
In this rapidly changing technological era, the safety and efficiency of the mining industry have always been a focal point of concern. Imagine how transport vehicles can navigate freely in the narrow and deep mine tunnels, avoiding collisions with obstacles and tunnel walls. This not only tests the driver’s skills but also relies on advanced environmental perception technology. Today, let us reveal how the authors from Inner Mongolia University of Technology’s School of Mechanical Engineering applied sensor fusion technology to empower mine transport vehicles with the superpower of “seeing in all directions” through their paper published in the journal Metal Mine.
Challenges and Opportunities in Mine Safety
The mine, a treasure trove of rich resources, presents numerous challenges during the extraction process. The mine environment is complex and variable, with dim lighting and dust everywhere; drivers can easily become fatigued during long hours of work, and their visibility can be severely hindered. These factors significantly increase the risk of safety accidents involving mine transport vehicles. Statistics show that the casualties and property losses from mine transport accidents each year are alarming. Therefore, improving the environmental perception capabilities of mine transport vehicles to ensure safe driving has become a pressing issue in mining technology.
Limitations of Single Sensors
Sensors play a crucial role in environmental perception. However, a single sensor often falls short in the complex mine environment. For instance, while LiDAR has high detection accuracy and is unaffected by sudden changes in light, it can experience data drift in close-range detection; ultrasonic radar can compensate for close-range blind spots but has limited detection range. This means that relying solely on one type of sensor would greatly diminish the environmental perception capability of mine transport vehicles.
The Rise of Sensor Fusion Technology
To overcome the limitations of single sensors, researchers proposed sensor fusion technology. In simple terms, sensor fusion integrates information collected from multiple sensors to achieve a more comprehensive and accurate environmental perception result. In the field of mine transport vehicles, the fusion of LiDAR and ultrasonic radar has become a research hotspot. LiDAR provides high-precision long-range detection, while ultrasonic radar compensates for close-range blind spots. Together, they enhance the vehicle’s environmental perception capability.
Innovative Path of Researchers
This research team is a leader in this field. They proposed a state estimation algorithm based on the fusion of LiDAR and ultrasonic radar to address the complexity of the mine environment. This algorithm is designed based on the improved Iterative Extended Kalman Filter (IEKF), fully utilizing the advantages of both sensors to achieve precise perception of the environment surrounding mine transport vehicles.
IEKF Algorithm: Enhancing Data Precision
The IEKF algorithm is an advanced data fusion technology that can optimally estimate the state of dynamic systems in the presence of uncertainty. In the algorithm designed by the researchers, ultrasonic radar data is used as a prior state estimate, while LiDAR data is used to correct and update the prior state. Through this iterative process, the algorithm can gradually approach the true environmental state, resulting in more accurate perception outcomes.
IEKF Algorithm Prediction and Correction Update Process
The researchers stated that compared to the traditional EKF algorithm, the IEKF algorithm has better approximation effects in dealing with nonlinear problems, significantly improving estimation accuracy. Additionally, they validated the algorithm’s effectiveness through joint simulation with PreScan and Simulink. The simulation results indicate that the algorithm can accurately detect the positional relationship between mine transport vehicles and obstacles in the mine environment, reducing the mean absolute error of detection distance and effectively solving the data drift issue of LiDAR in close-range detection compared to single sensor detection results.
Field Testing: Impressive Results
To further validate the algorithm’s practical effectiveness, the researchers conducted field tests in a mine environment.They selected a mine shuttle as the test subject, which primarily functions to load coal from continuous miners and transport it to the feeder crusher for unloading. During the testing process, the vehicle traveled along a predetermined route, and the researchers monitored the distance between the vehicle and obstacles or tunnel walls in real-time using the sensor fusion algorithm.
Mine Transport Vehicle Operating Route
Test results showed that when the vehicle was traveling straight, both the ultrasonic radar and LiDAR did not detect the tunnel wall, and the output of the fusion result was defaulted to 0. When the vehicle began to turn, LiDAR was the first to detect the tunnel wall, outputting the fusion result based on LiDAR’s detection. As the vehicle continued to move, when the distance between the vehicle and the tunnel wall was less than the detection range of the ultrasonic radar, both sensors detected the target, outputting the result processed by the fusion algorithm.Throughout the testing process, the sensor fusion algorithm accurately reflected the distance relationship between the vehicle and obstacles or tunnel walls, with detection accuracy far exceeding that of a single sensor.
Data Speaks: Accurate and Reliable
Data is the strongest proof. The researchers conducted a comparative analysis of the detection results from the sensor fusion algorithm and the single sensor. The results showed that the average absolute error of the sensor fusion algorithm was only 0.04547 meters, significantly lower than LiDAR’s 0.14561 meters and ultrasonic radar’s 0.05690 meters. In close-range detection, LiDAR is prone to data drift, with an average absolute error reaching as high as 0.61321 meters. In contrast, the sensor fusion algorithm effectively avoids this issue, with an average absolute error of only 0.04706 meters in close-range drift. These data fully demonstrate the superior performance of the sensor fusion algorithm in mine environmental perception.
Comparison of Various Sensors Detecting Distance to Tunnel (Path 1)
Error Analysis of Different Sensor Results
Smart Mining:Mine Safety Is Not a Dream
The successful application of sensor fusion technology provides a strong guarantee for the safe operation of mine transport vehicles. By monitoring the distance relationships between vehicles and obstacles or tunnel walls in real-time, drivers can more accurately grasp changes in the vehicle’s surrounding environment, allowing them to take evasive measures in a timely manner to avoid safety accidents. Furthermore, this technology can also be combined with mine autonomous driving systems to achieve unmanned driving and intelligent scheduling of mine transport vehicles, further improving the efficiency and safety of mining operations.
With the continuous advancement of technology and the expanding application scenarios, the application prospects of sensor fusion technology in the mining field will be even broader. In the future, we can foresee that smart mining will no longer be an unattainable dream. By comprehensively utilizing advanced technologies such as the Internet of Things, big data, and artificial intelligence, mining operations will achieve comprehensive intelligent and automated management. Transport vehicles will be able to navigate autonomously and intelligently avoid obstacles; mining equipment will be remotely monitored and operated accurately; safety management will provide real-time warnings and rapid responses. All of this will greatly enhance the efficiency and safety of mining operations, contributing to the sustainable utilization of mineral resources.
↓ Ask “Super Miner I-Miner” ↓
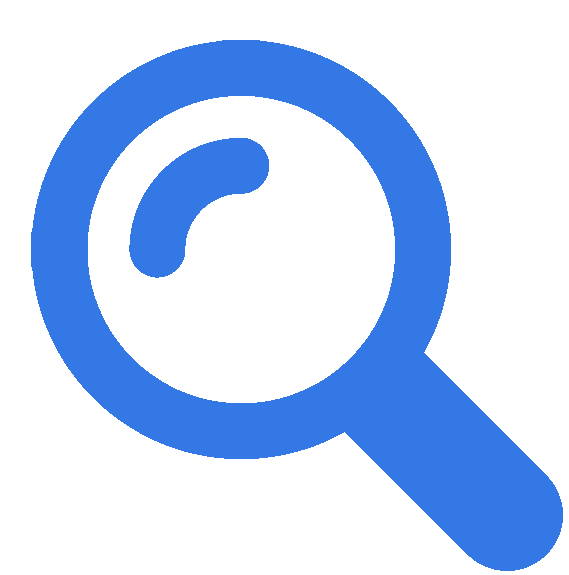
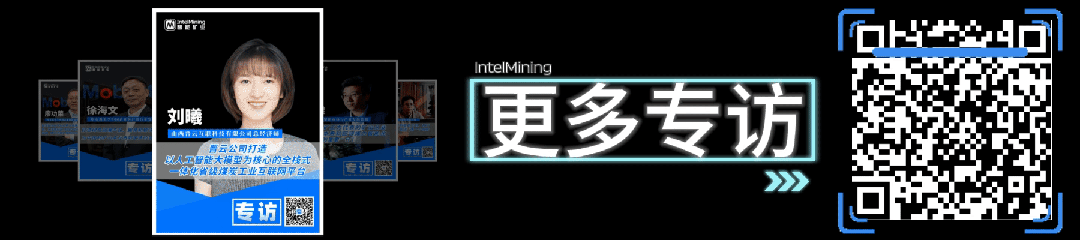
@Creating a Comprehensive Technology Service Platform for Mining www.intelmining2018.com
❖ Disclaimer: The content is sourced from public channels such as the internet and WeChat official accounts. The copyright of reprinted articles belongs to the original authors or institutions. Reproduction is for reference and communication purposes only and not for commercial use. If there is any infringement, please contact us for removal.
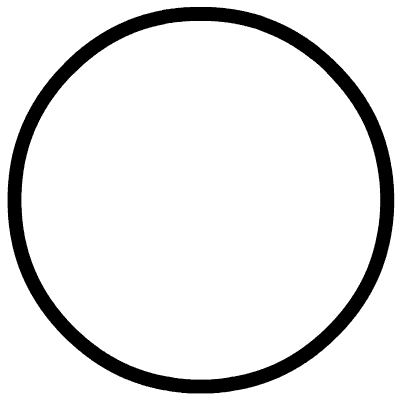