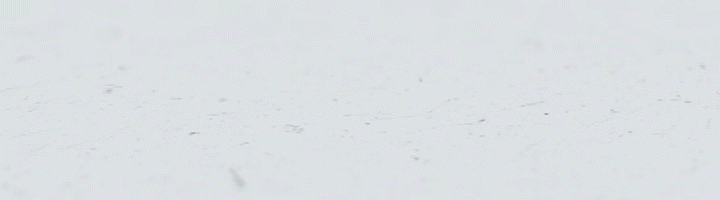
According to the report released by VoxelMatters on the 3D printing market for consumer goods, the number of 3D printed consumer parts reached nearly 37 million in 2023, a 23% increase compared to 2022. 3D printing technology is fundamentally transforming the manufacturing methods in the consumer goods industry, opening up new growth paths.
Xinjinghe’s subsidiary, Leiming Laser, has developed the LiM-X400M device to meet the efficient production needs of users in the consumer goods industry, primarily providing integrated metal 3D printing solutions for mold manufacturing, 3C electronics, medical, education, cultural and creative fields. Based on the efficient and stable production of the device, we have further upgraded the LiM-X400M series devices after comprehensive user feedback and multiple optimization tests.
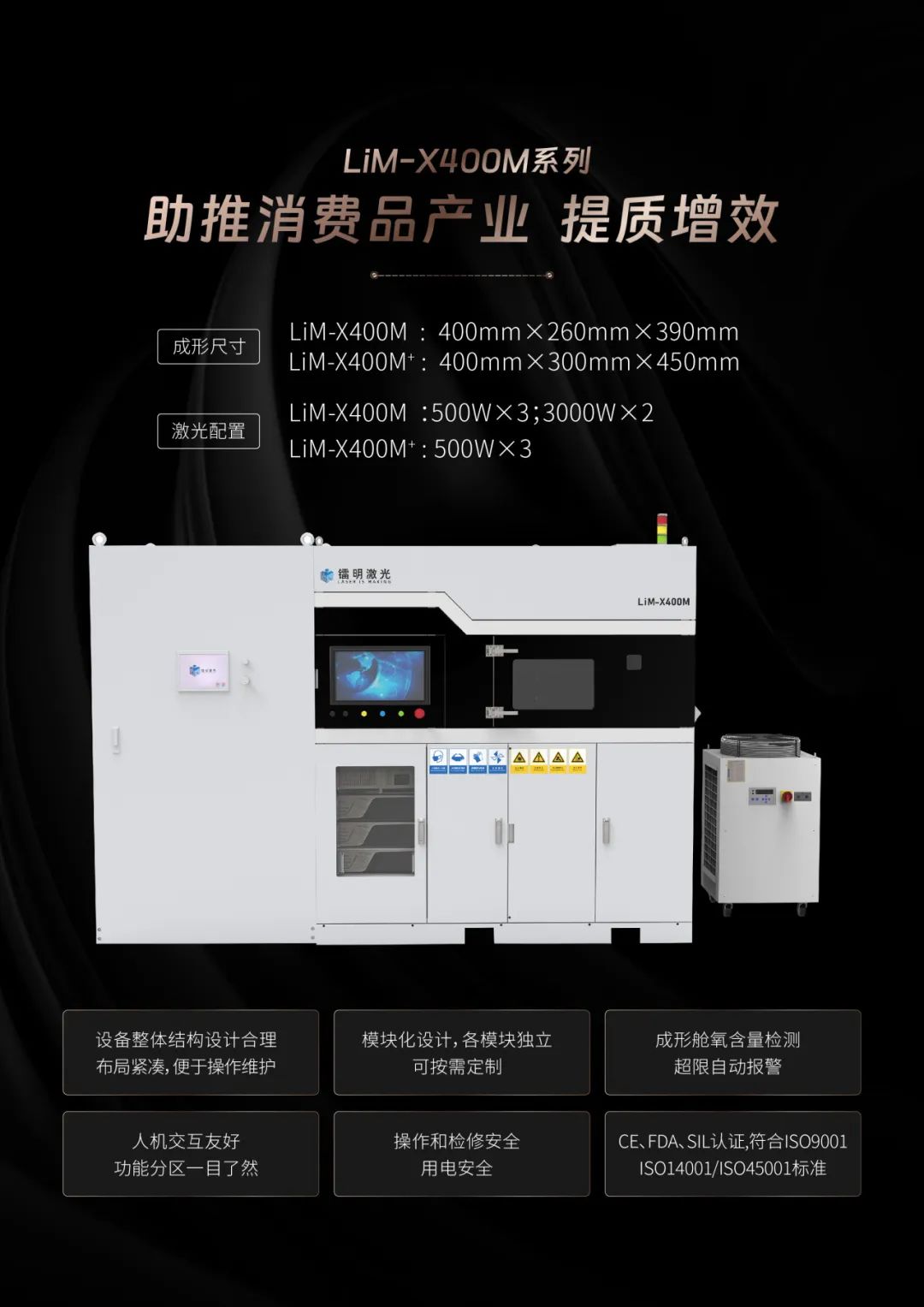
On one hand, the LiM-X400M device’s laser configuration has been updated, allowing users to choose two 3000W ultra-high-power lasers, achieving a large layer thickness printing of 0.4mm, further enhancing production efficiency. On the other hand, we have launched the LiM-X400M+ device, with an upgraded forming size of 400mm×300mm×450mm, providing a larger forming space to meet more users’ demands for the production of complex structural parts and mass production.
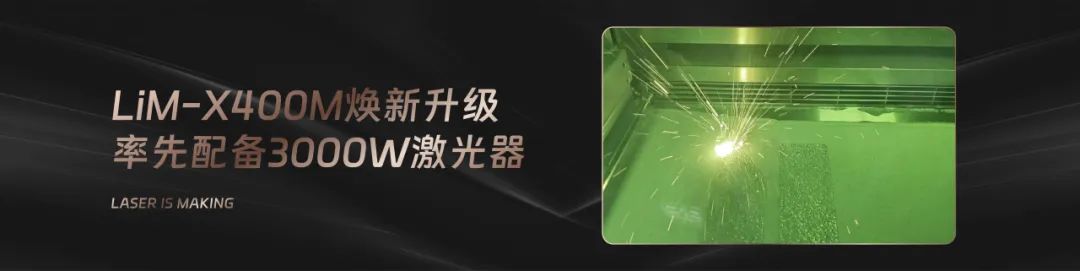
Multiple Layer Thickness, One Print, Higher Efficiency
The LiM-X400M series devices are equipped with self-developed software, enabling the completion of parts with multiple layer thicknesses in one print, such as flexibly adjusting a 0.04mm layer thickness to 0.02mm, saving downtime for intermediate operations and effectively improving part forming efficiency.
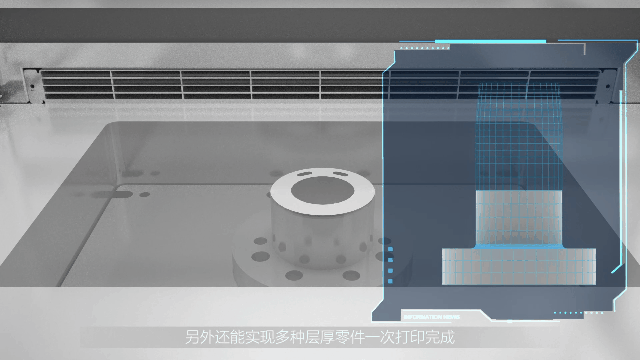
Substrate Temperature, Set Separately, Superior Forming
The slicing end provides a temperature control function, allowing for different substrate temperatures to be set for different printing heights and stages (substrate preheating temperature range is 20°C~350°C), ensuring smooth printing while effectively improving stress and deformation caused by product structural features, thus ensuring forming quality.
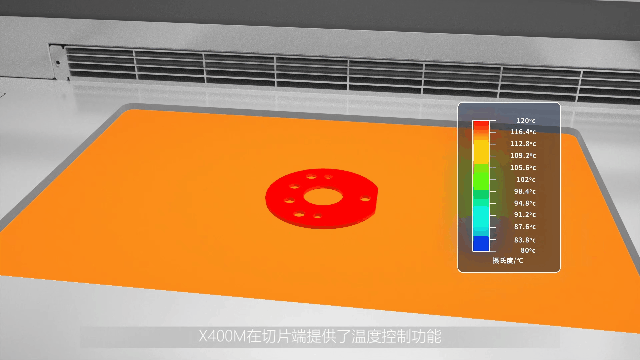
Efficient Prediction, Avoid Problems, Smarter Management
For the most common overflow powder barrel full alarm during printing, predictive maintenance is provided, allowing users to predict the cleaning time of the overflow powder barrel through the powder amount curve, avoiding unexpected downtime. Sensor data and log files during the printing process will be recorded by printing job, supporting production quality management.
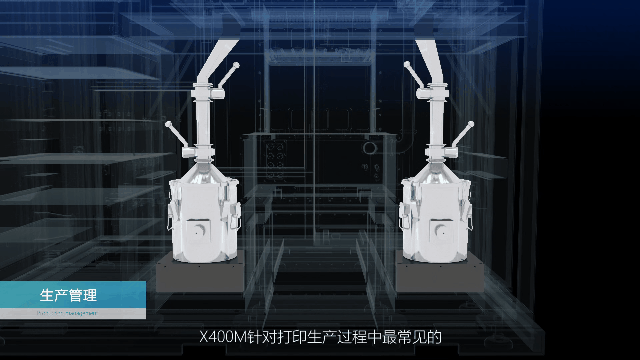
Process Detection, Real-time Monitoring, More Consistent Quality
A configurable melt pool monitoring system allows for real-time monitoring, analysis, and evaluation of the melt pool information of the laser scanning melting device, achieving defect detection and process quality traceability in additive manufacturing. On one hand, it can detect whether the melt pool is unstable in real-time, and on the other hand, it can serve as a quantitative pointer for process strategy optimization to ensure part quality and consistency.
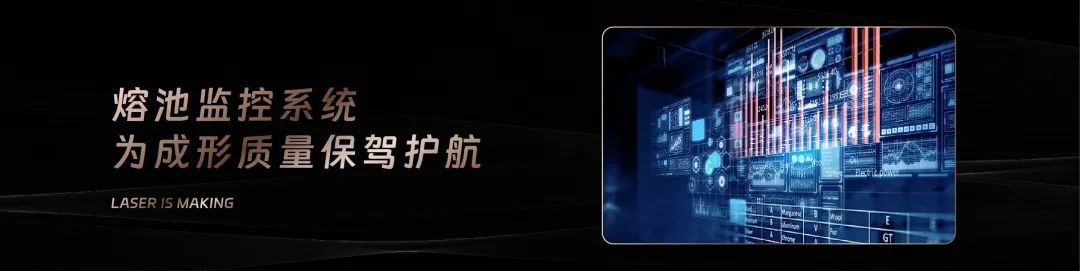
Since the release of the LiM-X400M series devices, their stability, forming quality, and production efficiency have been well recognized by users. In the mold manufacturing field, they have significantly improved mold performance and production efficiency; in the 3C electronics field, they efficiently meet the new product trial and small batch production needs, injecting vitality into the industry’s continuous development.
Shaped Cooling Waterway Molds
The injection molding process involves injecting high-temperature molten plastic into a lower temperature mold under high pressure, cooling and solidifying to obtain the desired finished product. Mold temperature control is a crucial part of the injection molding process, typically achieved using a cooling waterway system for rapid and uniform cooling. The design of the cooling waterway layout directly affects the quality and production cycle of injection molded products.
In traditional processing methods, the mold cooling waterway can only form cylindrical straight holes, which cannot closely fit the surface of the injection molded part to achieve the best mold temperature state, resulting in uneven cooling, low efficiency, and impacting the quality and production efficiency of the finished product.
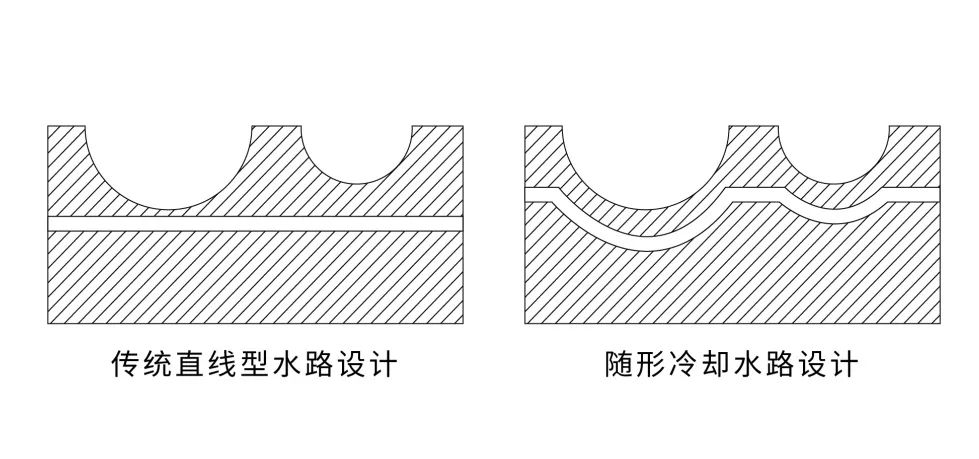
Comparison of Traditional Waterway and Shaped Cooling Waterway
Metal 3D printing technology can break through traditional processing limitations, producing molds with complex shaped cooling waterway systems: within a reasonable range, the shape and cross-section of the cooling waterway can be freely designed, closely following the contour changes of the mold cavity surface, achieving faster and more uniform cooling effects, thereby improving the quality of injection molded parts, shortening cooling time, and increasing production efficiency.
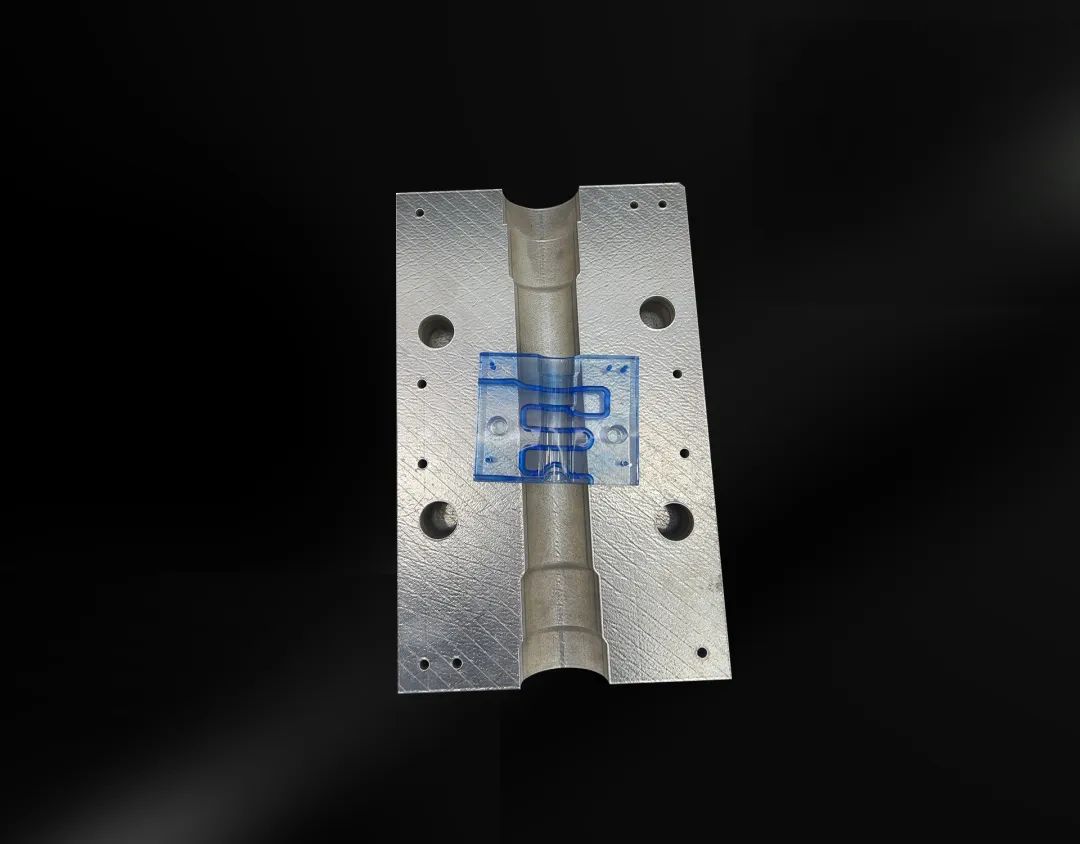
Mold Blank and Internal Waterway Display
Mold Size: 344mm×204mm×85mm
Forming Material: Stainless Steel
This mold blank is produced by LiM-X400M series device large-format printing, with rich internal flow channels and complex structures, effectively reducing production difficulty and significantly improving production efficiency.
Grafted Waterway Molds
In the practical application of mold manufacturing, various factors such as technology, cost, and efficiency are often integrated, using a combination of additive manufacturing and traditional subtractive processing to produce special structural components, known as graft printing. This method is mainly used to separately form the shaped cooling parts of mold inserts on the cutting surfaces of traditionally machined parts, which helps reduce internal stress, avoid the risk of deformation and cracking, and achieve the production of complex waterway molds at lower cost and higher efficiency.
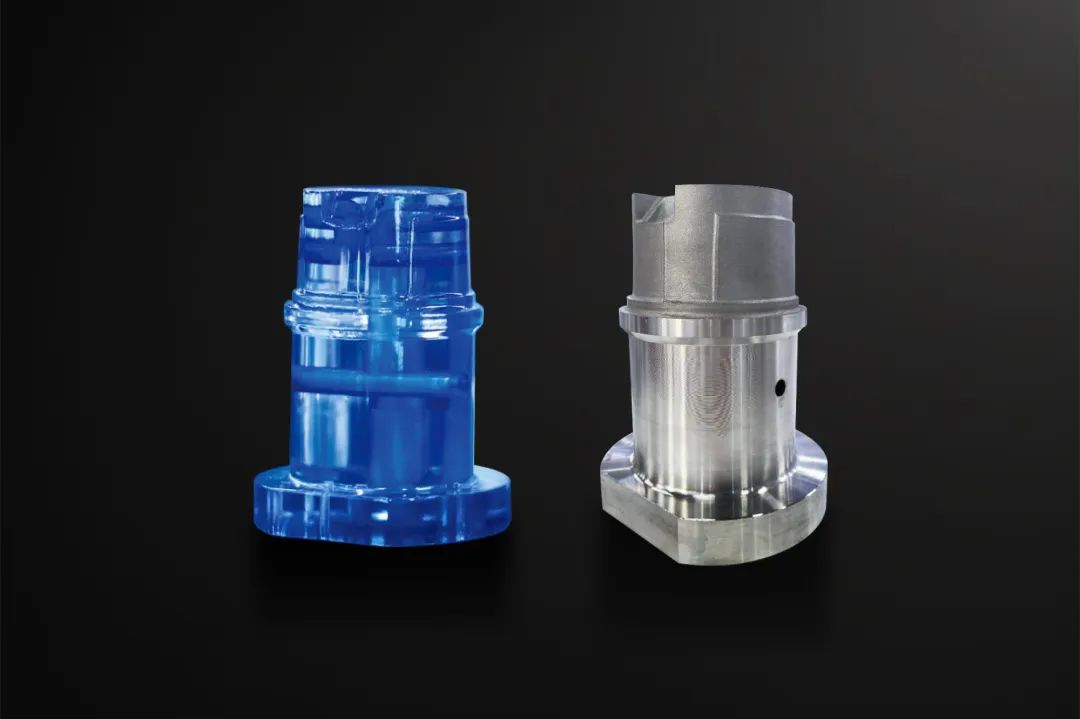
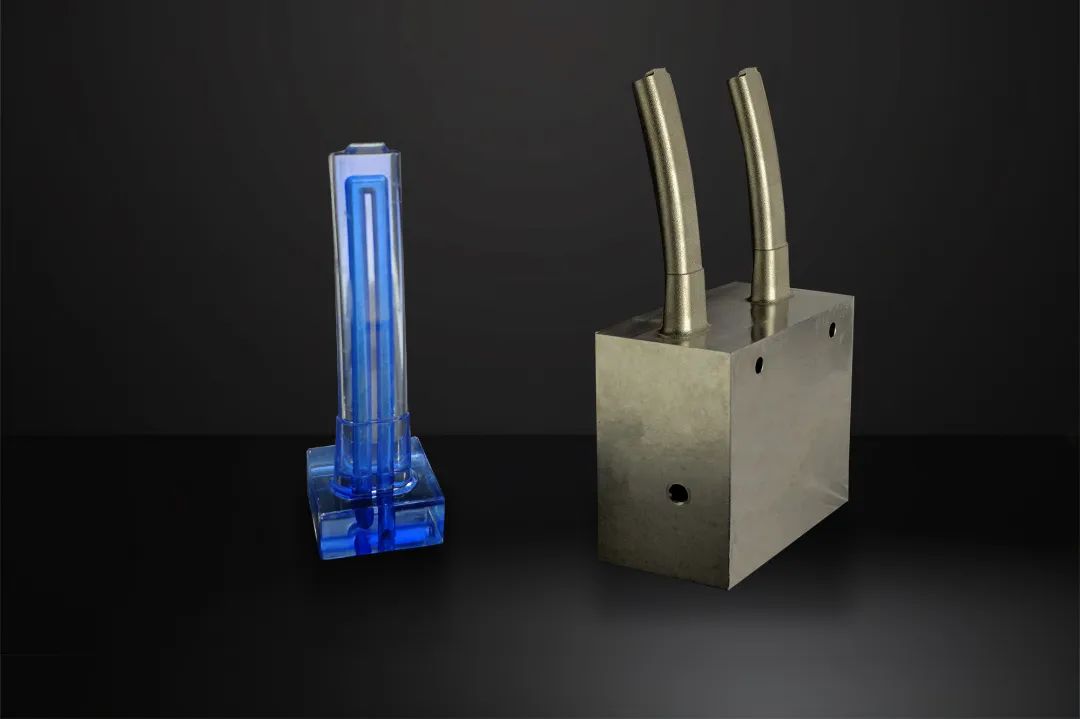
Grafted Waterway Molds and Internal Flow Channel Display
However, during the forming process, it is necessary to effectively fuse different components and different metal materials, while efficiently and accurately calculating the positional deviation of the shaped cooling parts and grafted bases, which requires high technical demands. Leiming Laser’s automatic grafting technology, based on “machine vision,” completes high-precision calibration for grafting formation, with positioning accuracy reaching ±0.1mm, achieving stable and efficient graft printing.
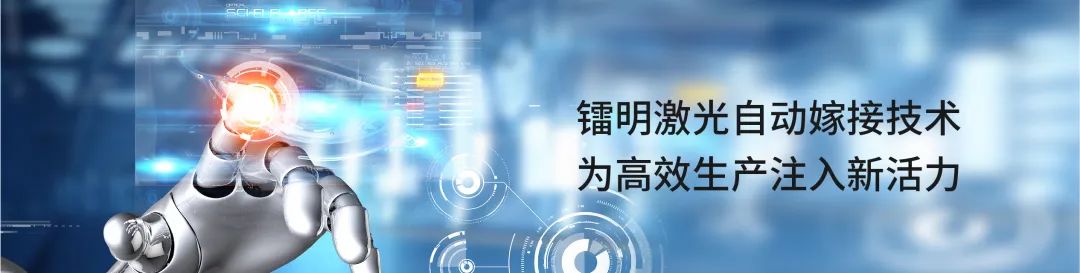
Small Scale Batch Production Applications
In the 3C electronics field, Leiming Laser’s LiM-X400M series devices also achieve batch production of precision components such as watch frames, hinges, and mobile phone frames, thanks to their high quality, high efficiency, and high precision forming capabilities.
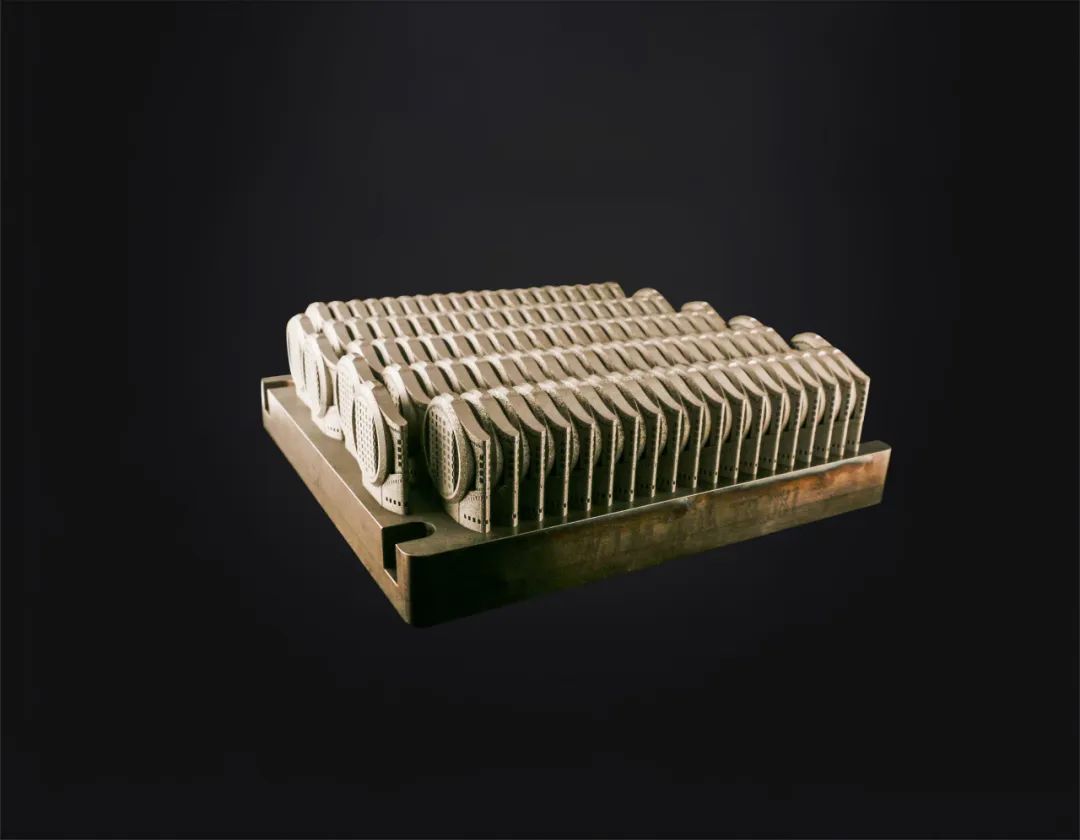
Full Plate Printing of Titanium Alloy Watch Frames
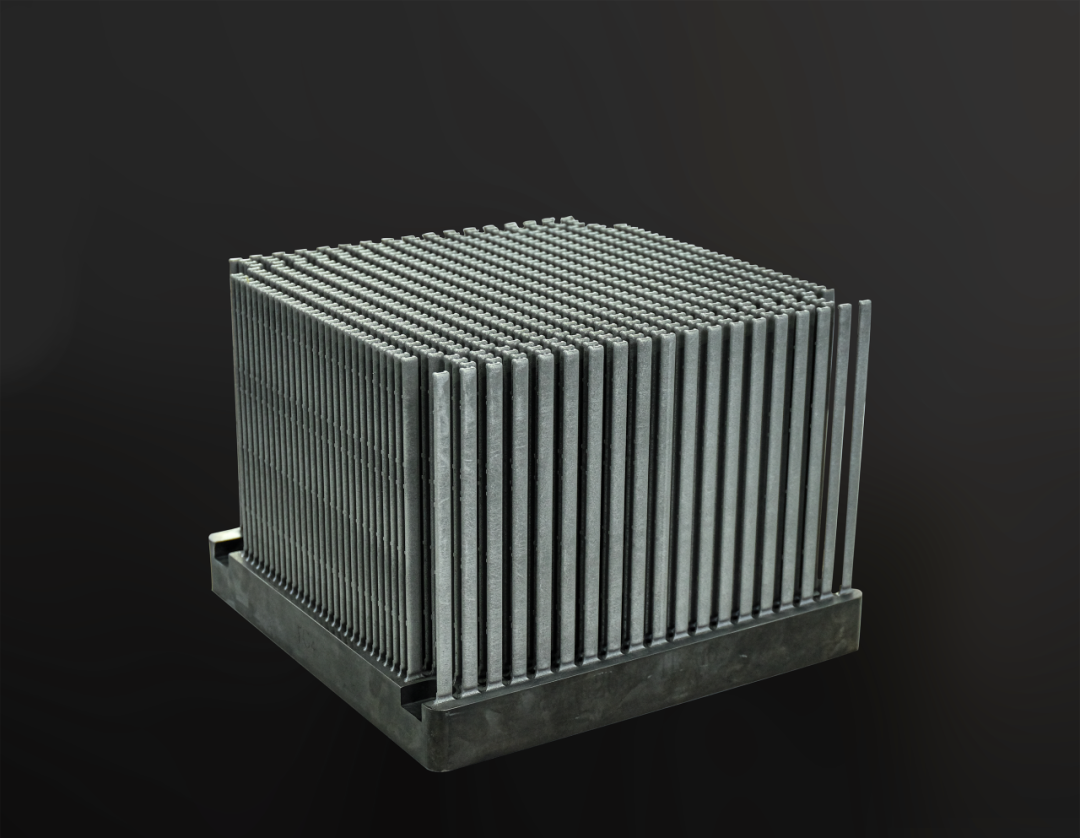
Full Plate Printing of Mobile Phone Hinges
Innovation is ongoing and unceasing. Xinjinghe always adheres to application-driven and market-oriented principles, focusing on the demand characteristics of various fields, exploring rich application scenarios, and laying out future industries in advance, providing more users with high-quality and efficient integrated metal 3D printing solutions to assist users in transformation and upgrading.