The “Ecological Industry Science and Phosphorus Fluorine Engineering” column mainly publishes content related to the manufacturing of high-value products involving life and health, new energy, and new energy vehicles, based on the preparation technology of high-end new materials produced from accompanying resources. The phosphorus and fluorine (or nitrogen, potassium, sulfur, silicon, magnesium, titanium, coal) industry involves the separation, extraction, or coupling and synergistic technology from raw materials to processes, products, and materials, fluorochemical technology and fluorine-containing new materials, new energy (power battery) materials, biomimetic materials, energy storage materials, optoelectronic functional materials, electronic chemicals, functional fine chemicals, and life health (food and medical) materials, such as ingredients and functional additives used for food quality improvement and nutritional enhancement; various organic phosphates used to prepare phosphorus-containing drugs with antibacterial, antiviral, anti-parasitic, anti-tumor, anti-inflammatory and analgesic properties, beneficial for nerve and cardiovascular health; red phosphorus for pesticide insecticides used for crop protection; high-purity and special functional phosphorus products, such as lithium-ion batteries, solar cells, optical and sensing element materials, electronic-grade phosphoric acid, ion exchange agents, catalysts, and other high-value products.
This column is open for long-term submissions, and we welcome contributions! The “Ecological Industry Science and Phosphorus Fluorine Engineering” The only online submission website: https://lfyf.cbpt.cnki.net/. Manuscript requirements can be found in the “Submission Announcement for the Ecological Industry Science and Phosphorus Fluorine Engineering” (click to jump). Submission inquiries: 0371-63887309 67781991.
[Publication Source]Chen Weifeng, Cao Jingtong, Meng Qingwen, et al. Research Progress on Synthesis and Application of Trifluorochloroethylene Based Polymers [J]. Ecological Industry Science and Phosphorus Fluorine Engineering, 2024, 39(9): 53-59.
Chen Weifeng, Cao Jingtong, Meng Qingwen, Yu Guojun, Qiu Kanhui
This article was published in the September 2024 issue of Ecological Industry Science and Phosphorus Fluorine Engineering
[Author Introduction]Chen Weifeng (1977-), Senior Engineer at Juhua Group Co., Ltd., engaged in research on fluorinated polymers and fluorinated fine chemicals.

▼Advertisement
[Abstract] This paper expounds the structure and properties of two trifluorochloroethylene based polymers, polytrifluorochloroethylene (PCTFE) and ethylene-trifluorochloroethylene copolymer (ECTFE), and introduces the synthesis methods and modification research progress of PCTFE and ECTFE both domestically and internationally. It points out the urgent need to develop high-quality trifluorochloroethylene based polymer resins and products domestically and to achieve industrialization as soon as possible; increase research efforts on the modification of trifluorochloroethylene based polymers, collaborate upstream and downstream, jointly expand new application areas, further improve product added value, and promote the high-quality development of trifluorochloroethylene based products.
[Keywords] Trifluorochloroethylene; Polytrifluorochloroethylene; Ethylene-trifluorochloroethylene Copolymer; Structure; Properties; Synthesis Process; Modification
Research Progress on Synthesis and Application of Trifluorochloroethylene Based Polymers
CHEN Weifeng, CAO Jingtong, MENG Qingwen, YU Guojun, QIU Kanhui (Juhua Group Co., Ltd., Quzhou 324004, China)
Abstract: The structures and properties of two trifluorochloroethylene based polymers such as polytrifluorochloroethylene (PCTFE) and ethylene-trifluorochloroethylene copolymer (ECTFE) are expounded, and the research progress on their synthesis process and modifications are introduced. It is pointed out that there is an urgent need to develop high-quality trifluorochloroethylene based polymer resins and products domestically and to achieve industrialization as soon as possible; increase research efforts on the modification of trifluorochloroethylene based polymers, collaborate upstream and downstream, jointly expand new application areas, further improve product added value, and promote high-quality development of trifluorochloroethylene based polymers.
Key words:trifluorochloroethylene; PCTFE; ECTFE; structure; properties; synthesis process; modification
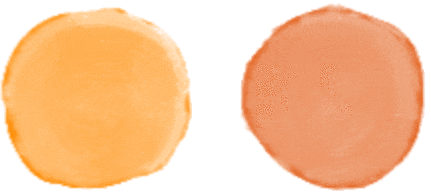
0 Introduction
Polytrifluorochloroethylene (PCTFE) and ethylene-trifluorochloroethylene copolymer (ECTFE) are the two most important trifluorochloroethylene based polymers, which have attracted much attention due to their excellent properties such as water vapor permeability resistance, corrosion resistance, optical transparency, and creep resistance in specific fields. In 1934, researchers from Germany’s IG Farbenindustrie AG, SCHLOFFER and SCHERER[1] first prepared PCTFE, but due to its poor performance, it could not be practically applied. In 1938, with the commencement of the Manhattan Project, PCTFE experienced rapid development as a material for separating uranium isotopes. Subsequently, Hooker Company commercialized the production of PCTFE lubricants, and companies such as 3M (Minnesota Mining and Manufacturing Company), Honeywell, and Japan’s Daikin also developed PCTFE products and achieved commercialization. Domestic research on PCTFE began later than in Europe and America, starting in the 1960s, and has not yet achieved commercialization.
ECTFE is an alternating copolymer of ethylene and trifluorochloroethylene (CTFE) with a molar ratio of nearly 1:1, first synthesized by DuPont in 1946[3], and commercialized by the American Applied Chemistry Organization (now Solvay) in 1947. Currently, global production capacity is concentrated in Solvay[4], while only a few companies in China have pilot production facilities, with no reports of industrialization.
The performance of PCTFE mainly depends on molecular weight and crystallinity. At low molecular weight, the melting temperature is low, providing good fluidity and lubricity, and it can usually be used as a lubricant. At high molecular weight, it has better thermal stability. Low crystallinity PCTFE possesses good ductility and transparency, while high crystallinity PCTFE, although slightly less transparent, has higher mechanical strength and strong gas and liquid barrier capabilities. As a copolymer of CTFE and ethylene, ECTFE exhibits excellent corrosion resistance, weather resistance, and barrier properties, along with good tensile, bending, and wear resistance. The strength, wear resistance, and creep resistance of ECTFE are significantly greater than those of PTFE (polytetrafluoroethylene) and FEP (fluorinated ethylene-propylene copolymer), making it widely used in anti-corrosion coatings, linings, membrane materials, and electrical materials.
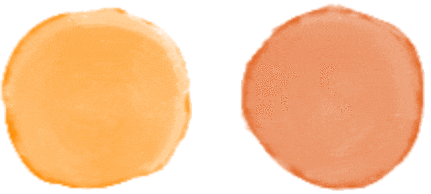
1 Structure of Trifluorochloroethylene Based Polymers
1.1 PCTFE
PCTFE, as one of the earliest discovered and commercialized fluoropolymers, has undergone a series of studies regarding its structure. The backbone of the PCTFE molecule is tightly wrapped by fluorine and chlorine atoms, preventing the carbon skeleton from exposure (see Figure 1). PCTFE is a semi-crystalline polymer with a crystallinity of 40% to 80%.
Figure 1 Molecular structure of PCTFE
In 1973, MENCIK et al.[5] discovered that PCTFE has a quasi-hexagonal crystal system (lattice parameters a=b=0.644 nm, c=4.15 nm, α=β=90° and γ=120°). PRICE et al.[6] found that the crystallization of PCTFE at 175 to 190 °C is mainly heterogeneous nucleation, while the crystallization process at 150 to 175 °C is mainly a combination of homogeneous nucleation and heterogeneous nucleation; they also mentioned the influence of molecular weight on the crystallization rate. HOFFMAN et al.[7-8] discovered that the crystal growth of PCTFE is similar to that of polyethylene spherulites, consisting of folded chain crystallization, and studied the process and mechanism of PCTFE segment relaxation under different temperature conditions, calculating the relaxation time and energy barrier required to reach the equilibrium state of chain segment arrangement, comparing the actual relaxation time and activation energy, suggesting that there are at least three types of α relaxation in the crystal phase of PCTFE, namely coupling flip of chains within the crystal, axial rotation of short molecular chains, and small rotational and folding movements of chains on the rough surfaces of folded chain crystals. TATSUNO et al.[9] found that intense molecular motion occurs in PCTFE at temperatures above 120 °C. Therefore, they concluded that PCTFE crystals are more fluid than other semi-crystalline fluoropolymers (such as polyvinylidene fluoride), indicating the presence of structural defects in PCTFE.
1.2 ECTFE
In 1972, SIBILIA et al.[10] discovered that ECTFE, obtained by copolymerizing ethylene and trifluorochloroethylene in a molar ratio of 1:1, has a semi-crystalline internal structure with a melting point as high as 241 °C.
In 2022, YANG et al.[11] studied the isothermal (IT) and non-isothermal (NIT) crystallization kinetics, morphology, and structure of ECTFE through differential scanning calorimetry (DSC), polarized optical microscopy (POM), and X-ray diffraction (XRD), finding that the equilibrium melting point of ECTFE is 238.66 °C, and the activation energy for isothermal crystallization is -137.68 kJ/mol, with ECTFE exhibiting spherical or hexagonal crystal structures.
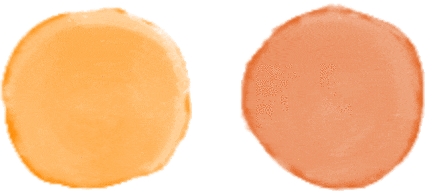
2 Performance of Trifluorochloroethylene Based Polymers
2.1 Performance of PCTFE
2.1.1 Chemical Properties
The high content of fluorine and chlorine endows PCTFE with excellent chemical corrosion resistance and chemical inertness; PCTFE can only be corroded by molten alkali metals or chlorosulfonic acid at high temperatures and can be used to make corrosion-resistant pumps and valves for transporting strong acids and bases at temperatures not exceeding 100 °C. Furthermore, due to the presence of chlorine atoms, PCTFE has poor symmetry, thus its transparency, processability, and creep resistance are much better than those of PTFE.
2.1.2 Thermal Properties
The glass transition temperature of PCTFE is 71 to 99 °C, and the melting point is 211 to 216 °C. When the temperature exceeds 310 °C, PCTFE decomposes in the presence of O2 into —CF CF2, CF2 CFCl, CF2 CCl2, etc. ZULFIQAR et al.[12] studied the pyrolysis process of PCTFE, finding that PCTFE decomposes into CTFE monomers, which are generated from the cleavage of C—C bonds producing terminal chain free radicals; simultaneously, chlorine atoms undergo intramolecular transfer, i.e., terminal free radicals seize chlorine atoms from other sequences, leading to chain scission, degradation, and transfer reactions. Moreover, MA et al.[13] found that PCTFE, as a low-temperature polymer, exhibits excellent low-temperature toughness and creep durability in liquid nitrogen, liquid oxygen, and liquefied natural gas. Therefore, PCTFE is widely used as lining material for pipelines transporting liquefied natural gas, liquid oxygen, and liquid nitrogen, as well as for sealing liquid fuels and low-temperature valves.
2.1.3 Mechanical Properties
Replacing fluorine atoms in polytetrafluoroethylene with chlorine atoms can improve mechanical properties, including tensile strength, compressive strength, and creep retention time[14]. The mechanical properties of PCTFE can be adjusted by controlling its crystallinity and molecular weight. For example, PCTFE with high crystallinity is brittle, with reduced impact strength and elongation at break, while low crystallinity PCTFE has better toughness. BROWN et al.[15] studied the tensile and compressive responses of PCTFE under different temperature and strain rate conditions, finding that the tensile and compressive recovery of PCTFE exhibits significant asymmetry and is strongly dependent on temperature and strain rate; when the temperature exceeds Tg, the mechanical toughness of PCTFE significantly increases. ZHANG et al.[16] found that the hardness and elastic recovery rate of PCTFE samples increase with decreasing temperature, while the compression ratio shows a downward trend.
2.1.4 Dielectric Properties
PCTFE has wide frequency low dielectric constant and dielectric loss characteristics, making it an excellent choice for high-frequency communication materials. Due to its good electrical performance, PCTFE can be used as a coating material for electrical components such as cables, connectors, and circuit boards in humid environments. HARA et al.[17] found that the dipole interaction of crystalline regions and terminal groups has a strong impact on the dielectric properties of low molecular weight PCTFE. SCOTT et al.[18] studied the dielectric relaxation process of PCTFE under low-frequency conditions, finding that high-crystallinity PCTFE exhibits three dielectric loss peaks, corresponding to loss at the surface of crystalline spherulites, movement of molecular chain segments in the amorphous region, and reorganization of defects within crystalline regions. Song Hangling et al.[19] found that the crystalline morphology of PCTFE affects its high-frequency dielectric properties, with lower crystallinity and smaller crystalline size PCTFE exhibiting lower dielectric constant and dielectric loss.
2.1.5 Barrier Properties
PCTFE exhibits excellent water vapor barrier properties, with a permeability of only 0.171 kg/(m2·h), making it the best water vapor barrier material among various plastics. It is typically used as packaging films in aerospace, national defense, medical devices, electronic components, etc., accounting for 75% of the PCTFE market share. The Aclar film produced by Honeywell can be used for packaging products or spare parts that are sensitive to moisture. Furthermore, PCTFE has low absorption rates for infrared and ultraviolet light, with some PCTFE film products having a light transmittance of up to 90%.
2.2 Performance of ECTFE
2.2.1 Chemical Properties
ECTFE is a polymer known for its chemical corrosion resistance, suitable for various industrial applications. It is resistant to strong acids, corrosive media, oxidants, and many solvents at high concentrations/high temperatures, similar to polytetrafluoroethylene. To date, no substance has been found to corrode ECTFE or cause it to crack below 120 °C. The continuous use temperature range for ECTFE is -76 to 150 °C, and in engineering applications, there is no need to add additives such as UV stabilizers, thermal stabilizers, plasticizers, lubricants, or flame retardants, and it exhibits outstanding impact resistance and excellent mechanical strength. Therefore, it can be used to make linings or anti-corrosion coatings for valves, pipelines, pumps, containers, and storage tanks, widely applied in chemical, petrochemical, and pharmaceutical fields.
ECTFE exhibits anti-permeation properties towards macromolecules, which is typically slow and not obvious in practical applications. However, small molecules may permeate through the polymer matrix. When ECTFE is used as a lining or coating, the permeability of certain small molecules determines the lifespan of the equipment. Small molecules such as H2O, O2, Cl2, H2S, HCl, HF, HBr, N2, H2, and CH3OH have relative mobility in the polymer matrix, which can produce measurable effects. Due to the presence of chlorine atoms in the polymer chain, ECTFE occupies free volume, restricting the movement of small molecules within the material, and is often used to protect fiber-reinforced plastics (FRP) or steel from corrosive substances.
Solvay’s Halar901 resin can be made into films for seawater treatment and wastewater desalination. The film made from Solvay’s Halar500 resin remains stable under UV irradiation, has low water vapor permeability, and good light transmittance, making it a substitute for glass in photovoltaic panels. Additionally, ECTFE can also replace glass for decorative and protective films on building surfaces, and its flame retardant and high-temperature resistance properties are outstanding.
In terms of flame retardancy, ECTFE has a limiting oxygen index of 52%, which falls between the limiting oxygen indices of fully fluorinated polymers PTFE, PFA (perfluoroalkoxy), and FEP and other partially fluorinated polymers (such as PVDF with a limiting oxygen index of 44% or ETFE with a limiting oxygen index of 30%).
ECTFE is an electrical insulator with high resistivity, low dielectric constant, and low dissipation factor, making it suitable for wire and cable sheathing. ECTFE also exhibits good UV resistance, especially against UV-A and UV-B.
2.2.2 Surface Properties
ECTFE differs from all other fluorinated polymers in its unique surface smoothness and cleanliness, which facilitates particle shedding, prevents particle capture, and reduces biofilm and colony formation. It is used as a coating anti-corrosion system for clean ventilation ducts in the semiconductor field, which can reduce pollutant accumulation and minimize corrosion, maintaining system cleanliness.
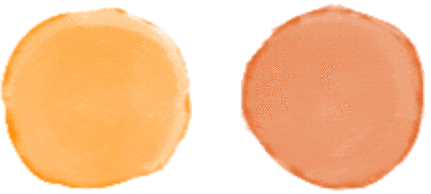
3 Synthesis of Trifluorochloroethylene Based Polymers
3.1 Synthesis Methods of PCTFE
Currently, the synthesis of PCTFE mainly adopts free radical polymerization processes, with the industrial focus on suspension polymerization and emulsion polymerization. The polymerization reaction is generally initiated by free radicals, often using an oxidation-reduction system. Additionally, solution polymerization or polymerization initiated by ultraviolet or γ-ray radiation can also be employed.
3.1.1 Suspension Polymerization
PCTFE suspension polymerization is usually carried out at low temperatures and pressures, using water or a water/alcohol mixed solution as the reaction medium. During the reaction process, promoters, pH buffers, chain transfer agents, and molecular weight regulators need to be added to promote the reaction and adjust product performance. Wei Changpei[20] found that by increasing the polymerization reaction pressure and the concentration of monomers in the reaction system while adding a small amount of emulsifying surfactant, the reaction rate and molecular weight of PCTFE can be controlled. However, the suspension polymerization synthesis of PCTFE has its limitations, as during the polymerization reaction, the chain ends are easily introduced with unstable groups such as acyl fluorides and carboxyl groups due to the influence of initiators, chain transfer agents, and rearrangement reactions. These unstable groups can easily decompose or cross-link during processing due to heat, leading to reduced thermal stability and discoloration of PCTFE products. How to solve this problem has become a key research focus in current suspension polymerization studies.
China’s Grand Energy Materials (Dalian) Co., Ltd.[21] disclosed a method for preparing high-temperature degradation-resistant polytrifluorochloroethylene, using deionized water as the medium, with inorganic peroxide initiators under the presence of reducing agents to initiate the polymerization of trifluorochloroethylene (CTFE) at a reaction temperature of 20 to 80 °C and a pressure of 0.4 to 1.5 MPa. After filtration, washing, and drying, fluorination end-capping is performed using F2/N2 mixed gas, yielding high-temperature degradation-resistant polytrifluorochloroethylene resin. This resin has good processability and does not degrade or discolor at processing temperatures of 300 °C. However, end-capping treatment with F2 increases the likelihood of molecular structure damage and is not environmentally friendly.
Shandong Huaxia Shenzhou New Materials Co., Ltd.[22] added pH buffers and molecular weight regulators in solvents, initiating the reaction under an oxidation-reduction initiator (a mixture of persulfate and bisulfite), controlling the temperature at 10 to 70 °C, resulting in a PCTFE resin with high-temperature stability that does not degrade or discolor at 240 to 280 °C.
3.1.2 Emulsion Polymerization
In emulsion polymerization, in addition to the monomer, initiators, emulsifiers, pH buffers, and dispersing media need to be added. In early emulsion polymerization for synthesizing PCTFE, the initiators used were alkali metal persulfates or bisulfites, and the emulsifiers were perfluorocarboxylic acids or chlorofluorocarboxylic acids and their salts[23-24].
ENOKIDA et al.[25] successfully synthesized a stable PCTFE polymer using carboxylate salts as emulsifiers in an emulsion polymerization method.
China National Chemical Corporation Blue Sky Group Co., Ltd.[26] disclosed a preparation method for PCTFE resin, using a horizontal reactor with a length-to-diameter ratio ≥ 1.0 as the polymerization equipment; the polymerization reaction of trifluorochloroethylene monomer or trifluorochloroethylene monomer with other co-monomers occurs under constant pressure conditions, improving the reaction rate and polymerization efficiency; a semi-mechanical, semi-chemical condensation method is used to effectively separate impurities in the emulsion. Wet heat treatment reduces residual unstable groups, effectively lowering the product’s volatile content and significantly improving the product’s appearance.
3.1.3 Bulk Polymerization
PCTFE bulk polymerization typically uses organic peroxides, such as alkali metal fluorides[27], benzoyl peroxide[28], or di-tert-butyl peroxide[29] as initiators, initiating the monomer polymerization reaction in the liquid or gas phase. Compared to suspension polymerization and emulsion polymerization, bulk polymerization has a higher conversion rate and is easier for post-processing. However, bulk polymerization requires reactions at extremely high temperatures or pressures, and may even require critical CO2 or ultraviolet light to initiate the reaction. These factors limit the application of bulk polymerization in the industrial production of PCTFE. REARICK et al.[30] obtained PCTFE emulsions with w(solid) within 12% using the bulk polymerization method in horizontal reactors.
3.2 Synthesis Methods of ECTFE
3.2.1 Suspension Polymerization
Suspension polymerization generally uses water as the reaction medium, allowing gaseous ethylene to contact a suspension of trifluorochloroethylene, adjusting the ethylene pressure or reaction temperature to control the polymer’s composition. The physical or mechanical properties of the resulting polymer depend not only on the polymer composition but also on the degree of alternation of the monomers. The degree of alternation of the monomers largely depends on the reaction temperature. The pH of the aqueous medium affects the polymerization rate. The pH of the aqueous medium can be controlled by buffers to maintain a range of 7 to 12, preferably between 7 and 9[31]. SCOGGINS et al.[32] disclosed a process for copolymerizing trifluorochloroethylene and ethylene using oxidants and reductants, maintaining the pH between 7 and 12 by adding sufficient water-soluble buffering compounds.
The initiators used in suspension polymerization are mostly peroxides, with the amount of initiator generally determined by the conditions of the polymerization reaction and the type of initiator, usually 0.05% to 0.50% of the total mass of the monomer. Suspension polymerization requires the addition of surfactants, with fluorinated surfactants being optimal. KATO et al.[33] successfully synthesized homogeneous, high-performance fluorinated polymers through suspension polymerization using surfactants with small chain transfer coefficients, with a formula of CnF2n+1CO2X or CnF2n+1SO3X (where n is an integer from 4 to 12, and X is NH4 or alkali metal).
3.2.2 Emulsion Polymerization
This is currently the most commonly used method for synthesizing polymers both domestically and internationally, using fluorinated vinyl compounds for free radical emulsion polymerization, or copolymerizing fluorinated monomers with non-fluorinated olefin monomers to obtain fluorinated polymer emulsions. Emulsion polymerization has a high polymerization rate, yielding high molecular weight polymers. Wang Wengui[34] used perfluorooctanoic ammonium as an emulsifier, ammonium persulfate as an initiator, and borax as a pH buffer to obtain ECTFE emulsion through emulsion polymerization, followed by demulsification, washing, and drying to finally obtain ECTFE. However, the emulsifier used, perfluorooctanoic ammonium, is environmentally unfriendly and has been explicitly banned from use.
China National Chemical Corporation Blue Sky Group Co., Ltd.’s Gao Zihong et al.[35] provided a synthesis method for ECTFE, copolymerizing at least ethylene, trifluorochloroethylene, CF3—CX CY2 (where X and Y are independently selected from H, F, Cl, or Br) and R—O—CH CH2 (where R is a straight-chain alkyl, branched alkyl, cycloalkyl, or C2—C16 straight-chain alkyl, branched alkyl, cycloalkyl substituted by C1, Br) to form copolymers. The ECTFE synthesized by this method is suitable for protecting equipment against corrosion/microbial attachment. Additionally, a preparation method for melt-blown ECTFE was disclosed, with co-monomers including ethylene, trifluorochloroethylene, and modified monomer A (Rx—(CF2)m—O—CF CF2). The ethylene-trifluorochloroethylene copolymer synthesized by this method has good mechanical strength, low melting temperature, and ultra-high melt index, suitable for producing melt-blown nonwovens (used for industrial filtration filter elements)[36].
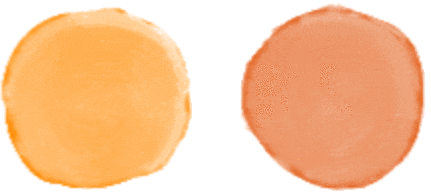
4 Modification of Trifluorochloroethylene Based Polymers
PCTFE and ECTFE are widely used in many fields, such as film packaging materials (PCTFE can be used for packaging films in pharmaceuticals, medical devices, field-induced luminescent components, electronic components, military items, and aerospace), low-temperature corrosion-resistant materials (PCTFE has high compressive strength and is suitable for use as high-pressure corrosion-resistant gaskets in chemical equipment; ECTFE can be used for equipment/container lining coatings for corrosion resistance), membrane materials (ECTFE is used for separation membranes in wastewater treatment and seawater desalination), etc., but there are still some shortcomings. For instance, PCTFE is only soluble in a few highly toxic organic solvents at high temperatures (>100 °C), making solvent processing impossible; PCTFE has a high melting temperature (Tm) and melt viscosity, making melt processing quite difficult and expensive; high crystallization rate and high crystallinity lead to poor toughness of PCTFE, limiting its further development. Moreover, the traditional synthesis solvents for ECTFE are highly toxic, placing significant pressure on the environment. Polymer modification is a common method for optimizing its performance and broadening its application fields.
4.1 Research on PCTFE Modification
4.1.1 Copolymer Modification
Copolymer modification of PCTFE involves adding other monomers during the polymerization process to improve certain defects in PCTFE materials. The copolymerization process can be achieved through traditional free radical polymerization reactions and controllable free radical polymerization reactions, with a wide variety of copolymer monomers. Currently, the PCTFE copolymers that have been studied more include ECTFE and trifluorochloroethylene-vinylidene fluoride copolymers (P(CTFE-co-VDF))[37]. In addition, researchers have also achieved copolymerization with CTFE and propylene[38], isobutylene[39], acrylic (ester) compounds[40], vinyl ethers, and other copolymer monomers.
P(CTFE-co-VDF)[41] is a random copolymer of vinylidene fluoride and trifluorochloroethylene, synthesized via traditional free radical copolymerization or controllable free radical polymerization[42], with the structure of [ (CF2CFCl)x(CH2CF2)y] n. P(CTFE-co-VDF) was first synthesized in 1955, and subsequently commercialized by Kellogg Company under the trade name Kel-F. During the polymerization process, different ratios of VDF monomers can be added, resulting in varying performance of the copolymers. The amount of VDF is crucial to the performance of the copolymers. For example, copolymers containing only a small amount of VDF are semi-crystalline and still maintain thermoplasticity. The introduction of VDF disrupts the regularity of the PCTFE molecular chain, leading to a significant decrease in copolymer crystallinity and a lower melting point compared to PCTFE, making it more suitable for thermoplastic processing. When the molar fraction of VDF is 30% to 75%, the resulting copolymer becomes an amorphous polymer primarily exhibiting elastomeric properties, with high-temperature resistance, oil resistance, chemical resistance, and radiation resistance, and can be cross-linked using diamines, diphenols, or peroxides as crosslinking agents.
4.1.2 Blending Modification
Polymer blending modification is an efficient and convenient method to improve the comprehensive performance of polymers through physical blending. Feng Na et al.[43] improved the instability of PCTFE during processing by adding rare earth stabilizers, and as the stabilizer dosage increased, the dynamic thermal stability of PCTFE significantly improved. When 6 phr stabilizers were added, both mechanical toughness and processing capability improved synchronously. Wu Lei et al.[44] improved the mechanical and processing performance of PCTFE by blending it with nucleating agents. Li Ji et al.[45] blended PCTFE with core-shell acrylate copolymers (ACR) or CTFE copolymers, enhancing the toughness of PCTFE, which is attributed to improved interfacial compatibility, resulting in reduced crystal size and crystallinity.
In addition to the toughening of PCTFE, studies have also been conducted on modifying the mechanical properties of PCTFE. WEI et al.[46] incorporated carbon fibers (CFs) into PCTFE, studying the effects of CF content and length on the mechanical properties of the composites. The results showed that as the CF content increased, the flexural strength initially rose and then fell. Additionally, CFs shorter than 5 mm exhibited a better reinforcing effect. Wen Jialiang et al.[47] prepared CF-reinforced PCTFE composites using extrusion compression methods, with minimal decomposition of the PCTFE melt under low extrusion rates and short screw lengths, significantly improving compressive strength and modulus.
MABRY et al.[48] introduced a fluorinated polyhedral oligomeric silsesquioxane (POSS) into PCTFE, demonstrating that this filler imparts good hydrophobicity to the composites. The improvement in processing performance after modification did not compromise the thermal stability and mechanical properties of PCTFE.
4.1.3 Surface Modification
In certain specific application fields, PCTFE needs to be compounded with other materials to compensate for its shortcomings and improve comprehensive performance. For this purpose, PCTFE needs to have sufficient adhesion to other materials. However, due to the low surface energy of PCTFE materials, surface modification is usually required to reduce the interfacial tension with the attached materials. Compared to other fluorinated resins, PCTFE has unique reactivity due to the presence of chlorine atoms. Therefore, reactive functional groups can be introduced into PCTFE through nucleophilic substitution and elimination reactions. SIERGIEJ et al.[49] reacted phenyl lithium with PCTFE in THF under a helium atmosphere to obtain phenyl-modified PCTFE material, where the chlorine atoms in PCTFE were replaced by phenyl groups. OKUBO et al.[50] performed surface modification of PCTFE films using atmospheric pressure non-thermal plasma graft polymerization, resulting in a reduction of the water contact angle of the modified films from 91° to 42°, achieving a peel strength of 13.3 N·mm between the PCTFE films and aluminum foil in T-peel tests.
4.2 Research on ECTFE Modification
ECTFE is insoluble in any solvent at room temperature and cannot be made into films using traditional dry or wet methods; however, ECTFE can dissolve in certain specific solvents when heated, and hollow fiber membranes or flat membranes can be prepared using the thermal-induced phase separation (TIPS) method. URSINO et al.[51] investigated a low-melting-point ethylene-chlorotrfluoroethylene (LMP ECTFE) and used it to prepare solvent-resistant flat membranes. Among the different types of non-toxic solvents tested, diethyl adipate (DEA) was selected for preparing flat membranes through thermal-induced phase separation (TIPS), and the newly developed LMP ECTFE membranes were found to be very suitable for organic solvent separation. FALBO et al.[52] prepared flat membranes from Halar@901 through TIPS at 180 °C. These flat membranes exhibited good organic solvent selectivity and high flux, capable of separating organic solvent mixtures, such as ethanol/cyclohexane mixtures.
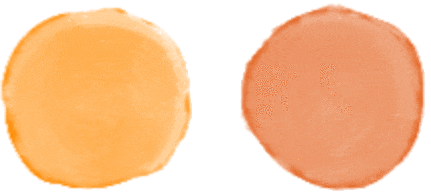
5 Outlook
Trifluorochloroethylene based polymers, especially PCTFE resins and ECTFE resins, still have irreplaceable roles in aerospace, new energy, semiconductors, and electronic communication fields, with broad application prospects, and their production technology is monopolized by multinational companies. Therefore, there is an urgent need to develop high-quality trifluorochloroethylene based polymer resins and products domestically and to achieve industrialization as soon as possible. Furthermore, domestic research efforts on the modification of trifluorochloroethylene polymers should be increased, and upstream and downstream collaboration should be strengthened to jointly expand new application areas, further improve product added value, and promote the high-quality development of trifluorochloroethylene based polymer products.
[References]
[1] Lin Yu, Jiang Wei, Ye Haihua, et al. Research Progress and Application of Fluoropolymers [J]. Guangzhou Chemical Industry, 2022, 50(22): 45-49. LIN Y, JIANG W, YE H H, et al. Research Progress and Application of Fluoropolymers [J]. Guangzhou Chemical Industry, 2022, 50(22): 45-49.
[2] Yu Guojian. Study on Crystallization Behavior and Toughening Modification of PCTFE [D]. Dalian: Dalian Polytechnic University, 2014. YU G J. Study on Crystallization Behavior and Toughening Modification of PCTFE [D]. Dalian: Dalian Polytechnic University, 2014.
[3] Hanford W E. Copolymerization of Chlorotrifluoroethylene and Olefin Hydrocarbons: US2392378 [P]. 1946-01-08.
[4] Wang Wengui, Yang Yong, Chen Bingni. Research Progress of Ethylene-Trifluorochloroethylene Copolymers (ECTFE) [J]. Organo-Fluorine Industry, 2007(2): 28-32. WANG W G, YANG Y, CHEN B N, et al. Research Progress of ECTFE [J]. Organo-Fluorine Industry, 2007(2): 28-32.
[5] Mencik Z. Crystal Structure of Polychlorotrifluoroethylene [J]. Journal of Polymer Science. Part B: Polymer Physics, 1973, 11(8): 1585-1599.
[6] Price F P. The Development of Crystallinity in Polychlorotrifluoroethylene [J]. Journal of the American Chemical Society, 1952, 74(2): 311-318.
[7] Hoffman J D, Weeks J J. Rate of Spherulitic Crystallization with Chain Folds in Polychlorotrifluoroethylene [J]. The Journal of Chemical Physics, 1962, 37(8): 1723-1741.
[8] Hoffman J D, Williams G, Passaglia E. Analysis of the α, β, and γ Relaxations in Polychlorotrifluoroethylene and Polyethylene: Dielectric and Mechanical Properties [J]. Journal of Polymer Science: Polymer Symposia, 1966, 14(1): 173-235.
[9] Tatsuno H, Aimi K, Ando S. Solid-State 19F MAS NMR Study on the Conformation and Molecular Mobility of Poly(Chlorotrifluoroethylene) [J]. Magnetic Resonance in Chemistry, 2007, 45(5): 401-409.
[10] Sibilia J P, Roldan L G, Chandrasekaran S. Structure of Ethylene-Chlorotrifluoroethylene Copolymers [J]. Journal of Polymer Science. Part B: Polymer Physics, 1972, 10(3): 549-563.
[11] Yang X D, Yu B, Sun H, et al. Isothermal and Non-Isothermal Crystallization Kinetics of Poly(Ethylene-Chlorotrifluoroethylene) [J]. Polymers, 2022, 14(13): 2630.
[12] Zulfiqar S, Rizvi M, Munir A, et al. Thermal Degradation Studies of Copolymers of Chlorotrifluoroethylene and Methyl Methacrylate [J]. Polymer Degradation and Stability, 1996, 52(3): 341-348.
[13] Ma Z Y, Li W S. Properties and Application of Polychlorotrifluoroethylene [J]. Organo-Fluorine Industry, 2005(4): 11-12. MA Z Y, LI W S. Properties and Application of Polychlorotrifluoroethylene [J]. Organo-Fluorine Industry, 2005(4): 11-12.
[14] Teng H. Overview of the Development of the Fluoropolymer Industry [J]. Applied Sciences, 2012, 2(2): 496-512.
[15] Brown E N, Rae P J, Orler E B. The Influence of Temperature and Strain Rate on the Constitutive and Damage Responses of Polychlorotrifluoroethylene (PCTFE, Kel-F 81) [J]. Polymer, 2006, 47(21): 7506-7518.
[16] Zhang X H, Zhou J Y. Study on Low Temperature Performance of Ultra-Low Temperature Valves with PCTFE Gasket [J]. Chem Eng Machinery, 2017, 44(5): 497-501.
[17] Hara T. Dielectric Properties of Low Molecular Weight Polychlorotrifluoroethylene [J]. Japanese Journal of Applied Physics, 1967, 6(2): 135.
[18] Scott A H, Scheiber D J, Curtis A J, et al. Dielectric Properties of Semicrystalline Polychlorotrifluoroethylene [J]. Journal of Research of the National Bureau of Standards Section A-Physics and Chemistry, 1962, 66: 269-305.
[19] Song Hangling, Han Aichun, Zhang Yao, et al. Effects of Crystalline Morphology on the High-Frequency Dielectric Properties of Poly(Trifluorochloroethylene) [J]. Polymeric Materials Science and Engineering, 2018, 34(6): 49-53.
[20] Wei Changpei. PCTFE Molecular Weight Control and Methods for Improving Polymerization Rate [J]. Organo-Fluorine Industry, 2023(1): 8-9.
[21] Li W S, Jiang Y W, Tang H, et al. A Method for Preparing Polytetrafluoroethylene: CN103172773A [P]. 2013-06-26. LI W S, JIANG Y W, TANG H, et al. A Method for Preparing Polytetrafluoroethylene: CN103172773A [P]. 2013-06-26.
[22] Wang Hanli, Zhang Lianhan, Wang Jun. Preparation Method of Polytetrafluoroethylene Resin: CN105542046A [P]. 2016-05-04. WANG H L, ZHANG L H, WANG J, et al. Preparation Method of Polytetrafluoroethylene Resin: CN105542046A [P]. 2016-05-04.
[23] Gurnani P, Perrier S. Controlled Radical Polymerization in Dispersed Systems for Biological Applications [J]. Progress in Polymer Science, 2020, 102: 101209.
[24] Ding Zhicheng. Emulsion Polymerization of Vinylidene Chloride and Acrylate and Its Performance Research [D]. Changchun: Changchun University of Technology, 2019. DING Z C. Synthesis and Properties of Emulsion Copolymerization of Vinylidene Chloride and Acrylate [D]. Changchun: Changchun University of Technology, 2019.
[25] Enokida T, Yamada O. Process for Producing Fluorinated Copolymer, Fluorinated Copolymer, Crosslinkable Composition Containing Same and Sealant: US6281312 [P]. 2001-08-28.
[26] Zhang Tingjian, Zhang Jianxin, Wang Zhongquan, et al. A Type of Polytetrafluoroethylene Resin and Its Method: CN106832072B [P]. 2019-05-17. ZHANG T J, ZHANG J X, WANG Z Q, et al. A Type of Polytetrafluoroethylene Resin and Its Method: CN106832072B [P]. 2019-05-17.
[27] Lazár M. Influence of the Solvent on the Polymerization Velocity of Trifluorochloroethylene [J]. Journal of Polymer Science, 1958, 29(120): 573-578.
[28] Yu Tao. Study on the Free Radical Polymerization Behavior of Ionic Liquids as Solvents [D]. Changchun: Changchun University of Technology, 2017. YU T. The Behaviors Investigation of Free Radical Polymerization with Ionic Liquids as Solvent [D]. Changchun: Changchun University of Technology, 2017.
[29] Harriman L W, Teumac F N. Process for Polymerizing Chlorotrifluoroethylene: US3244684 [P]. 1966-04-05.
[30] Rearick J S, Schaaf R P. Process for Polymerizing CF2=CFCl in Slurry Systems: US2742454A [P]. 1956-04-17.
[31] Chin H B, Chandrasekaran S. Copolymerization of Ethylene and Chlorotrifluoroethylene in an Aqueous Emulsion: US4482685 [P]. 1982-09-30.
[32] Scoggins L. Copolymerization of Chlorotrifluoroethylene and Ethylene Using a Redox Catalyst: US3767634 [P]. 1973-10-23.
[33] Kato K, Funaki A, Takakura T. Method for Producing a Fluorine-Containing Copolymer: US5663251 [P]. 1997-09-02.
[34] Wang Wengui. Synthesis and Properties of Ethylene/Trifluorochloroethylene Copolymers [D]. Shanghai: Tongji University, 2008. WANG W G. Synthesis and Properties of Ethylene/Trifluorochloroethylene Copolymers [D]. Shanghai: Tongji University, 2008.
[35] Gao Zihong, Zhang Wanli, Qin Sheng, et al. A New Structure Copolymer of Ethylene and Trifluorochloroethylene, Its Preparation Method and Application: CN104892811A [P]. 2015-09-09. GAO Z H, ZHANG W L, QIN S, et al. A New Structure Copolymer of Ethylene and Trifluorochloroethylene, Its Preparation Method and Application: CN104892811A [P]. 2015-09-09.
[36] Zhang Wanli, Sun Bin, Chen Ke, et al. A Melt Blown Ethylene-Trifluorochloroethylene Copolymer and Its Preparation Method: CN114349888A [P]. 2022-04-15. ZHANG W L, SUN B, CHEN K, et al. A Melt Blown Ethylene-Trifluorochloroethylene Copolymer and Its Preparation Method: CN114349888A [P]. 2022-04-15.
[37] Boschet F, Ameduri B. (Co)Polymers of Chlorotrifluoroethylene: Synthesis, Properties, and Applications [J]. Chemical Reviews, 2014, 114(2): 927-980.
[38] Ishigure K, Tabata Y, Oshima K. 19F Nuclear Magnetic Resonance Spectra of Tetrafluoroethylene-Propylene Copolymers [J]. Macromolecules, 1973, 6(4): 584-588.
[39] Ishigure K, Tabata Y, Oshima K. Nuclear Magnetic Resonance Spectra of a Isobutylene-Chlorotrifluoroethylene Copolymer [J]. Macromolecules, 1970, 3(1): 27-29.
[40] Thomas W M, O’Shaughnessy M T. Kinetics of Chlorotrifluoroethylene Polymerization [J]. Journal of Polymer Science, 1953, 11(5): 455-470.
[41] Reddy C K, Raju L Y, Srinivas P V, et al. Preparation and Characterization of Core-Shell Nanoparticles Containing Poly(Chlorotrifluoroethylene-co-Ethylvinylether) as Core [J]. Journal of Applied Polymer Science, 2011, 122(3): 1807-1814.
[42] Ameduri B. From Vinylidene Fluoride (VDF) to the Applications of VDF-Containing Polymers and Copolymers: Recent Developments and Future Trends [J]. Chemical Reviews, 2009, 109(12): 6632-6686.
[43] Feng Na, Yu Guojian, Li Wenshuang, et al. Effect of Rare Earth Compound Stabilizer on Polytrifluorochloroethylene Materials [J]. Plastics Science and Technology, 2014, 42(6): 109-112. FENG N, YU G J, LI W S, et al. Effect of Rare Earth Compound Stabilizer on Polytrifluorochloroethylene Materials [J]. Plastics Science and Technology, 2014, 42(6): 109-112.
[44] Wu Lei, Zhang Deshun, Hu Wei, et al. Polytetrafluoroethylene Modified by Monocyclic Carboxylate Nucleating Agent: CN104693649A [P]. 2015-06-10. WU L, ZHANG D S, HU W, et al. Polytetrafluoroethylene Modified by Monocyclic Carboxylate Nucleating Agent: CN104693649A [P]. 2015-06-10.
[45] Li Ji, Feng Na, Zhang Guixia, et al. Performance and Crystallization Behavior of PCTFE Toughened by Core-Shell ACR [J]. China Synthetic Resin and Plastics, 2015, 32(3): 40-43. LI J, FENG N, ZHANG G X, et al. Performance and Crystallization Behavior of PCTFE Toughened by Core-Shell ACR [J]. China Synthetic Resin and Plastics, 2015, 32(3): 40-43.
[46] Wei Changpei, Shi Tuo. Studies on Reinforced Polychlorotrifluoroethylene [J]. Organo-Fluorine Industry, 1995(1): 1-3. WEI C P, SHI T. Studies on Reinforced Polychlorotrifluoroethylene [J]. Organo-Fluorine Industry, 1995(1): 1-3.
[47] Wen Jialiang, Zhai Yingwen, Cui Yu, et al. Processing Technology of CF Reinforced Polychlorotrifluoroethylene Composite [J]. Eng Plastics Appl, 2018, 46(1): 58-61. WEN J L, ZHAI Y W, CUI Y, et al. Processing Technology of CF Reinforced Polychlorotrifluoroethylene Composite [J]. Eng Plastics Appl, 2018, 46(1): 58-61.
[48] Mabry J M, Vij A, Viers B D, et al. Hydrophobic Silsesquioxane Nanoparticles and Nanocomposite Surfaces: An Overview of the Synthesis and Properties of Fluorinated Polyhedral Oligomeric Silsequioxanes (POSS) and Fluorinated POSS Nanocomposites [J]. Science and Technology of Silicones and Silicone-Modified Materials, 2007, 964: 290-300.
[49] Siergiej R W, Danielson N D. Phenyl-Modified Kel-F as a Column Packing for Liquid Chromatography [J]. Analytical Chemistry, 2002, 55(1): 17-22.
[50] Okubo M, Tahara M, Saeki N, et al. Surface Modification of Fluorocarbon Polymer Films for Improved Adhesion Using Atmospheric-Pressure Nonthermal Plasma Graft-Polymerization [J]. Thin Solid Films, 2007, 516(19): 6592-6597.
[51] Ursino C, Simone S, Donato L, et al. ECTFE Membranes Produced by Non-Toxic Diluents for Organic Solvent Filtration Separation [J]. RSC Advances, 2016, 6(84): 81001-81012.
[52] Falbo F, Santoro S, Galiano F, et al. Organic/Organic Mixture Separation by Using Novel ECTFE Polymeric Pervaporation Membranes [J]. Polymer, 2016, 98: 110-117.
This article is copyrighted by the Editorial Department of “Ecological Industry Science and Phosphorus Fluorine Engineering”. For any reproduction or citation, please indicate that it is reproduced or cited from “Ecological Industry Science and Phosphorus Fluorine Engineering”.
Contact Information for the Editorial Department of “Ecological Industry Science and Phosphorus Fluorine Engineering”:
Tel: 0371-6388 7309 6778 1991
E-mail: [email protected]
Welcome to Subscribe/Submit/Advertise
“Ecological Industry Science and Phosphorus Fluorine Engineering” welcomes subscriptions
“Ecological Industry Science and Phosphorus Fluorine Engineering” Call for Papers
“Ecological Industry Science and Phosphorus Fluorine Engineering” is eager to recruit advertising clients
The only online submission website:
https://lfyf.cbpt.cnki.net/
