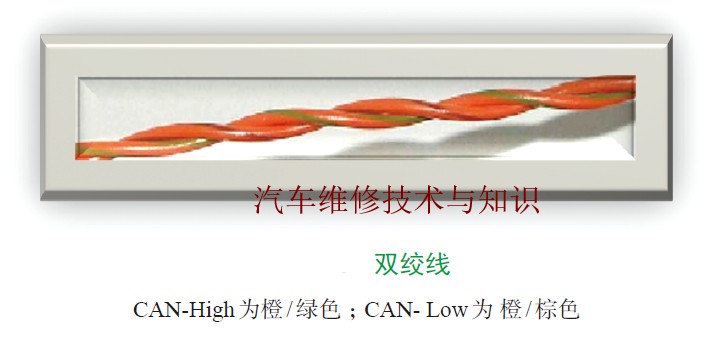
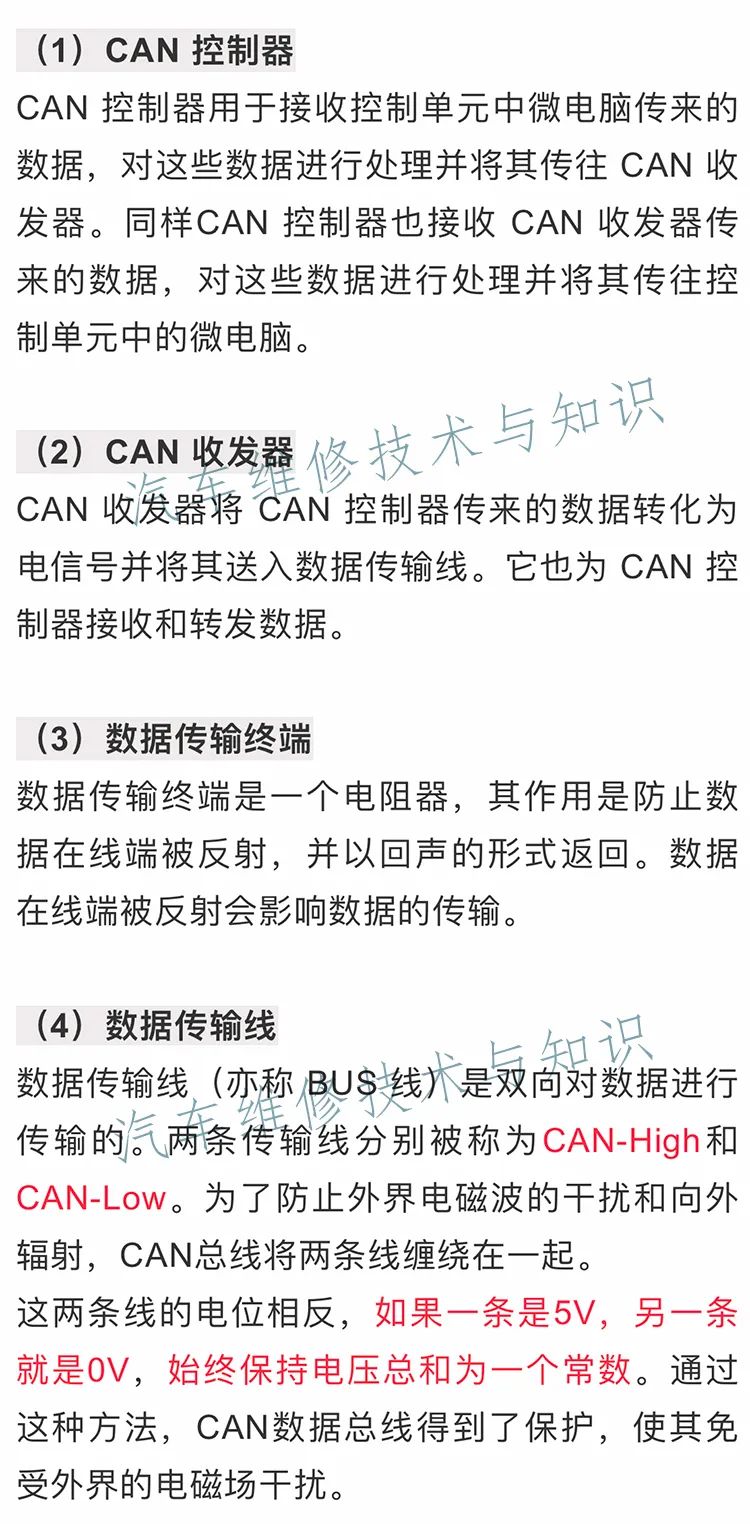
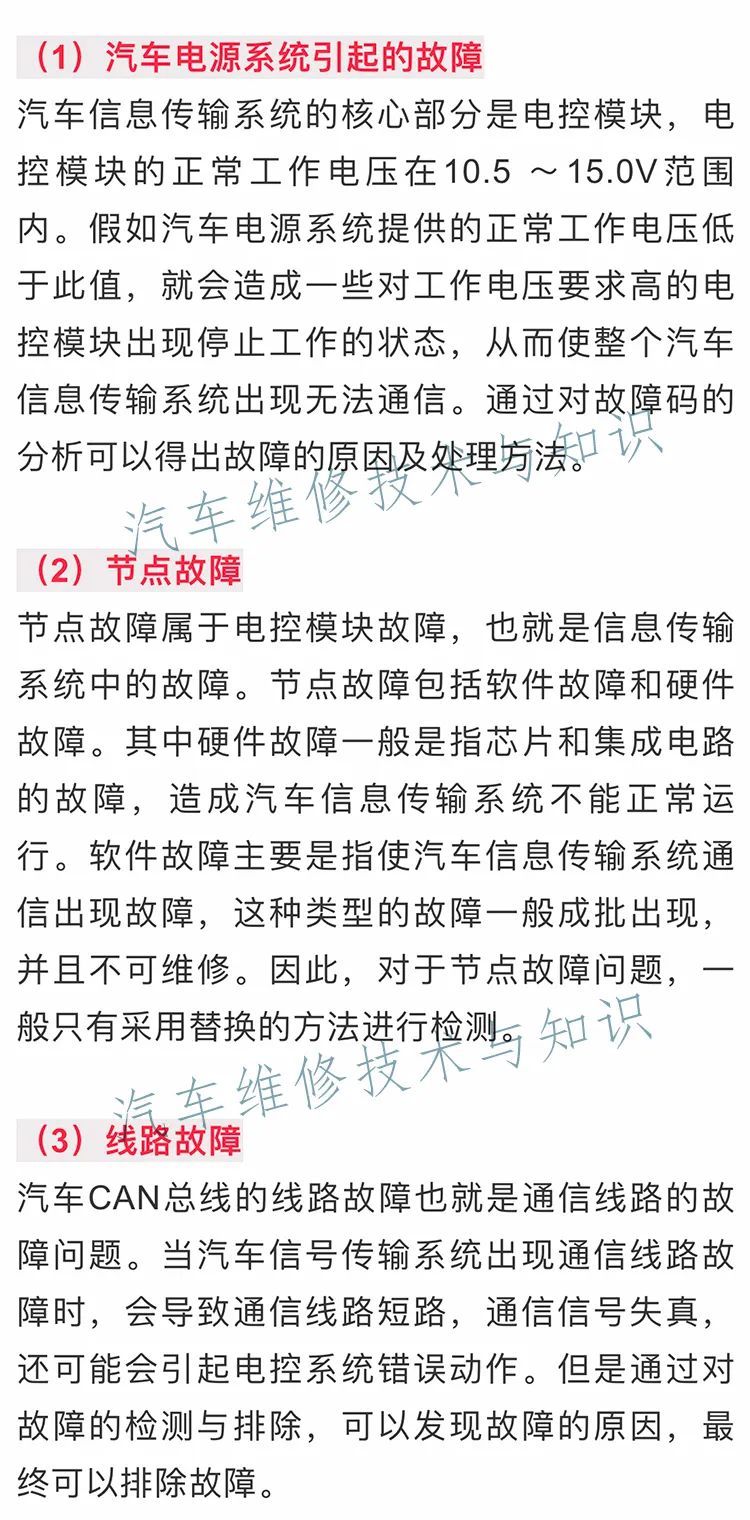
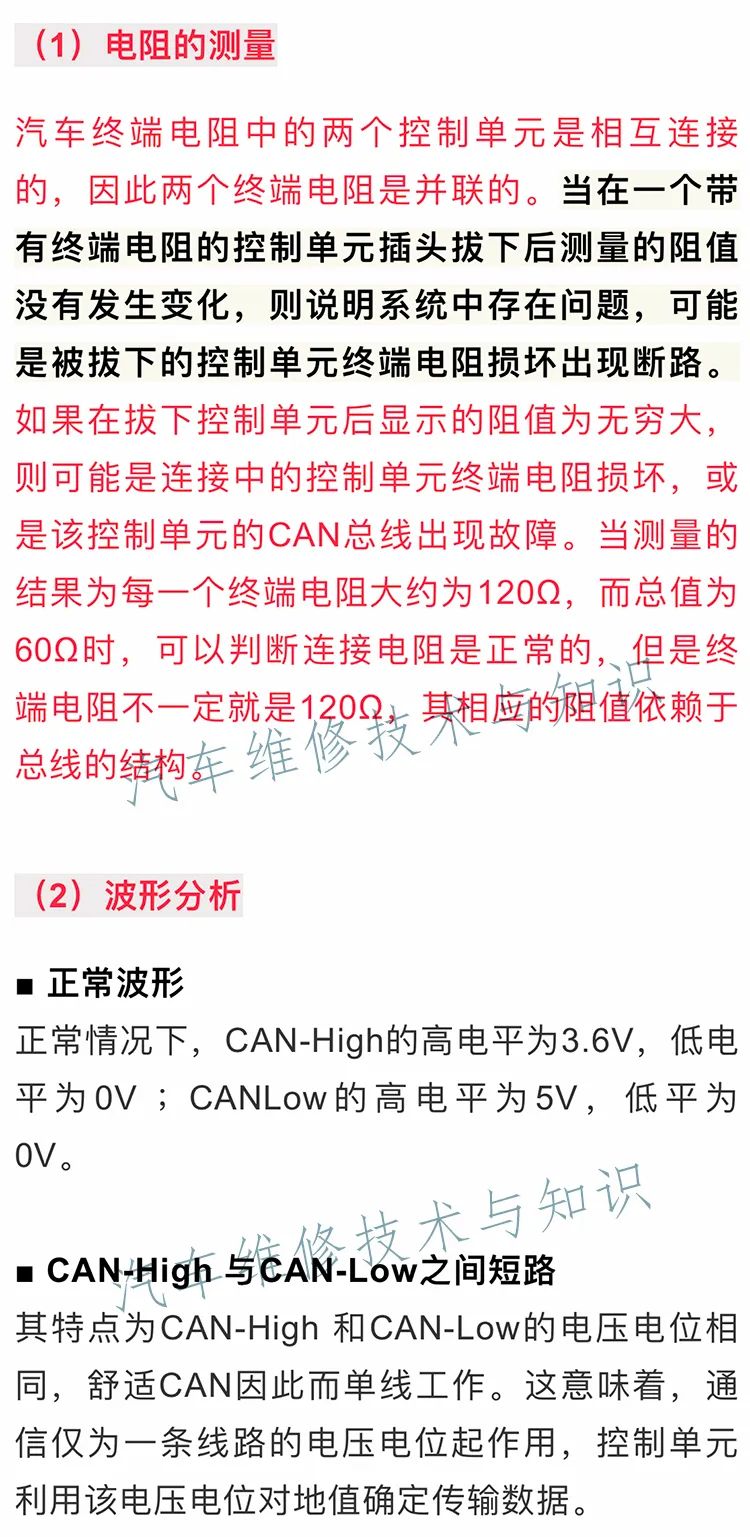
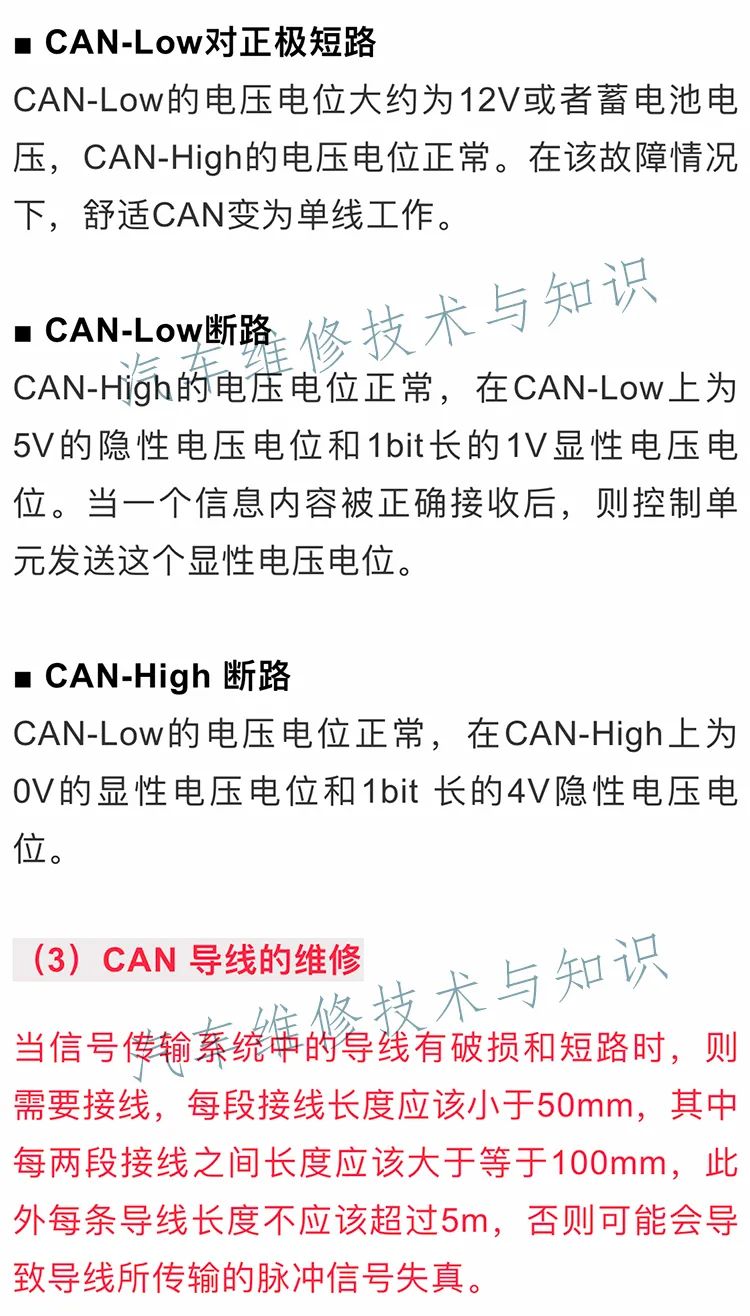


-
Steps, Methods, and Precautions for CAN Bus Fault Diagnosis
-
Common Maintenance Methods for CAN Bus (Must-Have Tips)
-
Common Faults and Diagnosis Methods of FlexRay Bus Systems
-
Types of Automotive Buses, Fault Characteristics & Case Analysis
-
[Typical Cases] Automotive Bus Fault Repair Cases (3 cases)
-
Case Analysis of Air Conditioning Cooling Faults Caused by Automotive Buses (2 cases)
