First Author: Xue Zhixin
Corresponding Author: Xu Guiyin
Affiliation: Donghua University
Summary of Results
The low cost, low temperature, and fast charging performance of sodium-ion batteries (SIBs) have attracted widespread attention. The membrane is one of the essential key components of the battery, affecting the interface structure and internal resistance of the battery, as well as characteristics such as capacity, cycling, and safety performance. Therefore, the membrane must have excellent wettability, mechanical properties, pore size distribution, ionic conductivity, and thermal stability. Currently, research on sodium-ion battery membranes mainly focuses on the modification of commercial PP and PE membranes and other new types of membranes, which have excellent chemical stability and cycling stability. These membranes have good electrochemical stability and high mechanical strength, but their stability at high temperatures is relatively poor, and there is a problem with poor electrolyte wettability. Therefore, in sodium-ion batteries, the membrane is one of the challenges, and there are still significant challenges in practical applications.
Introduction
Lithium-ion batteries and sodium-ion batteries emerged in the late 1970s. Lithium-ion batteries have developed rapidly due to their electrochemical performance and currently dominate the market. Lithium-ion batteries occupy a dominant market share in many application scenarios, such as smartphones, electric vehicles, solar energy storage, and aerospace-related manufacturing. Meanwhile, the export proportion of lithium batteries is also increasing year by year (Figure 1a-b). However, this widespread use has led to a shortage of lithium, and costs have increased accordingly. Statistics show that global lithium resources are mainly concentrated in South America and Australia, while China’s lithium resources account for only 6% of global reserves (Figure 1c). The shortage of lithium will restrict its sustainable development.
Sodium has similar physical and chemical properties to lithium, but its abundance on Earth is 440 times that of lithium (Figure 1d). Sodium resources are widely distributed and easily extracted, and compared to lithium batteries, the cost of large-scale commercialization of sodium batteries is significantly lower. In recent years, with the development of the energy vehicle industry in our country and the increase in market demand, the research and development of SIBs have also made steady progress. SIBs outperform lithium batteries in low-temperature performance, fast charging performance, and safety performance, but still have some shortcomings. The low energy density, low cycling stability, and rapid capacity decay of SIBs limit their potential applications.
The structure of sodium-ion batteries is similar to that of lithium-ion batteries, mainly consisting of key materials such as positive electrode materials, negative electrode materials, electrolytes, and membranes. Sodium ions oscillate back and forth between the positive and negative electrodes, similar to a rocking chair. During charging, sodium ions are extracted from the positive electrode, pass through the electrolyte and membrane, and eventually embed in the negative electrode. Electrons flow through the external circuit from the negative electrode to the positive electrode to balance the charge, and the discharging process is the opposite of this (Figure 2). As an important component of the internal structure, the membrane can isolate the positive and negative electrodes, store the electrolyte, and facilitate the free transport of sodium ions, significantly impacting the electrochemical performance of the battery. The ideal membrane for high-energy-density sodium batteries needs to possess excellent chemical stability to have high corrosion resistance to organic electrolytes; high mechanical strength to prevent sodium dendrites from penetrating the membrane, causing internal short circuits; high wettability to expand the contact area between the membrane and the electrolyte, thereby improving ionic conductivity, enhancing the battery’s charge and discharge performance and capacity; appropriate pore size to promote the formation of uniform sodium ion channels, thus improving ion transport efficiency; good thermal stability to maintain the integrity of the membrane, continue to isolate the positive and negative electrodes, and prevent short circuits; thin membranes can provide more space for the active materials of the positive and negative electrodes, thus improving the energy density of the battery; low production costs allow sodium-ion batteries to be widely promoted and sustainably developed in the market.
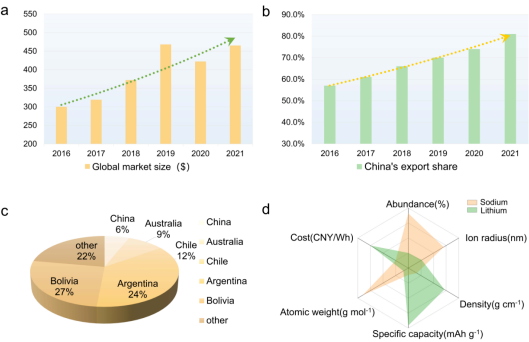
Figure 1: (a-b) Global lithium battery market size and China’s lithium battery export volume; (c) Global lithium resource distribution; (d) Comparison of sodium and lithium properties.
Figure 2. Structure of sodium-ion batteries (left) and performance requirements of membranes (right).
Currently, the main materials for sodium-ion battery membranes are polyethylene, polypropylene membranes, and their composite membranes. Polyolefin membranes are low-cost, have strong mechanical properties, and good chemical stability, but their thermal stability and electrolyte compatibility still have issues. Glass fiber has high porosity, excellent thermal stability, and high ionic conductivity, and is widely used as a membrane for sodium-ion batteries in laboratories, but still has problems such as large thickness and poor mechanical properties (Figure 3). To avoid affecting the electrochemical performance of sodium batteries while having high thermal stability, researchers have improved the thermal stability of the membranes by coating them with inorganic ceramic powders or polar polymers with good thermal stability, thereby effectively enhancing the battery’s safety, high-power fast charging, and discharging performance. However, this may lead to a reduction in pore size and an increase in membrane thickness, negatively impacting battery performance. Additionally, cellulose-based materials are widely available, have high wettability, good thermal stability, biocompatibility, and environmental friendliness, meeting the needs for sustainable development in the battery field. However, cellulose-based membranes are still in the laboratory research stage and require further exploration for commercialization. Furthermore, using interlayers that promote interfacial ionic transport, designing composite membranes that prevent sodium dendrite growth, or using inorganic solid electrolytes with low elastic modulus are also feasible.
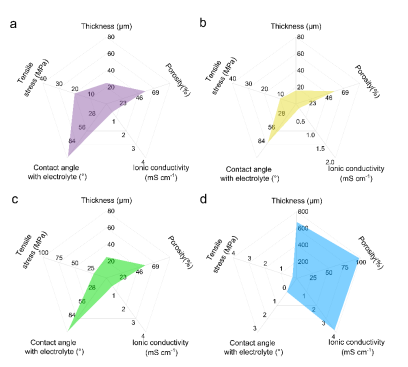
Lithium-sulfur battery mechanism reinterpreted! Duan Xiangfeng’s significant Nature today!
2024-02-01
Xue Dongfeng et al. Next Materials: Key degrees of freedom research for next-generation quantum functional materials
2024-02-01
School-enterprise cooperation, latest Nature on solar cells!
2024-02-01
Tianjin University Huang Chengde team MTE review: Modification strategies for magnesium-ion battery positive electrode materials
2024-02-01
Beijing University Huang Jiaqi & Yuan Hong Adv. Funct. Mater.: In-situ polymerization integrated ultra-thin electrolyte/positive electrode design for high energy density solid-state lithium batteries
2024-02-01
Screening zinc alloy anodes with hydrogen evolution suppression capability
2024-02-01
Northeast Normal University Liu Bingqiu / Li Lu / Wang Chunang team ESM: High-entropy charge compensation mechanism inducing manganese charge redistribution in aqueous potassium-ion batteries
2024-02-01
Jiangsu University of Science and Technology Shi Weilong / Guo Feng team JCIS: Plasma coupling enhanced photothermal composite photocatalysts for near-infrared photochemical hydrogen production
2024-02-01
Advancing industrialization: How stacking pressure affects & enhances electrochemical performance of all-solid-state batteries
2024-01-31
Peking University Pang Quanquan / Wu Limai Liqiang Nature Communications: New progress in 85°C fast charging molten salt aluminum-sulfur batteries
2024-01-31