1. Module Implementation Methods
1.1Chassis
The chassis is the foundation supporting various components of the mobile robot, consisting of a frame and corresponding mechanical devices. The design is handled by mechanics, considering component layout, load capacity, vibration reduction, and other factors under the condition of other module selections.
1.2Drive Device
The AGV cart senses external environmental information and its own status through internal and external sensors, completing corresponding actions. The AGV cart transmits the signal to the onboard controller based on the position information obtained from the guiding sensors, calculating the actual control command value for the cart according to the target values provided by the cart’s path. After processing the signals (i.e., setting the cart’s speed and steering angle), the controller sends commands to the servo motor of the steering wheel drive unit to make adjustments, thus controlling the steering wheel to allow the AGV cart to travel along the navigation route on the road surface. Therefore, the coordinated control of the steering wheel is particularly important. By keeping the steering wheels synchronized, it can control the series of actions of the AGV cart on the ground, such as moving forward, backward, rotating, and turning.
According to mobility characteristics, mobile robots can be divided into two types: non-omnidirectional mobile robots and omnidirectional mobile robots. Movement of objects on a plane can produce three degrees of freedom: forward/backward, left/right, and rotation. If the degrees of freedom are less than three, it is a non-omnidirectional mobile robot; if it has all three degrees of freedom, it is called an omnidirectional mobile robot.
1、Common Wheels and Functions of AGV:
Drive Wheel: The wheel is equipped with a traction motor, which only drives the wheel forward or backward, but can be used in groups to form a dual-wheel differential drive system;
Steering Wheel: Equipped with a steering motor, it can only rotate around its center without forward momentum, unable to drive the chassis forward;
Omni Wheel: Also known as a swivel caster, it can rotate omnidirectionally and is generally fixed under the chassis, providing auxiliary support;
Directional Wheel: That is, a fixed wheel, with only one degree of freedom, installed under the chassis to guide the movement of the chassis, ensuring stability during the chassis’s movement;
2、Drive Classification:
The driving methods mainly include single steering wheel drive, differential drive, double steering wheel drive, and multi-steering wheel drive. Multi-steering wheel drive is generally used for heavy-duty AGV with a load of more than 10T.
Single steering wheel drive is used for three-wheeled models, differential drive is used for three or four-wheeled models, double steering wheel drive is used for four-wheeled models, and multi-drive is used for multi-wheeled models: multi-steering wheel drive refers to more than four steering wheels, generally used for heavy-duty AGV with a load of more than 10T, with a relatively complex motion model. The driving part has basically been realized domestically.
1)By driving method:
Single wheel drive, double wheel drive, multi-wheel drive;
2)By driving structure:
Differential structure, steering wheel structure, Mecanum wheel structure, track structure, axle structure;
3)By wheel system:
-
Single group differential
-
Double group differential
-
Multi-group differential
-
Differential
-
Single steering wheel
-
Double steering wheel
-
Multi-steering wheel
-
Mecanum wheel
1.2.1Dual Wheel Differential Chassis
Motion Characteristics: Forward, backward, left/right turning, and rotation in place;
1.2.1.1Six-Wheel Drive Wheel with Shock Absorption Chassis
Structural Style:4 auxiliary wheels +2 shock-absorbing drive wheels
Characteristics:Suitable for carrying materials, suitable for the traction point on the AGV drive center with two directional wheels and two omni wheels; low requirements on the radial force of the output shaft of the reduction motor, occupies little space; AGV self-weight increases with the load; prone to driving wheel slippage and floating mechanism jamming issues.

1.2.1.2Six-Wheel Three-Point Support Chassis
Structural Style:4 auxiliary wheels +2 drive wheels, one end connects two omni wheels and drive wheels through a seesaw structure, while the other end connects two omni wheels through a seesaw structure, forming a three-point support structure;
Characteristics:Suitable for carrying materials, suitable for the traction point on the AGV drive center with two directional wheels and two omni wheels; as the load increases, the pressure on the drive wheels also increases, ensuring sufficient adhesion for the drive wheels; higher requirements on the radial bearing capacity of the drive reducer, relatively complex structure, occupies more space.

1.2.1.3Four-Wheel Segmented Chassis
Structural Style:Segmented structure, the front end consists of two drive wheels and one omni wheel, the rear end is hinged with the front end, and the rear end has one omni wheel;
Characteristics:Suitable for carrying materials, suitable for the traction point on the AGV drive center with two directional wheels and two omni wheels; as the load increases, the pressure on the drive wheels also increases, ensuring sufficient adhesion for the drive wheels, occupies little space; higher requirements on the drive wheels and the radial force of the output shaft of the reducer;
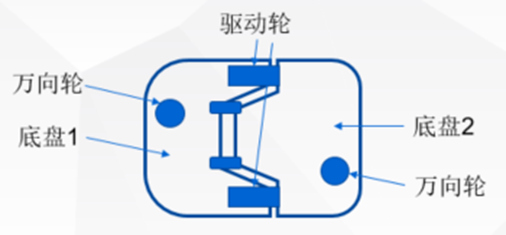
1.2.1.4Four-Wheel Three-Point Support Chassis
Structural Style:Two drive wheels plus two omni wheels connected by a seesaw structure;
Characteristics:Suitable for carrying materials, suitable for the traction point on the AGV drive center with two directional wheels and two omni wheels; as the load increases, the pressure on the drive wheels also increases, ensuring sufficient adhesion for the drive wheels, occupies little space; higher requirements on the drive wheels and the radial force of the output shaft of the reducer;
Applicable Situations
lDual wheel differential chassis is only suitable for AGV with length and width close to each other;
lNot suitable for pulling fully omnidirectional wheel material carts;
lSuitable for pulling two directional wheels and two omni wheels material carts, and the traction point must be placed at the center point of the drive wheel;
The aspect ratio of the AGV being large may cause the following problems:
-
AGV may move in an S-shape during high-speed linear movement.
-
AGV may derail during high-speed straight movement.
-
AGV may derail while turning.
1.2.2Differential Steering Drive Chassis
1.2.2.1Unidirectional Differential Steering Drive Chassis
Structural Style:Two omni wheels +Two directional wheels +A group of differential steering drive, two directional wheels +A group of differential steering drive;
Characteristics:Suitable for pulling and carrying materials, can achieve forward, left/right turning and short-distance linear reversing; can pull two directional wheels and two omni wheels and fully omnidirectional wheel material carts;
1.2.2.2Bidirectional Differential Steering Drive Chassis
Structural Style:Four omni wheels +Two groups of differential steering drive;
Characteristics:Suitable for pulling and carrying materials, can achieve forward, backward, lateral movement, and left/right turning; mainly used for pulling fully omnidirectional wheel material carts;
1.2.2.3Omnidirectional Differential Steering Drive Chassis
Structural Style:Four or more differential steering drives (mostly in pairs)
Characteristics:Suitable for pulling and carrying materials, can achieve forward, backward, lateral movement, left/right turning; mainly used for carrying materials over 10 tons;
1.2.2.4Comparison
Unidirectional Differential Steering Drive Rear TractionAGV vs. Dual Wheel Differential Rear TractionAGV
-
Cost: Mechanical+Electrical costs are comparable;
-
Traction Effect: With the same load, both are the same when moving straight, but the differential steering drive requires greater driving force when turning (the differential steering drive has an angle with the AGV body when turning, while the dual wheel differential structure has an angle of0); dual wheel differential is better;
-
Walking Method: Differential steering drive can only reverse for a short distance in a straight line, while dual wheel differential can walk in both directions; dual wheel differential is better;
-
Force Effect1: When pulling fully loaded materials, the traction pin experiences tensile force, the pressure on the directional wheels of the differential steering drive increases, and the pressure on the drive wheels of the dual wheel differential increases, allowing the latter to increase traction; dual wheel differential is better;
-
Force Effect2: When fully loaded, differential steering requires sufficient pressure on the directional wheels and drive wheels; insufficient pressure on the directional wheels may cause lateral movement when turning, and insufficient pressure on the drive wheels may cause slipping, while dual wheel differential prevents lateral movement and ensures driving force is on the drive wheels, only requiring sufficient pressure on the drive wheels; dual wheel differential is better.
1.2.3Steering Wheel Drive Chassis
The steering wheel can achieve three degrees of freedom of motion in the plane, with each wheel containing two motors, one for traction to drive the wheel forward or backward; the other is a steering motor to rotate the wheel around its longitudinal axis for steering the chassis.
The steering wheel type AGV wheel structure mainly adopts horizontal and vertical steering wheels. As shown in the figure, both structures are equipped with high-power steering wheels for movement and a gear disk on top. In terms of control methods, both use high-power servos to drive the direction of the steering wheels and speed of movement, along with a low-power steering motor for angle control of the steering wheels. The servo power supply has two types: DC and AC. Compared to DC power supply, AC power supply has more interference and is more complex in control; horizontal steering wheels can be smaller than vertical steering wheels but are more expensive.
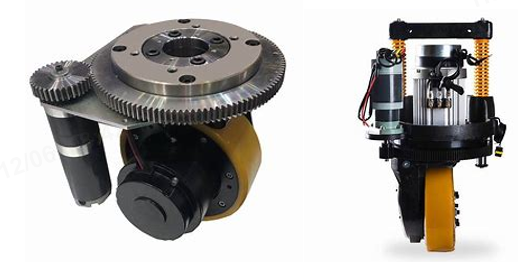
Figure: Horizontal Steering Wheel and Vertical Steering Wheel
The steering wheel integrates the drive motor, steering motor, reducer, and other integrated mechanical structures, combining product, movement, traction, and steering functions, capable of carrying and pulling heavier goods. It can be rapidly deployed for AGV, mobile robots, etc. Perfectly meets the application needs of AGV. Therefore, steering wheel drive is the development direction of AGV applications. Compared to traditional AGV cart differential control methods, steering wheels have higher integration, stronger adaptability, and higher accuracy and faster response when used with servo systems.
Steering wheel drive is a mechanism where the steering wheel serves as the driving unit;
Advantages: Simpler mechanical structure, greater load capacity, better passability;
Disadvantages: Higher installation height requirements, lower static friction coefficient, higher cost;
1.2.3.1Unidirectional Steering Wheel Drive Chassis
Structural Style: One steering wheel + Two directional wheels;
Characteristics: The steering wheel drive is a hard connection with the chassis; this type of AGV needs to avoid having the center of gravity too close to the steering wheel, making the AGV unstable during operation. Suitable for pulling and carrying materials, can achieve forward, left/right turning, and short-distance linear reversing.
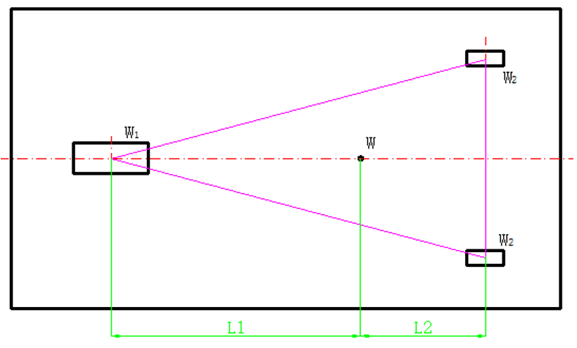
1.2.3.2Bidirectional Steering Wheel Drive Chassis
Structural Style1: Two steering wheels with floating mechanisms + Four omni wheels;
Structural Style2: Two omni wheels and two drive wheels, one omni wheel connected to one drive wheel through a seesaw structure;
Characteristics: Suitable for pulling and carrying materials, can achieve forward, backward, left/right turning, rotation in place, and lateral movement;
Advantages: By adjusting the angles and speeds of the two steering wheels, the cart can change lanes and steer without turning the front of the cart, and can even achieve turning movements around any point as a radius, with strong flexibility.
Disadvantages: Two sets of steering wheels increase costs, and the AGV often requires coordinated control of both steering wheels during maneuvers, which increases the requirements for motor and control precision, further raising development difficulty and costs.
1.2.3.3Omnidirectional Multi-Steering Wheel Drive Chassis
Structural Style: Four omni wheels, three or more steering wheels with floating mechanisms; or directly composed of three or more steering wheels; each wheel serves as both a drive wheel and a steering wheel, with each wheel having two motors for separate control, one motor controls the cart’s movement, and the other motor controls the cart’s steering;
Characteristics: High load capacity, can achieve forward, backward, left/right turning, rotation in place, and lateral movement;
Advantages: Flexible steering, able to move freely in tight spaces without complicated algorithms. The movement of the cart can be achieved through the coordination of the speed and rotation direction of each wheel.
Disadvantages: The overall structure is relatively complex.
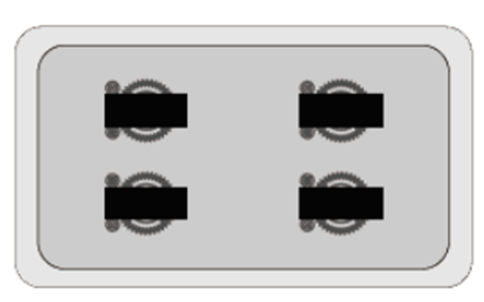
1.2.4Drive Bridge Chassis
Structure: Steering power and driving power are separated, using an electric drive bridge for driving power, adding steering force on auxiliary wheels for the AGV drive chassis; the front steering mechanism + rear drive bridge structure;
Application: Currently, this structure is mainly used in civilian products for outdoor operations, such as electric tricycles, electric sweeping vehicles, electric sightseeing cars, electric handling vehicles, electric traction vehicles, cleaning vehicles, electric wheelchairs, electric trailers, etc. These vehicles, combined with steering power, control modules, and detection modules, form the AGV product. Drive bridge AGV is widely used in heavy-duty ports, while other outdoor scenarios are still in the initial stages, with major domestic players being Zhenhua Heavy Industry and Siasun.
1.2.5Four-Wheel Differential Steering Chassis
Structural Style:Four drive wheels;
Characteristics:Can move forward, backward, left/right turning, and rotation in place, suitable for light loads and low-frequency operations. Due to sliding friction between the drive wheels and the ground during steering, wear on the drive wheels will be significant, leading to a relatively short lifespan.
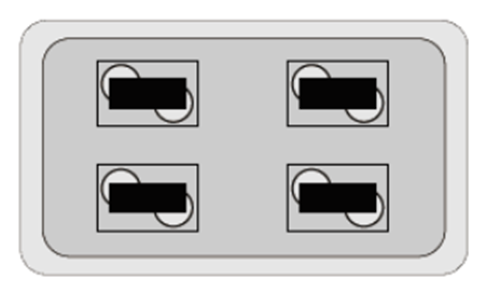
1.2.6Mecanum Wheel Chassis
Structural Style:Four or more Mecanum wheels;
Characteristics:Can move forward, backward, left/right turning, rotation in place, lateral movement, and diagonal movement.
Advantages:Flexible movement, high fine-tuning ability, small footprint;
Disadvantages:High internal resistance, low efficiency, high cost, high requirements for ground flatness;
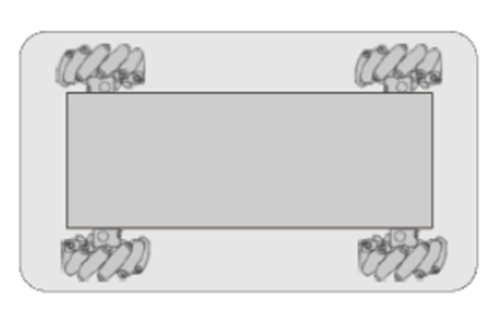
1.2.7Comparison of Different Drive Wheels
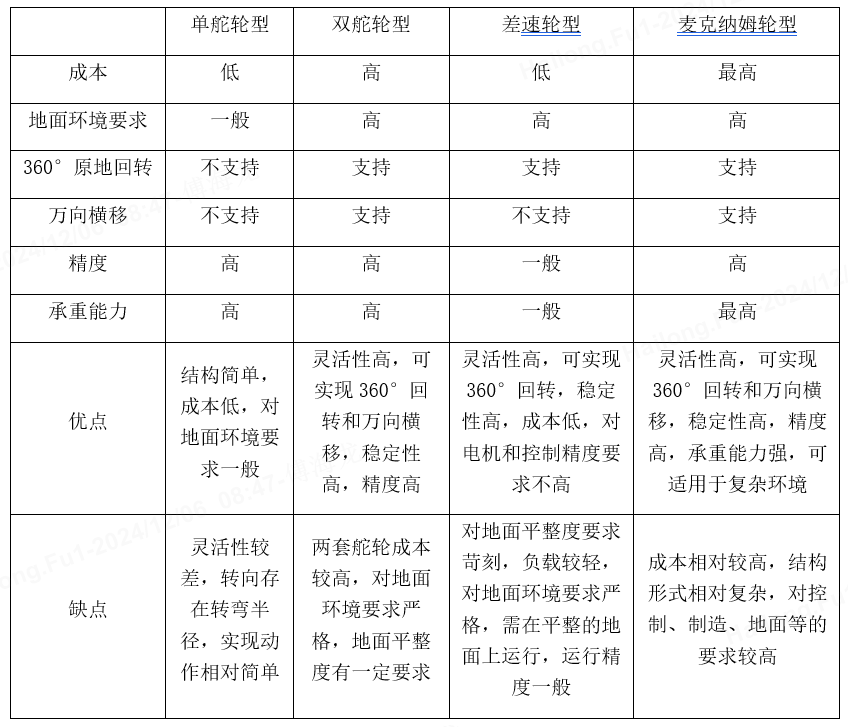
1.3Navigation Devices
Based on the operating environment of the system and the requirements of the actuator’s movements, determine the specific navigation method, considering factors such as navigation accuracy, anti-interference ability, flexibility, and maintainability.
Common navigation methods and their principles and characteristics are as follows: based on the process flow and path design results, calculate the quantity of navigation medium (metal wire, magnetic tape, laser reflectors, reflective materials, etc.) and determine their arrangement methods.
1.3.1Electromagnetic Navigation
Metal wires are buried underground and electromagnetic signals are loaded. The mobile robot achieves navigation by recognizing the frequency of the electromagnetic signals.
1.3.2Magnetic Tape Navigation
Magnetic tape navigation technology is similar to electromagnetic navigation, using magnetic tape laid on the ground instead of buried metal wires to achieve navigation through magnetic induction signals.
1.3.3Inertial Navigation
Uses inertial elements (accelerometers) to measure the robot’s own acceleration, integrating to obtain speed and position, thus achieving navigation and positioning of the robot. The devices that make up the inertial navigation system are all installed within the robot, and during operation, they do not rely on external information, making them highly resistant to interference, representing a type of autonomous navigation system;
1.3.4Laser Reflector Navigation
Install accurately positioned laser reflectors around the path of the mobile robot. The mobile robot emits and receives reflected laser beams to determine its current position and heading, thus achieving navigation.
1.3.5Laser Natural Navigation
Relies on laser radar as a sensing device, emitting and receiving reflected laser beams to obtain the surrounding environment’s contour, calculating to determine its current position and heading, thus achieving laser radar-based positioning, obstacle avoidance, navigation, and other capabilities.
Although compared to traditional AGV, laser AGV initially possesses sensing and autonomous planning capabilities, its sensing capability is weak, such as being unable to distinguish between types of obstacles and unable to provide flexible obstacle avoidance strategies based on different obstacles. Its contour matching-based positioning method also cannot effectively address the impacts of highly dynamic scene changes.
1.3.6Optical Navigation
Set color bands or light-sensitive bands along the path of the mobile robot, achieving navigation through optical recognition.
1.3.7QR Code Navigation
Set QR code signs containing position and heading information along the path. The mobile robot reads the information to obtain its position and heading, thus achieving navigation.
1.3.8Visual Navigation
Mainly relies on computer vision as its sensing means, capable of obtaining visual semantic understanding of the environment, enabling flexible obstacle avoidance, accurate positioning, and efficient path planning in complex dynamic environments.
1.3.9Comparative Analysis
Table: Comparison of Advantages and Disadvantages of Common Navigation Methods
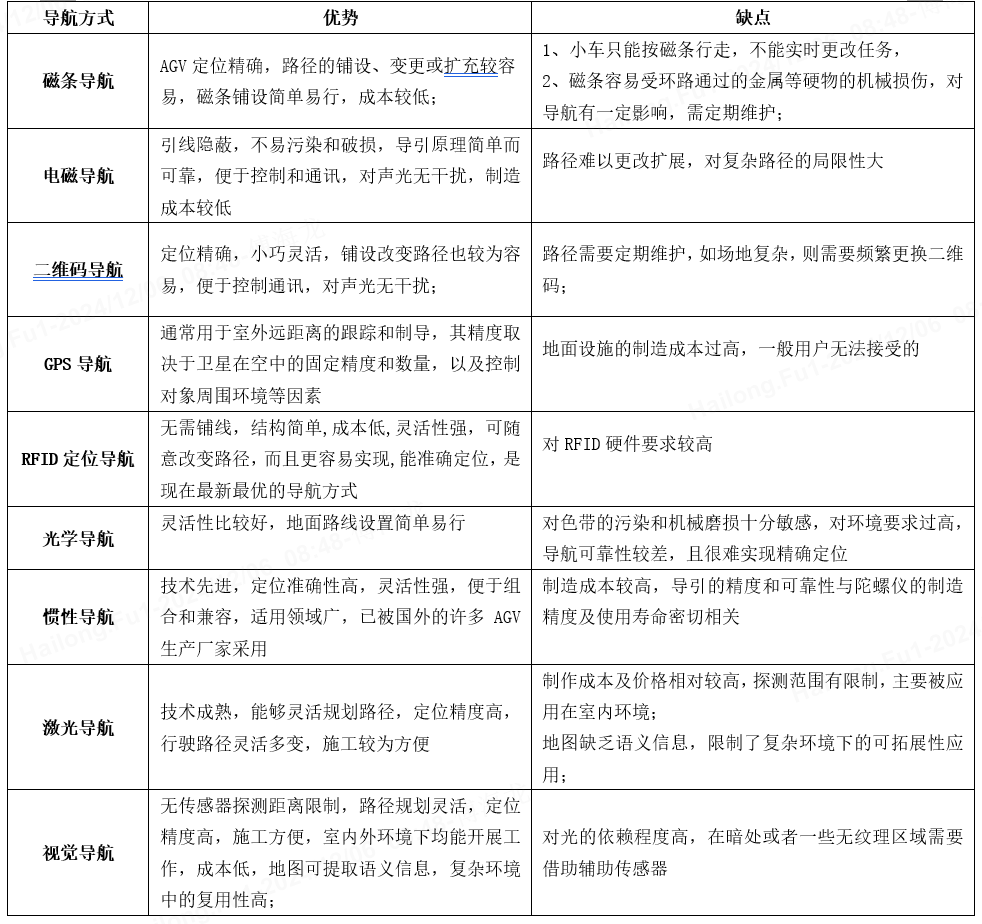
Table: Comparison of Laser AGV and Visual AGV Capabilities
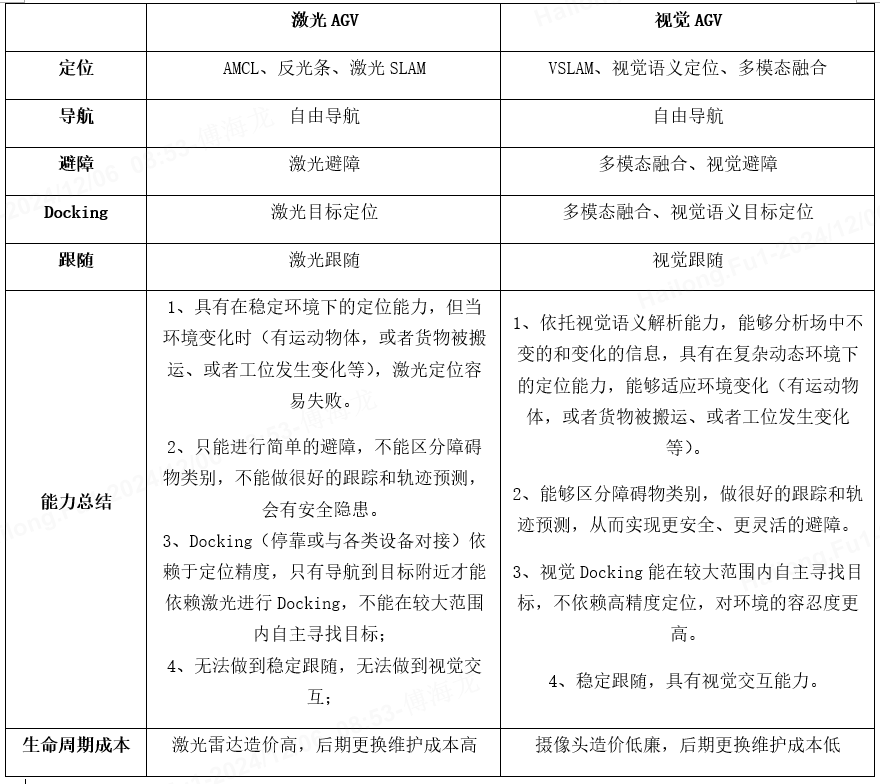
Table: Comparison of Advantages and Disadvantages of Laser SLAM and Visual SLAM
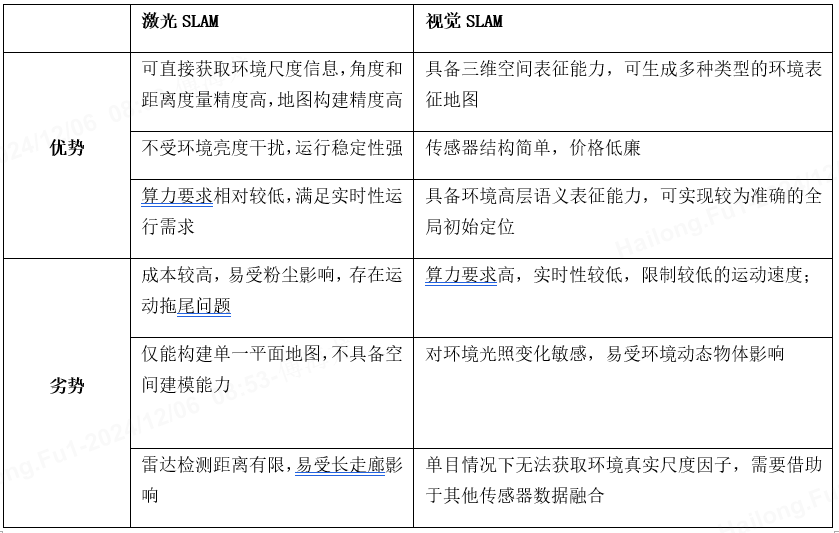
1.4Control System
The AGV controller serves as the “brain” of the AGV, being the core of the entire AGV, mainly controlling the behavior of various hardware of the cart. It is essentially a computer. It undertakes the realization of the main functions of the AGV, serving as the main controller of the AGV system, with motion control and navigation positioning being the two main functions of the AGV controller. From a hardware perspective, the onboard controllers currently used in AGV can be divided into three types: PLC, industrial control computers, and microcontrollers;
1.Motion Control
Realizes control of the motion mechanisms on the AGV, with different control algorithms used for different motion mechanisms. Currently, mainstream motion control models include: differential wheels, single steering wheels, double steering wheels, differential wheel groups, Mecanum wheel systems, etc.
2.Navigation and Positioning
The operation of the AGV requires accurate movement to the specified position assigned by the system, thus the AGV needs to use related sensors and navigation positioning algorithms to record and reach the assigned position.
3.Safety Protection
The AGV is a robotic worker in factories, and its working area often overlaps with that of human workers. Therefore, safety functions are essential. Through related sensors: laser radar, ultrasonic sensors, anti-collision strips, and other hardware, the working safety of the AGV can be greatly improved. Safety protection is an essential function of the AGV, generally adhering to relevant industry standards and national standards.
4.Auxiliary Functions
Such as control of light strips, horns, etc.
5.Expansion Functions
AGV expansion solutions: functions kits such as forklifts, lifting, rollers, and storage for user selection.
1.4.1 PLC (Programmable Logic Controller)
PLC is known for its good stability and high reliability, but its strength lies in logic control, generally only capable of simple motion control and numerical calculations, with low development difficulty, but poor openness (not easy to expand its software functions and hardware modules).
1. Navigation Methods: AGV carts using magnetic navigation or QR code navigation can complete positioning and navigation control with PLC;
For laser/natural contour navigation AGV products, ordinary PLC products cannot adapt, requiring self-development of related products or purchasing laser navigation modules.
2. The motion control of the wheel system is completed by the MC module on the PLC, supporting secondary packaging development;
3. Safety functions, auxiliary functions, and expansion functions on the PLC are very easy to implement, whether using ladder diagrams or ST.
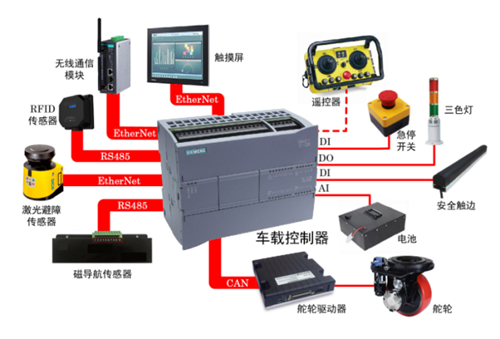
1.4.2 Industrial Control Computer
Industrial control computers are essentially personal computers, designed to have strong anti-interference capabilities, suitable for harsh industrial environments such as vibration and electromagnetic radiation. Industrial control computers are compact and small, capable of running general-purpose operating systems such as Windows and Linux; due to the use of general-purpose hardware and operating systems, industrial control computers have good flexibility and lower development difficulty.
Advantages: Flexible operating systems, rich peripherals and IO interfaces, and abundant system resources and data processing capabilities;
Disadvantages: Higher software development costs, building the ROS system and developing laser navigation and motion control algorithms have certain technical barriers;
1. Motion Control
First, understand the control protocols supported by the selected motors (not discussing pulse-type motors); currently, mainstream protocols include CANOPEN CiA402 protocol, with hardware such as CAN+CANOPEN drivers or CANOPEN over EtherCat for motor control. Alternatively, use soft PLC solutions, such as installing TwinCat soft PLC kernel on industrial control computers for related control.
2. Navigation Control
Due to the rich interfaces and strong computing and data storage capabilities of industrial control computers, hardware such as USB3.0 and Gigabit RJ45 network ports can connect to laser radar and transmit large amounts of point cloud data at speeds of several tens of milliseconds.
The technical difficulty of building visual systems on industrial control computers is not high, capable of achieving QR code positioning or laser navigation + QR code assisted positioning functions.
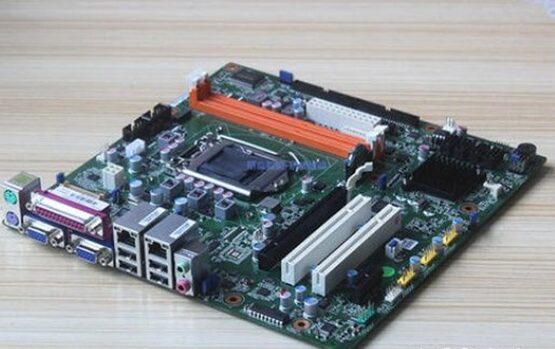
1.4.3 Microcontroller as the Hardware Body
Generally based on ARM, X86, or other chips or core boards developed with peripheral circuits.
Industrial control boards, PLC boards are also microcontrollers, just with higher integration, better universality, and expandability.
If a customized development of a high-performance, low-cost AGV controller is required, choose a hardware architecture of ARM/X86+FPGA+DSP, which has high labor costs for experienced embedded software and hardware engineers and relatively long development time. This basically achieves core technology autonomy. The premise is that the product definition must be clear.
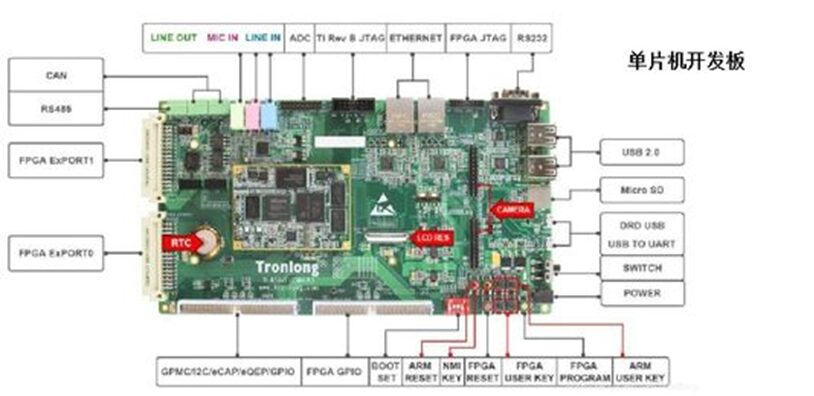
Advantages: Flexible, can be freely developed, while PLC is more modular and can only be called;
Disadvantages: Stability depends on the algorithm capabilities of the developers;
Current Capability: AGV with a load of 1.5 tons has been stably controlled;
Modular Part: Power board and main control board are fixed, only the wiring board is modified (depending on project needs)
1.4.4 Comparison
1、Cost:
PLC and industrial control computers are expensive, with just a CAN bus communication module possibly costing thousands of yuan;
Microcontrollers are inexpensive, with the best chips and peripheral hardware costing at most hundreds of yuan;
2、Development Difficulty:
Embedded development for microcontrollers requires high personnel qualifications, and for complex projects with many functions, development costs can be high, requiring significant time and financial investment; and since AGV is a highly customized industry, if modifications to the C language code are needed for each application, maintenance costs are very high.
PLC programming is intuitive, with PLC manufacturers completing most of the underlying development, requiring only calls;
3、Programming Language:
PLC programming generally uses ladder diagrams;
Industrial control computers can install soft PLC and develop using ladder diagrams or high-level languages like C++;
Microcontrollers can install soft PLC systems or develop directly using C language. However, considerable effort is required to design and debug various underlying communication programs, making development the most challenging;
4、Correlations:
The internal circuit of a PLC is a microcontroller; the programming language of an industrial control computer may use common PLC languages like ladder diagrams or ST; microcontrollers can also run embedded real-time operating systems, forming a powerful multitasking computer. Thus, while each has its areas of applicability, they also complement each other, evolving into a situation where each contains elements of the other.
1.4.5 AGV Controller
To meet the demands of complex projects involving advanced algorithms such as laser positioning, non-complete constraint kinematics, path planning, and Kalman filtering, many companies have begun to develop their own AGV controllers. To save costs, they often choose open-source libraries, thus opting for a control system built on the ROS open-source platform. Some manufacturers also choose mature open soft PLCs, performing secondary development based on them to create integrated products with unique algorithms.
However, they face numerous issues. Firstly, due to the lack of mature solutions for reference, engineering implementation requires a long period of trial and error;
Secondly, to achieve the functions of a soft PLC, it is necessary to complete the design of the PLC language interpreter, develop the programming GUI, handle lower-level technical issues such as multi-process scheduling, and also write lower-level bus communication library functions and design driver programs.
The market has seen the emergence of AGV controllers, such as Sweden’s NDC CVC600, Switzerland’s BlueBotics ANT, Zhejiang Kecong Intelligent’s MRC5000, and Shanghai Xianzhi Robotics’ SRC. Compared to general industrial motion controllers or PLCs, these controllers integrate mature navigation and motion control algorithms (such as laser positioning algorithms, Mecanum wheel control algorithms), saving users a lot of work, and they also have higher stability and protection levels, but their prices are also high (ranging from 10,000 to 60,000 yuan).
1.5Communication Module
Industrial wireless clients (wireless network cards)
The communication system accepts commands from the monitoring system on one hand, transmitting them promptly and accurately to other subsystems to complete the actions specified by the monitoring system, while on the other hand receiving feedback information from each subsystem to return to the monitoring system, serving as the basis for the monitoring system to coordinate, manage, and control. Since the position of the AGV is not fixed and there are many devices in the entire system, wireless communication is most suitable for communication between the control console and the AGV. The control console and each AGV form a point-to-multipoint wireless local area network.
1.7Power Module
The energy system of the AGV system is one of the key systems, including: intelligent battery charging management system, intelligent charger, battery power detection, and battery. The battery selection is as follows:
1.7.1Nickel-Cadmium Battery
Nickel-cadmium batteries are a type of DC power supply battery that can be charged and discharged over 500 times, being economical and durable. They have very low internal resistance, allowing for rapid charging and providing large currents for loads. The voltage change during discharge is also very small.
They have good large current discharge characteristics, strong resistance to overcharging and discharging, and simple maintenance. The discharge voltage of nickel-cadmium batteries varies based on their discharge devices, with each cell battery (Cell) being approximately 1.2V, with a discharge termination voltage of 1.0V/cell.
1.7.2Nickel-Hydrogen Battery
Nickel-hydrogen batteries have twice the energy of nickel-cadmium batteries and can be rapidly charged within an hour with a dedicated charger. Their self-discharge characteristics are better than nickel-cadmium batteries, allowing them to retain charge for longer after charging, and can also be charged and discharged over 500 times.
1.7.3Lead-Acid Battery
The electrodes are mainly made of lead and its oxides, with the electrolyte being a sulfuric acid solution. Lead-acid batteries are the most widely used batteries in AGV. They have good reversibility, stable voltage characteristics, long lifespan, wide applicability, abundant raw materials, and can be recycled with low costs.
1.7.4Ternary Lithium Battery
Lithium batteries have a high energy density; compared to high-capacity nickel-chromium batteries, their volume energy is 1.5 times higher, and their energy density is 2 times higher. The average operating voltage is 3.6V, which is three times that of nickel-chromium and nickel-hydrogen batteries, and the operating voltage is stable and high capacity, with an operating temperature range of -20°C to 60°C. They have a long charge-discharge lifespan, with at least 70% capacity remaining after 500 discharges due to their high energy density, high voltage, and stable operation.
Ternary lithium batteries refer to lithium batteries that use nickel-cobalt-manganese oxide as the positive electrode material and graphite as the negative electrode material. Generally, lithium batteries using nickel-cobalt-manganese oxide or nickel-cobalt-aluminum oxide ternary positive electrode materials have a higher voltage platform than lithium iron phosphate, with higher voltage platforms yielding larger capacity. Under the same volume or weight, ternary lithium batteries with higher voltage platforms have longer endurance. In terms of high-rate charging and low-temperature performance, ternary lithium batteries also have significant advantages, though their costs are higher.
1.7.5Lithium Iron Phosphate Battery
Lithium iron phosphate batteries use lithium iron phosphate as the positive electrode material, featuring the advantages of not containing precious metal elements, high-temperature resistance, strong safety stability, low cost, and better cycle performance.
1.7.6Battery Selection Comparison Analysis
Lead-acid batteries have significant drawbacks such as large weight, short cycle life, and short endurance time, while lithium batteries have advantages in cost-effectiveness, small volume, long cycle life, endurance capability, and fast charging, better meeting the flexible, efficient, and energy-saving application needs of AGV. Therefore, lithium batteries are currently the main application in AGV. Based on varying requirements for volume, application scenarios, functions, and load requirements, the demands for lithium batteries in AGV also vary. The battery capacity ranges from 0.3KWh to 40KWh.
Currently, for types of AGV such as handling (non-heavy loads), inspection, picking, and assembly, lithium iron phosphate batteries are primarily used. For special application environments requiring low load and high efficiency, smaller battery size and higher endurance make ternary batteries more favorable. However, heavy-duty applications such as forklift-type AGV still primarily use lead-acid batteries, with lithium iron phosphate gradually replacing them.
The batteries and management systems of AGV serve as the primary power source for AGV products, and their size, capacity, and weight must be considered from the initial product design phase, as these factors not only relate to the product’s industrial design but also impact its performance and power consumption.
In battery selection, factors such as nominal voltage, peak voltage, internal resistance, self-discharge rate, charging time, and charging methods are all important considerations. At the same time, integrating an intelligent battery management system will make the safety, flexibility, efficiency, and reliability of AGV products even more prominent.
Previous Articles Review:
[Special] Selection Design of Steering Wheels for AGV/AMR – Taking CFR Steering Wheels as an Example
[Free Download] Mobile Robot (AGV/AMR) Operating Environment Engineering Manual
How to Choose Support Casters for AGV?