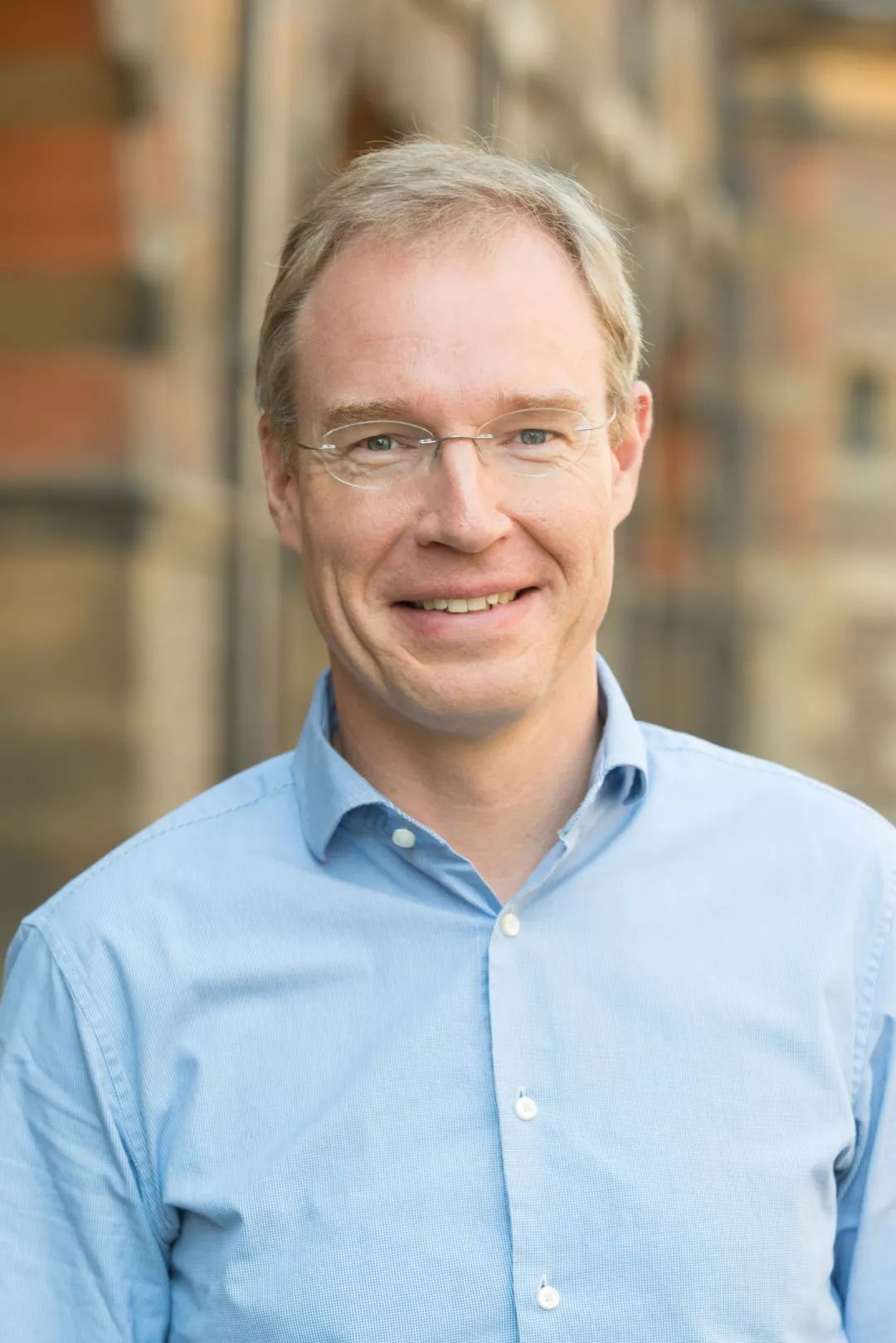
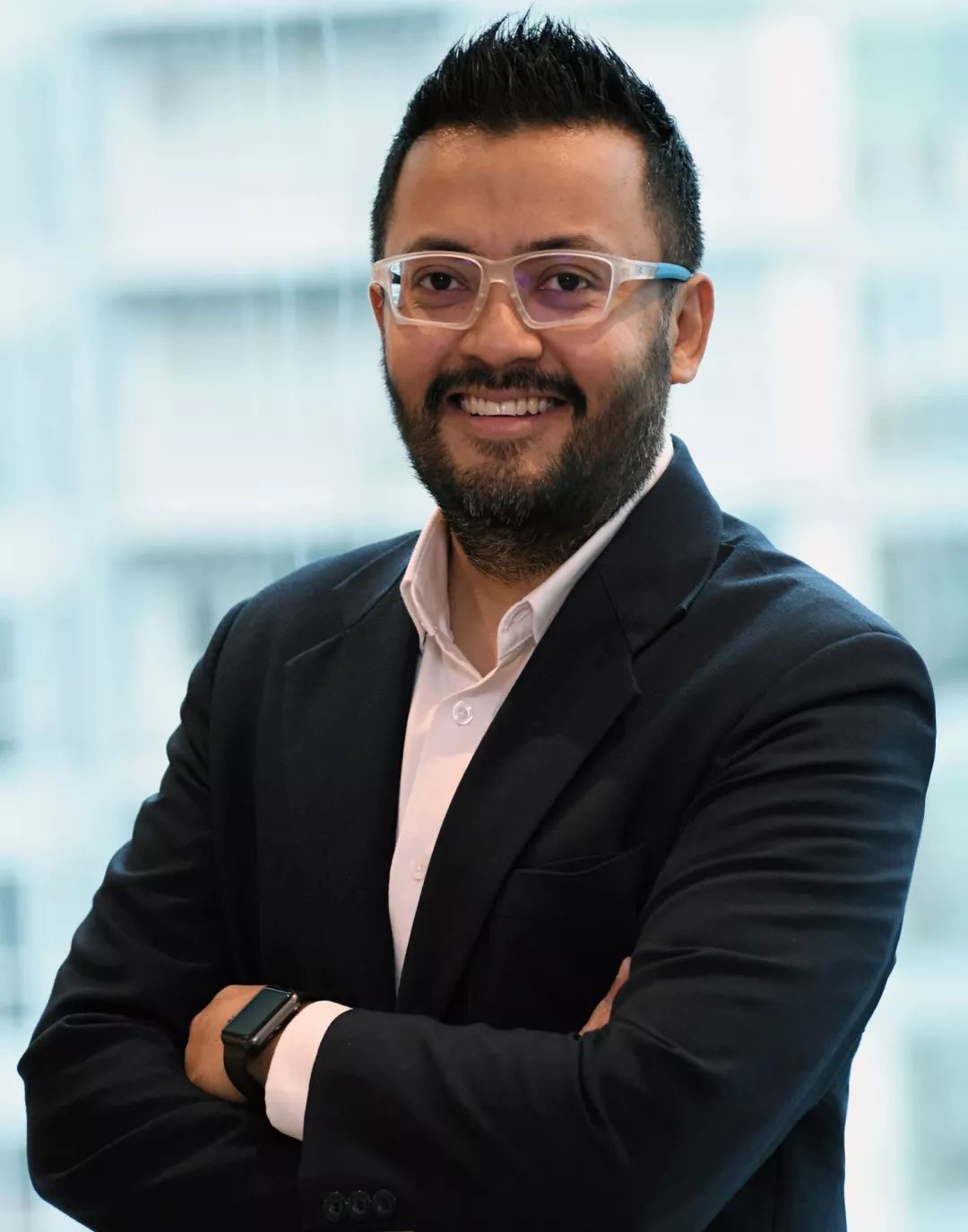
Karel Eloot
Ani Bhalekar

Almost all global manufacturers are testing Industrial Internet of Things (IIoT) technologies, but in a recent McKinsey survey, nearly 70% of executives reported that their IoT projects are stuck in a pilot dilemma and cannot scale at the company level. Moreover, respondents indicated that only 15% of industrial IoT projects achieve scale within a year, and a quarter of these projects have pilot phases lasting over two years.
This is clearly unsatisfactory; to remain competitive in the era of Industry 4.0, relying solely on pilots is insufficient. Worse still, since pilots often cannot exhaustively explore the various possibilities brought about by IoT-driven technological transformation, they are likely to be canceled due to a lack of long-term vision and blueprint. However, the good news is that a well-designed IT/OT architecture will help companies launch vibrant industrial IoT pilot projects, thereby accelerating the realization of scale benefits.
Pilot projects often struggle due to their limited scope, which hampers scalability. Therefore, it is imperative to design use cases that can deliver end-to-end value for the entire company from the outset. This also means that the entire IT/OT architecture must be designed from the beginning, incorporating all use cases. As IT/OT environments become increasingly complex, two key points must be considered when prioritizing use cases:
1. Predefine KPIs related to business value creation and use them to prioritize use cases;
2. Build the technical capabilities needed to support these use cases while constructing the technical architecture solution (also known as a ‘platform’) and applications specifically targeting these use cases.

Industrial IoT Architecture Parallel to Automation Architecture
In the previous blog post, we mentioned that building a scalable technology architecture in industrial settings is particularly challenging and described the factors that contribute to these difficulties, such as the complexity of the industrial automation ecosystem, diverse sensor systems, traditional machines that cannot interconnect, and insufficient coordination between IT and OT.
As a result, industrial companies often struggle to determine the most effective way to find solutions that can truly unlock data and analytical value. Various types of vendors are grasping trends, introducing new technologies, aiming to ensure they can capture a share of this billion-dollar market (as shown in the figure).
On one hand, established traditional industrial automation vendors have significant influence over control points, and they are introducing complementary IoT solutions to help manufacturers deploy end-to-end industrial IoT platforms. On the other hand, this competitive field also includes mature vendors from both OT and IT domains, each with different technological advantages. Some are attempting to build products that cover the vast majority of IT/OT automation architectures, while others focus on a specific niche.
We surveyed five top automation vendors and found that most are still expanding their industrial IoT products and capabilities. Therefore, the entire landscape is not yet established. For example, in areas where these vendors have more mature architectures, they can offer nearly 50 proprietary technologies, such as manufacturing execution systems and similar technologies, while the standardization of industrial use cases has yet to begin. We also found that several large vendors lack services in areas such as automation, human-machine interaction, sensors, and RFID.

Traditional Software Vendors Also Attempting to Solve Industrial IoT Issues
Complicating matters further, traditional software vendors are also competing for market share in the industrial cloud ecosystem. Most of them have entered this ecosystem from the bottom up, first becoming Infrastructure as a Service (IaaS) providers, then pursuing vertical integration of Platform as a Service (PaaS), ultimately leading to the provision of non-industrial Software as a Service (SaaS). This natural extension results in the supply of industrial Software as a Service.
As for automation architecture, many large industry players are initiating competition, but no clear leader has emerged. For factory operators, they have established mature and friendly cooperative relationships with IT and OT technology service providers, but they can hardly predict who will dominate, making it challenging for their internal teams to sift through the continuously improving services offered by vendors. The only clear point at present is that no single vendor can meet all the needs of a company.

Effective Methods for Building Scalable Industrial IoT Architecture
Understanding your starting point and goals helps you find direction in the most complex environments. The same applies to building a scalable industrial IoT platform. We recommend that our clients take the following steps when initiating industrial IoT pilots. In future blog posts, we will delve into these steps one by one with appropriate examples:
■ First, create a reliable list of use cases. Focus not only on the factory itself but also extend to the supply chain and design, viewing the process through the lens of digitizing the complete value chain. This list does not need to be exhaustive but should be representative, covering architectures that can help us achieve our goals. Subsequently, you can determine the corresponding technical architecture requirements for each use case to ensure that technology can ultimately achieve the scale you need at the right speed and cost.
■ Develop a future reference architecture based on business needs. First, assess the existing IT/OT architecture from the factory to the entire enterprise, focusing on all aspects, including technical architecture, manufacturing applications, and tools. At the same time, review past industrial IoT pilots to identify pain points that hinder project advancement.
■ Prearrange for data experts to be involved. Involve data scientists in the design of the reference architecture to avoid delays and unnecessary iterations during implementation, as data scientists clearly know what data will be needed when building analytical models. Data scientists also need to work with process engineers to ensure the accuracy and appropriateness of data source collection.
■ Define the core architecture. Evaluate the pros and cons of selecting a platform, vendor ecosystem, or hybrid approach, and then align with the overall direction.
■ Recommend technical solutions for use cases. Reach a consensus on the technical architecture requirements for priority use cases and compile decision criteria. Customize assessments for industrial IoT platform providers based on these decision criteria to identify the optimal solution.
■ Select vendors based on technical and talent capabilities. While acquiring appropriate technology is crucial, its effectiveness depends on system integration capabilities.
■ In the short term, deploy technology for priority use cases. For priority use cases, carefully selected vendors should be introduced into the organizational ecosystem.
■ In the long term, develop and adjust the IT/OT blueprint. Draft the IT and OT blueprint, aligning it with the organization’s broader business goals and core technologies, and continuously integrate and optimize. However, it should be noted that the duration and time required for ERP implementation can vary significantly.
This approach will help your company find direction and quickly realize value in the complex field of industrial IoT.
Click to view the previous blog:
Outpacing the Last Mile of IT/OT Integration to Avoid the Industrial 4.0 Pilot Dilemma

Authors:
The authors would like to thank Mike Coxon, Subu Naranayan, and Bodo Koerber for their contributions to this article.
Karel Eloot is a Senior Partner at McKinsey & Company, based in the Shanghai office;
Ani Bhalekar is a Partner at McKinsey & Company, based in the Singapore office..
Welcome to follow the WeChat public account of the “Digital Capability Center”
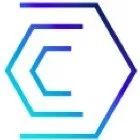

DCC (Digital Capability Center), established by McKinsey in collaboration with Tsinghua University, aims to assist Chinese enterprises in successfully upgrading their manufacturing through digital transformation in the era of Industry 4.0.