In the era of the Industrial Internet of Things (IIoT), when selecting controllers for industrial automation applications, it is essential to consider not only basic parameters but also data processing, communication, and high-speed control functionalities.
Most industrial controllers, such as Programmable Logic Controllers (PLCs) and Programmable Automation Controllers (PACs), can handle basic functions like real-time control of discrete and analog input/output (I/O) connections. In fact, this type of functionality is inherent in most controllers, with the primary focus being the capacity to handle the number of I/O points, which is usually straightforward to determine.
To better adapt to the implementation of IIoT, companies need to consider other advanced features when purchasing industrial controllers, such as data processing, communication, and high-speed control. Understanding how to implement the required functionalities of controllers and how new features will improve design can help manufacturing enterprises enhance efficiency.
01
Data Processing Functionality
Modern controllers with advanced tag name programming typically offer various data processing functionalities, including built-in data logging. Some advanced controllers can even interact with standard databases in enterprise-level systems, such as Enterprise Resource Planning (ERP) systems.
Recording data directly onto USB storage devices connected to the controller is an essential feature and is often a requirement in many applications. Controllers with data logger functionality typically support formatted USB flash drives or miniSD cards, with each storage space capable of holding up to 32GB.
Data logging is usually event-based or scheduled. Events are triggered by state changes, such as Boolean data state transitions. Scheduled data logging is set to occur periodically, such as every minute, hour, day, or month.
The number of loggable tags is usually limited, but at least 50 tag values should be configured for each scheduled or triggered item. System errors should also be stored along with the time and date of the error or event occurrence. Log file names should be configurable or automatically generated based on user preferences.
In addition to on-site data recording, some controllers can communicate with information technology enterprise systems. An OPC server connected to the controller is one example. It allows the server to collect real-time data from the controllers in the factory floor and retrieve, add, delete, and update data records in a standard database. This is accomplished through connections supporting Microsoft Access-compatible databases, Structured Query Language (SQL) servers, or Open Database Connectivity (ODBC).
Some software tools available on the market allow users to establish connections between IT enterprise systems and PLCs, enabling data collection from PLCs to be stored in databases. The configuration workload for these servers is typically minimal, allowing users to set them up to only collect the data required for their processes.
These database functionalities provide practical applications for tracking material movement and production metrics. Controllers executing actual production tasks can track progress on the factory floor to ensure optimization of manufacturing time. They can also track material consumption. This information can be used to adjust inventory to ensure sufficient material supply when needed.
By recording production data while manufacturing parts or products, these functionalities can also be used to track the status of products from start to finish. Saving the status of the final product, along with the built-in date/time stamp functionality of the database, can meet quality assurance or audit requirements.
02
Communication Functionality
Another important feature to consider when selecting automation controllers is communication capability. Multiple Ethernet and serial communication ports should be provided to facilitate easy integration with Human-Machine Interfaces (HMIs), motor drives, and other devices (Figure 1). These high-speed Ethernet ports can also be used for point-to-point (P2P) or business system networks. Support for EtherNet/IP and Modbus TCP/IP Ethernet protocols is also crucial.
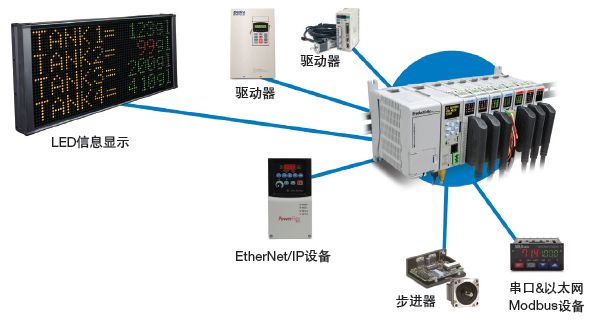
Figure 1: Productivity depends on data collection. The communication and data processing functionalities of controllers can connect to many different devices. Image source: Automation Direct
At the same time, controllers should provide other communication ports for USB input/USB output, miniUSB, miniSD, remote I/O, RS-232, and RS-485 connections. These connections enable simple programming access, connection with high-speed devices like drives, and integration with monitoring HMIs. They also support email sending, scanner/client and adapter/server connections, and other communication functionalities for remote access.
Remote monitoring applications allow users to connect to the controller using Wi-Fi or cellular network links. By configuring user tags for remote access within the tag database, remote users can monitor local controllers.
In hardware configurations related to remote access, modern controllers should have built-in security with the ability to select corresponding tags in the database to enable remote access when the remote functionality must be enabled. Additionally, for any device accessible from the internet, it is strongly recommended to use firewalls for security. Although remote access functionalities of controllers can and should be configured with password protection, a secure and encrypted Virtual Private Network (VPN) connection is a better choice due to internet security risks (Figure 2).
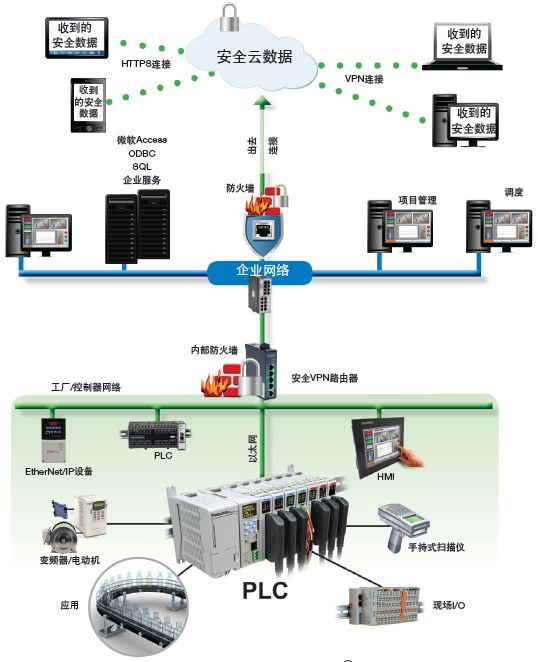
Figure 2: Retrieving remote data from controllers. Some modern controllers have up to seven built-in communication ports, providing critical functionalities for connecting factory floors and enterprise-level business networks.
Another protective feature related to remote controller access is account and IP address separation configuration, allowing users to upload, download, or edit programs under a given remote access connection. An account should not simultaneously allow remote monitoring and program modification. Controllers should support remote monitoring applications and include necessary security measures. Authorized users should be able to connect smartphones or tablets to the controller for remote monitoring via Wi-Fi or cellular connection.
Other web server functionalities in controllers can allow remote troubleshooting of issues via system tags, error logs, and event history, enabling remote users to check data files recorded on the controller’s hard drive or miniSD card.
03
High-Speed Control Functionality
Another important reference feature when purchasing modern controllers is the ability to control motion and other high-speed applications. Executing these functionalities requires high-speed I/O, as well as powerful processors and the ability to prioritize high-speed tasks.
While some controllers provide coordination between multiple motion axes, even coordinating motion between two axes usually requires special hardware and built-in controller functionalities. First, high-speed output modules and high-speed input modules are needed. High-speed output modules generate pulse and direction commands to command servo drives controlling two or more servo motors. These pulse and direction commands can control various applications, such as cutting lengths, stitching, and coordinated x-y axis movement.
Registration functionalities can also be used for motion commands generated by high-speed output modules. Registration functionalities can use the built-in I/O of the module to trigger multiple internal and external position-based events. Signals from sensors via high-speed input modules can trigger the start or stop of motion, capture encoder feedback position, or open/close or pulse outputs.
Programmable Drum Switches (PDS) and Programmable Limit Switches (PLS) provide additional high-speed control functionalities. PDS, like encoders, can monitor multiple devices at rates up to 1MHz. These input signals are used to coordinate and control outputs at thousands of times per second. This type of hardware configuration provides precise and accurate motion control, independent of the controller scan time, which can vary based on processor load.
PLS instructions work similarly to mechanical rotary cams with limit switches, but the virtual shape of the cam can be controlled in real-time. Since this functionality typically operates with high-speed inputs, it is entirely independent of processor load and related scan times, providing accurate and repeatable timing for high-speed applications. When selecting PLCs, PACs, and other industrial controllers, users need to consider control and I/O requirements that go beyond basic functionalities (Figure 3). For many applications, controllers also need to have extensive data logging and communication functionalities, as well as control for high-speed applications like coordinated motion.
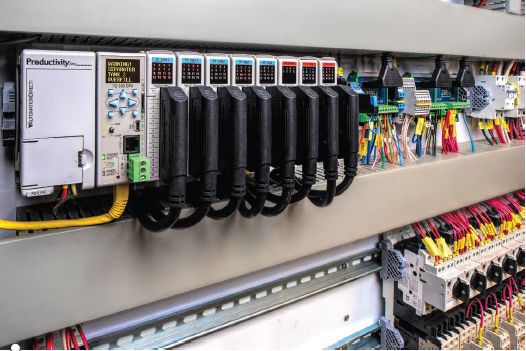
Figure 3: The functionalities of controllers are continuously expanding. Features such as data processing, communication, and high-speed control should be considered during the selection process to improve design.
– END –
This article is from Control Engineering China (July 2019) in the “Technical Articles” section, originally titled: 3 Key Points for Choosing Industrial Controllers
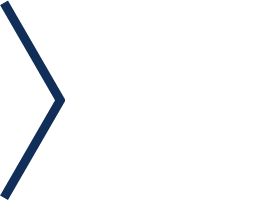
This Issue Magazine
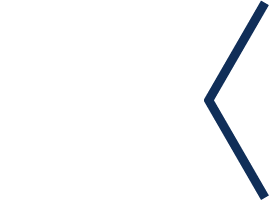
Good News: The mini-program for Control Engineering China is now online. Click on the magazine cover to open the mini-program and read past magazines.
Recommended Reading
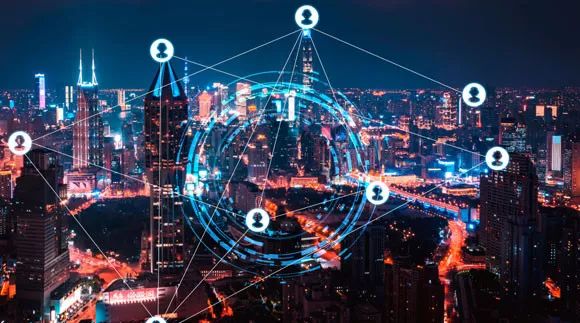
[In-Depth Interpretation] The Most Common Messaging Protocol in IIoT — MQTT
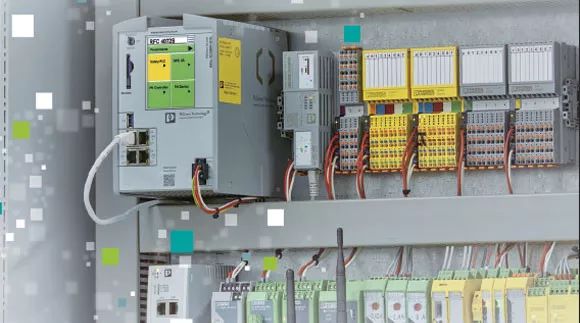
Six Important Factors to Consider When Choosing an Industrial Automation System Integrator
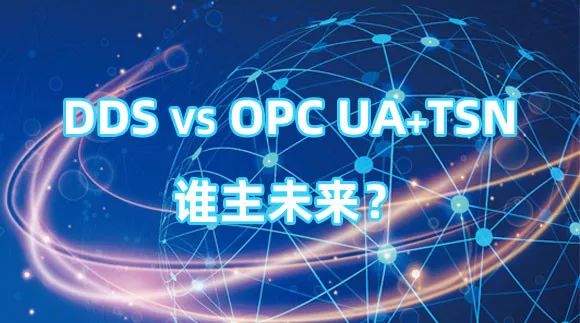
DDS, OPC UA, TSN — The Future of IIoT Communication Standards in Manufacturing
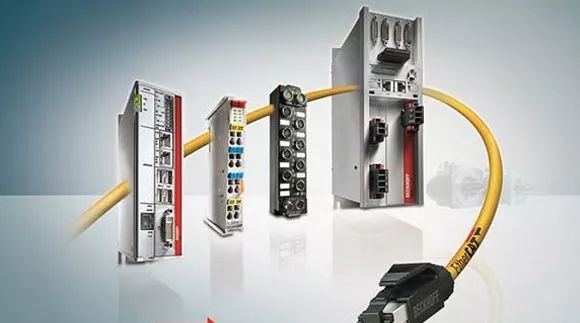
Making Fault Diagnosis Easier — Software Unlocks EtherCAT Ethernet Protocol Diagnostics
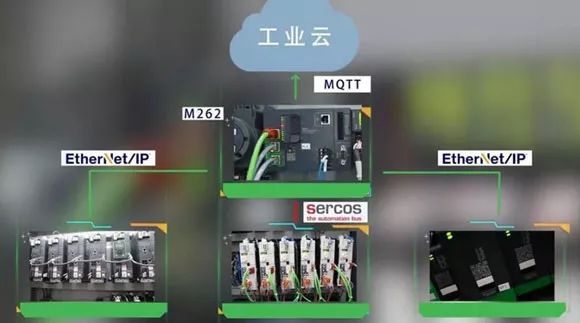
The Future of OEM: How to Rapidly Develop IIoT-Ready Machines
Read a high-quality original article every day, follow us!