Introduction
Automotive Aluminum Alloy Materials
Reducing the weight of the body structure is key to achieving lightweight vehicles. Aluminum alloy, with its high specific strength, good corrosion resistance, formability, and connectivity, has become one of the preferred materials for body structure lightweighting. Currently, commonly used deformed aluminum alloys in automotive body structures include 5xxx and 6xxx series. The 7xxx series aluminum alloys are used less frequently due to cost reasons.
Table 1 Common Deformed Aluminum Alloy Grades and Properties for Automotive Body Structures
Application of Aluminum Alloy in Body Structures
1.Audi e-tron
Audi e-tron is a typical model that transitioned from a previous generation steel body (approximately 18% aluminum alloy) to a steel-aluminum hybrid body (approximately 50% aluminum alloy). The Audi e-tron not only uses aluminum alloy materials extensively in its outer panels but also incorporates a certain proportion of aluminum alloy materials in its structural components. The main aluminum alloy sheet used is the 6xxx series, which accounts for 42%, as shown in Figure 1.
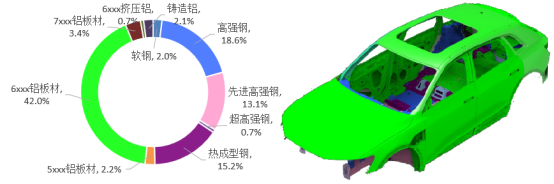
Figure 1 Material Proportion of Audi e-tron Body Structure
As shown in Figure 2, the most significant weight reduction effect of aluminum alloy in the vehicle body components is observed in the roof and cross beams, achieving a weight reduction ratio of 58%. The aluminum alloy upper body also reduced weight by 80.6 kg compared to the steel upper body.
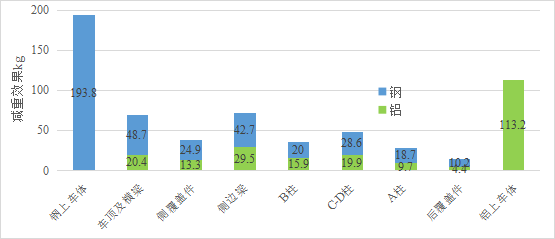
Figure 2 Weight Reduction Effect of Aluminum Alloy Body Structure in Audi e-tron
Among the aluminum alloy components in Audi e-tron, the most typical and concerning aspect for designers is the aluminum alloy B-pillar and its corresponding crash safety results. The upper part of the B-pillar in Audi e-tron uses high-strength 6xxx aluminum alloy as the outer panel, 7xxx aluminum alloy as the inner panel, and the lower part uses laser welded 6xxx aluminum alloy. The B-pillar design achieves the same structural safety as hot-formed steel when responding to side impacts, which verifies the safety of this aluminum alloy B-pillar solution, as shown in Figure 3.
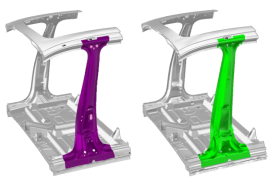
Figure 3 Aluminum Alloy Solution for Audi e-tron B Pillar
Compared to the steel B-pillar solution, while the aluminum alloy B-pillar increases the number of integrated components, it achieves a weight reduction of 2.1 kg, as shown in Figure 4.
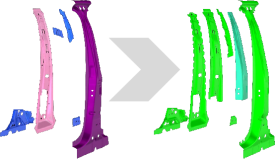
Figure 4 B-Pillar Structural Design Illustration
In addition to the B-pillar, the design of the roof integrated components in the Audi e-tron has also undergone significant changes. Besides extensively using aluminum alloy materials, the structure has been adjusted accordingly, integrating the roof beam design, reducing the use of inner reinforcement components from 20 to 14, and the weight has decreased from 48.7 kg to 20.4 kg, as shown in Figure 5.
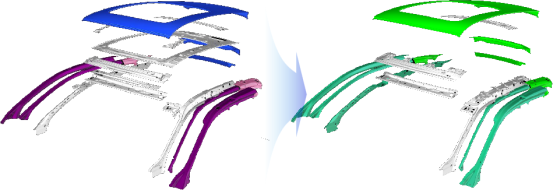
Figure 5 Roof Structural Design
Since the roof beam and B-pillar are crucial for the overall collision safety of the vehicle, the safety of the aluminum alloy material replacement solution has also become a key consideration for body engineers. As shown in Figure 6, the specific strength of the aluminum alloy materials used in the e-tron is comparable to and even slightly higher than that of hot-formed steel, allowing for a certain degree of weight reduction while ensuring safety.
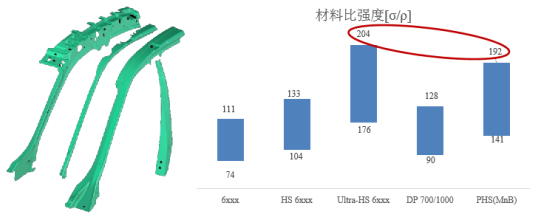
Figure 6 Comparison of Specific Strength of Different Material Solutions for Audi e-tron Roof and B-Pillar
2.Chevrolet Corvette
Compared to Audi e-tron, the application of aluminum alloy materials in Chevrolet Corvette has new characteristics, including the use of aluminum profiles, cast aluminum, and aluminum profile enhanced embedded structures.
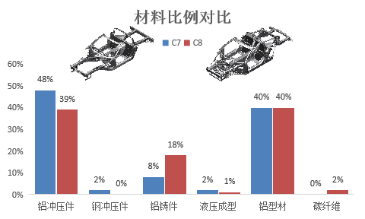
Figure 7 Body Structure Forming Method Distribution of Chevrolet Corvette
1) Use of Aluminum Profiles.
As shown in Figure 7, the materials used in Chevrolet Corvette are primarily aluminum sheets and aluminum profiles. The use of aluminum stamped parts has decreased to some extent in C8 compared to C7, mainly due to the rising prices of aluminum sheets, while the use of aluminum castings has increased. At the same time, the use of aluminum profiles has consistently remained at 40%. One major reason is that the mold costs for aluminum profiles are significantly lower compared to aluminum sheets, and Japanese companies have long started their technological layout in aluminum profiles.
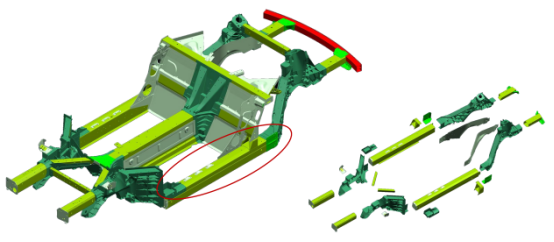
Figure 8 Use of Aluminum Profiles in Body Structure Framework
2) Use of Cast Aluminum.
For the tower structure in the body framework, which is a stress concentration point, higher crush strength and fatigue strength are often required. Using cast aluminum as the material for the tower structure can achieve higher strengths than steel due to the possibility of adding more reinforcement ribs in the design, as shown in Figure 9. More importantly, through casting processes, significant cost savings can be achieved in transportation, assembly, and connection, leading to better economic efficiency and lower carbon effects.
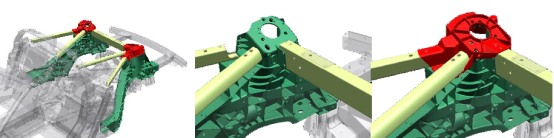
Figure 9 Use of Cast Aluminum
3) Enhanced Embedded Structures.
Due to the higher material costs of 7xxx aluminum alloys compared to 6xxx aluminum alloys, and the production efficiency being only one-third of that of 6xxx aluminum alloys, the most used aluminum profile in Chevrolet Corvette is still the 6xxx aluminum alloy. However, for the 6xxx aluminum alloy, the design of this model adopts enhanced embedded structures to achieve higher strength, as shown in Figure 10.
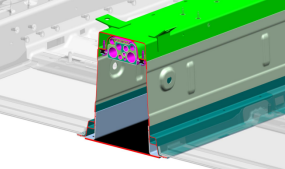
Figure 10 Use of Enhanced Embedded Structures for Aluminum Profiles
Note: The images and data cited in this article are sourced from ECB2021 Source: China Body Conference
Edited by: Chang Da
☞ Jinfen’s Favorite Book Rankings
☞ Mechanical Book Rankings
☞ Production Management Rankings
☞ Design Software Rankings
-
How to Quickly Publish Articles in “Automotive Engineer” Magazine -
BYD Will Supply Batteries to Tesla; The Eight Processes of Blade Battery Production Are Not Simple! -
New Energy Vehicles Show Strong Production and Sales Performance in May; June Is Expected to Be Even Better -
What Are “4680” and “All-Ear” Batteries? No Company Dares to Disclose This Technology at Present! -
3D Printing Tools Assist in Efficient Processing of Motor Housings and Transmissions -
Hydrogen Storage Cylinder Materials and Forming Technologies Restrict the Development of Hydrogen Fuel Vehicles; How to Break the Deadlock? -
The “Metaverse” of Automotive Air Conditioning Production Lines -
Types, Functions, and Design Principles of Common Process Holes in Automotive Body -
It Is a “Smart-Level” Craft Tool That Ensures Automotive Quality, Indispensable in Industrial Production -
The Necessity and Goals of Building a Digital Factory for New Energy Batteries -
Ren Zhengfei’s Recommended 5G Empowerment Has Already Been Published! This PPT Lets You Know Everything. -
Great Wall’s Xu Shui Intelligent Factory: 286 Robots Create the Luxury and Safety of VV5s
For Submissions, Please Click the Image Above