TL;DR:
What should an ideal scheduling tool look like in factory operations?
■ Real-time monitoring of production processes to provide actionable suggestions at any time.
■ Features a visual user interface that can update data in seconds.
■ Simple and efficient operation, allowing for drag-and-drop actions.
■ Maintains real-time updates of production data for personnel, equipment, and inventory status.
■ Automatically allocates capacity reasonably to fulfill production and customer quotation commitments.
■ Shared data sources that can link all critical input information.
■ Automatically integrates front-end devices to achieve IoT connectivity.
For most product manufacturers and subcontractors, achieving fast and efficient operations requires not only durable, reliable, and well-maintained process equipment but also comprehensive design, simulation tools, and manufacturing digitalization tools.
Under the planning of Dassault Systèmes’ unified platform, SOLIDWORKS DELMIAworks has undergone multiple iterative upgrades, achieving seamless integration with other software within the platform, thereby aiding companies in comprehensive digital construction.
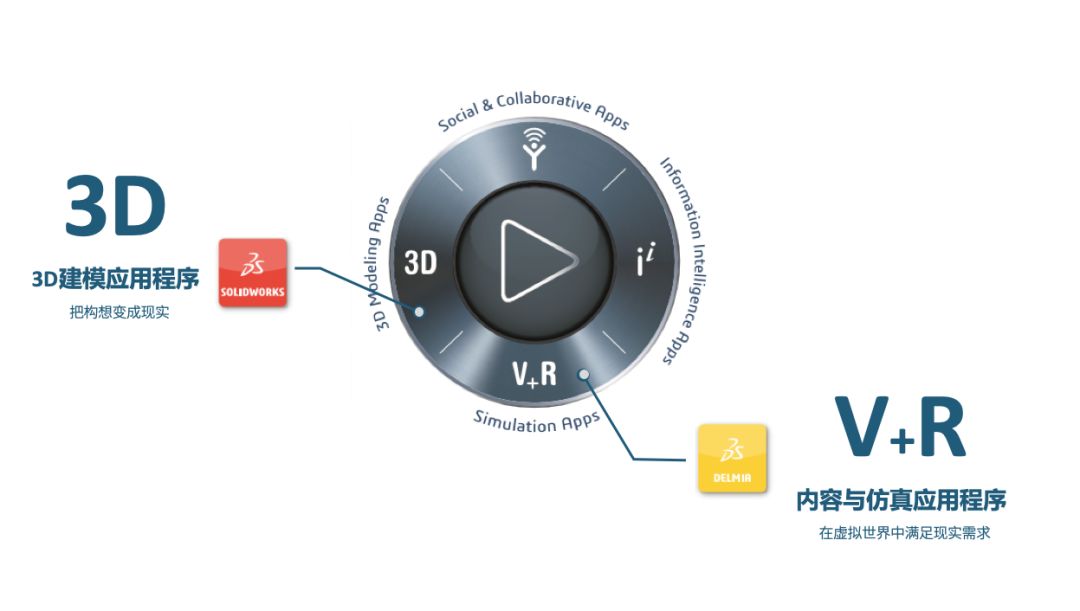
DELMIAworks and SOLIDWORKS belong to the 3D modeling and simulation application modules of 3D EXPERIENCE, operating independently yet seamlessly connected.
During actual factory operations, operations managers often encounter numerous obstacles. Scheduling production alone is a challenge for managers as they need to consider labor, suppliers, material supply, and customer demand deadlines, while also facing issues with incomplete plans, cumbersome scheduling processes, and outdated systems.
For instance, manufacturers may be using inefficient traditional enterprise resource planning (ERP) demand reports, material requirements, or other enterprise planning software to schedule production. They may also rely on outdated systems such as: kanban cards, documents printed for purchase orders, spreadsheets, printed emails/information, whiteboards with handwritten notes, or even paper records.
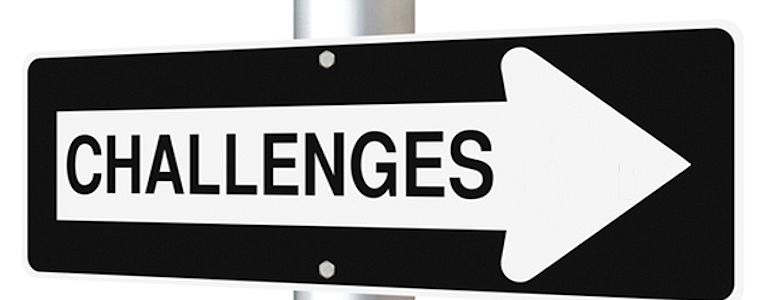
Prem Vrat, G. D. Sardana, and B. S. Sahay point out in their book “Productivity Management: A System Approach” that “ineffective production planning, scheduling, and follow-up waste manufacturing resources.” They further explain that: “It can also be the cause of planning delays, machine idleness, queue production, and machine busy times.”
Therefore, for manufacturing plant production teams and schedulers, they expect to have better tools for planning and scheduling. This leads us to consider two questions: What should an ideal scheduling tool look like? What attributes and functions can make it usable, efficient, and effective? SOLIDWORKS DELMIAworks believes that an ideal scheduling tool should have the following scheduling functions:
1. Ability to interact in real-time and provide actionable suggestions;
2. A grid-like user interface that can visualize updates in seconds;
3. Drag-and-drop scheduling;
4. Real-time updates of key inputs such as raw material inventory levels, equipment tooling readiness, production capacity, and availability of qualified operators on working days;
5. Algorithms that handle infinite and finite capacity based on process types to fulfill production and customer quotation commitments;
6. A single database that can directly link to the real-time status of all critical inputs;
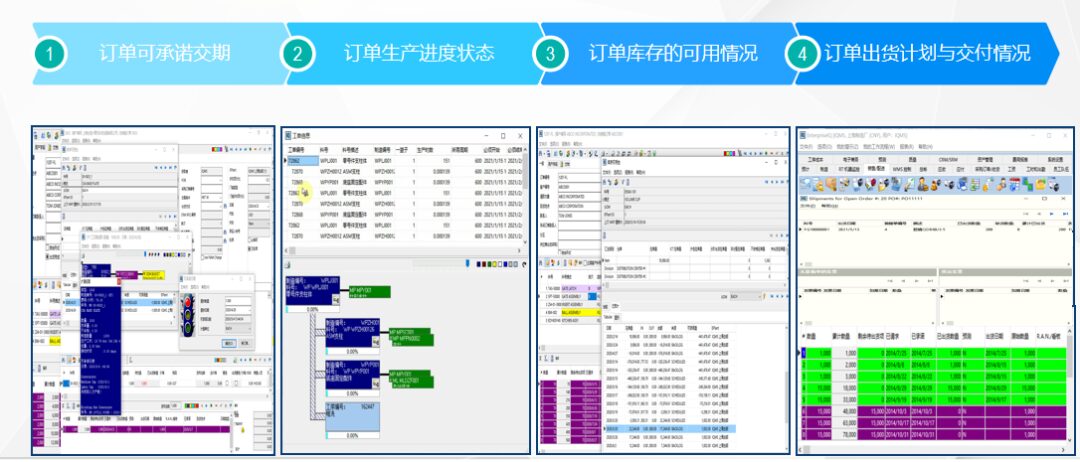
These features of scheduling tools have already been integrated into today’s SOLIDWORKS DELMIAworks software: RealTime™ production monitoring, integrated with a built-in drag-and-drop scheduling program. This solution can leverage Industrial IoT (IIoT) technology to achieve innovative, smart, and interconnected manufacturing, thus ensuring reliable return on investment (ROI).
Next, we will learn how three manufacturers have leveraged drag-and-drop scheduling and RealTime™ production monitoring from SOLIDWORKS DELMIAworks to enhance their production planning processes and efficiency.
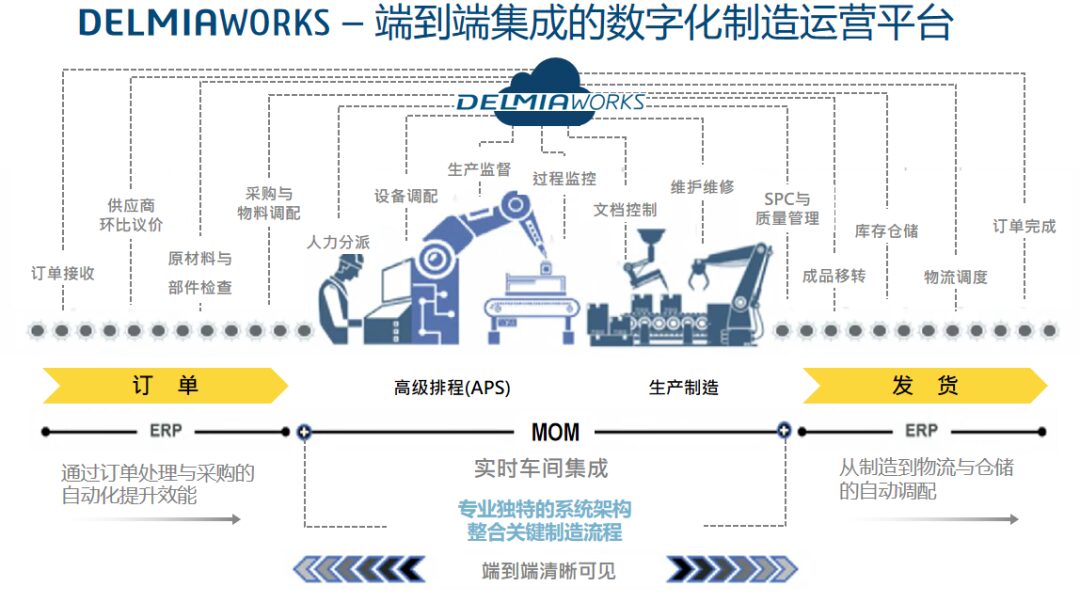
1. Real-time Control of Processes
Earlier, we studied some challenges faced by Nissen Chemitec America, which relied on Electronic Data Interchange (EDI) data to schedule daily plans, forecast demand, and communicate with customers and suppliers. Today, using the SOLIDWORKS DELMIAworks system, Nissen Chemitec America’s EDI push data has been elevated to a whole new level as the company also utilizes real-time production monitoring.
As part of the SOLIDWORKS DELMIAworks system, it provides Nissen Chemitec America with a simple, economical, and efficient method to automatically capture and utilize data from the workshop as production occurs in real time. Moreover, RealTime device monitoring connects each work center to the SOLIDWORKS DELMIAworks database, allowing Nissen Chemitec America to track jobs from planning to production.
Since production data is directly transmitted to the ERP database, job status is automatically updated every minute. Additionally, the system supports powerful visual planning and reporting interfaces that anyone can use from anywhere (inside or outside the company) to assess job status, track equipment downtime, view quality data, and more.
2. Increased Efficiency and Cost Savings
Another two manufacturers benefiting from SOLIDWORKS DELMIAworks real-time production monitoring are Tessy Plastics and Mar-Bal, Inc. At Tessy Plastics, providing accurate production information to all employees and managers is considered key to improving operational efficiency.
“We have information centers throughout the plant, so everyone can see our performance,” explains Doug Jobe, Operations Director at Tessy Plastics. “We view automation as a large collective. This includes injection molding machines matched to capacity, as well as machines that correspond to matched capacities. What we do with SOLIDWORKS DELMIAworks is combine all these elements into a system that works efficiently.”
Meanwhile, Mar-Bal, Inc. has achieved immediate and long-term savings through SOLIDWORKS DELMIAworks’ manufacturing ERP solution. Annually, its four plants save approximately 270,000 dollars and nearly 4,400 potential machine hours that were previously lost due to downtime from monthly inventory checks. Mar-Bal found that the key to significant savings was adding SOLIDWORKS DELMIAworks real-time production monitoring to their ERP system to track production as it occurs.
3. Enhanced Operational Efficiency and Customer Satisfaction
SOLIDWORKS DELMIAworks RealTime production monitoring and drag-and-drop planning features integration give manufacturers a competitive edge. This system reduces reliance on one or two individuals to perfectly remember many details and coordinate responses to constantly changing information. When significant changes occur in planning, reallocating resources impacts the entire enterprise.
Another unique aspect of SOLIDWORKS DELMIAworks’ drag-and-drop planning feature is its efficiency and ease of use. When changes are made by dragging and dropping one or more variable factors into the mix, the system automatically reconfigures resources to optimize them. It manages this complexity at lightning speed — a true advantage for production leaders.
The system can compute updates for tens of thousands of orders within seconds to minutes. This instantaneous, real-time updated information throughout the SOLIDWORKS DELMIAworks system enables employees to quickly respond to customers when delivery dates or quantities need to change, or goods are shipped earlier than expected.
Real-time production monitoring from SOLIDWORKS DELMIAworks’ drag-and-drop visual planning can rapidly enhance productivity, boost management confidence, reduce manufacturing costs, and deliver greater value to global manufacturers.
Click below to read the original article for more content related to SOLIDWORKS DELMIAworks.