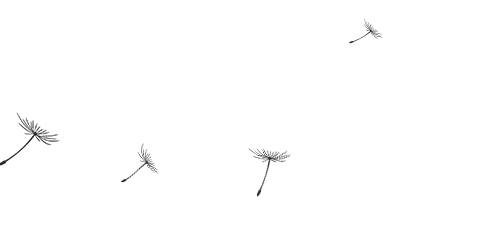
Get more IIoT insights
Click the blue words
Follow us
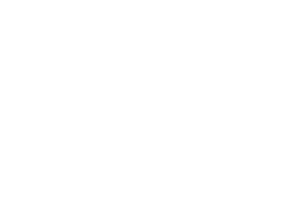
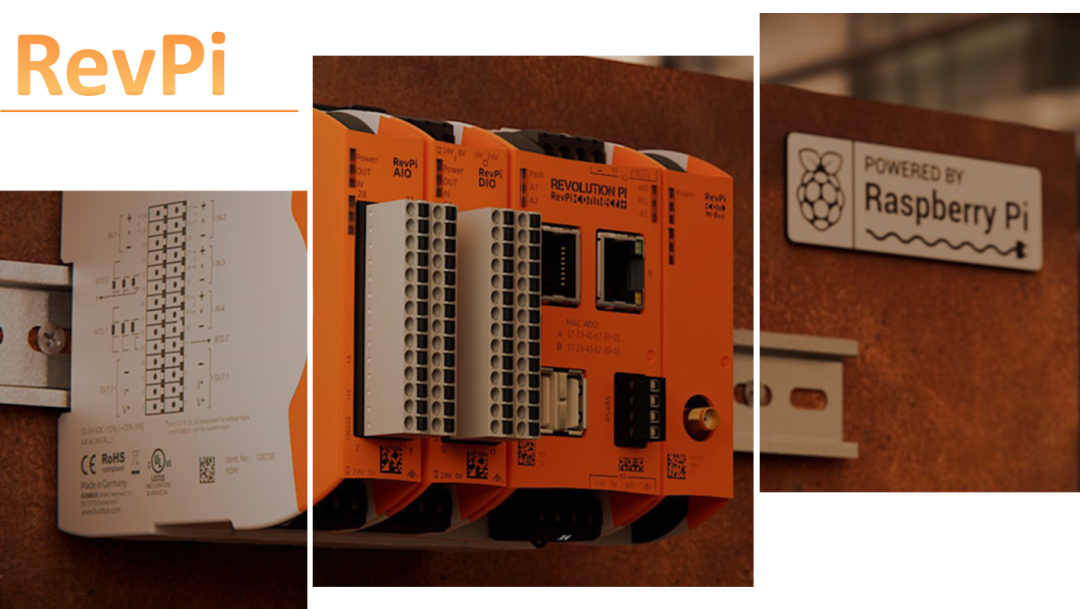
HongKe
IIoT
HongKe Industrial Raspberry Pi with CODESYS
Control Remote IO Modules
HongKe Technology
Hong
/
Ke
/
Solution
01
Background Knowledge
Ethernet Remote IO Modules are industrial-grade remote acquisition and control modules that provide passive node switch input acquisition, relay output, high-frequency counters, and other functions. The module uses industrial-grade components, with a wide voltage input of 10-30VDC, capable of operating normally in a temperature range of -30℃~60℃. Currently, commonly available remote IO modules support field buses such as Modbus and EtherCAT.
Ethernet remote IO modules are widely used, mainly in distributed data acquisition and control, especially suitable for scenarios where data points and control points are dispersed.
The traditional data acquisition scheme is achieved through industrial computers + IO boards, where various instrument signals are directly connected to the IO board via cables, resulting in high wiring costs and significant signal attenuation.
However, Ethernet remote IO modules can be directly connected to PLCs or industrial computers. By connecting the IO to the PLC or industrial computer with a single Ethernet cable, various instrument controller signals can be directly accessed to the Ethernet IO module nearby, which has the following benefits:
-
Saves the cost of using industrial computers and IO boards, as Ethernet IO modules can be directly integrated into the upper computer system;
-
Replaces 4-20mA signal transmission with 10/100MHz Ethernet transmission, increasing transmission speed;
-
Reduces signal remote transmission attenuation by using a single Ethernet cable instead of various instrument controller signal lines;
-
The signal cables of instrument controllers only need to connect to the Ethernet IO module, greatly reducing cable costs and wiring workload.
HongKe Industrial Raspberry Pi, as an industrial-grade controller, supports connecting and controlling Ethernet remote IO modules through field buses. Below are the specific operation configurations.

02
Preparation Work
1. Hardware Preparation
-
HongKe Industrial Raspberry Pi Connect + CODESYS Module *1
-
EtherCAT IO Module (Digital Input & Output Module) *2
-
Switch Box *1
-
Lighthouse *1
2. Software Preparation
-
CODESYS Software: Installed on PC
-
CODESYS Runtime: Raspberry Pi Multi-Core Version

03
OperationSteps
1. Hardware Connection
HongKe Industrial Raspberry Pi Ethernet Port A connects to the router, Ethernet Port B connects to the EtherCAT IO module
2. Configure EtherCAT Master
(1) Import EtherCAT IO Module Description File
① Path: Tools → Device Repository
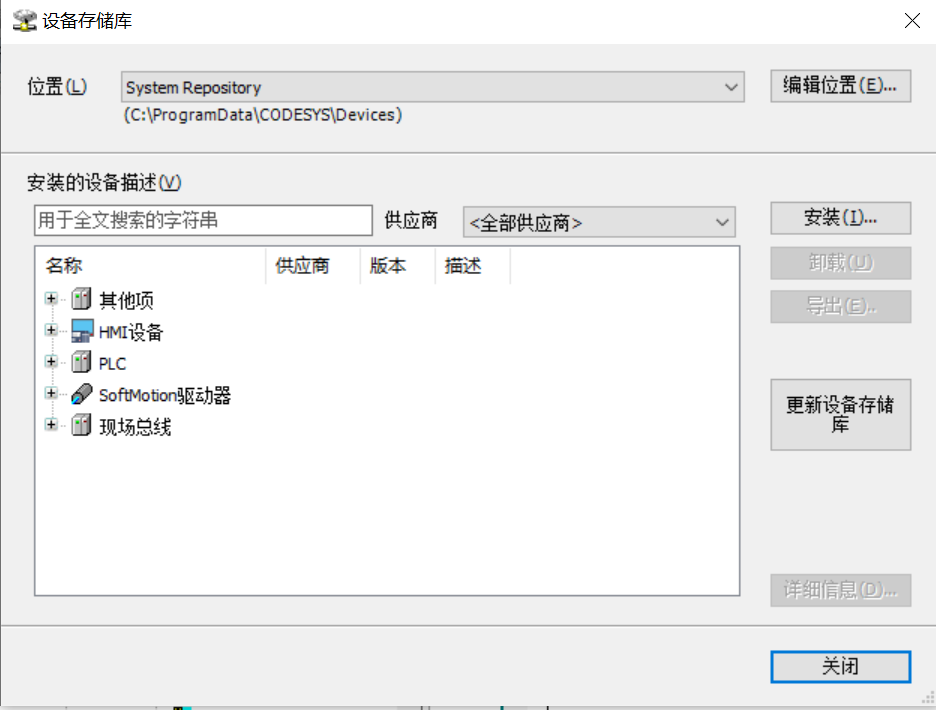
② Click “Install” to install the corresponding EtherCAT IO module description file
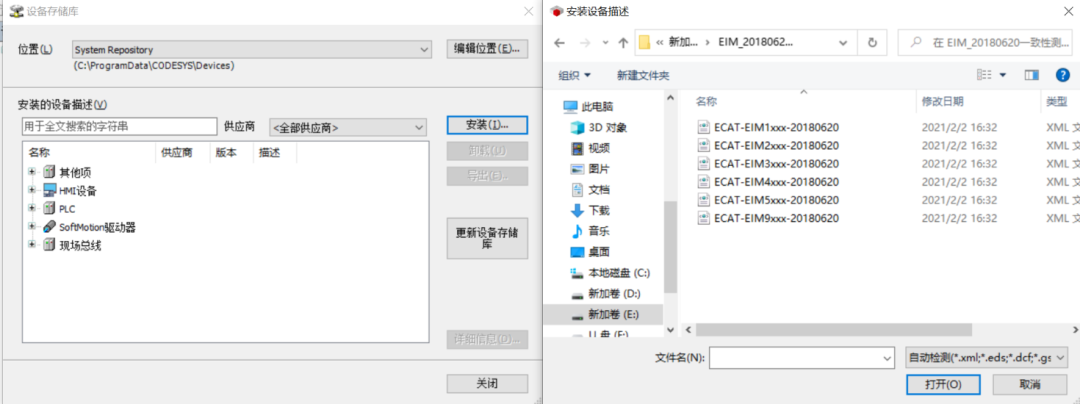
(2) Add Device: Right-click “Device”, select “Add Device”
① Select “Other Items”, add HongKe Industrial Raspberry Pi model
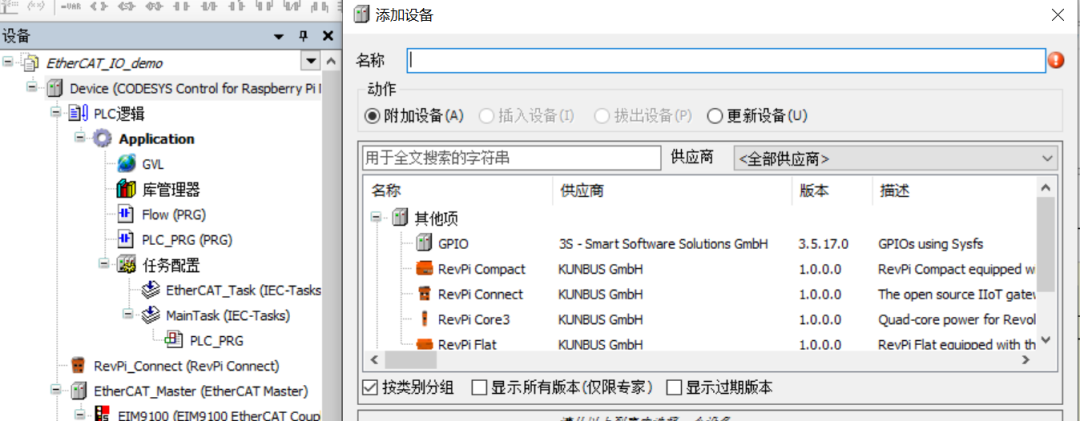
② Select “Field Bus”, add “EtherCAT” → “Master” → “EtherCAT Master”
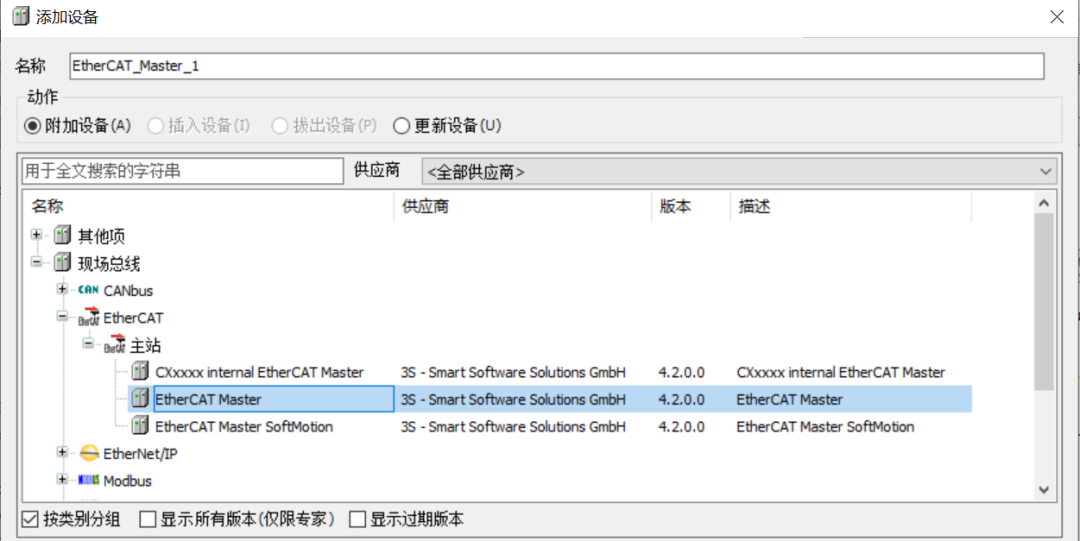
(3) Add EtherCAT IO Module
① Configure the connection Ethernet port between HongKe Industrial Raspberry Pi and EtherCAT IO module, choose based on the actual connected Ethernet port
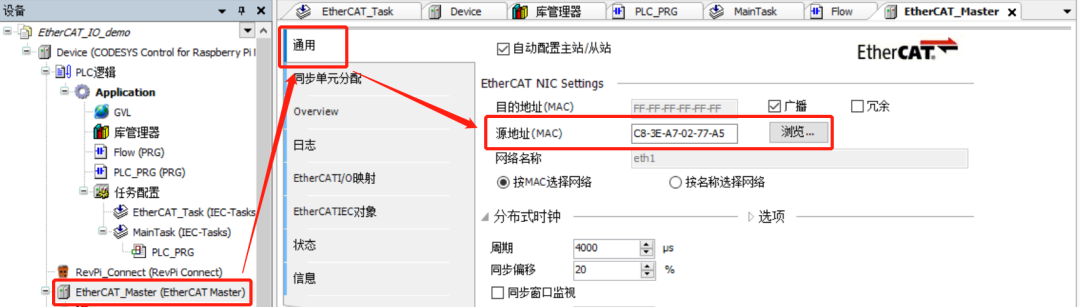
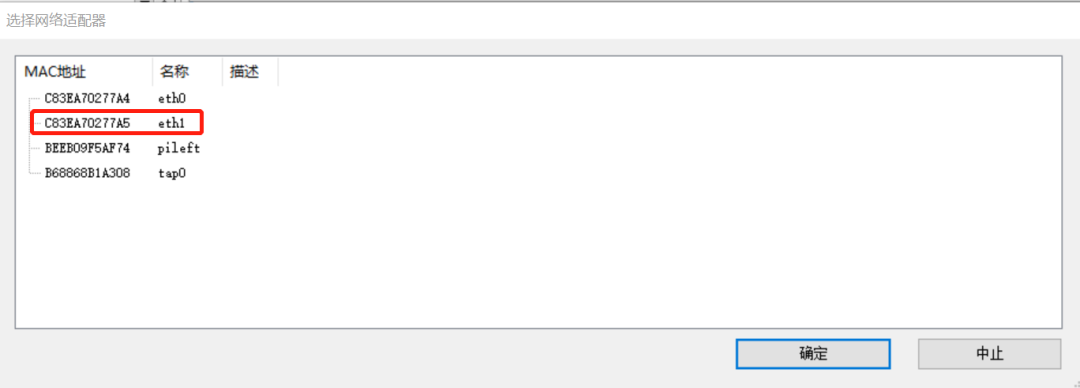
② Log in to the device, Path: Online → Login
③ Scan the EtherCAT IO module, the software will automatically recognize the EtherCAT IO module connected to the HongKe Industrial Raspberry Pi
Path: Left directory “EtherCAT_Master” → Scan Device → Select the corresponding module, click Copy
3. Define Variables
(1) Define EtherCAT IO Input Variables
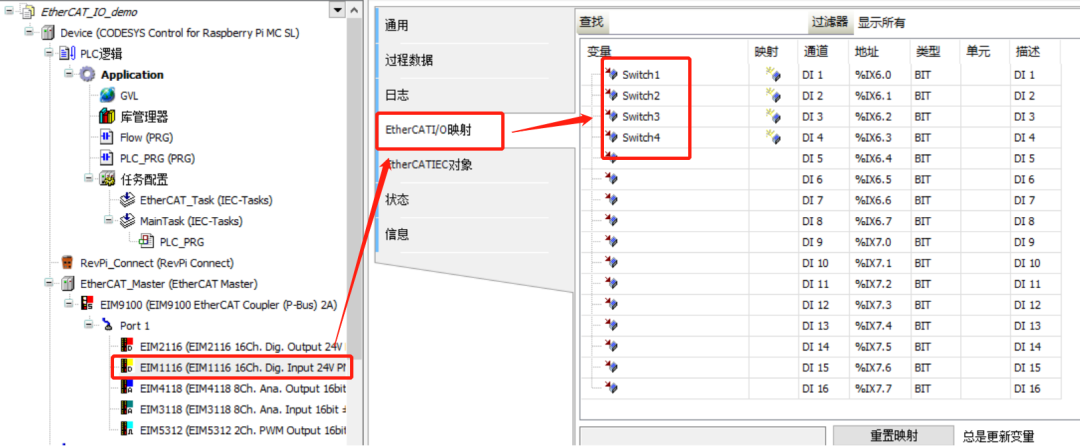
(2) Define EtherCAT IO Output Variables
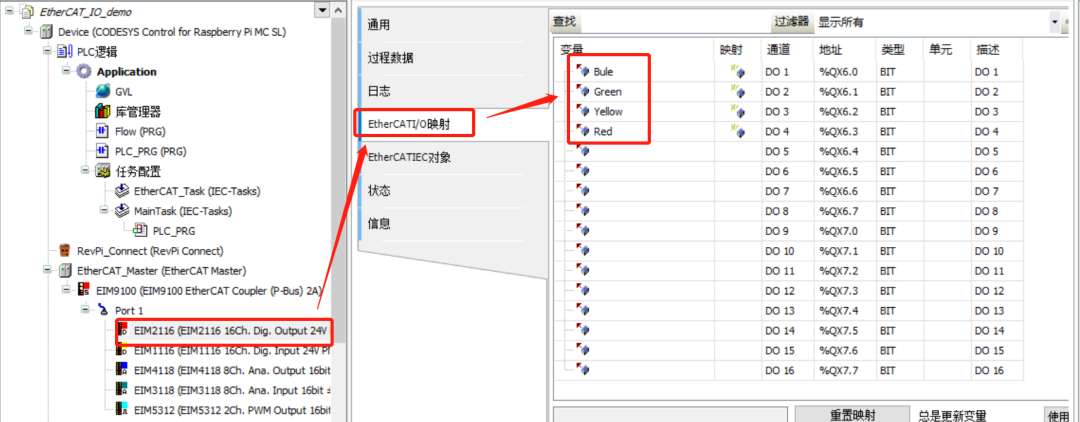
(3) Define Global Variables
① Add a global variable list, customize the name
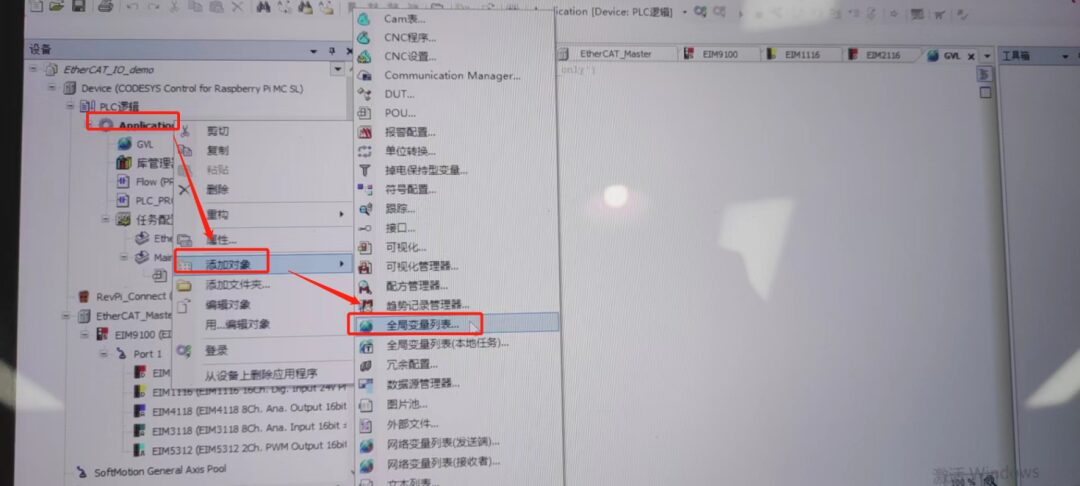
② Define Variables
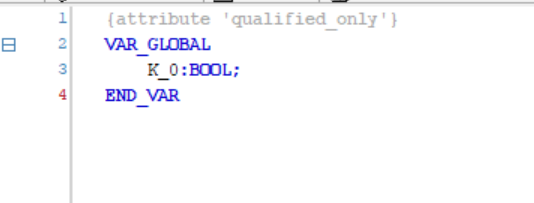
(4) Define Local Variables
Click on the program: PLC_PRG, add the following variables:
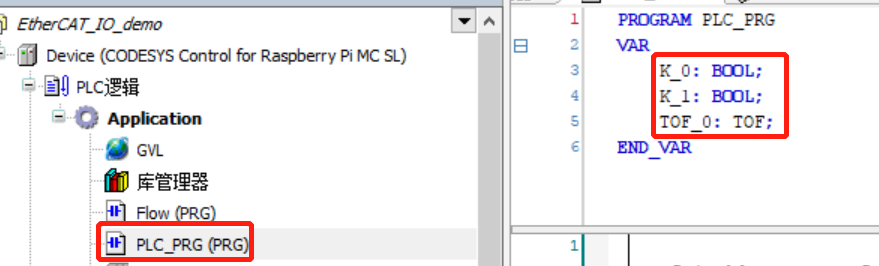
4. Write Program
(1) Add Program: Flow, the control program for the running light is written in Flow, as follows:
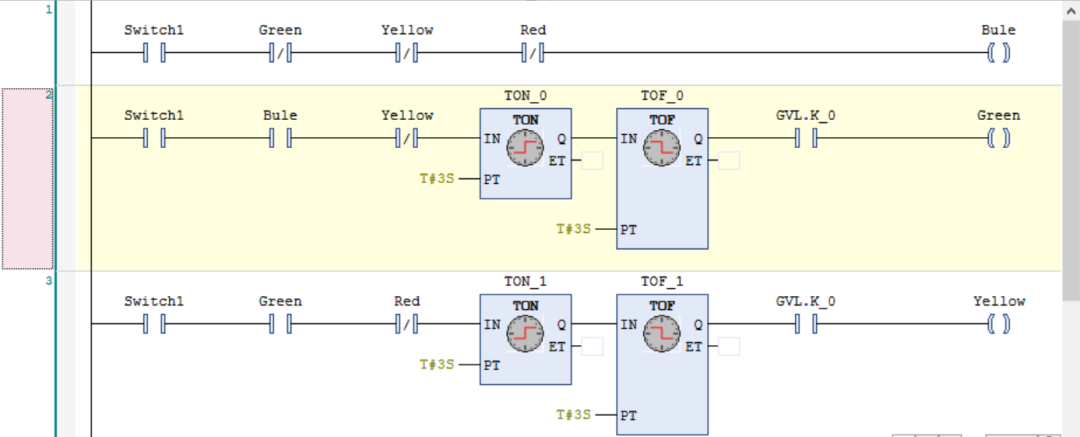
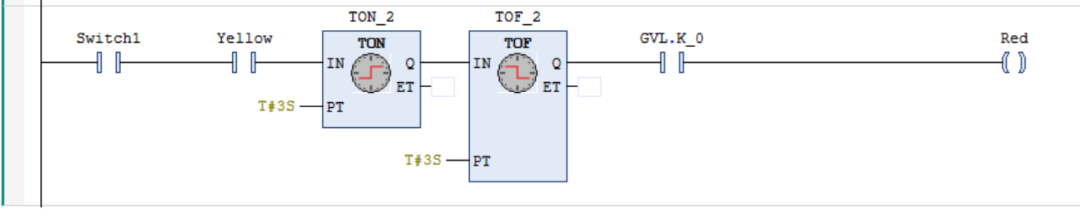
(2) Write Main Program: PLC_PRG, the overall control program for the running light:
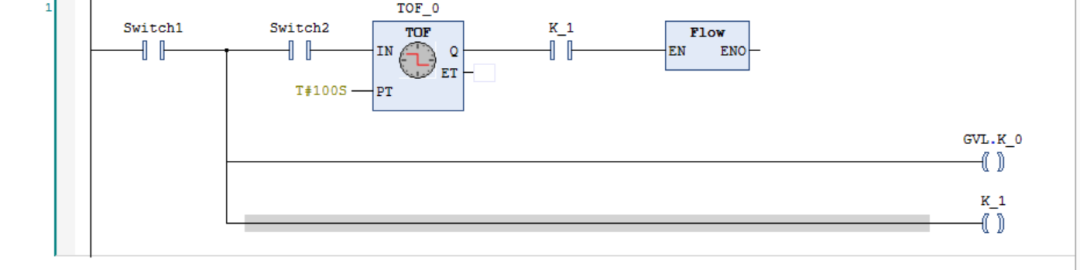
5. Run the Program

04
Conclusion
The content above mainly shares the operation steps for controlling EtherCAT IO modules with HongKe Industrial Raspberry Pi combined with CODESYS. As long as the corresponding EtherCAT IO description file is provided, the HongKe Industrial Raspberry Pi can control remote IO modules. In addition to controlling remote IO modules through CODESYS, HongKe Industrial Raspberry Pi also supports protocol control through protocol stack development packages.
Moreover, HongKe Industrial Raspberry Pi supports multiple field bus protocols such as MODBUS, CANopen, Profinet, etc., which can adapt to various field bus protocol remote IO modules, helping more enterprises achieve digital transformation quickly and cost-effectively without the need for dedicated remote IO modules.
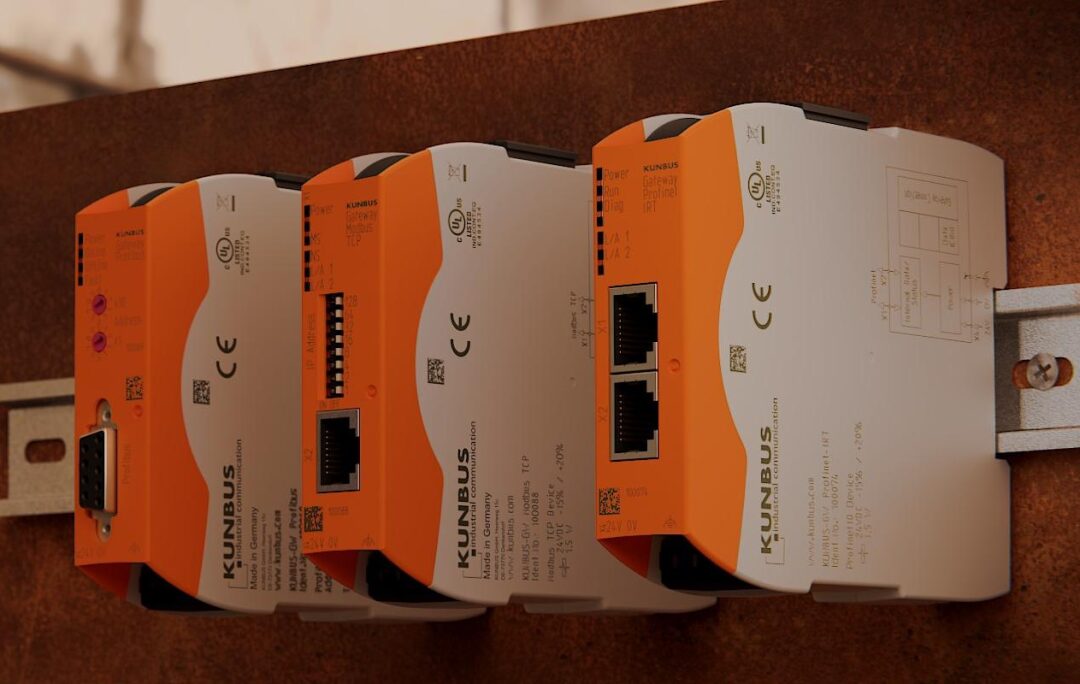
HongKe–Industrial Internet of Things
HongKe is a high-tech company with over 3 years of experience in the IIoT industry, collaborating with top companies worldwide including EXOR, Eurotech, Unitronics, Matrikon, KUNBUS, etc., providing advanced solutions for Industrial 4.0 such as industrial touch screens, high-end edge computers, IoT development frameworks, PLC and HMI integrated machines, OPC UA, industrial-grade Raspberry Pi, SCADA. All members of the IoT division are professionally trained and certified, with an average of over 3 years of technical experience, consistently earning excellent customer reputation. We actively participate in industry associations, making significant contributions to the promotion of advanced technology. To date, HongKe has provided various solutions from hardware to software for many users in the industry and has participated in numerous OEM equipment R&D and migration projects, as well as smart factory and Industrial 4.0 upgrade projects for end users.
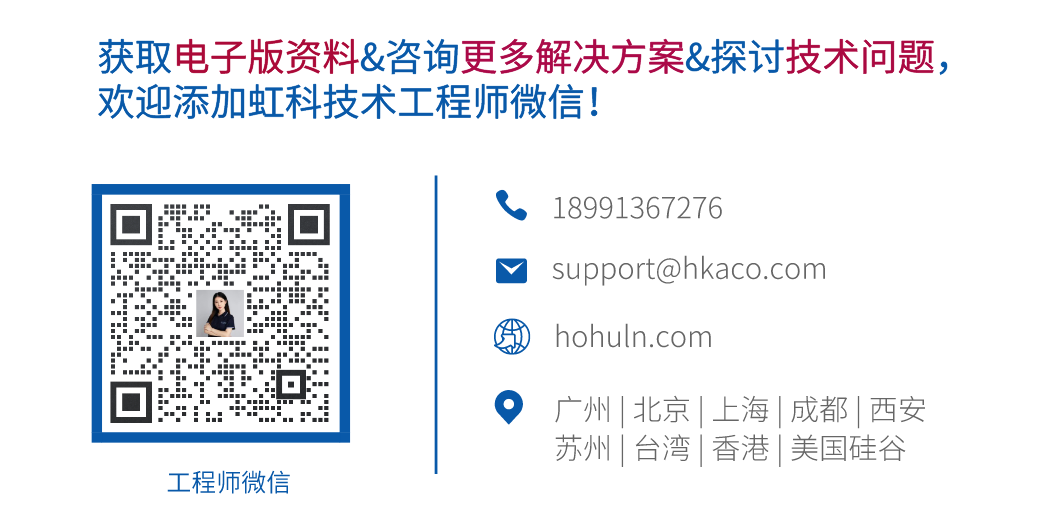
Scan the QR code to get more cutting-edge IIoT knowledge
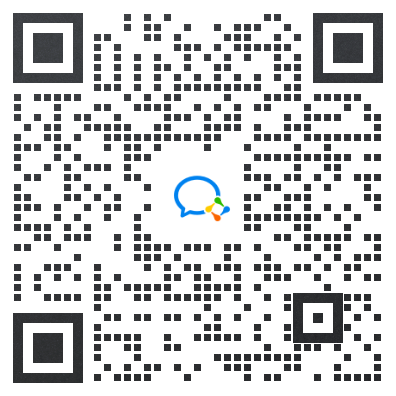
Past Articles
Highlights
RevPi Application Cases · Here
● Quickly upload sensor data to the cloud in just 4 steps using CloudRai.Box
● How to achieve industrial protocol and MQTT conversion in a low-code/no-code manner?
● Five possible uses of industrial Raspberry Pi as soft PLC
● How industrial Raspberry Pi combined with CODESYS can easily solve three major challenges faced by IIOT
Edge Computing · What You Should Know
● Want to achieve device service? You need a powerful edge device!
● What is the machine-as-a-service model?
● What characteristics should HMI for the food & pharmaceutical industry possess?
● Application of smart industrial control screen eX707 in underwater remote control robots
What You Want to Know · OPC UA
● How to solve the troublesome DCOM configuration
● Step-by-step guide to mastering all your UA servers using OPC UA data platform
MQTT Broker · HiveMQ
● Facilitate communication between AGV carts and control systems
● IAV uses HiveMQ with automotive data to build a city flood warning system
● BMW car-sharing application relies on robust HiveMQ for reliable connections
Click below “Read the original text” for more