1. Bandwidth
Generally refers to the range of signals where the sensor output response decreases to the square root of one-half of its maximum response or half of the power. Simply put, it indicates the range that the sensor can sample, and the bandwidth is the indicator of the sensor’s response range to external signals, mainly describing the dynamic characteristics of the sensor (whether it can keep up with the frequency of the measured changes). The effective bandwidth refers to the bandwidth that the sensor can actually guarantee measurement accuracy. Here, the bandwidth is actually described from the frequency domain. In other words, this is essentially the same as frequency response, which is the sensor’s ability to react to external signals! From the perspective of the transfer function, most sensors can be simplified to a first or second-order element.
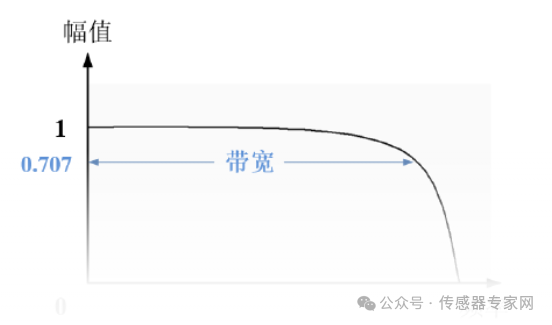
2. Sensitivity
Sensitivity refers to the ratio of the output change △y of the sensor under steady-state operation to the input change △x.
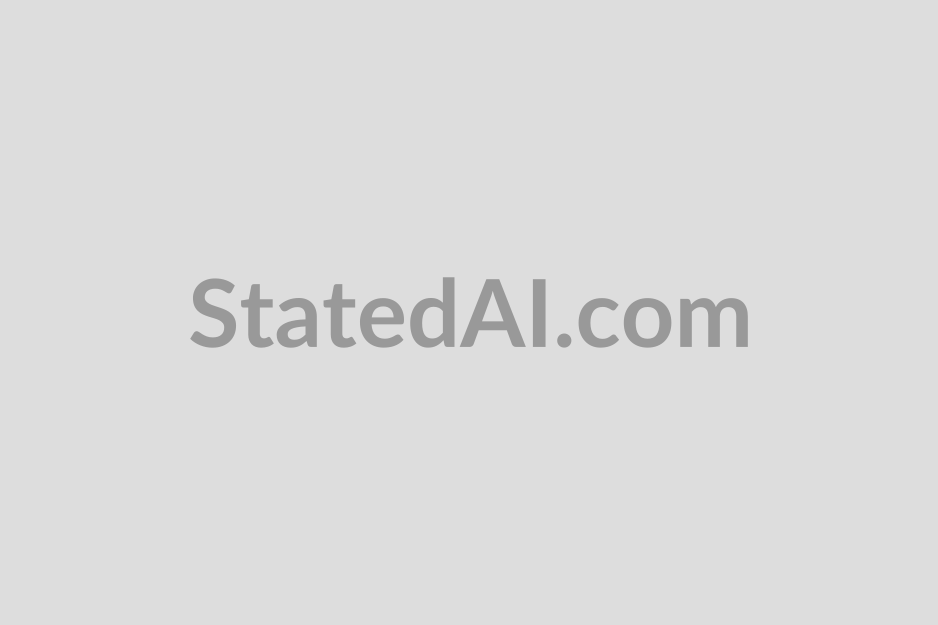
Generally, within the linear range of the sensor, higher sensitivity usually means a higher signal-to-noise ratio, corresponding to a larger output signal value for the measured changes, which is more favorable for signal processing. However, it should be noted that high sensitivity in sensors can easily mix in external noise unrelated to the measurement, which is then amplified by the system, affecting measurement accuracy. Therefore, the sensor itself should have a high signal-to-noise ratio to minimize interference signals introduced from the outside.
3. Zero Drift
Zero drift refers to the change in output when the input value of the sensor is zero. The most common factor causing zero drift is temperature drift. Causes of zero drift include: aging of sensitive components, stress, charge leakage, temperature changes, etc.
4. Resolution
Resolution refers to the smallest change that the sensor can detect within a specified measurement range, which is the minimum value of the change that the sensor can detect. For example, using a meter stick can only measure millimeter-level distances, while a micrometer can detect changes at the 1/‰ millimeter level. Resolution is an absolute value with units. For instance, if the resolution of a temperature sensor is 0.1 degrees Celsius and the full scale is 500 degrees Celsius, then its resolution is 0.1/500=0.02%.

5. Accuracy
Accuracy refers to the ratio of the value within three times the standard deviation around the true value to the range, which is the difference between the measured value and the true value. If the purpose of measurement is qualitative analysis, one can choose sensors with high repeatability, but should not choose sensors with high absolute accuracy. If quantitative analysis is required, one must choose sensors whose accuracy meets the requirements.
(1) Causes of systematic errors: inherent errors in measurement principles and algorithms, inaccurate calibration, environmental temperature effects, material defects, etc.; (2) Causes of random errors: transmission gaps, aging of components, etc.
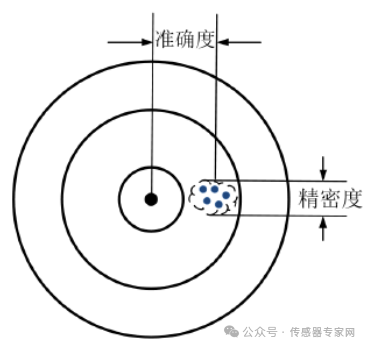
6. Repeatability
The repeatability of a sensor refers to the differences between measurement results when measuring multiple times in the same direction under the same conditions. Also known as repeat error, reproducibility error, etc. The smaller the repeatability error, the better the repeatability, and the better the stability of the sensor.
7. Frequency Response Characteristics
The frequency response characteristics of the sensor determine the frequency range of the measured quantity, and it must maintain fidelity within the allowable frequency range. In fact, the sensor’s response always has a certain delay, and the shorter the delay time, the better. Sensors with high frequency response can measure a wide range of signal frequencies, while due to structural characteristics, mechanical systems have large inertia, so sensors with low frequency response can only measure lower signal frequencies.
8. Hysteresis
Simply put, hysteresis refers to the inconsistency of the input-output mapping curve of the sensor in the forward and reverse directions. The causes of hysteresis include: material characteristics of the sensor’s sensitive component, mechanical structural characteristics (friction, transmission gaps, etc.), etc.
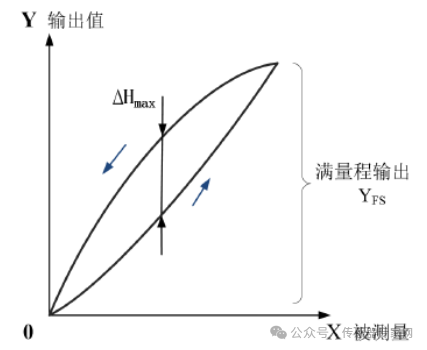
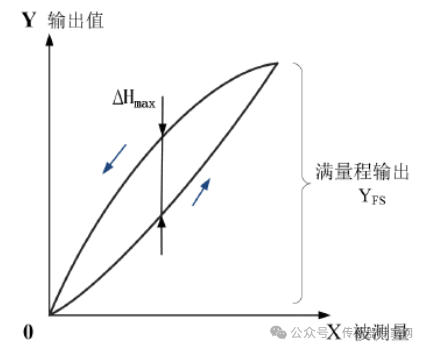
9. Linear Range
The linear range of a sensor refers to the range where the output is proportional to the input. Theoretically, within this range, the sensitivity remains constant, and the wider the linear range of the sensor, the larger its measurement range. However, in reality, no sensor can be absolutely linear; its linearity is relative. When the required measurement accuracy is relatively low, within a certain range, sensors with small non-linear errors can be considered linear for ease of measurement.
10. Sampling Frequency
Sampling frequency refers to the number of measurement results that the sensor can sample within a unit time, reflecting the sensor’s rapid response capability. Sampling frequency is a technical index that must be fully considered when measuring rapidly changing data.
With different sampling frequencies, the accuracy indices of the sensor also change accordingly. Generally speaking, the higher the sampling frequency, the lower the measurement accuracy. However, the accuracy provided by the sensor is often obtained under sampling speed or even static conditions. Therefore, when choosing a sensor, both accuracy and speed must be considered simultaneously.
Source: Electrical Control Technology Master