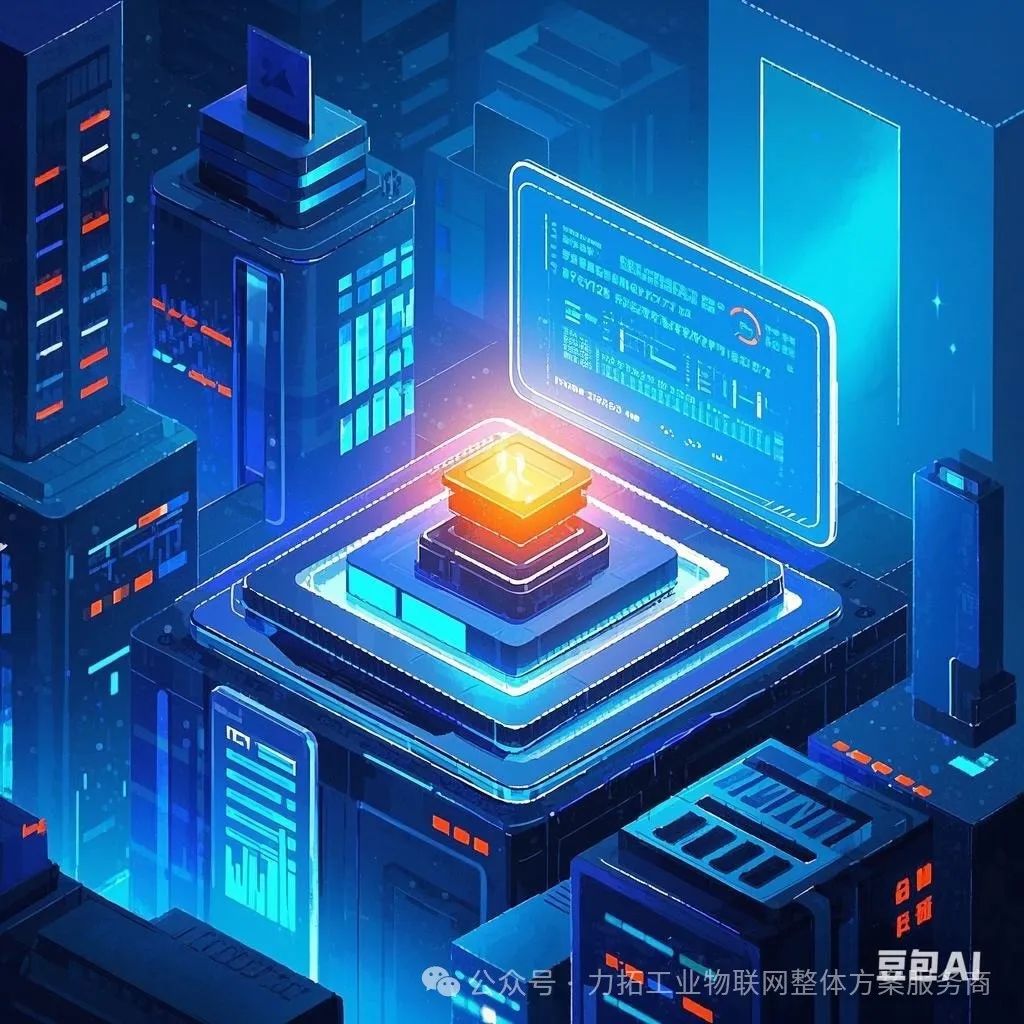
In the current era of rapid technological development, the manufacturing industry stands at the crossroads of digital transformation. As an important component of the new generation of information technology, the Industrial Internet of Things (IIoT) is driving the manufacturing industry into a new era of digitization and intelligence with unprecedented force. It connects devices, machines, systems, etc., into a vast network, achieving real-time data collection, transmission, and analysis, which brings profound changes to various aspects of manufacturing, including production, management, and supply chain.
Optimizing Production Processes, Improving Efficiency and Quality
In traditional manufacturing, production processes often face the problem of information silos, where effective communication between devices and processes is lacking. The emergence of the Industrial Internet of Things breaks down this barrier. By deploying numerous sensors on production equipment, real-time data on equipment operation and production progress can be collected. For example, in an automobile manufacturing plant, the IIoT allows every robot and production line to be interconnected. Sensors can monitor parameters such as temperature and vibration in real-time; once an anomaly is detected, the system can immediately issue an alert and automatically adjust to prevent production interruptions caused by equipment failures. Additionally, product information on the production line can also be tracked in real-time, from the arrival of raw materials to the completion of finished products, with quality data recorded at every stage. This not only helps to identify quality issues promptly but also optimizes production processes through data analysis, enhancing overall product quality.
Enabling Remote Monitoring and Predictive Maintenance of Equipment
In the past, equipment maintenance relied heavily on regular inspections, which were both labor-intensive and struggled to identify potential failures in advance. With the help of the IIoT, companies can monitor equipment remotely. Technicians do not need to be on-site; they can view equipment operating status in real-time through mobile phones, computers, and other terminals. For instance, in the petrochemical industry, large refining equipment distributed across various locations is connected to a control center via the IoT. Managers can remotely monitor critical indicators such as pressure and flow. More importantly, based on the data collected through the IoT, big data analysis, and artificial intelligence algorithms can be used for predictive maintenance. The system can predict when and where equipment might fail, allowing maintenance personnel to prepare in advance and perform maintenance before failures occur, significantly reducing downtime and increasing equipment utilization while lowering maintenance costs.
Driving Supply Chain Collaboration and Improving Response Speed
The supply chain in manufacturing involves numerous links and enterprises, and traditional supply chain information transfer often suffers from delays and inaccuracies. The IIoT brings transparency and collaboration to supply chain management. In the raw material procurement phase, suppliers can share inventory information in real-time through the IoT, enabling manufacturing companies to grasp the supply situation of raw materials promptly and avoid production halts due to shortages. During product transportation, IoT devices can track the location, temperature, humidity, and other information of goods in real-time. For example, vehicles transporting food and pharmaceuticals can take immediate action if there is an abnormal temperature in the cargo area, ensuring product quality and safety. Furthermore, manufacturing companies can quickly adjust production plans based on real-time market demand data through the IoT and collaborate with upstream and downstream enterprises to enhance the entire supply chain’s responsiveness to market changes.
Facilitating Personalized Custom Production
As consumer demands become increasingly diverse, personalized custom production has become a trend in the manufacturing industry. The IIoT enables manufacturing enterprises to shift from mass production to mass customization. Consumers’ personalized needs are transmitted to the enterprise’s production system through the network, allowing production equipment to achieve flexible manufacturing via the IoT. For instance, clothing manufacturing companies can obtain consumers’ body measurements, style preferences, and other information through the IoT, enabling equipment on the production line to automatically adjust parameters to produce garments that meet each consumer’s needs. This personalized custom production model not only enhances consumer satisfaction but also reduces inventory backlog and improves the economic benefits of enterprises.
The Industrial Internet of Things provides comprehensive support for the digital upgrade of the manufacturing industry. From production to management, from supply chain to product customization, every aspect undergoes profound changes due to the IIoT. Manufacturing enterprises should actively embrace IIoT technology and accelerate their digital transformation to remain competitive in the fierce market and create a brighter future.
Ritop – Professional EPC Solution Provider for Industrial IoT
Remote Monitoring, Industrial Interconnection
Visual Management, Cost Reduction and Efficiency Increase
Business Consultation + V: shjsztc3949
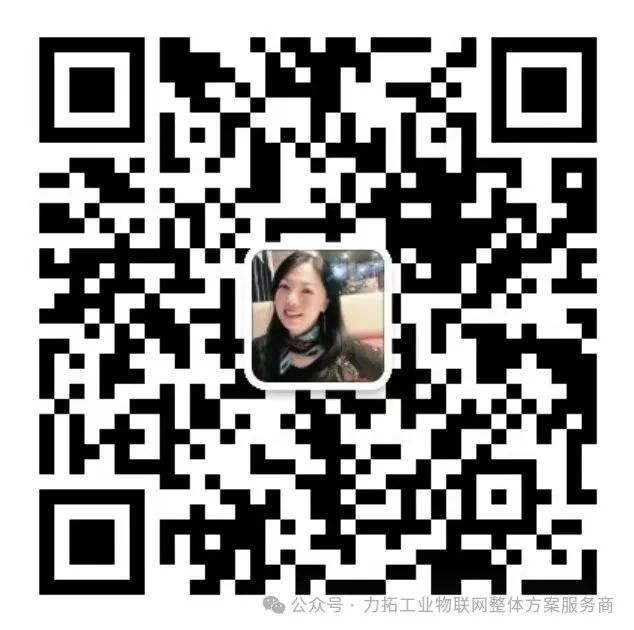