Click Blue Text Reply 「1」 to receive six industry gift packages
(Big Data, Cloud Computing, Artificial Intelligence, Blockchain…)
——–
Author / Song Pengfei · Editor / Jenny Robin
Source / Broadband Capital
The Japanese Ministry of Internal Affairs and Communications recently released a popular short film “Connecting the World After 5G”. In just over three minutes, the film intensively presents application scenarios such as ultra-high-definition video, autonomous driving, telemedicine, smart retail, instant translation, AR/VR, and more, all supported by 5G. Although people are no longer unfamiliar with these concepts, with the support of 5G, it seems that the distance to making these dreams a reality is a little closer.
It is worth noting that the consumer-oriented field is only a part of the empowerment that 5G provides. The greater value of 5G will be realized in the industrial sector, which is not as publicly focused. In fact, on December 1st of last year, South Korea launched the world’s first commercial 5G service, and the first 5G customers from the three major operators were all enterprises.
This issue of “CBC Insights” invites Song Pengfei, Vice President of Broadband Capital, to discuss “Industrial IoT”, analyzing the pain points and needs of enterprises with case studies, as well as the corresponding 5G application scenarios.
The article mainly revolves around the following topics:
-
The Difference Between Industrial IoT and Consumer IoT
-
Four Levels of Industrial IoT Applications
-
The Potential Impact of 5G on Industrial IoT
-
5G Applications in Industrial IoT
/ When Industrial IoT Meets 5G /
For the average consumer, the concept of 5G might just mean faster internet speeds; the enhanced browsing experience brought by 5G’s large bandwidth is the most intuitive, allowing users to watch higher-definition videos in real time on their phones.
However, the improvements in experience brought by lower latency and higher reliability for end users are relatively minor; the latency when opening a webpage drops from 50ms to 10ms, which consumers typically do not perceive as a difference.
In the industrial sector, the situation is completely different. Many years ago, the concept of the industrial internet was proposed, but even now, with the widespread adoption of mobile internet, the proportion of connected devices in the industrial sector remains quite low, and the applications involving connected devices are still very shallow. The main reason is that the current internet does not meet the requirements in terms of latency and reliability.
01
The Boundaries of IoT
The Internet of Things (IoT) is a broad and general concept. In terms of large application areas, it can be divided into consumer-grade IoT and industrial-grade IoT.
The performance requirements for these two categories of IoT differ greatly. Major scenarios for consumer-grade IoT include wearable devices, shared economy, smart homes, etc., which are closely related to consumers’ lives. The connections are primarily via GPRS, WiFi, and Bluetooth, with the main performance requirement being low power consumption.
Smart homes have rapidly developed recently. On one hand, advancements in interactive technology have enhanced voice interaction experiences, while on the other hand, the reduction in the cost of connection modules in the industrial chain has made it feasible to connect and control a large number of appliances in the home through a speaker as an entry point, leading to the emergence of industry-leading companies like Xiaomi IoT, Tuya, and Espressif.
However, in the industrial IoT field, the situation is different. The characteristics of various vertical industries in the industrial sector vary greatly, with high knowledge barriers, and the manufacturing processes in the industrial sector require very high reliability and stability. The current operator networks still struggle to meet the performance requirements of industrial IoT. Therefore, progress in IoT in the industrial sector has been relatively slow, and mature business models and large-scale companies have not yet emerged.
02
The Current State of Industrial IoT
The industrial sector includes numerous vertical industries, with major industries including manufacturing, transportation, energy, construction, and mining. The characteristics of each industry differ greatly, and the integration of IoT with each industry must be adjusted according to the specific characteristics of that industry.
If we abstract the application of IoT in industries, we can summarize it into four levels: data collection and display, basic data analysis and management, deep data analysis and application, and industrial control.
These four levels summarize the current applications and value of industrial IoT from shallow to deep, based on the depth of the business processes involved; the shallower the application, the fewer business processes involved, and the stronger the generality, leading to broader application fields.
a
Data Collection and Display
This mainly involves transmitting data collected from industrial equipment sensors to a cloud platform and presenting the data visually.
Currently, most industrial equipment, such as CNC machine tools, wind turbines, and industrial vehicles, come equipped with numerous sensors and provide centralized data interfaces. Only a small number of older devices or those with specific data requirements need to have sensors and data collection devices installed separately.
In terms of data transmission, equipment within factories, which have complex environments, generally use wired connections to link machine tools to centralized data processing devices, which then connect to the cloud platform via 4G or fixed networks; equipment outside the factory, such as industrial vehicles, complete data collection and transmission through terminals equipped with built-in 4G communication modules.
The challenges in data collection lie in adapting and ensuring compatibility with the data protocols of a large number of different brands of industrial equipment. Ultimately, data visualization is a core demand for clients, allowing for monitoring the status of networked devices through a unified platform, facilitating timely awareness of equipment anomalies, and improving management efficiency.
b
Basic Data Analysis and Management
Based on the device data collected on the cloud platform, basic data analysis is performed, generating some SaaS applications, such as alerts for abnormal equipment performance indicators, fault code queries, and fault cause correlation analysis.
This level of data analysis still leans towards a phase of generic analytical tools, not involving in-depth industry knowledge-based data analysis specific to vertical fields. Based on these data analysis results, some general equipment management functions will also emerge, such as turning equipment on and off, adjusting states, remotely locking and unlocking machines, etc. These management applications vary based on specific industry needs.
c
Deep Data Analysis and Applications
Deep data analysis involves specific industry knowledge and requires industry experts to implement it, establishing data analysis models based on the characteristics of the equipment and its field.
Currently, this is often applied in the field of fault prediction, where predicting faults in large industrial equipment has always been a challenging issue, such as machine tools and wind turbines. Once a major fault occurs, the implications and subsequent repair costs are significant. Real-time data collection and fault prediction can greatly reduce the impact of equipment failures.
Using machine learning, combined with the knowledge of industry experts, deep industry applications can be developed, such as improved manufacturing processes and optimized manufacturing workflows, thus enhancing the efficiency of industrial equipment usage.
d
Industrial Control
The goal of industrial IoT is to implement precise control over industrial processes.
Based on the aforementioned processes of sensor data collection, display, modeling, analysis, and application, decisions are formed in the cloud and converted into control instructions that industrial equipment can understand, thus operating industrial equipment to achieve precise information exchange and efficient collaboration among industrial equipment resources.
Currently, most industrial control systems in various scenarios still need to be deployed locally. Due to limitations in communication technology and processing capabilities, industrial cloud platforms do not yet deeply involve industrial control. 5G technology can meet the communication capabilities required by industrial systems, achieving the goal of industrial control.
03
Application Cases of Industrial IoT
Manufacturing can generally be divided into discrete manufacturing and process manufacturing based on the characteristics of the product manufacturing process.
Discrete manufacturing products are often components processed and assembled through multiple non-continuous processes, such as 3C products, automobiles, machinery, etc., where the production process is discrete. Process manufacturing, however, involves raw materials processed through a series of devices and equipment according to fixed processes, with a high degree of automation in the production process, such as petroleum, chemicals, natural gas, and paper manufacturing.
The entire production chain involved in discrete manufacturing is long, and each link in the production chain operates independently, resulting in significant capacity differences, which can lead to issues in the connections between links, affecting the final product’s production. For instance, in the mobile phone manufacturing sector, sometimes the production capacity cannot keep up with the release of new models, which may be due to a low yield of a specific component in the production chain. Therefore, providing a unified IoT platform in the discrete manufacturing sector, connecting the various links of production from an informational standpoint, becomes very meaningful.
Specifically, in the manufacturing process, most of the equipment involved are machine tools. Currently, there are some companies in China exploring the direction of machine tool information networking, which is also a typical application in industrial IoT.
By collecting and managing information from CNC machine tools and related sensors, two aspects of value can be achieved:
a
Device Level
Obtaining performance data about devices can assist in pricing second-hand equipment. Additionally, fault information codes can be obtained to timely understand equipment fault conditions, facilitating subsequent repairs.
b
Management Level
Connecting workshop operators with the production process can facilitate personnel management. This bottom-up data can address the reliance on human management in workshop settings.
Through SaaS-level applications, equipment status information can be clearly displayed, and various management and control applications can be developed to enhance the efficiency of machine tools and factory production. Once the various links in the discrete manufacturing chain are connected through a unified IoT platform, it becomes easier to manage the overall manufacturing process from a global perspective.
The construction machinery sector is also an application of industrial IoT. After equipping construction machinery with IoT access terminals, timely location and status information of the equipment can be obtained, enhancing equipment usage and management efficiency. IoT access services generally consist of two parts: the provision of IoT access terminals and the industrial IoT big data platform.
The IoT access terminals mainly include positioning modules and communication modules, generally using GPRS or 4G access methods. Their main function is to obtain the location information of the equipment, deploy it within construction machinery, and also gather some status information of the equipment, transmitting this information to the cloud platform in real-time.
▲ Source: Tiejia Network Tiejia Cloud Box
The IoT cloud platform can query the location and parameters of each mechanical device in real-time and monitor the production operation data of the equipment. In case of abnormal equipment parameters, warning information can be pushed to achieve precise monitoring of the equipment. Additionally, the platform can diagnose and analyze vehicle faults and find solutions to assist after-sales personnel in timely repairs, enhancing service quality.
Moreover, the IoT platform can analyze the distribution of online equipment numbers, equipment utilization rates, average working hours, and regional work intensity of equipment, allowing for predictive analysis of the after-sales service spare parts market, thus optimizing production plans and inventory.
▲ Source: Tiejia Network Tiejia IoT Cloud Platform
The above two are just typical application cases. Many companies in the market focus on various subfields of industrial IoT platforms, with most of their business concentrated on the data collection and display layer. A smaller portion involves the second layer, performing some basic data analysis and management based on the specific characteristics of the clients’ industries, but very few reach the third and fourth layers.
The reasons for this are, on one hand, that shallow applications are more generic and technically easier to implement, with lower requirements for the team’s technical and industry depth; on the other hand, the current level of connectivity technology still cannot meet the demands of industrial-grade applications, especially in terms of network low latency and reliability, leading to network connections being unable to participate in the business and production processes of industrial systems.
04
The Potential Impact of 5G on Industrial IoT
a
Technical Features of 5G
5G is not designed for a specific “killer application” but is aimed at many applications that are even yet to be known. The design of the 5G system adopts a top-down approach, first defining future application scenarios, then abstracting the technical requirements from those scenarios, and finally finding solutions and developing specific solutions for each requirement.
Due to the broad requirements of the system, the technologies from past generations of communication systems do not meet the needs of 5G. Among the many preset scenarios of 5G, the ITU (International Telecommunication Union) categorizes the technical requirements of 5G into three main areas:
■ Ultra-high data rates (Enhanced Mobile Broadband, eMBB)
Providing extremely high data transmission rates and strong signal coverage capabilities.
■ Massive connectivity (Massive Machine-Type Communications, mMTC)
Providing the capability for massive device data connections, which is a fundamental requirement for IoT.
■ Ultra-low latency (Ultra-Reliable Low Latency Communications, uRLLC)
Providing ultra-reliable low-latency communication services that require extremely high availability, reliability, and very low latency.
b
Demand for Industrial IoT
For the industrial sector, a high-reliability, low-latency communication system is crucial.
Historically, the applications of industrial IoT have been limited to surface-level data collection and display, along with some management functions that extend from this, making it difficult to involve core areas such as the control of industrial systems. The main constraining factor is the stability and latency of the communication systems.
Industrial equipment investments are substantial, whether it be machine tools, production lines, or machinery; failures during production can lead to stoppages that affect the entire production line or even the whole product delivery cycle.
To ensure stability, control systems in the industrial sector remain primarily local, deploying a large number of hardware and software systems. This not only makes the entire control system very complex and costly but also limits the system’s flexibility and scalability. In today’s rapidly changing consumer demands, if production systems cannot keep up with changes in consumer needs, many new opportunities will be missed.
Current mobile communication systems have not deeply penetrated the industrial IoT field. Although 4G has significantly improved in speed, meeting user needs for watching videos anytime, the reliability and latency of the network still have a lot of room for improvement and cannot meet the requirements of industrial scenarios.
4G applications in industrial scenarios are mostly in areas where real-time requirements are not high, serving as a means to upload data to the cloud. For instance, in factory settings, machine tools may collect data every 5-10 seconds, and this data is typically aggregated at a unified terminal, which then sends it to the cloud platform via 4G.
To ensure the stability of data transmission from machine tools, wired connections are commonly used between the machine tools and the unified terminal within the factory. This connection method is still relatively heavy, and a large amount of cabling can complicate the internal structure of the factory. When the performance of mobile network systems improves to the point where they can replace wired cabling, the complexity of the factory’s internal structure will also reduce, making management easier.
The demands for communication systems in the industrial sector can be well met by the technical standards of 5G, with extremely low latency ensuring real-time monitoring and control requirements; high reliability of network quality ensuring the stability requirements of industrial systems; and large bandwidth enabling the transmission of high-definition 3D video and even AR, significantly enhancing operational precision in remote control scenarios.
05
5G Applications in Industrial IoT
At the World Mobile Congress held in Shanghai in June 2018, a reporter from CCTV Finance experienced a demonstration of 5G smart industrial applications brought by China Mobile:
A digger located at a construction site in Shijiazhuang was connected through 5G technology to an onsite control room, allowing it to operate even in harsh environments, potentially creating a site without human presence.
Visitors could operate the digger in real-time from the control room, controlling its movements such as moving forward and backward, rotating, and coordinating the large and small arms for digging and loading operations. The large screen opposite the control panel transmitted real-time high-definition video, synchronizing the actual scene and panoramic video effects.
Although this is just a scenario demonstration, it represents the potential application value of 5G in the industrial field and the direction of future applications. Currently, 5G commercial use has not officially begun, and no mature 5G application scenarios have emerged, but many research institutions focusing on the 5G field are exploring what specific applications and commercial value 5G can bring to the industrial sector.
Ericsson shared two specific research cases with us, demonstrating how 5G technology can improve industrial efficiency and enhance commercial and social value.
Ericsson collaborated with the Fraunhofer Institute for Production Technology (Fraunhofer IPT) to research new methods to improve industrial control processes and detect defects in real-time during the production manufacturing process. One application area is in the manufacturing of turbine blades, which are key components in jet engines, consisting of a wheel and numerous blades around the edge of the wheel. The manufacturing of turbine blades is a typical application in metal processing.
▲ Source: Ericsson 5G Research
Ensuring high quality in turbine blades is crucial, as high-quality blades are essential for the safety of jet engines. The blades are processed using milling machines, and during the processing, there are many issues, the most critical of which is that the milling process is difficult to monitor, a common issue in the metal processing field.
This means that until the milling process is fully completed, operators cannot know the result, and a milling process can last for a day or even up to 100 hours. Due to processing defects, the rework rate of the final processed product is often as high as 25%, extending the overall production cycle.
Processing defects can arise from many causes, but one of the main reasons is the vibrations of the milling cutter or machine tool, which affect the processing results. This vibration can be detected through real-time monitoring of the processing process, allowing for data feedback to optimize the processing in real-time, ultimately reducing the rework rate. The inability to promptly detect issues during the processing is a phenomenon that exists throughout the manufacturing industry. Although the processing of turbine blades is just one specific case, the vibration issue during the processing is prevalent in the machine tool processing field. In the future, the manufacturing of turbine blades will trend towards thinner designs, making the processing results more susceptible to vibrations.
Fraunhofer IPT’s solution to this issue is divided into two parts: real-time monitoring and real-time control—
a
Real-time Monitoring
Sensors are attached to the blade part, and communication modules are added to the wheel part, allowing for real-time monitoring of the results of blade processing. If a processing defect occurs, further processing of the defective components can be halted immediately, or the defect can be located for rework;
b
Real-time Control
A data model is established based on the processing results, allowing for real-time adjustments to the ongoing processing, such as changing the milling cutter’s speed, to prevent processing defects from occurring.
▲ Source: Ericsson 5G Research
The ultimate vision is to establish a fully automated factory, connecting all equipment and managing it through a unified system.
However, current communication technologies cannot adequately support this solution, and 5G is key to this solution. In this case, the greatest advantage of 5G is its ability to provide extremely low latency and stable networks. To achieve real-time control, sensor information needs to be responded to and processed within 1 millisecond, and 5G ensures the realization of real-time control through its extremely low latency capabilities, making it applicable in the turbine blade production process.
Fraunhofer has also calculated the economic value generated by introducing 5G to improve production technology. The traditional rework rate for turbine blade processing is as high as 25%, meaning that for every four blades processed, one needs rework. This cost is very high, and reducing the rework rate can generate significant economic value.
If the introduction of 5G and IoT technology can automate the process and reduce the rework rate by 10%, it equates to a reduction in processing time per unit product. In terms of machine costs, the cost per blade can be reduced by 3,600 euros, with a global production of about 100,000 blades per year, meaning that implementing real-time monitoring through 5G technology could save 360 million euros annually.
The mining industry is a foundational industry for global economic activity, with a massive market size. The combined annual revenue of the top 40 mining companies worldwide exceeds 500 billion dollars.
Improving profitability in the mining industry requires relentless efforts in mining efficiency, transportation, and metal extraction technologies to optimize the flow efficiency of ores. However, increased investment in these areas faces diminishing marginal returns. Automation is becoming a new opportunity and focus in the mining industry. A prerequisite for achieving automation is a relatively complete network coverage and connectivity within the mining area, where the environment is harsh, making the deployment of mobile communication networks a good solution.
Sweden’s Boliden Company is one of the world’s top mining companies, with eight mines globally; among them, the Aitik mine in northern Sweden is the largest open-pit mine in Europe. Boliden and Ericsson jointly established a research group to explore how 5G technology can help the mining industry improve efficiency and economic value.
▲ Source: Boliden Official Website
Aitik is a rapidly expanding mine. To obtain copper ore, a large volume of rock must be moved. Each year, the amount of rock transported back and forth in the mine continues to grow. Depending on the location of the ore, the rock-to-ore ratio varies, averaging that for every ton of copper ore obtained, an additional ton of rock must be moved. Aitik’s current annual output is 36 million tons of ore, and it is expected to grow to 45 million tons soon, which will correspondingly increase the amount of rock that needs to be moved.
The complexity and busyness of the mine are extremely high, and adding giant equipment to remove rocks and maintaining the utilization of this new equipment is no simple task.
▲ Source: Boliden Official Website
Additionally, ores are obtained through drilling and blasting, and each blast generates toxic gases, meaning that humans can only enter the mining area after these gases have been dissipated, which are all factors affecting mining efficiency.
To address these issues, a good solution is automation and remote-controlled equipment.
Automated drilling rigs can autonomously move from one drill hole to the next along a preset path and can automatically repeat tasks. Traditionally, human operators were required on-site to operate the equipment to move the drill rig. If a task or movement path was not pre-set, operators could use cameras equipped on the drill rig to control their movements remotely.
In most cases, automation can complete the majority of the work; however, in a few situations where human assessment and decision-making are necessary, such as evaluating rock conditions, human involvement is still required for remote or even on-site evaluations.
▲ Source: atlascopcomr
Aitik converted five traditional drilling rigs into automated and remotely controlled rigs by installing cameras, upgrading control systems, and adding communication modules. However, the current network bandwidth only supports medium-quality video transmission, which limits the remote control capabilities.
The retrofitted automated rigs can increase annual working hours from 5,000 to 7,000, meaning that Boliden can accomplish the workload that previously required seven or more rigs with just five improved rigs.
Additionally, automation also reduces the need for personnel, service stations, and parking areas, easing the pressure on busy transportation routes within the mining area. The reduction in personnel also lowers safety risks for workers in the mining area, allowing Boliden to increase blasting workloads while maintaining the same number of equipment and employees. According to estimates, using automation technology for drilling and blasting can save Aitik mine 2.5 million euros annually.
To achieve complete automation, remote-controlled equipment and high-performance communication systems are essential. Currently, the communication technology used in the mining industry is still WiFi, which, after careful optimization, can be acceptable in terms of coverage and performance; however, it can only handle simple, repetitive tasks in automation, such as adjusting the drilling pattern.
Boliden has previously deployed WiFi communication systems at the Aitik mine to meet the needs of controlling drilling rigs. While this has improved productivity levels to some extent, the performance of WiFi still has many shortcomings. After all, WiFi is not designed for outdoor large-area coverage, and Aitik’s open-pit mine is precisely such a scenario. The limited connectivity of WiFi also restricts the potential to connect other automated machinery.
From the entire mining industry down to Boliden as a company, the performance of the WiFi communication system severely limits further development in automation, as achieving complex drilling, automated mining trucks, and automated planning and scheduling systems requires a high-performance communication system to meet these needs. 5G is the most suitable communication system, capable of handling the transmission of 3D high-definition video and significantly improving the precision of remote control, thus enabling the remote management of highly complex tasks.
▲ Source: Ericsson 5G Research
To achieve the goal of automation in the mining area, Boliden’s communication system needs to meet the following demands:
-
First, to ensure remote monitoring, the communication system needs to have high bandwidth and low latency capabilities;
-
Secondly, the system within the mining area must be adaptable to other automated and remote-controlled devices, including different brands and control systems;
-
Additionally, it must achieve full coverage, reaching every corner of the mine to ensure that all machines and personnel can be connected and located;
-
Finally, it must ensure the stable operation of the system in the complex and variable environment of the mine.
The 5G communication system can meet Boliden’s highest demands, including bandwidth, network service quality, latency, and positioning. By introducing a high-performance communication network, the mine becomes safer and more efficient. Although some applications may not require large amounts of data transmission, applications such as remote real-time control of machinery can only be realized with a 5G communication system. With the empowerment of 5G, the mining industry may become one of the innovative fields, generating new applications and business models.
06
5G Empowerment, A Long Way to Go
With the resolution of latency and stability issues, the constraints on connecting a large number of devices in the industrial sector are eliminated. This massive market, previously untouched by the internet, is akin to the emergence of 4G and smartphones, which opened the door to mobile internet; 5G faces an opportunity that may be even larger than mobile internet.
Because the number of connections provided by 5G, the value it offers, and the payment capabilities are not comparable to those of mobile internet, many believe that the greatest opportunity for 5G lies in industrial internet.
Although 5G technology is still not mature and large-scale deployment and application have a long way to go, we believe that the direction of 5G empowering the industrial sector is clear, and the future is promising.
— END —
This article is an authorized reprint and does not represent the position of the enterprise service industry headline. For reprints, submissions, content cooperation, or reporting inquiries, please contact WeChat: qifutoutiaozhushou3W
Selected Hot Articles
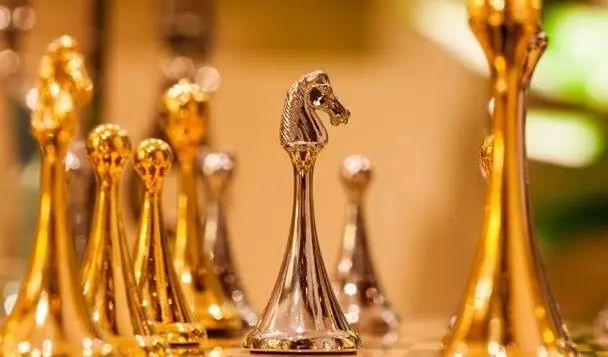
2018 Latest To B Unicorn Company List (Including Valuation)
It must be acknowledged that the growth cycle of domestic unicorn companies is becoming increasingly shorter.
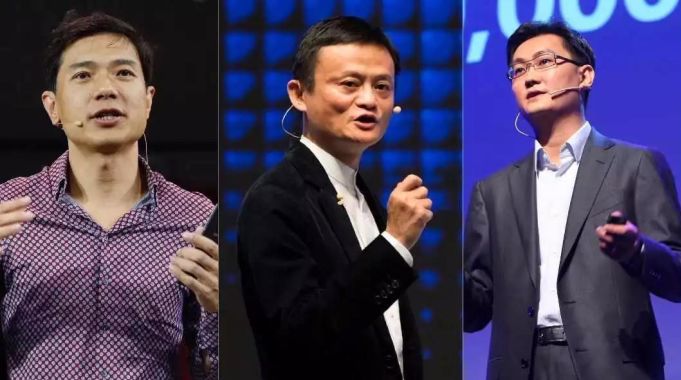
2018 BAT Investment Report
2018 was an unstable year.
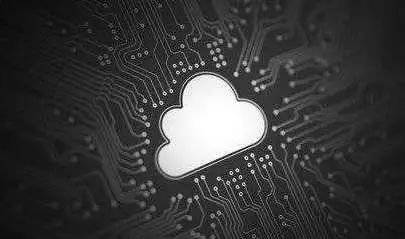
The Ten-Year Journey of Cloud Computing in China
Where there is cloud, there is a river and lake. Where there is a river and lake, there are bound to be conflicts and disputes.
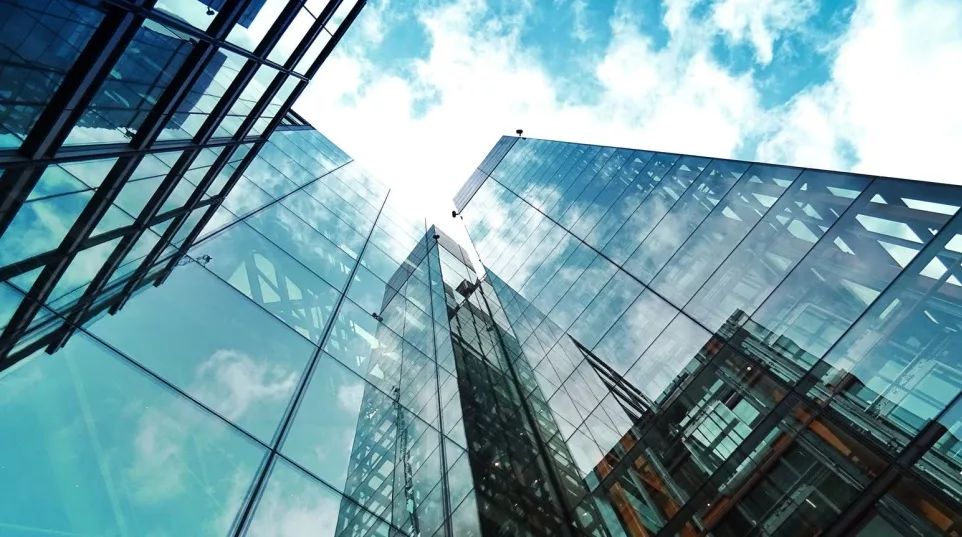
To C Decline, To B Rise
The To B internet is destined to be a marathon-style industrial revolution.
Recommended Reading