the pulse string instruction speed control mode (PTI), which conforms to standard application habits.
At the same time, only one pulse input channel is allowed, and other control signals can be freely allocated to digital input and output terminals. Please refer to the operation manual.
Digital inputs support both NPN and PNP types. The wiring diagram for the 24V power supply is as follows:
(1) 24V power supply for SINAMICS V90. All PTO signals must be connected to controllers using the same 24V power supply, such as SINAMICS V90.
(2) Isolated digital input power can use the controller’s power.
(3) Isolated digital output power can use the controller’s power.
SINAMICS V90 Servo Drive
Motor brake signal (only for SINAMICS V90 200V drive). The SINAMICS V90 200V drive requires an external relay to connect the motor brake.
Wiring diagram for the SINAMICS V90 pulse sequence version system
Wiring diagram for the SINAMICS V90 PROFINET version
1. SIMOTICS S-1FL6 low inertia motors SH20, SH30, and SH40 use cable-type connectors.
2. The brake cable connection shown here is only applicable to V90 400V drive. The V90 200V drive requires an external relay to connect the motor brake cable.
3. The SINAMICS V90 PTI drive must connect the relay through the set value cable, while the SINAMICS V90 PROFINET drive connects the relay through the I/O cable.
4. The I/O cable must be used to implement the brake control for the SINAMICS V90 PROFINET 200V drive and to achieve additional DI/DO applications beyond PROFINET communication.
Are you “watching” me?
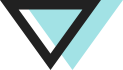