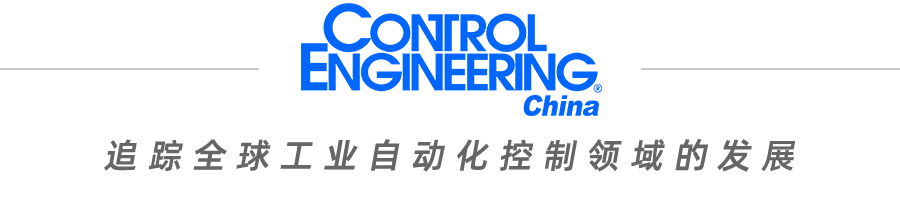
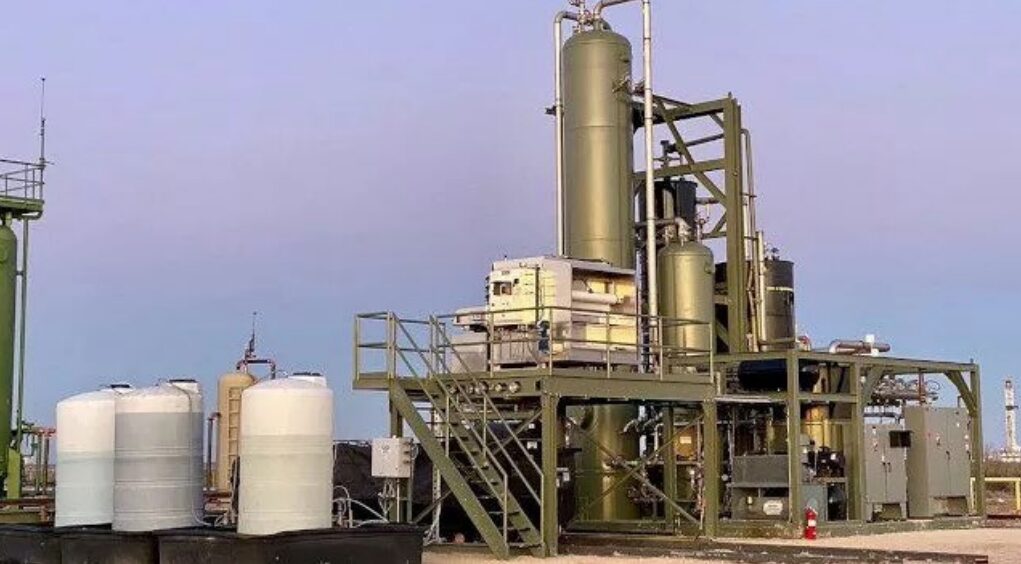
Image Source: Moxa
Author | Eddie Lee
Utilizing IT/OT convergence technologies, through monitoring and data acquisition (SCADA) software, industrial PCs for edge computing, machine learning software, and cloud connectivity, helps create sustainable applications.
A process for measuring and removing hydrogen sulfide (H2S) from natural gas uses sensors, industrial computers (PCs) for edge processing, cloud-based applications, machine learning, and monitoring and data acquisition (SCADA) systems to process agricultural-grade elemental sulfur for fertilizers and other applications. The automation system reduced manual measurement and total labor costs by 75%, making the plant more cost-effective.
01
Measuring and Removing Hydrogen Sulfide from Natural Gas
Hydrogen sulfide is a colorless, flammable gas that poses significant risks to human safety, regulatory compliance, and infrastructure integrity. This toxic gas exists in about 40% to 60% of gas wells globally, and nearly all gas wells in North America, characterized by its distinct rotten egg smell, is an irritant and chemical asphyxiant that affects the central nervous system and respiration. It must be removed from natural gas, and there are various technologies for removing hydrogen sulfide.
While there are chemicals that can directly remove hydrogen sulfide from gas, handling them can be expensive and dangerous. These chemicals are only cost-effective when dealing with low concentrations of hydrogen sulfide. To handle large amounts of hydrogen sulfide, large plants would need to be constructed to remove these toxic chemicals. Most gas wells only have moderate levels of hydrogen sulfide, which is not sufficient to justify building a $50 million facility or to process with chemicals costing $10/lb. There are not many good technologies available to effectively remove hydrogen sulfide between these two options.
02
New Chemical Processes and Control Systems for Hydrogen Sulfide Removal
Streamline Innovations significantly improved the redox process and created one of the most efficient hydrogen sulfide treatment solutions on the market. Their Valkyrie hydrogen sulfide and acid gas treatment system employs the latest chemical processes and advanced control systems to remove hydrogen sulfide from natural gas at both single well and field-wide scales. Compared to all other competing products, it can remove 100% of hydrogen sulfide from the natural gas stream, helping customers significantly reduce operational costs. Most importantly, the Valkyrie system converts hydrogen sulfide into agricultural-grade elemental sulfur, benefiting soil remediation, crop fertilizers, and pest control.
So far, Streamline Innovations has produced over 20 million pounds of sulfur at its plants in Texas and New Mexico and is expanding into international markets, biogas treatment, and refinery processing. If left untreated, this sulfur would convert to sulfur dioxide, a major contributor to acid rain.
03
Challenges Facing Redox Process Control Systems
The redox process requires precise chemical reactions. However, it is challenging to optimally control both oxidation and reduction processes. What makes it more challenging is the varying concentrations and flow rates of hydrogen sulfide in natural gas. Therefore, constant adjustments are needed for the quantity of chemical reagents added to the gas. If too much is added, the chemical process may stop. If too little is added, some hydrogen sulfide may enter the pipeline. For this reason, in older processes, experts in the field needed to check concentrations and flow rates every few minutes.
Unfortunately, experts cannot stay at natural gas facilities all the time and cannot visit frequently, especially in small installations at remote wells. Streamline’s Valkyrie process replaces the