
With the rapid development of industrial technology, distributed control systems and fieldbus control systems have emerged one after another. In some industries, some people believe that FCS is developed from PLC, while others believe that FCS is developed from DCS. There is a close connection between FCS, PLC, and DCS, yet there are essential differences.

DCS (Distributed Control System), also known as distributed control system, is a computer control system that is developed and evolved based on centralized control systems.
FCS (FieldBus Control System) is a control system that interconnects various controllers and instruments in the field using an open, interoperable network called fieldbus, while completely decentralizing control functions to the field, thus reducing installation costs and maintenance expenses.
PLC (Programmable Logic Controller).
Detailed Comparison of FCS and DCS
FCS is developed from DCS and PLC, possessing the characteristics of both DCS and PLC, while also making a revolutionary step forward. Currently, new types of DCS and PLC are trending towards each other. New types of DCS already have strong sequential control capabilities; new types of PLC are also competent in processing closed-loop control, and both can form large networks, resulting in significant overlap in the application scope of DCS and PLC.
The key to DCS systems is communication. It can also be said that the data bus is the backbone of the distributed control system DCS. Since its task is to provide a communication network among all components of the system, the design of the data bus itself determines the overall flexibility and safety. The media for the data bus can be: twisted pair, coaxial cable, or fiber optic cable. By examining the design parameters of the data bus, one can basically understand the relative advantages and disadvantages of a specific DCS system.
To ensure the completeness of communication, most DCS manufacturers can provide redundant data buses. To ensure the safety of the system, complex communication protocols and error detection technologies are employed. The so-called communication protocol is a set of rules that ensures the transmitted data is received and understood exactly as sent. Currently, two types of communication methods are generally used in DCS systems, namely synchronous and asynchronous. Synchronous communication relies on a clock signal to regulate data transmission and reception, while asynchronous networks use a report system without a clock.
Figure: Traditional Method: One-to-one I/O wiring between field devices and controllers
Figure: Fieldbus Technology: Using a single cable to connect all field devices
Performance |
FCS |
DCS |
Structure |
One-to-many: one transmission line connects multiple instruments, bidirectionally transmitting multiple signals. |
One-to-one: one transmission line connects one instrument, unidirectionally transmitting one signal. |
Reliability |
Good reliability: digital signal transmission has strong anti-interference capability and high precision. |
Poor reliability: analog signal transmission not only has low precision but is also easily interfered with. |
Loss of Control State |
The operator in the control room can understand the working status of field devices through field instruments, adjust parameters, and predict or locate faults, keeping the equipment under the operator’s process monitoring and control. |
The operator in the control room neither understands the working status of the analog instruments nor can adjust parameters, nor predict faults, leading to a “loss of control” state for the instruments. |
Control |
Control functions are decentralized among various intelligent instruments. |
All control functions are centralized in the control station. |
Interchangeability |
Users can freely choose the most cost-effective field devices and instruments provided by different manufacturers and interconnect instruments of different brands, achieving “plug and play”. |
Although analog instruments standardized signal (4~20mA DC), most technical parameters are still determined by the manufacturer, leading to poor interchangeability between different brands of instruments. |
Instruments |
Intelligent instruments not only possess the functions of detection, transformation, and compensation of analog instruments but also have digital communication capabilities and control and computation abilities. |
Analog instruments only possess detection, transformation, and compensation functions. |
Communication Method |
Uses dual digital, bidirectional transmission communication method. From the lowest level of sensors, transmitters, and actuators, the fieldbus network is adopted, and communication networks are interconnected layer by layer up to the highest level. Multiple branch communication lines extend to the production site to connect field digital instruments, using one-to-N connections. |
Adopts a hierarchical architecture, where the communication network is distributed across layers and uses digital communication methods, with only the conventional analog instruments at the production site still using one-to-one analog signal (e.g., 4~20mA DC) transmission, forming a “semi-digital signal” system. |
Decentralized Control |
Eliminates the DCS input/output unit, replaced by field instruments, thus breaking down the functions of the DCS control station and distributing functional blocks to the digital instruments on the fieldbus, achieving complete decentralized control. |
The analog instruments at the production site are concentrated at the input/output unit, while all functions related to input, output, control, and computation are centralized in the DCS control station. DCS is merely a “semi-decentralized” system. |
Interoperability |
As long as the field devices adopt the same bus standard, products from different manufacturers can be interconnected and interchangeable, and can be uniformly configured, completely changing the closed and proprietary nature of traditional DCS control layers, thus having good integrability. |
Field-level devices are developed independently by each manufacturer, and due to proprietary and incompatible communication protocols, products from different manufacturers are difficult to interconnect and interoperate. |
PLC and DCS
PLC:
-
Developed from switch control to sequential control, transport processing, and continuous PID control from the bottom up, with PID at the interrupt station.
-
A PC can serve as the master station, with multiple identical PLCs as slave stations.
-
A PLC can also serve as the master station, with multiple identical PLCs as slave stations, forming a PLC network. This is more convenient than using a PC as the master station because when user programming is involved, there is no need to know the communication protocol, just follow the manual format.
-
The PLC grid can serve as an independent DCS or as a subsystem of DCS.
-
PLC is mainly used for sequential control in industrial processes, while new PLCs also have closed-loop control functions.
DCS:
-
The distributed control system DCS integrates 4C (Communication, Computer, Control, CRT) technologies into a monitoring technology.
-
A large system with a tree topology from top to bottom, where communication (Communication) is key.
-
PID at the interrupt station connects computers with field instruments and control devices in a tree topology and parallel continuous link structure, with many cables running from relay stations to field instruments.
-
Analog signals, A/D—D/A, mixed with microprocessors.
-
One instrument connects to I/O via a pair of wires, linked to the local area network (LAN) by the control station.
-
DCS is a three-level structure for control (engineer station), operation (operator station), and field instruments (field measurement and control station), used for large-scale continuous process control, such as in petrochemicals.
Industry Experts Discuss the Differences Between PLC and DCS
PLC and DCS cannot be compared; PLC is a controller and an isolated product, while DCS is a system. However, PLC can be compared with the control station of DCS; the cycle period of PLC is around 10 milliseconds, while that of DCS control station is around 500 milliseconds. PLC has better openness and stronger independent working ability as a product.
—— OMRON Company
DCS is a system that includes upper software, networks, and controllers, while PLC is merely a controller. To form a system, it also requires an upper SCADA system and the connected network.
For PID loop control, Mitsubishi’s process controllers can also achieve FBD programming like SAMA configuration; DCS systems are larger, with more control loops and more controls and algorithms, capable of completing more complex inter-loop controls. The hardware reliability is similar. DCS can achieve I/O redundancy, while PLC cannot. Relatively speaking, systems formed by PLC are lower in cost.
—— Mitsubishi Electric Automation Precision Control Department Manager
DCS is a “distributed control system” that includes field controllers, operator station computers, engineer station computers, and the network system connecting them; DCS software is an integrated solution that addresses all technical issues of the system, with tight integration between system components.
PLC is a device that is equivalent to the field controller in DCS; on the software side, it is a localized solution with loose organization between stations.
—— Technical Manager of B&R responsible for APROL product application development
Analyzing the differences between DCS and PLC, the two key points are: first, DCS is distributed control with a global database; second, PLC uses a sequential scanning mechanism, while DCS is time-based control. Our system meets the first point; for example, a modification of an I/O tag can be synchronized in HMI.
—— Rockwell Automation Process Market Product Manager
Understanding PLC and DCS Through Comics
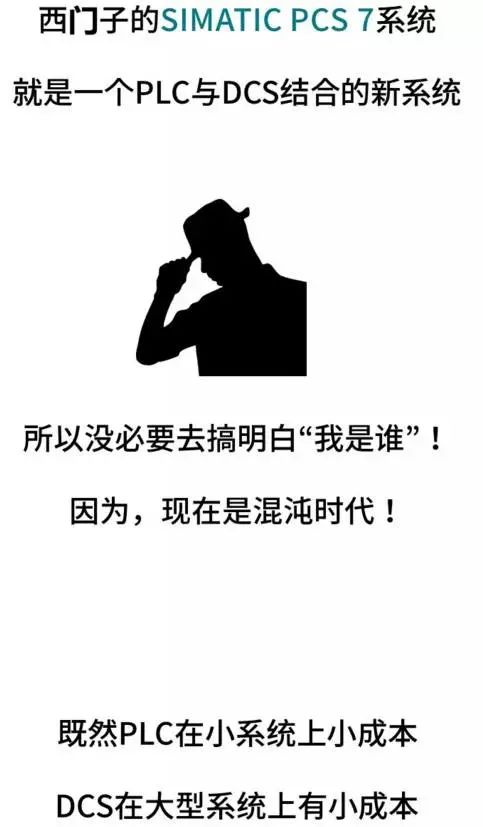
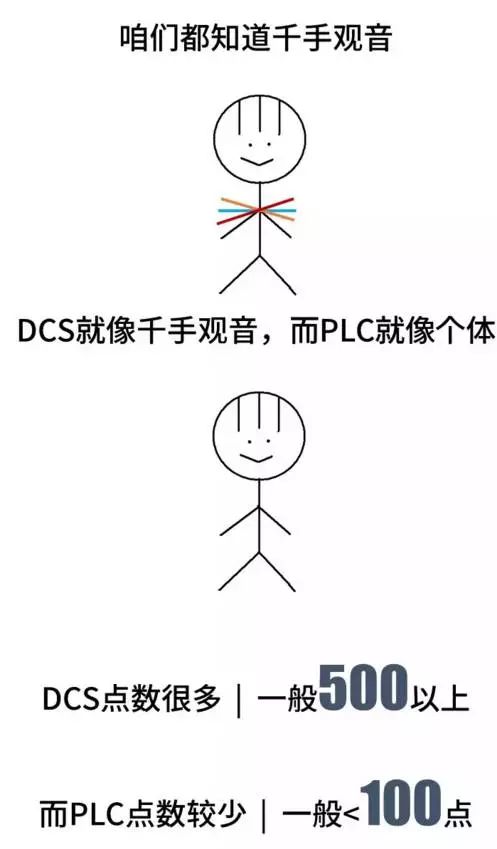
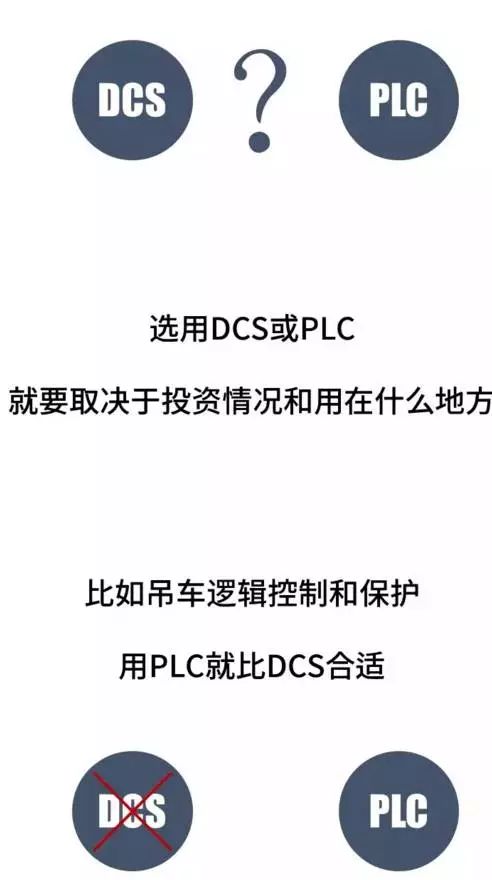
Feel free to share, like, and comment…
Share your feelings…
Pump Butler
Pump ● IT
·↓ Long press the QR codeto recognize and follow↓·