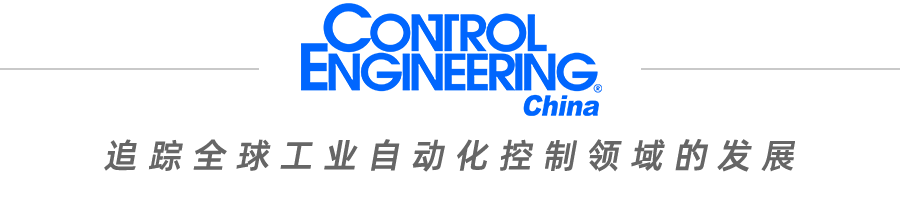

This image is provided by: Hongke
Author | Hongke Industrial IoT Team
01
The Necessity of Predictive Maintenance
With the rise of a new round of technological revolution and industrial transformation, technologies such as the Industrial Internet of Things, big data, and artificial intelligence are rapidly penetrating and integrating with various fields of economic and social life. Due to the market’s demand for refined cost control, the importance of equipment has become increasingly prominent, and maintenance strategies for equipment must inevitably upgrade from reactive maintenance to preventive maintenance, and further to predictive maintenance.
Currently, there are three maintenance methods: reactive maintenance, preventive maintenance, and predictive maintenance. Reactive maintenance is performed after a device fails, which is a costly maintenance method. Preventive maintenance is planned but not goal-oriented maintenance based on time, performance, and other conditions, relying more on experience. Predictive maintenance involves state monitoring and health assessment of equipment, performing maintenance as needed. Compared to reactive and preventive maintenance, this method is characterized by intelligence, reduced maintenance costs, and minimized downtime.
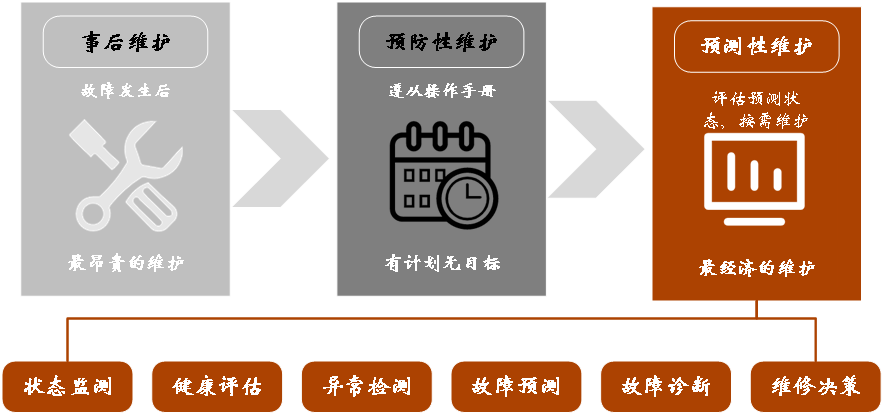
02
Methods of Predictive Maintenance
Predictive maintenance can be classified based on components into hardware, solutions, and services. Predictive maintenance services mainly include consulting, maintenance, support, and system integration. Based on monitoring methods, it can be divided into ultrasonic monitoring, vibration monitoring, infrared thermal imaging, current monitoring, temperature monitoring, and oil analysis, among which vibration monitoring is the primary method for predictive maintenance of equipment, capable of identifying early faults and determining fault locations without disassembling the equipment.
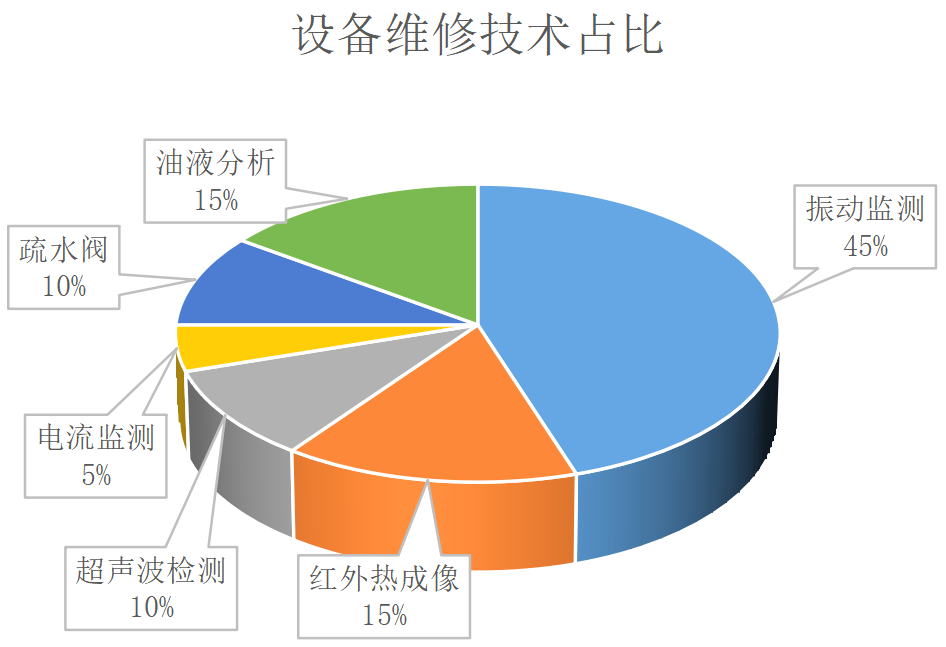
Data analysis shows that current factory faults are mainly mechanical, control, program, and communication types, with mechanical faults being the most prevalent. As equipment operates, it exerts different forces on various components, leading to different mechanical failures over time, such as bearing wear, looseness, and resonance.
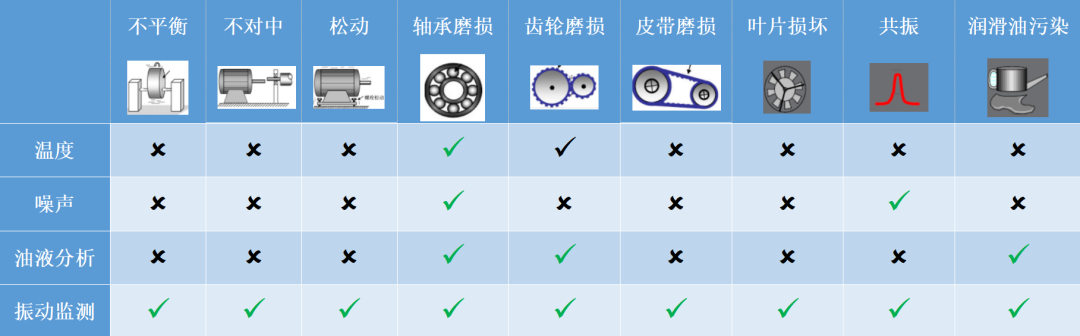
These various faults can cause different degrees of mechanical vibration, thus vibration monitoring is also the most effective detection technology for mechanical faults. Common vibration monitoring methods include portable vibration monitoring systems, online vibration monitoring systems, and wireless vibration monitoring systems, each with different characteristics and application scenarios. Hongke has accumulated rich experience in fault monitoring and offers an intelligent wireless vibration monitoring solution applicable to continuously operating rotating equipment.
03
Hongke Wireless Vibration Monitoring Solution
The Hongke wireless vibration monitoring solution mainly includes Accel 310 High-Resolution Wireless Vibration System, an automated diagnostic platform, and a predictive portal. In this solution, users can obtain hourly vibration and temperature scalar data for assets and receive daily vibration diagnostic analyses, enabling around-the-clock fault monitoring of assets. Supported by the automated diagnostic platform, combined with a rich database and advanced algorithms, accurate fault information can be obtained, and users can log into the predictive portal to view health scores for assets, factories, and enterprises, thus receiving prioritized maintenance recommendations.
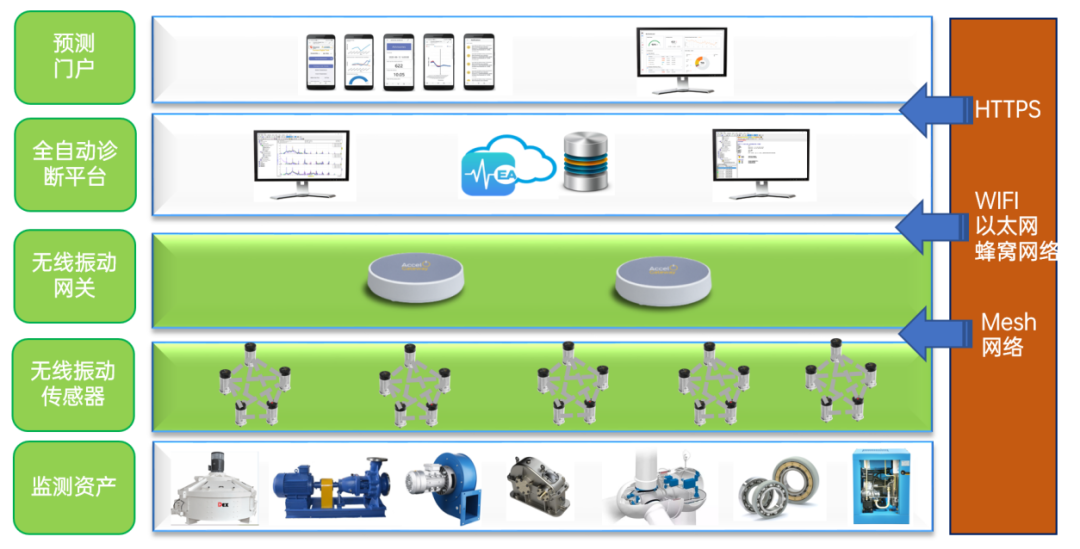
(1) Accel 310 Wireless Vibration Sensor
■ Integration of vibration and temperature piezoelectric sensor;
■ Sampling rate can reach 26.7KHz, capable of detecting up to 10KHz FFT;
■ Unique impact demodulation function, capable of detecting machine faults at speeds as low as 350rpm;
■ Wirepas mesh network, sensors automatically search for and connect to nearby gateways upon activation;
■ 3.6V lithium thionyl chloride battery, with a lifespan exceeding 3 years under standard usage conditions.
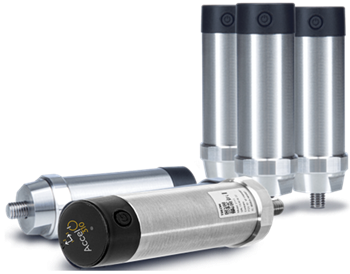
(2) Accel 310 Wireless Vibration Gateway
■ Uses Wirepas mesh network, providing reliable communication;
■ Gateway and cloud platform are pre-configured;
■ Can quickly configure Ethernet/WIFI/cellular networks to connect the Accel 310 system to the cloud platform;
■ Models with IP20 or IP66/IP67 protection levels can be selected based on application requirements.
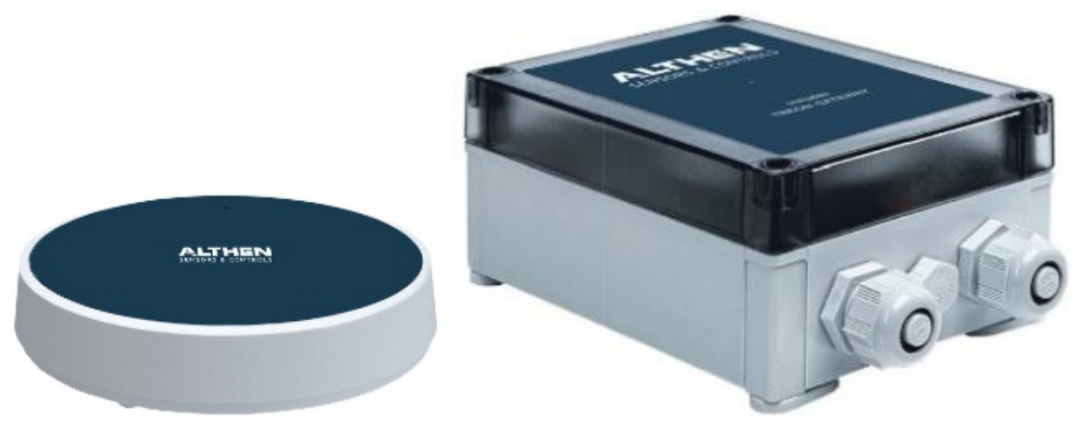
(3) Automated Diagnostic Platform
■ Can apply over 6000 diagnostic rules, 1200+ fault diagnostic conditions, and identify faults for over 40 types of industrial machines;
■ Can instantly process vibration measurements and provide fault diagnosis, severity, maintenance recommendations, and maintenance priorities for each machine.
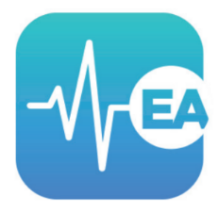
(4) Predictive Portal
■ Can quickly log in via computer or mobile web, viewing the health status of equipment assets and factory performance anytime, anywhere;
■ Both workshop managers and corporate decision-makers can receive alerts for faults, production risks, business metrics, etc.;
■ Can monitor the status of wireless vibration system hardware to ensure normal operation of the wireless system.
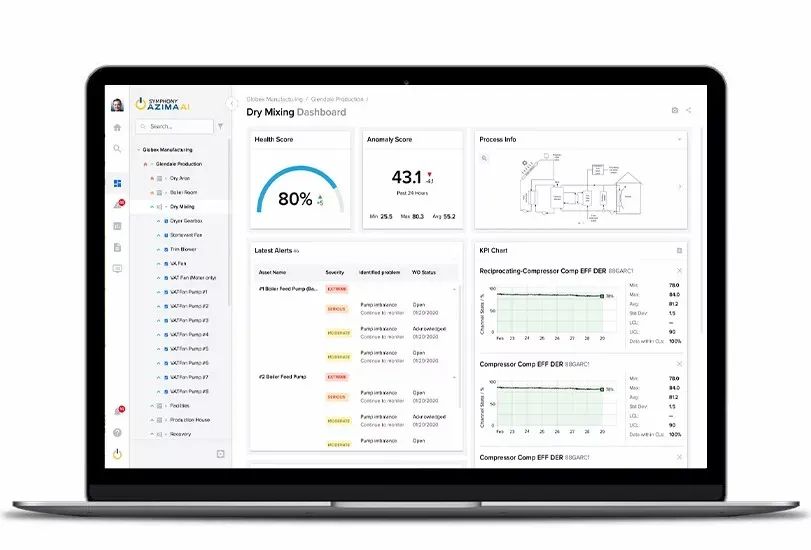
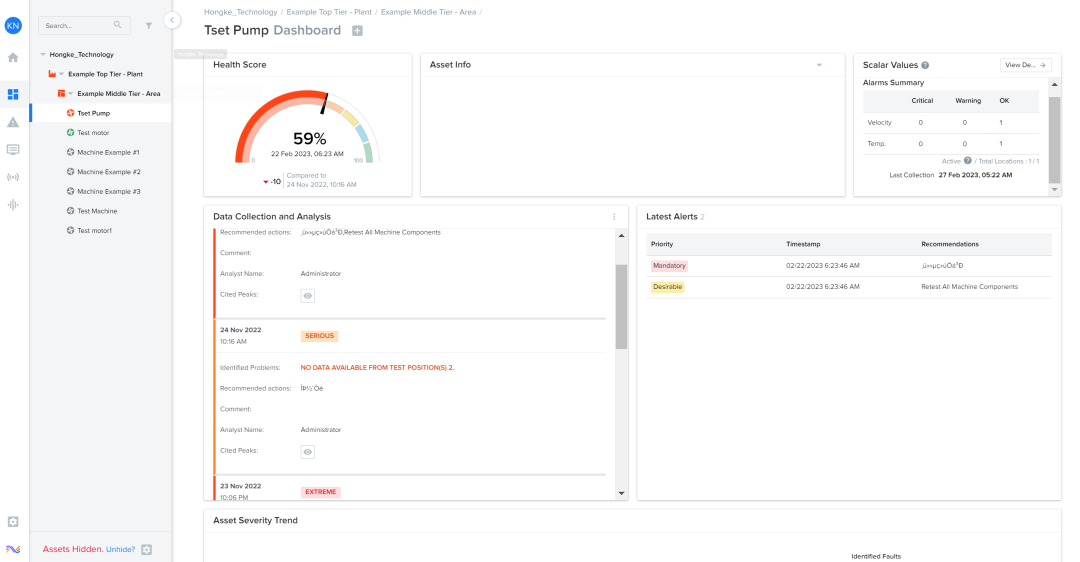
04
Application Cases
Case 1
A chemical enterprise needs to monitor the condition of centrifugal pumps in the workshop, where bearings, as critical components of rotating equipment, are common sites for mechanical failures. We recommended the client use Hongke Wireless Vibration Monitoring System for bearing fault monitoring. From April 2022 to mid-April, the wireless vibration system detected a sharp increase in bearing severity, and the expert diagnostic platform recommended checking the bearing lubrication. The user checked and found that the lubricant was depleted, and after addressing the lubricant pump issue, the data trend significantly declined within just 5 minutes, maintaining a steady trend over time, thus preventing more severe faults due to lack of lubrication.
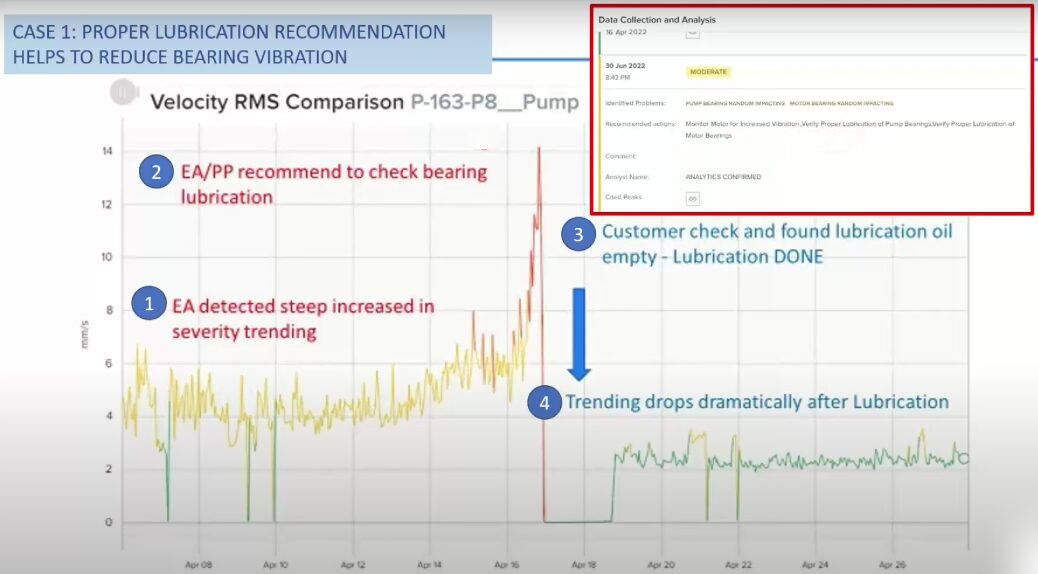
Case 2
A water treatment plant needs to monitor the vibrations of pumps, where common faults include bearing wear, blade wear, and shaft misalignment. We recommended the Hongke wireless vibration monitoring solution to the client, and after some time of use, the wireless vibration monitoring system detected an increase in impact trends, showing a level of 7.1g exceeding the allowable limit of 6.0. Diagnostic analysis indicated bearing wear. The expert automatic vibration system advised the user to shut down for inspection, and upon disassembling the pump, the user found that the rolling bearing cage was damaged. After replacing the bearing, the impact demodulation trend decreased, and by June 8, 2022, the impact demodulation showed the bearing health range was between 4g and 5g.
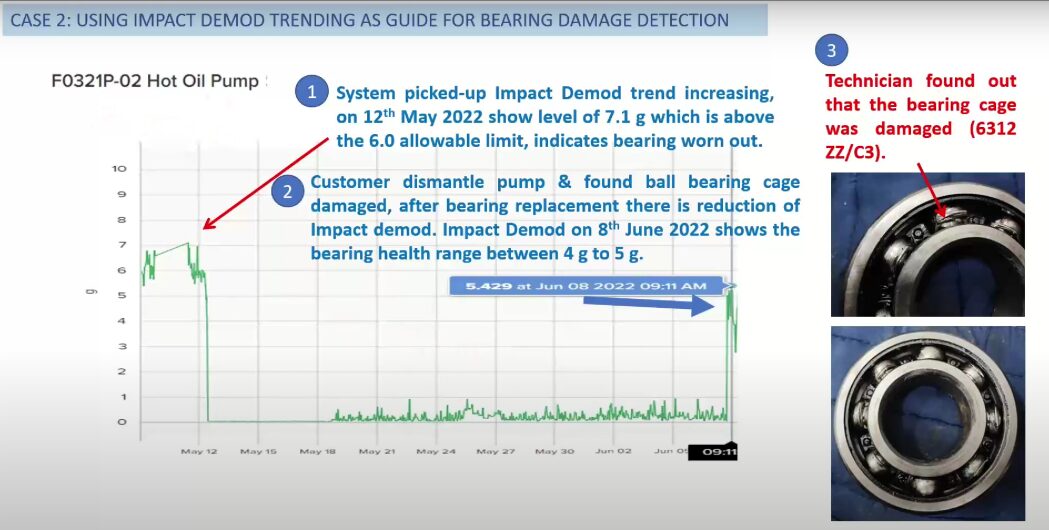
05
Conclusion
As an important application in the Industrial Internet of Things industry, predictive maintenance is increasingly valued by the market, further promoting the transformation of manufacturing development towards an intelligent new model. Through the wireless vibration monitoring solution provided by Hongke, real-time predictive maintenance of industrial assets has been achieved, reducing unplanned maintenance and safety incidents, thereby lowering annual maintenance costs for enterprises. At the same time, it has effectively increased asset lifespan, improved operational uptime, and ensured corporate benefits.
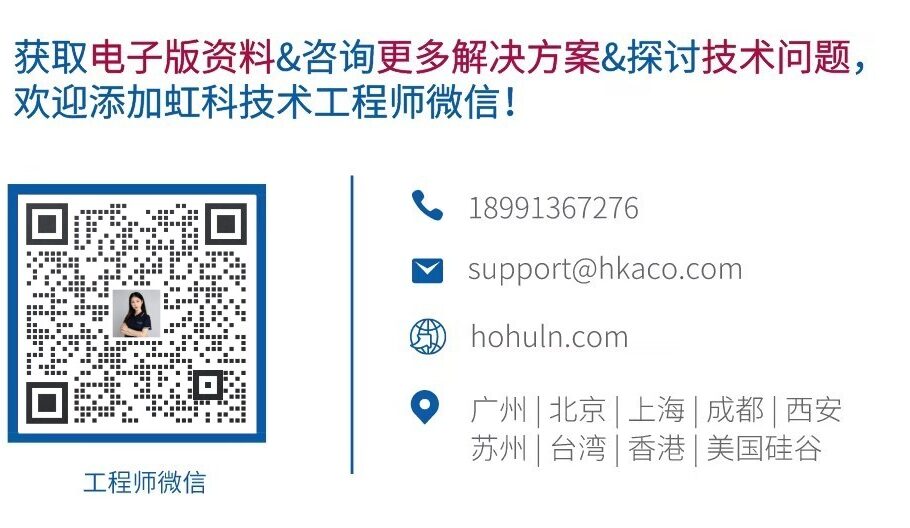
From March 1 to 3, 2023, Hongke will participate in the Guangzhou International Industrial Automation Technology and Equipment Exhibition (SIAF). Our professional technical engineers will showcase our latest intelligent manufacturing solutions, including Industrial IoT, Industrial Automation, Intelligent Sensing, AR, at booth 【C45-3, Hall 11.2】 in Area B of the Guangzhou Import and Export Fair Complex. We welcome you to visit the Hongke booth for discussions!
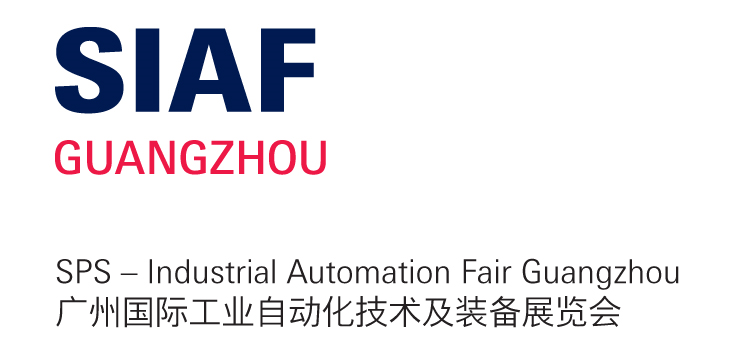
Date: March 1-3
Location: Guangzhou Pazhou Exhibition Hall, Area B, Hall 11.2, C45-3
– END –